J. Cent. South Univ. Technol. (2011) 18: 29-35
DOI: 10.1007/s11771-011-0654-1

Raman spectroscopy investigation of structural and textural change in C/C composites during braking
LEI Bao-ling(雷宝灵), YI Mao-zhong(易茂中), XU Hui-juan(徐惠娟),
RAN Li-ping(冉丽萍), GE Yi-cheng(葛毅成), PENG Ke(彭可)
State Key Laboratory of Powder Metallurgy, Central South University, Changsha 410083, China
? Central South University Press and Springer-Verlag Berlin Heidelberg 2011
Abstract: The microstructure and texture of C/C composites with a resin-derived carbon, a rough laminar (RL) pyrocarbon and a smooth laminar pyrocarbon, before and after braking tests, were investigated by Raman spectroscopy. The full width at half maximum (FWHM) of the D-band indicates the amount of defects in the in-plane lattice, while the G-to-D band intensity (peak area) ratios (IG/ID) is used to evaluate the degree of graphitization. The results show that the FWHM of D-band of sample with RL pyrocarbon changes greatly from 36 cm-1 to 168 cm-1 after braking tests, which indicates that a large number of lattice defects are produced on its wear surface. However, the graphitization degree of resin-derived carbon sample rises significantly, because the IG/ID increases from 0.427 to 0.928. Braking tests under normal loading conditions, involving high temperature and high pressure, produce a lot of lattice defects on the wear surface, and induce the graphitization of the surface. Sample with RL pyrocarbon having a low hardness is easy to deform, and has the most lattice defects on the wear surface after braking. While raw materials with resin-derived carbon have the lowest graphitization degree which rises greatly during braking.
Key words: C/C composites; Raman spectroscopy; graphitization degree; braking
1 Introduction
Carbon fiber reinforced carbon matrix (C/C) composites display good mechanical behavior under specific conditions such as high temperature. Their low density is also a primary quality governing their use for manufacturing brake discs of heavy vehicles, such as aircraft or trains. Compared with metallic brake systems, brakes made of C/C composites do not fail by fatigue [1], because of the formation of an interfacial debris layer during friction process. Accordingly, high friction and low wear can be achieved, providing both frictional and structural elements in the disk brake. Additionally, compared with conventional steel/ceramet brakes, apparently large weight saving and long braking life C/C composites are expected [2].
The C/C composites currently used as aircraft brake discs are either polyacrylonitrile (PAN) /chemical vapor infiltrated (CVI)-based or pitch/resin/CVI-based composites. Owing to their different formulae and processes, the friction and wear performances of various composites are different. Friction and wear behaviors of a C/C brake disc depend upon many parameters, such as fiber and matrix types, load, speed, temperature and humidity. And many investigations on friction and wear properties of this material have been reported in the past [3-11].
However, few references are focused on the detailed wear-induced microstructural variation for C/C composites. In some previous works, the wear surface of C/C composites was investigated by transmission electron microscopy (TEM)/selected-area diffraction (SAED) technique. MURDIE et al [12] confirmed that the film type debris is comprised of plastically deformed and fractured components of the composites, including fibers, CVI carbon and resin char. Thy also indicated that a thin, amorphous film with nonuniform distribution forms during the wear process. However, in Ref.[13] it was proved that high temperature and high pressure, induced by the wear, cause pitch matrix to be graphitized. More recently, RIETSCH et al [14] found that the wear debris consisted of carbon particles with a low degree of structural organization and with a surface rich in oxygen and hydrogen. To our knowledge, diffraction techniques are usually used to characterize highly ordered solid materials. For disordered materials, however, Raman spectroscopy is more promising, because it is sensitive not only to crystal structures but also to molecular structures (short-range order). The Raman signals of graphite crystals result from lattice vibrations and are very sensitive to the degree of structural disorder. Therefore, Raman spectroscopy is appropriate to analyze the microstructure of carbon materials with defects.
Great progress in tribological properties of C/C composites has been achieved. However, a detail how the structure and texture of C/C composites vary during braking has not been achieved. In order to get further insight into the transformation process, the microstructure and texture of three C/C composites samples with different matrix carbon textures, before and after braking tests, were investigated by Raman spectroscopy. The effects of matrix carbon texture and braking condition on the formation of friction layer were also analyzed.
2 Experimental
2.1 Materials
Three kinds of composites with a resin-derived carbon (A), a rough laminar (RL) pyrocarbon (B) and a smooth laminar (SL) pyrocarbon (C) were made from a three-dimensional needled carbon fiber perform. Preform of sample A was densified by impregnating with resole-type phenolic resin, and performs of samples B and C were densified by CVI in C3H6+N2 atmosphere. The densities of the C/C composites are 1.72-1.75 g/cm3 and volume fractions of carbon fibers in the materials are 33%-35%. All samples were subjected to a final heat treatment at 2 300 °C.
2.2 Braking tests
Braking tests were carried out using a sub-scale dynamometer equipped with annulus-shaped disks as the rotor and the stator, as shown in Fig.1. When the flywheel, which rotated with the dynamic ring sample simultaneously, was accelerated to a certain rotational velocity, braking was achieved through the friction between the dynamic and static rings under a certain braking pressure. The relationship between braking moment and braking time was recorded by computer. The dimensions of the disks were 45 mm in inner radius,
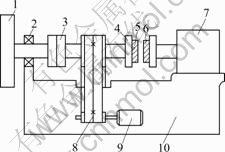
Fig.1 Schematic diagram of home-made laboratory scale inertia type of dynamometer: 1—Inertial wheel; 2—Bearing; 3—Clutch; 4—Specimen holder; 5—Rotor; 6—Stator; 7—Pressing cylinder; 8—Strap; 9—Electric motor; 10—Lathe bed
75 mm in outer radius and 16 mm in thickness. Braking tests were performed under normal loading conditions with a braking speed of 25 m/s, a constant pressure of 0.6 MPa and an inertia of 0.3 kg·m2, respectively. Both the stator and the rotor had continuous fibers orientated parallel to the wear face.
2.3 Microstructure characterization
2.3.1 Polarized light microscopy (PLM)
A MeF3 PLM was used for the characterization of the microstructure of the matrix. Samples were mounted in epoxy resin ground and polished using diamond polishing slurries a grain size from 6 μm down to 0.25 μm.
2.3.2 Transmission electron microscopy (TEM)
A 200 μm-thick sample was cut from the composites with diamond saw, mechanically thinned to 80 μm using sandpaper, and then the middle of the sample was reduced with dimpler to 20 μm, to effectively reduce the difference of thinning rate between of carbon fiber and matrix carbon under the Ar+ ions. Two argon ion guns operating at 4 kV and 12 mA at an angle of 4° relative to the sample surface were used for the final thinning of the sample from both sides. TEM observation was performed on a JEOL2010.
2.3.3 X-ray diffractometry (XRD)
The XRD measurements were performed with a diffractometer D/ruax 2550PC (Cu Kα1). The operating power was 35 kV and 40 mA. The spectra were recorded directly from the powder of the raw C/C composites. The diffraction pattern was recorded at room temperature in 2θ range from 10° to 60° (resolution: 0.02°, counting time: 5 s per interval). The 2θ value was obtained from the (002) diffraction peaks. The interlayer spacing, d(002) was calculated using the Bragg equation.
2.3.4 Raman microspectroscopy (RMS)
The RMS of the raw materials (unworn) was performed on the cross section of polished samples. And samples of the friction layers were directly drilled from wear surface after braking tests to a diameter of 8 mm. All samples were detected at two different points: carbon fiber and matrix. The analyses were conducted with a Lab Ram HR-010 spectrometer (HORIBA Jobin Yvon) with a 632.8 nm emission. The laser power was kept below 0.5 mW to avoid heating of the sample. The objective of the microscope allowed a lateral resolution of about 1 μm and the thickness analyzed was in the range of 50-100 nm.
3 Results and discussion
3.1 Microstructure
BOURRAT and TROUVAT [15] indicated that PLM is a simple and reliable method to distinguish the optical anisotropy, and it is introduced for measuring preferred orientation of pyrocarbon structures more exactly and quantitatively [16]. Fig.2 shows the microstructures of three kinds of C/C composites for brake discs under polarized light.
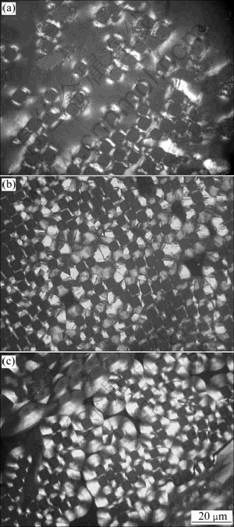
Fig.2 Detailed PLM microstructures of C/C composites: (a) Sample A; (b) Sample B; (c) Sample C
Sample A exhibits a resin-derived carbon structure with optical anisotropy near carbon fibers (Fig.2(a)), largely due to the stress graphitization during heat treatment process. Sample B clearly shows a typical RL structure, with an average extinction angle Ae=20°, consisting of heterogeneous substructures. While sample C shows SL structure with Ae=13°, and there are some gaps among pyrocarbons.
In the SAED pattern, the full width at half maximum (FWHM) of the azimuthal opening of the (002) reflection plane is used to characterize the texture degree. TEM morphology and SAED pattern of different places of three samples are shown in Fig.3. Due to the same heat treat temperature, carbon fibers in three samples show the same texture degree.
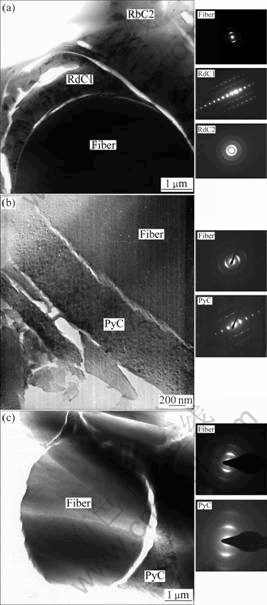
Fig.3 TEM images and SAED patterns of samples (PyC: Pyrocarbon; RdC: Resin-derived carbon): (a) sample A; (b) Sample B; (c) Sample C
As we know, furan-resin-derived carbon can generally produce glass-like carbon having entangled graphene layers (graphite structured) after high temperature heat treatments, but they can produce well- graphitized thin skin on surfaces. Resin-derived carbon can be graphitized when it is pressed during carbonization process, even though the stress is quite low [17]. Fig.3(a) shows that carbon fiber is surrounded by resin-derived carbon regularly and obvious cracks appear between carbon layers. SAED results indicate that resin-derived carbon near the carbon fiber has high texture degree, while carbon far from the fiber is characterized by a low texture degree. Thermal stress is generated at the interface between resin-derived carbon and carbon fiber during the high temperature treatment process, due to their different thermal expansion coefficients, and the high temperature of 2 300 °C results in the stress graphitization on the surface of resin-derived carbon.
Fig.3(b) shows that pyrocarbon with high texture degree surrounds the carbon fiber in sample B. On the contrary, pyrocarbon in sample C is low textured (Fig.3(c)), which is in agreement with the PLM result.
3.2 XRD results of samples
The XRD spectrum for the raw C/C composites shows the evidence of the degree of graphitic order as indicated by the average crystallite size and interlayer spacing d(002). As seen in Table 1, the d-spacing of sample B is the smallest, since the RL-structured pyrocarbon is easy to be graphitized. In contrast, sample C with SL is difficult to be graphitized, so the corresponding d-spacing is rather large. Additionally, the size of crystalline perpendicular to the hexagonal layers (Lc) of sample A is less than that of sample C, which means that the d(002) of sample A is less than that of sample C, but there are a few hexagonal carbon layers stacked in parallel in sample A.
3.3 RMS
Pyrocarbons are paracrystalline materials [18].
Table 1 Physical properties of three samples
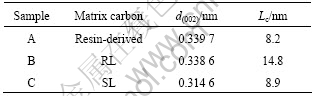
Therefore, pyrocarbon structure has to be described at a nanometer range (also called structure) and at long range (texture) [19]. BOURRAT and TROUVAT [15] proposed to measure the crystalline defects of the lattice at short range and the anisotropy of the texture at long range.
Experimental results from graphitization studies of carbon materials showed that the FWHM of both the D- and G-band are correlated with the structural state of the material [20]. FWHM of D-band is very sensitive to the low energy defects. For a homogeneous family of carbon, it was proposed to discriminate, with success, the amount of defects in the lattice [21]. Therefore, FWHM of D- band was chosen as the in-plane structural ordering parameter.
The optical micrographs and corresponding Raman spectra of the raw materials and the wear surfaces are presented in Figs.4, 5 and 6. Polished surfaces of PLM samples, also used for RSM tests, are perpendicular to
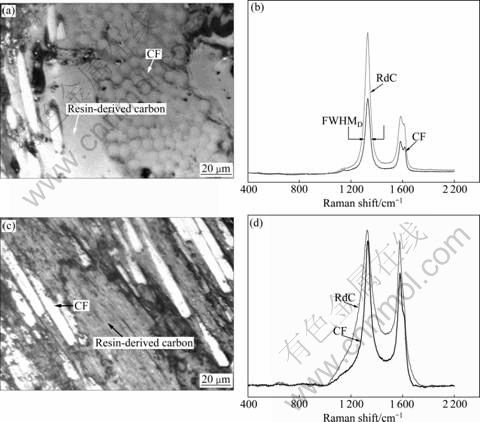
Fig.4 Optical micrographs and Raman spectra of sample A (CF: Carbon fiber): (a) Optical micrograph of polished section of raw materials; (b) Raman spectra of two different points on raw samples; (c) Optical micrograph of wear surface; (d) Raman spectra of two different points on wear surface
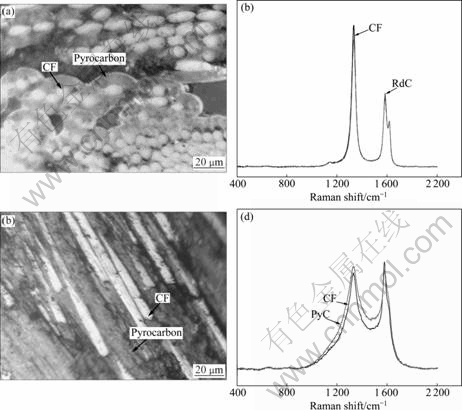
Fig.5 Optical micrographs and Raman spectra of sample B: (a) Optical micrograph of polished section of raw materials; (b) Raman spectra of two different points on raw samples; (c) Optical micrograph of wear surface; (d) Raman spectra of two different points on wear surface
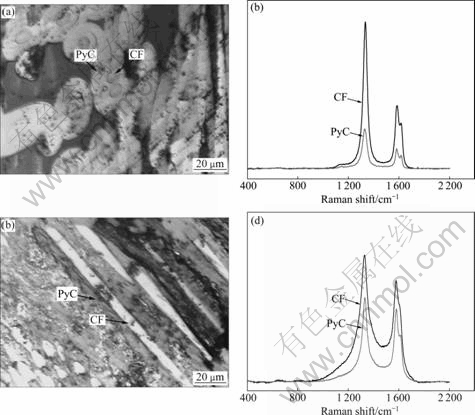
Fig.6 Optical micrographs and Raman spectra of sample C: (a) Optical micrograph of polished section of raw materials; (b) Raman spectra of two different points on raw samples; (c) Optical micrograph of wear surface; (d) Raman spectra of two different points on wear surface
the fiber cloth direction, while wear surfaces are parallel to the fiber cloth direction, because the braking tests were performed with the orientation parallel to the carbon cloth. Fibers of raw material A are surrounded by resin-derived carbons (Fig.4(a)), while fibers of raw materials B and C are surrounded by RL and SL pyrocarbon, respectively (Fig.5(a) and Fig.6(a)). After braking tests, a friction layer forms on the wear surface, and some fibers are chopped off (Fig.4(c), Fig.5(c) and Fig.6(c)).
Raman spectra of different samples show that main peaks of all samples are observed at similar positions: G- band at about 1 580 cm-1, D-band at about 1 330 cm-1 and D′-band, also disorder-induced, clearly at around 1 620 cm-1. FWHM of D-band is calculated as shown in Fig.4(b). By comparing the shape of bands before and after braking tests, all of the three samples have a common feature that both D-band and G-band are broadened after braking tests, which means that lattice defects are brought to the wear surface during braking tests. Furthermore, graphitization takes place on the wear surface to some extent, because the IG/ID values of the wear surface are higher than those of the raw materials.
Decreased FWHM of G- and D-band as well as increased IG/ID indicates the increased degree of graphitization of the investigated carbonaceous materials [22-24]. However, SADEZKY et al [25] indicated FWHM of G- and D-band are not correlated with each other, and they are independent of the signal intensity ratios. Fig.7 gives the FWHM of D-band (vertical axis) and the IG/ID (abscissa) of the test points on different samples. Before braking, FWHM of D-band of carbon fiber and pyrocarbon of sample B are 38 cm-1 and 36 cm-1, respectively, which are lower than those of samples A (38 cm-1 and 53 cm-1) and C (40 cm-1 and 46 cm-1). In other words, there are few lattice defects in
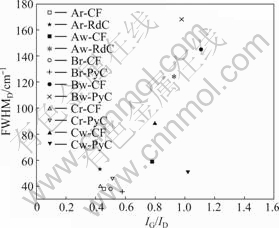
Fig.7 Raman parameters of different samples (Ar: Raw materials of sample A; Aw: Wear surface of sample A; Br: Raw materials of sample B; Bw: Wear surface of sample B; Cr: Raw materials of sample C; Cw: Wear surface of sample C)
the raw material of sample B. Meanwhile, IG/ID of the pyrocarbon in raw material B is 0.579, which is higher than that of samples A (0.427) and C (0.511). This result is consistent with the degree of graphitization from XRD. Effects of fibers in the composites on the XRD patterns could be neglected, since their contributions to the diffraction signal remain always much lower than those of the various pyrocarbon matrices [21]. Therefore, results of pyrocarbon are mainly considered here.
After braking, carbon layers are deformed and a uniform compacted film forms on the wear surface. From Raman spectra, FWHM of D-band and IG/ID of every test point on the wear surface increase compared with the values of corresponding point on the raw materials, which indicates that the lattice structure of materials is destroyed during the formation of the friction layer, and there are more lattice defects on the wear surface. However, the increase of IG/ID means the increase of the graphitization degree, which may be resulted from the high temperature and high pressure during braking tests.
By comparing Raman spectra of the three samples with the different matrices, it can be seen that the FWHM of D- band of sample with RL pyrocarbon changes greatly from 36 cm-1 to 168 cm-1 after braking tests, which means that a large number of lattice defects are produced on the wear surface during braking. This is because sample B with the RL pyrocarbon has high graphitization degree and low hardness, the carbon layers on the friction surface are easy to deform, and the microstructure is destroyed enormously. For sample A, the resin-derived carbon has low graphitization degree, and is easy to be graphitized during braking, so the IG/ID of sample A increases significantly from 0.427 to 0.928. On the contrary, sample C with SL pyrocarbon has high hardness, the carbon layers on the friction surface are difficult to deform, the FWHM of D-band varies from 46 cm-1 to 51 cm-1, and few defects are detected on its wear surface.
4 Conclusions
1) There are a large amount of low energy structure defects in matrix carbon of C/C composites. Raw materials with different carbon matrices show different graphitization degrees. Sample B with RL pyrocarbon has low FWHM of D-band (36 cm-1) and high IG/ID (0.579), which is in good agreement with the XRD results. By comparing Raman parameters of different carbon matrices, spectral analyses indicate that FWHM of D- band is just related to the defects in the in-plane lattice, while IG/ID marks the degree of graphitization.
2) Braking tests under normal loading conditions deform the microstructure during the deformation of the friction layer. Increased FWHM of D-band for three different samples indicates that a large number of lattice defects are brought during braking. However, the rise of the graphitization degree is supported by the increase of IG/ID, which may result from the high temperature and high pressure during braking tests.
3) RL pyrocarbon has high graphitization degree and low hardness, and is easy to deform. The FWHM of D-band of sample B with RL pyrocarbon changes greatly from 36 cm-1 to 168 cm-1 after braking tests, which indicates there are a large number of lattice defects on the wear surface. Sample A with resin-derived carbon has the lower graphitization degree, and is easy to be graphitized during braking, so the IG/ID of sample A increases greatly from 0.427 to 0.928. While sample C with SL pyrocarbon having high hardness is difficult to deform, the FWHM of D band varies from 46 cm-1 to 51 cm-1, and few defects are detected on its wear surface.
References
[1] SAVAGE G. Carbon-carbon composites [M]. London: Chapman and Hall, 1993: 101-105.
[2] WINDHORST T, BLOUNT G. Carbon-carbon composites: A summary of recent developments and applications [J]. Materials & Design, 1997, 18(1): 11-15.
[3] YEN B K. Roles of oxygen in lubrication and wear of graphite in “dusting” and ambient condition [J]. Journal of Materials Science Letters, 1995, 14(21): 1481-1483.
[4] LEE K J, CHENG H Z, CHEN J S. Effect of densification cycles on continuous friction behavior of carbon-carbon composites [J]. Wear, 2006, 260(1/2): 99-108.
[5] RAN Li-ping, YI Mao-zhong, WANG Chao-sheng, YI Zhen-hua, YANG Lin. Wear behavior of C/C-Cu composites under different loads [J]. Journal of Central South University of Technology: Natural Science Edition, 2007, 38(4): 595-601. (in Chinese)
[6] ROUSSEAU B, ESTRADE-SZWARCKOPF H, BONNAMY S, GOULDER M, BERTHIER Y, JACQUEMARD P. Optical and scanning electron microscopies cross-fertilization: Application to worn carbon/carbon composite surface studies [J]. Cabon, 2005, 43(6): 1331-1334.
[7] OZCAN S, FILIP P. Microstructure and wear mechanisms in C/C composites [J]. Wear, 2005, 259(1/6): 642-650.
[8] XIONG Xiang, HUANG Bai-yun, LI Jiang-hong, XU Hui-juan. Friction behaviors of carbon/carbon composites with different pyrolytic carbon textures [J]. Carbon, 2006, 44(3): 463-467.
[9] LEI Bao-ling, YI Mao-zhong, XU Hui-juan. Simulation of temperature field of carbon/carbon composite during braking [J]. The Chinese Journal of Nonferrous Metals, 2008, 18(3): 377-382. (in Chinese)
[10] WANG Xiu-fei, YIN Cai-liu, HUANG Qi-zhong, HE Liang-ming, SU Zhe-an, YANG Xin. Wet friction performance of C/C-SiC composites prepared by new processing route [J]. Journal of Central South University of Technology, 2009, 16(4): 525-529.
[11] DON J, WANG Z. Effects of anti-oxidant migration on friction and wear of C/C AIRCRAFT Brakes [J]. Applied Composite Materials, 2009, 16(2): 73-81.
[12] MURDIE N, JU C P, DON J, FORTUNATO F A. Microstructure of worn pitch/resin/CVI C-C composites [J]. Carbon, 1991, 29(3): 335-342.
[13] LEE K J, LIN JHC, JU C. Microstructure study of PAN-pitch carbon–carbon composite lubricative film [J]. Materials Chemistry and Physics, 2003, 78(3): 760-766.
[14] RIETSCH J C, DENTZER J, DUFOUR A, SCHNELL F, VIDAL L, JACQUEMARD P, GADIOU R, VIX-GUTERL C. Characterizations of C/C composites and wear debris after heavy braking demands [J]. Carbon, 2009, 47(1): 85-93.
[15] BOURRAT X, TROUVAT B. Pyrocarbon anisotropy as measured by electron diffraction and polarized light [J]. Journal of Materials Research, 2000, 15(1): 92-101.
[16] REZNIK B, HUTTINGER K J. On the terminology for pyrolytic carbon [J]. Carbon, 2002, 40(4): 621-624.
[17] TANABE Y, YASUDA E, KIMURA S. Microstructural development of furan resin derived carbon by hot-pressing [C]// 18th Biennial Cnf on Carbon. Worcester, USA, 1987: 241-242.
[18] MARSH H, RODRIGUEZ-REINOSO F. Science of carbon materials [M]. Alicante: Universidad, 2000: 74-79.
[19] FERRARI A C. Raman spectroscopy of graphene and graphite: Disorder, electron-phonon coupling, doping and nonadiabatic effects [J]. Solid State Communications, 2007, 143(1/2): 45-57.
[20] CHAUDHURIA S N, CHAUDHURI R A, BENNERC R E, PENUGONDAC M S. Raman spectroscopy for characterization of interfacial debonds between carbon fibers and polymer matrices [J]. Composite Structures, 2006, 76(4): 375-387.
[21] VALLEROT J M, BOURRAT X, MOUCHON A, CHOLLON G. Quantitative structural and textural assessment of laminar pyrocarbons by Raman spectroscopy, electron diffraction and few other techniques [J]. Carbon, 2006, 44(9): 1833-1844.
[22] ZICKLER GERALD A, SMARSLY B, GIERLINGER N, PETERLIK H, PARIS O. A reconsideration of the relationship between the crystallite size La of carbons determined by X-ray diffraction and Raman spectroscopy [J]. Carbon, 2006, 44(15): 3239-3246.
[23] TUINSTRA F, KOENIG J L. Raman spectrum of graphite [J]. The Journal of Chemical Physics, 1970, 53(3): 1126-1130.
[24] CUESTA A, DHAMELINCOURT P, LAUREYNS J, MARTINEZ- ALONSO A, TASCON J M D. Raman microprobe studies on carbon materials [J]. Carbon, 1994, 32(8): 1523-1532.
[25] SADEZKY A, MUCKENHUBER H, GROTHE H, NIESSNER R, POSCHL U. Raman microspectroscopy of soot and related carbonaceous materials: Spectral analysis and structural information [J]. Carbon, 2006, 43(8): 1731-1742.
(Edited by YANG Bing)
Foundation item: Project(2006CB600906) supported by the National Basic Research Program of China
Received date: 2010-01-12; Accepted date: 2010-04-13
Corresponding author: YI Mao-zhong, Professor, PhD; Tel: +86-731-88830894; E-mail: yimaozhong@126.com