
Effects of sodium tungstate on properties of micro-arc coatings on magnesium alloys
ZHAO Fang(赵 芳)1, LIAO Ai-di(廖爱娣)2, ZHANG Rong-fa(张荣发)1, 2, ZHANG Shu-fang(张淑芳)1, 2,
WANG Hai-xia(王海霞)1, SHI Xing-mei(史兴梅)1, LI Ming-jie(李明杰)1, HE Xiang-ming(何向明)1, 2
1. School of Materials Science and Engineering, Jiangxi Science and Technology Normal University,Nanchang 330013, China;
2. Jiangxi Key Laboratory of Surface Engineering, Jiangxi Science and Technology Normal University,Nanchang 330013, China
Received 23 September 2009; accepted 30 January 2010
Abstract: Anodic coatings were prepared by micro-arc oxidation on AZ91HP magnesium alloys in a base solution containing 10 g/L NaOH and 12 g/L phytic acid with addition of 0-8 g/L sodium tungstate. The effects of sodium tungstate on the coating thickness, mass gain, surface morphology and corrosion resistance were studied by eddy current instrument, electronic scales, scanning electron microscope and immersion tester. With the addition of sodium tungstate, the electrolytic conductivity increases and the final voltage decreases. The sodium tungstate has a minor effect on the coating thickness, but lightens the coating color. With increasing sodium tungstate concentration, the size of micropores on the coatings is enlarged and the corrosion resistance of the anodized samples decreases.
Key words: magnesium alloy; micro-arc oxidation; electrolyte; sodium tungstate
1 Introduction
Micro-arc oxidation (MAO), developed under the traditional oxidation, is an effective method to improve the corrosion and wear resistance of magnesium alloys. The coating properties are mainly determined by the concentrations and compositions of the electrolytes[1]. Due to the health and environmental pressure, some environmentally friend processes have been developed in alkaline solutions containing some inorganic additives such as silicate[1-4], borate[5] and aluminate[5-6]. Among the oxysalts, sodium silicate is a favorable additive of electrolyte[3] and widely used in MAO. Recently, sodium tungstate (Na2WO4) has been used as an electrolyte in MAO on magnesium alloys[4, 7-8]. DING et al[4] systematically studied the effects of sodium tungstate on the microstructure, compositions and mechanical tribological characteristics of the oxide coatings. The results show that with increasing concentration of Na2WO4 in the solution, the microhardness of the oxide coatings increases, while the wear rates decrease. However, the effect of Na2WO4 on the corrosion resistance, one of the important coating properties, is not evaluated.
Phytic acid (C6H18O24P6), first known as the storage form of phosphorus in seeds[9], is a naturally occurring acid and innoxious, biocompatible and green to the environment. A variety of benefits of phytic acid on human health have been reported, including anti-canner agent, inhibitor for renal stone development and antioxidant agent. Phytic acid can also be used in treating metals to prevent rust as a replacement for cyanide[10]. Recently, C6H18O24P6 was used as a main electrolyte in MAO on magnesium alloys[11-12]. The result showed that the corrosion resistance of anodic coatings formed in the C6H18O24P6 solution was better than that in sodium silicate solution[12]. However, to the best of the author’s knowledge, there is no report about the effects of Na2WO4 on coating properties formed in an alkaline solution containing C6H18O24P6.
In this work, the influence of Na2WO4 on coating thickness, surface morphology, mass gain and corrosion resistance were studied with an eddy current instrument, scanning electron microscope, electronic scales and immersion tester.
2 Experimental
An ingot of AZ91HP magnesium alloy was employed and its chemical compositions were as follows (mass fraction, %): Al 8.93, Zn 0.47, Mn 0.22, Si 0.03, Cu 0.002, Ni 0.001, Fe 0.001and Mg balance.
Samples for MAO treatment were cut into 5 cm× 7 cm×1 cm and were anodized after being ground, washed, degreased and dried. The base solution was 10 g/L NaOH and 12 g/L phytic acid. 0-8 g/L Na2WO4 was separately added into the base solution to form different solutions as listed in Table 1.
Table 1 Compositions and concentrations of different anodizing processes

The equipment for MAO consisted of a MAOI-50C power supply, a stainless steel barrel and a stirring and cooling system that controlled the solution temperature below 30 ℃. The treatment was performed by the unipolar (positive) pulse under a constant current control mode. The electrical parameters were fixed as follows: current density of 40 mA/cm2, frequency of 2 000 Hz, duty cycle of 20% and treatment time of 3 min. The solution conductivity was measured by a DDS-307W microprocessor conductivity meter. The coating thickness was measured by a TT230 current instrument, which was calibrated with the same base metal. The morphologies of the treated samples were observed by a scanning electron microscope (SEM QUANTA 200) after being washed, dried and coated with gold. The compositions of anodic films were determined by EDX analysis. The anodized samples were tested under immersion conditions in a 3.5% (mass fraction) NaCl solution for 24 h to evaluate the corrosion performance.
3 Results and discussion
3.1 Final voltage and coating thickness
The solution conductivity, final voltage, coating thickness and color obtained in different processes are listed in Table 2.
With the increase of Na2WO4 concentration, the number of ions in the solution increases and therefore the solution conductivity (k) increases (see Table 2). As the reciprocal of the electrolyte conductivity, the electrolyte
Table 2 MAO parameters, coating thickness and color obtained by different processes
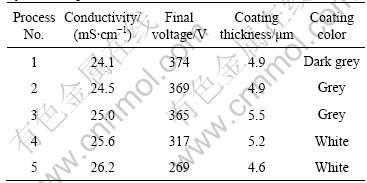
resistivity (ρ) is correlated with the breakdown voltage according to the empirical equation[13]:
UB=aB+bBlg ρ (1)
where aB and bB are the constants for a given metal and electrolyte composition, ρ is electrolyte conductivity.
According to Eq.(1), the breakdown voltage increases with increasing electrolyte resistivity or decreasing solution conductivity. Under the condition of the same electric parameters, with the increase of Na2WO4 concentration, the solution conductivity increases, which results in the decrease of breakdown voltage as well as the final voltage.
In the base solution, the coating thickness is 4.9 μm. After different concentrations of Na2WO4 are added, the coating thickness changes between 4.6 μm and 5.5 μm, which indicates that Na2WO4 has a minor effect on the coating thickness.
The color of the anodized sample obtained in the base solution is dark grey. The samples obtained in the solution with 2 g/L and 6 g/L Na2WO4 are grey and white, respectively, which indicates that Na2WO4 can change the coating color.
3.2 Surface morphology and chemical compositions of anodic coatings
The surface morphologies of the anodic coatings obtained by different processes are shown in Fig.1. It can be seen that, all the coatings, whether obtained with or without Na2WO4 addition, show typically porous structure, but they are slightly different in pore size and uniformity. In Na2WO4-free base solution, the pore size and the distances between two adjacent pores of the coatings are 1.0 μm and 0.6-2.0 μm, respectively (see Fig.1(a)). After adding 2 g/L Na2WO4, the micropores become larger. In addition, the coating surface becomes rougher (see Fig.1(b)). With increasing Na2WO4 concentration, the coatings become rougher and rougher (see Figs.1(c) and 1(d)). The coatings formed in the solution containing 8 g/L Na2WO4 are very irregular (see Fig.1(e)).
The EDX spectra of anodic coatings obtained in the base solution with and without Na2WO4 addition are shown in Fig.2. In Na2WO4-free solution, the anodic coatings contain C, O, Mg, Al and P, indicating the presence of species derived from both the substrate and electrolyte. After adding Na2WO4 (for example 2 g/L Na2WO4), additional W element is found in the coatings (see Fig.2) and it is attributed to Na2WO4 in the solution.
The chemical compositions of anodic coatings formed in the solution with different concentrations of Na2WO4 are listed in Table 3. With increasing Na2WO4, the W content of the coatings increases.
3.3 Mass gain of anodized sample
The mass gain per unit area of each sample treated by different processes is shown in Fig.3.
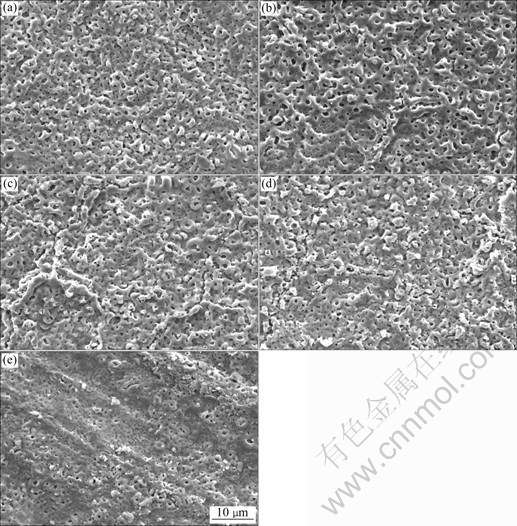
Fig.1 Surface morphologies of anodic coatings obtained by different anodizing processes: (a) No.1; (b) No.2; (c) No.3; (d) No.4; (e) No.5
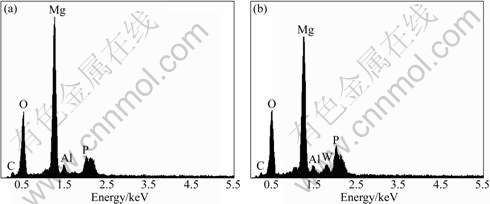
Fig.2 EDX spectra of anodic coatings formed in base solution (a) and with addition of 2 g/L Na2WO4 (b)
Table 3 Chemical compositions of anodic coatings obtained by different processes (mass fraction, %)
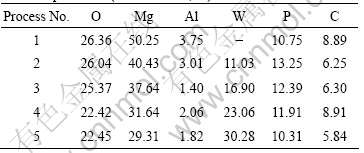
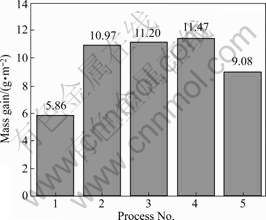
Fig.3 Mass gain of each anodized sample by different processes
In the base solution, the mass gain per unit area of the sample treated by MAO is 5.86 g/m2. After addition of 2 g/L Na2WO4, the value increases evidently and reaches 10.97 g/m2.
In the solution, Na2WO4 took part in the coating formation and entered into the coatings, existing as WO3/Na2WO4 or W element[4]. Because the density of these tungstate-containing compounds is large, the mass gain per area of the coatings increases quickly. With increasing Na2WO4 concentration, on one hand, the sparks on the sample surface become large resulting in the accelerated dissolution speed of anodic coatings in the solution. Meanwhile, the pore size of the anodic coatings become large. The conditions as above result in the decrease of the coating mass. On the other hand, the increase of W content in the coatings causes the increase of the coating mass. Under the conjunct effects, the mass gain of the sample treated in the solution of 8 g/L Na2WO4 is the minimum.
3.4 Corrosion resistance of anodized sample
After being immersed in 3.5% NaCl for 24 h, the samples treated by different processes were taken out from the solution, washed with distilled water, dried by hot wind and observed by the naked eye. The results of the corrosion resistance are listed in Table 4.
According to Table 4, with the increase of Na2WO4 concentration, the corrosion resistance of the anodized samples decreases.
Table 4 Results of immersion experiment for anodized samples by different processes
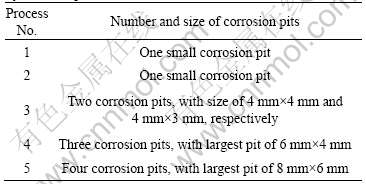
The corrosion resistance of anodic coatings depends on a lot of factors such as the substrate alloy[14], coating composition[15], thickness[16] and porosity[14]. The results showed that anodic coatings with higher chemical stability compounds offered an opportunity to produce layers with better corrosion resistance[15]. In addition, the corrosion resistance of anodized samples improves with the coating thickening under the constant coating porosity[16], but decreases with the increase of coating porosity[14]. In the experiment, after addition of Na2WO4, the tungstate-containing compounds such as WO3/Na2WO4 or W form and they are not stable in water. For example, Na2WO4 is soluble in water, while WO3 can react with OH- ions to produce soluble WO42- according to
WO3+2OH-=WO42-+H2O (2)
Meanwhile, the coating thickness does not increase greatly, but the diameter of micropores on the coatings increases. Therefore, in the corrosive environment, the corrosive medium can easily penetrate the pores and reaches the substrate, which decreases the corrosion resistance of the anodized samples.
4 Conclusions
1) In the base solution containing phytic acid, sodium tungstate can change the coating color but has a minor effect on the coating thickness.
2) Sodium tungstate takes part in coating formation, which results in the increase of the mass gain per area and the microarc pores of anodic coatings.
3) The immersion test shows that sodium tungstate decreases the corrosion resistance of the anodized samples.
References
[1] CAI Q Z, WANG L S, WEI B K, LIU Q X. Electrochemical performance of microarc oxidation films formed on AZ91D magnesium alloy in silicate and phosphate electrolytes [J]. Surface and Coatings Technology, 2006, 200: 3727-3733.
[2] YABUKI A, SAKAI M. Anodic films formed on magnesium in organic, silicate-containing electrolytes [J]. Corrosion Science, 2009, 51: 793-798.
[3] CHAI L Y, YU X, YANG Z H, WANG Y Y, OKIDO M. Anodizing of magnesium alloy AZ31 in alkaline solutions with silicate under continuous sparking [J]. Corrosion Science, 2008, 50: 3274-3279.
[4] DING J, LIANG J, HU L T, HAO J C, XUE Q J. Effects of sodium tungstate on characteristics of microarc oxidation coatings formed on magnesium alloy in silicate-KOH electrolyte [J]. Trans Nonferrous Met Soc China, 2007, 17: 244-249.
[5] BARTON T F, JOHNSON C B. The effect of electrolyte on the anodized finish of a magnesium alloy [J]. Plating and Surface Finishing, 1995, 82: 138-141.
[6] KHASELEV O, WEISS D, YAHALOM J. Structure and composition of anodic films formed on binary Mg-Al alloys in KOH-aluminate solutions under continuous sparking [J]. Corrosion Science, 2001, 43: 1295-1307.
[7] CHEN F, ZHOU H, YAO B, QIN Z, ZHANG Q F. Corrosion resistance property of the ceramic coatings obtained through microarc oxidation on the AZ31 magnesium alloy surfaces [J]. Surface and Coatings Technology, 2007, 201: 4905-4908.
[8] WU C S, ZHANG Z, CAO F H, ZHANG L J, CAO C N. Study on the anodizing of AZ31 magnesium alloys in alkaline borate solutions [J]. Applied Surface Science, 2007, 253: 3893-3898.
[9] RABOY V. Seeds for a better future: “Low phytate” grains help to overcome malnutrition and reduce pollution [J]. Trends in Plant Science, 2001, 6: 458-462.
[10] DOST K, TOKUL O. Determination of phytic acid in wheat and wheat products by reverse phase high performance liquid chromatography [J]. Analytica Chimica Acta, 2006, 558: 22-27.
[11] ZHANG R F, ZHANG S F, DUO S W. Influence of phytic acid concentration on coating properties obtained by MAO treatment on magnesium alloys [J]. Applied Surface Science, 2009, 255: 7893-7897.
[12] ZHANG R.F, XIONG G Y, HU C Y. Comparison of coating properties obtained by MAO on magnesium alloys in silicate and phytic acid electrolytes [J]. Current Applied Physics, 2010, 10: 255-259.
[13] BURGER F J, WU J C. Dielectric breakdown in electrolytic capacitors [J]. Journal of Electrochemistry Society, 1971, 118: 2039-2042.
[14] SHI Z M, SONG G L, ATRENS A. Influence of the β phase on the corrosion performance of anodised coatings on magnesium- aluminium alloys [J]. Corrosion Science, 2005, 47: 2760-2777.
[15] LIANG J, SRINIVASAN P B, BLAWERT C, DIETZEL W. Comparison of electrochemical corrosion behaviour of MgO and ZrO2 coatings on AM50 magnesium alloy formed by plasma electrolytic oxidation [J]. Corrosion Science, 2009, 51: 2483-2492.
[16] ZHANG R F, SHAN D Y, CHEN R S, HAN E H. Effects of electric parameters on properties of anodic coatings formed on magnesium alloys [J]. Materials Chemistry and Physics, 2008, 107: 356-363.
(Edited by LONG Huai-zhong)
Foundation item: Projects(GJJ08363, GJJ09573) supported by the Scientific Research Fund of Jiangxi Provincial Education Department, China
Corresponding author: ZHANG Rong-fa; Tel: +86-791-3831266; E-mail: rfzhang-10@163.com