文章编号:1004-0609(2008)12-2245-08
基于有限元模拟的空拔铜管拉拔参数的优化
杨晓静1,孙方宏1,张志明2,沈荷生2,郭松寿3
(1. 上海交通大学 机械与动力工程学院,上海 200240;
2. 上海交通大学 微纳米科学研究院,上海 200240;
3. 上海交友钻石涂层有限公司,上海 200240)
摘 要:为研究拉拔参数对铜管空拔变形的影响,运用非线性有限元分析软件对铜管空拔过程进行仿真,分析空拔过程中铜管与模具的轴向及径向应力分布规律,并以此阐述空拔铜管的缩径缺陷。利用正交实验法模拟研究拉拔参数(工作锥半角α、过渡圆弧半径R、定径带长度L、摩擦因数μ、拉拔速度v)对铜管空拔的影响,并采用极差分析和方差分析对模拟结果进行分析,得到铜管一定减面率条件下的最佳拉拔参数(α=9°,R=5 mm,L=2 mm, μ=0.05, v=100 m/min)及各因素对分析指标的影响。在此基础上对优化方案进行数值模拟,模拟结果表明了正交实验对铜管空拔参数优化的有效性。这对实际中提高铜管空拔质量,延长模具寿命有重要的指导意义。
关键词:空拔;铜管;拉拔参数;有限元;正交实验法
中图分类号:TG 356.5 文献标识码: A
Optimization of drawing parameters for copper tubes with hollow sinking based on FEM simulation
YANG Xiao-jing1, SUN Fang-hong1, ZHANG Zhi-ming2, SHEN He-sheng2, GUO Song-shou3
(1. School of Mechanical Engineering, Shanghai Jiao Tong University, Shanghai 200240, China;
2. Research Institute of Micro/Nanometer Science and Technology, Shanghai Jiao Tong University, Shanghai 200240, China;
3. Shanghai Jiaoyou Diamond Coating Co. Ltd., Shanghai 200240, China)
Abstract: In order to investigate the influence of drawing parameters on the deformation of copper tubes in hollow sinking, the nonlinear finite element software was used to simulate the whole copper tube hollow sinking process. The distributions of the axial stress and radial stress were analyzed, and the mechanism of drawn copper tubes diameter shrinking was explained. The influences of drawing parameters (the semi-angle of drawing dies α, the transition arc radius R, the length of bearing part L, the friction coefficient μ, the drawing velocity v) on copper tubes hollow sinking were investigated by using orthogonal experiment. The optimal drawing parameters (α=9°, R=5 mm, L=2 mm, μ=0.05, v=100 m/min) under certain reduction of area and the influence of factors on analysis indexes were obtained according to the simulation results by range analysis and variance analysis. Furthermore, the optimal drawing parameters were simulated by FEM, and the simulation results confirmed the effectiveness of the orthogonal experiment in optimizing tubes drawing in hollow sinking. It is of great significant for improving the quality of drawn copper tubes and prolonging the lifetime of drawing dies.
Key words: hollow sinking; copper tube; drawing parameter; finite element; orthogonal experiment
空拔是一种广泛应用的管材加工方法,它能有效实现管材拉拔减径,获得所需的力学性能。但同时空拔管材的成形过程十分复杂,属于弹塑性变形与接触非线性耦合的多重非线性问题,使得空拔管的理论研究十分困难。随着计算机技术的发展,基于有限元法的数值模拟在管材拉拔中得到广泛应用。KAZUNARI等[1]利用二维轴对称有限元法对Ti-Ni形状记忆合金管的空拔及短芯头拉拔进行研究,并分析了拉拔过程中管材的应力应变分布。TAKASHI等[2]采用数值模拟与实验方法对比研究了钢管空拉及带芯头拉拔后的残余应力分布。权国政等[3]基于有限元分析软件Deform-3D,建立了铝管空拔成形的动力学模型,得到了摩擦因数对拉拔力的影响曲线,并划分了铝管空拔过程的变形区。薛隆泉等[4]应用ANSYS显式动力分析模块建立了钢管三维空拔模型,得到了空拔过程各种场量分布及各工艺参数对拔制力的影响。俞庆 等[5]对钢管空拔及短芯棒拉拔进行三维动态模拟,从钢管的应力分布规律角度阐述了实际生产中产生的问题的不同机理,并就两种拉拔方式中工艺参数对拔制力的影响进行了深入研究。
本文作者以大型有限元软件ANSYS为研究平台,采用轴对称弹塑性有限元法对铜管的空拔过程进行仿真,以得到铜管及模具的轴向、径向应力分布,并阐述了空拔铜管拉拔后的缩径缺陷。而后采用正交实验法研究了模具孔型参数及拉拔条件对铜管空拉的影响,并以铜管空拉缩径量和模具上最大等效应力为正交实验分析指标,分别利用极差分析法和方差分析法对模拟结果进行分析,以得到铜管一定减面率条件下的最佳拉拔参数及各因素对分析指标的影响规律。并在此基础上对优化方案进行数值模拟,以证明正交实验分析的有效性。
1 弹塑性有限元的基本理论
空拔铜管是一个多重非线性耦合问题,既有接触非线性,又有几何和边界非线性。图1所示为铜管及模具空拔几何模型。由图1可见,铜管的变形区分为减径区Ⅰ和定径区Ⅱ,α是模具工作锥半角,R为工作锥与定径带处过渡圆弧半径,L为定径带长度。T1、T2、N1、N2分别为铜管在减径区及定径区所受的摩擦力及正压力。拉拔过程中,铜管在拉拔力的作用下逐渐与模具接触,并在模具工作锥挤压下产生径向收缩及轴向伸长;进入定径区后,铜管产生弹性恢复,但仍受到模具的正压力及切向摩擦力的的作用。
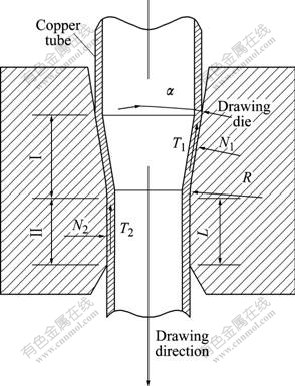
图1 铜管空拔示意图
Fig.1 Schematic illustration of copper tube in hollow sinking
1.1 本构方程
弹塑性有限元法的本构关系在弹性阶段符合虎克定律,进入塑性状态后符合Prandtl-Reuss理论[6]。
根据Prandtl-Reuss理论及Mises屈服准则得到大变形弹塑性速率本构方程一般可表示为
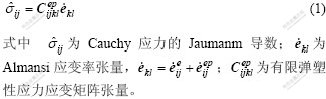
1.2 边界条件
金属塑性成形中,通常工件的变形是在与模具的接触状态下进行的,模具通过该接触表面把力和速度的作用施加在工件上,使之产生塑性变形。因此接触边界条件的处理对模拟分析有重要影响。当两个物体相接触时,为满足接触边界不互相过分渗透,要在垂直目标面的方向施加一个适当的力,使渗透深度在容差范围内。当采用罚函数和拉格朗日乘子组合法时[7]:
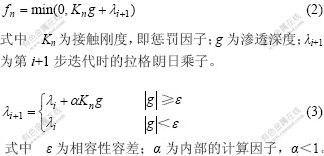
在产生接触单元时,可以在单元属性中指定接触刚度及相容性容差的大小,从而控制接触面之间的深度。ANSYS给出的接触刚度的选择范围是

拉拔过程中的接触问题需要计算摩擦,摩擦使有限元数值计算求解的收敛变得困难。影响摩擦的因素很多,如接触面上的润滑条件、模具表面状态及材料化学成分、性能等。摩擦问题对金属流动有显著影响,同时影响产品质量及模具寿命。本研究中采用的摩擦模型为Coulomb摩擦,接触表面的摩擦应力表达如 下[8]:
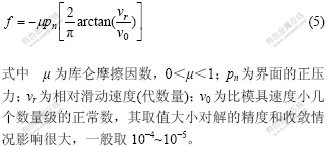
2 模型建立及模拟参数
模拟中,铜管拉拔前外径为d11.2 mm,壁厚为0.35 mm,拉拔后外径为d9.52 mm。铜管空拔过程按以下条件建立仿真模型:
1) 建立几何模型。由于铜管空拔过程为轴对称,因此可将仿真模型简化为轴对称模型。仿真中,铜管模拟初始长度为40 mm。考虑到铜管拉拔后的实际长度增加,为模拟整个拉拔过程,在铜管前端施加的位移要略大于铜管变形后的长度。
2) 定义材料模型。铜管材料为TP2(磷脱氧铜),被假定为弹塑性材料,考虑材料的强化效应,在ANSYS软件中采用多线性等向强化(MISO)材料模型,通过多线性来表示弹塑性材料的应力-应变关系,材料初始屈服服从von Mises 屈服准则。铜管材料屈服强度为407.4 MPa,其单向拉伸的应力-应变关系为
(MPa),铜管的弹性模量为117.2 GPa,泊松比为0.3。模具假定为弹性材料,其弹性模量为700 GPa, 泊松比为0.21。
3) 单元选择及网格划分。铜管及模具均采用具有轴对称功能的PLANE182结构单元进行分析,网格划分采用四节点的平面单元。初始的有限元网格模型(扩展的三维模型)如图2所示。引用接触单元对CONTACT172和TARGET169建立铜管与模具间的接触与摩擦。并利用接触单元的高斯积分点作为接触检验点,确定接触面的法向刚度及切向刚度,制定最大的允许穿透。摩擦因数是通过接触体材料属性的定义而确定的。
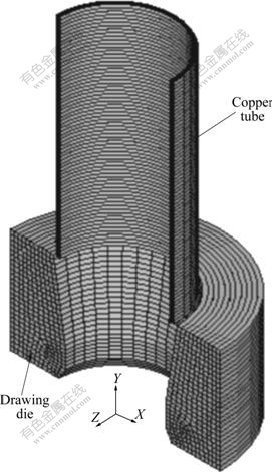
图 2 铜管空拔三维有限元模型
Fig.2 3D FE model of copper tube in hollow sinking
4) 加载及求解。根据实际拉拔要求,模拟中,对模具施加径向及轴向的零位移约束,在铜管前端施加轴向位移来代替实际的拉拔力,并通过铜管轴向位移与拉拔时间的匹配来实现对实际拉拔速度的设定。在求解时打开大应变效应及自动时间步长,仿真中共设置一个载荷步。
3 模拟结果分析
3.1 铜管空拔的应力分析
在空拔过程中,铜管内表面处于自由变形状态,而外表面与模具接触,由于摩擦力的影响,使铜管外表面比内表面承受更高的纵向流动阻力,从而使铜管断面上金属纵向流动不均[4]。图3所示为铜管空拔的轴向应力分布。由图中知,铜管稳态拉拔时,其轴向应力模式有3次变化:1) 非接触变形的Ⅰ区;2) 接触变形的Ⅱ区和Ⅲ区;3) 定径区Ⅳ。在非接触变形的Ⅰ区,铜管没有与模具接触,但在拉拔力作用下,铜管向外弯曲,使Ⅰ区铜管外表面产生轴向拉应力,而内表面产生轴向压应力。在接触变形Ⅱ区,由于模具工作锥的挤压作用,使铜材的轴向应力产生与Ⅰ区完全相反的应力模式,即外表面为轴向压应力,内表面为轴向拉应力。在Ⅲ区,铜管在拉拔力及模具工作锥作用下向内弯曲,因此铜管的轴向应力模式与Ⅱ区相同。铜管进入定径区Ⅳ后,铜管发生与Ⅲ区相反的变形,使其外表面形成强拉应力区,内表面形成强压应力区。若此时轴向拉应力过大,将使铜管外表面产生微裂纹甚至拉断。
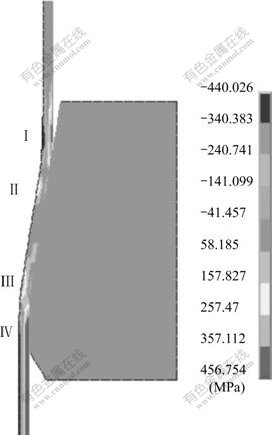
图3 空拔铜管轴向应力分布
Fig.3 Axial stress distribution of copper tube in hollow sinking
图4所示为空拔铜管的径向应力分布。由图4可知,铜管稳态空拔时,其径向应力分布有两个应力集中区,一个在铜管与模具开始接触位置附近,一个在工作锥与定径带的过渡圆弧处。在应力集中区,铜管外表面及模具都受较大的径向压应力,从而使模具在此两处较易发生磨损。
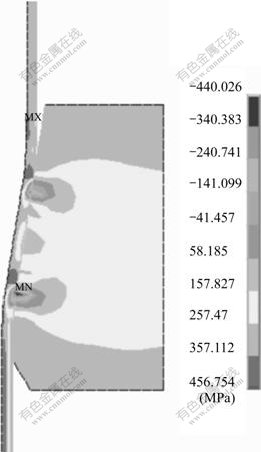
图4 空拔铜管径向应力分布
Fig.4 Radial stress distribution of copper tube in hollow sinking
铜管空拔过程中, 由于金属材料的流动惯性,使其从变形区的工作锥进入定径带后,仍有径向的金属流动,从而导致铜管与模具定径带间形成非接触变形区。这种非接触变形将导致铜管拉拔后的缩径,如图5示。
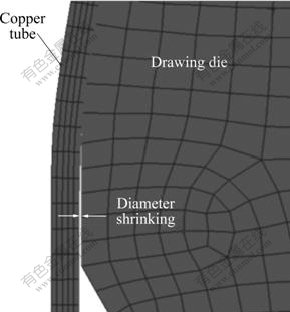
图5 空拔铜管缩径现象
Fig.5 Diameter shrinking of copper tube in hollow sinking
3.2 影响铜管空拔因素的正交实验分析
3.2.1 实验因素选择
在铜管空拔中,为减小拉拔后铜管的外径偏差及
提高模具的使用寿命,根据实际铜管空拔的要求,正交实验设5个因素,即:因素A工作锥半角α;因素B,过渡圆弧半径R;因素C,定径带长度L;因素D,摩擦因数μ;因素E,拉拔速度v。每个因素分别有5个水平,如表1所列。因此,正交实验安排采用L25(56 )的正交表,如表2所列。模拟中考虑到铜管空拔缩径,采用的模具孔径为d9.58 mm。
表1 空拉铜管的水平因素表
Table 1 Factors and levels of orthogonal experiment
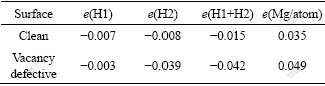
表2 正交实验方案及结果
Table 2 Scheme and results of orthogonal experiment
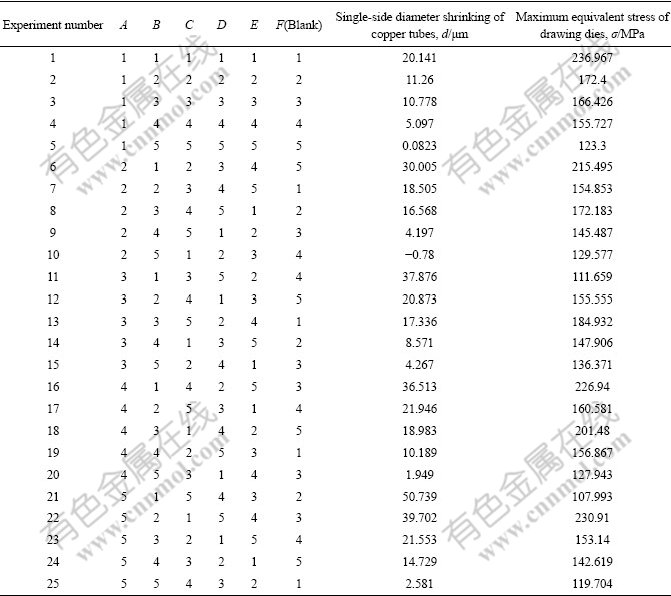
3.2.2 极差分析
正交实验的极差分析中,因素的极差值越大反映了其对结果的影响显著性越高。表3所列为正交实验模拟结果的极差分析,表中Ki为同一因素下
水平的平均值(i=1, 2, 3, 4, 5),RX为因素X的极差。由表中数据知,在各因素对空拔铜管单边缩径的影响中,过渡圆弧半径的影响最显著,其次为模具工作锥半角的影响,其它因素由于极差相对较小,其影响可忽略。在影响模具最大等效应力的各因素中,过渡圆弧半径仍是最显著的影响因素,其次是定径带长度和拉拔速度的影响。因此,兼顾各因素对两大分析指标的综合影响,得到铜管在一定减面率下空拔的最佳拉拔方案:A2B5C3D1E2,即模具工作锥半角为9?,过渡圆弧半径为5 mm,定径带长度为2 mm,摩擦因数为0.05,拉拔速度为100 m/min。
表3 模拟结果的极差分析
Table 3 Range analysis of simulation results

3.2.3 方差分析
为进一步了解实验各因素对模拟结果影响的量化估计,对正交实验结果进行方差分析。表4所列为各因素对两大指标影响的方差分析结果,表中‘*’表示因素的影响性显著,‘#’表示因素对指标有影响,但不显著。分析中,F为分布统计量,因素的显著性水平表α=0.01。由表中数据知,在空拉铜管单边缩径的影响因素中,过渡圆弧半径的F值大于F的临界值,说明该因素对铜管空拉缩径的影响程度较大;其次为工作锥半角的影响;而其它因素由于方差较小,其影响可以忽略。在模具最大等效应力影响的各因素中,虽然其F值都小于F临界值,但相对而言,过渡圆弧半径的影响还是最为显著,而其它因素的影响相对较小。
表4 模拟结果的方差分析
Table 4 Variance analysis of simulation results
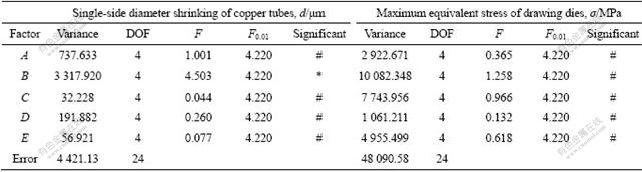
极差分析与方差分析的结果表明,在影响铜管空拉缩径与模具最大等效应力的各因素中,过渡圆弧半径的影响较为显著。因此,要获得高质量的空拉铜管及延长模具寿命,过渡圆弧半径的合理设计是非常重要的。其次,工作锥半角、定径带长度、摩擦因数及拉拔速度的影响也不容忽视。
3.2.4 优化方案的模拟分析
图6(a)~(c)为在优化方案(模具工作锥半角为9?,过渡圆弧半径为5 mm,定径带长度为2 mm,摩擦因数为0.05,拉拔速度为100 m/min)下,铜管及模具的等效应力分布和铜管外表面点的径向位移曲线。由图6可知,空拔时铜管的最大等效应力是在模具的整个工作锥部分;模具的最大等效应力在工作锥与定径带的过渡圆弧位置,且值为114.862 MPa。进而证明过渡圆弧半径对模具最大等效应力有重要影响。在优化的拉拔参数下,由铜材的径向位移所得拉拔后铜材外径为9.523 2 mm,与铜管理论外径的误差为0.03%。该模拟结果较正交实验模拟结果有明显的优化。
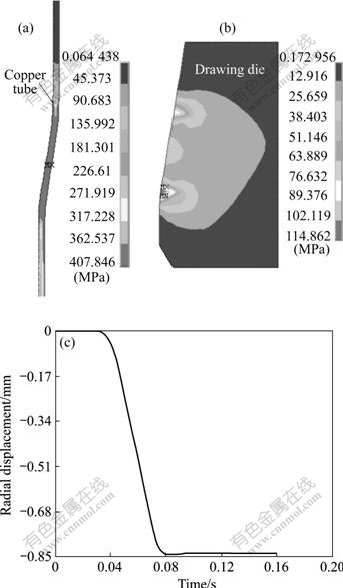
图6 优化方案的铜管空拔模拟
Fig.6 Simulation of optimal scheme of copper tube in hollow sinking: (a) Equivalent stress distribution of copper tube; (b) Equivalent stress distribution of drawing die; (c) Radial displacement of copper tube outer surface
4 结论
1) 通过对铜管空拔过程的有限元仿真,得到了稳态拉拔时铜管及模具的轴向及径向应力分布,并阐述了铜管空拔后的缩径缺陷。
2) 根据对模拟结果的极差与方差分析可知,在各影响因素中,过渡圆弧半径对两大分析指标的影响始终最为显著,且随着过渡圆弧半径的增加,铜管拉拔后的单边缩径量和模具上最大等效应力都在不断减小;同时铜管拉拔后的单边缩径量随模具工作锥半角的增大有显著增加,而模具定径带长度的增加却有利于模具上最大等效应力的减小,对比而言,其它影响因素对分析指标的影响变化相对较小。
3) 根据正交实验分析,得到一定拉拔条件下优化的铜管空拔参数:即模具工作锥半角为9?,过渡圆弧半径为5 mm,定径带长度为2 mm,摩擦因数为0.05,拉拔速度为100 m/min。
4) 对优化方案进行数值模拟,所得拉拔后铜管外径与理论外径误差为0.03%,同时模具的最大等效应力在过渡圆弧位置,且值为114.862 MPa,模拟结果表明正交实验分析对空拉铜管拉拔参数优化的有 效性。
REFERENCES
[1] KAZUNARI Y, MASAKI W, HIROSHI I. Drawing of Ni-Ti shape-memory-alloy fine tubes used in medical tests[J]. Journal of Materials Processing Technology, 2001, 118: 251?255.
[2] TAKASHI K, KEIGO N, TOMOHIRO S. Effect of plug on leveling of residual stress in tube drawing[J]. Journal of Materials Processing Technology, 2008, 204: 162?168.
[3] QUAN Guo-zheng, ZHOU Jie, WANG Meng-han, QUAN Guo-hui, TONG Ying. Deforming mechanism of non-mandrel drawing process of circular aluminum tube by simulation[J]. Trans Nonferrous Met Soc China, 2006, 16: s1301?s1304.
[4] 薛隆泉, 何亚峰, 刘荣昌, 代春英, 陈军涛. 基于ANSYS/LS-DYNA的空拔钢管有限元分析[J]. 塑性工程学报, 2005, 12(5): 74?77.
XUE Long-quan, HE Ya-feng, LIU Rong-chang, DAI Chun-ying, CHEN Jun-tao. FEA on empty-sunken steel tube based on ANSYS/LSDYNA[J]. Journal of Plasticity Engineering, 2005, 12(5): 74?77.
[5] 俞 庆, 张 侃, 何亚峰. 拔制方式对冷拔钢管拔制效果影响的显式动力分析[J]. 塑性工程学报, 2007, 14(1): 89?93.
YU Qing, ZHANG Kan, HE Ya-feng. Explicit dynamic analysis on the result actions of drawing styles in cold steel tube drawing process[J]. Journal of Plasticity Engineering, 2007, 14(1): 89?93.
[6] 李尚健. 金属塑性成形过程模拟[M]. 北京: 机械工业出版社, 1999: 24 ?27.
LI Shang-jian. Simulation of metal plastic forming process[M]. Beijing: Machinery Industry Press, 1999: 24?27.
[7] 苏 岚, 王先进, 唐 荻, 孙吉先, 田荣彬. 有限元法处理金属塑性成型过程的接触问题[J]. 塑性工程学报, 2000, 7(4): 12?15.
SU Lan, WANG Xian-jin, TANG Di, SUN Ji-xian, TIAN Rong-bin. A study on contact problem of plastic metal forming with finite element method[J]. Journal of Plasticity Engineering, 2000, 7(4): 12?15.
[8] 刘建生, 陈慧琴, 郭晓霞. 金属塑性加工有限元模拟技术与应用[M]. 北京: 冶金工业出版社, 2003: 38?39.
LIU Jian-sheng, CHEN Hui-qin, GUO Xiao-xia. Finite element simulation and application of metal plastic forming[M]. Beijing: Metallurgical Industry Press, 2003: 38?39.
[9] CHEN Dyi-Cheng, HUANG Jheng-Yu. Design of brass alloy drawing process using Taguchi method [J]. Mater Sci Eng A, 2007, 464: 135?140.
[10] 王继周, 李晋霞, 邰振中. 管材拉拔中的不均匀变形与残余应力[J]. 塑性工程学报, 2001, 8(4): 40?44.
WANG Ji-zhou, LI Jin-xia, TAI Zhen-zhong. Inhomogeneous deformation and residual stress in tube drawing[J]. Journal of Plasticity Engineering, 2001, 8(4): 40?44.
[11] 申卫华, 李章刚, 刘化民, 张士宏. 铜管游动芯头拉拔模具角度优化的有限元模拟[J]. 塑性工程学报, 2005, 12(2): 61?64.
SHEN Wei-hua, LI Zhang-gang, LIU Hua-min, ZHANG Shi-hong. FEM simulation of the optimization of the die angle with the floating plug drawing process of copper tubes[J]. Journal of Plasticity Engineering, 2005, 12(2): 61?64.
[12] KAZUNARI Y, HIROAKI F. Mandrel drawing and plug drawing of shape-memory-alloy fine tubes used in catheter and stents[J]. Journal of Materials Processing Technology, 2004, 153/154: 145?150.
[13] SADOK L, KUSIAK J, PACKO M, RUMINSKI M. State of strain in the tube sinking process[J]. Journal of Materials Processing Technology, 1996, 60: 161?166.
[14] ALEXANDROVA N. Fracture analysis of tube drawing with a mandrel[J]. Journal of Materials Processing Technology, 2003, 142: 755?761.
[15] 苌群峰, 李大永, 彭颖红, 曾小勤. AZ31镁合金板材温热冲压数值模拟与实验研究[J]. 中国有色金属学报, 2006, 16(4): 580?585.
CHANG Qun-feng, LI Da-yong, PENG Ying-hong, ZENG Xiao-qin. Numerical simulation and experimental study of warm deep drawing of AZ3 1 magnesium alloy sheet[J]. The Chinese Journal of Nonferrous Metals, 2006, 16(4): 580?585.
[16] 韩宝云, 金 明, 钟倩霞. 钢管中式模空拔过程计算机有限元仿真研究[J]. 计算机应用, 2000, 29(5): 42?46.
HAN Bao-yun, JIN ming, ZHONG Qian-xia. Computer FE simulation of steel tube free sinking process with arc die[J]. Journal of Computer Application, 2000, 29(5): 42?46.
[17] SEET H L, LI X P, LEE K S, LIU L Q. Cold drawing of micro Ni80Fe20/Cu composite wires[J]. Journal of Materials Processing Technology, 2007, 192/193: 350?354.
基金项目:国家自然科学基金资助项目(50575135);教育部新世纪优秀人才计划资助项目(NCET-06-0399)
收稿日期:2008-01-14;修订日期:2008-07-28
通讯作者:孙方宏,教授,博士;电话:021-34206557;E-mail: sunfanghong@sjtu.edu.cn
(编辑 何学锋)