
J. Cent. South Univ. (2020) 27: 2220-2226
DOI: https://doi.org/10.1007/s11771-020-4443-6

Phase investigations of manganese–bismuth alloyed in a microwave furnace
Panita THONGJUMPA1, Thanida CHAROENSUK2, 3, Upsorn BOONYANG2, 4,Phimphaka HARDING2, 4, Chitnarong SIRISATHITKUL1, 2, 3
1. Division of Physics, School of Science, Walailak University, Nakhon Si Thammarat 80160, Thailand;
2. Functional Materials and Nanotechnology Center of Excellence, Walailak University,Nakhon Si Thammarat 80160, Thailand;
3. Thailand Center of Excellence in Physics, Ministry of Higher Education, Science,Research and Innovation, 328 Si Ayutthaya Road, Bangkok 10400, Thailand;
4. Division of Chemistry, School of Science, Walailak University, Nakhon Si Thammarat 80160, Thailand
Central South University Press and Springer-Verlag GmbH Germany, part of Springer Nature 2020
Abstract: Implementation of manganese–bismuth (MnBi) alloys as high-performance permanent magnets is a challenge for physicists and engineers because the ferromagnetic low-temperature phase (LTP) is not exclusively obtained. In this work, melting powered by four commercial magnetrons of 2000–2500 W in a microwave furnace is demonstrated as a new route to alloy MnBi. Under an argon atmosphere, microwave heating transferred to pieces of broken Bi ingots and Mn flakes for 2 h gave rise to products of inhomogeneous composition and morphology. Scanning electron micrographs were classified into three regions according to morphology and elemental composition. Cubic-like clusters characterized as Mn precipitated over light solidified Bi-rich regions, and the MnBi phase was formed in homogeneous regions with a balanced composition between Mn and Bi. A ferromagnetic hysteresis loop was obtained in the ground powder with a coercivity of 40 kA/m. Subsequent annealing at 553 K under a pressure of 414 kPa for 12 h enhanced the MnBi phase with extended regions of balanced composition. It follows that the coercivity was increased to 60 kA/m. However, remanent magnetization was slightly reduced. This MnBi alloyed by microwave radiation can be further used in rare-earth-free magnets.
Key words: microwave; manganese; bismuth; scanning electron microscopy; magnetic properties; coercivity
Cite this article as: Panita THONGJUMPA, Thanida CHAROENSUK, Upsorn BOONYANG, Phimphaka HARDING, Chitnarong SIRISATHITKUL. Phase investigations of manganese–bismuth alloyed in a microwave furnace [J]. Journal of Central South University, 2020, 27(8): 2220-2226. DOI: https://doi.org/10.1007/s11771-020-4443-6.
1 Introduction
Ferromagnetic low-temperature phase (LTP) manganese–bismuth (MnBi) exhibits substantial magnetocrystalline anisotropy and a positive temperature coefficient of coercivity. These magnetic properties coupled with a relatively high Curie temperature are desirable for permanent magnets at elevated temperatures. The goal of developing these rare-earth-free magnets is to provide an alternative to neodymium–iron–boron magnets with higher maximum energy products ((BH)max) than those of ferrites. Whereas substantial values of (BH)max are already achieved in laboratories [1-3], and the values are still less than half of the theoretical prediction in the MnBi at room temperature [4, 5]. Because of the vast difference between the melting points of Mn (1519 K) and Bi (544 K), the peritectic reaction to form the LTP MnBi is complicated. During the solidification process, Mn tends to segregate from the MnBi liquid [6-9]. Therefore, it is difficult to obtain the high purity LTP MnBi phase during the alloying process.
Because common techniques cannot directly synthesize LTP MnBi, arc-melting [1, 3, 9-11] and melt-spinning [2, 12-14] are employed to initiate the alloying and are followed by the annealing treatment to enhance the LTP MnBi [3, 9, 12-15]. Experimental conditions have been varied to promote this ferromagnetic phase. The quenching rate during the solidification affecting Mn grains in the microstructure significantly influences the MnBi formation [14]. The ball-milling technique successfully reduces the MnBi grain size, hence increasing the coercivity [1, 2, 10, 11]. In addition, the magnetic separation of the LTP MnBi phase from other non-magnetic phases [2] and the magnetic field applied during the annealing process [16] were suggested to enhance the magnetic properties. The doping of MnBi by Al and Cu increased the coercivity but tended to reduce the magnetization [17]. Different structures, such as MnBi films, were also prepared by the sputtering technique [18]. In addition to the hysteresis loops of MnBi-based alloys, anisotropic magnetoresistance was reported as well [19].
This work reports a new alloying technique powered by microwave. Microwave has increasingly been used in the synthesis of magnetic materials because the energy in the process can be optimized and efficiently used [20]. However, there are no reports on microwave synthesis of MnBi in the literature. Because the microwave is unable to heat metals directly, the power generated by four commercial magnetrons was transferred to melt Mn and Bi via a silicon carbide (SiC) plate and an alumina (Al2O3) crucible. The products then received further heat treatments that are commonly applied to MnBi magnets to enhance their magnetic properties [9, 15].
2 Experimental
A microwave furnace was developed for metal melting with a maximum temperature of 1573 K. The cavity of 0.28 m×0.28 m×0.28 m was made from stainless steel-304 sheets. The furnace was evacuated by a rotary pump and filled with argon to minimize oxidation. Microwaves of 2450 MHz were generated from four commercial magnetrons of 1000 W each and supplied to the cavity through waveguides installed on its four sides. To synthesize the alloy, a Mn:Bi atomic ratio of 2:1 was employed to compensate for the slow diffusion of Mn in forming MnBi [5, 21]. Mn flakes (99.9%) and Bi ingots (99.99%) were broken into small pieces, and then put in an Al2O3 crucible. The crucible was then placed on a SiC plate at the center of the microwave cavity. Under an argon atmosphere, microwave heating at approximately 2000-2500 W radiation was transferred from the SiC plate eventually to pieces of Mn and Bi inside the crucible. SiC was chosen based on its heat conversion from microwave absorption [22]. The samples were prepared using a heating time of 2 h, with a maximum temperature above the melting point of Mn of approximately 1520 K.
The obtained alloys were coarsely ground, and then annealed at 553 K under a pressure of 414 kPa for 12 h. With closer contact by high pressure application for an extended period of time, the LTP MnBi was increased by the diffusion of Mn into Bi at elevated temperature. After the pressing– annealing, the products were ground into powders for characterization. Differential thermal analysis (DTA) was scanned using a DTA7 (PerkinElmer) at the rate of 5 K/min. Phases of the products were characterized by SuperNova single crystal X-ray diffractometer in micro powder mode with a Cu microfocus X-ray source and a HyPix 3000 detector. Crystallite size (d) was calculated from the peak width using the Scherrer formula [23]:
(1)
where b is the broadening of the diffraction line measured at half maximum intensity and l is the wavelength of Kα.
To examine the morphology and elemental compositions, field-emission scanning electron microscope (FESEM: Zeiss Merlin Compact) and energy-dispersive X-ray spectroscope (EDS: Oxford Aztec connected Zeiss Merlin Compact) were respectively used. In addition, the magnetic properties were measured by vibrating sample magnetometer (VSM) in a sweeping ± 1200 kA/m magnetic field. The coercivity was the x-intercept of hysteresis loops and the magnetic squareness was estimated from the ratio of magnetization in a zero field (remanent magnetization) to that in a 1200-kA/m field.
3 Results and discussion
In Figure 1, the diffraction pattern before (a) and after (b) the annealing are compared. The sample exhibits mixed phases of hexagonal MnBi, cubic Mn and rhombohedral Bi. The strongest peak is indexed to Bi at 27.2°(012) and other peaks corresponding to Bi are located at 22.5°(003), 39.6°(110), 45.9°(006), 46.7°(021), 48.7°(202), 56.0°(024), 62.2°(116), and 64.5°(122) (ICSD Reference: 01-085-1329). The strongest MnBi peak is revealed at 28.1°(101) and minor peaks are at 23.9°(100), 29.2°(002), 38.0°(102), 42.1°(110), 51.2°(103), 51.4°(201), 52.1°(112), 58.1°(202), and 68.6°(211) (NIST Reference: 03-065-8164). After annealing at 553 K, the diffraction peaks located at the comparable positions exhibit an even greater intensity of the MnBi phase. The crystallite sizes, calculated from the major MnBi peaks with the Scherrer formula, are respectively 22.5 and 23.1 nm before and after the annealing.
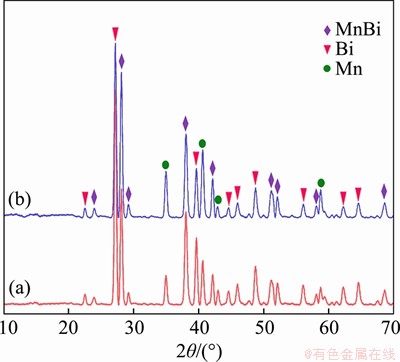
Figure 1 XRD patterns of products after alloying in microwave furnace for 2 h (red/bottom) (a) and subsequent annealing at 553 K for 12 h (blue/top) (b)
MnBi alloys, after heating for 2 h (a) and annealing for 12 h (b), can be classified into three regions according to their morphology, as shown in Figure 2, and elemental composition, as exemplified in Figure 3. Bulky cubic-like particles are the remaining Mn clusters, consistent with the characterization by XRD, and the lighter regions are the Bi [21]. Homogeneous regions among Mn- and Bi-rich particles are characterized as the MnBi phase. The dominant feature before annealing is cubic-like Mn particles of 4-5 μm embedded in lighter Bi-rich regions. After annealing, the surfaces are more homogeneous. Figure 3 shows the EDS spectra, which confirm regional compositions corresponding to Mn, Bi, and MnBi with a balanced composition. Areas with a balanced composition between Mn and Bi are increasingly observed after the annealing. In addition, it is notable that some Mn-rich regions, shown in Figure 3(a), contain high amounts of O. Despite its absence from XRD patterns, the MnO phase is likely present and was previously detected in MnBi alloys by the X-ray absorption [24].
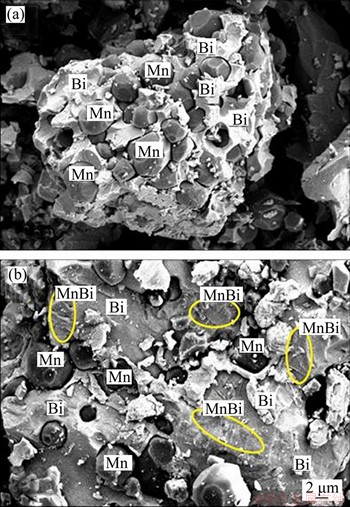
Figure 2 FESEM images of products after alloying in microwave furnace for 2 h (a) and subsequent annealing at 553 K for 12 h (b)
Although the Mn and Bi are subjected to temperatures beyond their melting points for up to 2 h in the microwave furnace, the single phase with homogeneous morphology is not yet obtained. The morphology can be more homogeneous if the starting materials are in the form of fine powders [24], but this method is not cost-effective for large scale production. Moreover, the Mn–Bi phase diagram suggests that the formation of high- temperature phase (HTP) MnBi due to a peritectic reaction occurs at 719 K upon cooling [6]. The following peritectic reaction below 628 K is so slow that it is difficult for the LTP MnBi to form. The HTP MnBi transforms to the LTP MnBi with some precipitated Mn below 613 K, and the LTP MnBi reverts to the HTP MnBi above 628 K upon heating. In addition to the difficulty in LTP MnBi formation, the eutectic reaction between MnBi and Bi results in a Bi-rich liquid. After heating for 2 h, Mn likely segregates from the solidified liquid upon cooling as evident in Figure 2(a) before annealing.
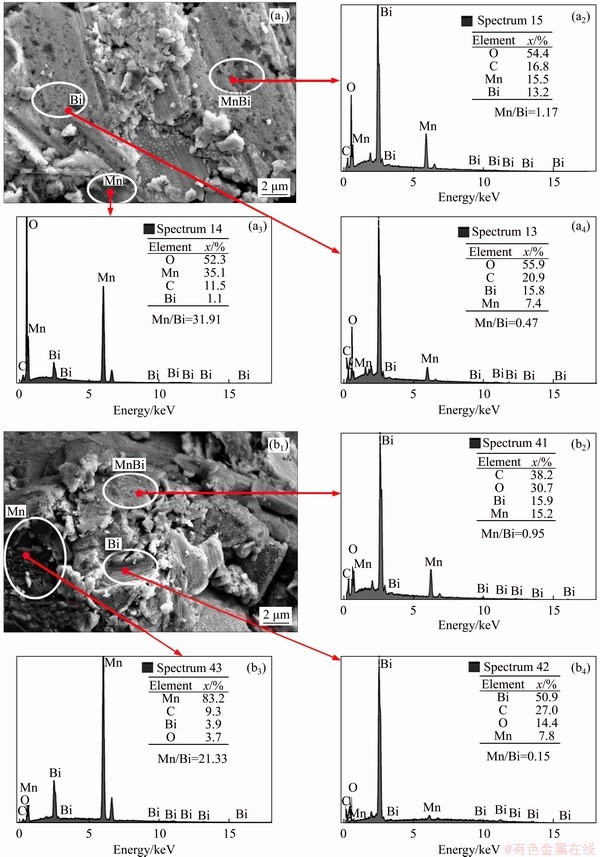
Figure 3 EDS spectra of selected areas on surface after alloying in microwave furnace for 2 h (a) and subsequent annealing at 553 K for 12 h (b)
The formation of LTP MnBi is dependent on several factors, including the composition and heating condition. A higher fraction of Mn in the starting materials is used to compensate for the loss of Mn during the process. In addition to the heating time and temperature, the heating rate also affects LTP formation. By comparing the differential scanning calorimetry (DSC) of different heating rates, XIANG et al [5] demonstrated that an endothermic transition was shifted from 545 to 567 K as the heating rate was raised from 5 to 40 K/min. By using the heating and cooling rates from 5 to 50 K/min, FANG et al [25] showed that the transition between LTP and the high temperature phase (HTP) was reversible. Interestingly, the microwave heating in this work attained a rate exceeding 50 K/min. The DTA of this MnBi alloyed by microwave heating, shown in Figure 4, is consistent with DSC curves in the literature. With a scanning rate of 5 K/min, endothermic transitions at 480, 545 and 620 K correspond to the removal of water from the structure, Bi melting, and LTP formation, respectively [25, 26]. In addition to the endothermic transitions, a broad exothermic peak around 1172 K due to the crystallization of MnBi is predominantly observed.
According to hysteresis loops in Figure 5, the alloying gives rise to the LTP MnBi with ferromagnetic properties. The magnetization for (a) is as high as 20 A·m2/kg when the saturation is reached in a1200-kA/m field. After annealing for 12 h, the coercivity for (b) is increased from 40 to 60 kA/m, which is in accordance with the enhanced MnBi phase in the XRD pattern. However, the magnetization is not saturated in 1200 kA/m, and the remanent magnetization is slightly reduced from 8.7 to 7.9 A·m2/kg. Thus, the magnetic squareness is decreased from 0.45 to 0.35 as a result of annealing.
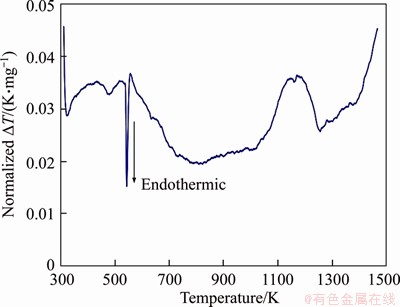
Figure 4 DTA curve of product after alloying in microwave furnace for 2 h
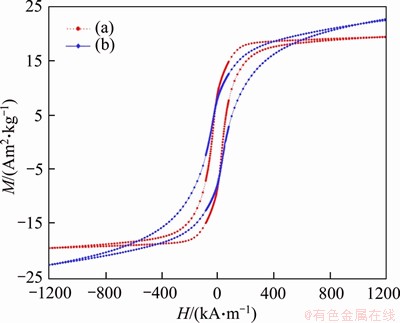
Figure 5 M-H curves of products after alloying in microwave furnace for 2 h (red/dash/round) (a) and subsequent annealing at 553 K for 12 h (blue/solid/ square) (b)
In the mixed MnBi, Mn- and Bi-rich phases,the magnetization is attributed to the LTP MnBi. Reduction in magnetization often indicates surface oxidation and decomposition of the LTP MnBi [27, 28]. KIM et al [2] suggested that stress and heat applied during the process lead to the thermal decomposition of the LTP MnBi. Although the remanent magnetization, shown in Figure 5, is indeed decreased, the saturation magnetization tends to increase. This suggests that the LTP MnBi is not decomposed under this pressing–annealing condition. Furthermore, the increase in coercivity indicates that the grain size is not enhanced at 553 K. The tradeoff between coercivity and remanent magnetization observed in Figure 5 is due to the intergranular exchange interaction [29]. With a decrease in exchange length after the annealing– pressing, the coercivity is increased but the remanent magnetization is decreased. Overall the magnetic properties of the annealed sample are still inferior to those reported in REfs. [3, 9, 12-15]. Nevertheless, this is the first report on the microwave alloying of LTP MnBi, and the magnetic properties can further be improved by subsequent magnetic separation and particle refinement [2, 30]. The compaction in the magnetic field also promotes a highly textured alignment resulting in both the increased coercivity and remanent magnetization desirable for permanent magnets [1, 31].
4 Conclusions
The reaction of Mn and Bi at an atomic ratio of 2:1 under microwave radiation at 2000-2500 W under an argon atmosphere yields MnBi phase alloys. By heating for 2 h, the as-synthesized alloy shows ferromagnetic properties with a coercivity of 40 kA/m and magnetization up to 20 A·m2/kg. The as-synthesized alloys were subsequently annealed at 553 K under a pressure of 414 Pa for 12 h to enhance the LTP MnBi, and the coercivity was increased to 60 kA/m as a result. However, the remanent magnetization was slightly reduced from 8.7 to 7.9 A·m2/kg after the annealing.
Acknowledgements
This work is financially supported by Thailand Center of Excellence in Physics (Grant No. ThEP-60-PIP-WU3). It is partially supported by the New Strategic Research (P2P) project, Walailak University, Thailand. The authors would like to thank P. JANTARATANA and D. SRINUAM for facility supports and P. SAETANG for assistance. P. HARDING thanks the National Science Technology and Innovation Policy Office for Integrated Research and Innovation Plan (Grant No. 256113A3050001) for XRD services.
References
[1] POUDYAL N, LIU X, WANG W, NGUYEN V V, MA Y, GANDHA K, ELKINS K, LIU J P, SUN K, KRAMER M J, CUI J. Processing of MnBi bulk magnets with enhanced energy product [J]. AIP Advances, 2016, 6: 056004. DOI: 10.1063/1.4942955.
[2] KIM S, MOON H, JUNG H, KIM S M, LEE H S, CHOI-YIM H, LEE W. Magnetic properties of large-scaled MnBi bulk magnets [J]. Journal of Alloys and Compounds, 2017, 708: 1245-1249. DOI: 10.1016/j.jallcom.2017.03.067.
[3] NGUYEN V V, NGUYEN T X. Effect of microstructures on the performance of rare-earth-free MnBi magnetic materials and magnets [J]. Physica B, 2018, 532: 103-107. DOI: 10.1016/j.physb.2017.06.018.
[4] PARK J, HONG Y K, LEE J, LEE W, KIM S G, CHOI C J. Electronic structure and maximum energy product of MnBi [J]. Metals, 2014, 4(3): 455-464. DOI: 10.3390/met4030455.
[5] XIANG Z, WANG T, MA S, QIAN L, LUO Z, SONG Y, YANG H, LU W. Microstructural evolution and phase transformation kinetics of MnBi alloys [J]. Journal of Alloys and Compounds, 2018, 741: 951-956. DOI: 10.1016/ j.jallcom.2018.01.147.
[6] CUI J, KRAMER M, ZHOU L, LIU F, GABAY A, HADJIPANAYIS G, BALASUBRAMANIAN B, SELLMYER D. Current progress and future challenges in rare-earth-free permanent magnets [J]. Acta Materialia, 2018, 158: 118-137. DOI:10.1016/j.actamat.2018.07.049.
[7] JANOTOVA I, SVEC P, SVEC P, MATKO I, JANICKOVIC D, KUNCA B, MARCIN J, SKORVANEK I. Formation of magnetic phases in rapidly quenched Mn-based systems [J]. Journal of Alloys and Compounds, 2018, 749: 128-133. DOI: 10.1016/j.jallcom.2018.03.208.
[8] MARKER M C J, TERZIEFF P, KAINZBAUER P, BOBNAR M, RICHTER K W, IPSER H. BiMn: Synthesis, separation by centrifugation, and characterization [J]. Journal of Alloys and Compounds, 2018, 741: 682-688. DOI: 10.1016/j.jallcom.2018.01.235.
[9] CUI J, CHOI J P, POLIKARPOV E, BOWDEN M E, XIE W, LI G, NIE Z, ZARKEVICH N, KRAMER M J, JOHNSON D. Effect of composition and heat treatment on MnBi magnetic materials [J]. Acta Materialia, 2014, 79: 374-381. DOI: 10.1016/j.actamat.2014.07.034.
[10] KANARI K, SARAFIDIS C, GJOKA M, NIARCHOS D, KALOGIROU O. Processing of magnetically anisotropic MnBi particles by surfactant assisted ball milling [J]. Journal of Magnetism and Magnetic Materials, 2017, 426: 691-697. DOI: 10.1016/j.jmmm.2016.10.141.
[11] LI B, MA Y, SHAO B, LI C, CHEN D, SUN J, ZHENG Q, YIN X. Preparation and magnetic properties of anisotropic MnBi powders [J]. Physica B, 2018, 530: 322-326. DOI: 10.1016/j.physb.2017.11.085.
[12] GABAY A M, HADJIPANAYIS G C, CUI J. Preparation of highly pure α-MnBi phase via melt-spinning [J]. AIP Advances, 2018, 8: 056702. DOI: 10.1063/1.5006491.
[13] SAITO T, NISHIMURA R, NISHIO-HAMANE D. Magnetic properties of Mn-Bi melt-spun ribbons [J]. Journal of Magnetism and Magnetic Materials, 2014, 349: 9-14. DOI: 10.1016/j.jmmm.2013.08.031.
[14] NGUYEN V V, NGUYEN T X. An approach for preparing high-performance MnBi alloys and magnets [J]. Journal of Electronic Materials, 2017, 46(6): 3333-3340. DOI: 10.1007/s11664-017-5409-9.
[15] XIE W, POLIKARPOV E, CHOI J P, BOWDEN M E, SUN K, CUI J. Effect of ball milling and heat treatment process on MnBi powders magnetic properties [J]. Journal of Alloys and Compounds, 2016, 680: 1-5. DOI: 10.1016/j.jallcom.2016. 04.097.
[16] MIYAZAKI D, MITSUI Y, UMETSU R Y, TAKAHASHI K, UDA S, KOYAMA K. Enhancement of the phase formation rate during in-field solid-phase reactive sintering of Mn-Bi [J]. Materials Transactions, 2017, 58(5): 720-723. DOI: 10.2320/matertrans.mbw201609.
[17] RAMAKRISHNA V V, KAVITA S, GAUTAM R, RAMESH T, GOPALAN R. Investigation of structural and magnetic properties of Al and Cu doped MnBi alloy [J]. Journal of Magnetism and Magnetic Materials, 2018, 458: 23-29. DOI: 10.1016/j.jmmm.2018.02.076J.
[18] CESPEDES E, VILLANUEVA M, NAVIO C, MOMPEAN F J, GARCIA-HERNANDEZ M, INCHAUSTI A, PEDRAZ P, OSORIO M R, CAMARERO J, BOLLERO A. High coercive LTP-MnBi for high temperature applications: From isolated particles to film-like structures [J]. Journal of Alloys and Compounds, 2017, 729: 1156-1164. DOI: 10.1016/ j.jallcom.2017.09.234.
[19] TEREKHOV А V, SOLOVJOV A L, PROKHVATILOV A I, MELESHKO V V, ZOLOCHEVSKII I V, CWIK J, LOS A, SHEVCHENKO A D, IVASISHIN O M, KOVALYUK Z D. Anomalous anisotropic magnetoresistance and magnetization in Mn3.69Bi95.69Fe0.62 [J]. East European Journal of Physics, 2017, 4(4): 12-17. DOI: 10.26565/2312-4334-2017-4-02.
[20] LIU B G, YU Y T, PENG J H, SRINIVASAKANNAN C, ZHANG L B, GUO S H. Preparation of microsized hematite powder from ferrous sulfate via microwave calcination [J]. Journal of Central South University, 2017, 24(8): 1720-1726. DOI: 10.1007/s11771-017-3579-5.
[21] NGUYEN T X, NGUYEN V V. Fabrication of MnBi alloys with high ferromagnetic phase content: Effects of heat treatment regimes and dopants [J]. Journal of Materials Science: Materials in Electronics, 2019, 30: 6888-6894. DOI: 10.1007/s10854-019-01003-x.
[22] KAUSHAL S, GUPTA D, BHOWMICK H. On development and wear behavior of microwave processed functionally graded Ni-SiC clads on SS-304 substrate [J]. Journal of Materials Engineering and Performance, 2018, 27(2): 777-786. DOI: 10.1007/s11665-017-3110-z.
[23] VOROKH A S. Scherrer formula: Estimation of error in determining small nanoparticle size [J]. Nanosystems: Physics, Chemistry, Mathematics, 2018, 9(3): 364-369. DOI: 10.17586/2220-8054-2018-9-3-364-369.
[24] SIRISATHITKUL C, CHAROENSUK T. Effects of composition and heat treatment on manganese-bismuth magnets [J]. Micro & Nano Letters, 2019, 14(6): 661-664. DOI: 10.1049/mnl.2018.5227.
[25] FANG H L, LI J H, SHAFEIE S, HEDLUND D, CEDERVALL J, EKSTROM F, GOMEZ C S, BEDNARCIK J, SVEDLINDH P, GUNNARSSON K, SAHLBERG M. Insights into phase transitions and magnetism of MnBi crystals synthesized from self-flux [J]. Journal of Alloys and Compounds, 2019, 781: 308-314. DOI: 10.1016/j.jallcom. 2018.12.146.
[26] ANAND K, CHRISTOPHER N, SINGH N. Evaluation of structural and magnetic property of Cr-doped MnBi permanent magnet material [J]. Applied Physics A, 2019, 125: 870. DOI: 10.1007/s00339-019-3156-x.
[27] MOON K W, JEON K W, KANG M, KANG M K, BYUN Y, KIM J B, KIM H, KIM J. Synthesis and magnetic properties of MnBi(LTP) magnets with high-energy product [J]. IEEE Transactions on Magnetics, 2014, 50: 2103804. DOI: 10.1109/TMAG.2014.2329555.
[28] CHEN Y, SAWATZKI S, ENER S, SEPEHRI-AMIN H, LEINEWEBER A, GREGORI G, QU F, MURALIDHAR S, OHKUBO T, HONO K, GUTFLEISCH O, KRONMULLER H, SCHUTZ G, GOERING E. On the synthesis and microstructure analysis of high permanence MnBi [J]. AIP Advances, 2016, 6: 125301. DOI: 10.1063/1.4971759.
[29] LEWIS L H, CREW D C. The coercivity-remanence tradeoff in nanocrystalline permanent magnets [J]. Materials Research Society Symposia Proceedings, 2002, 703: 565-369. DOI: 10.1557/proc-703-u2.8.
[30] ZHANG W, BALASUBRAMANIAN B, KHAREL P, PAHARI R, VALLOPPILLY S R, LI X Z, YUE L P, SKOMSKI R, SELLMYER D J. High energy product of MnBi by field annealing and Sn alloying [J]. APL Materials, 2019, 7: 121111. DOI: 10.1063/1.5128659.
[31] QIAN H D, PARK J H, LIM J T, YANG Y, SI P Z, KIM J W, CHOI C J, CHO K M. Magnetic properties of MnBi bulk magnets with NaCl and C addition [J]. AIP Advances, 2019, 9: 115213. DOI: 10.1063/1.5122677.
(Edited by YANG Hua)
中文导读
微波辐射法制备锰铋合金
摘要:得到高性能永磁体锰铋(MnBi)合金对物理学家和工程师来说是一个挑战,因为纯的铁磁低温相(LTP)不容易获得。在本工作中,在微波炉中由四个2000~2500 W的商用磁控管驱动的熔化被证明是一种新的合成MnBi的路线。在氩气气氛下,微波加热碎Bi锭和Mn片2 h,得到成分和形貌不均匀的产物。按形貌和元素组成将扫描电子显微照片分为三个区域。立方团簇状的Mn沉淀在明亮的富铋固化区,MnBi相在Mn与Bi组分平衡、均匀的区域形成。在矫顽力为40 kA/m的磨碎粉末中存在铁磁磁滞回线。随后在414 kPa、553 K下退火12 h,MnBi相得到扩展,矫顽力提高到60 kA/m,但残余磁化强度略有降低。微波辐射法得到的MnBi合金可用于无稀土磁体。
关键词:微波;锰;铋;扫描电镜;磁性能;矫顽力
Foundation item: Project(ThEP-60-PIP-WU3) supported by the Thailand Center of Excellence in Physics
Received date: 2019-11-15; Accepted date: 2020-06-20
Corresponding author: Chitnarong SIRISATHITKUL, PhD, Associate Professor; Tel: +66-75672939; E-mail: schitnar@wu.ac.th; ORCID: https://orcid.org/0000-0002-7837-3515