Trans. Nonferrous Met. Soc. China 31(2021) 576-585
Novel high strength Al-10.5Si-3.4Cu-0.2Mg alloy produced through two-stage solution heat treatment
Mohsen ABDI, Saeed G. SHABESTARI
School of Metallurgy and Materials Engineering, Iran University of Science and Technology (IUST), Narmak, 16846, Tehran, Iran
Received 1 May 2020; accepted 28 October 2020
Abstract: Mechanical properties of aluminum-silicon-copper alloys are enhanced through precipitation hardening. The response of these alloys to age-hardening is very slow. To overcome this problem, 0.2, 0.4 and 0.7 wt.% magnesium were added to Al-10.5Si-3.4Cu alloy. The new alloys were subjected to two types of precipitation hardening processes different in the solutionizing stage. The results showed that the presence of various amounts of magnesium in the composition of this alloy accelerates the response to ageing treatments, increasing the hardness and strength. Higher mechanical properties can be achieved when the alloys were subjected to a two-stage solution heat treatment. It is found that Al-10.5Si-3.4Cu alloy containing 0.2 wt.% Mg treated through a two-stage solution process, has optimum properties with ultimate tensile strength of 383.9 MPa, yield strength of 289.7 MPa and elongation of 3.97%, and can be used as a substitute for a large number of aluminum castings which need high strength and excellent castability.
Key words: high strength alloy; AlSiCuMg alloy; two-stage solution heat treatment; precipitation hardening
1 Introduction
Aluminum-silicon alloys are the most important aluminum casting alloys, mainly because of their high fluidity, low shrinkage during casting, high corrosion resistance, good weld and solder ability and low coefficient of thermal expansion [1-3]. Aluminum-silicon alloys have many applications in automotive and aerospace industries. The main purpose of using these alloys in the automotive industries is vehicle weight reduction and decreasing the fuel consumption [1,2]. These alloys are ideally suited for manufacturing pistons and other major vehicle parts because of their exceptional castability, wear resistance and low expansion [2]. Thus, the structure and mechanical properties of aluminum-silicon alloys and, consequently their service performance, are primarily dependent on the composition design, manufacturing process and heat treatment [2,4]. Production of high quality and excellent mechanical properties aluminum-silicon alloys are possible with these two following procedures: (1) addition of alloying elements during melt production and melt treatment of the liquid alloy through grain refining and modification, and (2) applying a suitable heat treatment.
In recent years, aluminum-silicon-copper alloys with 7-10 wt.% Si and 2-4 wt.% Cu are very important in automotive industries [3,5-7]. Other alloying elements such as Fe, Mg, Mn and Zn are commonly used in these alloys [5,6]. The properties of these ternary alloys are between their component of Al-Si with good castability and Al-Cu with high mechanical properties [8]. Aluminum-silicon-copper alloys offer a combination of a high strength with an excellent castability, light weight and good machinability with regard to both permanent molds and sand castings [9,10]. Aluminum-silicon- copper alloys are seldom used in as-cast condition because they have poor mechanical properties in this condition. For this reason, a number of attempts are made to improve their mechanical properties including chemical treatment, solid solution hardening, and precipitation hardening [10].
The solution treatment of aluminum-silicon- copper alloys during heat treatment is very slow because: (1) The diffusion rate of Cu in Al matrix is low; (2) The maximum solution temperature in these alloys is low to prevent incipient melting of Cu-rich compounds [11,12].
The above-mentioned reasons prolong obtaining the maximum hardness during heat treatment. Mg, as an alloying element, even at low concentration, has a large influence on the age hardening response [11]. The morphology of eutectic Si also has an extremely large effect on mechanical properties of these alloys. The structural modification of Si particles may be obtained by these three methods [1]: (1) addition of chemical modifiers, (2) using high cooling rate, and (3) solution heat treatment.
380 commercial alloy is a kind of aluminum- silicon-copper alloys that has 9-10 wt.% Si and 3-4 wt.% copper with low amount of other alloying elements. In this work, the effects of different amounts of Mg element as well as two types of solution heat treatment on the microstructure and mechanical properties of A380.3 casting alloys were investigated.
2 Experimental
2.1 Alloying and casting
In this research, two stages of alloying were carried out. Firstly, 13 kg of A380.3 alloy was melted in a graphite crucible in an electrical resistance furnace and held at a temperature of (780±5) °C. The chemical composition of A380.3 alloy is given in Table 1. A suitable amount of pure silicon was added into the melt, and then it was uniformly dispersed using a steel bar coated with graphite to let the silicon to be dissolved completely. This was carried out to increase the amount of Si content of the alloy to the appropriate content.
Manganese was added into the melt using Al-75wt.%Mn master alloy. Mn is the most effective element to eliminate detrimental effect of impure iron in aluminum alloys [13-15]. Then, molten metal was poured into the steel permanent mold coated with graphite. The chemical composition of the alloy after the first stage of alloying is presented in Table 2.
Table 1 Chemical composition of A380.3 alloy (wt.%)

Table 2 Chemical composition of alloy after first stage of alloying (wt.%)

Secondly, the ingot was cut into four parts. In each pouring experiment, 3 kg of the ingot was melted in a graphite crucible in an electrical resistance furnace and held at a temperature of (720±5) °C. Degassing treatment was carried out using nitrogen base degasser, with the amount of 0.6 wt.% of the melt. It was inserted into the melt using a steel plunger, coated with graphite. After 5 min, Al-10wt.%Sr master alloy was added to increase the amount of Sr of the melt to 0.015 wt.%. To add magnesium in the range of 0-0.7wt.%, the appropriate amoumts of pure Mg was wrapped in aluminum foil and inserted into the melt. Table 3 shows the final composition of various alloys investigated.
Table 3 Chemical composition of new alloys after second stage of alloying (wt.%)
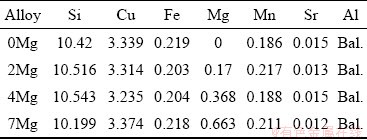
The molten metal of each alloy was poured into a preheated Y-block mold at (250±5) °C coated with graphite. The as-cast block is shown schematically in Fig. 1. To perform thermal analysis on the alloys, about 150 g of each melt was poured into a cylindrical steel mold preheated up to (250±5) °C. A K-type thermocouple was located in the center of the cylindrical mold. Temperature versus time was measured and data were transferred into a high-speed data acquisition system (A/D converter) linked to a notebook computer. In order to obtain reproducible results, the thermocouple was placed exactly at the same position in each experiment. Analog to digital convertor used in this work has a sensitive 16-bit convertor (resolution of 1/216 or 0.0015%), response time of 0.02 s, and high accuracy detection. In order to check the reproducibility and the accuracy, each test was repeated at least three times. The variations of temperature versus time were recorded with the frequency of 10 readings per second and plotted using Origin Pro. 9.0 software (Origin Lab Corporation, Northampton, MA). A complete explanation was reported elsewhere [16-18]. Computer-aided cooling curves (CA-CC) and their first derivative curves were plotted for each alloy.
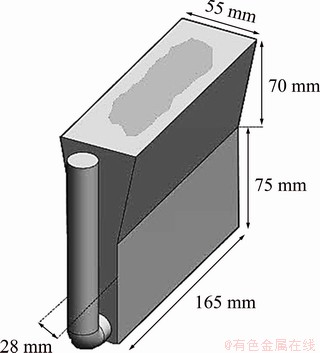
Fig. 1 Schematic of casting in Y-block mold
2.2 Heat treatment
Homogenizing heat treatment was performed on all as-cast alloys at 480 °C for 9 h. Their feeding part was cut off, and 26 samples were prepared from the main part of each block having dimension of 3 cm × 2 cm × 2 cm. Two types of solution heat treatment were applied to the samples. Firstly, 13 samples were solution-treated at 495 °C for 8 h. Secondly, the other 13 samples were solution- treated at 495 °C for 8 h, and then immediately heated to 515 °C for 2 h to perform the solution process perfectly. It is worth to mention that the samples were put into a steel basket for more convenient performing of the quenching experiment.
After solutionizing, the samples were water- quenched at 20 °C. Then, the samples were aged at 185 °C for different time. The hardness of the samples was measured as a function of ageing time. Each hardness value was the average of five hardness measurements for each condition.
2.3 Tensile test
Standard ASTM B 557 was used for the preparation of suitable tensile specimens. This standard is applicable for wrought and cast aluminum and magnesium alloys. Tensile test experiments were performed using Galdbini tensile apparatus controlled by a computer. Strain rate was 3 mm/min at ambient temperature during tensile test. The yield strength (YS) was calculated according to the standard 0.2% offset strain.
2.4 Metallography
The as-cast and heat-treated microstructure of the samples, containing different amounts of Mg, was investigated through standard metallographical methods. SEM-EDS analysis was performed on the samples to tentatively identify intermetallic compounds.
3 Results and discussion
3.1 Thermal analysis
Thermal analysis was performed to find the best solution temperature for all alloys containing different amounts of magnesium. In order to measure the solidification temperature of the last phase to solidify in the alloys, cooling curves and their first derivative curves were extracted. It has been reported that the solidification temperature of Cu-rich intermetallic phase is less than the formation temperatures of other phases [12]. The cooling curves and their first derivative curves of the alloys are shown in Fig. 2. The last solidification point was characterized on the cooling curves, and the exact temperature was specified using Origin Pro software.
The solidification temperature of the last phase, θ-Al2Cu, is presented for each alloy in Table 4. Accordingly, higher amount of Mg led to the lower formation temperature of the θ-Al2Cu phase. The minimum temperature of 510.2 °C was obtained where the alloy contained 0.7% Mg. This exhibits that the best temperature for solution treatment can be 15-20 °C higher than 495 °C, which is usually used for aluminum-silicon-copper alloys.
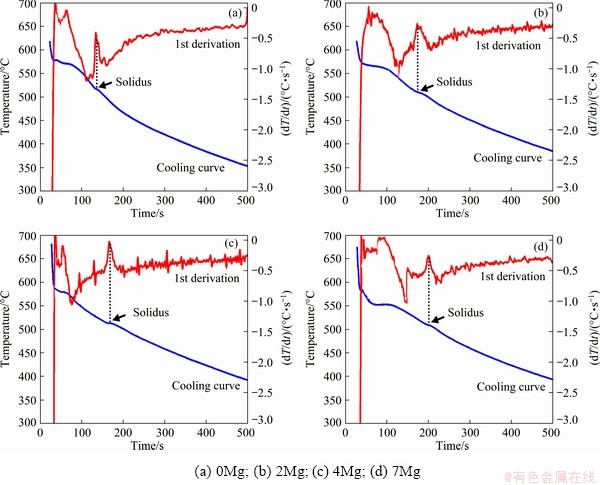
Fig. 2 Cooling curves and their first derivative curves of alloys (Arrow indicates instant of solidus)
Table 4 Solidification temperature of last phase θ-Al2Cu formed in alloys
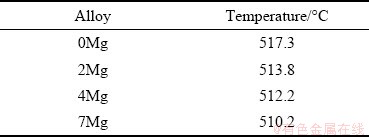
3.2 Microstructural characterization
Figure 3 shows the microstructures of the alloys with a single-stage solution treatment. The ageing process was not performed on the samples observed in Fig. 3. The microstructure consisted of α(Al) solid solution with light color as the matrix accompanied by eutectic Si particles with gray color. In addition to these phases, α-Al15(Fe,Mn)3Si2 intermetallics were also observed which were not affected during solution treatment. The morphology of this phase was not changed during heat treatment. Some coarse θ-Al2Cu phases were observed in the microstructure of the alloys after heat treatment with a single-stage solution treatment. Mechanical properties of the alloy was not as high as expected, because the distribution of fine precipitates after ageing process did not occur. It should be noted that the accumulation of θ-Al2Cu phases in the grain boundaries resulted in a decrease in elongation as well.
Figure 4 shows the microstructures of alloys with a two-stage solution heat treatment. They were observed immediately after quenching and before ageing process. The predominant structure of the alloys included α(Al) solid solution with light color as the matrix associated with eutectic Si particles with gray color. The coarse θ-Al2Cu phases completely dissolved during two-stage solution heat treatment. Therefore, their solid solution phase has a high degree of super saturation. Consequently, high amount of strengthening elements is available to develop fine precipitates during the ageing process. As a result, the response of the alloys to the ageing process is extremely improved.
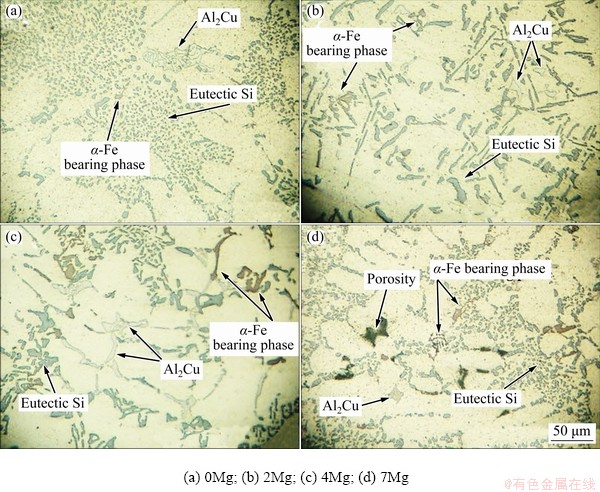
Fig. 3 Microstructures of alloys after single-stage solution treatment
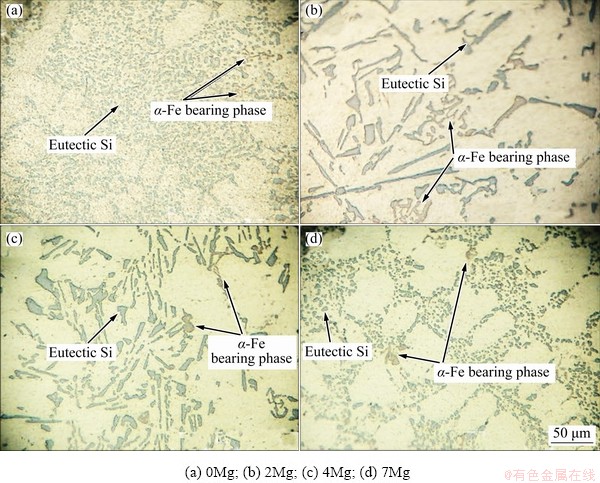
Fig. 4 Microstructures of alloys after two-stage solution treatment
3.3 Mechanical properties
Figure 5 shows the hardness of the alloys containing different amounts of Mg as a function of ageing time at ageing temperature of 185 °C under two types of solution heat treatment. As observed in this figure, the presence of Mg increased the hardness of Al-Si-Cu alloys, and the response of the alloys to ageing process was accelerated. According to the references [19,20], the presence of Mg in Al-Si-Cu casting alloys leads to the precipitation of Mg2Si, Al8Mg3FeSi6 and Al5Mg8Cu2Si6 intermetallics, which results in strengthening after precipitation heat treatment. The hardness of the alloy having no Mg was increased by about HB 10, where it experienced a single-stage solution treatment and then aged for 12 h at 185 °C. On the other hand, hardness of the alloy containing 0.2% Mg, was increased by about HB 35, where it experienced a single-stage solution treatment and then aged for 2 h at 185 °C.
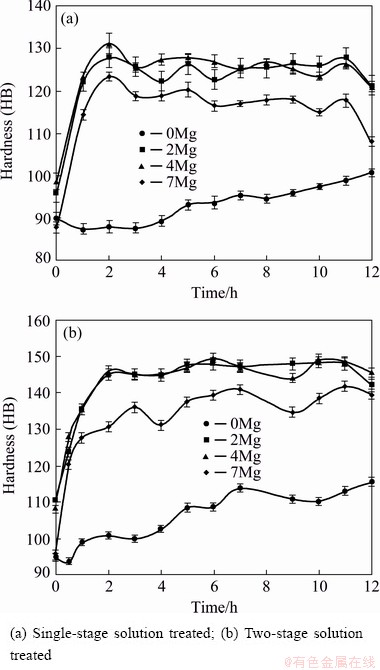
Fig. 5 Hardness as function of ageing time at 185 °C
Hardness of the alloy containing 0.7% Mg is less than that of the others. This is because of some porosities observed in alloy containing 0.7% Mg. According to EDWARDS et al [21], the impact of Mg on porosity formation in Al-Si-Cu casting alloys is not clear due to the desire of Mg to react with oxygen to form MgO. Macro-porosity (1-10 mm), which is mainly comprised of massive shrinkage cavities, occurs in long-freezing range alloys and addition of Mg promotes these kinds of porosities [22]. On the other hand, exceeding the Mg level in the alloy composition leads to the formation of much more low-melting-point Al5Mg8Cu2Si6 intermetallics, which are prone to incipient melting during solutionizing [9]. Porosity is the most important factor on the hardness of alloys [23-25]. It can also be observed that the hardness of the alloys subjected to a two-stage solution treatment is higher than that of the alloys treated through a single-stage solution treatment. For example, the maximum hardness of the alloy containing 0.2% Mg and single-stage solution treated, was HB 130, while by performing a two-stage solution treatment on the same alloy, the maximum hardness was increased to HB 150.
Figure 5 also shows that the rate of hardness promotion in the alloy containing no Mg and two-stage solution treated, was higher than that of the alloy subjected to a single-stage solution treatment. In other words, the hardness was increased by HB 20 after a two-stage solution treatment followed by 12 h ageing. However, in the case of performing a single-stage solution treatment and ageing for the same 12 h, the hardness was increased by only HB 10.
Table 5 presents the results of tensile test. Each datum is the average of five tensile test measurements. The alloy having no Mg and just homogenized, named 0MgH, is considered as the reference specimen. It is compared with the alloys containing various amounts of Mg experienced different solution treatments. Then, they were aged for the same ageing time of 5 h at ageing temperature of 185 °C. “H”, “1S” and “2S” are used as the symbols of the homogenized alloy, single-stage solution treated and two-stage solution treated alloy, respectively. According to Table 5, the alloy containing 0.2% Mg, being treated through a two-stage solution treatment, has the optimum properties compared to the others. This new alloy has an extraordinary strength compared with the casting aluminum alloys and also has a desirable elongation. The excellent casting property of this new alloy is due to the presence of a considerable amount of silicon.
Figure 6 illustrates the mechanical properties of the alloys containing 0.2% Mg which were given two types of solutionizing treatment followed by artificial ageing at 185 °C for 5 h, compared with those of the initial specimen.
Table 5 Mechanical properties of alloys
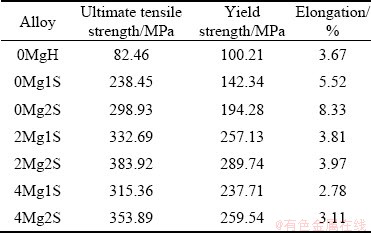
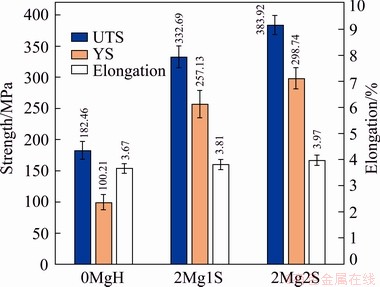
Fig. 6 Mechanical properties of alloy containing 0.2% Mg with two types of solution treatment and aged for 5 h at 185 °C, compared with reference specimen
The results show that by adding 0.2% Mg to Al-10.5Si-3.4Cu alloy and applying age hardening with a single-stage solution treatment, the ultimate tensile strength (UTS), yield strength (YS), and elongation were improved by 82%, 156% and 3.8%, respectively. However, age hardening of this alloy after applying two-stage solution treatment resulted in an improvement of ultimate tensile strength, yield strength, and elongation of 110%, 189% and 8.1%, respectively, compared with the reference specimen. This is due to the effect of magnesium as a strengthening element which increases the volume fraction of fine and well-distributed precipitates during the ageing process.
3.4 Fractography
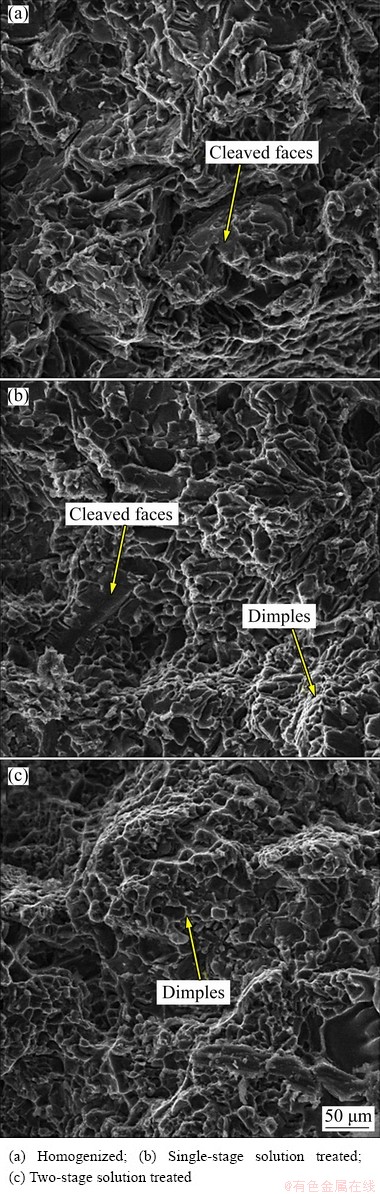
Fig. 7 Fracture surface morphologies of sample 0Mg
The fracture surface morphologies of alloys without Mg addition under different heat treatment conditions are shown in Fig. 7. In accordance with the microstructures, the alloy 0MgH as the reference specimen revealed the presence of severe cleaved faces and intergranular cracks, which led to brittle failure. The brittle fracture may be dominated by the presence of undissolved block-like Al2Cu phases at grain boundaries [26]. By performing a single-stage solution treatment at 495 °C for 8 h followed by artificial ageing at 185 °C for 5 h, brittle cleavage and small areas of plastic deformation (dimples) were dominated (Fig. 7(b)). As illustrated in Fig. 7(c), the fracture surface of the alloy 0Mg2S indicated the brittle to ductile transition due to complete dissolution of θ-Al2Cu phases after two- stage solution treatment.
Figure 8 displays the fracture surface morphologies of the alloys 2Mg and 4Mg heat-treated through single-stage and two-stage solution treatment followed by artificial ageing at 185 °C for 5 h. It was obvious that most of Cu-rich phases dissolved into the surrounding matrix due to two- stage solution treatment for both alloys. Therefore, the plastic deformation areas on fracture surfaces were larger than those of the alloys performed by a single-stage solution treatment.
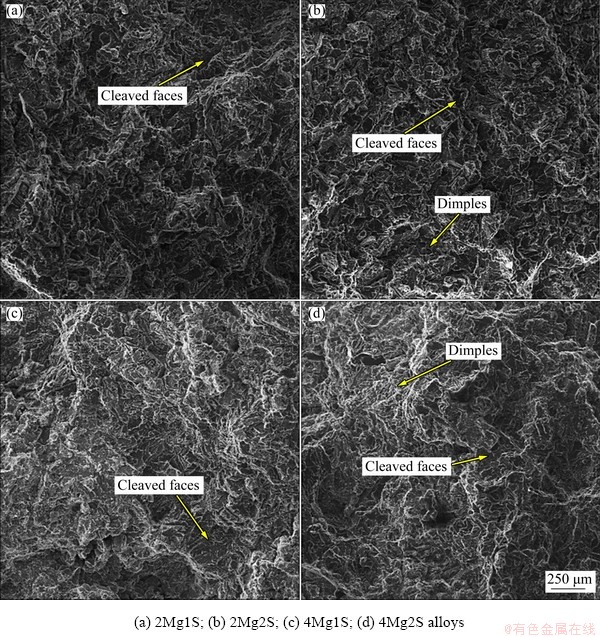
Fig. 8 Fracture surface morphologies of alloys
It can be concluded that adding magnesium more than 0.2% as an alloying element to Al-10Si-3.5Cu alloy led to the increase in the porisities. The macroscopic observation of the structure of the alloy 4Mg and 7Mg by naked eye revealed the presence of porosity. A comparison between elongation of the alloys 2Mg and 4Mg, as listed in Table 5, showed that the elongation of the alloy 4Mg was less than that of the alloy 2Mg in each heat treatment condition. Figure 9 shows fracture surface morphology of the alloy 4Mg in higher magnification, which demostrated the presense of porosity among denderits, resulting in the reduction in elongation and strength of this alloy.
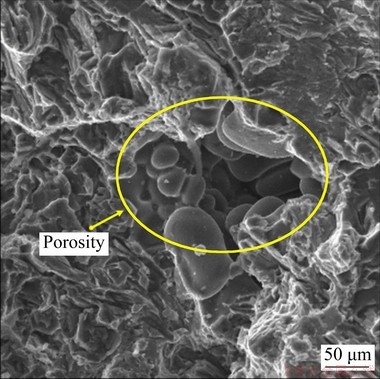
Fig. 9 Presence of porosity on fracture surface of 4Mg alloy
4 Conclusions
(1) That the morphology of α-Al15(Fe,Mn)3Si2 intermetallics is not changed during heat treatment, but the Cu and Mg-rich phases are dissolved completely by applying a suitable solution treatment.
(2) An increase in the content of Mg decreases the nucleation temperature of the θ-Al2Cu phase. The minimum temperature of 510.2 °C is obtained for the alloy containing 0.7% Mg. This exhibits that the best temperature for solution treatment can be 15-20 °C higher than 495 °C.
(3) The addition of 0.2% Mg to aluminum- silicon-copper alloys can significantly increase the response of the alloy to the ageing process. In other words, the alloys containing magnesium achieve its hardness peak after ageing for 3 h at 185 °C; however, the alloy having no magnesium does not achieve the maximum hardness even after 12 h ageing at 185 °C in both single-stage or two-stage solution treated samples.
(4) The hardness of the alloys subjected to a two-stage solution treatment is higher than that of the alloys treated through a single-stage one.
(5) A new alloy of Al-10.5Si-3.4Cu-0.2Mg is introduced. It has superior mechanical properties with ultimate tensile strength of 383.9 MPa, yield strength of 289.7 MPa, elongation of 3.97%, and hardness of HB 144.8. Compared to other aluminum cast alloys, this new alloy is of a higher strength, more desirable elongation, and higher castability.
References
[1] MA Z, SAMUEL E, MOHAMED A M A, SAMUEL A M, SAMUEL F H, DOTY H W. Parameters controlling the microstructure of Al-11Si-2.5Cu-Mg alloys [J]. Material and Design, 2010, 31: 902-912.
[2] BECKER H, BERGH T, VULLUM P E, LEINEWEBER A, LI Y. Effect of Mn and cooling rates on α-, β- and δ-Al-Fe-Si intermetallic phase formation in a secondary Al-Si alloy [J]. Materialia, 2019, 5: 100198.
[3] LIU K, CHEN X G. Influence of the modification of iron- bearing intermetallic and eutectic Si on the mechanical behavior near the solidus temperature in Al-Si-Cu 319 cast alloy [J]. Physica B: Condensed Matter, 2019, 560: 126-132.
[4] YU J M, WANDERKA N, RACK A, DAUDIN R, BOLLER E, MARKOTTER H, MANZONI A, VOGEL F, ARLT T, MANKE I, BANHARTA J. Influence of impurities, strontium addition and cooling rate on microstructure evolution in Al-10Si-0.3Fe casting alloys [J]. Alloys and Compounds, 2018, 766: 818-827.
[5] GOWRI S, SAMUEL F H. Effect of alloying elements on the solidification characteristics and microstructure of Al-Si- Cu-Mg-Fe 380 alloy [J]. Metallurgical and Materials Transaction A, 1994, 25: 437-448.
[6] FARAHANY S, OURDJINI A, IDRSI M H, SHABESTARI S G. Evaluation of the effect of Bi, Sb, Sr and cooling condition on eutectic phases in an Al-Si-Cu alloy (ADC12) by in situ thermal analysis [J]. Thermochimica Acta, 2013, 559: 59-68.
[7] WANG X F, SHI T Y, WANG H B, ZHOU S Z, PENG W F, WANG Y G. Effects of strain rate on mechanical properties, microstructure and texture of Al-Mg-Si-Cu alloy under tensile loading [J]. Transactions of Nonferrous Metals Society of China, 2020, 30: 27-40.
[8] SAMUEL A M, SAMUEL F H. Effect of alloying elements and dendrite arm spacing on the microstructure and hardness of an Al-Si-Cu-Mg-Fe-Mn 380 aluminum die-casting alloy [J]. Material Science, 1995, 30: 1698-1708.
[9] MOHAMED A M A, SAMUEL F H, AL KAHTANI S. Influence of Mg and solution heat treatment on the occurrence of incipient melting in Al-Si-Cu-Mg cast alloys [J]. Material Science and Engineering A, 2012, 543: 22-34.
[10] TAVITAS-MEDRANO F J, MOHAMED A M A, GRUZLESKI J E, SAMUEL F H, DOTY H W. Precipitation-hardening in cast Al-Si-Cu-Mg alloys [J]. Material Science, 2010, 45: 641-651.
[11] SJOLANDER E, SEIFEDINE S. The heat treatment of Al-Si-Cu-Mg casting alloys [J]. Materials Processing Technology, 2010, 210: 1249-1259.
[12] SJOLANDER E, SEIFEDINE S. Optimisation of solution treatment of cast Al-Si-Cu alloys [J]. Material and Design, 2010, 31: s44-s49.
[13] SHABESTARI S G. The effect of iron and manganese on the formation of intermetallic compounds in aluminum-silicon alloys [J]. Materials Science and Engineering A, 2004, 383: 289-298.
[14] SHABESTARI S G, MAHMUDI M, EMAMY M, CAMPBELL J. Effect of Mn and Sr on intermetallics in Fe-rich eutectic Al-Si alloy [J]. Cast Metals Research, 2002, 15: 17-24.
[15] SHABESTARI S G, GRUZLESKI J E. Modification of iron intermetallics by strontium in 413 aluminum alloys [J]. AFS Transaction, 1995, 285-293.
[16] SHABESTARI S G, GHONCHEH M H, MOMENI H. Evaluation of formation of intermetallic compounds in Al2024 alloy using thermal analysis technique [J]. Thermochimica Acta, 2014, 589: 174-182.
[17] ABDI M, SHABESTARI S G. Effect of gas-induced semi- solid process on solidification parameters and dendrite coherency point of Al-4.3Cu alloy using thermal analysis [J]. Thermal Analysis and Calorimetry, 2019, 136: 2211-2220.
[18] SEDIGHI O, SHABESTARI S G, YAVARI F. Investigation on the effect of Sn on solidification and microstructure of AZ91 magnesium alloy using cooling curve thermal analysis [J]. Thermochimica Acta, 2018, 667: 165-172.
[19] SAMUEL F H, OUELLET P, SAMUEL A M, DOTY H W. Effect of Mg and Sr additions on the formation of intermetallics in Al-6wt.%Si-3.5wt.%Cu-(0.45-0.8)wt.%Fe 319-type alloys [J] Metallurgical and Materials Transactions A, 1998, 29: 2871-2884.
[20] ALFONSO I, MALDONADO C, GONZALEZ G, BEDOLLA A. Effect of Mg content and solution treatment on the microstructure of Al-Si-Cu-Mg alloys [J] Material Science, 2006, 41: 1945-1952.
[21] EDWARDS G A, SIGWORTH G K, C'ACERES C H, ST.JOHN D H, BARRESI J. Microporosity formation in Al-Si-Cu-Mg casting alloys [J]. AFS Transaction, 1997: 809-818.
[22] SAMUEL A M, DOTY H W, VALTIERRA S, SAMUEL F H. Defects related to incipient melting in Al-Si-Cu-Mg alloys [J] Materials and Design, 2013, 52: 947-956.
[23] REYNAUD C, TEVENOT F. Porosity dependence of mechanical properties of porous sintered SiC: Verification of the minimum solid area model [J]. Material Science Letters, 2000, 19: 871-874.
[24] HOSSEINI V A, SHABESTARI S G, GHOLIZADEH R. Study on the effect of cooling rate on the solidification parameters, microstructure, and mechanical properties of LM13 alloy using cooling curve thermal analysis technique [J]. Materials and Design, 2013, 50: 7-14.
[25] AMNE ELAHI M, SHABESTARI S G. Effect of various melt and heat treatment conditions on the impact toughness of A356 aluminum alloy [J]. Transactions of Nonferrous Metals Society of China, 2016, 26: 956-965.
[26] SAMUEL A M, DOTY H W, VALTIERRA S, SAMUEL F H. Relationship between tensile and impact properties in Al-Si-Cu-Mg cast alloys and their fracture mechanisms [J]. Materials and Design, 2014, 53: 938-946.
通过双级固溶热处理制备新型高强Al-10.5Si-3.4Cu-0.2Mg合金
Mohsen ABDI, Saeed G. SHABESTARI
School of Metallurgy and Materials Engineering, Iran University of Science and Technology (IUST), Narmak, 16846, Tehran, Iran
摘 要:通过析出硬化提高Al-Si-Cu合金的力学性能。这些合金对时效硬化的反应非常缓慢。为了解决这一问题,在Al-10.5Si-3.4Cu合金中分别加入0.2%、0.4%和0.7%(质量分数)的镁。该新型合金在固溶处理阶段经过两种不同的析出硬化过程。结果表明,添加不同含量的镁可加速该合金对时效处理的响应,提高其硬度和强度。双级固溶热处理可以提高合金的力学性能。添加0.2% Mg 的Al-10.5Si-3.4Cu 合金通过双级固溶热处理后获得最佳的性能,其极限抗拉强度为383.9 MPa,屈服强度为 289.7 MPa,伸长率为3.97% , 可替代需要高强度和优良铸造性能的铝铸件。
关键词:高强合金;AlSiCuMg合金;双级固溶热处理;析出硬化
(Edited by Bing YANG)
Corresponding author: Saeed G. SHABESTARI; E-mail: shabestari@iust.ac.ir
DOI: 10.1016/S1003-6326(21)65520-6
1003-6326/
2021 The Nonferrous Metals Society of China. Published by Elsevier Ltd & Science Press