
Effect of high intensity conditioning on aggregate size of fine sphalerite
SUN Wei(孙 伟), XIE Ze-jun(谢泽军), HU Yue-hua(胡岳华),
DENG Mei-jiao(邓美姣), YI Luan(易 峦), HE Guo-yong(何国勇)
School of Mineral Processing and Bioengineering, Central South University, Changsha 410083, China
Received 31 May 2007; accepted 11 October 2007
Abstract: High intensity conditioning(HIC) was used as a model to study the fundamental of fine sulphide particle flotation. The effect of impeller design, mechanical energy input, and agitation speed on aggregate size of fine sphalerite was tested. The aggregate size of fine sphalerite was measured with the Malvern Hydro 2000 Mastersizer. The results show that the size of aggregates of sphalerite particles ground for 3 min can be enlarged significantly with the activator and collector addition in HIC using the high energy impeller. The improved particle aggregation by using the high energy impeller is not directly related to a higher energy input into the system. With the same energy input into HIC, the aggregate size obtained with the high energy impeller is much coarser than that obtained with the low energy impeller. With the new impeller in HIC, the sphalerite aggregate size decreases with increasing agitation speed from 700 to 2 500 r/min. However, the recovery does not decrease until the agitation speed reaches 2 500 r/min.
Key words: high intensity conditioning; sphalerite; fine particle flotation; impeller design; image analysis; mechanical energy input; agitation speed
1 Introduction
With the depletion of high grade ore deposits, finely disseminated, low grade ores have to be processed in many mineral industries. However, in order to achieve acceptable liberation for these ores, extensive grinding is often inevitable, producing a large proportion of fine particles below 10 μm in size. From image analysis of Missouri lead ore tailings, for example, CORNELL and O’CONNOR[1] reported that the tailings must be reground to 20 μm or less to liberate sulfide values for subsequent separation. YOON et al[2] also reported that ideal particle liberation to produce a clean coal containing less than 2% ash content was achieved only after grinding the particles below 10 μm in size.
Flotation, as a dominant separation technique, has been employed by the mineral industries to recover the fine valuable mineral particles. It has been well documented that for a wide variety of minerals, reagent combinations and flotation machines, flotation is more efficient for particles in the size range of 10-100 μm [3-5]. The particles of size less than 10 μm can be detrimental to flotation, resulting in low recovery due to reduced flotation rates, poor selectivity due to mechanical entrainment of fine gangue particles and slime coating, and excessive reagent consumption due to an increased solid/liquid interfacial area[6]. Extensive research has been devoted to fine particle flotation in order to overcome these recognized difficulties. A notable contribution among different approaches is the development of new flotation devices, including the Leeds flotation column[7], air-sparged hydrocyclone[8], free jet type flotation cell[9], static flotation apparatus [10], packed column[11], microbubble flotation column [12], Jameson cell[13], centrifugal force field flotation cell[14] and feed-line aeration flotation column[15]. These evolutional devices have shown some degree of success in some applications. Process developments including carrier flotation[16-17], shear-flocculation flotation[18], selective flocculation flotation[19-24], oil agglomeration flotation[25-26], hydrodynamic cavitation flotation[27] and high intensity conditioning [28-30] have also advanced fine particle flotation technology in a number of cases. However, full potential and general acceptance of these developments by the industry remains to be realized as we progress in the fundamental understanding of fine particle flotation processes. Determining the role of shear-induced aggregation and hydrodynamic cavitation in high intensity conditioning serves as an example. The fundamental knowledge and direct scientific evidence in this area are rather limited. In this study, we used high intensity conditioning as a model to study the fundamentals of fine sulphide particle flotation.
2 Experimental
2.1 Sample
We used sphalerite as example mineral, which was provided by Matagami Corp. The sample was crushed in turn by jaw crusher, cone crusher and disk crusher to a size below 0.5 mm of 80%. The major metallic element components of the sample are listed in Table 1, which were got from an absorption spectrophotometer analysis.
Table 1 Major metallic elements component of sphalerite sample (mass fraction, %)

Before high intensity conditioning, the sample was ground with an agitation mill to a size less than 7.9 μm.
2.2 Image analysis and processing
A CPL high speed camera with a 75 mm lens at F5.6 and 1000 f/s shutter speed was used to image aggregates. Aggregates were sampled from conditioning cell into a silica glass tank, which was back illuminated on a refraction screens located behind the sample tank that provided very even illumination. Aggregate images were directly captured and analyzed. Pixel resolution was calibrated by imaging a ruler located in the plane of the rising aggregates.
2.3 Particle size measurement
The aggregate size was measured with the Malvern Hydro 2000 Mastersizer.
3 Result and discussion
3.1Effect of impeller design on aggregates size of fine sphalerite
The effect of different types of impellers on fine particle flotation has been reported recently[30-31]. Clearly, people have recognized that the design of the impeller and the subsequently created fluid flow conditions can have a distinct impact on the particle- particle and particle-bubble interactions. Based on the analysis described above and the fundamental knowledge accumulated during previous shear flocculation studies, a simpler impeller was made in this study. Fig.1 shows the photographs of the low energy impeller and high energy impeller. These two impellers have the same diameter of 50 mm, height of 5 and 8 mm, respectively.
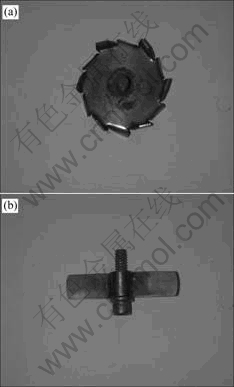
Fig.1 Photographs of low energy impeller (a) and high energy impeller (b)
Fig.2 shows a comparison of particle aggregation of ground sphalerite by HIC using different impellers at 700 r/min, corresponding to an energy input of 1.9 and 7.5 kW?h/m3 for the low energy and high energy impellers, respectively. The aggregate size was measured with the Malvern Hydro 2000 Mastersizer.
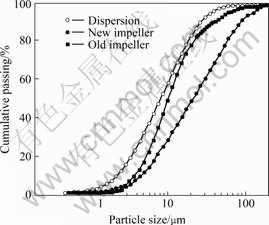
Fig.2 Particle size distribution of fine sphalerite aggregates determined by Malvern Mastersizer (Aggregation was formed by HIC at 700 r/min for 10 min using two different impellers in presence of one dose activator and collector addition. Sphalerite sample was ground for 3 min at 480 r/min with ceramic media)
As shown in Fig.2, a much larger aggregate size is obtained by using the high energy impeller compared with the low energy impeller. For a feed of fine sphalerite with d20=3 μm, d50=8 μm and d80=17 μm, HIC with the low energy impeller only increases the aggregate size by 2 μm, i.e. d20=5 μm, d50=10 μm and d80=19 μm. This marginal increase in aggregate size appears to be related to the increased hydrophobicity of particles with the addition of one dose activator and collector. However, by using the high energy impeller, the measured aggregate sizes become d20=7 μm, d50= 20 μm and d80=50 μm with the same level chemical addition. Since the high energy impeller incurs a higher energy dissipation rate, it is evident that a higher energy input under a given pulp chemistry condition is beneficial for fine particle aggregation. This observation is consistent with that previously reported in literature.
Fig.3 shows a snapshot of images recorded by the on-line visualization system with and without chemicals during HIC using the two different impellers. Under dispersion conditions, there is no noticeable difference in the size of aggregates formed in HIC using two different impellers. With the addition of one dose activator and collector, more large aggregates (as large as 100 μm) are observed using the high energy impeller than the low energy impeller in HIC. Such a significant increase in the aggregate size would enhance the sphalerite flotation kinetics. This finding is in line with the results obtained by HU et al[31]. In their study, different flotation recoveries of fine wolframite (<5 μm) were obtained by using impellers of different designs.
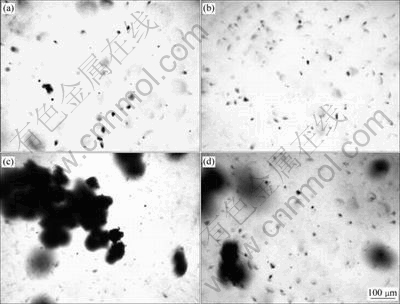
Fig.3 Snapshot of images after HIC using two different impellers: (a, b) Without chemicals; (c, d) With chemicals; (a, c) New impeller; (b, d) Old impeller
3.2 Effect of mechanical energy input on aggregates size of fine sphalerite
As shown above, fine sphalerite becomes much more aggregated in HIC with the high energy impeller than that with the low energy impeller. In the case of low energy impeller, only marginal aggregation is observed. Since the high energy impeller provides a higher energy input than the low energy impeller for a given agitation time at a fixed rotation speed, the improved aggregation with the high energy impeller may be due to a higher mechanical energy input into the system.
To further confirm that the degree of aggregation by HIC is indeed related to the energy input, the aggregation tests were performed with both the low and high energy impellers for the same energy input by changing either impeller rotation speed or agitation time. The results obtained at an energy input of 7.53 kW?h/m3 are shown in Fig.4. To have this level of energy input, the agitation was performed at 700 r/min for 10 and 40 min with the high energy and low energy impellers, respectively. Alternatively, a rotational speed of 1 500 r/min for 10 min using the low energy impeller would provide the same level of energy input. For comparison, the results obtained with the low energy impeller at 700 r/min for 10 min, equivalent to an energy input of 1.9 kW?h/m3, are also included in this figure.
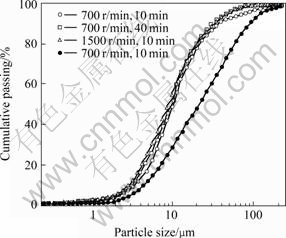
Fig.4 Particle size distribution of fine sphalerite aggregates determined by Malvern Mastersizer (HIC was performed with one dose chemical addition at two different energy input levels of 1.9 and 7.5 kW?h/m3, provided by low energy impeller (open symbols) and high energy impellers (filled symbols))
As shown in Fig.4, increasing the energy input from 1.9 to 7.5 kW?h/m3 by increasing the agitation time from 10 to 40 min using the low energy impeller at an agitation speed of 700 r/min causes little change in aggregate size distribution. Similarly, increasing the agitation speed to 1 500 r/min for the same period (10 min) of agitation to reach an input energy level of 7.5 kW?h/m3 with the low energy impeller shows little change in aggregate size distribution. This finding indicates that the low energy impeller is indeed not effective for inducing particle aggregation, regardless of the energy input provided. However, at the same energy input level of 7.5 kW?h/m3 using the high energy impeller, the aggregate size is significantly greater than that obtained with the low energy impeller. This observation suggests that the energy dissipation pattern plays a more significant role than total energy input in fine particle aggregation. It is evident that the slurry flow pattern created by impeller design determines the hydrodynamic force, which balances molecular forces of colloidal particles and hence the degree of aggregation. An important implication from this finding is that to fully utilize the advantages of high intensity conditioning in fine particle aggregation and flotation, a suitable design of the impeller and a favourable hydrodynamic environment are of critical importance. It is therefore highly desirable to establish a correlation between the energy input and the aggregate size in the context of impeller designs and fluid flow patterns.
3.3Effect of agitation speed
For a typical shear flocculation system, the effect of agitation speed or shear rate on particle aggregation has been well established. There exists a threshold level of agitation speed, at which the maximum size aggregates can form. Under turbulent flow conditions as used in our HIA system, such a relation may be extremely complex and difficult to establish, but the general trend similar to the shear flocculation should still be valid. Fig.5 shows the size distribution of aggregates formed in HIA with the high energy impeller at different agitation speeds.
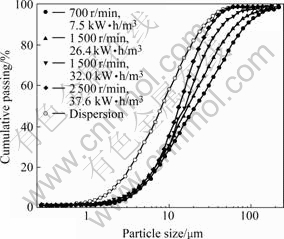
Fig.5 Particle size distribution of fine sphalerite aggregates (Aggregates of sphalerite particles ground for 3 min were formed by HIC using high energy impeller at different agitation speeds with one dose chemical addition)
Although there is a negligible difference in the aggregate size distribution below 10 μm, the aggregates larger than 20 μm become progressively more finely distributed with increasing the agitation speed. For example, d80 decreases from 50 to 20 μm when the agitation speed increases from 700 to 2 500 r/min, equivalent to an energy input increase from 7.5 to 37.6 kW?h/m3. The effect of agitation speeds on particle size distribution and morphology of aggregates is confirmed by the images recorded with the on-line visualization system. As shown in Fig.6, the aggregate size decreases with increasing the agitation speed while the aggregate morphology remains the same.
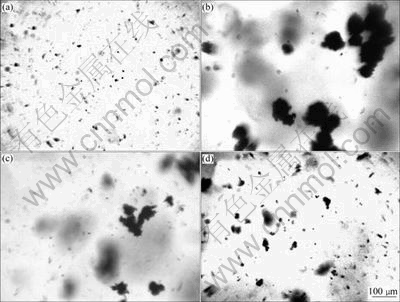
Fig.6 Photographs of fine sphalerite aggregates formed by HIC with high energy impeller at different agitation speeds: (a, b) 700 r/min; (c) 1 500 r/min; (d) 2 500 r/min (all with one dose chemical addition, except for (a) in which no chemicals were added)
The corresponding effect of agitation speed on flotation recovery is shown in Fig.7. When the agitation speed in HIC with the high energy impeller increases from 700 to 2 000 r/min, the change in flotation recovery is negligible. A further increase in agitation speed to 2 500 r/min, however, causes a noticeable reduction in flotation recovery. Considering a progressive reduction in aggregate size with increasing agitation speed of HIC, in contrast to a sudden reduction in recovery at an agitation speed above 2 000 r/min, it appears that there is a critical aggregate size around 10 mm below which flotation becomes drastically ineffective.
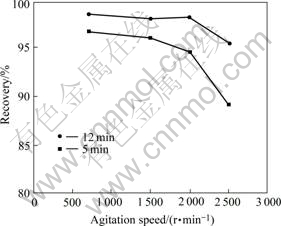
Fig.7 Effect of agitation speed in HIC with high energy impeller on flotation recovery of fine sphalerite with one dose activator and collector addition using a Denver flotation cell
The results presented here clearly demonstrate a significant role of impeller design in enhancing fine particle aggregation and flotation. A great deal of efforts has been devoted to examining the effect of turbulence- controlled micro-processes in flotation machines on particle-bubble interactions[32]. The reality is that there is still a long way to go to establish what kind of impeller design, cell structure and fluid flow pattern could benefit the fine particle aggregation and flotation. The complex interconnection of the impeller design, energy input and fluid flow conditions can be well illustrated from a well-known example of daily life: a food blender used in kitchen. Even with a single type of the impeller installed for a given feed blender, by applying different levels of energy to cause different fluid flow patterns, the feed blender can function to chop, grind, mix, etc. It seems that to fully understand the role of impeller design and fluid flow patterns in enhancing fine particle aggregation and flotation is very important.
4 Conclusions
1) High energy impeller was manufactured for the purpose of promoting fine particle aggregation under HIC. The results show that the aggregates of sphalerite particles ground for 3 min could be enlarged significantly with the activator and collector addition in HIC using the high energy impeller.
2) The improved particle aggregation by using the new impeller is not directly related to a higher energy input into the system. With the same energy input into HIC, the aggregate size obtained with the high energy impeller is much coarser than that obtained with the low energy impeller.
3) With the new impeller in HIC, the sphalerite aggregate size decreases with increasing agitation speed from 700 to 2 500 r/min. However, the recovery does not decrease until the agitation speed reaches 2 500 r/min.
References
[1] CORNELL W L, O’CONNOR W K. Using image analysis to determine liberation sizes in a bulk sulfide concentrate from Missouri lead ore tailings [C]// VASSILIOU A H, HAUSEN D M, CARSON D J T, ed. Process Mineralogy VII. Proceedings of the Metallurgical Society Annual Meeting. Denver, Colorado, 1987: 461-474.
[2] YOON R H, LUTTRELL G H, ADEL G TM, TRIGG R D. Cleaning of ultra fine coal by micro bubble flotation [C]// Proceedings of First Annual Pittsburgh Coal Conference. Pittsburgh, Pennsylvania, 1984: 880-896.
[3] TRAHAR W J. A rational interpretation of the role of particle size in flotation [J]. International Journal of Mineral Processing, 1981, 8: 289-295.
[4] KUSAKA E, ARIMOTO Y, NAKAHIRO Y, WAKAMATSU T. Collectorless liquid-liquid extraction of fine mineral particles using various organic liquids as the oil phase [J]. Minerals Engineering, 1994, 7(1): 39-48.
[5] SINGH R, RAO S S, MAULIK S C, CHAKRAVORTY N. Fine particles flotation–Recent trends [J]. Transactions of the Indian Institute of Metals, 1997, 50(5): 407-419.
[6] FUERSTENAU D W. Flotation science and engineering advances and challenges [C]// FORSSBERG E, ed. Proceedings of XVI International Mineral Processing Congress. Amsterdam: Elsevier Science Publishers B. V., 1988: 63-80.
[7] DELL C C, JENKINS B W. The Leeds flotation column [C]// Proceedings of 7th International Coal Preparation Congress. Australia, 1976: 153-168.
[8] MILLER J D, VAN CAMP M. Fine coal flotation in a centrifugal field with an air sparged hydrocyclone [J]. Minerals Engineering, 1982, 61(3): 1575-1580.
[9] ALIZADEH A, SIMONIS W. Flotation of finest and ultra-finest size coal particles [J]. Aufbereitungs-Technik, 1985, 6: 363-366.
[10] VARBANOV R, NIKOLOV D, BALINOVA S, BALINOV B. Model investigation of static flotation [J]. Institution of Mining and Metallurgy, 1985, 3: 125-127.
[11] YANG D C. Column Froth Flotation. US 4592834 [P]. 1986-06-03.
[12] YOON R H, ADEL G T, LUTTRELL G H. Development of the microbubble column flotation process [C]// Proceedings of Second International Conference on Processing and Utilization of High-Sulfur Coals. Carbondale, Illinois, 1987: 179-200.
[13] JAMESON G J. A new concept in flotation column design, in column flotation [C]// SASTRY K V S, ed. Proceedings of SME Annual Meeting. Phoenix, Arizona, 1988: 281-286.
[14] TILS H M G C, TELS M. A study into fine particle flotation separation characteristics with application to centrifugal force field flotation cells [J]. International Journal of Mineral Processing, 1992, 36: 201-217.
[15] XU M, QUINN P, STRATTON-CRAWLEY R. A feed-line aerated flotation column (Part 1): Batch and continuous testwork [J]. Minerals Engineering, 1996, 9(5): 499-507.
[16] SOMASUNDARAN P. Principles of selective aggregation [M]// SOMASUNDARAN P, ARBITER M, ed. Beneficiation of Mineral Fines – Problems and Research Needs. New York: AIME, 1976: 183-196.
[17] CRISTOVEANU I E, MEECH J A. Carrier flotation of hematite [J]. CIM Bulletin, 1985, 78: 35-42.
[18] WARREN L J. Shear–flocculation of ultrafine scheelite in sodium oleate solutions [J]. Colloid Interface Sci, 1975, 50: 307-315.
[19] YARAR B, LEE Y J. Selective flocculation of minerals (1): Basic principles [J]. Trans Inst Min Metall, 1970, 79: C23-C33.
[20] YARAR B, KAOMA J. Selective flocculation of minerals (2): Experimental investigation of quartz, calcite, and galena—Discussion [J]. Trans Inst Min Metall, 1970, 79: C173-C178.
[21] ATTIA Y A. Development of a selective flocculation process for a complex copper ore [J]. Int J Miner Process, 1977, 4: 209-225.
[22] RUBIO J, MARABINI A M. New basis for selective flocculation of mineral slimes [J]. Trans Inst Min Metall, 1977, 86: C97-C100.
[23] OSBORNE D G. Recovery of slimes by a combination of selective flocculation and flotation [J]. Trans Inst Min Metall, 1978, 87: C189-C193.
[24] SRESTY G C, SOMASUNDARAN P. Selective flocculation of synthetic mineral mixtures using modified polymers [J]. Int J Miner Process, 1980, 6: 303-320.
[25] HOUSE C I, VEAL C J. Selective recovery of chalcopyrite by spherical (oil) agglomeration [J]. Minerals Engineering, 1989, 2(2): 171-184.
[26] DRZYMALA J. Oil agglomeration of sulfurized pyrite [J]. Minerals Engineering, 1991, 4(2): 161-172.
[27] ZHOU Z A, XU Z, FINCH J A, HU H, RAO S R. Role of hydrodynamic cavitation in fine particle flotation [J]. International Journal of Mineral Processing, 1997, 51: 139-149.
[28] HEYES G W, PHELAN J M. The application of separate conditioning to improve zinc metallurgy at Woodlawn Mines [C]// Proceedings of Third Mill Operators Conference. Cobar: Australian Institute of Mining and Metallurgy, 1988: 85-92.
[29] BULATOVIC S M, SALTER R S. High intensity conditioning – A new approach to improving flotation of mineral slimes [C]// Conference of Metallurgists, Processing of Complex Ores. Halifax, Canada, 1989: 169-175.
[30] ENGEL M D, MIDDLEBROOK P D, JAMESON G J. Advances in the study of high intensity conditioning as a means of improving mineral flotation performance [J]. Minerals Engineering, 1997, 10(1): 55-68.
Foundation item: Project(50674103) supported by the National Natural Science Foundation of China; Project(2005CB6237601) supported by the National Basic Research Program of China
Corresponding author: SUN Wei; Tel/Fax: +86-731-8879815; E-mail: sunmenghu2002 @163. com
(Edited by YUAN Sai-qian)