
Structure and erosion resistance of Ni60A/SiC coatting by laser cladding
LOU Bai-yang(楼白杨), CHEN Zhen(陈 阵), BAI Wan-jin(白万金), DONG Gang(董 刚)
MOE Key Laboratory of Mechanical Manufacture and Automation, Institute of Material and Surface Engineering, Zhejiang University of Technology, Hangzhou 310014, China
Received 27 August 2005; accepted 8 February 2006
Abstract: The Ni60A and Ni60A/SiC coatings were obtained by laser cladding on 0.45% C steel. The microstructure and hardness of the coatings were studied by SEM and XRD. The erosion resistances of Ni60A and Ni60A/SiC coatings were also investigated. The results show that the structure of different coatings is up to the temperature gradient and solidifying velocity in metal-melting region during laser cladding process. The coatings consist of a cladding layer, in which dendritic crystal and bulky cell-like crystal exist mainly, and a thermo-affected layer. Ni60A/SiC coating has higher microhardness than that of Ni60A coating, which is mainly caused by SiC and complicated phases formed by Ni, Cr, Fe, C and Si. It is obvious from the erosion test that the Ni60A/SiC coating has high erosion resistance.
Key words: laser cladding; Ni60A; SiC; erosion resistance
1 Introduction
Laser cladding is using high energy density laser beam to melt the cladding materials and makes them coagulate on the surface of the base materials. Laser cladding coating has high strength, good process property, high wear resistance, erosion resistance, heat resistance and so on, showing many engineering applications, which is becoming one of the best important research domain in the laser manufacture[1-6]. The coatings are made by two main methods: powder feeding and prefabricating. Contrasted with powder feeding method, prefabricating method can form grain-strengthening composite coatings. As ceramics has many advantages, the metal/ceramic composite coatings by prefabricating and powder feeding in laser cladding have been studied more and more in recent years and addition of powder ceramics such as WC, Al2O3 and TiC into the coating was reported in many research works [7-11]. Among them, the composite coating on the surface of common carbon steel by using laser cladding is getting more and more concerned[12-15], but researches and reports about SiC composite coating and its erosion resistance were limited. SiC has many characteristics like high melting point (2 500 ℃), high hardness (26.46 kN) and cheep price. Further more, it can be easily made in particle and fibre shapes, which is more attracted to be used as the enforcement phase in coating.
In this study, Ni60A/SiC coating on the 0.45% C steel was made by laser cladding, and the microstructure, formation mechanism and erosion resistance of the coating were researched.
2 Experimental
The 0.45% C steel was used as the base material, and samples were machined in size of 15 mm×20 mm×40 mm and then cleaned and burnished to remove the oil and rust. SiC and Ni60A (Ni-based alloy) powders were mixed as the coating material. The SiC and Ni60A were fine powders and Ni60A component is shown in Table 1.
SiC and Ni60A powder were difficult to mixed even because of their different densities, so the high-energy ball milling machine was used to mix the powders with 25% SiC and 75% Ni60A (volume fraction) at 200 r/min for 10 h. The self-made organic adhesive was used to paste the powders and Ni60A/SiC composite was cladded on the surface of 1 mm base steel in thickness. After that, the samples were heated at 150 ℃ for 2 h
Table 1 Chemical components of Ni60A powder(mass fraction, %)

The CO2 crosscurrent laser functional machining system (GFT-IVB, 7 kW) was used in cladding with broadband integral lens at 3 kW output power, 2 mm×10 mm rectangle facula and 180 mm/min scan velocity. To avoid oxidation, Ar gas was used during the cladding process.
After polishing and corroding, the cladding samples were observed by XRD and SEM, and tested for microhardness and erosion resistance.
An erosion test device was made, as shown in Fig.1.
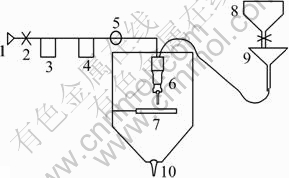
Fig.1 Sketch map of erosion resistance test device: 1 Entrance of compressed air; 2 Air pressure controller; 3 A inhaler; 4 B inhaler; 5 Manometer; 6 Sandblast; 7 Adjustable-pitch platform; 8 SiC packet; 9 Sand amount controller; 10 Sand recycle bin
In the erosion test, erosion angle, amount and the speed of the sands were controlled. The erosion resistance was expressed by mass loss calculated from the following formula:
ε=m/M
where ε is the erosion rate (mg/g); m is the mass loss (mg) and M is the amount of used SiC.
3 Results and analysis
3.1 Microstructure
There are 2 layers in the coating: cladding layer (CL) and thermo-affected layer (TL), as shown in Fig.2. The thermo-affected layer has low-carbon martensite because of laser heating and is easily to be eroded. The cladding layer consists of cell-like crystal and dendritic crystal as shown in Fig.3. The dendritic crystal occurs in the outside region of cladding layer. According to component super-cooling theory[16], the solidification structure depends on temperature gradient that exists in melting pool and solidification velocity. In melting pool, temperature gradient decreases gradually from outside (surface) to inside. Great temperature gradient makes dendritic crystal grow rapidly in the outside cladding layer. In the inside cladding layer joined with base steel, crystal grows unorderly because of the smaller temperature gradient where cell- like crystal is formed.
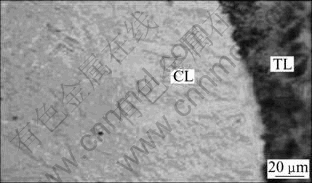
Fig.2 Microstructure of laser-cladding coating
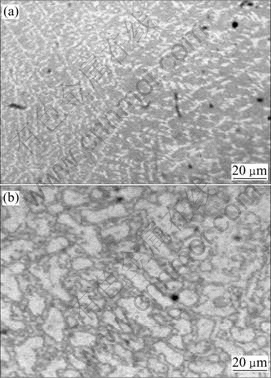
Fig.3 Microstructures of cladding layer: (a) Cell-like crystal structure; (b) Dendritic crystal structure
3.2 Analysis of phases
Fig.4 shows the XRD pattern of the sample. It shows that the main phases in the cladding coating are Ni2.9Cr0.7Fe0.36, Fe7C3 and Fe0.79C0.12Si0.09.

Fig.4 X-ray diffraction pattern of laser cladding SiC cermet
According to HOADLYS’ math simulation model computing of one dimension of laser surface melting process[17], the cooling temperature is
(1)
where θ(z, t) is the temperature, z is the distance from the layer to the surface, t is the time, θ0 is the environmental temperature, γ=t-τ, and τ is laser/material interaction time.
When z=0 on the material surface, the equation can be simplified into
θ(t)= θ0+
(2)
From above equations, it is computed that the surface temperature is 5 300 ℃ during laser cladding process which is far higher than the decomposition temperature of SiC (2 500 ℃), leading to ablation and decomposition of some SiC. With increase of laser power and decrease of scan velocity, ablation and decompo- sition of SiC increase greatly. So SiC can be hardly found in the XRD pattern separately and then other new phases containing Si form.
3.3 Analysis of microhardness
The microhardnesses of laser cladding Ni60A layers with 25% SiC and without SiC particle were tested. Fig.5 shows the microhardness distribution of each layer from surface to base. It shows that addition of SiC can enforce the microhardness of laser cladding. According to the phase analysis before, SiC particles can decompose in the coating. Contrasted with Ni60A coating, Ni60A/SiC has high microhardness, which is caused not only by dispersion intensifying effect of the SiC particles, but also by the new complicated phases. Some C and Si from decomposed SiC can make solid solubility enforcement, which raises microhardness also.
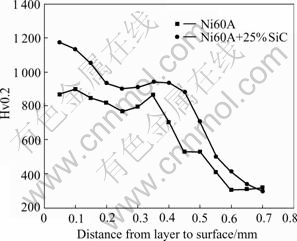
Fig.5 Micro-hardness distribution of laser cladding Ni based layers with and without SiC granule
3.4 Analysis of erosion resistance
Table 2 shows the microhardness and erosion resistance of the two different coatings. It can be seen that both two coatings have high hardness and better erosion resistance than the 0.03% C steel. The coating, with addition of SiC, has the highest erosion resistance. Contrasted with A3 steel, Ni60/SiC coating increases the erosion resistance by 99% at erosion angle 30? and 67% at erosion angle 90?, respectively.
Table 2 Microhardness and erosion resistance of coatings
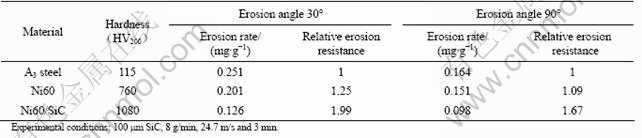
4 Conclusions
1) The structure of different coatings is up to the temperature gradient and solidifying velocity in the liquid of the melt during cladding process. dendritic crystal and bulky cell-like crystal exist mainly in the coating.
2) Ni60/SiC coating has higher microhardness than that of Ni60 coating, which is mainly caused by SiC and complicated phases formed by Ni, Cr, Fe, C and Si.
3) The Ni60/SiC coating has high erosion resistance.
References
[1] ZHANG Wei-ping, LIU Shuo. Microstructure of Fe-Ti-B composite coating prepared by laser cladding [J]. The Chinese Journal of Nonferrous Metals, 2005, 15(4): 558-564.(in Chinese)
[2] GUO J K. Multiphase material-an attractive trend for material research [J]. Research & Development of the World Science and Technology, 2000, 22(1): 17-18.
[3] ZENG Da-wan, XIA Hui, XIE Chang-sheng. Microstructure and solidification process of the laser clad Ni alloy [J]. Rare Metal Materials and Engineering, 2000, 29(2): 109-113.
[4] SILVAIN J F, NIINO H, YABE A. Nucleation and growth of surface microstructures on Nd: YAG laser ablated elastomer/carbon composite [J]. Composites: Part A, Applied Science and Manufacturing, 2000(3): 469-478.
[5] LIU Shuo, ZHANG Wei-ping. Microstructure reinforced Ni-base alloy composite coating by laser cladding [J]. Transactions of the China Welding Institution, 2005, 26(2): 13-16.
[6] YANG Sen, LIU Wen-jin, ZHONG Min-lin. Research on TiC particulate nickel based alloy composite coating produced by powder feeding laser cladding [J]. Applied Laser, 2003, 23(5): 265-267.
[7] HUA Guo-ran, HUANG Yin-hui, ZHAO Jiang-feng, WANG Lei, TIAN Zong-jun, ZHANG Jian-hua, ZHANG Yong-kang. Plasma-sprayed ceramic coating by laser cladding of Al2O3 nano-particles [J]. The Chinese Journal of Nonferrous Metals, 2004, 14(2): 199-203.(in Chinese)
[8] JIANG Wen-ping, MOLIAN U P. Nanocrystalline TiC powder alloying and glazing of H13 steel using a CO2 laser for improved life of die-casting dies [J]. Surface and Coating Technology, 2001(135): 139-149.
[9] KATHURIA Y P. Nd-YAG laser cladding of Cr3C2 and TiC cermets. [J]. Surface and Coatings Technology, 2001, 140(3): 195-199.
[10] WU Ping, JIANG En-yong, ZHOU Chang-chi, TANG Xi-nan. Microstructure and properties of Ni/WC composite prepared by laser cladding [J]. Chinese Journal of Lasers, 2003, 30(4): 357-360.(in Chinese)
[11] CHONG P H, MAN H C, YUE T M. Microstructure and wear properties of laser surface-cladded Mo-WC MMC on AA6061 aluminum alloy [J]. Surface Coatting and Technology, 2001, 145(1-3): 51-59.
[12] OUYANG J H, NOWOTNY S, RICHTER A, BEYER E. Laser cladding of yttria partially stabilized ZrO2 (YPSZ) ceramic coatings on aluminum alloys [J]. Ceramics International, 2001, 27 (1): 15-24.
[13] HIDOUCI A., PELLETIER J M, DOCOIN F, DEZERT D, GUERJOUMA R E. Microstructural and mechanical characteristics of laser coatings. [J]. Surface and Coatings Technology 2000, 123(1): 17-23.
[14] SONG Wu-gang, ZHOU Gang, XIE Chang-sheng. The effect of Creq/Nieq on structure and craze sensitivity of laser cladding [J]. Laser Technology, 1999, 23(3): 142-145.
[15] YU Ju-mei, CHAO Ming-ju, LIANG Er-jun, YUAN Bin. Effect of TiO2 on the microstructure and properties of laser cladding layers of Fe-based alloy [J]. Applied Laser, 2003, 23(4): 201-204.
[16] TILLER W A, JACKSON K A, RUTTER J W, CHALMERS B. The redistribution of solute atoms during the solidification of metals [J]. Acta Metal, 1953, 1: 428-437.
[17] HOALLY A F A, RAPPAZ M, ZIMMERMANN M. Heat flow simulation of laser remelting with experimental validation [J]. Metal Trans B, 1991, 22B(1): 101-109.
Corresponding author: LOU Bai-yang; Tel: +86-571-88320479; E-mail: lby00518@163.com
(Edited by LI Xiang-qun)