
Corrosion properties of plastically deformed AZ80 magnesium alloy
ZHANG Zhi-min(张治民),XU Hong-yan(徐宏妍), LI Bao-cheng(李保成)
School of Materials Science and Engineering, North University of China, Taiyuan 030051, China
Received 23 September 2009; accepted 30 January 2010
Abstract: AZ80 magnesium alloys were deformed at 200, 250, 300, 350 and 400 ?C with different deformation degree of 50%, 75%, 83%, 87% and 90%, respectively. The corrosion properties of different deformed AZ80 samples were studied by galvanic test in 3.5% NaCl solution. The results show that plastic deformation could improve the corrosion resistance of AZ80 alloy; and the corrosion rate of AZ80 deformed at 250 ?C with the deformation degree of 83% was the lowest, which was 33% of the as-cast AZ80 alloy. Further studies of the microstructure show that the refined grain size and continuously distribution of β phase around the grain boundary did have a positive effect on the improvement of corrosion resistance of AZ80 alloys. For AZ80 alloys, the smaller the grain size is, the more homogeneous the structure is, and the better the corrosion resistance is.
Key words: corrosion property; plastic deformation; AZ80 magnesium alloy
1 Introduction
Magnesium alloys, with a relatively high specific strength and excellent technological properties, have a high potential for use as a lightweight structural material in automotive and aerospace applications[1]. However, the susceptibility to corrosion is a major obstacle to the growth of magnesium alloys in their applications.
Many efforts were paid to improve the corrosion resistance of magnesium alloys, such as new alloy designs[2], surface modification treatments[3], protective films and coatings[4]. It is reported that microstructural parameters, such as grain size and phase distribution, play a role in determining the corrosion resistance of magnesium-base alloys[5], and β phase Mg17Al12 is bi-functional to the corrosion behavior[6]. It was also found that plastic deformation can improve the mechanical properties and corrosion resistance of magnesium alloys[7]. Some researchers believe that the improvement of corrosion properties of plastically deformed magnesium alloys are of the refined grain size[8].
In this study, AZ80 alloys were deformed at different temperatures with different deformation degrees.
The effect of plastic deformation on corrosion properties of AZ80 magnesium alloys was studied by galvanic corrosion test, and the corrosion mechanism of plastic deformed AZ80 alloys was also analyzed.
2 Experimental
2.1 Materials
The experimental material is AZ80 magnesium alloy with the chemical compositions listed in Table 1.
Table 1 Chemical compositions of AZ80 magnesium alloy (mass fraction, %)
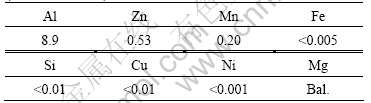
As-cast AZ80 alloy bars were first homogenized at 450 ?C for 16 h, and then cut along the axial direction to plates with 150 mm long, 17 mm wide and different thickness of 2, 4, 6, 8 and 10 mm. These plates were compressed isothermally at different temperatures of 200, 250, 300, 350 and 400 ?C with different deformation degrees of 50%, 75%, 83%, 87%, and 90%, respectively.
2.2 Electrochemical tests
Corrosion properties of deformed AZ80 alloys were measured by galvanic test in 3.5% NaCl solution at room temperature without stirring or deaeration. A saturated calomel electrode (SCE) and carbon steel plate were used as the reference and couple electrode, respectively. The working electrodes were the deformed AZ80 alloys, which were embedded in an epoxy resin to provide insulation, leaving a 1 cm2 surface exposed to the electrolyte. Polishing was carried out on samples with SiC paper up to 2 000 grit before measurements. The galvanic corrosion measurement duration was 1 h. Before and after measurement, the free corrosion potentials were measured for 15 min.
2.3 Microstructure observations
Following standard metallographic procedures, the polished surfaces of the deformed samples were etched using a solution containing 2% oxalic acid and 2% nitric acid, and their microstructures were examined with Image MAT A1 optical microscope. For comparison, the microstructure of the as-cast AZ80 alloy was also observed.
3 Results and discussion
3.1 Galvanic corrosion of plastically deformed AZ80 alloys
The free corrosion potentials of different AZ80 alloys are listed in Table 2. It is clearly that corrosion
Table 2 Free corrosion potentials of different plastically deformed AZ80 alloys in 3.5%NaCl solution
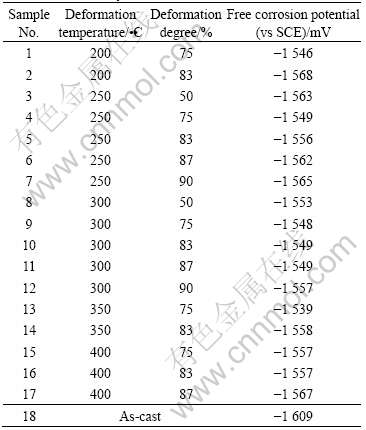
potentials of the deformed samples are higher than those of the as-cast alloy, and the same phenomenon has been observed in the hot-extruded AZ31 alloys[9]. The potential difference between a pair of metals gives the driving force for galvanic corrosion. When coupling with the same cathode, the higher the free corrosion potential of the anode is, the lower the corrosion rate is. Therefore, plastic deformation can increase the galvanic corrosion resistance of AZ80 alloys.
Fig.1 shows the normalized integrated galvanic currents of AZ80-carbon steel couples, where the value for the couple with AZ80 deformed at 250 ?C and 83% deformation degree is set to 1.
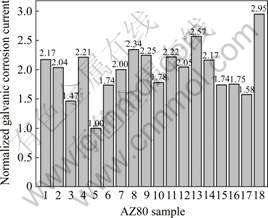
Fig.1 Normalized galvanic corrosion currents of AZ80 alloys
It can be known from the anodic reaction (Mg→Mg2++2e-) of AZ80 alloys that 2 mol electron transfer will cause the oxidation of 24 g Mg. Therefore, higher integrated corrosion current indicates worse anti-galvanic corrosion properties. It is clear that the galvanic corrosion resistance of deformed AZ80 is better than that of the as-cast one. Moreover, the measurements showed that, the current increment decreases with corrosion for deformed AZ80 while increases for as-cast alloy (Fig.2). So, it can be concluded that, with the increase of time, the corrosion rate decreases for all the deformed AZ80 alloys and increases for the as-cast alloy. MATHIEU et al[10] also proved that corrosion rate is variable based on the investigation of AZ91D. With increase of time, the corrosion rate of semi-solid cast AZ91D first decreased then increased intensively after 24 h, while for die-casting AZ91D, the corrosion rate decreased stably with corrosion time.
It can be observed from Fig.1 that, the galvanic corrosion resistance is low for AZ80 deformed at 200 ?C and 350 ?C and high for AZ80 deformed at 250 ?C and 400 ?C. Moreover, the galvanic corrosion resistance of AZ80 deformed at 400 ?C is almost invariable independently on the deformation degree; While for alloys deformed at 250 ?C , the galvanic corrosion resistance changes intensively with deformation degree and becomes best when the deformation degree is 83%. The results show that the lowest corrosion rate of the deformed AZ80 alloy is only 33% of that of the as-cast AZ80.
From Fig.2(a), it can be clearly observed that the increment of coupling-time dependent galvanic electric quantity of deformed AZ80 alloys is smaller than that of the as-cast alloy. Fig.2(b) shows the typical galvanic current of deformed AZ80 alloy, which decreases with the increase of the coupling time. These results reveal that, during immersion, the surface state of the deformed sample turns from activity to passivity.
Generally, the higher the free corrosion potential difference between AZ80 and contact material is, the higher the normalized integrated corrosion current is[11-12], but the results do not correspond with each other in this work (Fig.1 and Table 2). This implies that the surface state of deformed AZ80 changes during galvanic test.
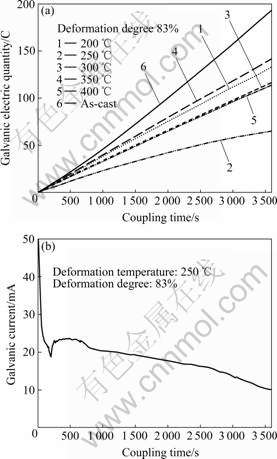
Fig.2 Coupling-time dependent galvanic electric quantity(a) and coupling-time dependent galvanic current(b) of AZ80 deformed at 250 ?C and 83% deformation degree
3.2 Microstructures of plastically deformed AZ80 alloys
Many investigations show that the corrosion of magnesium alloy is affected by their microstructures, such as the shape and size of grains, and the dispersion of phases[13]. The better corrosion resistance of die-casting AZ91D compared with mould AZ91 is due to the finer grains in die-casting alloys[10].
The as-cast AZ80 consists of a primary α-Mg matrix and continuous eutectic micro-constituents, i.e., a continuous fine lamellar (α+β) eutectics plus coarse β particles arranged net-like along and adjacent to the α-Mg grain boundary (Fig.3). After plastic deformation, the grain sizes are much finer and structures are much homogenous.
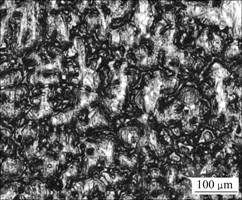
Fig.3 Microstructure of as-cast AZ80 alloy
At low deformation temperature (200-250 ?C), intermetallic β particles (Mgl7All2) are broken directly and scattered among the matrix, without solving in the α-matrix. So, there are lots of second phases (Mgl7All2) at lower deformed temperature, which is approved by the high mechanical properties of deformed AZ80 alloys[7]. The grain size of AZ80 alloy deformed at 200 ?C is still large, because recrystallization does not occur yet. When being deformed at 250 ?C, at lower deformation degree of 50%, the microstructure is similar to that of the as-cast alloy. With deformation degree increasing to 75%, recrystallization begins and deformed and recrystallized grains coexist in the structure. Full crystallization becomes possible under the deformation degree of 83%, where the grain size is much fine and β particles are homogeneously distributed along the α-Mg grain boundary. If the deformation degree is increased to 90%, there is not enough time for crystallization to complete and many non-recrystallized grains appear again, even more local rheological microstructure can be observed (Fig.4). Local rheology is found in microstructure of homogenized ZM21 alloy deformed at 300-500 ?C with strain rate higher than 1 s-1[14].
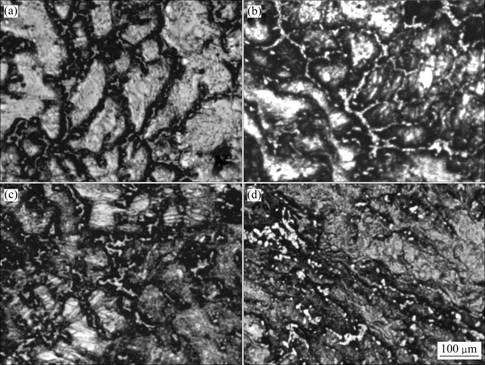
Fig.4 Microstructures of AZ80 alloys plastically deformed at 250 ?C with deformation degree of 50%(a), 75%(b), 83%(c) and 90%(d)
When deformation temperature is between 300 ?C and 350 ?C, the structure is nonuniform and local rheology co-exists at the same time. At 400 ?C, recrystallization becomes complete and the volume fraction of new grains increases. Although the size of recrystallization grain is significantly increased, the grains are entirely homogeneously equiaxed. At the same time, a large number of fine β particles (Mg17A112) continuously distribute along the α-Mg grain boundary (Fig.5).
3.3 Corrosion mechanism of plastic deformed AZ80 alloys
Because of the segregation of phase in the tissue, micro-cells are formed due to the different corrosion potentials in different parts of the magnesium alloy, which cause the rapid oxidation of the place with relatively low corrosion potential. Compared with α-Mg (corrosion potential of -1.6 V), β-phase (corrosion potential of -1.3 V) is the cathode, and this will cause the corrosion of α-Mg. Oppositely, cathodic reaction occurs mainly in β-phase and the corrosion rate of β-phase is relatively low. So, β phase has different effects on the corrosion behavior of AZ80 magnesium alloy. On one hand, β phase may act as galvanic cathode to accelerate the corrosion of α phase; On the other hand, β phase can be a barrier to prevent the corrosion of
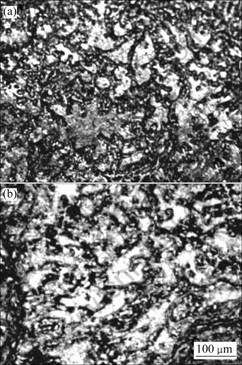
Fig.5 Microstructures of AZ80 alloys plastically deformed at 400 ?C with deformation degree of 50%(a) and 83%(b)
AZ80[15]. The galvanic tests show that, with increase of coupling time, the electronic quantity increment increases for as-cast AZ80 and decreases for plastically deformed AZ80, specially for sample deformed with deformation degree of 83% (Fig.2). These imply that β phases are galvanic cathodes in as-cast AZ80 and barriers in deformed AZ80, that is, β phases accelerate the corrosion rate of as-cast AZ80 and prevent the corrosion of deformed AZ80. Moreover, the degree to decrease the corrosion rate is higher in deformed AZ80 with homogenous structure than in deformed alloy with nonuniform structure (see sections 3.1 and 3.2).
In this work, the area ratio of β phase to α-Mg in sample deformed at 250 ?C with deformation degree of 83% reaches to 25%, which makes the sample have the best corrosion resistance. If area of β phase is much small, the protection surface cannot form and the corrosion resistance will be high. While if the area of β phase is much large, more than 40%, as in the AZ80 alloy deformed at 300 ?C and 350 ?C, the continuous β phase will be broken by the strain induced by mismatch, and the corrosion rate will be increased.
In as-cast AZ80, grain size is large and β phase acts as galvanic cathode to accelerate the corrosion rate of α-phase. With increasing the corrosion time, the area ratio of cathode (β phase) to anode (α-phase) in the galvanic corrosion surface is increased, which will further accelerate the corrosion rate and make β-phases fall down away the alloy, so new α grains are exposed to the corrosive environment and corroded. This process is repeated until all the members are damaged completely, as shown in Fig.6. On the contrary, after deformation, the grain is refined and quite lots of β particles distribute continuously along the grain boundary. In this case, β phase particles cannot be easily destroyed and, with the increase of corrosion time, the quantity of β phases in the exposed surface will increase and finally play the role of corrosion barrier. Although there are some grains of α phase still being corroded, most of the remaining α phase grains are protected under the β phase barrier, so the corrosion rate is decreased, as shown in Fig.7.
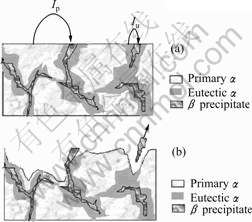
Fig.6 Corrosion process of as-cast AZ80: (a) Before corrosion; (b) During corrosion
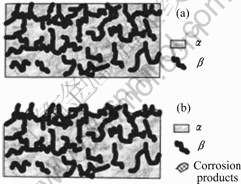
Fig.7 Corrosion process of plastically deformed AZ80: (a) Before corrosion; (b) During corrosion
Therefore, plastic deformation makes the grain refined and microstructure uniform. The increase of area ratio of β phase (Mg17A112) to α phase and continuous distribution of β phase in the exposed surface are contributed to the improvement of the corrosion resistance of AZ80.
4 Conclusions
1) Plastic deformation can refine the grain size and has positive effects on the improvement of corrosion resistance of AZ80 alloys, because α-Mg is protected under the coverage of continuously distributed β particles.
2) AZ80 alloy deformed at 250 ?C with the deformation of 83% has the best corrosion resistance, and the corrosion rate is only 33% that of the as-cast alloy.
3) When being deformed at 250 ?C, the corrosion rate of AZ80 magnesium alloy is dependent on the deformation degree. While at 400 ?C, the deformation degree has almost no effect on corrosion resistance.
References
[1] PARDO A, MERINO M C, COY A E, ARRABAL R, VIEJO F, MATYKINA E. Corrosion behaviour of magnesium/aluminium alloys in 3.5wt.% NaCl [J]. Corrosion Science, 2008, 50(3): 823-834.
[2] CHENG Ying-liang, QIN Ting-wei, WANG Hui-min, ZHANG Zhao. Comparison of corrosion behaviors of AZ31, AZ91, AM60 and ZK60 magnesium alloys [J]. Transactions of Nonferrous Metals Society of China, 2009, 19: 517-524.
[3] DUB? D, FISET M, COUTURE A, NAKATSUGAWA I. Characterization and performance of laser melted AZ91D and AM60B [J]. Mater Sci Eng A, 2001, 299(1/2): 38-45.
[4] SALMAN S A, ICHINO R, OKIDO M. Improvement of corrosion resistance of AZ31 Mg alloy by anodizing with co-precipitation of cerium oxide [J]. Transactions of Nonferrous Metals Society of China, 2009, 19: 883-886.
[5] LU Sheng, ZHOU Xiao-yan, CHEN Jing, HOU Zhi-dan. Corrosion and high-temperature oxidation of AM60 magnesium alloy [J]. Transactions of Nonferrous Metals Society of China, 2007, 17: s156-s160.
[6] SONG G L, ATRENS A. Corrosion mechanisms of magnesium alloys [J]. Advanced Engineering Materials, 1999, 1(1): 11-33.
[7] XU Hong-yan, WANG Qiang, ZHANG Zhi-min. Effect of thermal processing on microstructure and mechanical properties of AZ80 magnesium alloy [J]. Transactions of Nonferrous Metals Society of China, 2008, 18: s122-s126.
[8] SONG G L, ATRENS A, DARGUSCH M. Influence of microstructure on the corrosion of diecast AZ91D [J]. Corrosion Science, 1999, 41(2): 249-273.
[9] ZHANG Zhi-min, XU Hong-yan, WANG Qiang. Corrosion and mechanical properties of hot-extruded AZ31 magnesium alloys [J]. Transactions of Nonferrous Metals Society of China, 2008, 18: s140-s144.
[10] MATHIEU S, RAPIN C, HAZAN J, STEINMETZ P. Corrosion behaviour of high pressure die-cast and semi-solid cast AZ91D alloys [J]. Corrosion Science, 2002, 44(12): 2737-2756.
[11] HOCHE H, BLAWERT C, BROSZEIT E, BERGER C. Galvanic corrosion properties of differently PVD-treated magnesium die cast alloy AZ91 [J]. Surface and Coatings Technology, 2005, 193: 223-229.
[12] HE Wen-xiong, WANG Er-de, HU Lian-xi, YU Yang, SUN Hong-Fei. Effect of extrusion on microstructure and properties of a submicron crystalline Cu-5wt.%Cr alloy [J]. Journal of Materials Processing Technology, 2008, 208(1/3): 205-210.
[13] MATHIEU S, RAPIN C, HAZAN J, STEINMETZ P. Corrosion behaviour of high pressure die-cast and semi-solid cast AZ91D alloys [J]. Corrosion Science, 2002, 44(12): 2737-2756.
[14] ZHAO M C, LIU M, SONG G L, ANDREJ A. Influence of the β-phase morphology on the corrosion of the Mg alloy AZ91 [J]. Corrosion Science, 2008, 50(7): 1939-1953.
[15] SONG G L, ATRENS A, DARGUSCH M. Influence of microstructure on the corrosion of diecast AZ91D [J]. Corrosion Science, 1999, 41(2): 249-273.
(Edited by LIU Hua-sen)
Foundation item: Projects(50605059, 50735005) supported by the National Natural Science Foundation of China; Project(2008062) supported by Shanxi Province Foundation for Returness
Corresponding author: XU Hong-yan; Tel: +86-351-3557485; E-mail: xuhongyan@nuc.edu.cn