Article ID: 1003-6326(2005)05-1125-05
Effect of deformation temperature and strain rate on semi-solid deformation behavior of spray-formed Al-70%Si alloys
ZHANG Di(张 迪)1, YANG Bin(杨 滨)1, ZHANG Ji-shan(张济山)1,
ZHANG Yong-an(张永安)2, XIONG Bai-qing(熊柏青)2
(1. State Key Laboratory for Advanced Metals and Materials, University of Science and Technology Beijing, Beijing 100081, China;
2. General Research Institute for Nonferrous Metals, Beijing 100088, China)
Abstract: Spray-formed Al-70%Si(mass fraction) alloys were deformed by compression in the semi-solid state. The effects of the deformation temperature, strain rate and the microstructure were studied. Two strain rates(1s-1and 0.1s-1) and six deformation temperatures (600℃, 720℃ , 780℃, 900℃, 1000℃ and 1100℃) were chosen. The stress—strain curve exhibits a peak at low strain and then decreases to a plateau before it starts to increase again as the strain increases. The stress required for deformation at lower strain rate and at higher deformation temperatures is less than those at higher strain rate and at lower deformation temperatures. Four mechanisms of semi-solid deformation can be used to explain the different behaviors of the stress—strain curves under different conditions.
Key words: Al-70%Si alloy; semi-solid state; stress—strain curve CLC number: TG146.2
Document code: A
1 INTRODUCTION
The study on the semi-solid deformation behavior of metals and alloys was first carried out by Spencer and his co-workers at MIT in 1970s[1]. Since then, semi-solid processing (SSP) has been studied and used as near-net-shape processing technology compared with conventional methods[2, 3]. The material in the semi-solid state was easy to deform; while it kept its shape and exhibited certain strength. SSP can reduce the thermal shock imposed on the mould, increase mould life and reduce the force applied during forming[4, 5]. During the past three decades, most of the studies were concentrated on the stress—strain relationship during the semi-solid deformation in order to describe a deformation behavior of Al and Pb-Sn alloys in the semi-solid state[6-11].
With low thermal expansion coefficient, low density and high thermal conductivity, Al-Si alloys were widely used in electronic packaging industry[12-14]. Spray deposition (S/D) is an emerging advanced material processing method and has matured to become a viable technology for the production of near-net shape preforms. The process involves the stage of gas atomization and droplet deposition on a substrate. In the process the alloy charge is melted in a crucible located on the top of the spray chamber and atomized by pulsed high-velocity gas such as nitrogen and argon. The droplets are cooled by the gas and accelerated to a substrate where a bulk-net or near-net shape preform is built up. It has been demonstrated that alloys fabricated by spray-forming frequently exhibit an equiaxed, non-dendritic grains, fine microstructure and improved mechanical properties compared with those of the conventional cast. For the equiaxed microstructure that was observed in some spray-formed materials, these materials will show some thixotropic behaviors. For this reason the semi-solid process was chosen as the sequential forming process.
In this work compression tests on spray-formed Al-70%Si(mass fraction) alloys were carried out to study the deformation behavior in the semi-solid state. The typical stress—strain curve and the effect of deformation temperature and strain rate on the Al-70%Si alloys were also studied.
2 EXPERIMENTAL
Al-70%Si preform was prepared by spray deposition and the cylindrical specimens were cut from the preform with a size of 10mm in diameter and 15mm in height.
The compression test was carried out on a Gleeble-1500 dynamic material testing machine. The samples were placed between two graphite plates, through the center of which two thermocouples were inserted to contact the samples to control and monitor the temperature.
The heating rate was 10℃/s. After an isothermal holding at a predetermined temperature for 3min, the samples were compressed with a height reduction of 50% (true strain 0.69) at different strain rates and temperatures (see Table 1) corresponding to the pre-selected volume fraction of solid in the range of 0.3-0.65 as shown in Fig.1, determined by Scherrer equation(non-equilibrium lever rule) in Si-Al binary phase diagram. The samples were quenched immediately after the deformation to preserve the deformed microstructures.
Table 1 Experimental parameters used
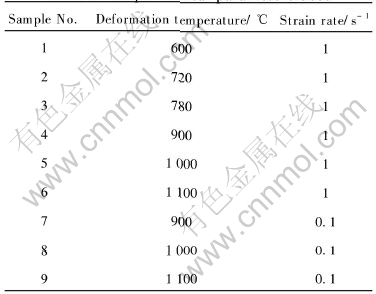
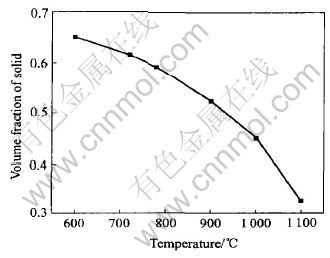
Fig.1 Solid fraction as function of temperature in Al-70%Si alloy
To avoid the liquid phase segregation and control the growth of the primary silicon size, the deformation temperature was chosen between 600℃ and 1100℃ in the liquid-solid two-phase region. Under a high strain rate the specimens tend to damage seriously after the deformation, while under a low strain rate the deformation time may be long enough to cause a serious liquid segregation. Thus two strain rates(1s-1, 0.1s-1) were chosen to study the effects of the strain rates.
SEM and imaging analysis were used to study and analyze the microstructure, the size of the primary phase, the morphology and the distribution of primary phase.
3 RESULTS AND DISCUSSION
The true stress σz (along ram movement direction) is defined as the load F divided by an approximation of the instantaneous area which is calculated on the basis of overall volume conservation:

where D0 and h0 are the initial diameter and initial height of the specimen; Δh is the displacement of the specimen.
The true strain is calculated by

Figs.2(a) and (b) show the microstructures of the spray deposited material. A non-dendritic structure with a very fine primary Si phase and α(Al) with the Al-Si eutectic phase in the interstitial spaces is seen. The average size of the primary silicon phase is 20μm. Fig.2 also shows that the microstructures of the cross section of the specimens before (Fig.2(c) and (d)) and after ((e) and (f)) semi-solid deformation at 720℃ have the similar particle morphology to that of the spray deposited state consisting of fine non-dendritic structure. It is observed that the silicon is embedded into the aluminum matrix during isothermal holding to form a mesh structure. An increase in the primary silicon size is observed due to isothermal holding at 720℃ for 3min. The average size of the silicon is approximately 33μm before the deformation and 30μm after the deformation.
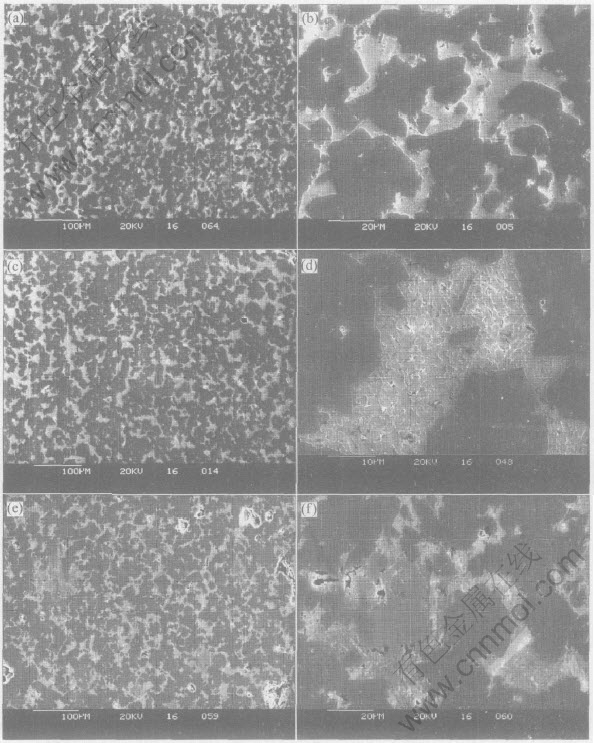
Fig.2 Microstructures of spray deposited Al-70%Si ((a) and (b)),
before ((c) and (d)) and after ((e) and (f)) semi-solid deformation at 720℃
Typical stress—strain curves obtained from the test at different temperatures corresponding to different solid contents are shown in Fig.3. The typical stress—strain curve can be divided into three stages. The stress increases in the initial stage to a peak and then decreases to a plateau before it starts to increase again with increasing strain. Chen and Tsao[15]proposed four main physical mechanisms of the semi-solid deformation, i.e. rearrangement of the solid particles; flow of the liquid phase; the sliding among solid particles; and the plastic deformation of the solid particles. The force required to operate the former two mechanisms is less than that used for the other two mechanisms. The former two mechanisms are dominant when the solid particles are surrounded by the liquid phase; while the other two mechanisms are dominant when the solid particles are interconnected. The flow of the liquid phase can enhance the rearrangement of the solid particles.
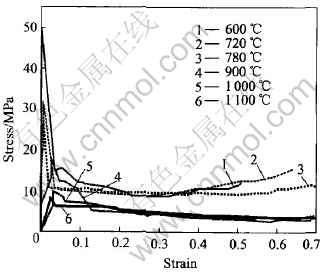
Fig.3 Stress versus strain curves of semi-solid deformation of spray-formed materials
at different temperatures with strain rate of 1s-1
At the initial stage of the deformation, the solid particles are partially interconnected and the liquid phase fills the interstitial spaces. Both the mechanisms of flow of liquid and the rearrangement of solid particles control the deformation for the reason that the force to operate these two mechanisms is less than that of the other two mechanisms. Since the rearrangement of solid particles depends on time, the flow of liquid will be the only mechanism that plays important roles in this stage. During this stage a liquid segregation is produced by the flow of liquid, and some of the liquid phase is pushed to the edge of the specimen, while the solid phase is concentrated on the center of the specimen. As the deformation continues, the rearrangement of solid particles starts to set in since the required deformation force is reached. After the stress reaches the peak value, the deformation enters into the second stage. Because most of the solid phase is concentrated on the center while the liquid phase is pushed to the edge of the specimen, the sliding among solid particles and the plastic deformation of solid particles become the main deformation mechanisms. In this stage the specimen exhibits an apparent damage due to the local deformation. After the stress decreases to a plateau value, the deformation enters into the third stage, in which the stress becomes insensitive to the increasing strain. In this stage the silicon particles contact with each other again. The slide of the particles and the flow of liquid phase may be difficult. The silicon particles form a solid skeleton, which results in the slight variation of the stress.
The stress—strain behavior of all the materials at different temperatures shows similar trends. The stress exhibits a maximum value (peak) at a relatively low strain, in the strain range of 0-0.035. Then the peak stress decreases to a plateau. The stress at the plateau does not vary obviously with the strain. Fig.4 shows the variation of the peak stress as a function of the deformation temperature. The effects of the deformation temperature are equivalent to those of the volume fraction of solid since the deformation temperature is a function of the solid fraction. For all the experiments the specimen at 600℃ shows the highest peak and plateau stresses. Then the stress decreases with increasing temperature due to the larger volume fraction of liquid and a better plasticity of the solid particles at higher deformation temperature.
Fig.5 shows the stress—strain curves obtained from the test at a lower strain rate (0.1s-1). The stress—strain behavior at the lower strain rate under different temperatures shows similar trends as discussed above. Fig.6 shows the variation of the peak stress as a function of the deformation temperature. For all the experiments the specimen at 900℃ has the highest peak stress than the other specimens and the stress decreases with increasing temperature. The peak stress at higher strain rate is higher than that at a relatively lower strain rate.
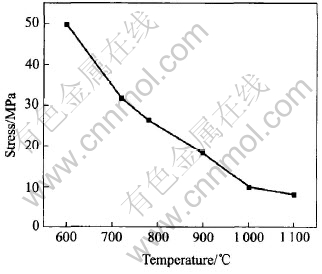
Fig.4 Peak stress as function of deformation temperature

Fig.5 Stress versus strain curves of semi-solid deformation of spray-formed specimens
under different temperatures with strain rate of 0.1s-1
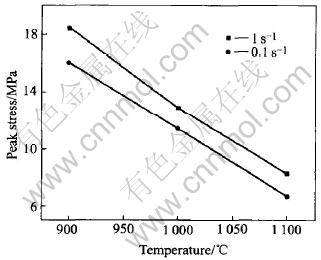
Fig.6 Peak stress as function of deformation temperature at different strain rates
The lateral flow rate of the liquid phase (vr) can be expressed as a function of the volume fraction of solid (φs) and the strain rate
:

where R and H are the radius and the height of the cylindrical specimen. As the deformation temperature increases corresponding to the increasing volume fraction of liquid, liquid phase is increased and there is much space for the liquid phase to flow, which leads to a lower deformation force. On the other hand, as the deformation temperature decreases, the solid particles contact with each other to form a skeleton, thus the required deformation stress will be increased. As the strain rate increases, the required liquid flow rate to achieve the deformation increases, which may result in a higher deformation force.
4 CONCLUSIONS
1) For the spray-formed Al-70%Si alloys, the deformation stress increases in the initial stage to a local maximum, then decreases to a plateau before it starts to increase again with increasing strain.
2) The typical stress—strain curve of the spray-formed Al-70%Si is divided into three stages and four mechanisms can be applied to explain the different behaviors of the stress—strain curves of spray-formed materials under various conditions in the semi-solid state.
3) The required deformation stress increases with increasing strain rate, while decreases with increasing deformation temperature.
REFERENCES
[1]Spencer D B, Mehrabian R, Flemings M C. Rheological behavior of Sn-15%Pb in the crystallization range [J]. Metall Trans A, 1972, 3: 1925-1932.
[2]Brown S B, Flemings M C. Net-shape forming via semi-solid processing [J]. Adv Mater Proc, 1993, 1: 36-40.
[3]Flemings M C. Behavior of metals and alloys in the semi-solid state [J]. Metall Trans A, 1991, 22A: 957-981.
[4]Flemings M C, Rick R U, Yong K P. Rheocasting [J]. Mater Sci Eng A, 1976, 125: 103-117.
[5]Ward P J, Atkinson H V, Anderson P R G, et al. Semi-solid processing of novel MMCs based on hypereutectic aluminium-silicon alloys [J]. Acta Metall, 1996, 44: 1717-1727.
[6]Tzimas E, Zavaliangos A. Mechanical behavior of alloys with equiaxed microstructures in the semi-solid state at high solid content [J]. Acta Metall, 1999, 47: 517-528.
[7]Kopp R, Choi J G, Neudenberger D. Simple compression test and simulation of Sn-15%Pb alloys in the semi-solid state [J]. J Mater Process Technol, 2003, 135: 317-323.
[8]Kang C G, Choi J S, Kim K H. The effect of strain rate on microscopic behavior in the compression forming of semi-solid aluminium alloy[J]. J Mater Process Technol, 1999, 88: 159-168.
[9]WANG Ping, DONG Wei-guo, LU Gui-min, et al. Deformation behabvour of semi-solid A356 alloy[J]. J Northeastern University, 2003, 24: 586-588.(in Chinese)
[10]ZHANG Da-hui, MAO Wei-min, ZHONG Xue-you. Effect of deformation rate on deformation behaviour of semi-solid AlSi7Mg alloy[J]. The Chinese Journal of Nonferrous Metals, 2000, 10(S1): 132-134.(in Chinese)
[11]LIU Hui-min, CHENG Jun-sheng, CUI Hua, et al. Temperature effect on thixoforming of spray-formed 7075 alloy[J]. J Univ Sci Technol Beijing, 2004, 24: 391-394.(in Chinese)
[12]Jacobson D M. Lightweight electronic packaging technology based on spray formed Si-Al [J]. Powder Metallurgy, 2000, 43: 200-202.
[13]Sangha S P S, Jacobson D M, Ogilvy A J W, et al. Novel aluminium-silicon alloys for electronics packaging [J]. Engineering Science and Education Journal, 1997, 10: 195-201.
[14]Jacobson D M. Spray-formed silicon-aluminium alloys [J]. Advanced Materials and Processes, 2000, 3: 36-39.
[15]Chen C P, Tsao C Y A. Response of spray-formed stirred-cast and conventional cast Pb-Sn alloys to deformation in the semi-solid state [J]. J Mater Sci, 1995, 30: 4019-4026.
[16]Chen C P, Tsao C Y A. Semi-solid deformation of non-dendritic structures—(Ⅰ): phenomenological behavior [J]. Acta Matell, 1997, 45: 1955-1968.
Foundation item: Project(2012012) supported by the Natural Science Foundation of Beijing, China
Received date: 2004-08-19; Accepted date:2005-04-15
Correspondence: ZHANG Di, PhD; Tel: +86-10-62332244; E-mail: zhandi1211@hotmail.com
(Edited by YANG Bing)