J. Cent. South Univ. Technol. (2009) 16: 0444-0450
DOI: 10.1007/s11771-009-0075-6

Feasibility analysis for monitoring fatigue crack in
hydraulic turbine blades using acoustic emission technique
WANG Xiang-hong(王向红)1, ZHU Chang-ming(朱昌明)1, MAO Han-ling(毛汉领)2, HUANG Zhen-feng(黄振峰)3
(1. School of Mechanical Engineering, Shanghai Jiaotong University, Shanghai 200030, China;
2. Guangxi Radio and Television University, Nanning 530004, China;
3. School of Mechanical Engineering, Guangxi University, Nanning 530004, China)
Abstract: In order to investigate the feasibility of monitoring the fatigue cracks in turbine blades using acoustic emission (AE) technique, the AE characteristics of fatigue crack growth were studied in the laboratory. And the characteristics were compared with those of background noise received from a real hydraulic turbine unit. It is found that the AE parameters such as the energy and duration can qualitatively describe the fatigue state of the blades. The correlations of crack propagation rates and acoustic emission count rates vs stress intensity factor (SIF) range are also obtained. At the same time, for the specimens of 20SiMn under the given testing conditions, it is noted that the rise time and duration of events emitted from the fatigue process are lower than those from the background noise; amplitude range is 49-74 dB, which is lower than that of the noise (90-99 dB); frequency range of main energy of crack signals is higher than 60 kHz while that in the noise is lower than 55 kHz. Thus, it is possible to extract the useful crack signals from the noise through appropriate signal processing methods and to represent the crack status of blade materials by AE parameters. As a result, it is feasible to monitor the safety of runners using AE technique.
Key words: fatigue; crack; acoustic emission; hydraulic turbine; blade
1 Introduction
Francis turbine runners take on an important task to convert water energy to mechanical energy. And cracks happen on the turbine blades frequently and easily. FISHER [1] indicated that most of the regular cracks were fatigue cracks when blades were subjected to vibratory alternate stress. The existence of cracks seriously endangers the operating stability and safety of power stations, so it is necessary to monitor the initiation of cracks and to master the developing trend of the cracks.
All the time, researchers have been looking for methods to solve the problem of blade cracks. Trials were used to solve it initially, but the method had a long periodicity and high cost. It was studied by numerical method later [2]. At present, researchers focus on the investigation of dynamic behaviors of hydraulic turbine runners [3-4]. That is, at the stage of design or after accident emerging, a finite element software is used to simulate running states of runners. However, all these methods are not active. Although researchers had done a large number of studies in the aspects of design and manufacture, the crack problem of Francis turbine runners could not be solved magnificently. In recent years, studies on health monitoring of turbine runners
primarily have been focused on cavitation monitoring and diagnosis [5]. As far as the authors are aware, there is little work on cracks monitoring of Francis turbine runner blades.
The conventional non-destructive testing (NDT) methods, such as ultrasonic testing, radiographic testing and penetrant testing, are active testing methods, which are used to detect the pre-existent defects. They are not suitable for monitoring developing cracks and defects in material. Acoustic emission (AE), developed over four decades as a passive non-destructive evaluation technique, is a highly sensitive technique for detecting active microscopic events in a material and structure, as well as crack initiation and propagation. Furthermore, improvements in AE test technique permit reliable AE measurements and continuous monitoring under cyclic loading. The AE technique has been widely used to inspect and monitor defect formation, fatigue crack growth and failures in structural materials and components [6-11]. However, many studies of crack signals were only done in the laboratory. Few researches were combined with background noise on site.
This is a pre-requisite study on using AE technique to monitor the fatigue cracks of turbine runner blades. The AE characteristics of fatigue cracks in the blade
material were recognized in the laboratory. Then the characteristics were compared with those received from background noise on site.
2 Experimental
2.1 Preparation of specimen
Hydraulic pressure produces bending stress on the blades when runners operate under stable state [3]. Crack signals of a blade material from three-point bending fatigue tests were received. The material generally used for blades, 20SiMn steel, was chosen. Table 1 lists the chemical composition and the mechanical properties of the steel. Three-point bending (SENB) specimens were machined according to the ASTM standard E647 [12], i.e., Length(S)×width(W)×height(B)=240 mm×60 mm×20 mm. Their crack plane orientation was L-T (where L is the direction of principal deformation (maximum grain flow), T is the direction of least deformation). Fig.1 shows the specimen dimensions, where a is the crack length, A is the length of the specimen, and d is the distance between the two sensors. The specimens were pre-cracked by electric spark line cutting.
Table 1 Composition and mechanical properties of 20SiMn steel
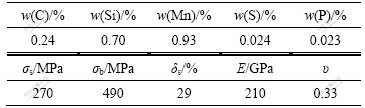
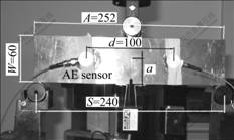
Fig.1 Dimension of SENB specimen and layout of AE sensor (Unit: mm)
2.2 Instrument
All specimens were tested in a load-controlled mode of an Instron 8801 servohydraulic test machine at room temperature. The crack length was measured using the compliance method by a crack opening displacement (COD) gauge. The experimental setup is shown in Fig.2. The AE parameters and waveforms were recorded via Physical Acoustics Corporation SAMOS system. Two SR150 AE sensors (50-400 kHz) and two model 2/4/6 pre-amplifiers (10 kHz-2 MHz) were used. In addition, the interface between the AE sensors and the specimens was filled with vaseline as a couplant. The sensor locations are shown in Fig.1.
2.3 Experimental procedure and measurement
The values of the AE test parameters chosen for the experiments are summarized in Table 2. The threshold of 42 dB in the fatigue tests was selected, which was just
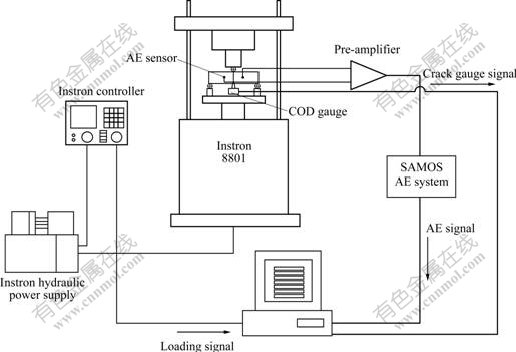
Fig.2 Sketch of three-point bending fatigue testing with AE system
Table 2 AE test parameters
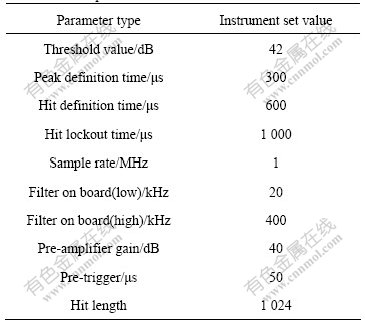
above the background noise level determined using a dummy specimen without a slot when the hydraulic power supply was turned on. The COD gauge was mounted on the bolt-on knife-edge attachments that were bonded to the surface of the notch before the tests (see Fig.1). In order to accelerate the occurrence of cracks, a load slightly larger than the maximum fatigue load was used to the specimens in a descending mode before the fatigue test according to the standard ASTM E647. As a result, the pre-crack included two parts: the crack produced by electric spark line cutting and fatigue loading. Table 3 lists the pre-crack length for each specimen at which the experimental data begin to be collected. The specimens were subjected to cyclic tension-tension loading in the sinusoidal wave shape with the stress ratio of 0.1. In order to reduce the testing time, the loading frequency was set to 10 Hz as it had little effect on fatigue crack growth [4]. Signal conditioning was performed by the preamplifiers. The conditioning signal was fed to the main data acquisition board. The loading process was terminated when the crack length reached 45 mm. The AE parameters, waveforms and the crack length were stored during testing process. Then all the data were processed by a computer.
3 Results and discussion
3.1 Fatigue behavior study using classical fracture mechanics approach
In the elastic fracture mechanics, the SIF and crack growth rate can be approximated by the Paris-Erdogan equation:
where n is the number of fatigue cycles, a is the crack length, ?K is the applied SIF range, and C and m are assumed to be constants for a given material. The SIF range ?K for the SENB specimen is given as [12]:
(2)
where ?P=Pmax-Pmin is the applied load range, W and B are the width and the thickness of the test specimen, S is the span and

(3)
The testing results of the first specimen SENB1 are used to explain the fatigue crack growth of the 20SiMn steel. The increment of the crack length of specimen SENB1 is plotted in Fig.3. It is observed that the crack length increases sharply after 1.75×10-5 cycles. The crack growth rate exceeds 1×10-6 m/cycle at this point and quickly increases in succession. For the ductile metal materials, the SIF range of crack transited from region II (middle crack growth rate) to region III (high crack growth rate) is determined according to the empirical equation
. For 20SiMn steel,
Table 3 Fatigue test parameters and fit coefficients
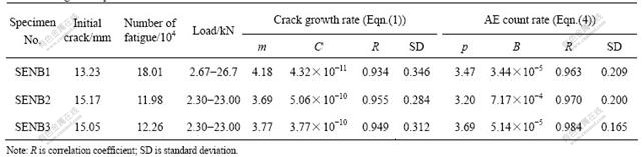
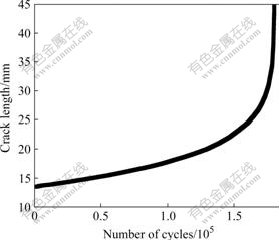
Fig.3 Plot of crack length against loading cycles for specimen SENB1
?KT is about 48 MPa?m0.5. And the SIF range is 50 MPa?m0.5 at 1.75×105 cycles in the test. Therefore, the test comes into the transition period from region II to region III after 1.75×105 loading. At the same time, the fracture surface becomes rougher and rougher with the increment of the crack length (see Fig.4).
The correlation between the SIF and crack growth rate is shown in Fig.5. It is observed that the dispersivity of the experimental data is minor besides the initial stage of cyclic loading due to the effects of the initial state of the system and the cyclic softening of the material. It is an approximately linear relationship between lg(da/dn)
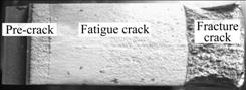
Fig.4 Fracture surface for specimen SENB1
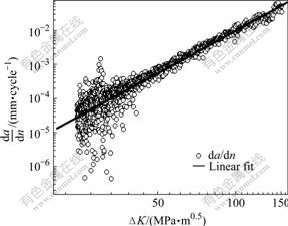
Fig.5 Correlation of crack growth rate vs SIF range and associated linear fit for specimen SENB1
and lg?K, which is coincided with Eqn.(1). The fit coefficients are listed in Table 3.
3.2 Fatigue behavior characterization using AE parameters
Some researches indicated that AE parameters such as count had a correlation with the SIF [13-14]. Following Eqn.(1), a similar correlation between AE count rate and SIF range is formulated:
(4)
where N is the total AE count (number of times the AE signal amplitude exceeds a threshold value), B and p are the parameters related to the material properties.
A plot of the cumulative number of counts against cycles for specimen SENB1 is shown in Fig.6. Similarly, the cumulative number of counts increases sharply after 1.75×105 cycles due to the crack growth rate gradually transiting to the rapid region.
The correlation of the duration vs energy is shown in Fig.7, which indicates that the duration is proportional
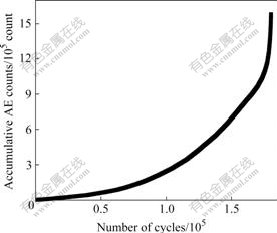
Fig.6 Cumulative number of counts during three-point bend fatigue test for specimen SENB1
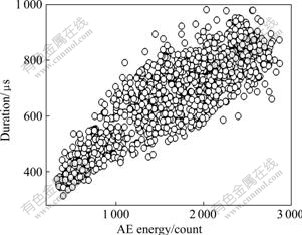
Fig.7 Correlation of AE energy vs duration
to the energy because the duration reflects the releasing mode of energy [15]. And the correlation can be used to monitor the onset of failure. Events with evidently higher durations and energies may predict failure approached. For specimen SENB1, the failure initiates while the duration is above 840 μs and the energy is above 2 500 counts.
The correlation between the count rate and SIF range is shown in Fig.8. Just like Fig.5, the dispersivity of the experimental data is minor besides the initial stage of cyclic loading. They are also a linear relationship in logarithmic coordinate (fit coefficients see Table 3), which is consistent with Eqn.(4).
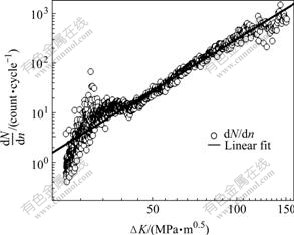
Fig.8 Correlation of AE count rate vs SIF range and associated linear fit for specimen SENB1
The fatigue testing parameters and the fit coefficients of the three specimens are summarized in Table 3. It shows that the longer the pre-crack, the shorter the number of the loading cycles in a given load. For the 20SiMn steel, under bending load with the stress ratio of 0.1, coefficient m (3.6-4.2) is basically coincided with that in Ref.[11]. Coefficient p is between 3.2 and 3.7. As a result, the fatigue life of structures can be predicted according to the results.
3.3 AE characteristics of background noise on site and fatigue crack signals
The background noise was received from No.1 turbine unit of some power plant (see Fig.9). The operational conditions included: the rated speed was 75 r/min, the operating power was 302.5 MW and the water head was 55 m. The AE testing parameter setup was the same with that in the fatigue tests.
The AE characteristics of the fatigue crack signals and the background noise are listed in Table 4. It shows that the values of the AE parameters of the two kinds of signals are very different. The rise time and duration of the crack signals are shorter than those of the background
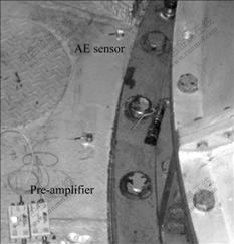
Fig.9 Receiving background noise on site
noise. The amplitude is between 49 dB and 74 dB, which is lower than that in the background noise (90-99 dB). The peak frequency is above 80 kHz while it is below 60 kHz in the noise.
Table 4 AE parameter characteristics of fatigue crack signals and background noise
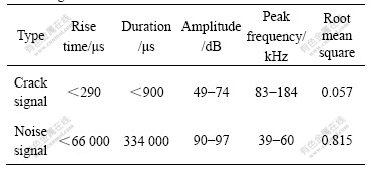
The waveforms and the corresponding spectrograms of both the crack signals and the background noise are shown in Fig.10. The maximum amplitude of the noise is 1.5 V, which is greater than that of the metal crack signal, 0.3 V. The energy of the background noise is mainly concentrated on 30-55 kHz while it is concentrated on 60-150 kHz for the crack signal.
Both the AE parameters and the waveforms indicate the difference of the two kinds of signals, which is due to different mechanisms of the signals produced. The AE source of the ductile blade material is very weak [16], so the amplitude is low. Furthermore, the frequency range of AE signals of metal materials is 100-500 kHz [17]. However, the background noise is made up of periodic vibration signals of turbine units, which has a longer duration and rise time and a lower frequency range. As a result, it is possible to extract the useful crack signals through suitable signal processing methods because of different values of the AE parameters of the two kinds of signals.
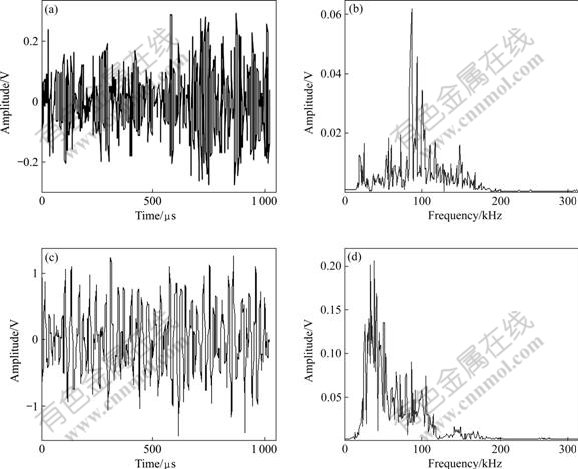
Fig.10 Waveforms and FFT spectra: (a) Time domain of fatigue AE signal; (b) Frequency domain of fatigue AE signal; (c) Time domain of background noise; (d) Frequency domain of background noise
4 Conclusions
(1) AE parameters and fatigue cracks have coincidence relations. The AE energy and duration are useful parameters to embody the blade failure. The failure initiates while the duration is above 840 μs and the energy is above 2 500 counts in the tests for 20SiMn steel under the given testing conditions.
(2) The correlations of the crack growth rates and AE count rates vs the SIF range are obtained. The fatigue life can be predicted by the correlations.
(3) The values of the AE parameters of fatigue crack signals and background noise are very different because of different producing mechanisms. The background noise is continuous vibration signal, which has longer duration and rise time, lower frequency range and higher amplitude. As a result, the two kinds of signals can be distinguished by the AE parameter filtration and the extraction of the crack signals with the low signal-to-noise ratio.
(4) The AE characteristics obtained in the fatigue tests provide a reference for the security evaluation and lifetime prediction of real hydraulic runners using AE technique. Although the results cannot be directly used in the non-destructive inspection of real structures, they may nevertheless be helpful for gaining a general understanding of the AE characteristics of blade fatigue process and the affecting factors.
Acknowledgements
The authors wish to express their gratitude to the Institute of Electricity Experiment and Yantan Water Power Plant, Guangxi Province, for their assistance in undertaking this investigation.
References
[1] FISHER D. The cause of runner crack and the solutions implement for the Xiaolangdi Hydroelectric project [C]// Proceedings of the XXIst IAHR symposium on Hydraulic Machinery and Systems. Lausanne: IAHR, 2002: 9-12.
[2] MASSE B, PAGE M, MAGNAN R, GIROUX A M. Numerical simulations: A tool to improve performance of hydraulic turbines [C]// Waterpower. Las Vegas: ASCE, 1999: 1-10.
[3] CARPINTERI A, BRIGHENTI R, HUTH H J, VANTADORI S. Fatigue growth of a surface crack in a welded T-joint [J]. International Journal of Fatigue, 2005, 27(1): 59-69.
[4] HUTH H J. Fatigue design of hydraulic turbine runners [D]. Trondheim: Norwegian University of Science and Technology, 2005: 61-72.
[5] ESCALER X, EGUSQUIZA E, FARHAT M, AVELLAN F, COUSSIRAT M. Detection of cavitation in hydraulic turbines [J]. Mechanical Systems and Signal Processing, 2006, 20(4): 983-1007.
[6] ENNACEUR C, LAKSIMI A, HERVE C, CHERFAOUI M. Monitoring crack growth in pressure vessel steels by the acoustic emission technique and the method of potential difference [J]. International Journal of Pressure Vessels and Piping, 2006, 83(3): 197-204.
[7] MBA D, HALL L D. The transmission of acoustic emission across large-scale turbine rotors [J]. NDT & E International, 2002, 35(8): 529-539.
[8] HUANG Song-ling, LI Lu-ming, SHI Ke-ren, WANG Xiao-feng. Magnetic field properties caused by stress concentration [J]. Journal of Central South University of Technology, 2004, 11(1): 23-26.
[9] ZHANG Ping, XU Jian-guang, LI Ning. Fatigue properties analysis of cracked rock based on fracture evolution process [J]. Journal of Central South University of Technology, 2008, 15(1): 95-99.
[10] ZHANG Guo-qing, SU Bing, PU Geng-qiang, WANG Chen-tao. Fatigue properties of 48MnV steel with twin arc apraying 3Cr13 coatings [J]. Journal of Central South University of Technology, 2005, 12(S2): 112-118.
[11] YU Sheng-fu, WANG Tie-qi, YANG Qi-liang, SHEN Man-de. Fracture toughness and fatigue crack growth rate of 20MnSi steel [J]. Materials for Mechanical Engineering, 2005, 29(6): 17-19. (in Chinese)
[12] ASTM E647-00: Standard test method for measurement of fatigue crack growth rates [S]. 2000.
[13] GONG Z, DUQUESNAY D L, MCBRIDE S L. Measurement and interpretation of fatigue crack growth in 7075 aluminum alloy using acoustic emission monitoring [J]. Journal of Testing and Evaluation, 1998, 26(6): 567-574.
[14] ROBERTS T M, TALEBZADEH M. Acoustic emission monitoring of fatigue crack propagation [J]. Journal of Constructional Steel Research, 2003, 59(6): 695-712.
[15] ROQUES A, BROWNE M, THOMPSON J, ROWLAND C, TAYLOR A. Investigation of fatigue crack growth in acrylic bone cement using the acoustic emission technique [J]. Biomaterials, 2004, 25(5): 769-778.
[16] MOORTHY V, JAYAKUMAR T, RAJ B. Influence of micro structure on acoustic emission behavior during stage 2 fatigue crack growth in solution annealed, thermally aged and weld specimens of AISI type 316 stainless steel [J]. Materials Science and Engineering A, 1996, A212(2): 273-280.
[17] LADEMO O G, HOPPERSTAD O S, LANGSETH M. An evaluation of yield criteria and flow rules for aluminium alloys [J]. International Journal of Plasticity, 1999, 15(2): 191-208.
(Edited by YANG You-ping)
Foundation item: Project(50465002) supported by the National Natural Science Foundation of China
Received date: 2008-08-26; Accepted date: 2008-11-08
Corresponding author: WANG Xiang-hong, PhD; Tel: +86-21-62932641-810; E-mail: wangxianghong2000@gmail.com