
Tool-workpiece interaction and shear layer flow during
friction stir welding of aluminium alloys
Z. W. CHEN, S. CUI
Department of Mechanical and Production Engineering, AUT University, New Zealand
Received 15 July 2007; accepted 10 September 2007
Abstract: Material flow phenomena during friction stir welding (FSW) and the forming mechanism of “onion rings” are complicated and currently not fully understood. In the present FSW study aluminium alloys 5083 and A356, with the latter more readily welded than the former, were used. The experiments were conducted to obtain samples of tool and workpiece “frozen” together during FSW for analysis. Two deposition modes for forming the weld nugget zone were observed, one for each alloy with the present FSW parameters. The first is the deposition of shear layers forming the “onion rings” in 5083 alloy nugget. The tool-workpiece interaction leading to the layer thickness being equal to the ratio of welding speed and tool rotation speed is suggested. The second mode is the combination of depositing the rotational shear material in the lower part on the advancing side and the drag flow of material from the retreating site forming the rest of the A356 nugget. The latter mode resulted in the absence of a clear ring structure.
Key words: friction stir welding (FSW); deposition; nugget zone; rotation
1 Introduction
Friction stir welding (FSW), invented by TWI in 1991, is a relatively new solid-state joining and efficient manufacturing enabling technology. Many aspects of FSW have been studied quite extensively in recent years and comprehensively reviewed by MISHRA and MA[1]. They concluded that material flow during FSW is complicated and not well understood. REYNOLDS[2], in presenting a special issue of Science and Technology of Welding and Joining on FSW, commented that tool-workpiece contact condition and the forming mechanism of weld nugget have remained uncertain or controversial. These condition/mechanism need to be understood in order to model and predict heat generation, material flow and microstructure evolution during FSW.
Marker technique has been used quite widely to study material flow during FSW[3-11]. Using this technique, the final distribution of the marker material is located to estimate material flow. Examination of the shear material around the pin during FSW has also been made using stop action technique [5, 8,10,12], where FSW (the machine) is stopped as nearly simultaneously as possible. The samples including the tool and workpiece material “frozen” together are then prepared and examined. In these studies of using marker material and “frozen” tool-workpiece, some general features of material flow have been identified. Recently, we have developed a technique for the pin to break and embed in the workpiece during FSW.
Using both marker material and stop action, GUERA et al[5] identified a heavily deformed zone with some trace of marker material around the pin and thus suggested a continuous rotation zone during FSW of 6061 alloy. Further experiments[8, 10] confirmed GUERA et al’s observation. It is however not certain how the shear layer rotates with the pin while it partially detaches behind to form the weld nugget zone. As summarized by YAN et al[13], although the banded structures (the “onion rings”) in the weld nugget are the common feature of FSW and there have been many studies on these structures, their forming mechanisms are not fully understood. YAN et al’s study demonstrated the relationship between the banded structures and periodic variation of FSW parameters.
Further suggestions on the forming mechanism of “onion rings” are continuing to be made, based on the patterns observed in FS welds. However, due to the experimental difficulty on observing directly or obtaining truly “frozen” tool-workpiece samples, how these structures form has remained unclear.
In a recent study of using pin-breaking technique to obtain better “frozen” samples, we have shown that under the steady-state FSW condition using a work hardened alloy (5083), a shear layer detached completely from the pin on the trailing-retreating site during each revolution. The layer detached into a stable cavity leaving little material to rotate with the pin. The mechanism governing the deposition once in a cycle had however not been revealed. In the present study, we have included the use of not only a work hardened alloy but also a cast alloy, with the latter significantly easier to weld than the former[14]. We have further improved the sampling technique for a more detailed examination of the pin-workpiece interaction region. After analyzing the structure features, material flows resulting in the formation of the weld nugget zones with banded and non-banded structures for the two different alloys, respectively, are revealed.
2 Experimental
All FSW experiments, as schematically illustrated in Fig.1, were conducted using a milling machine. Workpiece materials were 6 or 8 mm thick aluminium alloy 5083 (Al-4.5Mg-0.6Mn) rolled plates and A356 (Al-7Si-0.3Mg) cast alloy (machined to 6 or 8 mm from ingots). Microstructure of the cast alloy is shown in Fig.2, consisting of α(Al) dendrites and Al-Si eutectic. Dendrites appear darker in the low magnification macrograph taken using a stereomicroscope and lighter in the higher magnification micrograph using a normal microscope. Deformation during FSW changes the morphology of the dendrite shape and can provide information on material flow.
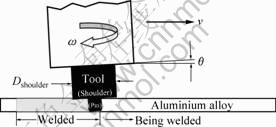
Fig.1 Schematic illustration of FSW and processing parameters
FSW tools (lefthand-thread pins) were made using H13 tool steel, and hardened to a hardness HRC>50. Dshoulder was either 16 or 20 mm, outer Dpin was 6 mm and Lpin was 5.5 or 7 mm. FSW parameters were θ at 0? or 2?, v at 1-3 mm/s and w at 710-800 r/min. These are normal FSW parameters, except a non-zero tilt angle is normally used for a featureless tool shoulder. In the present work, we aimed to analyze samples where the pin could stop rotation suddenly and embed into the workpiece during FSW. To obtain these samples, experiments were conducted using pin-breaking technique and details of this have been recently described. The use of θ= 0? was to more focus on the flow forming the weld nugget, as it is known that a tilted tool increases the amount of the top shoulder flow above the weld nugget[14]. After welding, metallography samples were prepared for examination, following the normal procedure.
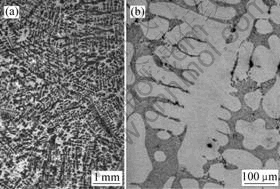
Fig.2 Microstructures of A356 cast alloy-micrographs taken by stereomicroscope and normal microscope: (a) At low magnification; (b) At higher magnification
3 Results and discussion
3.1 General features of weld zones
Fig.3 and Fig.4 show the cross sections of the typical FS defect-free welds using the two different alloys. The top ~1/3 of the welds formed primarily due to the shearing and particularly forging actions of the tool shoulder, hence named shoulder flow zone. A larger Dshoulder which provides more frictional heat and a lower v which results in a lower rate of heat lost need to be used for alloy 5083 welds with defects free in the shoulder flow zone[14]. The present work focuses on the weld nugget zone below the shoulder flow zone.
As shown in Fig.3, the nugget zone of 5083 weld formed with the typical “onion rings” well developed. On the other hand, as shown in Fig.4, a ring structure has not been observed in the A356 weld. The boundary of the weld nugget on the retreating side (on the right) is less clear in the macrograph due to a low degree of deformation and thus the zone has been marked. There are two regions in the A356 nugget zone. The first is the region marked RSM (rotational shear material) where the original dendritic feature has disappeared completely, due to heavy deformation. The origin of RSM will be revealed in the next section below. The second is the rest of the nugget where the original dendrites, having gone through some degrees of deformation, could be recognized as deformed dendrites. Material in the central-upper area of this nugget region has experienced a higher degree of deformation.
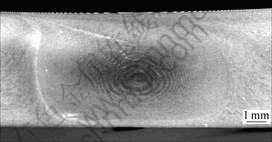
Fig.3 Cross section of alloy 5083 sample (advancing side on left) made at Dshoulder=20mm, v =1 mm/s, ω=800 r/min and θ = 2?, showing “onion rings” in nugget zone
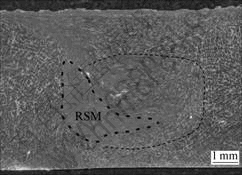
Fig.4 Cross section of cast alloy A356 alloy sample (advancing side on left) made using Dshoulder=16 mm, v =3 mm/s, ω=800 r/min and θ=2?, showing absence of clear “onion rings” in nugget zone (outlined)
3.2 Shear zone and nugget formation
From our recent work, we can summarize the 2D shear flow during FSW of 5083 as shown in Fig.5. A cyclic deposition of a newly formed layer should establish during FSW and the newly formed layer will continue to flow for a short distance around the pin to the back until the pin detaches from it. This detachment/deposition occur once every revolution while the detached layers continue to fill the cavity being created due to the forward travel of the pin. In the present work, the use of θ= 0? has reduced the amount of shoulder flow considerably[14]. Hence, the banded structures that form the “onion rings” immediately behind the pin had been less covered by the shoulder flow material and could be better examined. The SEM image of such a sample in Fig.6 provides a better view of how a fresh shear layer detaches from behind the pin during FSW.
As demonstrated previously, the heavily deformed shear material in thread space starting from the front part (advancing side) of the pin deposited behind the pin into a layer. This is also indicated in Fig.5. The transformation of the shape (from a thread space shape to a layer) is the consequence of the detaching material from each space being wiped down by the upper flank of each thread. Each thread space shape becoming a layer can thus only take place once in a cycle. In each cycle the advancement of the pin (λ) is equal to v/ω. Thus, for the sample as shown in Fig.6, λ=0.16 mm.
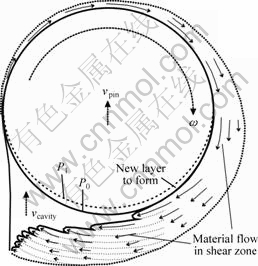
Fig.5 Schematic illustration of material flow in shear zone around pin during FSW of 5083 alloy, with P0 represent present cycle and P1 next
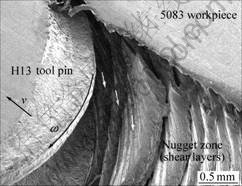
Fig.6 SEM image of 5083 sample with pin broken and embedded made using Dshoulder=16 mm, v =1.9 mm/s, ω=710 r/min and θ= 0?, with motions of pin and deposited shear layers indicated
For A356, a sample free of coverage of the top shoulder flow has not been obtained. This is due to the more readily flow of this alloy. Thus, examination using SEM on the trailing part of the pin could not be conducted. However, cross sectioning a sample with a broken pin embedded could be done in the same manner. A very different feature of shear material is observed, as shown in Figs.7 and 8. A continuous rotation zone is clearly seen in Fig.7. The heavily deformed material (named RSM) rotating in the thread space during FSW can also be suggested examining the macrograph in Fig.8. As a large portion of RSM resided in thread space did not detach, it needed to flow downward pushed or sheared by the frank of the rotating thread. Thus, a high portion of RSM detached from the lower or the bottom of the pin, as is also clear in Fig.8.
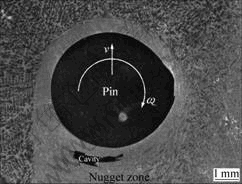
Fig.7 Longitudinal cross-section of A356 weld plate with broken pin embedded made at Dshoulder=16 mm, v =1.9 mm/s, ω=710 r/min and θ= 0?, taken along plane ~2.5 mm from bottom of pin (sectioned plan parallel to plate)
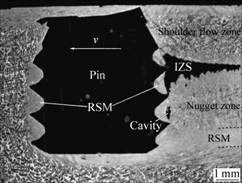
Fig.8 Longitudinal cross-section of A356 weld plate with broken pin embedded made using Dshoulder=16 mm, v=1.9 mm/s, ω=710 r/min and θ= 0?, sectioned along mid-section of pin (normal to plate)
Hence, for A356 alloy, there are two flows forming the weld nugget. The first is the RSM flow forming the shape of RSM region of the nugget as marked in Fig.4. The lower region of the less deformed material, in both Fig.4 and Fig.8, is the transitional flow dragged by the RSM flow. The second flow is one that forms the mid-upper region of the nugget (Fig.4) from the retreating side dragged by the rotating pin and RSM (Fig.7). The shape of the less deformed region of the nugget in Fig.4 is thus consistent with the patterns observed in Figs.7 and 8.
4 Conclusions
1) A shear layer detached completely when 5083 alloy was used in the present FSW condition. The detached material evolved from a shape of thread space to a layer during each cycle due to the interaction with the thread and thus λ=v/ω.
2) When A356 alloy was used, the deposition was the result of the presence of RSM which was deposited into the lower advancing side forming that portion of the nugget. Material in the retreating side and underneath the depositing RSM dragged by the rotating pin and the depositing RSM, respectively, form the rest of the nugget.
References
[1] MISHRA R S, MA Z Y. Friction stir welding and processing[J]. Mater Sci Eng R, 2005, 50: 1-78.
[2] REYNOLDS A P. Guest editorial–Friction stir welding[J]. Science and Technology of Welding and Joining, 2007, 12(4): 282-283.
[3] COLLIGAN K. Material flow behavior during friction stir welding[J]. Welding Journal, 1999, 78: 229s-237s.
[4] SEIDEL T U, REYNOLDS A P. Visualization of the material flow in AA2195 friction-stir welds using a marker insert technique[J]. Metall Mater Trans A, 2001, 32: 2001-2879.
[5] GUERRA M, SCHMIDT C, MCCLURE J C, MURR L E, NUNES A C. Flow patterns during friction stir welding[J]. Materials Characterization, 2003, 49: 95-101.
[6] ZETTLER R, LMOLINO S, dos SANTOS J F, DONATH T, BECKMANN F, LIPPMAN T, LOHWASSER D. A study on material flow in FSW of AA 2024-T351 and AA 6065-T4 alloys[C]//Proceedings of the 5th International Symposium on Friction Stir Welding. Metz, TWI, 2004.
[7] COLLIGAN K J, CHOPRA S K. Examination of material flow in thick section friction stir welding of aluminium using a stop-action technique[C]//Proceedings of the 5th International Symposium on Friction Stir Welding. Metz, TWI, 2004.
[8] SCHMIDT H, HATTEL J H. An analytical model for prescribing the flow around the tool probe in friction stir welding[C]//Proceedings of the Symposium on Friction Stir Welding and Processing Ⅲ. San Francisco, 2005: 205-212.
[9] ZHAO Y H, LIN S B, QU F X, WU L. Influence of pin geometry on material flow in friction stir welding process[J]. Mater Sci Technol, 2006, 22: 45-50.
[10] SCHMIDT H N B, DICKERSON T L, HATTEL J H. Material flow in butt frction stir welds in AA2024-T3[J]. Acta Materialia, 2006, 54: 1199-1209.
[11] SCHNEIDER J, BESHEARS R, NUNES Jr A C. Interfacial sticking and slipping in the friction stir welding process[J]. Mater Sci Eng A, 2006, 435/436: 297-304.
[12] FONDA R W, BINGERT J F, COLLIGAN K J. Development of grain structure during friction stir welding[J]. Scripta Materialia, 2004, 51: 243-248.
[13] YAN J H, SUTTEN M A, REYNOLDS A P. Processing and banding in AA2524 and AA2024 friction stir welding[J]. Science and Technology of Welding and Joining, 2007, 12(5): 390-401.
[14] CHEN Z W, PERIS R MAGINNESS R, XU Z. Material flow and the shear layer in the upper weld zone during friction stir welding of aluminium alloys[J]. International Journal of the Society of Materials Engineering for Resources, 2006, 14: 77-81.
Corresponding author: CHEN Z W; Tel: +64 9 921 9999 x8737; E-mail: zhan.chen@aut.ac.nz
(Edited by CHEN Ai-hua)