
Oxidation behavior of Fe40Al-xWC composite coatings obtained by high-velocity oxygen fuel thermal spray
XIANG Jun-huai(向军淮)1, 2, 3, ZHU Xing-he(朱星河)1, CHEN Gang(陈 钢)1,
DUAN Zhi(段 智)1, LIN Yan(林 彦) 2, LIU Ying(刘 莹)3
1. Jiangxi Hengda Hi-tech Co. Ltd, Nanchang 330000, China;
2. Jiangxi Key Laboratory of Surface Engineering, Jiangxi Science and Technology Normal University,
Nanchang 330013, China;
3. School of Mechanical and Electrical Engineering, Nanchang University, Nanchang 330031, China
Received 10 August 2009; accepted 15 September 2009
Abstract: The Fe40Al-xWC (x=0, 10, 12, 15) coatings with dense structure were successfully deposited by high-velocity oxygen fuel (HVOF) spraying of a mixture of Fe, Al and WC powders. The objective of the present work is to provide insight into the oxidation behavior of the as-deposited coatings at 650 ℃ under 0.1 MPa flowing pure O2. The present results show differences in the oxidation behavior of Fe40Al coating and Fe40Al-xWC composite coatings. The irregular Fe2O3 layer is seen on the top surface of the composite coatings. Fe40Al coating and Fe40Al-15WC composite coating both suffer a catastrophic corrosion due to the formation of a porous structure during 24 h of oxidation. However, Fe40Al-10WC and Fe40Al-12WC composite coatings show a good oxidation resistance behavior due to their dense structure.
Key words: Fe40Al; WC; HVOF; composite coatings; oxidation
1 Introduction
The exposure of metallic materials to high temperatures in oxidizing environments leads to corrosion. Iron aluminium intermetallics, especially those based on FeAl with up to 35%-50% Al (molar fraction), have been intensively studied as potential substitutes for high temperature superalloys in some applications both as bulk materials or coatings. Like general intermetallic compounds, they combine many beneficial properties like low cost, low density, good wear resistance, ease of synthesis and high resistance to oxidation and corrosion[1-5]. However, industrial application of these iron aluminium intermetallics has been very limited due to their poor ductility and fracture toughness at room temperature as well as difficulty in shaping[6].
To utilize their excellent oxidation and corrosion resistance, FeAl alloys are often deposited onto carbon steels and stainless steels for better corrosion protection. Methods of deposition used include weld overlay, fluidized bed CVD processes, cathodic arc deposition, electro-spark deposition, magnetron sputter deposition and thermal spray. One of the techniques used in thermal spray is high-velocity oxygen fuel(HVOF) spraying, in which feeding powders are heated by gas fuel and propelled by high-velocity gas stream onto properly prepared surface of samples or parts, whereupon powders are deformed and mechanically adhered to the surface[7]. HVOF spraying enables to obtain coatings with low porosity and oxide content, with a good adherence and beneficial compressive stresses. However, FeAl coatings are thought to exhibit poor wear-resistance at room temperature[3]. Therefore, we fabricated Fe40Al-xWC composite coatings by HVOF spraying to improve wear-resistance of FeAl coatings. The purpose of the present work is to investigate the effect of WC addition on the oxidation resistance of Fe40Al coatings.
2 Experimental
The powder mixture of Fe and Al with a nominal composition of Fe40Al (molar fraction) was ball milled for more than 1 h. Various amounts of WC powders ranging from 0-15% (mass fraction) were introduced to Fe40Al (molar fraction, %) mixture as feedstock for HVOF spraying. Average size of the starting powder of Fe, Al or WC is less than 60 mm. The equipment used for the spraying process is a DF-3000 system. Different combined parameters have been tested to assess the optimal ones with regard to the minimal oxidation rate and porosity. The spraying parameters are shown in Table 1. These Fe40Al-xWC (x=0, 10, 12, 15) coatings were sprayed by HVOF spraying on flat and circular samples of low alloyed carbon steel Q235, which previously grit blasted to provide mechanical bonding.
Table 1 Thermal spraying parameters
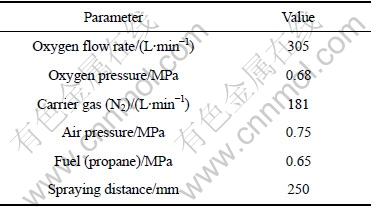
Isothermal oxidation tests were performed for samples with all sides covered by the composite coatings at 650 ℃ under 0.1 MPa flowing pure O2. Continuous mass change measurements were carried out by a Cahn Versatherm TGA system for 24 h. The oxidized specimens were examined by means of X-ray diffractometer (XRD), scanning electron microscope (SEM) and energy-dispersive X-ray microanalyzer (EDX).
3 Results and discussion
3.1 Oxidation kinetics
The kinetic curve and the corresponding parabolic plot for the oxidation of individual Fe40Al-xWC coatings at 650 ℃ are shown in Figs.1(a) and (b), respectively. All the kinetic curves are rather regular and can be approximately considered to be composed of a parabolic oxidation stage after 3 h, except for the oxidation of Fe40Al coating, which shows a continuous decrease in the slope of the parabolic plot up to the end of the test. Approximate values of the parabolic rate constants, calculated from analysis of the mass-gain data vs. the square root of time, are reported in Table 2.
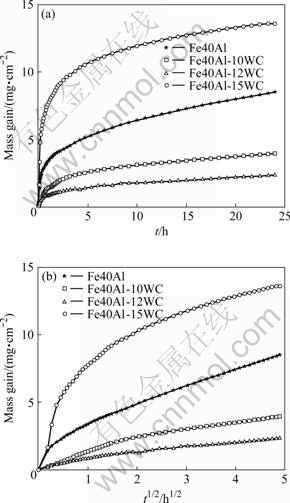
Fig.1 Oxidation kinetics of Fe40Al-xWC (x=0, 10, 12, 15) coatings under 0.1 MPa O2 at 650 ℃: (a) Normal plots; (b) Parabolic plots
Table 2 Approximate parabolic rate constants for oxidation of Fe40Al-xWC (x=0, 10, 12, 15) coatings at 650 ℃
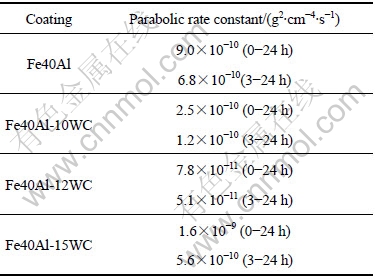
Fe40Al-12WC composite coating presents the best oxidation resistance. On the whole, the oxidation rate of Fe40Al-12WC or Fe40Al-10WC coatings are much smaller than that of the Fe40Al or Fe40Al-15WC coatings. Although the Fe40Al-15WC coating corroded much more rapidly than the Fe40Al coating after 24 h oxidation, the former shows a little lower oxidation rate than the latter after 3 h.
3.2 Microstructure prior to oxidation
Fig.2 shows cross-sectional morphologies of as-deposited Fe40Al-xWC coatings (x=0, 10, 12, 15). Coatings with thickness of 200-400 mm were obtained. Both Fe40Al coating and Fe40Al-xWC coatings prepared by HVOF spraying had typical aspects of thermally sprayed lamellar structure. The thickness of thermally sprayed coatings formed with the same depositing conditions was affected by the addition of different amount of WC powders. Although the addition of 15% WC increased the thickness of Fe40Al coatings greatly, probably as a result of increased wetting and bond strength of the coating, additions of 10% WC only increased the thickness a little.
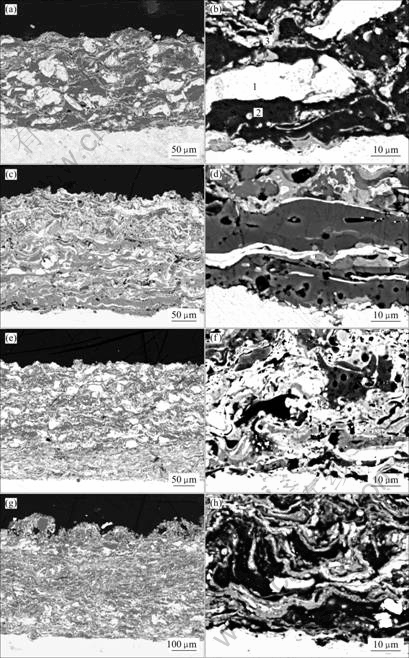
Fig.2 SEM/BEI micrographs showing cross-sectional morphology of as-deposited coatings: (a) Fe40Al at low magnification; (b) Fe40Al at high magnification; (c) Fe40Al-10WC at low magnification; (d) Fe40Al-10WC at high magnification; (e) Fe40Al-12WC at low magnification; (f) Fe40Al-12WC at high magnification; (g) Fe40Al-15WC at low magnification; (h) Fe40Al-15WC at high magnification
According to the EDX analysis and XRD spectrum, the majority metallic phases in all coatings were Fe, Al and iron aluminide (Fe3Al and FeAl). White WC particles were embedded in the metal matrix of the composite coating. From Fig.2, the coating consisted of highly deformed regions, and small fully melted regions. The highly deformed regions were original particles not fully melted: the light phase (Location 1 in Fig.2(b)) is Fe and the dark phase (Location 2 in Fig.2(b)) is Al. A little Fe oxides were present around the highly deformed regions of Fe. In the fully melted regions (Location 3 in Fig.2(b)), iron aluminides (Fe3Al and FeAl) were present, sometimes mixed with oxides of Fe and Al. Fe3Al could be formed due to Al evaporation and oxidation during spraying. The presence of Fe3Al in FeAl HVOF coatings was also reported by XIAO and CHEN[7]. On the whole, the distribution of all kinds of phases of composite coatings is more even than that of Fe40Al coating.
3.3 Oxidation behavior
Fig.3 shows cross-sectional morphologies of as-deposited Fe40Al-xWC coatings (x=0, 10, 12, 15) oxidized at 650 ℃ for 24 h. Fe40Al coating suffered a catastrophic corrosion due to the formation of a lot of large cavities during 24 h oxidation, as seen in Fig.3(a). Fe40Al-15WC coatings also exhibited a bad oxidation resistant behavior for the same reason. Since the number of cavities was less than that of Fe40Al coating, Fe40Al-15WC coating (Fig.3(g)) showed a little lower oxidation rate after 3 h. However, Fe40Al-10WC and Fe40Al-12WC (Figs.3(c) and (e)) coatings presented a good oxidation resistance behavior with regards to their compact coating structures during the whole oxidation periods.
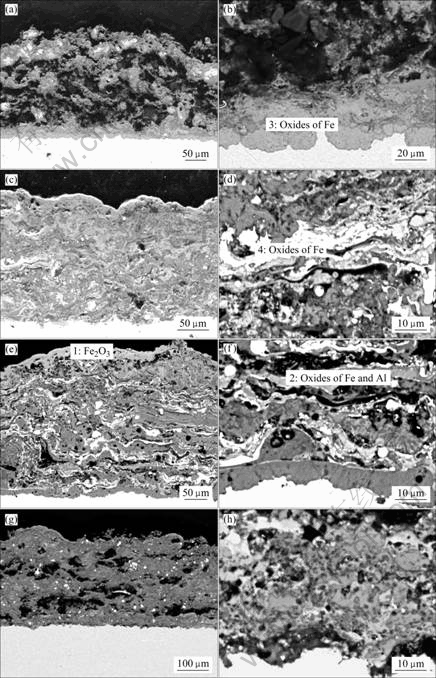
Fig.3 SEM/BEI micrographs showing cross-sectional morphology of as-deposited coatings oxidized in 0.1 MPa pure O2 at 650 ℃ for 24 h: (a) Fe40Al at low magnification; (b) Fe40Al at high magnification; (c) Fe40Al-10WC at low magnification; (d) Fe40Al-10WC at high magnification; (e) Fe40Al-12WC at low magnification; (f) Fe40Al-12WC at high magnification; (g) Fe40Al-15WC at low magnification; (h) Fe40Al-15WC at high magnification
According to the analysis of XRD spectra, all composite coatings formed an outermost continuous Fe2O3 layer, for example, Location 1 in Fig.3(e). The absence of other peaks in XRD spectra indicated that the Fe2O3 layer was thick. Large islands of Fe and Al in all
coatings diminished greatly during the oxidation periods. This suggested a diffusion between different phases of the initial coating, leading to a homogenous composition, when being held at 650 ℃. Such phenomenon was already proposed by HEARLEY et al for NiAl[8]. According to the EDX analysis,the contents of oxygen in all coatings increased after oxidation, probably due to the inward oxygen diffusion and reaction in the coatings.
The majority oxides in all coatings are the mixture of oxides of Fe and Al (26.8%Fe, 11.8%Al and 61.4% O, by EDX analysis), as seen at Location 2 in Fig.3(f). The presence of Al2O3 and FeO suggested the possibility of their reaction to form FeAl2O4 spinel. A continuous thick layer of Fe oxides formed at the coating/steel interface due to the porous microstructure of Fe40Al coating, which resulted in the oxidation of the matrix steel. On the contrary, this phenomenon was not present for the composite coating due to their relatively dense structure. Only a few islands of pure Fe (not shown in Fig.3) and their oxides (Location 4 in Fig.3(d)) were present in local place. After 24 h oxidation, iron aluminides (Fe3Al and FeAl) could still be found in all coatings, as seen at Location 5 in Fig.3(h).
For Fe-Al alloy, the critical Al content required to form an externally protective scale was within the range of 10%-28% Al between 600 and 1 300 ℃[9-10]. For the Fe3Al and FeAl bulk intermetallics which showed a parabolic rate, the aluminium oxide was expected to form a completely protective scale not only because of its high stability but also mainly because of enough high Al content in such alloys[11-14].
The present study concerns the oxidation behavior of a thermally-sprayed coating. Therefore, not only element composition but also the intrinsic microstructure and further parameters can play an important role in modifying the oxidation kinetics. The heterogeneous structure provides further oxidation paths. In addition, apart from the internal coating structure, external finishing should also be taken into account for the present Fe40Al-xWC coatings. While works performed with bulk materials deal with mirror-like polished surfaces, HVOF spraying coatings result in their characteristic roughness depending on the powder particle sizes and spraying parameters. From foregoing discussion, the Al content of the Fe40Al-xWC coatings (x=0, 10, 12, 15) is not enough to form an externally protective alumina layer. Moreover, the porous structure of Fe40Al coating formed by outwards iron diffusion during the oxidation period weakened its oxidation resistance. However, adding 10%-12% WC hard particles favored building a dense coating with much lower oxidation rate.
4 Conclusions
1) Both Fe40Al coating and Fe40Al-xWC composite coatings prepared by high velocity oxygen fuel technique had typical aspects of thermally sprayed lamellar structure. The majority phases in all coatings were Fe, Al and iron aluminides (Fe3Al and FeAl). White WC particles were embedded in the metal matrix of the composite coating.
2) Fe40Al coating suffered a catastrophic corrosion due to the formation of a porous structure during 24 h oxidation. Fe40Al-15WC coating also exhibited a bad oxidation resistant behavior for the same reason. However, Fe40Al-10WC and Fe40Al-12WC composite coatings presented a good oxidation resistance behavior with regards to their compact coating structures.
3) The majority oxides in all coatings were the mixture of oxides of Fe and Al. The Al contents of the Fe40Al-xWC coatings (x=0, 10, 12, 15) are not enough to form an external protective alumina layer.
References
[1] HOUNGNIOUC, CHEVALIER S, LARPIN J P. High temperature oxidation behavior of iron-aluminide diffusion coatings [J]. Oxid Met, 2006, 65: 409-439.
[2] GUILEMANY J M, CINCA N, DOSTA S, LIMA C R C. High-temperature oxidation of Fe40Al coatings obtained by HVOF thermal spray [J]. Intermetallics, 2007, 15: 1384-1394.
[3] GUILEMANY J M, LIMA C R C, CINCA N, MIGUEL J R. Studies of Fe-40Al coatings obtained by high velocity oxy-fuel [J]. Surf Coat Technol, 2006, 201: 2072-2079.
[4] YAMAGUICHI M, INUI H, ITO K. High temperature structural intermetallics [J]. Acta Mater, 2000, 48: 307-322.
[5] DEEVI S C, SIKKA V K. Nickel and iron aluminides: An overview on properties, processing, and applications [J]. Intermetallics, 1996, 4: 357-375.
[6] DEEVI S C, SIKKA V K, LIU C T. Processing, properties, and applications of nickel and iron aluminides [J]. Prog Mater Sci, 1997, 42: 177-192.
[7] XIAO Cheng-bo, CHEN Wei-xing. Sulfidation resistance of CeO2-modified HVOF sprayed FeAl coatings at 700 ℃ [J]. Surf Coat Technol, 2006, 201: 3625-3632.
[8] HEARLEY J A, LITTLE J A, STURGEON A J. Oxidation properties of NiAl intermetallic coatings prepared by high velocity oxy-fuel thermal spraying [C]// Proceedings of the 15th Thermal Spray Conference. Nice (France): 1998, 1: 89-94.
[9] XIANG Jun-huai, NIU Yan, WU Wei-tao. Critical Al content to form external-alumina scales on Cu-Al alloys [J]. Intermetallics, 2007, 15: 635-638.
[10] PINT B A, LEIBOWITZ J, DEVAN J H. The effect of an oxide dispersion on the critical Al content in Fe-Al alloys [J]. Oxid Met 1999, 51: 181-197.
[11] PEDRAZA F, GROSSEAU-POUSSARD J L, DINHUT J F. Evolution of oxide scales on an ODS FeAl intermetallic alloy during high temperature exposure in air [J]. Intermetallics, 2005, 13: 23-33.
[12] KUPKA M. High temperature strengthening of the FeAl intermetallic phase-based alloy [J]. Intermetallics, 2006, 14: 149-155.
[13] TORTORELLI P F, NATESAN K. Critical factors affecting the high-temperature corrosion performance of iron aluminides [J]. Mater Sci Eng A, 1998, 258: 115-125.
[14] XU C H, GAO W, LI S, Oxidation behaviour of FeAl intermetallics: The effect of Y on the scale spallation resistance [J]. Corros Sci, 2001, 43: 671-688.
Foundation item: Project(209069) supported by the Key Research Program of Ministry of Education of China; Projects(2008GZC0065; 2007GZC0611) supported by the Natural Science Foundation of Jiangxi Province, China
Corresponding author: XIANG Jun-huai; Tel: +86-791-3801423; E-mail: xiangjunhuai@163.com
DOI: 10.1016/S1003-6326(09)60067-4
(Edited by YANG Hua)