Article ID: 1003-6326(2005)02-0280-06
Mechanical properties of fine grained
superalloy K4169 with addition of refiners
HUANG Tai-wen(黄太文)1, LIU Lin(刘 林)2, YANG Ai-min(杨爱民)2,
XIONG Yu-hua(熊玉华)3, ZHANG Rong(张 蓉)1
(1. State Key Laboratory of Solidification Processing, Northwestern Polytechnical University, Xi'an 710072, China;
2. Department of Mechanical Engineering, Xi'an Petroleum Institute, Xi'an 710065, China;
3. Beijing General Research Institute for Non-ferrous Metals, Beijing 100088, China)
Abstract: Grain refinement of superalloy K4169 was achieved by adding refiners into the alloy melt and their effects on the mechanical properties were investigated. The tensile properties at room temperature and 700℃ and low cycle fatigue properties at room temperature were compared for both conventional and fine grained test bars. The results indicate that the rupture strength, yield strength, elongation and reduction of area for refined grains are all much superior to those for coarse ones. Whereas the elongation and reduction of area of fine grained samples decrease at 700℃. Low cycle fatigue properties of samples with refined grains at room temperature are improved significantly. In addition, the degree of dispersion of low cycle fatigue data of samples with refined grains is diminished.
Key words: superalloy; grain refinement; refiner; tensile properties; LCF CLC number: TG113.25; TG146.1
Document code: A
1 INTRODUCTION
The integral fine-grained cast techniques for superalloys[1, 2] have been used in small aero engines for many years in order to achieve uniform properties, homogeneous microstructures and morphology of precipitates such as carbides and γ′ phase. The current integral fine-grain casting techniques still utilize thermal control or vibrating methods to control grain size in which complicated equipment is needed and production cost is increased, therefore, a simple method, chemical addition method in which the refiners are added to the alloy melt before pouring is paid more attention to. However, some researchers indicate that some chemical addition can cause crack propagation or variation of constitution which makes the heat treatment of the alloy difficult due to the different physical-chemical properties between the master alloy and refiner[3-5]. Accordingly, more detailed investigations on chemical refinement of superalloys should be performed. In the previous work[6], the refined structures of superalloy K4169 were obtained by adding some intermetallic compounds as refiners. The present paper will continue to study their effects on mechanical properties.
2 EXPERIMENTAL
2.1 Experimental materials
A Fe-Ni based superalloy K4169 was used in this work. It has the following chemical compositions(mass fraction, %): 0.05C, 0.01Co, 52Ni, 3.05Mo, 5.3Nb, 18.4Cr, 0.55Al, 1.05Ti and balance Fe.
2.2 Melting and casting
A ZG 200 type vacuum melting and casting unit was used to cast conventional and fine-grained ingots. The essential processing parameters are listed in Table 1. The preheating temperature of the ceramic mould was kept at 900℃ in all cases. The refiner was added before pouring. The melt was subsequently poured into metallographic samples for investigating mechanical properties. Details of the experimental process have been described elsewhere[6].
2.3 Mechanical property tests
The test bars for mechanical property were processed into property samples with reference to Chinese National Standard GB 6397—86. Tensile properties at room temperature and 700℃ were tested with a WJ-10B universal mechanical strength tester and a ZDM-5 tensile tester, respectively, The fatigue test samples were prepared with 6mm in diameter and the fatigue tests were carried out with a 100kN MAYES mechanical fatigue equipment at room temperature in static air under whole strain controlled pull-press loading in all re-direction axis at nominal strain amplitude of ±0.22%-±0.9%, with triangle wave at strain ratio R=-1 and loading rate of 1×10-4mm/s. Some of those samples were examined by Cambridge S-360 scanning electron microscope(SEM).
Table 1 Grain structure features under various casting conditions
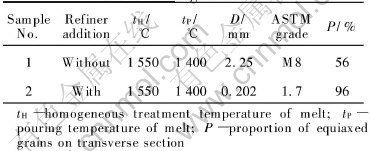
3 EXPERIMENTAL RESULTS
3.1 Grain structure
Table 1 illustrates the experimental scheme and processing parameters, together with characteristic parameters of grain structures under various refining processing. The corresponding grain structures are shown in Fig.1. It can be seen that adding refiner into the melt can markedly reduce the grain size(D) and improve the fraction of equiaxed grain at traverse cross-section(P).
3.2 Tensile properties
Table 2 lists the data of tensile properties at room temperature and 700℃. When the grain size is between 0.20 and 2.25mm, the yield strength, ultimate strength, elongation and reduction of area are increased markedly along with the progress of grain refinement at room temperature. At 700℃, the situations are the same for both strengths. In terms of elongation and reduction of area, the behavior is different. When grains are refined, the value of them drops.
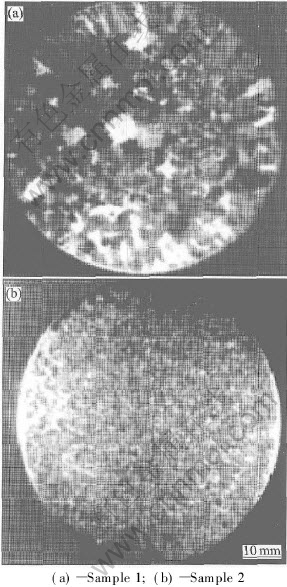
Fig.1 Grain structures of cylindrical ingots obtained
The experiment facts that refined structures have superior tensile properties to large grain structures(LGS) are attributed to that refined structures have more grain boundaries than coarse grain to accomplish the strengthening effect when grain boundaries can inhibit dislocation gliding[7]. Moreover, the refinement of grain leads to the uniformity structures and precipitates distribution, so less stress is produced and crack propagation is delayed, while coarse structures produce constitution segregation and coarse precipitates, which cause higher stresses and crack among grain boundaries or particles.
Table 2 Tensile properties for samples with different grain sizes
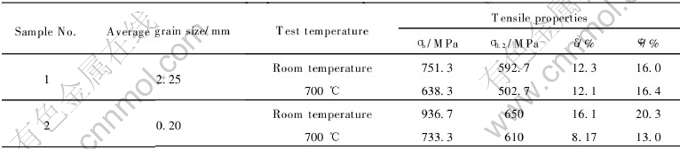
The fracture morphologies of tensile samples are shown in Fig.2. As compared with the toughness nest characteristic (Fig.2(a))of fine grain structure(FGS), the morphologies of LGS show that the sample fractures along interdendritic areas (Fig.2(b)). So interdendritic areas of LGS may be a factor of weakness of tensile properties. The previous investigation[6] indicated that interdendritic segregation of conventional grained structure is more serious than that of FGS. Thus, much more positive segregation elements, such as Mo, Nb, will accumulate in interdendritic areas of LGS. Enrichment of Mo and Nb elements may produce δ and Laves phase which will deteriorate mechanical properties. Therefore, we can conclude that the decrease of elemental micro-segregation of FGS makes a contribution to improving tensile properties. Figs.2(c) and (d) show the fracture morphologies at 700 ℃. Fig.2(c) shows that many microminiature second phase particles such as carbides in fine grain samples inhibit dislocation gliding in stead of being channels of cracks at 700℃. Also, the fact that the fracture surface of both FGS and LGS samples shows transgranular fracture is due to the strengthening effect of grain boundaries at 700℃. Therefore, FGS has a higher strength than LGS at 700℃ as listed in Table 2. In transient-fracture areas of FGS , a typical quasi-cleavage characteristic(Fig.2(d)), which is a kind of brittle transgranular rupture, is observed. Such kind of fracture surface generally shows less micro-roughness according to the limited amount of plastic deformation. Transcrystalline crystallographic facets are more frequently observed, suggesting that sliding plane decohesion plays an important role in the fracture process[8]. Since the total plastic strain of such kind of fracture is more than that of cleavage, but less than that of ductile fracture, it is consistent with the experimental results that the values of elongation and reduction of area of FGS drop at 700℃.
3.3 Low cycle fatigue properties
Fig.3 illustrates the low cyclic fatigue(LCF) life at various strain amplitudes. It can be seen that finer grain improves the LCF life significantly at room temperature. Especially, the lower the strain amplitude, the larger the difference of fatigue life is. Fatigue life of fine-grained sample increases from about 20% at Δεt=0.2% to about 100% at Δεt=0.6%. In addition, the dispersion degree of LCF data of fine-grained samples is diminished. Table 3 lists the variance logarithm of fatigue life. It can be seen that the values of fatigue life for fine-grained samples are larger than those for coarse grained samples at all strain levels. Other researchers have gained the same results[1, 9]. This is related to the modulus values of the alloys. The finer grained materials have higher and more consistent modulus than conventionally cast alloys, reflecting the superior isotropic behavior of former and implying reduced scatter values and higher statistical stability. The fracture surfaces were examined in order to compare the fracture morphology between LGS and FGS. In the two different samples, the fracture surfaces have similar multiple fatigue crack headstreams(Fig.4(a)). Those fracture surfaces illustrate transgranular fracture with fatigue striations usually observed for cycle dependent deformation. But the fracture morphology is different(Figs.4(b) and (c)). It can be attributed to that the higher yield strength of FGS accomplished by uniform structures and precipitates distribution leads to higher fatigue crack driver than that of LGS which brings multiple slip systems and crack growth path as shown in Fig.4(c). In addition, we can find in the fatigue fracture surface that the second phase particle inhibits fatigue crack (Fig.4(d)) which improves FGS low cyclic fatigue life of FGS as that in the tensile properties. Furthermore, in all of those fracture surfaces of FGS there is no chemical addition particle found that induces crack propagation or turns into a crack headstream. Both the mechanical properties and the fracture morphology strongly suggest that the selection of chemical refiner is successful.
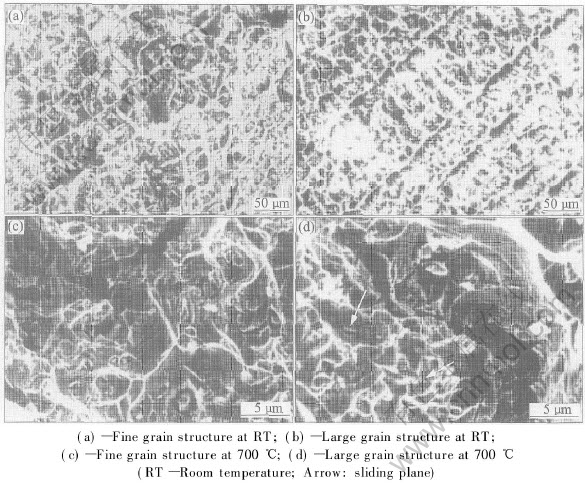
Fig.2 Fractographs of tensile samples
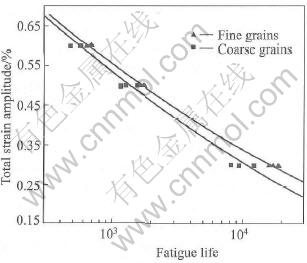
Fig.3 Fatigue life of K4169 superalloy with different grain structures at room temperature
Table 3 Variance logarithm of fatigue life(lnS*n)
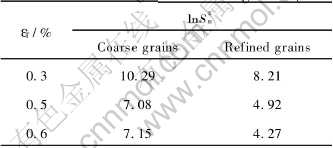
4 DISCUSSION
4.1 Tensile properties at 700℃
Elevation of testing temperature has obvious effects on tensile properties of materials. Strength data of fine grain structures are still higher than those of coarse grain structures at 700℃, indicating equal strength temperature (tequ) is higher than 700℃ for tensile deformation of alloy K4169. But elongation and reduction in area decrease at 700℃ with refinement of grain structure which is similar to the result of Bouse[10].The behavior of FGS is something like intermediate temperature brittleness (ITB) which is also observed in other superalloys[11, 12]. Since LGS ductility doesnt distinctly drop at 700℃, microstructure may influence the ITB behavior. HE et al[13]have studied the low ductility at intermediate temperature of Ni-base superalloy M963. Their results indicated that the dislocations were trapped in the narrow connected slip bands within matrix channel and the deformation was very inhomogeneous, leading to ductility decrease under solution treatment; while the dislocations became trapped in the γ/γ′ interfaces and were more homogeneously distributed, leading to the better ductility observed under aging treatment. But in this work the deformation of FGS must be homogeneous because of fine grained structure and uniform precipitates distribution. Therefore current results can not be explained by previous work.
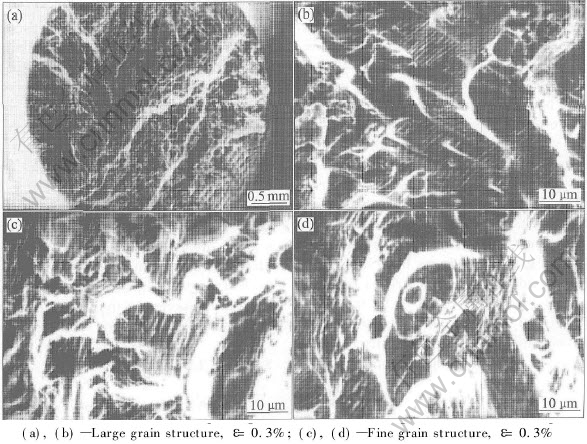
Fig.4 Fracture surface morphologies of two different grain structured samples
It can be explained by changes of fracture toughness according to Tetelmans fracture toughness formulation[14]:
KⅠC=2.9σ0.2[exp(σb/σ0.2-1)-1]1/2ρ1/2(1)
where ρ is the radius of end of crack. Obviously, the larger the value of (σb /σ0.2) is, the larger the fracture toughness is and the less the brittleness of the grain structure is. From the experimental results in Table 3, the values of (σb /σ0.2)of refined structure vary from 1.45 to 1.20 as temperature changes from room temperature to 700℃. That is refined structure becomes more brittle at elevated temperature. While the values of (σb /σ0.2)of coarse grain structure have no change (from 1.27 to 1.27). Its fracture toughness KⅠC changes little and keeps at larger value, so that refined structure produces crack propagation quickly and its deformation amount is less. That is why elongation and reduction of area of refined structure are less than those of the coarse grain structure.
Another explanation of the facts above is that the precipitates at grain boundaries have lower capability to resist oxidation than γ matrix at 700℃, resulting in crack propagation rate to be faster at grain boundaries and crack to occur at surfaces of grain boundaries. As a result, the ductility level of fine-grained sample with much more grain boundaries is reduced.
4.2 Effects of grain-refinement on LCF properties
The total fatigue life of a specimen consists of a crack initiation phase and a crack propagation phase. It is mentioned that fatigue cracks of superalloys initiate on slip bands (or multiple slip systems), carbides and micropores at room temperature. Those slip bands or multiple slip systems are a consequence of local accumulation of the inhomogeneous plastic strain. Nilsson and Thorvaldsson[15] pointed out that, stress agglomeration under cyclic load was impeded in fine grain specimens, and inhomogeneous plastic fluid is diminished, as a result, fatigue crack initiation phase is prolonged. Additionally, grain refinement restricts the porosity and carbide size. So fine grain samples are superior to coarse ones in this instance.
Fatigue crack propagation(FCP) frequently accounts for a high ratio in fatigue life. A class of models have been developed in which the FCP process is viewed as one in which cyclic damage accumulates ahead of the crack tip with a local LCF mechanism in the processing zone(a small region). The model predicts that the resistance to FCP can be increased by increasing the grain size because of lower average strain in the critical crack tip zone. On the other hand, in an extensive study of FCP in commercial alloys, it is shown that the FCP rate tends to decrease with increasing strength[16]. So there are inconsistent factors that affect FCP of fine-grained sample which has a high strength and small grains. Recently, the fatigue crack growth rate of a polycrystalline IN718 superalloy with two different grain sizes was investigated by Osinkolu et al[17]. The results showed that the difference of FCP between FGS and LGS depended on the loading cycle and testing temperature. LGS material is less resistant to fatigue crack growth than FGS material in the tensile loading cycle. The result shown in Fig.3 that finer grain improves fatigue life more significantly at lower strain amplitude indicates that the FCP rate of fine grain structure decreases. The observed result may be rationalized by taking the difference of the mechanical properties into consideration. The reason is that the crack growth rate is usually taken to be proportional to the crack tip opening displacement(DCTO). Since DCTO=Δk2/(σyE), any variation in E or σy will in turn lead to changes in crack growth rate. In fact, a good integrated properties of the strength and plasticity are essential to LCF. It is shown that both strength and plasticity of fine-grained samples are more superior to those of coarse ones. So finer grain structure improves the LCF properties.
5 CONCLUSIONS
1) All tensile properties such as rupture strength, elongation for fine-grained samples are more superior to those of the coarse-grained ones at room temperature. At 700℃, the situations are the same for both strengths, but the values of elongation and reduction of area drop for refined grains. This is caused by the different value of σb /σ0.2 at various temperatures.
2) Finer grain improves the low-cycle fatigue life significantly at room temperature, ranging from 20% to 100%, according to the strain amplitude. In addition, the dispersion degree of low-cycle fatigue life data of fine-grained samples is diminished.
REFERENCES
[1]Woulds M, Benson H. Development of a conventional fine grain process [A]. Gell M. Superalloy 1984 [C]. New York: Met Soc TMS-AIME, 1984. 3-12.
[2]Brinegar J R, Norris L F, Rozenberg L. Microcast-X fine grain casting—a progress report [A]. Gell M. Superalloy 1984 [C]. New York: Met Soc TMS-AIME, 1984. 23-32.
[3]Denzine A F, Kolakowski T A, Wallance J F. Grain refinement of cast nickel-base superalloys and its effect on properties [A]. Proc AGARD Conf on Advanced Casting Technology [C]. Paris: Advisory Group for Aerospace Research and Development, 1982. 12-16.
[4]Dennison J P. Grain refinement by the introduction to the melt of oxide particles pre-dispersed in melt strip [A]. Abbaschian G J, David S A. Grain Refinement in Casting and Welds [C]. New York: The Metallurgical Society of AIME, 1983. 139-149.
[5]Zhen B L, Liu L, Yong Z Y, et al. Grain refinement of superalloy In 738LC[J]. Metall, 1994, 48(2): 118-122.
[6]XIONG Yu-hua, YANG Ai-min, GUO Yi-ping, et al. Grain refinement of superalloy K3 and K4169 by addition of refiners[J]. Sci Techn Adv Mater, 2001, 2: 13-17.
[7]Wei C N, Bor H Y, Ma C Y, et al. A study of IN-713LC superalloy grain refinement effects on microstructure and tensile properties[J]. Materials Chemistry and Physics, 2003, 80: 89-93.
[8]Kolbe M, Neuking K, Eggeler G. Dislocation reactions and microstructural instability during 1025℃ shear creep testing of superalloy single crystals [J]. Mater Sci Eng, 1997, A234-A236: 877-879.
[9]Ewing B A, Green K A. Polycrystalline grain controlled casting for rotating compressor and turbine components [A]. Gell M, Kortovich C S, Bricknell R H, et al. Superalloy 1984 [C]. New York : The Metallurgical Society of AIME, 1984. 33-42.
[10]Bouse G K. Mechanical properties of microcast-X alloy 718 fine grain investment casting [A]. Loria A. Superalloy 718-Metallurgy and Application [C]. Pittsburgh: TMS, 1989. 69.
[11]Jensen R R, Tien J K. Temperature and strain rate dependence of stress-strain behavior in a nickel-base superalloy [J]. Metall Trans A, 1985, 16A: 1049-1068.
[12]Milligan W W, Antolovich S D. The mechanisms and temperature dependence of superlattice stacking fault formation in the single-crystal superalloy Pwa 1480 [J]. Metall Trans A, 1991, 22: 2309-2318.
[13]He L Z, Zheng Q, Sun X F, et al. Low ductility at intermediate temperature of Ni-base superalloy M963 [J]. Materials Science and Engineering A, 2004, 380: 340-348.
[14]Macha D E, Cole G R, Butzer J A. Fine grain investment-cast integral turbine wheels [A]. Abbaschian G J. Grain Refinement in Casting and Welds [C]. New York: The Metallurgical Society of AIME, 1983. 197-219.
[15]Nilsson J O , Thorvaldsson T. Low cycle-fatigue behaviour of alloy 800H at 600℃—effect of grain size and γ′-precipitate dispersion [J]. Fatigue & Structures, 1985, 8(4): 373.
[16]Gayda J, Miner R V. Effects of processing and microstructure on the fatigue behaviour of the nickel-base superalloy[J]. Met Trans, 1983, 14A: 2301-2308.
[17]Osinkolu G A, Onofrio G, Marchionni M. Fatigue crack growth in polycrystalline in 718 superalloy[J]. Materials Science and Engineering, 2003, A356: 425-433.
Foundation item: Project(G2000067202) supported by the National Basic Research Program of China
Received date: 2004-11-20; Accepted date: 2005-01-18
Correspondence: HUANG Tai-wen, PhD Candidate; Tel: +86-29-88493264; E-mail: taiwen_h@yahoo.com
(Edited by YANG Bing)