Trans. Nonferrous Met. Soc. China 22(2012) s845-s850
Mathematical model determination for improvement of surface roughness in magnetic-assisted abrasive polishing of nonferrous AISI316 material
Jae-Seob KWAK
Department of Mechanical Engineering, Pukyong National University, San 100, Yongdang-Dong, Nam-Gu, Busan 608-739, Korea
Received 21 May 2012; accepted 21 September 2012
Abstract:The new magnetic-assisted abrasive polishing process for non-ferrous materials was proposed in order to increase the magnetic flux density which directly influences the contact force between the workpiece and the abrasives. The permanent magnets were installed under the workpiece and their effects were verified by the experiments. The effect of polishing factors on the improvement of surface roughness was evaluated based on the Taguchi experimental method, and the optimal conditions for polishing AISI316 stainless steel were determined. The predicting model for improving surface roughness was developed and the validity of the developed model was tested. The results show that the permanent magnets are very useful in improving the surface roughness in the magnetic-assisted abrasive polishing process.
Key words: nonferrous metals; surface analysis; magnetic-assisted abrasive polishing process; contact force
1 Introduction
An abrasive polishing process assisted by a magnetic field, called magnetic-assisted abrasive polishing, has been proposed to produce a high finish surface, and unconstrained abrasives remove materials under the presence of a magnetic field [1-3]. This process can be employed to precisely finish most mechanical parts, since the magnetic-assisted abrasive polishing process possesses many attractive advantages, such as lower machining force, self-adaptability to a complicated workpiece profile, and easy controllability of cutting edges. In addition, the polishing tool requires neither compensation nor dressing process because abrasives that float over the workpiece are not restricted with a formal shape, as in other conventional machining processes. From these features, the magnetic-assisted abrasive polishing can reduce process time and reduce production costs.
In past years, a lot of research on magnetic-assisted abrasive polishing for ferrous and non-ferrous materials was carried out [4,5]. From the previous studies for cases of nonferrous materials such as a stainless steel, it is seen that the effectiveness of magnetic-assisted abrasive polishing is much lower than for ferrous materials [6]. The reason for these phenomena is that the magnetic-assisted abrasive polishing basically works with the help of the magnetic force, but the magnetic force decreases in the case of nonferrous materials. The lower magnetic force leads to lower contact forces between the workpiece and abrasives. The efficiency of the magnetic -assisted abrasive polishing also decreases. Thus, further study is necessary in order to additionally increase the magnetic force (or contact force) for nonferrous materials.
As one alternative solution, in this study, permanent magnets were installed under the workpiece to increase the contact force by improving the magnetic flux density of non-magnetic materials (AISI316 stainless steel) during the magnetic-assisted abrasive polishing process. The effect of the permanent magnets on the magnetic flux density and the surface roughness were verified. The optimal conditions for producing the better surface roughness were determined and a surface roughness predicting model was established.
2 Magnetic-assisted abrasive polishing
The working principle of magnetic-assisted abrasive polishing is shown in Fig. 1. The polishing system has a coil of wires wrapped around a steel rod called an inductor. This coil of wires is the main part of the magnetic-assisted abrasive polishing system to produce magnetic properties. According to Faraday’s Laws, a magnetic force is generated between the inductor and the workpiece when a direct current is supplied to the coil.
Usually small magnetic particles and abrasives are mixed up for making magnetic abrasives for magnetic-assisted abrasive polishing. These mixed particles sprinkled on the workpiece in advance are attracted to the inductor along lines of magnetic force. The particles attached to the inductor freely form a flexible abrasive brush, which is a machining tool in the magnetic-assisted abrasive polishing process.
The relative movement between the workpiece and abrasive occurs while the inductor rotates. Due to the lower force applied toward the workpiece in the magnetic-assisted abrasive polishing, a small amount of material was removed and a precise surface could be obtained by this process [7,8].
In the magnetic-assisted abrasive polishing process, a contact force between a workpiece and abrasives is closely related to the normal force toward the workpiece. The normal force (Fn) acting on the workpiece in a magnetic field is basically given as follows [9]:
(1)
where V and H represent the volume of working abrasives and the magnetic field strength, respectively.
is the gradient of the magnetic flux density and y is the direction of the magnetic field.
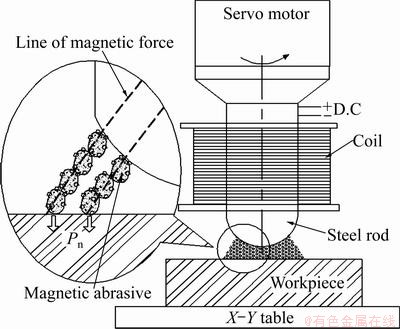
Fig. 1 Working principle of magnetic abrasive polishing
As shown in Fig. 1, the normal force can be represented as a term of an abrasive pressure (pn) toward the workpiece as follows:
(2)
where A is the contact area over the workpiece, N is the number of simultaneous working abrasives, pn represents the pressure of an individual working abrasive. The pressure toward the workpiece is represented as below [10]:
(3)
where B is the magnetic flux density,
is the permeability in vacuum, μb is the specific permeability of the magnetic brush. The contact force (Fc) which causes the abrasives penetrating into the workpiece can be represented as follows:
(4)
where
is the friction coefficient between the workpiece and the abrasive and fn is the normal force of an individual working abrasive. From Eq. (2) to Eq. (4), it is known that the magnetic flux density directly affects the contact force, and the contact force increases according to the increase of the magnetic flux density. As previously mentioned, it is necessary to increase the contact force for the polishing of non-ferrous materials because most nonferrous materials have a lower magnetic flux density [11].
In this study, to increase the contact force for polishing AISI316 stainless steel, which is a non-ferrous material, permanent magnets of NdBFe were installed on the opposite side of the polishing surface as the AISI316 stainless steel. The magnetic flux density and the surface roughness were evaluated by both conventional and proposed methods.
Figure 2(a) shows the measuring method and results for the magnetic density flux of the workpiece. The magnetic flux density of five points within the inductor diameter was tested using a thin probe type of a Gauss meter. As shown in Fig. 2(b), the maximum magnetic flux density without permanent magnets is about 135 mT, but with five permanent magnets it is about 190 mT. If more permanent magnets were installed, the magnetic density flux would increase further.
Figure 3 shows the measured surface roughness according to the polishing time to verify the effects of permanent magnets in the magnetic-assisted abrasive polishing of nonferrous materials. On the whole, better surface roughness with permanent magnets is obtained, and also improves dramatically after a polishing time of 10 min. The steady surface roughness settles after a polishing time of 20 min. From the experimental verifications, it is seen that what installs the permanent magnet for polishing of the non-ferrous materials is fundamentally very effective.
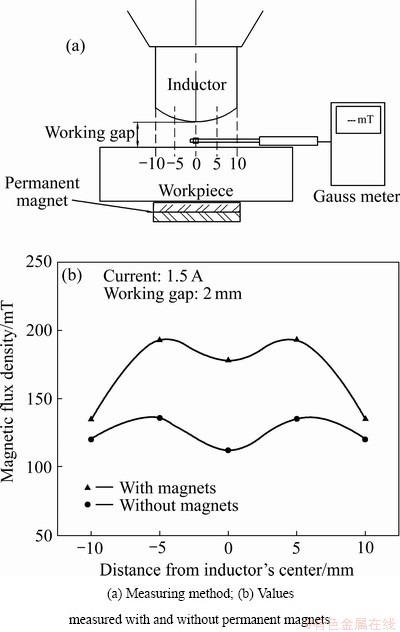
Fig. 2 Magnetic flux density
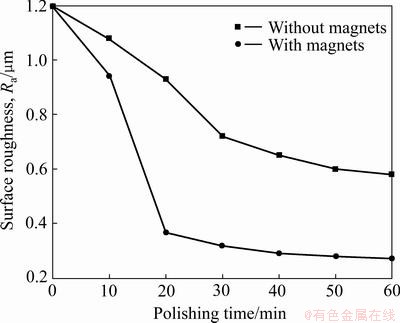
Fig. 3 Experimental results for surface roughness produced with and without permanent magnets
3 Experimentation with Taguchi method
Figure 4 shows the schematic diagram of the experimental set-up for the magnetic-assisted abrasive polishing, and Table 1 lists the fixed polishing conditions used in this study. The workpiece was AISI316 stainless steel which is a nonferrous material and needed to increase the magnetic flux density. Permanent magnets were installed underneath the polishing surface of the workpiece to improve magnetic force during the magnetic-assisted abrasive polishing.
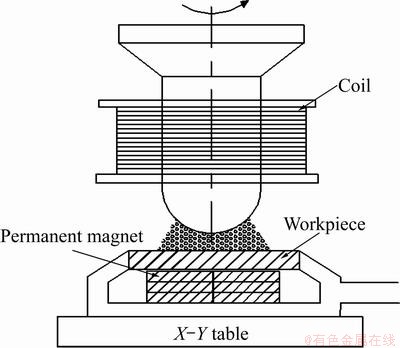
Fig. 4 Schematic diagram of magnetic-assisted abrasive polishing system
Table 1 Fixed experimental conditions
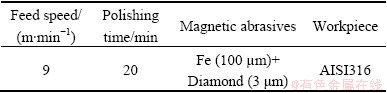
The feed speed was 9 m/min for the experiments. The polishing time was set at 20 min. Diamond abrasives of about 3 μm mixed with Fe particles of 100 μm in a diameter were used as magnetic abrasives.
The design of the experiments provides means how to efficiently perform experimentation to evaluate the effect of the process factors on the outcomes of the process. The Taguchi method is a popular experimental design method and its dominant advantage is to remarkably reduce the number of experiments by the use of an orthogonal array. A loss function used in the Taguchi method has been defined to gauge the deviation between the experimental and desired outcome of a performance characteristic. The loss function is furtherly transformed into a signal-to-noise ratio (SNR, RSN). Three different categories of performance characteristics are usually used in the calculation of the SNR, such as the-lower-is-the-better, the-higher-is-the-better, and the- nominal-is-the-better.
In this study, the-higher-is-the-better characteristic was used, since the process outcome to be evaluated was the improvement of the surface roughness after the magnetic-assisted abrasive polishing. The loss function for the improvement of surface roughness is as follows:
(5)
where Lij is the loss function of the ith performance characteristic in the j th experiment and yij is the measured experimental result; n is the number of the experimentation. The corresponding RSN is given by
(6)
Using the calculated SNR, the effects of the process factors on the improvement of surface roughness by the magnetic-assisted abrasive polishing were evaluated. The selected polishing factors and their levels are listed in Table 2. All four factors, which are rotational speed of the inductor, magnetic flux density from permanent magnets, applied current to the inductor and working gap between the workpiece and the inductor, are changed at three levels. An orthogonal array table based on the Taguchi method was selected and applied to the experimental conditions for the magnetic-assisted abrasive polishing.
Table 2 Polishing factors and levels used in experiments
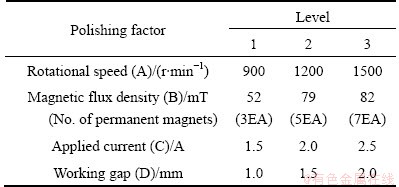
In this study, a stylus contact type of the surface roughness tester (SJ-301, Mitutoyo) was used for measuring the process effect after the magnetic abrasive polishing. To obtain more reliable experimental data, each surface roughness, which means that in this study an arithmetical mean deviation of the assessed surface profile was obtained in the central area of the workpiece at different three points and then it was arithmetically averaged. The reason to adopt this way is that the measured surface roughness values are a little difference according to a location and a trial of the measurement even though the same surface after polishing was tested.
4 Results and discussion
Experiments guided by Table 3 were conducted and then the surface roughness before and after the magnetic-assisted abrasive polishing was evaluated by the Taguchi method.
Table 4 lists experimental results and the calculated SNR. The workpiece surface of the AISI316 stainless steel before the magnetic-assisted abrasive polishing was ground and the average surface roughness is 0.4 μm. The initial ground surface roughness has a slight deviation because it is very difficult to produce the same surface roughness by the grinding process. After polishing 20 min, the surface roughness was improved in all experiments.
Table 5 lists the influence of the polishing factors on the improvement of the surface roughness after the magnetic-assisted abrasive polishing. It is seen that factor B of the magnetic flux density by the permanent magnets and factor D of the working gap have a dominant effect on the improvement of surface roughness. The applied current has no effect on the improvement of the surface roughness in this experimental range. This result means that the magnetic flux density by the permanent magnets can efficiently increase the magnetic force more than the applied current to the inductor.
Table 3 Orthogonal array table for experimentation
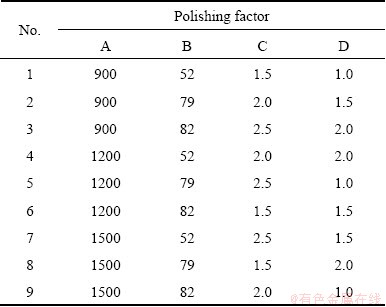
Table 4 Measured surface roughness and calculated SNR
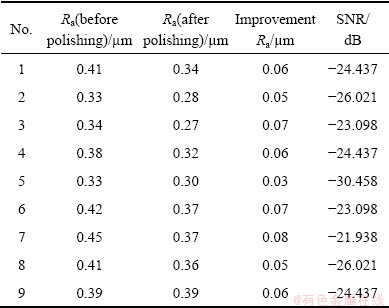
Table 5 Influence of polishing factors
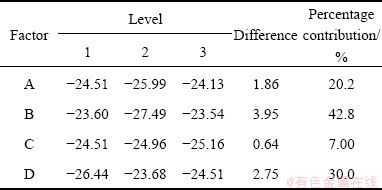
The main effect of the polishing factors on the surface roughness improvement after the magnetic- assisted abrasive polishing is shown in Fig. 5. In the Taguchi method, the higher SNR for the experimental results is desirable and the optimal conditions can be easily determined by selecting the combination of the maximal SNR in each factor. As shown in Fig. 5, the determined optimal conditions are a combination of A3B3C1D2 (rotational speed of 1500 r/min, magnetic flux density of 82 mT, applied current of 1.5 A and working gap of 1.5 mm, respectively). The optimal conditions were not tested in the previous experiments because the combination was not matched in Table 3. Table 6 presents the ANOVA (analysis of variance) table for the polishing factors to check significant factors.
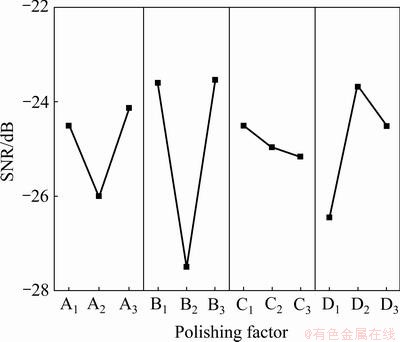
Fig.5 Analysis of main effect of polishing factors
Table 6 ANOVA for polishing factors
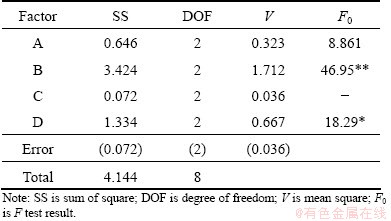
Based on the experimental results, a predicting model for the improvement of the surface roughness (RIS) by the magnetic-assisted abrasive polishing could be developed. In this study, the first-order mathematical model was assumed as
(7)
where
is the coefficient of the predicting model which should be determined in the mathematical model to predict the improvement of the surface roughness when the polishing factors such as the rotational speed (A), the magnetic flux density (B), the applied current (C), and the working gap (D) were properly selected.
Using the matrix approach and the experimental results listed in Table 4, the coefficients of the predicting model represented in the Eq. (7) can be determined and the developed predicting model for the improvement of surface roughness RIS is

(8)
Figure 6 shows the improvement of the surface roughness by the predicting model developed and the experimentation. Most predicted values are very similar to the experimental results.
To confirm the validity of the developed predicting model and to check the result of the optimal conditions, experiments were carried out. Table 7 shows the predicted and experimental results. The improvement of the surface roughness measured in experiments is about 0.11 μm and it coincides well with the predicted result of 0.10 μm from the developed model. Figure 7 shows some SEM images of the AISI316 stainless steel before and after the magnetic-assisted abrasive polishing. The grinding lines on the workpiece surface almost entirely disappear and a better surface is obtained after the magnetic-assisted abrasive polishing. This shows that the magnetic-assisted abrasive polishing process is very useful to improve the surface roughness of nonferrous AISI316 stainless steel.
Table 7 Confirmatory experiments
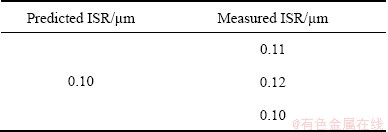
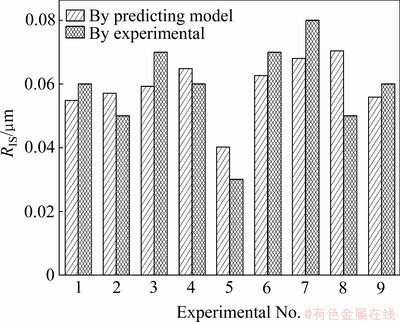
Fig.6 Comparison between predicted and experimental ISR
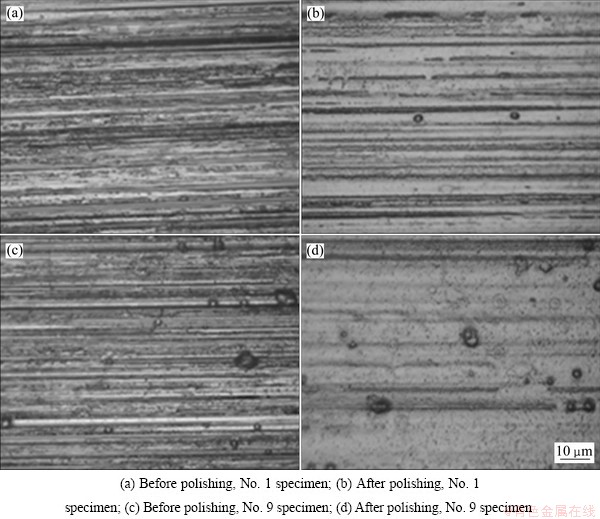
Fig.7 SEM images of AISI316 material before and after polishing
5 Conclusions
1) The proposed magnetic-assisted abrasive polishing installed with permanent magnets is very useful to increase the magnetic flux density of the AISI316 stainless steel.
2) Magnetic flux density given by the permanent magnets is the dominant polishing factor in the improvement of the surface roughness.
3) The optimal conditions for the improvement of the surface roughness are the rotational speed of 1500 r/min, the magnetic flux density of 82 mT, the applied current of 1.5 A and the working gap of 1.5 mm.
4) The predicting model for the improvement of the surface roughness is developed and the developed model is confirmed by the experiments.
References
[1] YIN S, SHINMURA T. A comparative study: Polishing characteristic and its mechanisms of three vibration modes in vibration-assisted magnetic abrasive polishing [J]. Int J Mach Tools Manuf, 2004, 44(4): 383-390.
[2] WANG A C, LEE S J. Study the characteristics of magnetic finishing with gel abrasive [J]. Int J Mach Tools Manuf, 2009, 49(14): 1063-1069.
[3] ZHANG L, ZHAO Y W, HE X S, KURIYAGAWA T. An investigation of effective area in electrorheological fluid-assisted polishing of tungsten carbide [J]. Int J Mach Tools Manuf, 2008, 48(3-4): 295-306.
[4] JAIN V K. Magnetic field assisted abrasive based micro-/nano- finishing [J]. J Mater Process Technol, 2009, 209(20): 6022-6038.
[5] SINGH D K, JAIN V K, RAGHURAM V. Parametric study of magnetic abrasive finishing process [J]. J Mater Process Technol, 2004, 149(1-3): 22-29.
[6] KWAK J S. Enhanced magnetic abrasive polishing of non-ferrous metals utilizing a permanent magnet [J]. Int J Mach Tools Manuf, 2009, 49(7-8): 613-618.
[7] SINGH D K, JAIN V K, RAGHURAM V, KOMANDURI R. Analysis of surface texture generated by a flexible magnetic abrasive brush [J]. Wear, 2005, 259(7-12): 1254-1261.
[8] JAIN V K, KUMAR P, BEHERA P K, JAYWAL S C. Effect of working gap and circumferential speed in the performance of magnetic abrasive finishing process [J]. Wear, 2001, 250(1-12): 384-390.
[9] YANG L D, LIN C T, CHOW H M. Optimization in MAF operations using Taguchi parameter design for AISI304 stainless steel [J]. Int J Adv Manuf Technol, 2009, 42(5-6): 595-605.
[10] KWAK J S. Application of Taguchi and response surface methodologies for geometric error in surface grinding process [J]. Int J Mach Tools Manuf, 2005, 45(3): 327-334.
[11] KIM S O, KWAK J S. Magnetic force improvement and parameter optimization for magnetic abrasive polishing of AZ31 magnesium alloy [J]. Transactions of Nonferrous Metals Society of China, 2008, 18(s1): 369-373.
(Edited by CHEN Can-hua)
Foundation item: Project (2011-0004048) supported by National Research Foundation of Korea (NRF) funded by the Ministry of Education, Science and Technology
Corresponding author: Jae-Seob KWAK; Tel: +82-51-629-6139; E-mail: jskwak5@pknu.ac.kr
DOI: 10.1016/S1003-6326(12)61814-7