J. Cent. South Univ. (2013) 20: 372–377
DOI: 10.1007/s11771-013-1497-8

Design of a novel 50 kW fast charger for electric vehicles
Yoon Hyok-min1, Kim Jong-hyun2, Song Eui-ho1
1. School of Mechatronics, Changwon National University, Changwon 641–773, Korea;
2. KERI, 28-1, Sungju-dong, Changwon 642–120, Korea
Central South University Press and Springer-Verlag Berlin Heidelberg 2013
Abstract: a novel 50 kW fast charger was proposed for electric vehicles. The proposed fast charger is divided into two main sections: an AC-DC converter performing a PFC function and a DC-DC converter performing a charging function. A transformer including leakage inductances was used in the AC-DC converter in order to obtain isolation and inductance. A series-connection topology was used in the DC-DC converter between the DC-bus and outlet. This topology enables high power conversion efficiency up to 95% for the DC-DC converter. In order to reduce the impact of the 50 kW charging on the AC grid, the proposed fast charger system includes a buffering battery unit between the two main power conversion units. This leads to reductions in the power installation costs of power companies and to improvements in the power quality on the AC grid. The performances of the proposed fast charger system were verified through simulations and experimental results.
Key words: fast electric vehicle charger; charging; infrastructure; buffering battery
1 Introduction
Recently, the automotive industry faced a critical turning point with the environmental concerns surrounding and caused by internal combustion engine vehicles (ICEVs). Electric vehicles (EVs) are becoming attractive alternatives to ICEVs as a result of their environmental advantages and the increasing price of oil. Therefore, the development and commercialization of a charging infrastructure for EVs, including electric bicycles, has become a focus in developed countries [1–3].
The charging infrastructure is composed of an operating system, customer information system and charging system. Among these systems, the charging system is the most important and fundamental element in the charging infrastructure. The charging system can be classified as either a slow charger or a fast charger depending on the charging time and charging method. The slow charger usually supplies approximately 3–4 kW of power to the EV and its charging time requires approximately 6–7 h. For this reason, the slow charger is appropriate for nighttime charging using a household AC utility. However, the fast charger supplies approximately 50 kW of power to the EV through the charging station, and the charging time requires less than 0.5 h [4–7].
In particular, the fast charger (called a Level III or off-board charger) can be installed in public places. It can be compared to a gas station for ICEVs. The development and validation of the fast charger has been conducted in many developed countries in Western Europe, the United States and Japan [8]. However, as the charging station becomes larger, it can cause negative influences on the power quality in the electricity distribution system. These negative influences often appear as voltage distortions and current harmonics; poor power quality including a low power factor has already been a problem in many countries [9–10]. A power factor correction (PFC) technology can be considered in order to resolve these problems; however, the impacts on the AC grid at peak charging power will remain [11–12].
In this work, a novel 50 kW fast charger system is described. The charger system improves the power factor in the AC grid and leads to a high power conversion efficiency. It is capable of charging a lithium-ion battery in an EV within a voltage range of 300–500 V by supplying a current of 0–125 A.
When the maximum power of 50 kW is supplied to the EV battery, the charging system can generate a voltage drop and distortions in the AC grid during the maximum charging current supplying interval. Through the introduction of the buffering battery (BB) unit in the DC-bus, these negative effects can be reduced. Furthermore, it can enable reductions in the power utility installation costs incurred by the electric company.
2 System configurations
The topology of the power converter must comply with several fundamental requirements in order to enable safe, secure, fast and efficient charging. Also, during the converter design process, special attention must be paid to the system optimization in order to meet the product requirement specifications in terms of efficiency, cost, size, volume, and weight. All components from the semiconductors to the heat-sinks including the passive filter components must be designed in order to develop an optimized system [5, 13–14].
A block diagram of the 50 kW fast charger is shown in Fig. 1. The main power conversion section consists of a PFC unit and a DC-DC converter. The buffering battery (BB) unit is located between the main power conversion units.
2.1 Power factor correction (PFC) unit
The scheme of the PFC unit is shown in Fig. 2. The PFC unit consists of a transformer connected Y-Δ and a three-phase PFC converter based on insulated gate bipolar transistors (IGBTs). The transformer performs
galvanic isolation between the AC utility and the fast charger system. Furthermore, it includes the internal leakage inductances that are used for the power factor correction operation. The PFC converter charges the buffering battery unit connected to the DC-bus and improves the power factor in the AC inlet.
2.2 Buffering battery (BB) unit
The fast charger does not need to continuously supply the maximum 50 kW power to the EV because the charging can be divided into three time periods: a full-rated power charging time period, an under-rated power charging time period, and a stand-by time period. Thus the average power supplied by the fast charger is lower than the maximum of 50 kW. Using the buffering battery unit between the PFC unit and the DC-DC converter, the maximum power can be supplied to the EV during the full-rated power charging time period. By considering the charging times, the PFC unit can be designed to have a small power rating as low as 20 kW. Since the PFC unit supplies power continuously to the buffering battery unit with a 20 kW power rating, the burden of the power utility on the inlet of the fast charger system can be reduced compared with a charger system without the buffering battery unit. The buffering battery unit consists of sixty-four lithium-ion cells and its voltage is normally 237 V.
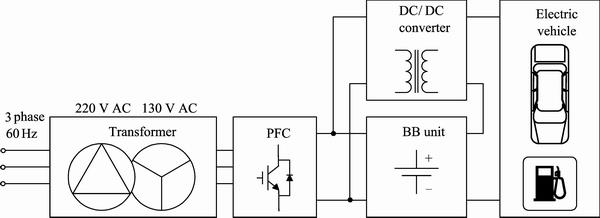
Fig. 1 Block diagram of proposed 50 kW fast charger
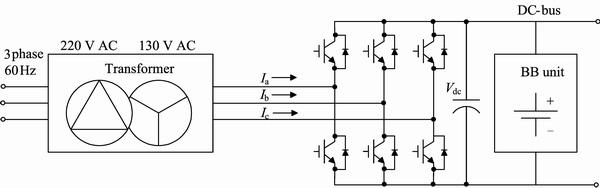
Fig. 2 Scheme of 20 kW PFC unit
2.3 DC-DC converter
The DC-DC converter is composed of a phase-shift full-bridge converter, three transformers, and three output filters. The phase-shift control is applied to reduce the switching loss in the DC-DC power conversion. In order to prevent the saturation of magnetic material, a capacitor (Cr) is used in each transformer primary side in order to equalize the flux displacement on the B–H curve.
The conventional and proposed DC–DC converters with a series-connection topology are shown in Fig. 3. The only difference between the system configurations is the additional connection in the proposed DC–DC converter. As shown in Fig. 3, the topology is simple and able to be implemented easily due to only having one additional connection. Therefore, the output voltage of the EV charger unit consists of the sum of the DC-bus voltage and the output voltage of the phase-shift full-bridge converter. This converter structure leads to efficiency increase of the fast EV charger.
The proposed DC-DC converter has a direct power transfer path and its effects are as follows: the nominal buffering battery voltage is 230 V, EV battery voltage is400 V, maximum charging current is 125 A, transferred power by direct line is and 28.75 kW, and transferred
power by DC-DC converter is 21.25 kW.
This demonstrates that approximately 60% of the maximum power rating does not need to be converted. The conventional system converts all charging power; however, the proposed system only converts 40% of the charging power. Thus, the proposed converter leads to improvements in the conversion efficiency [15].
2.4 Controller design
Lithium-ion battery charging is characterized by two main phases: constant current (CC) and constant voltage (CV), as shown in Fig. 4.
For fast and safe charging operations, the battery voltage and charging current for the EV are continuously monitored through on-board and off-board battery management systems (BMSs).
Considering the characteristics of the lithium-ion battery, the EV requires the maximum constant current mode until a specific voltage is reached. In the following mode, the EV requires a gradually reduced current.
Generally, the EV generates the stop command at 85% of the full battery capacity. In order to satisfy this requirement, the controller of the DC-DC converter uses a dual mode control strategy with a constant current
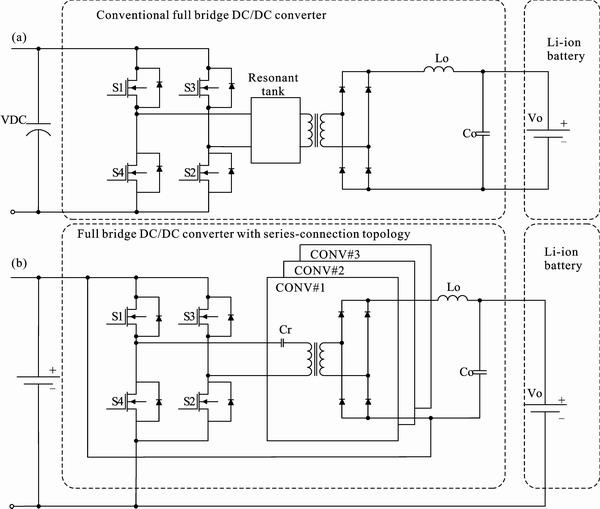
Fig. 3 Scheme of conventional DC-DC converter (a) and proposed DC-DC converter with series-connection (b)
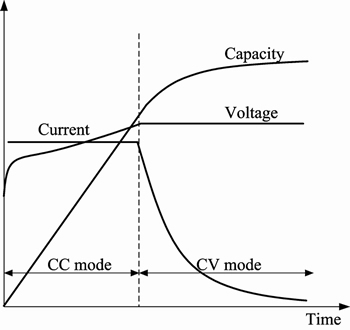
Fig. 4 Lithium-ion battery charging modes
mode and constant voltage mode. The block diagram of the controller for the EV battery is shown in Fig. 5.
3 Simulation results
Using the PSIM, the simulations for the DC-DC converter were performed using a DC-bus voltage of 230 V and a charging current of 125 A. The simulation circuit is shown in Fig. 6.
The waveforms of the IGBT output voltage, current and inductor current are shown in Figs. 7–9. The IGBT output voltage waveform implies that the full-bridge DC-DC converter operates in a phase-shift mode. The applied switching frequency was 15 kHz with a dead time of 4 ms.
4 Experimental results
The experimental waveforms of the IGBT output

Fig. 5 Block diagram of controller for EV battery
voltage and current for the phase-shift converter are shown in Figs. 10 and 11 under full load conditions. The IGBT modules as main switches were in the 600 V/400 A class. The bridge diode rectified voltage is shown in Fig. 12 with the IGBT output voltage. This system uses three 1 200 V/100 A bridge diode modules. Figures 13 and 14 show the voltage and current waveforms under half load conditions. In order to verify the control algorithm and hardware circuit performance of the charger, the proposed fast charger was designed and implemented. A photograph of the experimental setup of the fast charger is shown in Fig. 15.
The battery charging controller was implemented in software using a digital signal processor (TMS320F28335, Texas Instruments, USA).
The output voltage and current signals were measured using a 12-bit A/D converter in the digital signal processor (DSP). By setting period and phase angle register in the DSP, the generation of the PWM signals was simple in the DC-DC power conversion.
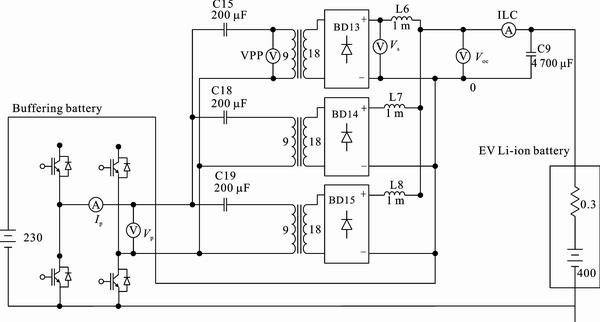
Fig. 6 Simulation circuit
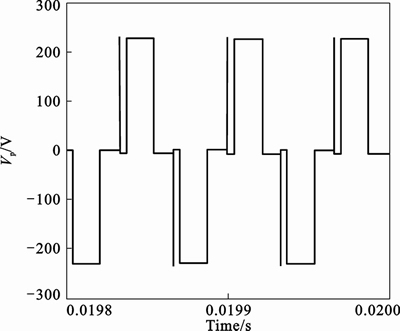
Fig. 7 IGBT output voltage (Vp) in proposed DC-DC converter
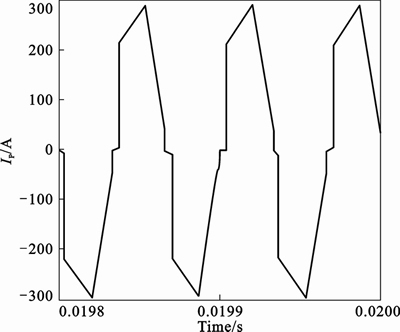
Fig. 8 IGBT output current (Ip) in proposed DC-DC converter
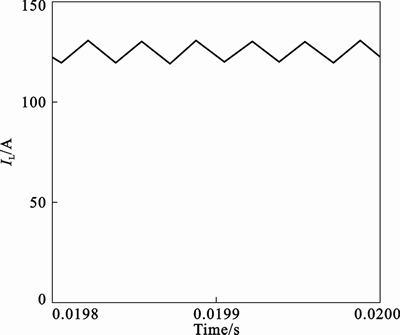
Fig. 9 Inductor current IL in proposed DC-DC converter
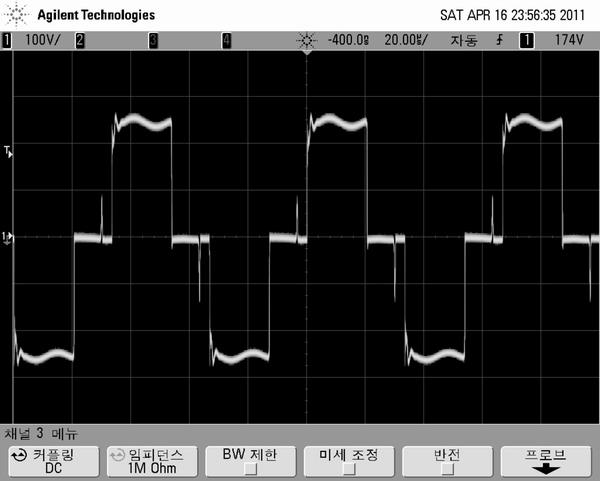
Fig. 10 Experimental waveforms of IGBT output voltage under full load conditions (Vp=100 V/div)
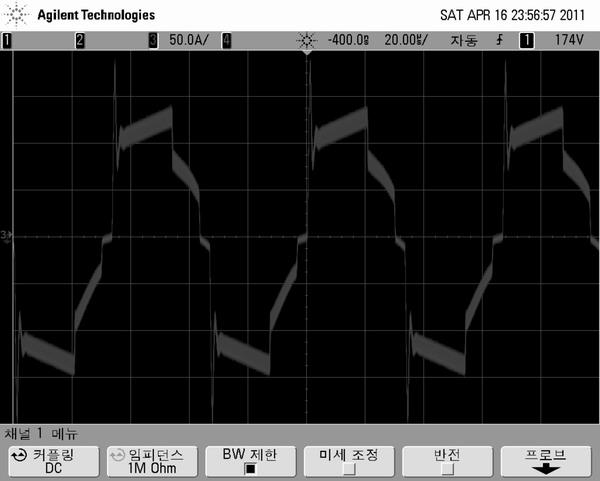
Fig. 11 Experimental waveforms of IGBT output current under full load conditions (Ip =50A/div)
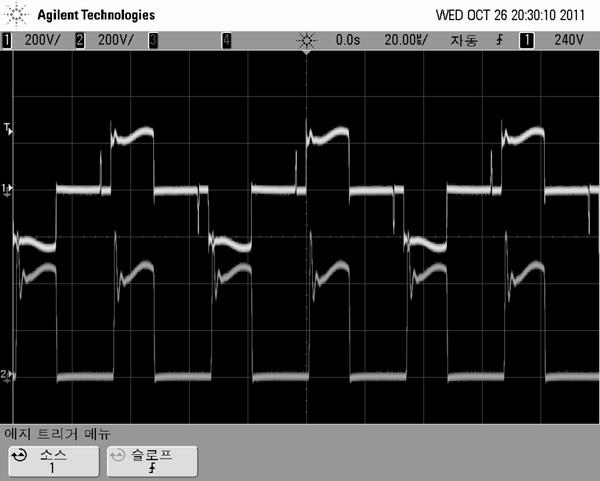
Fig. 12 Experimental waveforms of IGBT output voltage and diode rectified voltage under full load conditions (Vs=200 V/div)

Fig. 13 Experimental waveforms of IGBT output voltage under half load conditions (Vp=100 V/div)
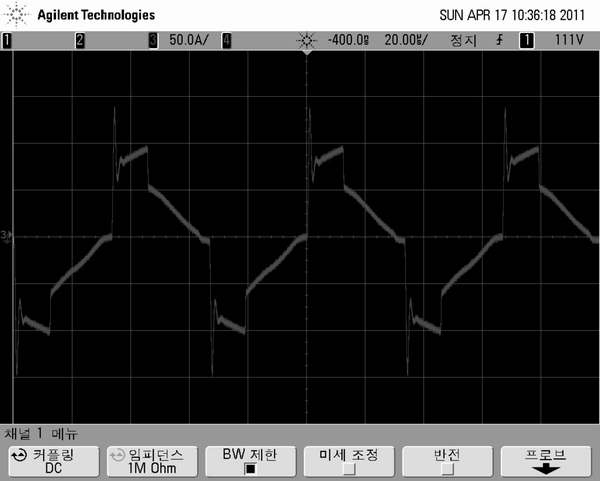
Fig. 14 Experimental waveforms of IGBT output current under half load conditions (Ip=50 A/div)
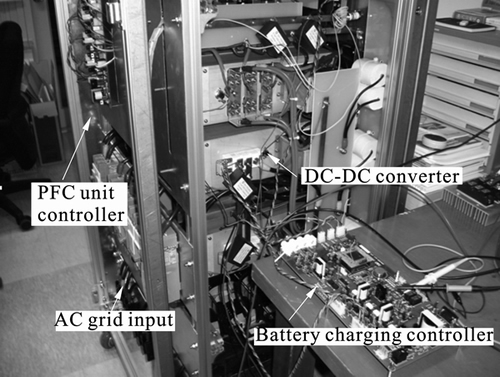
Fig. 15 Implemented 50 kW fast charger
5 Conclusions
a novel 50 kW fast charger is designed and implemented. The validity of the proposed system for a fast charger is verified through the simulations and experimental results. Using a series connection topology in the DC-DC conversion, the power conversion efficiency of the fast charger is improved. By introducing the buffering battery unit, the power installation cost can be reduced. Furthermore, with the buffering battery unit and PFC unit, the power quality of the AC grid can be improved. Currently, a 50 kW fast charger is being tested in the Mitsubishi i-Miev EV.
References
[1] KHAN I A. Battery chargers for electric and hybrid vehicles [C]// Proceedings of 1994 IEEE workshop on Power Electronics in Transportation, Dearborn, MI: IEEE, 1994: 103–112.
[2] TSAI Chia-chun, LIN Whei-min, LIN Chi-hsiang, WU Ming-shun. Designing a fast battery charger for electric bikes [C]// System Science and Engineering (ICSSE), Taipei, 2010: 385–389.
[3] DUSMEZ S, COOK A, KHALIGH A. Comprehensive analysis of high quality power converters for level 3 off-board chargers [C]// Vehicle Power and Propulsion Conference (VPPC) IEEE, Chicago: IEEE, 2011: 1–10.
[4] KUPERMAN A, LEVY U, GOREN J, ZAFRANSKI A, SAVERNIN A, PELED I. Modeling and control of a 50KW electric vehicle fast charger [C]// Electrical and Electronics Engineers in Israel (IEEEI), Eliat, 2010: 188–192.
[5] AGGELER D, CANALES F, ZELAYA-DE L PARRA H, COCCIA A, BUTCHER N, APELDOORN O. Ultra-fast DC-charge infrastructures for EV-mobility and future smart grids [C]// Innovative Smart Grid Technologies Conference Europe (ISGT Europe) IEEE PES, Gothenburg, Sweden, 2010: 1–8.
[6] BAUER P, ZHOU YI, DOPPLER J, STEMBRIDGE N. Charging of electric vehicles and impact on the grid [C]// MECHATRONIKA, 13th International Symposium, Teplice, 2010: 121–127.
[7] YILMAZ M, KREIN P T. Review of charging power levels and infrastructure for plug-in electric and hybrid vehicles [C]// Electric Vehicle Conference (IEVC), Greenville, 2012: 1–8.
[8] JOOS G, DE FREIGE M, DUBOIS M. Design and simulation of a fast charging station for PHEV/EV batteries [C]// Electric Power and Energy Conference (EPEC), London, 2010: 1–5.
[9] SUL Seung-ki, LEE Sang-joon. An integral battery charger for four wheel drive [J]. Industry Applications, IEEE Transactions on Volume, 1995, 31(5): 1096–1099.
[10] BOJRUP M, KARLSSON P, ALAKULA M, SIMONSSON B. A Dual Purpose Battery Charger for Electric Vehicles [C]// Power Electronics Specialists Conference, PESC 98 Record, 29th Annual IEEE, Fukuoka, 1998: 565–570.
[11] MASOUM A S, DEILAMI S, MOSES P S, ABU-SIADA A. Impacts of battery charging rates of plug-in electric vehicle on smart grid distribution systems [C]// Innovative Smart Grid Technologies Conference Europe (ISGT Europe) IEEE PES, Gothenburg, Sweden, 2010: 1–6.
[12] LEE Jung-hyo, MOON Jung-song, LEE Yong-seok, KIM Young-real, WON Chung-yuen. Fast charging technique for EV battery charger using three-phase AC-DC boost converter [C]// IECON 37th Annual Conference on IEEE Industrial Electronics Society, Mel bourne, 2011: 4577–4582.
[13] LACROIX S, LABOURE E, HILAIRET M. An integrated fast battery charger for electric vehicle [C]// Vehicle Power and Propulsion Conference (VPPC) IEEE, Lille, 2010: 1–6.
[14] YILMAZ A S, BADAWI M, SOZER Y, HUSAIN I. A fast battery charger topology for charging of electric vehicles [C]// Electric Vehicle Conference (IEVC) IEEE, Greenville, 2012: 1–5.
[15] MIN Byung-duk, LEE Jong-pil, KIM Jong-hyun. KIM Tae-jin, YOO Dong-wook, SONG Eui-ho. A new topology with high efficiency throughout all load range for photovoltaic PCS [J]. Industrial Electronics, IEEE Transactions, 2009: 4427–4435.
(Edited by HE Yun-bin)
Foundation item: Project supported by Changwon National University in 2011–2012
Received date: 2012–05–31; Accepted date: 2012–12–01
Corresponding author: Song Eui-ho, Professor, PhD; Tel: +82-55-213-3666; E-mail: ehsong@changwon.ac.kr