Article ID: 1003-6326(2005)06-1290-07
Tribological behavior of high specific strength
PTFE-Al alloy composite
XIANG Ding-han(向定汉)1, PAN Qing-lin(潘青林)2
(1. College of Materials Science and Technology,
Nanjing University of Aeronautics and Astronautics, Nanjing 210016, China;
2. School of Materials Science and Engineering, Central South University,
Changsha 410083, China)
Abstract: Solid lubricants lead to substantial weight savings relative to the use of liquid lubricant, especially in the weight-conscious aerospace industry. A new PTFE-Al alloy composite(A) containing 60% area proportion of PTFE composite was developed. Another type of common metal-plastics multilayer composite, also called DU, was selected for a comparative investigation. Friction and wear tests were carried out in an oscillating sliding tribotester in air at an oscillating frequency of 0.13Hz and contact mean pressures from 10 to 80MPa. The composites slid against a 38CrMoAlA steel shaft. The results show that the composite A exhibits low coefficient of dry sliding friction less than 0.1 and long wear life of 2000m. This is because the composite A can provide a sufficient solid lubrication during the whole tests. SEM examination of the transfer films for the composite A confirms that uniform, thin and coherent transfer films are prerequisites for low friction and good wear resistance.
Key words: composite; friction, wear; solid lubricant; polytetrafluoroethylene(PTFE); Al alloy; high load CLC
number: TB333 Document code: A
1 INTRODUCTION
Composite materials, one of the most rapidly growing classes of materials, are being used increasingly for such tribological applications. Under high vacuums, high temperatures, cryogenic temperatures, radiation, space or corrosive environments, solid lubricant may be the only feasible system. Especially, in the weight-conscious aerospace industry, solid lubricants lead to the substantial mass savings relative to the use of liquid lubricants[1]. For example, there were more than 1000 solid-lubricating machine elements in the Apollo Spacecraft.
A solid lubricant is defined as a material that provides lubrication, under essentially dry conditions, to two surfaces moving relatively to each other. Polytetrafluoroethylene(PTFE) is a commonly used self-lubricating material, which exhibits very low coefficient of friction and poor wear resistance. In order to enhance the wear resistance of PTFE, PTFE composites filled with the micro/nano inorganic particles have been extensively studied[2-5]. Khedkar et al[4] filled PTFE with 20%(mass fraction) glass fiber+5%MoS2. The wear resistance was improved by nearly two orders of magnitudes. Sawyer et al[5] also filled PTFE with alumina nanoparticles. At filler concentrations of 20%, the wear resistance was greatly increased by 600 times. Other polymers filled with inorganic particulates have been widely investigated in terms of their tribological behavior. Bahadur et al[6-11] reported that the fillers such as CuS, CuF2, CaS and CaO reduced the wear rate of polyamide. Unfortunately, polymer composites still exhibit low load-carrying capacity less than 10MPa. So far, the most effective approach to enhance load-carrying capacity of polymer composites is to combine the excellent dry sliding behavior of PTFE with the mechanical strength of conventional metallic bearings[2]. The development of PTFE composite dry bearing material(DU) was first begun by the Glacier Metal Company Ltd. Today, DU is one of the most common composite bearing materials. Solid lubricant embedded bushing is another of the heavily loaded self-lubricating bearings, which consists of bronze or brass with solid lubricant plugs embedded in the surface. However, the two self-lubricating heavily loaded composite bearings have been reluctantly used as the weight-conscious aerospace industry due to a low specific strength (strength to density).
The key to making strong but light self-lubricating materials is to find an appropriate metal as the backing of polymer composites. Aluminum alloys containing minor scandium(Sc) are of high specific strength, high ductility and good corrosion resistance, which are mainly applied in aerospace, nuclear energy and ships industry[12-14]. Therefore, if an aluminum alloy containing minor scandium Sc is selected as a backing material, a new self-lubricating Al alloy-PTFE composite is expected to be effectively strengthened without increasing its mass.
Based on the above observations and in our effort to develop a new self-lubricating metal-PTFE composite with high strength and light mass, it was decided to use a PTFE-20%(mass fraction) alumina composite as a solid lubricant and a high strength Al alloy containing minor Sc as the backing.
2 EXPERIMENTAL
2.1 Preparation of test specimens
In the present study, two self-lubricating composites such as a PTFE-Al alloy composite(A) and a metal-PTFE multilayer composite(DU) were prepared. For composite A, the thickness of the specimen was 5.0mm, which contained 60% area proportion of PTFE composite. DU, in agreement with commonly used dry bearings in aerospace, was chosen to carry out a comparative investigation. The two composites are shown schematically in Fig.1.
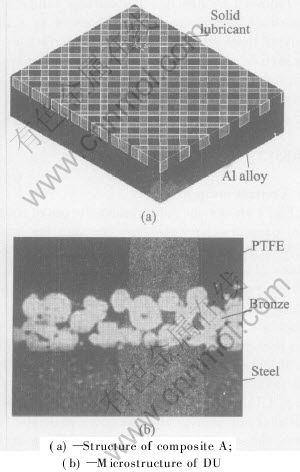
Fig.1 Schematic diagrams of two composites
The composite A consists of PTFE composite and Al alloy containing minor Sc with chemical composition of Al-6.2Zn-2.0Mg-0.3Mn-0.25(Sc+Zr). Al-Zn-Mg alloys are heat-treatable strengthening alloys, cold-rolled plates need solid solution and aging treatment. After 465℃/40min solution treatment, water quenching and 120℃/24h aging, samples were tested on Instron 8032 tensile testing machine and the tensile ratio was 2mm/min. The mechanical properties of Al alloy containing minor Sc are shown in Table 1.
Table 1 Mechanical properties of Al alloy containing minor Sc at room temperature
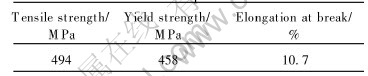
Sawyer et al[5] found that the steady state wear rate of the PTFE composite filled with 20% alumina nanoparticles was reduced by a factor of about 600 as compared to that of unfilled PTFE. In our study, the PTFE-20% alumina composite was selected as the composition of a solid lubricant. The PTFE powders with a grit size of about 50μm and alumina nanoparticles of 80nm were prepared. The PTFE powders and alumina nanoparticles were fully mixed ultrasonically, PTFE composite was compression molded using PTFE+20% alumina nanoparticles, in which the mixture was heated at a rate of 10℃/min to 380℃, held for 2h, then cooled to room temperature with the sintering apparatus.
2.2 Compression testing
In this work, the contact pair between cylindrical bearings of two composites and a steel shaft was a cylindrical surface contact. Therefore, a parameter was now introduced such that the contact mean pressure was defined as the normal load per unit projected area on a steel shaft.
Measuring contact mean pressure of two composites was performed as GB7314-87 Materials-Compression Testing Standards. The specimen of the composite was 55.0mm in inner diameter and 65.0mm in outer diameter, 50.0mm in width and 5.0mm in thickness. The cylindrical surface of steel shaft was 55mm in diameter. The schematic representation of the part related to loading of the apparatus is shown in Fig.2.
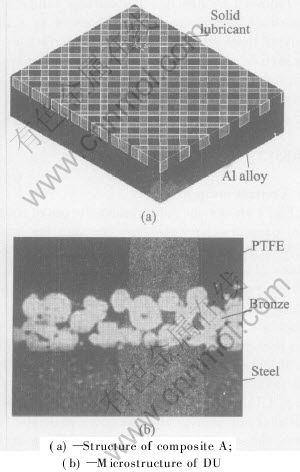
Fig.2 Schematic representation of part related to loading of apparatus
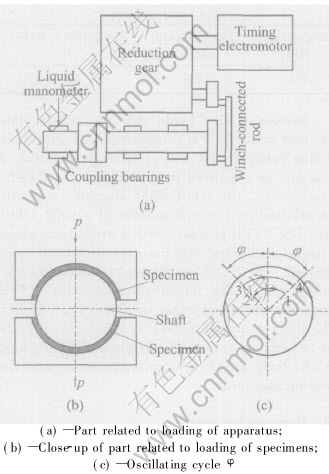
Fig.3 Schematic diagram of oscillating tribometer
2.3 Sliding friction testing
Sliding friction tests were carried out in laboratory air using a computer controlled oscillating tribometer. Fig.3 is the schematic representation of the part related to loading of the apparatus. The coefficient of friction was measured with the aid of two linear variable strain gauges and was recorded automatically throughout the tests connected to a PC.
A 38CrMoAlA alloy steel (C 0.35%-0.42%, Mn 0.3%-0.6%, Si 0.20%-0.40%, Cr 1.35%-1.65%, Al 0.70%-1.10%, Mo 0.15%-0.25%) bar, 55mm in diameter, was used as a shaft material. The shaft was treated by plasma nitriding. The contact pair between a shaft and specimens is shown in Fig.3(b). The surface roughness of the shaft surface was 0.1μm. The specimens of the two composites were 55mm in inner diameter, 65mm in outer diameter. The surface roughness of the specimens was 0.1μm.
Sliding friction tests were carried out at room temperature in ambient atmosphere ((55±5)% RH) under dry friction conditions, with an oscillating frequency of 0.13Hz in agreement with the actual operating conditions and contact mean pressures from 10 to 80MPa. The oscillating cycle φ was ±30° as shown in Fig.3(c). Then the surfaces of specimens and a 38CrMoAlA steel shaft were cleaned with acetone followed by drying. At the end each test, the specimens and a 38CrMoAlA steel shaft were cleaned with acetone followed by drying. At the start of sliding, during the so-called running-in period, the two composites exhibited a high coefficient of friction, followed by steady-state sliding motion until coefficient of friction remained constant. In our work, the coefficient of friction was reported during steady-state sliding period. Two replicate friction tests were performed in order to enhance accuracy of data, and the average of two replicate test results was reported. The variation in the data of the replicate friction test was within 10% of the average value.
2.4 Wear testing
Sliding wear tests were performed at room temperature in ambient atmosphere ((55±5)% RH), with an oscillating frequency of 0.13Hz, and a contact mean pressure of 80MPa, and an oscillating cycle φ of ±30°. Then the specimens and a 38CrMoAlA steel shaft were cleaned with acetone followed by drying. The surface temperature of specimen during tests was measured by a thermocouple inserted in a hole 0.8mm below the rubbing surface of specimen. The wear tests were interrupted at the intervals of 3.5h, 0.5h, and thereafter 4h for wear depth measurements of the wear to an accuracy of 0.5μm.
3 RESULTS AND DISCUSSION
3.1 Contact mean pressure
Fig.4 shows the compressive curves of contact mean pressure between two composites and a 38CrMoAlA steel shaft. It can be seen that the inflexions of compressive curves, labeled as M and N, were regarded as yield points, as well as were maximum values of contact mean pressures for the composites A and DU. The maximum contact mean pressure of composite A was 164MPa, while that of DU was 182MPa. The composite A exhibited a maximum contact mean pressure lower than that of DU. Because the DU was a metal-plastics multilayer composite, the thickness of plastics layer was about 0.1mm, the metal backing carried the external loads. However, the composite A containing 60% area proportion of plastics was only of 40% area proportion of Al alloy, leading to a low maximum contact mean pressure.
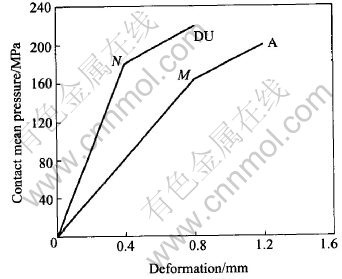
Fig.4 Compressive curve of contact mean pressures for two composites
Pure PTFE commonly exhibits very low friction and excellent corrosion resistance, but poor wear resistance. The PTFE-20% alumina composite exhibits very high wear resistance due to the presence of alumina nanoparticles. In general, the inorganic particle has a high compression strength, which can be used to enhance the mechanical strength of polymer composites, leading to improving wear resistance[2-11]. It should be emphasized that the improvement of the maximum contact mean pressure for two metal-PTFE composites is attributed to their metals backing. Metals such as high strength of Al alloys and plain carbon steels exhibit high strength and good thermal conductivity as compared to engineering plastics. Developing a novel composite A aims to combine high strength Al alloy with low friction of plastics, that is, to remain low friction of plastics and enhance mechanical strength.
3.2 Friction testing
Fig.5 shows the variation of the coefficient of friction of the composites A and DU with contact mean pressure. It can be observed that the steady-state coefficient of friction(μ) of the composite A varied in the range of 0.07-0.13, the coefficient of friction decreased with contact mean pressure increasing, then remained almost constant. Under the same loads conditions, the steady state coefficient of friction for DU varied in the range of 0.07-0.13. In the present case also similar trend was observed. It was also reported that the decreasing in coefficient of friction with loads(see Fig.5) was in agreement with our earlier studies[15,16].
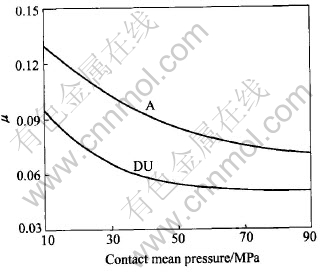
Fig.5 Variation of coefficient of friction with contact mean pressure for two composites
Fig.5 shows that composite A exhibits a coefficient of friction higher than that of DU. It is also a well-accepted fact that a thin transfer film is one of the prerequisites for low friction. Fig.6 shows a photograph of the worn surface of the specimen for composite A at a heavy contact pressure of 80MPa after 2000m. There existed some extrusions of solid lubricants in the both sides of the Al alloy backing, although the transfer films of contact surfaces were uniform, 40% area proportion of Al alloy contacted with a steel shaft, thus leading to a high coefficient of friction. For DU, the repeated sliding action on the contact surface would thus be able to form more uniform and coherent the transfer films, resulting in a low coefficient of friction.
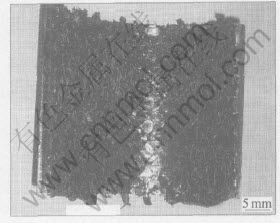
Fig.6 Optical micrograph of transfer films for composite A
3.3 Wear testing
The wear test results are shown in Fig.7. From the wear depth vs sliding distance plots, it was observed that when the wear depth was only 80μm under oscillating movement conditions at an contact mean pressure of 80MPa, composite A exhibited a long sliding distance of 2000m, while the DU only 800m.
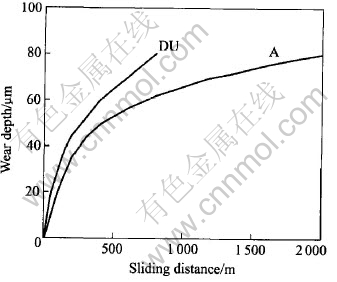
Fig.7 Variation of wear depth with sliding distance for two composites
DU, a metal-PTFE multilayer composite, is one of the most common composite bearing materials today. Generally, DU can withstand a maximum static normal pressure of 140MPa, but the steady normal pressure of 80MPa is applied, the term life of DU is about 800m (10000 cycles) under dry oscillating movement conditions. It can be seen that composite A exhibits a longer wear life than DU. For the DU, the thickness of PTFE composite was less than 0.1mm. While for the composite A, the thickness for metal-PTFE bilayer was 2mm, which provided a relatively sufficient lubrication leading to low wear loss. Besides, the composite A exhibited good wear resistance due to an Al alloy with excellent thermal conductivity helpful in dissipating frictional heating rapidly under the repeated oscillating action.
3.4 Effect of minor Sc on mechanical properties of Al alloy
As indicated in the preceding, the backing of Al alloy containing Sc with high strength and high toughness played a central role in determining a mechanical strength of composite A. In order to further understand the high wear resistance of composite A, we analyzed the microstructures of the Al alloy containing Sc as the backing by using an optical microscope and a TEM. Figs.8(a) and (b) give the microstructures of as-cast grains of Al alloy with or without minor Sc. It can be observed that the addition of minor Sc could obviously fine as-cast grains of Al alloy, while the microstructure of Al alloy without Sc was nonuniform. It is suggested that strengthening mainly comes from fine-grain strengthening. This is in agreement with the results of Yin et al[12, 13].
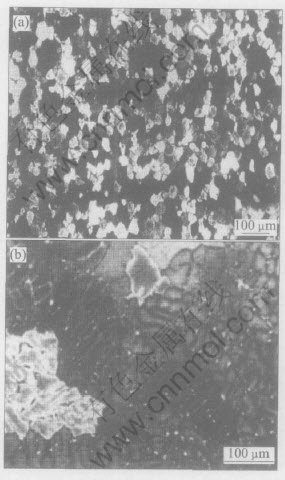
Fig.8 Microstructures of as-cast grains of Al alloy with(a) or without(b) minor Sc
One key factor that Sc affects the strength of Al alloy is that minor Sc dissolves in supersaturated solid solution α(Al). During homogenization treatment, the supersaturated solid solution decomposes under thermal activation, and many secondary aluminides containing Sc, Al3(Sc, Zr) precipitate. Fig.9 indicates the pattern, size and distribution of Al3(Sc, Zr) particles.
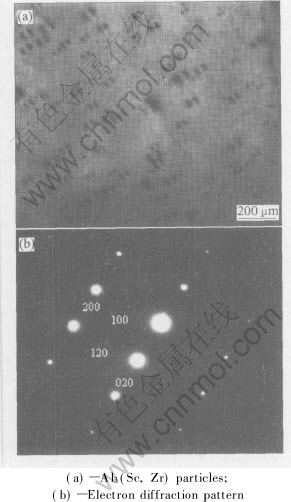
Fig.9 TEM microstructures of Al alloy containing minor Sc
PAN et al[13, 14] also reported that the secondary Al3(Sc, Zr) had strongly pinned dislocations and sub-boundaries, which could produce precipitation strengthening and effectively restrains recrystallization. It could be suggested that minor Sc in Al alloy resulted in refine-grain strengthening and precipitation strengthening, resulting in high strength and high toughness of the Al alloy. Thus, the improvement of wear resistance of PTFE-Al alloy composite was attributed to an increase in mechanical strengths of the Al alloy backing.
3.5 SEM analysis of worn surfaces
To understand the wear mechanism of composite A, we employed the scanning electron microscopy(SEM) to observe the worn surfaces. Fig.10 shows SEM micrographs of the worn surface for specimen of the composite at a contact mean pressure of 80MPa after 2000m. Fig.10(a) gives SEM micrograph of interface between the PTFE composite and the Al alloy backing. Interestingly, it could be observed that PTFE composite was higher than Al alloy backing. This was because the modulus of elasticity of PTFE composite was much lower than that of Al alloy, and PTFE composite could be subjected to a big amount of elastic deformation under similar loading conditions. It could be obviously observed that the transfer films of surface of Al alloy backing were still uniform, composite A remained a sufficient lubrication, and if the wear depth was allowed beyond the range of 80 μm, wear tests could be carried out. This was a main cause that composite A was of sliding wear life longer than that of the commonly used DU bearings.
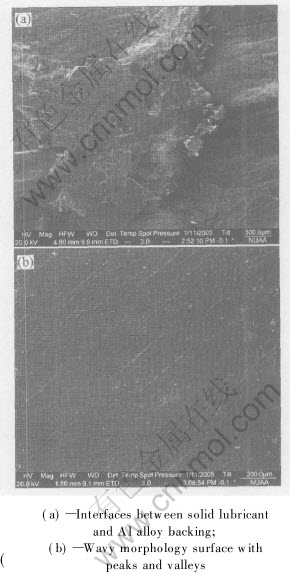
Fig.10 Worn surfaces of PTFE-AL alloy composite
Fig.10(b) shows the wavy morphology surface with peaks and valleys of the composite. It may be suggested that there existed abrasive wear mechanism under severe operating conditions. We also observed that there were some thin, uniform and coherent transfer films on counterface of the steel shaft, and the transfer films played an important role in reduction of friction and wear loss under the repeated oscillating sliding action. It was indicated that the dominant mechanism was still adhesive wear.
4 CONCLUSIONS
1) For composite A, the great improvement in a maximum contact mean pressure resulted from the Al alloy backing containing minor Sc, thus leading to a considerable increase in wear resistance.
2) The Al alloy containing minor Sc exhibited high strength, good ductility and toughness, especially excellent thermal conductivity helpful in dissipating frictional heating.
3) The newly developed composite A was of a low coefficient of friction and high wear resistance. This was because its area proportion of solid lubricant was up to 60%, which could provide a sufficient lubrication during the whole tests.
4) For composite A, SEM examination of the transfer film indicated that the uniform, thin and coherent transfer films were prerequisites for low friction and good wear resistance.
5) The analysis of worn surfaces for composite A confirmed that the adhesive wear was dominant, and abrasive wear occurred simultaneously under heavy loading and repetitive oscillating action conditions.
REFERENCES
[1]Miyashi K. Solid Lubrication Fundamentals and Applications [M]. New York: Marcal Dekker, Inc, 2001. 5.
[2]XIANG Ding-han, YAO Zheng-jun, WEN Jian-ping. Experimental investigation on dry frictional behavior of the two self-lubricating composites under heavy loading conditions [J]. Materials Letters, 2005, 59(18): 2352-2356.
[3]Wang Q H, Xue Q J, Liu W M, et al. The friction and wear characteristics of nanometer SiC and polytetrafluoroethylene filled polyetheretherketone [J]. Wear, 2000, 243(1-2): 140-146.
[4]Khekar J, Negulescu I, Meletis E I. Sliding wear behavior of PTFE composites [J]. Wear, 2002, 252(5-6): 361-369.
[5]Sawyer W G, Freudenberg K D, Bhimaraj P, et al. A study on the friction and wear behavior of PTFE filled with alumina nanoparticles [J]. Wear, 2003, 254(5-6): 573-580.
[6]Palabiyik M, Bahadur S. Tribological studies of polyamide 6 and high-density polyethylene blends filled with PTFE and copper oxide and reinforced with short glass fibers [J]. Wear, 2002, 253(3-4): 369-376.
[7]Cho M H, Bahadur S. Study of tribological synergistic effects in nano CuO-filled and fiber-reinforced polyphenylene sulfide composites [J]. Wear, 2005, 258(5-6): 835-845.
[8]Bahadur S, Gong D. Investigation of the influence of CaS, CaO, and CaF2 fillers on the transfer and wear of nylon by microscopy and XPS analysis [J]. Wear, 1996, 197:271-279.
[9]Kurokawa M, Uchiyama Y. Tribological properties and gear performance of polyoxymethylene composites [J]. ASME Trans J Tribo, 2003, 125(3): 661-669.
[10]Yamamoto Y J, Takashima T. Friction and wear of water lubricated PEEK and PPS sliding contacts [J]. Wear, 2002, 253(7-8): 820-826.
[11]Unal H, Sen U, Mimaroglu A. Dry sliding wear characteristics of some industrial polymers against steel counterface [J]. Tribo Int, 2004, 37(9): 727-737.
[12]PAN Qing-lin. Study of Microstructures and Mechanical Properties of Al-Mg-Sc and Al-Zn-Mg-Sc Alloys [D]. Changsha: Central South University of Technology, 2000.(in Chinese)
[13]YIN Zhi-min, JIANG Feng, PAN Qing-lin, et al. Microstructures and mechanical properties of Al-Mg and Al-Zn-Mg based alloys containing minor scandium and zirconium [J]. Trans Nonferrous Met Soc China, 2003, 13(3): 515-520.
[14]YIN Zhi-min, YANG Lei, PAN Qing-lin, et al. Effect of minor Sc and Zr on microstructures and mechanical properties of Al-Zn-Mg based alloys [J]. Trans Nonferrous Met Soc China, 2001, 11(6): 821-825.
[15]XIANG Ding-han, SHAN Kun-lun. Friction and wear behavior of self-lubricating and heavily loaded metal-PTFE composites [J]. Wear, 2005.(in press)
[16]XIANG Ding-han, PAN Qing-lin. Structural optimization and properties of brass-plastics self-lubricating composites [J]. The Chinese Journal of Nonferrous Metals, 2004, 14(6): 896-900.(in Chinese)
(Edited by YUAN Sai-qian)
Foundation item: Project(04G52044) supported by the Aeronautics Science Foundation of China
Received date: 2005-06-14; Accepted date: 2005-09-21
Correspondence: XIANG Ding-han, Professor, PhD; Tel: +86-25-84892952; E-mail: xiangdh@nuaa.edu.cn