Trans. Nonferrous Met. Soc. China 23(2013) 2491-2495
Three-point bending behavior of aluminum foam sandwich with steel panel
Guo-yin ZU, Ri-huan LU, Xiao-bing LI, Zhao-yang ZHONG, Xing-jiang MA, Ming-bo HAN, Guang-chun YAO
School of Materials and Metallurgy, Northeastern University, Shenyang 110819, China
Received 11 September 2012; accepted 3 December 2012
Abstract: Static three-point bending tests of aluminum foam sandwiches with glued steel panel were performed. The deformation and failure of sandwich structure with different thicknesses of panel and foam core were investigated. The results indicate that the maximum bending load increases with the thickness of both steel panel and foam core. The failure of sandwich can be ascribed to the crush and shear damage of foam core and the delamination of glued interface at a large bending load. The crack on the foam wall developed in the melting foam procedure is the major factor for the failure of foam core. The sandwich structure with thick foam core and thin steel panel has the optimal specific bending strength. The maximum bending load of that with 8 mm panel and 50 mm foam core is 66.06 kN.
Key words: aluminum foam sandwich; three-point bending; failure mode; panel thickness
1 Introduction
Sandwich composites consisting of steel panels and aluminum foam core have got much attention in various industries, such as train and automotive fields, because of their light weight, high specific strength and effective impact absorption capability [1-3]. The bending strength is improved significantly compared with that of the aluminum foam [4-7].
The power metallurgical method used to produce the aluminum foam sandwich with steel panel (AFSS) has been studied experimentally. However, there exist some shortcomings for this procedure, such as the high cost, complicated craft, strict requirement of equipments, and low utilization of raw materials. Though the bond strength is weaker than that by the metallurgical method, AFSS using adhesive to glue steel panel to foam core is got more attention for its simple and inexpensive craft, large size, optical thickness of metal panel [4,8].
BASTAWROS et al [9], JEON and ASAHINA [10], BELE et al [11], PAUL et al [12] and MU et al [13] have studied the deformation behavior and foam structure evolution of aluminum foam and aluminum foam sandwich (AFS) at adhesive interface. However, the deformation behavior and failure mechanism of the AFS under bending load have not been investigated abundantly due to their limited size and unstable interface.
In this work, three-point bending tests of AFSS were performed to analyze the static mechanics and deformation. A series of experiments for different thicknesses of steel panel and aluminum foam core were conducted to analyze the effect. The failure mode and bending strength were mainly studied.
2 Experimental
The aluminum foam cores with different thicknesses were fabricated by the melt foaming method. The thickness and chemical composition of steel panel are listed in Table 1.
The foam and panel were cut into 240 mm in length and 80 mm in width. The inside face of steel panels was brushed by steel brush to clean surface and increase the contact area between panel and core. The panels were then etched in HCl solution at room temperature for 5 min and ultrasonically washed finally. The foam cores were treated by 100 grid abrasive paper to increase the roughness. After that, the steel panels and foam core were glued together by the polyamide-epoxy resin with mass ratio of 1:1, and kept at ambient temperature for 24 h.
Table 1 Chemical composition and specification of panels

The static three-point bending tests with five duplicates were conducted on a CMT 5105 materials testing system at a pressure head speed of 5 mm/min. The diameter of pressure head was 20 mm, and the span was 150 mm.
3 Results and discussion
3.1 Effect of foam core thickness and panel thickness
Figure 1 shows the curves of deflection vs load of three-point bending tests. The peaks of curves show that the bending strength of AFSS increases with the rise of foam core thickness. There exists an exception for the 20 mm and 30 mm curves, which may be due to the mechanical mismatch of foam core and steel panel at the glued interface. However, these two curves reveal the effect of aluminum foam core on the improvement of energy absorption. The curve with 30 mm core has a wider platform at high loads than that with 20 mm core. Figure 1 makes clear that the bending strength of AFSS with thick foam core has a higher absolute value than the AFS with aluminum panel. In addition, a loading fluctuation occurs with 25 mm deflection during the failure.
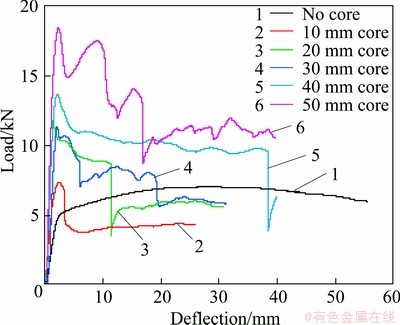
Fig. 1 Curves of deflection vs load of AFSS with different thickness core during bending test
During the bending, the aluminum foam core crushes and densifies, hence, the carrying capacity is improved. The bending load increases when the displacement rises. The glued interface will fail due to the significant inconsistent deformation between steel and foam core. This indicates a large range of fluctuation in curve. After that the load becomes nearly stable due to the compacted foam core.
The peak value of bending load and corresponding deflection, according to Fig. 1, are listed in Table 2. It indicates that the bending load increases remarkably with the rise of core thickness, while the corresponding bending deflection has a small correlation with core thickness. This is because the aluminum foam core has a good absorption of bending load, and delays the failure of whole structure. The large bending strength can be obtained due to this performance.
Table 2 Static three-point bending results of AFSS with 3 mm steel panel and different core thicknesses

Figure 2 presents the photographs of bending test of AFSS with 3 mm steel panel and 40 mm foam core. The failure of foam core is shown in Fig. 2(b), and the delamination of glued interface between panel and core is indicated in Fig. 2(d). During the bending process, the steel panel was also collapsed. The failure mode indicates that the thick foam core improves the AFSS bending strength by transforming the bending load into the bottom steel panel.
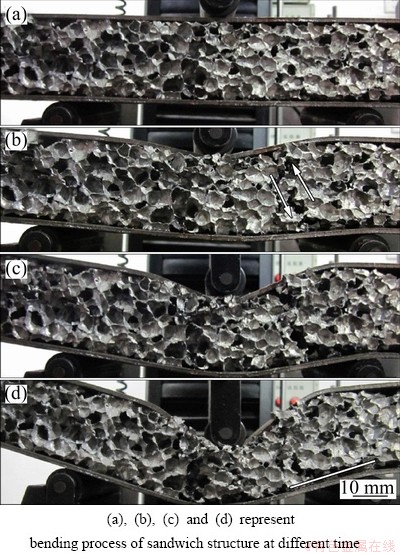
Fig. 2 Photographs of bending test of AFSS with 3 mm steel panel and 40 mm foam core
Meanwhile, the bending tests show that the initial failure of AFSS occurs as the shear damage of aluminum foam core. In our previous studies, the AFS with metallic bonded aluminum panel fails when the top panel collapses or the bottom interface delaminates [14]. This can be ascribed to the high strength of steel panel.
Thick steel panels were used to improve the strength and stiff of AFSS through damaging the light-weight performance. Figure 3 represents that the high bending strength is obtained with thick steel panel. The exception in the curve of 40 mm-thick core is clear to 5 mm and 6 mm steel panel, which may be due to the diversity of aluminum foam core. In addition, the bending strength of AFSS with 5 mm panel increases by 7%, while the mass increases by 25% compared with AFSS with 4 mm panel. The specific bending strength of that with 5 mm panel sharply drops.
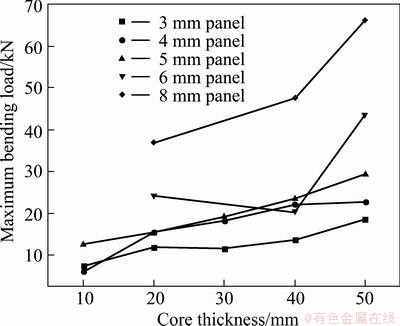
Fig. 3 Variation of the maximum bending load with core thickness
It is necessary to make an optimal thickness ratio of panel to core for the AFSS to obtain high specific bending strength [15]. Through comparing the effect of thickness of steel panel with foam core, the structure with thick foam core can be applied with the undemanding volume. For example, the AFSS with 3 mm panel and 50 mm foam core has a maximum bending load of 18.52 kN, while another AFSS structure with 5 mm panel and 20 mm core has a maximum load of 15.29 kN and is 1.6 times higher than the former.
3.2 Deformation behavior and failure mechanism
There exists a special delamination of adhesive and shear damage of foam core, as shown in Fig. 4, for the AFSS with thick steel panel, which is different from that with thin one. Because of the same raw materials, adhesive and glue procedure, the failure mode can be ascribed to the particular deformation behavior during the bending test.
The thick panel has high strength and stiff to resist the bending load. For the thick panel AFSS, the bending load can be dispersed into the foam core and transformed to the bottom panel under disperse load. Therefore, the load between top and bottom panel has a different form, as shown in Fig. 5(a). During three-point bending tests, the top panel gets a concentrated load into its middle position, while the bottom panel is supported by two points. When the foam core has enough strength to sustain the bending deformation and transform the bending load, the AFSS will be deformed as illustrated in Fig. 5(b). After the crush of foam core at large bending loads, there exists a tensile stress at the glued interface between top panel and foam core. Hence, the glued interface beside the pressure head delaminates as the form in Fig. 5(c). Because of the impact energy absorption of foam core, the bending load cannot cause the bottom panel to yield.
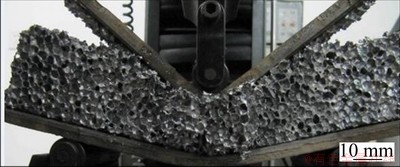
Fig. 4 Bending deformation of AFSS with 4 mm panel and 50 mm core
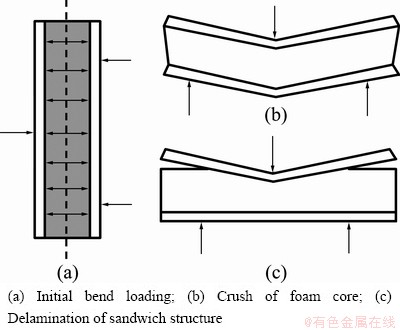
Fig. 5 Deformation behavior of AFSS during bend test
The adhesive strength of glued interface is important to the bending performance of AFSS [16]. Figure 6(a) shows the macroscopic graph of failed AFSS. It can be seen that the failure mostly concentrates upon the fracture or crush of aluminum foam core under tensile stress and shear stress, while seldom along the interface between panels and core. Figure 6(b) indicates that a lot of aluminum foams adhere to the steel panel when AFSS fails. This proves that the AFSS with efficient adhesive interface is able to resist the bending deformation if the foam core has a perfect impacting absorbing capacity.
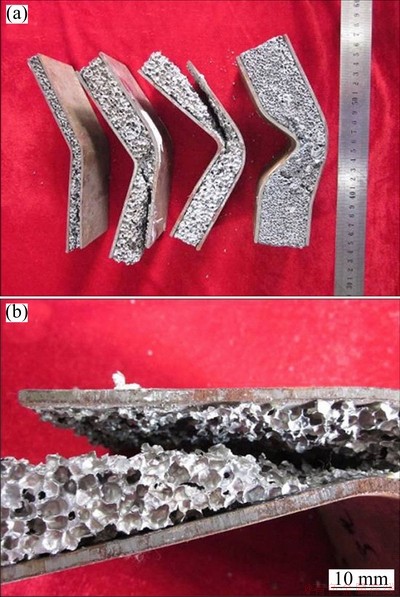
Fig. 6 Macroscopic graphs of failed AFSS with different sizes (a) and fracture of interfacial region (b)
According to above analysis, the bending resistance of AFSS mostly depends on the structure and defects of foam core. Figure 7(a) shows the SEM image of aluminum foam wall far from the fracture position, representing the typical Al-Si eutectic texture with some microcracks and voids. Owing to the small size of defects, there is a modest effect on the bending deformation. By contrast, the microstructure of foam wall near the fracture shown in Fig. 7(b) indicates that a crack with size of nearly 300 μm is propagating along the crack tip. It can be ascribed that the certain size of crack suffers some stress concentration from the external load [17]. The crack propagation due to the stress concentration rapidly aggravates with increasing bending load, and finally leads to the structural failure of AFSS.
The foam core fabricated by melt foaming method can be influenced by the cooling procedure. Figure 8(a) shows another typical microstructure of foam wall near the fracture which belongs to the AFSS with 6 mm panel and 40 mm foam core. It is different from that in Fig. 7(a). The reason may be that the surface of foam core gets a drastic cooling and rapidly solidifies due to the whole spray cooling technique. Therefore, the flow morphology at liquid state can be kept in the foam structure, as shown in Fig. 8. In addition, some internal stresses due to the unbalanced cooling exist in the foam core and result in some defects, such as microcracks and voids [6]. The cracks in Fig. 8(b) merge under bending deformation and cause the foam core to fracture. Consequently, the efficient structure and limited defects of aluminum foam core significantly influence the bending strength of AFSS.
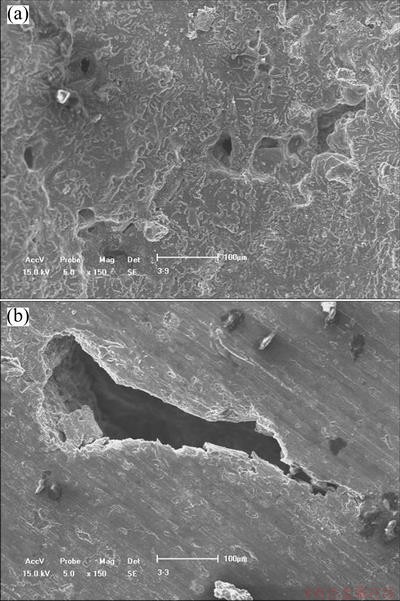
Fig. 7 SEM images of foam wall far from fracture (a) and near fracture (b)
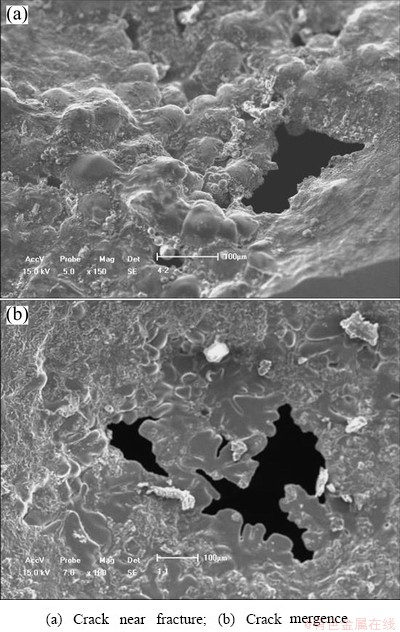
Fig. 8 SEM images of foam wall near surface of foam core with drastic cooling
4 Conclusions
1) The maximum bending load increases with the increase of thicknesses of both steel panel and foam core.
2) The failure mode of AFSS can be expressed as the initial crush and shear damage of foam core, and delamination of glued interface at large bending loads. The crack with certain size on the foam wall developed in the cooling process of melting foam craft is major factor for the failure of foam core.
3) There is an optimal specific bending strength of AFSS with thick foam core and thin steel panel. The maximum bending load of that with 8 mm panel and 50 mm foam core is 66.06 kN.
References
[1] GIBSON L J. Mechanical behavior of metallic foams [J]. Annu Rev Mater Sci, 2000, 30(1): 191-227.
[2] SUGIMURA Y, MEYER J, HE M Y, BARTSMITH H, GRENSTEDT J, EVANS A G. On the mechanical performance of closed cell Al alloy foams [J]. Acta Mater, 1997, 45(12): 5245-5259.
[3] BROTHERS A H, DUNAND D C. Mechanical properties of a density-graded replicated aluminum foam [J]. Mater Sci Eng A, 2008, 489(1-2): 439-443.
[4] BANHART J, SEELIGER H W. Aluminium foam sandwich panels: Manufacture, metallurgy and applications [J]. Adv Eng Mater, 2008, 10(9): 793-802.
[5] SALVO L, BELESTIN P, MAIRE E, JACQUESSON M, VECCHIONACCI C, BOLLER E, BORNERT M,DOUMALIN P. Structure and mechanical properties of AFS sandwiches studied by in-situ compression tests in X-ray microtomography [J]. Adv Eng Mater, 2004, 6(6): 411-415.
[6] LEHMHUS D,BUSSE M,CHEN Y,BOMAS H,ZOCH H W. Influence of core and face sheet materials on quasi-static mechanical properties and failure in aluminium foam sandwich [J]. Adv Eng Mater, 2008, 10(9): 863-867.
[7] NAMMI S K, MYLER P, EDWARDS G. Finite element analysis of closed-cell aluminium foam under quasi-static loading [J]. Mater Des, 2010, 31(2): 712-722.
[8] BANHART J. Manufacture, characterisation and application of cellular metals and metal foams [J]. Prog Mater Sci, 2001, 46(6): 559-632.
[9] BASTAWROS A F, BART-SMITH H, EVANS A G. Experimental analysis of deformation mechanisms in a closed-cell aluminum alloy foam [J]. J Mech Phys Solids, 2000, 48(2): 301-322.
[10] JEON I, ASAHINA T. The effect of structural defects on the compressive behavior of closed-cell Al foam [J]. Acta Mater, 2005, 53(12): 3415-3423.
[11] BELE E, BOUWHUIS B A, CODD C, HIBBARD G D. Structural ceramic coatings in composite microtruss cellular materials [J]. Acta Mater, 2011, 59(15): 6145-6154.
[12] PAUL A, SESHACHARYULU T, RAMAMURTY U. Tensile strength of a closed-cell Al foam in the presence of notches and holes [J]. Scripta Mater, 1999, 40(7): 809-814.
[13] MU Y L, YAO G C, LUO H J. Effect of cell shape anisotropy on the compressive behavior of closed-cell aluminum foams [J]. Mater Des, 2010, 31(3): 1567-1569.
[14] ZU G Y, SONG B N, ZHONG Z Y, LI X B, MU Y L, YAO G C. Static three-point bending behavior of aluminum foam sandwich [J]. J Alloy Compd, 2012, 540: 275-278.
[15] GUPTA N,RICCI W. Comparison of compressive properties of layered syntactic foams having gradient in microballoon volume fraction and wall thickness [J]. Mater Sci Eng A, 2006, 427(1): 331-342.
[16] NEMAT-NASSER S, KANG W, MCGEE J, GUO W G, ISAACS J. Experimental investigation of energy-absorption characteristics of components of sandwich structures [J]. Int J Impact Eng, 2007, 34(6): 1119-1146.
[17] MARKAKI A,CLYNE T. The effect of cell wall microstructure on the deformation and fracture of aluminium-based foams [J]. Acta Mater, 2001, 49(9): 1677-1686.
钢面板泡沫铝夹心板的三点弯曲行为
祖国胤,卢日环,李小兵,仲照阳,马幸江,韩明博,姚广春
东北大学 材料与冶金学院,沈阳 110819
摘 要:采用胶粘法制备大尺寸钢质泡沫铝夹心板,测试夹心板的三点弯曲强度,分析面板厚度、芯层厚度对夹心板弯曲性能的影响规律,研究弯曲载荷作用下的夹心板失效机理。结果表明:钢质泡沫铝夹心板可承受很高的弯曲载荷,夹心板抗弯强度随着芯层泡沫铝厚度的提高而提高。增加钢面板的厚度,夹心板抗弯强度整体呈增强趋势。当面板厚度为8 mm、芯层厚度为50 mm时,夹心板的极限抗弯强度可达66.06 kN。芯层泡沫铝内泡壁表面的大尺寸裂纹是夹心板在弯曲载荷作用下失效的主要原因;采用熔体发泡法制备的泡沫铝板材,因冷却强度过大而导致的附加应力使泡壁的强度下降,也是影响夹心板力学性能的主要因素。
关键词:泡沫铝夹心板;三点弯曲;失效机理;面板厚度
(Edited by Xiang-qun LI)
Foundation item: Projects (U1332110, 50704012) supported by the National Natural Science Foundation of China; Project (F10-205-1-59) supported by Science and Technology Foundation of Shenyang, China
Corresponding author: Guo-yin ZU; Tel: +86-24-83686462; Fax: +86-24-83682912; E-mail: zugy@smm.neu.edu.cn
DOI: 10.1016/S1003-6326(13)62759-4