
Fabrication and wear behavior of CNT/Al composites
JIANG Jin-long(姜金龙)1, WANG Hai-zhong(王海忠)2, YANG hua(杨华)1, XU Jin-cheng(徐金城)3
1. School of Science, Lanzhou University of Technology, Lanzhou 730050, China;
2. State Key Laboratory of Solid Lubrication, Lanzhou Institute of Chemical Physics, Chinese Academy of Sciences, Lanzhou 730000, China;
3. Department of Materials Science, Lanzhou University, Lanzhou 730000, China
Received 15 July 2007; accepted 10 September 2007
Abstract: Aluminum matrix composites reinforced with carbon nanotube were fabricated by a powder metallurgy method. The effects of carbon nanotube content on the relative density, the hardness, and the friction and wear behavior of the composites under dry sliding condition were investigated using the ball (pin)-on-block tester. By scanning electron microscopy (SEM), the worn surfaces and worn chips were observed, and the wear mechanism of composites was analyzed and discussed. The results indicate that the addition to the aluminum matrix of 2.0%(mass fraction) carbon nanotube causes the increase in the Vickers hardness of about 80%. Within the range of carbon nanotubes content from 1.0% to 2.0%, both the friction coefficient and wear rate of composites decrease with the increase of carbon nanotube content. The delamination wear is the main wear mechanism for the composites.
Key words: carbon nanotubes; Al matrix composite; wear behavior
1 Introduction
Since the discovery of carbon nanotubes (CNTs) in 1991 by IIJIMA[1], there has been much interest and significant research in the filed of carbon fiber materials and their composites. The ratio of length to diameter of nanotubes can reach 100-1 000 and their diameter is about several nanometers. They have superior mechanical properties, as well as excellent thermal stability and electrical conductivity. Carbon nanotubes exhibit almost five times the elastic modulus(about 1 TPa) and close to 100 times the tensile strength (about 150 GPa) of those of high strength steels[2-3].Therefore, defect free and light mass CNTs can be used as potential fiber materials for composites.
In recent years, much research has been focused on the development of CNT reinforced Al matrix composites[4-8], because Al matrix composites have wide prospects of application in aviation, spaceflight and automobile industries. DENG et al[6] found that the maximal increases of tensile strength and elastic modulus of the 1.0%(mass fraction) nanotube/2024Al composite, compared with the 2024Al matrix, are 35.7% and 41.3%, respectively. CI et al[7-8] investigated the chemical stability and interfacial reaction between multi-walled carbon nanotubes and aluminum. Many researches have been done on improving the strength properties and materials design of CNTs/Al composites. However, the research on wear behavior of CNT reinforced Al matrix composites has been rather limited. Thus, in this study, CNT reinforced aluminum matrix composites were fabricated by a powder metallurgy method. The effects of CNT content on the relative density, the hardness, and the friction and wear behavior of the composites under dry sliding condition were investigated.
2 Experimental
2.1 Materials and preparation of composites
The CNTs used in this work were synthesized by anodic arc discharge method[9]. With the addition of cocatalysts such as Fe, Ni, Co, web-like substances and thin films made up of CNTs, catalyst particles and amorphous carbon were obtained. The CNTs were subjected to an oxidation treatment in concentrated nitric acid for 48 h and hydrofluoric acid for 24 h, then filtered and washed with distilled water.
The aluminum powder (purity of 99.0%, grain size of 70 ?m) and CNTs were homogeneously mixed by hand grinding for 30 min, and ethanol was added to avoid possible oxidation. The mixture of CNTs and aluminum powder was uniaxially pressed in steel dies under a pressure of 300 MPa for 2 min. The specimens were isothermally sintered at 100 ℃ for 1 h and 600 ℃ for 2 h in a pure argon atmosphere. The specimens for testing, containing 0 to 3% of CNTs respectively, were 60 mm×10 mm×2 mm in size.
2.2 Friction and wear tests
The friction coefficient of the composites was measured using a reciprocating ball-on-block apparatus under dry condition. The counterpart was a ball with 3 mm diameter made from GCr15 steel with hardness of 61 HRC. The experiments were operated with loads of 1 N and 3 N at a sliding velocity of 0.16 m?s-1. The stroke length and testing distance were 10 mm and 50 cm, respectively.
The wear tests were conducted on a DMT-1 multi-functional reciprocating sliding wear apparatus (pin-on-block) under dry condition. The counterpart was a pin with 1.5 mm diameter made by high-speed steel with hardness of 45-50 HRC. The experiments were operated with loads of 1N and 3 N at a sliding velocity of 0.5 m?s-1. The stroke length and testing distance were 30 mm and 30 m, respectively. The ratio of mass loss to sliding distance was taken as the wear rate to evaluate wear resistance of the composites, and the average of the three replicates was cited as a result for each specimen in this article. All the friction and wear tests were performed at room temperature, and a relative humidity of 40%-60%. The morphologies of the worn surfaces were analyzed on a 6700F scanning electron microscope (SEM).
3 Results and discussion
3.1 Hardness of composites
The hardness of the composites was tested on a MH-5-VM Vickers tester with a contact load of 0.98 N for 15 s. The density of composites was measured by the Archimedes method, the relative density being obtained by comparing measured densities to the theoretical densities. The effects of CNT content on relative density and hardness of the composites are shown in the Table 1. The average of measured hardness from five different locations of the each specimen surface was considered the hardness of the specimen. It is showed that the Vickers hardness of the composites is 29-54, and the relative density is 93.5%-97%. The XRD patterns of Al and 3.0% CNTs/Al composite are shown in Fig.1. However, the (002) peak of carbon nanotubes can not be found at approximately 2θ=26?. The reason may be that the peaks of carbon nanotubes interfuse with backgrounds due to the low content and scattering coefficient of CNTs[10].
Table 1 Hardness and density of composites
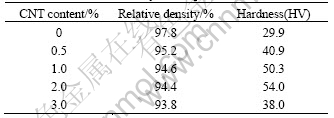
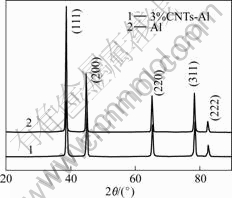
Fig.1 XRD patterns of Al and 3.0%CNTs/Al composite
3.2 Friction and wear of composites
The friction coefficients of CNT/Al under 1 N and 3 N loads are plotted in Fig.2. The friction coefficient of composites shows a decreasing trend with increasing content of carbon nanotubes. It is suggested that an increase in surface fraction of carbon nanotubes reduces the direct contact between the Al and the steel ball. Due to self-lubrication of CNTs, the friction coefficient of the composites decreases. Fig.2 also shows that the friction coefficient under a load of 3 N is slightly lower than those under a load of 1 N. The possible reasons are as follows. The contact surface proportion of composite and the counterpart ball is a nonlinear function of load because the composite and the steel ball are an elastic-plastic contact; when the load is 3 N, more carbon film can cover wear surface.
Fig.3 shows the effects of CNT content on the wear rates of the composites at a sliding speed of 0.5 m?s-1 under 1 N and 3 N of loads. Within the range of CNT content from 0 to 2.0 %, the wear rate of the composites shows a steadily decreasing trend with increasing content of CNTs. The favorable effects of CNT on wear resistance are attributed to their excellent mechanical properties and the efficiency reinforcement to Al matrix. However, owing to the agglomeration of the CNTs decreasing the hardness of the composites, when the CNT content is more than 2.0%, the wear rate of the composites exhibits a severe increase.
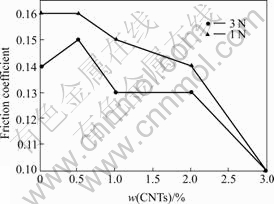
Fig.2 Friction coefficients of composites with increasing content of carbon nanotube
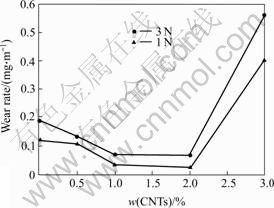
Fig.3 Relationship between wear rate of composites and content of carbon nanotubes
Fig.4 shows typical SEM morphologies of worn surfaces of the composites with different CNT contents under 1 N and 3 N loads. There is evidence of adhesion and ploughing on the Al worn surface, which shows a distinct characteristic of abrasive and adhesive wear. The counterpart pin is seized twice in the wear tests, which may be the result of the weld contact surface metal at some protruding points. Al wear particles on the worn surfaces are laminated by the pin on the contact area, forming plough. Because wear particles contain some aluminum oxide, ZHOU et al believed that the oxidation wear was the main wear mechanism of composites[11]. However, according to the SEM images of worn surfaces of the composite and the delamination theory of wear, it can be deduced that the delamination wear could be the main wear mechanism. Dislocations at the surface, subsurface crack and void are induced due to the repeated plastic deformation of the surface layer of composites. The cracks extend later and cause break and split of the hardened surface layer by shear deformation of the surface[12-13]. Because Al matrix is reinforced with carbon nanotubes, the plastic deformation of the matrix is restricted, which hinders the movement of the dislocations and formation of micro-cracks. It can be seen that the flake-like sheets scars in the worn surface of composite become smaller and more, and the evidence of ploughing become shallower, comparing Figs.4(a) and (b). It is suggested that the abrasive and adhesive wear of the composites is slighter than pure aluminum due to increases of hardness and self-lubrication of carbon nanotube, and the delamination wear becomes important. It can be seen that the 3.0% CNTs/Al composite exhibits a severe wear and the layer wear debris is found on the worn surface (Fig.4(c)), which attributes to generation of higher porosity in the composite matrix and causes an increase in the wear rate.
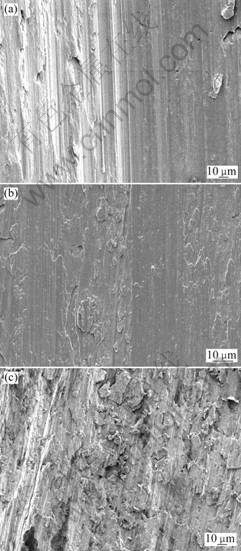
Fig.4 SEM images of worn surface of test specimens with (a) Al (1 N); (b) 2.0% CNTs/Al (3 N); (d) 3.0% CNTs/Al (1 N)
4 Conclusions
1) The hardness of the composites increases with increasing CNTs content, but then decreases for CNTs greater than 2.0%. The hardness of the composite with 2.0% CNTs is the highest.
2) Within the range of CNTs content from 1.0% to 2.0%, the CNTs can decrease both the friction coefficient and wear rate of the composites. The composite containing 2.0% CNTs exhibits the lower friction coefficient and wear rate.
3) The main wear mechanism is the delamination wear for the composites containing 2.0% CNTs.
References
[1] IIJIMA S. Helical microtubes of graphitic carbon[J]. Nature, 1991, 354: 56-58.
[2] WONG E W, SHEEHAN P E, LIEBER C M. Nanobeam mechanics: Elasticity, strength and toughness of nanorods and nanotubes[J]. Science, 1997, 277: 1971-1975.
[3] TREACY M J, EBBESEN T W, GIVSON J M. Exceptionaly high Young’s modulus observed for individual carbon nanotubes[J]. Natutre, 1996, 381: 678-680.
[4] KUZUMAKI T, MIYZA WA W, ICHINOSE H, ITO K. Processing of carbon nanotube reinforced aluminum composites[J]. J Mater Res, 1998, 13 (9): 2445-2449.
[5] GEORGE R, KASHYAP K T, RAHUL R, YAMDAGNI S. Strengthing in carbon nanotube/aluminium (CNT/Al) composite[J]. Scripta Materialia, 2005, 53(10): 1159-1163.
[6] DENG C F, WANG D Z, ZHANG X X, LI A B. Processing and properties of carbon nanotubes reinforced aluminum composites[J]. Materials Science and Engineering A, 2007, 444(1/2): 138-145.
[7] CI L J, RYU Z Y, JIN-PHILLIPP N Y, R?HLE M. Investigation of the interfacial reaction between multi-walled carbon nanotubes and aluminum[J]. Acta Materialia, 2006, 54(20): 5367-5375.
[8] DENG Chun-feng, ZHANG Xue-xi, WANG De-zun. Chemical stability of carbon nanotubes in the 2024Al matrix[J]. Materials Letters, 2007, 61(3): 904-907.
[9] WANG Q, DAI J F, LI W X, MA Q. Investigation of preparation parameters of carbon nanotubes[J]. Journal of Lanzhou University of Technology, 2004, 30(6): 27-29. (in Chinese)
[10] XU Long-shan, CHEN Xiao-hua, WU Yu-rong. Preparation of CNTs/ Cu composite[J]. The Chinese Journal of Nonferrous Metals, 2006, 16(3): 406-411. (in Chinese)
[11] ZHOU Sheng-ming, ZHANG Xiao-bin, DING Zhi-peng, MIN Chun-yan, XU Guo-liang, ZHU Wen-ming. Fabrication and tribological properties of carbon nanotubes reinforced Al composites prepared by pressureless infiltration technique[J]. Composites Part A: Applied Science and Manufacturing, 2007, 38(2): 301-306.
[12] SUH N P. The delamination theory of wear[J]. Wear, 1973, 25(1): 111-124.
[13] XU Jin-cheng, YU Hui, XIA Long, LI Xiao-long, YANG Hua. Effects of some factors on the tribological properties of the short carbon fiber-reinforced copper composite[J]. Materials and Design, 2004, 25(6): 489-493.
Foundation item: Project(3ZS061-A25-039) supported by the Natural Science Foundation of Gansu Province, China
Corresponding author: JIANG Jin-long; Tel: +86-931-2973780; E-mail: jinlong@lut.cn
(Edited by ZHAO Jun)