
High cycle fatigue behavior of the second generation single crystal superalloy DD6
SHI Zhen-xue, LI Jia-rong, LIU Shi-zhong, HAN Mei
National Key Laboratory of Science and Technology on Advanced High Temperature Structural Materials,
Beijing Institute of Aeronautical Materials, Beijing 100095, China
Received 20 May 2010; accepted 17 September 2010
Abstract: The second generation single crystal superalloy DD6 with 0.10%Hf and 0.34%Hf (in mass fraction) was subjected to high-cycle fatigue (HCF) loading at temperatures of 700 °C in ambient atmosphere. SEM was used to determine the initiation site and the failure mechanism. Evolution of the microstructure was investigated by TEM observation. The results show that fatigue limit of DD6 alloy with 0.34%Hf is a little smaller than that of the alloy with 0.10%Hf. The fatigue cracks initiated on the surface or near the surface of the specimens. The crack would propagate along {111} octahedral slip planes, rather than perpendicular to the loading axis of specimen. Typical fatigue striation formed in steady propagation of fatigue crack. The fracture mechanisms of the high cycle fatigue of DD6 alloys with 0.10%Hf and 0.34%Hf are quasi-cleavage fracture. Different types of dislocation structures were developed during high cycle fatigue deformation.
Key words: Hf; single crystal superalloy; DD6; high cycle fatigue
1 Introduction
In recent years, Ni-based single crystal superalloys have been widely used as turbine blade materials for advanced aircraft engines. Vibration in gas turbine engines is a potential cause for high cycle fatigue failure of turbine airfoils during engine operation[1-2]. Hence, the fatigue behavior of single crystal superalloys loaded by vibratory stresses is a major concern regarding the safety and reliability of gas turbine engines. Therefore, study on high cycle fatigue behavior of the single crystal superalloys becomes important.
As turbine blade geometries become more complex and larger, it is inevitable to form low angle grain boundary in casting process of single crystal superalloys[3]. Recently, grain boundary strengthening by additions of Hf, C, B and Zr has become a considerable research subject to deal with low angle grain boundary problems. ROSS and O′HARA[4], in their study of the alloy René N4, concluded that addition of minor elements at low level can enhance the grain boundary tolerance to 12°. In the modified PWA1483 with deliberate additions of Hf and B, there was no significant drop in creep strength even with grain boundary misorientation as high as 25°[5]. CMSX-486 alloy with full grain boundary strengthening elements shows no reduction in properties to 18° misorientation[6]. Other similar studies had been carried out[7-8].
DD6 is the second generation single crystal superalloy developed by Beijing Institute of Aeronautical Materials, and has many advantages such as high strength at elevated temperature, excellent comprehensive performance and good microstructure stability[9-10]. Effect of Hf content on the microstructures and stress rupture properties of DD6 single crystal superalloy has been investigated[11-12]. The purpose of this study is to evaluate the effect of hafnium addition on the high cycle fatigue properties and fracture characteristics of DD6 alloy. Further experiments would be carried out to assess the effect of Hf content on the strength of low angle boundary of DD6 alloy.
2 Experimental
The master alloy of DD6 alloy was smelted in a vacuum induction furnace. Hf in different contents was separately added in the molten alloy while contents of other elements were basically kept unchanged. The single crystal superalloy specimens with [001] orientation were cast by crystal selection method in the directionally solidified furnace with high temperature gradient. The chemical compositions of test alloys were analyzed by chemical analysis methods. Hf contents of two alloys were 0.10% and 0.34% (in mass fraction), respectively. The crystal orientations of the specimens were determined by Laue X-ray back reflection method, and the crystal orientation deviations of the specimens were maintained within 10° to the [001] orientation. The heat treatments of the specimens were carried out according to following heat treatment regime: (1 290 °C, 1 h)+(1 300 °C, 2 h)+(1 315 °C, 4 h, AC)+(1 120 °C, 4 h, AC)+(870 °C, 32 h, AC).
The standard cylindrical specimens for high cycle fatigue test were machined after heat treatment. All those specimens were fatigue tested under load control at a stress ratio R=σmin/σmax=-1 and a frequency of 30 Hz. Those tests were conducted at 700 °C in ambient atmosphere. Rotary bending loading mode was adopted and sinusoidal waveform was performed on the specimens. Fracture surfaces were examined using scanning electron microscope (SEM) after ultrasonic cleanout. Thin foils for transmission electron microscopy (TEM) observation were all cross-sectioned near the fracture surfaces and then prepared by twin-jet polishing method.
3 Results and discussion
3.1 Stress—fatigue life curve
S—N results of fatigue testing for DD6 alloys with 0.1%Hf and 0.34%Hf are shown in Fig.1. The arrows indicate that the specimens are not failure during fatigue tests. Fatigue strength at the 107th cycle is usually defined as the fatigue limit. As can be seen from Fig.1, S—N curves show a general trend that the fatigue life increases with decreasing cyclic stress amplitude. As for alloys with 0.10%Hf and 0.34%Hf, the fatigue limits are 460 and 440 MPa, respectively; indicating that the fatigue limit decreases a little with increasing Hf content.

Fig.1 Relationship between fatigue life and total stress amplitude for DD6 alloys with different Hf contents at 700 °C
The S—N curves were obtained by non-linear fitting with the Basquin equation[13], which can be written as
(1)
where σa is the alternating stress; σ′f is the fatigue strength coefficient; Nf is the number of cycles to failure; and b is the Basquin exponent. Values of σ′f and b calculated are listed in Table 1. It can be seen that σ′f drops and b rises with increasing Hf content.
Table 1 High cycle fatigue parameters of DD6 alloys with different Hf contents

3.2 Fractograph
Fracture surfaces of those alloys with different Hf contents are shown in Fig.2. Analyses on fractographs reveal that crack initiated on or near the surface without evidence of crack initiation from interior of the specimen. The specimen surface was oxidized during fatigue at 700 °C, forming a thin layer on the surface, from which the crack apparently originated, as shown in Figs.2(a) and (c) (short arrows). Crack initiation occurred at microporosity of subsurface, as shown in Figs.2(e) and (f). Such behavior has been documented for the single crystal superalloy CMSX-4[14]. All the cracks are prone to initiate on or near the specimen surface because the cyclic plastic deformation on or near the surface is higher than the interior one due to the reduced constraint of the surface layer. In the rotary bending loading mode, the specimen surface acquires the maximum cyclic stress compared with internal region.
In the range of current research, Hf content has very little effect on the fractograph. There are mainly two cases for the fracture surfaces of the alloy with Hf: some fracture surfaces consist of one plane and the others consist of several planes. The plane of crack propagation inclines approximately 50° to the [001] orientation, suggesting that crack growth occurs on {111} octahedral planes, rather than perpendicular to the loading axis. The matrix of DD6 alloy is of face-centered cubic structure and easy slipping systems are identified as {111} <110> at mediate temperatures, demonstrating that the fatigue crack is growing along {111} planes[15]. It was reported that the nickel-based superalloy might exhibit a faceted failure mode in which the facets display features of quasi-cleavage fracture[16]. As shown in Figs.2(a) and (c), the most evident feature on the fracture surfaces is the significant quasi-cleavage fracture along {111} planes. As shown in Figs.2(b) and (d), the most part of the fracture surfaces are occupied by plane with facets connected with ridges. The formation of those ridges was brought about by the simultaneous slip on different {111} planes[17]. It is evident from the specimen that the slip traces are shown on the slip plane, as shown in Fig.3. The presence of slip traces on the fracture surfaces provides another evidence for cyclic plastic deformation.
At the crack propagation stage, feature fatigue striations on the fracture surface can be seen in Fig.4. The direction of fatigue crack propagation is made out from the striations which are evidences of fatigue rupture. With the increase in the distance between two striations, the crack growth rate increases at the crack propagation stage. The long arrows in Fig.4 indicate the direction of fatigue crack propagation. Some secondary cracks were also observed in the crack propagation stage, as shown in Fig.5. At the end of crack propagation stage, the stepwise feature on the fracture surface can be seen in Fig.6. The planes forming into stepwise are also {111} octahedral planes.
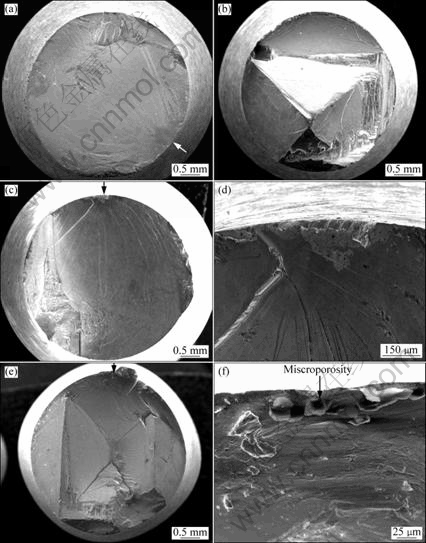
Fig.2 Fracture surfaces of alloys: (a) 0.10% Hf, Δσ/2=460 MPa, Nf=8.2×106; (b) 0.10% Hf, Δσ/2=500 MPa, Nf=3.5×105; (c), (d) 0.34% Hf, Δσ/2=480 MPa, Nf=5.2×106; (e), (f) 0.34% Hf, Δσ/2=460 MPa, Nf=1.71×106
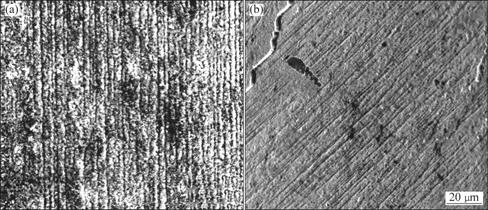
Fig.3 Slip bands on fracture surfaces of alloys: (a) 0.10%Hf, Δσ/2=460 MPa, Nf=8.2×106; (b) 0.34%Hf, Δσ/2=480 MPa, Nf=5.2×106
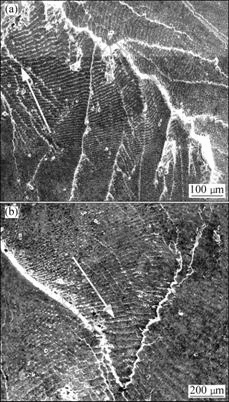
Fig.4 Fatigue striations on fracture surfaces of alloys: (a) 0.10%Hf, Δσ/2=460 MPa, Nf=8.2×106; (b) 0.34%Hf, Δσ/2=480 MPa, Nf=5.2×106
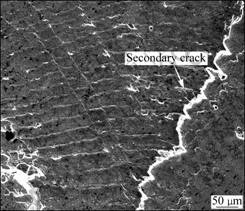
Fig.5 Secondary crack forming along fatigue striations (0.34%Hf, Δσ/2=480MPa, Nf=5.2×106)
3.3 Microstructure characterization
Figure 7 shows the microstructure of longitudinal section near fracture surface of the fatigue-ruptured specimens. It can be seen that nearly no change in shape and morphology of γ′ precipitates occurred during fatigue. The noticeable feature is that there is almost no residual eutectic in DD6 alloy with 0.10% Hf but there is a little amount of the residual eutectic for the alloy with 0.34% Hf. With increasing Hf content, the eutectic volume fraction increases because Hf lowers the liquidus temperature of the alloy. It is difficult for the high volume γ/γ′ eutectic to take into solution for avoiding incipient melting in the process of heat treatment, so a part of residual eutectics are preserved after heat treatment. The volume fraction of residual eutectics in DD6 alloy with 0.34%Hf is about 0.2%. It is possible that residual γ/γ′ eutectics near the specimen surface act as stress concentration sites and will become sites of crack initiation and easy ways for the crack propagation in fatigue test. WRIGHT et al[1] investigated the HCF for the single crystal superalloy PWA1484 and observed that fatigue crack initiated at residual eutectic[1]. Consequently, the fatigue limit of the alloy with 0.34%Hf exhibits a little smaller value than that of the alloy with 0.10%Hf.
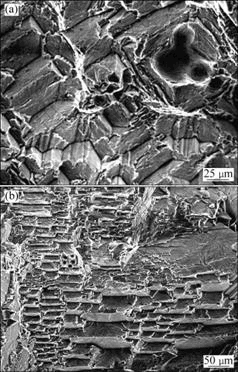
Fig.6 Cleavage steps on fracture surface: (a) 0.10%Hf, Δσ/2= 500 MPa, Nf=3.5×105; (b) 0.34%Hf, Δσ/2=460 MPa, Nf= 1.71×106
TEM observations were performed on the fatigued specimens. Dislocations in the specimens were inhomogenously distributed. Figures 8(a) and (b) show typical configuration of dislocations confined to the matrix of the alloy, but the dislocation density varied from place to place. They are the results of a cross slip. Such dislocations were generated as a result of multiple loops bowing out through the channels in the {111} planes, which can partially relieve the misfit at the γ/γ′ interfaces. No interfacial dislocation networks of high temperature creep were observed, indicating that no significant general plastic deformation occurred during fatigue. This is also supported by the observation that no change in the γ′ morphology occurred during fatigue, as shown in Figs.7(b) and (d).
With the constant accumulation of cyclic plastic deformation, the slip bands would be developed, as shown in Fig.8(c). The slip bands are filled with a large amount of dislocations. However, in the neighboring area of the slip bands, the density of dislocation is quite small. These bands would provide preferential sites for crack initiation and crack propagation along these bands would also be easier[18]. There was also evidence of particles sheared by single dislocation, dislocation pairs and super lattice stacking fault, as shown in Fig.8(d).
4 Conclusions
1) The fatigue limit of DD6 alloy with 0.34%Hf is a little smaller than that of the alloy with 0.10%Hf.
2) The fatigue strength coefficient drops and the Basquin exponent rises with increasing Hf content.
3) The fatigue crack initiation sites are mainly on surface or near surface of the specimens. The crack propagated along one or more intersecting {111} octahedral slip planes. Typical fatigue striations form on fatigue crack steady propagation.
4) The fracture mechanisms of high cycle fatigue of DD6 alloys with 0.10%Hf and 0.34%Hf are quasi- cleavage fracture.
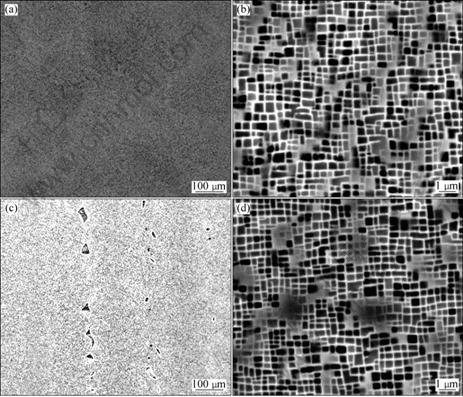
Fig.7 Microstructures of longitudinal sections near fracture surfaces of fatigue-ruptured specimens: (a), (b) 0.10%Hf; (c), (d) 0.34%Hf
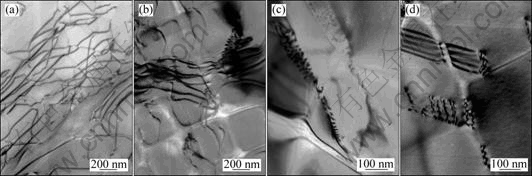
Fig.8 Dislocation configuration of alloys after fatigue fracture: (a) 0.10%Hf, Δσ/2=480 MPa, Nf=5.24×106; (b), (c) 0.34%Hf, Δσ/2=480 MPa, Nf=4.7×106; (d) 0.34%Hf, Δσ/2=460 MPa, Nf=1.71×106
References
[1] WRIGHT P K, JAIN M, CAMERON D. High cycle fatigue in a single crystal superalloy: time dependence at elevated temperature [C]//GREEN K A, POLLOK T M, HARADA H, HOWSON T W, REED R C, SCHIRRA J J, WALSTON S. Superalloys. Pennsylvania, PA: TMS, 2004: 657-666.
[2] LUKAS P, KUNZ L, SVOBODA M. High cycle fatigue of superalloy single crystals at high mean stress [J]. Materials Science and Engineering A, 2004, 387-389: 505-510.
[3] NEWELL M, DEVENDRA K, JENNINGS P A, D’SOUZA N. Role of dendrite branching and growth kinetics in the formation of low angle boundaries in Ni-base superalloys [J]. Materials Science and Engineering A, 2005, 412: 307-315.
[4] ROSS E W, O’HARA K S. René N4: First generation single crystal turbine airfoil alloy with improved oxidation resistance, low angle boundary strength and superior time rupture strength [C]// KISSINGER R D, DEYE D J, ANTON D L, CETEL A D, NATHAL M V, POLLOCK, T M, WOODFORD D A. Superalloys. Warrendale, PA: TMS, 1996: 19-25.
[5] SHAH D M, CETEL A. Evaluation of PWA1483 for large single crystal IGT blade applications [C]//POLLOCK T M, KISSINGER R D, BOWMAN R R, GREEN K A, MCLEAN M, OLSON S, SCHIRRA JJ. Superalloys. Warrendale, PA: TMS, 2000: 295-304.
[6] HARRIS K, WAHL J B. Improved single crystal superalloys, CMSX-4(CLS)[La+Y] and CMSX-486 [C]// GREEN K A, POLLOK T M, HARADA H, HOWSON T W, REED R C, SCHIRRA J J, WALSTON S. Superalloys. Pennsylvania, PA: TMS, 2004: 45-52.
[7] CHEN Q Z, JONE C N, KNOWLES D M. The grain boundary microstructures of the base and modified RR2072 bicrystal superalloys and their effects on the creep properties [J]. Materials Science and Engineering A, 2004, 385: 402-418.
[8] TAMAKI H, YOSHIMARI A, OKAYAMA A, NAKAMURA S. Development of a low angle grain boundary resistant single crystal superalloy YH61[C]//POLLOCK T M, KISSINGER R D, BOWMAN R R, GREEN K A, MCLEAN M, OLSON S, SCHIRRA J J. Superalloys. Warrendale, PA: TMS, 2000: 757-766.
[9] LI J R, ZHONG Z G, TANG D Z, LIU S Z, WEI P, WU Z T, HUANG D, HAN M. A low-cost second generation single crystal superalloy DD6 [C]//POLLOCK T M, KISSINGER R D, BOWMAN R R, GREEN K A, MCLEAN M, OLSON S, SCHIRRA J J. Superalloys. Warrendale, PA: TMS, 2000: 777-783.
[10] JIN Hai-peng, LI Jia-yong. Tensile properties of second generation single crystal superalloy DD6 after long term aging at high temperature [J]. Journal of Materials Engineering, 2007(3): 22-23. ( in Chinese)
[11] SHI Zhen-xue, LI Jia-rong, LIU Shi-zhong, LUO Yu-shi, ZHAO Jin-qian. Effects of Hafnium content on the as-cast microstructures of DD6 single crystal superalloy [J]. Rare Metal Materials and Engineering, 2010, 39(3): 490-493. ( in Chinese)
[12] SHI Z X, LI J R, LIU S Z, LUO Y S, ZHAO J Q. Effect of Hf on the microstructures and stress rupture properties of DD6 single crystal superalloy [J]. Rare Metal Materials and Engineering, 2010, 39(8): 1334-1338.
[13] ASTM. Annual book of ASTM standard, ASTM standard E606, vol.03.01 [R]. Philadelphia, PA, 1996.
[14] WASSON A J, FUCHS G E. The effect of carbide morphologies on elevated temperature tensile and fatigue behavior of a modified single crystal Ni-base superalloy [C]//REED R C, GREEN K A, CARON P, GABB P, FAHRMANN G, HURON E S, WOODARD S A. Superalloys. Pennsylvania, PA: TMS, 2008: 489-497.
[15] YI J Z, TORBET C J, FENG Q, POLLOCK T M, JONES J W. Ultrasonic fatigue of a single crystal Ni-base superalloy at 1000 °C [J]. Materials Science and Engineering A, 2007, 443: 142-149.
[16] M?LLER S, R?SLER J, SOMMER C, HARTNAGEL W. The influence of load ratio, temperature, orientation and hold time on fatigue crack growth of CMSX-4[C]//POLLOCK T M, KISSINGER R D, BOWMAN R R, GREEN K A, MCLEAN M, OLSON S, SCHIRRA JJ. Superalloys. Warrendale, PA: TMS, 2000: 347-355.
[17] LIU Y, YU J J, XU Y, SUN X F, GUAN H R, HU Z Q. High cycle fatigue behavior of a single crystal superalloy at elevated temperatures [J]. Materials Science and Engineering A, 2007, 454-455: 357-366.
[18] CHU Z K, YU J J, SUN X F, GUAN H R, HU Z Q. High cycle fatigue behavior of a directionally solidified Ni-base superalloy DZ951 [J]. Materials Science and Engineering A, 2008, 496: 355-361.
第二代单晶高温合金DD6的高周疲劳行为
史振学,李嘉荣,刘世忠,韩 梅
北京航空材料研究院 先进高温结构材料国防科技重点实验室, 北京 100095
摘 要:研究Hf含量为0.34%和0.10%Hf的第二代单晶高温合金DD6在700 °C的高周疲劳行为;采用扫描电镜对疲劳裂纹的萌生与失效机制进行分析,采用透射电镜研究变形后的显微组织。结果表明:含0.34%Hf的DD6合金比含0.10%Hf的合金的疲劳寿命稍有降低;疲劳裂纹萌生于试样表面、亚表面,沿{111}面扩展,而并不沿垂直应力轴方向扩展;断口上有典型的疲劳条带;Hf含量为0.34%和0.10%的DD6合金的高周疲劳断裂机制为类解理断裂。透射电镜分析表明,合金在循环变形中形成了不同形式的位错。
关键词:Hf;单晶高温合金;DD6;高周疲劳
(Edited by YANG Hua)
Corresponding author: SHI Zhen-xue; Tel: +86-10-62496338; Fax: +86-10-62496371; E-mail: shizhenxue@126.com
DOI: 10.1016/S1003-6326(11)60812-1