
Multi-wall carbon nanotubes reinforced aluminum composites synthesized by hot press sintering and squeeze casting
ZHANG Xue-xi(张学习), YANG Li(杨 丽), DENG Chun-feng(邓春锋), WANG De-zun(王德尊)
School of Materials Science and Engineering, Harbin Institute of Technology, Harbin 150001, China
Received 28 July 2006; accepted 15 September 2006
Abstract: Multi-wall carbon nanotubes (MWNTs) have high mechanical properties and are considered a kind of realistic reinforcement for polymers, ceramics and metals. The hot press sintering and squeeze casting were adopted to synthesize MWNTs reinforced aluminum composites. In hot press sintered MWNTs/Al composites, MWNTs agglomerates distribute along aluminum powders and have low bonding strength with aluminum. But MWNTs agglomerates distribute evenly in the squeeze cast MWNTs/Al composites. Some dispersed nanotubes bond well with aluminum matrix and few dislocations can be found in the nanotube areas, which implies little thermal residual stress in squeeze cast MWNTs/Al composites. This indicates that the strengthen mechanisms in nanometer sized MWNTs/Al composites may be different from that in micrometer sized whisker composites.
Key words: metal matrix composites (MMCs); carbon nanotubes (CNTs); mechanical properties; aluminum alloy; microstructure
1 Introduction
Multi-wall carbon nanotubes (MWNTs) are attractive for fabrication new advanced composites since their high modulus, mechanical strength and thermal stability[1-2]. MWNTs have elastic modulus of 300-400 GPa and bending strength of 14 GPa[3-4], but their densities are only about 1/6 of the irons[5]. Now, liquid process[6-7], solid process[8-14] and chemical method[15-16] were employed to synthesize MWNTs reinforced composites, in which the efficient dispersion of MWNTs in the matrix is necessary for effective transfer of their superior properties to the matrix[17-18]. MWNTs reinforced metal matrix composites (MMCs), such as CNTs/Al[8-10], CNTs/Ti[11], CNTs/Cu[12] and CNTs/Mg[13-14], were synthesized by hot press sintering. In order to achieve homogeneous dispersion of nanotubes in the composites, ZHONG et al[8] adopted nano-aluminum powder to fabricate CNTs/Al composite by hot press sintering. Nevertheless, it is still a challenge for dispersion of nanotubes in composites because of the high surface area and aspect ratio of MWNTs. Recently, in-situ formation of CNTs in metal-oxide composites[19] seemed to be an effective way to realize homogeneous dispersion of nanotubes in composites. Now, the way to synthesize MWNTs composites with a homogeneous dispersion state and good interfacial bonds is still an obstacle for the development of this kind of composite. So, the different microstructures and properties in MWNTs/Al composites synthesized by hot press sintering and squeeze casting were compared in order to evaluate the optimized fabrication method used nowadays.
2 Experimental
2.1 Purification and dispersion of MWNTs
The MWNTs made by fluidized bed reactor were supplied by the Shenzhen NanoPort Ltd. The composition measurement by a X-ray-fluorescence (XRF1800) is shown in Table 1. Considering the fabrication processing of MWNTs[20], we could deduce that the metallic impurities were mainly Ni and La2O3, which were often covered by carbon agglomerates[21]. The carbon was made of nanotubes, amorphous carbon and a few graphite nanoparticles. In order to remove amorphous carbon and catalyst metals, raw CNTs were purified by concentrated sulfate and nitric acids. Details of the purification processing were published elsewhere[10]. When the MWNTs solution with minor amount of sodium dodecylsulphate (SDS) were ultro-sonicated for over 2 h in distilled water at pH value of 5-7, the results show that MWNTs dispersed well in the solution and no obvious sediments appeared within 2 h.
Table 1 Compositions of raw MWNTs powder (mole fraction, %)

2.2 MWNTs/Al composites synthesized by hot press sintering
Commercial aluminum powder with purity of 99.6% was used as matrix metal. Their average diameter and surface area were 15 μm and 2 134.3 cm2/g, respectively. In order to disperse MWNTs uniformly with aluminum powder, the well dispersed MWNTs solution was stirred and ultrosonicated for 0.5 h, then the aluminum powder was slowly added into the solution by stirring and sonication. After stirring and sonication stopped, interestingly, the black solution became transparent, which revealed that the MWNTs were attached on the powder surface and deposited with them. The hot press sintering processing can be seen in Ref.[10].
2.3 MWNTs/Al composites synthesized by squeeze casting
MWNTs preforms made by wet method was easy to shrink to an irregular shape after drying. In order to overcome this, melamine of 50 μm was blended with MWNTs to make preform by wet method. The volume fraction of MWNTs in the preform was 15%. After the preform was dried in a vacuum oven, it showed fine outer shapes. The squeeze cast processing was as follows: the preform and die were preheated to 500 ℃, then the aluminum alloy melts of 800 ℃ was poured into the die and a pressure of 30 MPa was applied. After infiltration, the pressure was immediately raised to as high as 100 MPa and maintained for 5 min. The microstructures of the composites were observed by SEM and TEM equipped with EDS.
3 Results and discussion
3.1 Microstructures and purity of raw and purified MWNTs
Fig.1 shows the microstructures of the raw and purified MWNTs. Fig.1(a) shows that the MWNTs exist as macro-agglomerates of about a few hundreds of micrometers. These agglomerates are formed by the mechanical interactions of the long and irregular shaped nanotubes during fabrication processing. On the micro-scale, the nanotubes form micro-agglomerates by some black cluster, as shown in Fig.1(b). EDS spectrum (Fig.1(b)) shows that the clusters mainly contain C, Cl and Ni, the Cu and Zn peaks are caused by the copper grid. After the raw nanotube is stirred in concentrated sulfuric and nitric acids, the few black clusters can be seen at low or high magnification. The typical micrograph of the purified nanotubes is shown in Fig.1(c).
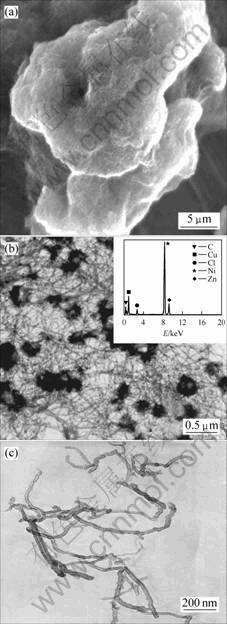
Fig.1 Morphologies and EDS analysis of raw and purified MWNTs: (a) Agglomerates in raw MWNTs; (b) Clusters in raw MWNTs; (c) Purified MWNTs
The purification effects are determined by thermogravimetric analysis (TGA) and derivative thermogravimetric analysis (DTG) in carbon dioxide flowing gas, as shown in Fig.2. From Fig.2, there are two peaks in the DTG traces of the raw MWNTs, but only one peak can be seen in the purified one. It is well known that the amorphous carbons are easier to oxide than nanotubes[22]. So, we can reasonably deduce that the first peak corresponds to the oxidation of amorphous carbon and the second peak corresponds to nanotubes. The oxidation peaks of amorphous carbon are removed by acid purification. We can also see that the oxidation peak temperatures of the raw and purified nanotubes are 924 and 1 048 ℃, respectively. This reveals that the purified nanotubes are more resistant to oxidation than raw nanotubes.
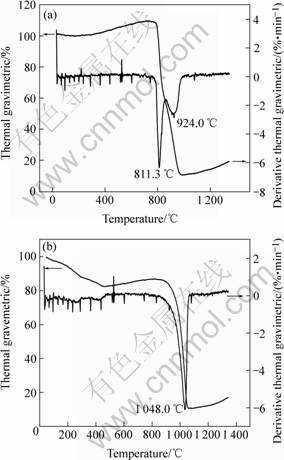
Fig.2 TGA and DTG curves of raw and purified MWNTs oxidized by carbon dioxide gas: (a) Raw MWNTs; (b) Purified MWNTs
3.2 Microstructures and hardness of hot press sintered composites
Fig.3 shows the TEM image of the hot pressed composites. It can be seen from Fig.3 that the MWNTs distribute between aluminum powders. The grain size of the aluminum matrix is very fine compared with aluminum powders. Some direct bonds between two aluminum powder can also be seen, with little alumina layer at the interface. When the MWNTs layer is very weak, they are harmful to the composites. The tensile properties of the composites are shown in Table 2. From Table 2, the tensile strength and modulus of the composites increase a little, but the elongation decreases sharply.
The composite fracture surface (Fig.4) shows that MWNTs agglomerate and crack between MWNTs agglomerates and aluminum powders. Some individual nanotubes bridging the MWNTs agglomerates and aluminum can also be seen. EDS analysis (Fig.4(c)) show the presence of carbon as well as aluminum on the MWNTs agglomerate surfaces.
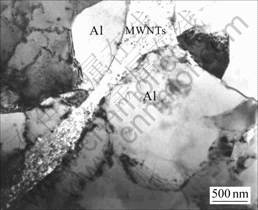
Fig.3 TEM image of hot pressed composites
Table 2 Tensile properties of aluminum and hot pressed composites

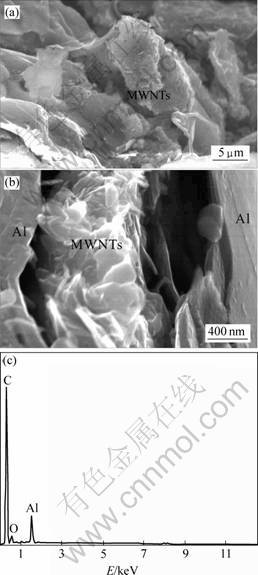
Fig.4 Fracture morphologies and EDS analysis of hot pressed composites: (a) MWNTs agglomerate; (b) Cracks along MWNTs agglomerates; (c) EDS analysis on MWNTs surface
3.3 Microstructures and hardness of squeeze cast composites
In squeeze cast MWNTs/Al composites, about 10 % of the preform was successfully infiltrated by aluminum melt. Fig.5(a) shows the microstructure of the deep etched squeeze cast composite. It shows that many MWNTs agglomerates are not infiltrated by aluminum and distribute evenly in the composite. TEM image (Fig.5(b)) shows that several dispersed nanotubes have good interfacial bonds with aluminum. There are no micro-pores at the interface. In addition, the grain boundary interacts with MWNTs, which indicates that MWNTs may pin the aluminum grain boundary during solidification processing after infiltration. Surprisingly, few dislocations can be found near nanotubes whatever tilting the sample, which is different from the whisker reinforced aluminum composites. In whisker composites, dislocating around whiskers are caused by the large thermal residual stress due to different coefficients of thermal expansion (CTE) between whisker and aluminum[23]. As the number of dislocations around nanotube directly relates to the thermal residual stress, we can deduce that the absence of dislocations in the squeeze cast MWNTs/Al composites implies little thermal residual stress presenting in the aluminum matrix around nanotubes. As CTEs of aluminum and nanotube vary very much, considerable thermal residual stress should be produced around nanotubes during cooling processing of the composites. In this sense, microstructures and strengthen mechanisms aroused by MWNTs (O. D. a few nanometers) may be different from that by whiskers (O. D. a few micrometers). JIANG [24] also employed squeeze casting to make sub-micrometer sized ceramic particles reinforced aluminum composites and found few dislocations around the ceramic particles as well. He thought that the dislocations might sink at the interfacial area of the composite. The mechanisms of the lack of dislocations in squeeze cast MWNTs/Al composites might be the same as the abovementioned composites.
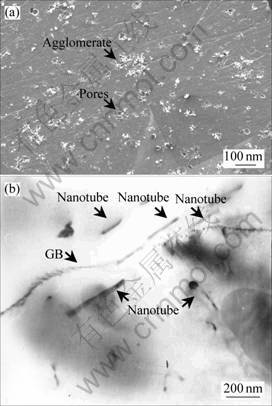
Fig.5 Distribution of MWNTs in squeeze cast composites: (a) SEM image; (b) TEM image
Fig.6 shows the hardness of the aluminum and composites. From Fig.6, the hardness of the squeeze cast composites is higher than that of the hot press sintered composite, the strength effects of the nanotubes are better in the former composites than those in the latter.
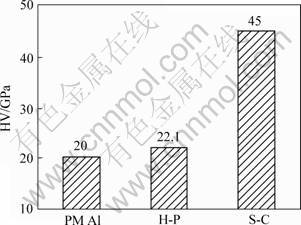
Fig.6 Hardness of hot-pressed (H-P) and squeeze cast (S-C) composites
3.4 Theoretical prediction of threshold infiltration pressure
The threshold infiltration pressure of the aluminum melt into the nanotube preforms might be calculated by Eqn.(1)[25]:

(1)
where γ is the surface tension of the melt alloy; Vf, D and L are the volume fraction, diameter and length of the fiber, respectively. θ* is defined by Eqn.(2):
θ* =arctg(D/L) (2)
For the MWNTs used here, D and L are 28 nm and 1 μm, respectively. γ is 0.865 N/m. P*—Vf plot is shown in Fig.7. Because the nanotubes distribute inhomogeneous in the preform, Vf is low at the nanotubes poor regions, leading to low P*. So, the alloy melt may quickly flow into the large inter-space between MWNTs agglomerates, trapping the air in them and resulting in the uninfiltrated areas in the MWNTs agglomerates, as shown in Fig.5(a).
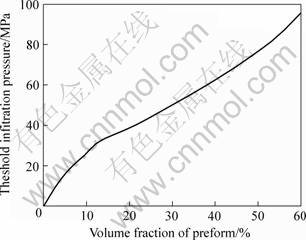
Fig.7 Threshold infiltration pressure of MWNTs preform
4 Conclusions
1) MWNTs agglomerates in hot press sintered composites, leading to easy crack initiation, propagation and accordingly poor mechanical properties of the composites.
2) It is difficult for aluminum melt completely infiltrating into the nanotube preform during squeeze casting processing since the high threshold infiltration pressure of MWNTs preforms.
3) In squeeze cast composites, dispersed nanotubes bond well with aluminum and few dislocations can be found near the nanotubes, which implies the exceptional strength mechanisms in this kind of composites.
References
[1] THOSTENSON E T, REN Z F, CHOU T W. Advances in the science and technology of carbon nanotubes and their composites: A review[J]. Comp Sci Technol, 2001, 61(13): 1899-1912.
[2] HARRIS P J F. Carbon nanotube composites[J]. International Materials Reviews, 2004, 49(1): 31-43.
[3] YU M F, LOURIE O, DYER M J, MOLONI K, KELLY T F, RUOFF R S. Strength and breaking mechanism of multiwalled carbon nanotubes under tensile load[J]. Science, 2000, 287(5453): 637-640.
[4] SALVETAT J P, KULIK A J, BONARD J M, BRIGGS G A D, STOCKLI T, METENIER K, BONNAMY S, BEGUIN F, BURNHAM N A, FORRO L. Elastic modulus of ordered and disordered multiwalled carbon nanotubes[J]. Adv Mater, 1999, 11(2): 161-165.
[5] CHENG H M. Synthesis, Structure, Physical Properties and Applications of Carbon Nanotubes[M]. Beijing: Chemical Industry Press, 2002. (in Chinese)
[6] BIAN Z, PAN M X, ZHANG Y. Carbon nanotube reinforced Zr52.5Cu17.9Ni14.6Al10Ti5 bulk metallic glass composite[J]. Appl Phys Lett, 2003, 12(25): 4739-4741.
[7] NOGUCHI T, MAGARIO A, FUKAZAWA S, SHIMIZU S, BEPPU J, SEKI M. Carbon Nanotube/aluminium composites with uniform dispersion[J]. Materials Transactions, 2004, 45(2): 602-604.
[8] ZHONG R, CONG H T, HOU P X. Fabrication of nano-Al based composites reinforced by single-walled carbon nanotubes[J]. Carbon, 2003, 41(4): 848-851.
[9] KUZUMAKI T, MIYAZAWA K, ICHINOSE H, ITO K. Processing of carbon nanotube reinforced aluminum composite[J]. Journal of Materials Research, 1998, 13(9): 2445-2449.
[10] ZHANG Xue-xi, DENG Chun-feng, WANG De-zun, GENG Lin. Synthesis and thermal stability of multiwall carbon nanotubes reinforced aluminum metal matrix composites[J]. Trans Nonferrous Met Soc China, 2005, 15(52): 240-244.
[11] KUZUMAKI T, UJIIE O, ICHINOSE H, ITO K. Mechanical characteristics and preparation of carbon nanotube fiber-reinforced Ti composite[J]. Adv Eng Mater, 2000, 2(7): 416-418.
[12] TU J P, YANG Y Z, WANG L Y, MA X C, ZHANG X B. Tribological properties of carbon-nanotube-reinforced copper composites[J]. Tribology Letters, 2001, 10(4): 225-228.
[13] CARRENO-MORELLI E, YANG J, COUTEAU E, HERNADI K. Carbon nanotube/magnesium composites[J]. Physica Status Solid, 2004, A201(8): R53-R55.
[14] YANG J, SCHALLER R. Mechanical spectroscopy of Mg reinforced with Al2O3 short fibers and C nanotubes[J]. Mater Sci Eng A, 2004, A370(1-2): 512-515.
[15] CHEN X H, XIA J T, PENG J C, LI W Z, XIE S S. Carbon-nanotube metal-matrix composites prepared by electroless plating[J]. Comp Sci Technol, 2000, 60(2): 301-306.
[16] DENG Fu-ming, CHEN Xiao-hua, CHEN Wei-xiang, LI Wen-zhu. Electroless plating Ni-P matrix composite coating reinforced by carbon nanotubes[J]. Trans Nonferrous Met Soc China, 2004, 14(4): 681-685.
[17] PARK C, OUNAIES Z, WATSON K A, CROOKS R E, SMITH J, LOWTHER S E, CONNELL J W, SIOCHI E J, HARRISON J S, CLAIR T L S. Dispersion of single wall carbon nanotubes by in situ polymerization under sonication[J]. Chem Phys Lett, 2002, 364(3/4): 303-308.
[18] LAU K T, HUI D. Effectiveness of using carbon nanotube as nano-reinforced for advanced composite structures[J]. Carbon, 2002, 40(9): 1605-1606.
[19] LUPO F, KAMALAKARAN R, SCHEU C, GROBERT N, RUHLE M. Microstructural investigations on zirconium oxide-carbon nanotube composites synthesized by hydrothermal crystallization[J]. Carbon, 2004, 42(10): 1995-1999.
[20] LI H, LIANG Q, GAO L Z, TANG S H, CHENG Z Y, ZHANG B L, YU Z L. Catalytic production of carbon nanotubes by decomposition of CH4 over the pre-reduced catalysts LaNiO3, La4Ni3O10, La3Ni2O7 and La2NiO4[J]. Catalysts Letters, 2001, 74(3/4): 185-188.
[21] YU H, ZHANG Q F, WEI F, QIAN W Z, LOU G H. Agglomerated CNTs synthesized in a fluidized bed reactor: agglomerate structure and formation mechanism[J]. Carbon, 2003, 41(14): 2855-2863.
[22] HERNADI K, LJUBOVIC E, SEO J W, FORRO L. Synthesis of MWNT-based composite materials with inorganic coating[J]. Acta Materialia, 2003, 51(5): 1447-1452.
[23] JIANG C H, WU J S, WANG D Z. Relaxation of residual stresses in 20%SiCw/6061Al composite as-extruded at high temperature[J]. Trans Nonferrous Met Soc China, 2001, 11(5): 729-732.
[24] JIANG L T. Microstructure in the Near-interfacial Areas in Sub-micrometer Al2O3 Reinforced Aluminum Composites[D]. Harbin: Harbin Institute of Technology, 2001. (in Chinese)
[25] GENG L, CAO L, ZHAO W, YAO C K. A study of fabrication technique of SiCw/Al composites by squeeze casting method[A]. Proceeding of MRS International Meeting on Advanced Materials[C]. Tokyo: Material Research Society, 1988: 29-34.
(Edited by LI Yan-hong)
Corresponding author: ZHANG Xue-xi; Tel: +86-451-86413921; Fax: +86-451-86413922; E-mail: xxzhang@hit.edu.cn