
J. Cent. South Univ. (2018) 25: 1350-1357
DOI: https://doi.org/10.1007/s11771-018-3831-7

Corrosion behaviors and mechanism of electroless Ni–Cu–P/n–TiN composite coating
ZHOU Hong-ming(周宏明)1, 2, HU Xue-yi(胡雪仪)1, LI Jian(李荐)1, 2
1. School of Materials Science and Engineering, Central South University, Changsha 410083, China;
2. Hunan Province Zhengyuan Energy Storage Materials and Devices Research, Changsha 410083, China
Central South University Press and Springer-Verlag GmbH Germany, part of Springer Nature 2018
Abstract: In the present investigation, electroless Ni–Cu–P/n–TiN composite coating was prepared using alkaline citrate-based bath. X-ray diffraction (XRD), scanning electron microscopy(SEM), energy-dispersive spectroscopy(EDS), electrochemical measurements, weight loss tests and Raman spectrometer were used to character the properties of the coating. As the Cu content increased from 7.3 wt% to 24.8 wt%, the corrosion current density of the Ni–Cu–P/n–TiN coating decreased from 10.80 to 4.34 μA. And the inclusion of Cu in Ni–P alloy resulted in refinement and less porosity in microstructure. The addition of TiN resulted in a slight decline in anti-corrosion property of the coating. As the mass loss test showed, Ni–24.8%Cu–P exhibited perfect corrosion resistance. Studies by Raman spectroscopy on coatings proved that Cu(II)3(PO4)(OH)3, Cu(OH)2 and CuO were examined while no compound of nickel was found, and Cu exhibited preferred corrosion in saline solution, providing cathodic protection to Ni alloy.
Key words: Cu content; TiN content; corrosion resistance; corrosion mechanism; cathodic protection
Cite this article as: ZHOU Hong-ming, HU Xue-yi, LI Jian. Corrosion behaviors and mechanism of electroless Ni–Cu–P/n–TiN composite coating [J]. Journal of Central South University, 2018, 25(6): 1350–1357. DOI: https://doi.org/10.1007/s11771-018-3831-7.
1 Introduction
Electroless plating is a well-established autocatalytic process [1], which is widely used in different industries for its proven benefits in controlling corrosion and wear resistance. Electroless nickel–phosphorous (Ni–P) coatings possess excellent structure and properties, depending on their phosphorous content [2]. Incorporating another metallic element such as copper [3], tungsten [4], cobalt [5] within electroless Ni–P binary alloy coating and thereby utilizing their great corrosion and wear resistance and hardness has led to a new generation of the electroless nickel composite coatings. It is well known that Ni–Cu alloys with about 30 wt% Cu content are highly corrosion resistant in many aggressive environments such as in chloride solution [6]. Some investigations have been made to obtain compact Ni–Cu–P alloys with 30 wt% Cu content with a deposition rate as high as for Ni–P coating [7]. LIU et al [8] investigate the corrosion rates of electroless Ni–Cu–P coatings in HCl and NaCl solutions. It was mentioned that codeposition of Cu in Ni–P matrix improved the corrosion resistance of the coatings [9–11].
Furthermore, incorporation of many fine solid particles within an electroless metal matrix can form composite materials [12–21] with various and excellent properties. Second phases of Al2O3 [22], ZrO2 [23, 24], and SiC [25, 26] nano-particles were widely used and investigated due to their excellent wear resistance and hardness. TiN should be an ideal candidate for coatings due to its high hardness, melting point and chemical resistance. The hardness of Ni–P–TiN increases 3 times compared to that of common Ni–P coating [27], and wear resistance also increases remarkably [27, 28]. However, adding TiN into Ni–P results a decline in anti- corrosion property.
In this work, the electroless deposition of four-component Ni–Cu–P/n–TiN coating was studied. Not much information is available on the behaviors and mechanisms in corrosion resistance of electroless Ni–Cu–P/n–TiN composite coating. Hence, the present study focuses on the behaviors and mechanisms in corrosion resistance of electroless Ni–Cu–P/n–TiN composite coating. Coating structure and surface morphology were characterized by scanning electron microscopy (SEM) and X-ray diffraction (XRD). Corrosion study was also conducted on these coatings in 3.5 wt% sodium chloride solution. And corrosion products were analyzed by Raman spectroscopy.
2 Experimental
The composition of coating bath is given in Table 1.
Table 1 Electroless bath composition
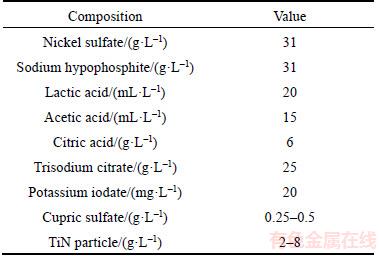
To suspend TiN completely in electroless bath, TiN nano-particles was dissolved in polyethylene glycol-2000 solution to form milky solution, and then added into plating solution with magnetic stirring after ultrasonic cleaning. The chemical composition of the steel specimens was determined by SPECTROLAB quantometer (Table 2). Schistose high-carbon steel specimens (<1 mm) were used as substrates. Those steel plates were pretreated as follows: degreased in absolute ethyl alcohol with ultrasonic cleaning for 20 min followed by rinsed with distilled water and then dipped in 15 wt% HCl solution for 10 s. Electroless deposition took place in the bath at temperature of 75–80 °C for 60 min, and prior to each deposition the bath’s pH was fixed at 4.8–5.1. The suspension bath was stirred by a mechanical stirrer at a constant speed of about 300 r/min.
Table 2 Chemical composition of SK2 steel (mass fraction, %)
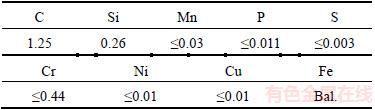
The surfaces of Ni–P–Cu/n–TiN composite coating were examined by a FSEM-SIRION200 scanning electron microscopy (SEM), with a GENESIS60S energy dispersive spectroscopy (EDS) and a D/Max 2500 X-ray diffraction (XRD) using Cu Kα radiation.
The corrosion performance of coated samples was evaluated in 3.5 wt% NaCl by potentiodynamic polarization and weight loss methods. The potentiodynamic polarization measurements were performed by the ZAHNER IM6ex electrochemical workstation at a constant voltage scan rate of 5 mV/s using a classical three electrode, a platinum plate as the counter electrode and the samples with an exposed area of 1 cm2 as the working electrode, respectively.
As to mass loss measurements, the mass of the coating samples before and after corrosion in the test solutions was determined by a Mettler Toledo analytical balance. After weighted, the parallel coating samples were immersed in a beaker with the test solution for different time defined as immersion time. Triplicate experiments were performed in each case and the mean value of the mass loss was calculated and used for the following analysis. The corrosion rate (V) was obtained according to Eq. (1) [29]:
(1)
where mi and mii are the mass of the specimens before and after corrosion, respectively, S is the total area of the coating, t is the immersion time, and △m is the mass loss of the specimens before and after corrosion for different time. For accurate comparison, all the samples had the same exposure area (1 cm2).
3 Results and discussion
3.1 Compositions and microstructures of coatings
The cross-sectional morphology of electroless Ni–Cu–P/n–TiN composite coating was studied using scanning electron microscopy (SEM), and the result is shown in Figure 1(a). The composite coating was divided into the transitional layer (≈1 μm) and the outer layer (8–12 μm) incorporated with TiN nano-particles.
The surface composition of the coating was determined by X-ray analysis (EDS). The examination of the line scanning from X to Y is shown in Figure 1(b). There was a sharp change of composition of the Cu and Ni. The matrix metal n was ternary Ni–Cu–P alloy, and the EDS analysis of point N (Figure 1(c)) shows that the content of Cu and P is about 5.6 wt% and 11.1 wt% respectively, leading to a high phosphorus and amorphous coating. As regards to the specimen’s microareas, seen in Figure 1(a) as the black point M, the analysis reveals that titanium is the dominant element there.
3.2 Effects of Cu and TiN on anticorrosion properties
Typical potentiodymical polarization curves of electroless Ni–Cu (0.0%, 7.3%, 10.0%, 24.8%, 30.3%)–P and Ni–24.8%Cu–P/n–TiN(0.00%, 3.30%, 4.36%, 4.70%) coatings are presented in Figure 2. The corrosion potential (Ecorr) and corrosion current (Icorr) obtained from the potentiodynamic polarization curves are summarized in Table 3.
From Figure 2(a), it is indicated that the corrosion potential was shifted to passive direction in the presence of Cu. And the Ni–Cu–P coatings had lower activity with respect to the Ni–P coating. Also, according to polarization curve, there is a considerable decrease in the corrosion current (10.80 to 4.34 μA) with Cu content increasing from 7.3% to 24.8%. Ni–24.8%Cu–P exhibited better corrosion resistance due to higher co-deposited Cu. However, excessive content of Cu had negative effects in the anti-corrosion properties of Ni–Cu–P coating. This can be attributed to the weak combination of the ternary Ni–Cu–P coating with the metal matrix as the Cu content over 30.3%, resulting in transverse corrosion in the coating.
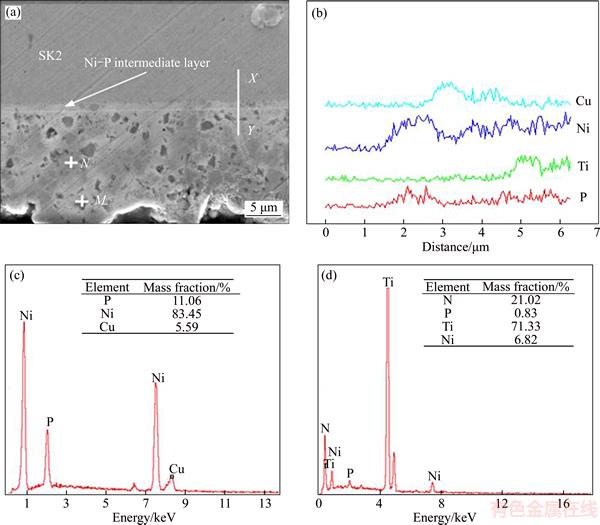
Figure 1 Cross-sectional morphology of Ni–Cu–P/n–TiN composite coating (a), EDS analysis of line X–Y (b), and EDS analysis of point N (c) and point M (d)
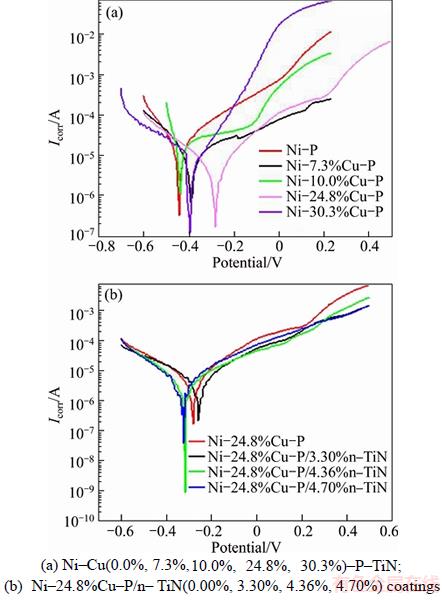
Figure 2 Potentiodynamic curves:
Table 3 Electrochemistry data of Ni–Cu(0.0%, 7.3%, 10.0%, 24.5%, 30.3%)–P and Ni–24.8%Cu–P/n– TiN(0.00%, 3.30%, 4.36%, 4.70%) coatings
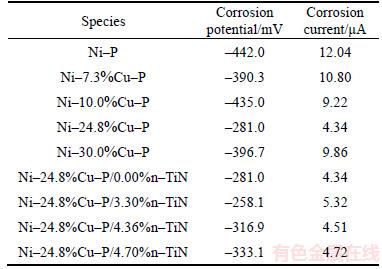
The potentiodynamic curves of Ni–24.8%Cu– P/n–TiN(0.00%, 3.30%, 4.36%, 4.70%) coatings in 3.5% NaCl solution are shown in Figure 2(b). When the TiN nano-particles are incorporated, the corrosion potential is shifted toward the active direction. There is only a slight fluctuation of the corrosion current value (4.34–5.32 μA) when the TiN content increases from 3.30% to 4.70%.
The results obtained from the polarization curves of the specimens were also confirmed by the mass loss curves. Figure 3 illustrated the relationships between mass loss (△m/S) and immersion time by mass loss measurements in 3.5% NaCl. The data of mass loss and immersion time was linear fitted. The corrosion rate (V) and correlation coefficient (R) were listed in Table 4.
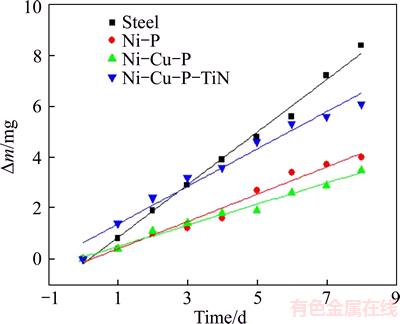
Figure 3 Results of mass loss test
Table 4 Corrosion rate of steel, Ni–P, Ni–24.8%Cu–P and Ni–24.8%Cu–P/3.30%n–TiN

As shown in Figure 3, the mass loss increased with the immersion time increasing for Ni–P coating. Meanwhile, the similar tendency can also be seen in Ni–24.8%Cu–P and Ni–24.8%Cu– P/3.30%n–TiN coatings. Clearly the anti-corrosion performance of Ni–24.8%Cu–P coating was the best. TiN nanoparticles are of low electric resistivity (down to 20 μΩ) [30] and can result in rough surface of Ni–P–Cu/n–TiN specimen. Therefore, by comparison, after introducing TiN particles into ternary Ni–Cu–P alloy, the corrosion rate of the Ni–24.8%Cu–P/3.30%n–TiN coating increased dramatically. Figure 4 illustrates surface morphology of Ni–P and Ni–24.8%Cu–P coating. As shown, the diameter of the spherical nodule of ternary Ni–Cu–P coating is 100–200 nm, which is less than that of Ni–P coating. Refinement and less porosity in microstructure are clearly seen in Figure 4(b). This can be attributed to the much greater reduction potential of cupric ions than nickel ions, therefore, copper ions have a greater preference to be deposited than nickel ions [31]. Thus, the point defects can be filled up by copper during the depositing process. Compact and less-porous coatings have superior corrosion resistance.
Figure 5 shows the surface topography of the Ni–24.8%Cu–P/(3.30%, 4.30%)n–TiN composite coatings. During electroless composite plating, the incorporation of TiN nano-particles leads to the heterogeneous nucleation of Ni nano-grains due to the same face-centered cubic structure of TiN and Ni crystalline phases. It is observed that as the TiN content increases from 3.30% to 4.30%, the amount of TiN agglomeration particles increases and the diameter of the TiN agglomerated particles also increases from 2 to 4–6 μm. The increased agglomerated grains are prone to detach from the ternary Ni–Cu–P matrix.
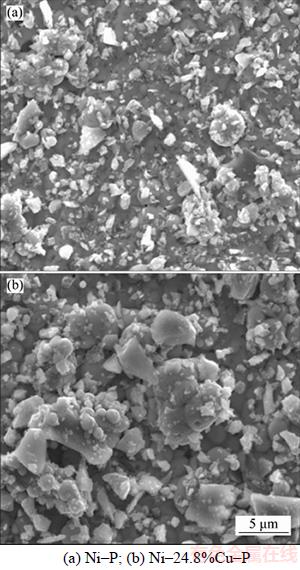
Figure 4 Surface morphology of electroless coatings:
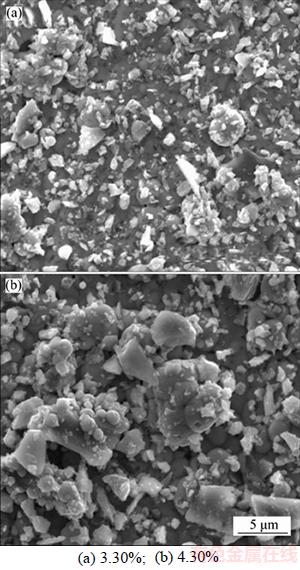
Figure 5 Surface topography of Ni–24.8%Cu–P/n–TiN composite coating with different TiN content:
3.3 Corrosion mechanism
Figure 6 shows the X-ray diffraction spectrum of the Ni–Cu–P/n–TiN composite coating exposed to 3.5% solution before and after corrosion. A broad peak at 45° could be seen in all the coatings which is related to the amorphous profile of Ni–P deposits. After conducting corrosion treatment, reduction of amorphous peak integration between 40°to 50°is observed. It is indicated that crystallization takes place in the coating during the procedure of corrosion.
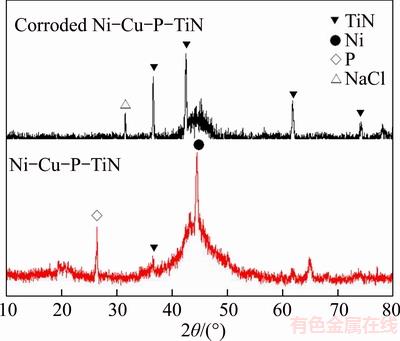
Figure 6 X-ray diffraction spectrum of coating exposed to 3.5% solution before and after corrosion
Furthermore, obvious TiN diffraction peaks were observed in corroded Ni–Cu–P/n–TiN coating XRD patterns.
Figure 7 illustrates the SEM images of electroless Ni–24.8%Cu–P/3.30%n–TiN composite coating before and after corrosion in 3.5% NaCl solution. It is observed that a typical cauliflower- like morphology with TiN particles embedding in it, the nodule diameter of ternary Ni–Cu–P alloy was about 2 μm, and a few TiN agglomerated particles were prone to detach from the surface because of lower cohesion with the ternary Ni–Cu–P alloy. After corrosion, obvious agglometation of ternary Ni–Cu–P alloy nodules and higher porosity among agglometations are observed in Figure 7(b). The incompact structure was the reason that TiN particles were easy to drop out from the ternary Ni–Cu–P alloy in the corrosion process. In addition, distinct nodulizing and refinement in TiN particle are also observed in Figure 7(b). This result is in agreement with the findings of the XRD patterns (Figure 6).
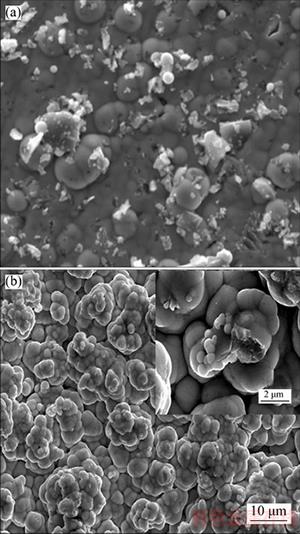
Figure 7 SEM images of Ni–24.8Cu–P/3.30%n–TiN composite coating before (a) and after (b) corrosion in 3.5 wt% NaCl solution
Figure 8 shows Raman spectra of the electroless Ni–24.8%Cu–P/3.3%n–TiN composite coatings exposed to 5.0 wt% HCl, 5.0 wt% NaOH, 3.5 wt% NaCl solution for 2 d, respectively.
It is exhibited that Cu(Ⅱ)3(PO4)(OH)3, Cu(OH)2 and CuO are detected and no compounds of Ni is found in the corrosion products after corroding in 5.0 wt% NaOH and 3.5 wt% NaCl solution. It is indicated that besides refining the structure of the coating, Cu exhibits preferred corrosion in saline and alkaline solutions, providing cathodic protection to Ni alloy. In comparison, after exposed to the dilute hydrochloric acid solution for 2 d, the whole steel substrate of the sample corrodes off completely, only leaving 2 curling thin film coatings. Furthermore, Fe3(PO4)2·8H2O is detected but no compounds of Ni or Cu is found from the products. When exposed to acid and salt solution, TiN particles in the coating are not stable, and TiO2, which is stable in the acid solution, is detectable from the corrosion products. And Na2Ti3O7 is also detected in the products after corroding in alkali and salt solutions.
4 Conclusions
1) The effects of Cu, TiN contents on the anti-corrosion behaviors of electroless Ni–P coating are studied. Experimental results show that when the Cu content increases from 7.3% to 24.8%, the self-corrosion current of the ternary Ni–Cu–P coatings decreases from 10.8 to 4.34 μA, but as the content increases to 30.3%, the corrosion current rises to 9.86 μA. The incorporation of TiN only results in a slight variation of the self-corrosion current from 4.34 to 5.32 μA, but it still has passive effects on the corrosion potential. Meanwhile, as the mass loss test shows, Ni–24.8%Cu–P exhibits better corrosion resistance compared with Ni–P and Ni–24.8%Cu–P/3.30%n–TiN.
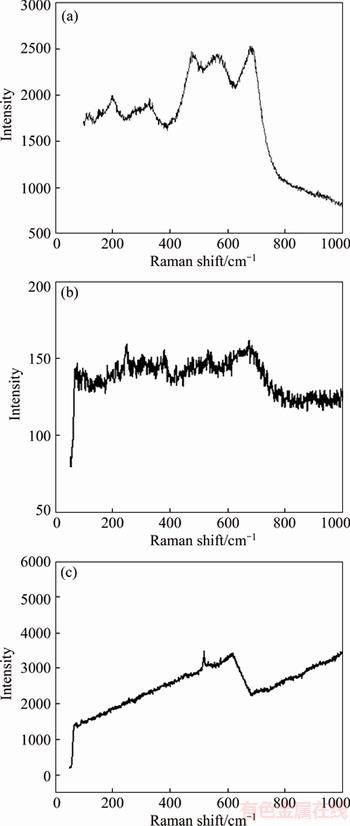
Figure 8 Raman spectra of coating exposed to 3.5 wt% NaCl (a), 5.0 wt% NaOH (b), 5.0 wt% HCl (c) solution respectively after corroding for 2 d
2) Based on SEM observation, incorporation of Cu results in refinement and less porosity in microstructure due to its excellent sedimentation capacity. However, as the TiN content in the coating improves, the amount and diameter of TiN agglomeration particles increases. And the increased agglomerated grains are prone to detach from the ternary Ni–Cu–P matrix.
3) The results obtained from Raman spectra analysis illustrate that Cu(Ⅱ)3(PO4)(OH)3, Cu(OH)2 and CuO are examined while no compound of nickel is found, and Cu exhibits preferred corrosion in saline solution, providing cathodic protection to Ni alloy.
References
[1] ASHASSI-SORKHABI H, ES’HAGHI M. Corrosion resistance enhancement of electroless Ni–P coating by incorporation of ultrasonically dispersed diamond nanoparticles [J]. Corrosion Science, 2013, 77(12): 185–193.
[2] BALARAJU J N, MILLATH-JAHAN S, ANANDAN C, RAJAM K S. Studies on electroless Ni–W–P and Ni–W–Cu–P alloy coatings using chloride-based bath [J]. Surface and Coating Technology, 2006, 200(16): 4885–4890.
[3] ASHASSI-SORKHABI H, DOLATI H, PARVINI-AHMADI N, MANZOORI J. Electroless deposition of Ni–Cu–P alloy and study of the influences of some parameters on the properties of deposits [J]. Applied Suface Science, 2002, 185(3, 4): 155–160.
[4] ZHAO Q, LIU Y, ABEL E W. Effect of Cu content in electroless Ni–Cu–P–PTFE composite coatings on their anti-corrosion properties [J]. Materials Chemistry and Physics, 2004, 87(2, 3): 332–325.
[5] SYED A S, GANESA S V, CHANDRAN K, GURUVIAH S. Performance of electroless nickel-tungsten alloys [J]. Key Engineering Materials, 1991, 20–28: 1371–1376.
[6] SRINIVASAN K N, SELVAGANAPATHY T, MEENAKSHI R, JOHN S. Electroless deposition of nickel-cobalt- phosphorus nano alloy [J]. Surface Engineering, 2013, 27(1): 65–70.
[7] CHASSING E, CHERCHAOUI M, SRHIRI A. Electrochemical investigation of the autocatalytic deposition of Ni–Cu–P alloys [J]. Journal of Applied Electrochemical, 1993, 23(11): 1169–1174.
[8] LIU Y, ZHAO Q. Study of electroless Ni-Cu-P coatings and their anti-corrosion properties [J]. Applied Surface Science, 2004, 228(1–4): 57–62.
[9] GULLA M. Metal finishing alloy: US, Patent 3764352 [P]. 1973.
[10] ARMYANOV S, GEORGIEVA J, TACHEV D, VALOVA E, NYAGOLOVA N, MEHTA S, LEIBMAN D, RUFFINI A. Electroless deposition of Ni-Cu-Palloys in acidic solutions [J]. Electrochemical Solid-State Letters, 1999, 2(7): 323–325.
[11] GAO Y R, LIU C M, FU S L, LI H Z, SHU X, GAO Y H. Pretreatment process and corrosion resistance of electroless nickel plating on ZM6 magnesium alloy [J]. Journal of Central South University: Science and Technology, 2011, 42(5): 1248–1253. (in Chinese)
[12] SUN W C, TAN M F, LU J H, ZHANG L, ZHOU Q. Corrosion and oxidation resistance of electroless Ni-P-Al2O3 composite coatings on carbon steel [J]. Applied Mechanics and Materials, 2010, 34–35: 831–835.
[13] CHI G J, YAO S W, FAN J, ZHANG Z H, REN G X. Study on photocatalytic antibacterial performance of Ni/TiO2 composite deposits [J]. Material Science and Technology, 2004, 12(1): 52–56.
[14] LIU Y Y, YU J, HUANG H, XU B H, LIU X L, GAO Y, DONG X L. Synthesis and tribological behavior of electroless Ni-P-WC nanocomposite coatings [J]. Surface and Coating Technology, 2007, 201(16, 17): 7246–7251.
[15] SHI L, SUN C, GAO P, ZHOU F, LIU W. Mechanical properties and wear and corrosion resistance of electrodeposited Ni-Co/SiC nanocomposite coating [J]. Applied Surface Science, 2006, 252(10): 3591–3599.
[16] BENEA L, BONORA P L, BORELLO A, MARTELLI S. Effect of SiC size dimensions on the corrosion wear resistance of the electrodeposited composite coating [J]. Wear, 2002, 53(1): 23–29.
[17] SAHOO P, DAS S K. Tribology of electroless nickel coatings–A review [J]. Materials & Design, 2011, 32: 1760– 1775.
[18] CHEN C K, FENG H M, LIN H C, HONG M H. The effect of heat treatment on the microstructure of electroless Ni-P coatings containing SiC particles [J]. Thin Solid Films, 2002, 416(1): 31–37.
[19] ZHOU H M, HU X Y, LI J. Effect of nano-Al2O3 on corrosion resistance of Ni-P composite coating by electro-brush plating [J]. Surface Technology, 2017, 46(7): 28–32. (in Chinese)
[20] REZRAZI M, DOCHE M L, BERCOT P, HIHN J Y. Au-PTFE composite coatings elaborated under ultrasonic stirring [J]. Surface and Coating Technology, 2005, 192(1): 124–130.
[21] VIDRICH G, CASTAGNET J F, FERKEL H. Dispersion behavior of Al2O3 and SiO2 nanoparticles in nickel sulfamate plating baths of different compositions [J]. Journal of Electrochemical Society, 2005,152(5): 294–297.
[22] ALIREZAEI S, MONIRVAGHEFI S M, SALEHI M, SAARCHI A. Wear behavior of Ni-P and Ni-P-Al2O3 electroless coatings [J]. Wear, 2007, 262(7, 8): 978–985.
[23] SONG Y W, SHAN D Y, CHEN R S, HAN E N. Study on electroless Ni-P-ZrO2 composite coatings on AZ91D magnesium alloys [J]. Surface Engineering, 2007, 23(5): 334–338.
[24] SZCZYGIEL B, TURKIEWICZ A, SERAFINCZUK J. Surface morphology and structure of Ni-P, Ni-P-ZrO2, Ni-W-P, Ni-W-P-ZrO2 coatings deposited by electroless method [J]. Surface and Coatings Technology, 2008, 20(9): 1904–1910.
[25] APACHITEI I, DUSZCZYK J, KATEGEMAN L. Electroless Ni-P composite coatings: The effect of heat treatment on the microhardness of substrate and coating [J]. Scripta Materialia, 1998, 38(9): 1347–1353.
[26] HUANG X, WU Y, QIAN L. The tribological behavior of electroless Ni-P-SiC (nanometer particles) composite coatings [J]. Plating and Surface Finishing, 2004, 91(7): 46–48.
[27] ZHAO F G, HUANG H, WANG F. Texture and mechanical property of brush electroplated (Ni-P)-TiN nanoparticles composite coating [J]. Plating and Finishing, 2010, 32(9): 1–4. (in Chinese)
[28] YU L H, HUANG W G, ZHAO X. Study on Ni-P-nanoTiN electroless composite coating [J]. Surface Technology, 2009, 38(5): 17–19.
[29] LAI C, LI X M, ZOU L K, CHEN Q, XIE B, LI Y L, LI XL, TAO Z. Corrosion of porous silicon in tetramethylammonium hydroxide solution [J]. Corrosion Science, 2014, 85(4): 471–476.
[30] MAFI I R, DEHGHANIAN C. Studying the effects of the addition of TiN nanoparticles to Ni-P electroless coatings [J]. Applied Surface Science, 2011, 258(5): 1876–1880.
[31] AAL A A, ALY M S. Electroless Ni-Cu-P plating onto open cell stainless steel foam [J]. Applied Surface Science, 2009, 255(13): 6652–6655.
(Edited by FANG Jing-hua)
中文导读
化学镀 Ni–Cu–P/n–TiN 复合镀层的耐腐蚀行为与机理研究
摘要:本文以碱性柠檬酸为镀液,通过化学镀方法,制备了Ni–Cu–P/n–TiN复合镀层。分别采用XRD、SEM和EDS分析镀层的物相组成和组成形貌,采用电化学测试、失重试验、拉曼光谱仪来表征镀层的耐腐蚀性能。实验结果表明:Cu可细化Ni–Cu–P/n–TiN胞状组织并减少其结构中的孔隙率,当Cu含量在7.3 wt%~24.8 wt% 时,复合镀层Ni–Cu–P/n–TiN的自腐蚀电流从10.80 μA下降至 4.34 μA;而TiN的掺杂会使复合镀层Ni–Cu–P/n–TiN的耐腐蚀性能降低。失重试验表明,当Cu含量为24.8wt%时,镀层Ni–Cu–P的耐腐蚀性能较好。通过拉曼曲线分析可知,复合镀层中Cu表现出优先腐蚀机制,形成了Cu(Ⅱ)3(PO4)(OH)3、Cu(OH)2和CuO等Cu金属的腐蚀产物,为镍合金提供了很好的阴极保护作用。
关键词:Cu含量;TiN含量;耐腐蚀性能;腐蚀机理;阴极保护
Foundation item: Project(K1403375-11) supported by Science and Technology Planning Project of Changsha, China; Project(2015D009) supported by the Planned Science and Technology Project of Qingyuan City, China; Project(2015B04) supported by the Planned Science and Technology Project of Qingcheng District, Qingyuan City, China
Received date: 2017-01-13; Accepted date: 2017-04-11
Corresponding author: LI Jian, PhD, Professor; Tel: +86–731–88877173; E-mail: ziliao2000@126.com; ORCID: 0000-0002-3703-7259