J. Cent. South Univ. (2016) 23: 1831-1838
DOI: 10.1007/s11771-016-3237-3

Effects of rapid solidification process and 0.1%Pr/Nd addition on characteristics of Sn-9Zn solder alloy and interfacial properties of Cu/solder/Cu joints
ZHAO Guo-ji(赵国际)1,2, WEN Guang-hua(文光华)1, SHENG Guang-min(盛光敏)1, JING Yan-xia(景彦霞)1
1. College of Materials Science and Engineering, Chongqing University, Chongqing 400044, China;
2. Chongqing Industry Polytechnic College, Chongqing 401120, China
Central South University Press and Springer-Verlag Berlin Heidelberg 2016
Abstract: Rapidly solidified Sn-9Zn-0.1Pr(/Nd) alloy foils were prepared by melt-spinning method. Through comparison, the effects of rapid solidification process and 0.1%Pr/Nd (mass fraction) addition on the microstructure, thermodynamic characteristic of Sn-9Zn solder alloy were analyzed. The tensile-shear tests were used to evaluate the mechanical properties of solder/Cu joints. The results show that the rapid solidification process can greatly refine the microstructure of Sn-9Zn-0.1Pr(/Nd) alloys. After rapid solidification, the effects of Pr/Nd addition on microstructure are depressed. The pasty range of the rapidly solidified Sn-Zn-RE solders is also reduced significantly. The mechanical properties of solder/Cu joints are obviously improved using the rapidly solidified Sn-9Zn-0.1Pr(/Nd) solder alloy, which results in the formation of uniform interface. The promotion effect of Nd addition in Sn-9Zn alloy on the interfacial reaction of solder/Cu joint is more remarkable than that of Pr.
Key words: rapid solidification; Sn-Zn-RE solder; microstructure; interfacial property
1 Introduction
In many countries, the usage of traditional Sn-Pb alloy solders has been banned in electronic industry due to the toxicity of Pb and Pb-containing compounds. Thus, the development of lead-free solders has been a key issue in electronics packaging industries. A variety of new lead-free solders have been developed to replace the usage of Sn-Pb solders in electronic industry in recent years. Varied kinds of solder alloys were used in many different fields [1-2]. Sn-Zn alloys have been valued in recent year because of their relatively low melting point, cost saving, and superior mechanical properties. They are considered to be an available candidate for replacing Pb-containing solders in microelectronics packaging and interconnection without increasing the soldering temperature [2-3]. However, some obvious disadvantages, such as poor wettability and easy oxidation, limit the practical use of the alloys [2-4].
Generally, two ways are used to improve the performance of Sn-Zn alloys: one is to develop or optimize the formulation of flux which is fitted for the soldering, and the other is to improve oxidation resistance by alloying. Alloying is a frequently used method [2-3]. Rare earth (RE) elements (such as Nd, Pr and Ce) are widely used in alloying into Pb-free solders to improve solder performance [2-4]. HU et al [5] found that the wettability of Sn-9Zn and mechanical properties of the solder joints were improved and enhanced with minor Nd addition, and the thickness of intermetallic compound (IMC) layer was repressed compared to that of Sn-9Zn. XUE et al [6] reported that the addition of RE element Nd could refine the microstructure of the solder.
Rapid solidification process has been used to optimize the properties and performance of solder alloys [7-8]. A few researches reported the properties improvement of Sn-Zn alloys due to the rapid solidification process [9-10]. However, studies on rapidly solidified Sn-Zn-RE alloys have less been reported in the literature. The purpose of this work is to study the effect of minor Pr/Nd addition and rapid solidification process on the characteristics of Sn-Zn solder, as well as the mechanical properties and interfacial microstructure of Cu/solder/Cu joints.
2 Experimental
The Sn-9Zn-XRE solders with X=0 and 0.1, were produced by melting pure Sn (99.99%), Zn (99.99%), Pr (99.99%) and Nd (99.99%) according to their mass fraction in a ZG-001 vacuum induction melting furnace. Subsequently, the rapidly solidified Sn-9Zn-0.1RE solder foils were obtained from the massive alloy. The rapid solidification process was performed with crystallization of the melt drop on a copper cylinder with a diameter of 350 mm. The copper cylinder with polished surface could rotate at a frequency of 25 r/s. The thickness of the obtained foil was about 60 μm.
A Mettler-Toledo TGA/DSC 1/1100 thermal analysis device was used to analyze the melting behavior of the solder alloys using a heating rate of 10 °C/min under argon atmosphere from 30 °C to 250 °C. Specimens for differential scanning calorimetry (DSC) were prepared and about 20 mg cut from the ingots and the rapidly solidified foils.
According to Chinese National Standard GB 11363—2008 [11], the Cu-solder-Cu joints for the test were prepared with two pure copper (99.8%) plates. Based on the pervious experimental work [12-13], two pure Cu (99.8%) specimens were soldered together with a solder sheet at 240 °C for 3 min in a SX-12 box-type furnace with the aid of commercial RMA flux. The interfacial morphology at the solder/Cu substrate interface was observed using a VEGA3 TESCAN scanning electron microscope (SEM). The samples for microstructural observation were etched slightly by 3%HCl + 5%HNO3 + 92%CH3OH solution after mechanical polishing. An ANS electronic universal testing machine was employed to carry out the tensile-shear tests with a strain rate of 0.5 mm/min at room temperature. Four joints were evaluated for each set of conditions.
3 Results and discussion
3.1 Microstructural observation
The microstructure of the as-solidified Sn-9Zn alloy was comprised of Sn-rich phases and large rod-like Zn-rich phases, as shown in Fig. 1. During the solidification process, the conglomeration of small Zn phases results in the formation of prolonged Zn phases [10]. Studies also showed that the cooling conditions on Sn-Zn system alloys could affect their microstructure obviously [14-15]. Figure 2(a) shows the microstructure of the rapid solidified Sn-9Zn solder alloy foil. The phase analysis result by XRD is shown in Fig. 2(b).
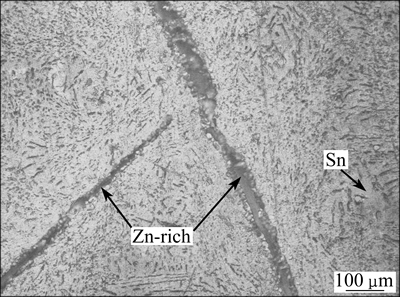
Fig. 1 Microstructure of as-solidified Sn-9Zn alloy
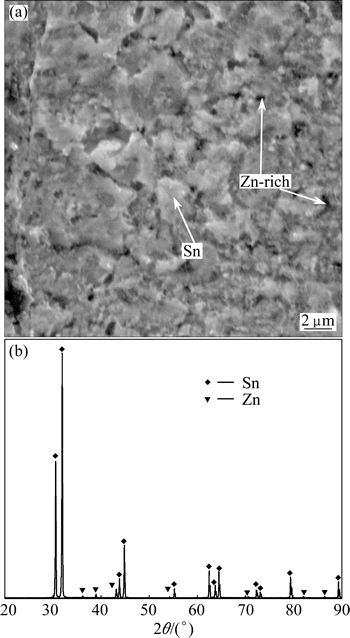
Fig. 2 Microstructure (a) and XRD pattern (b) of rapidly solidified Sn-9Zn alloy
Figure 2 indicates that the Sn-9Zn alloy maintains a crystal structure after the rapid solidification process. The granular Zn phases distribute freely in the matrix of Sn-rich phase. During the rapid solidification process, the advantage of the formation and growth of the primary phase Zn is not obvious. The Zn atoms dissolve in β-Sn and form a supersaturated β-Sn solid solution. In the case of rapid solidification, the conglomeration of the small Zn phases is difficult. Therefore, the large rod-like Zn phases cannot be formed in the rapidly solidified foils. The net-like dendrite structure is also formed due to the rapid branch of β-Sn.
The thickness of the obtained foil is about 60 μm. The heat dissipation mode in the solidification process is considered to be a way according to Newton’s law of cooling and its momentary cooling rate can be calculated by the following formula [16]:
(1)
where h is the coefficient of interfacial heat transfer, ρ is the density of alloy melt, cp is the specific heat at constant pressure, z0 is the thickness of the alloy foils, Tm is the melting temperature of melt, and TA is the cold mould temperature. Studies showed that a melt cooling rate on the order of 106 K/s might be produced by the rapid solidified process [9-10].
Figure 3 shows the microstructure of as-solidified and rapidly solidified Sn-9Zn-0.1RE solder alloys.
Compared with the as-solidified Sn-9Zn alloy (Fig. 1), a significant refined microstructure is obtained by adding minor RE elements Pr/Nd which have strong metamorphism (Figs. 3(a) and (c)). The Zn-rich phases distribute in β-Sn matrix as small granular substance. With an appropriate addition, the gather of RE elements at the forefront of solid/liquid interface make the composition degree of super-cooling increase. The crystal form of the alloy is changed from the plane to a growth of mode cellular dendrite β-Sn [17]. The dendrite spacing is finally decreased and the grains can be refined.
Figures 3(b) and (d) show the microstructure of the cross-section for the case of rapidly solidified Sn-9Zn-RE alloy foils. It is indicated that a uniform reticulation microstructure is formed in the foil after rapid solidification and the granular Zn-rich phases distribute in the Sn-rich matrix randomly. According to the binary phase diagram of Sn-Zn, atomic Sn can barely dissolve in the Zn phase, but Zn atoms can dissolve in β-Sn. During rapid solidified process, the advantage of the formation and growth of the primary phase is not obvious and a supersaturated β-Sn solid solution can be formed in the rapid solidification process [5-6]. The β-Sn phases branch rapidly in the rapid solidification process and form a net-like structure with dendrite. Meanwhile, the large rod-like Zn phases can not be formed in the rapidly solidified foils due to the fact that the conglomeration of small Zn phases is difficult on extremely short time scales. The effects of Pr/Nd addition on the microstructure of rapidly solidified Sn-9Zn-RE alloys are not obvious.
3.2 Melting characteristic of solders
DSC heating curves of the as-solidified Sn-9Zn, Sn-9Zn-0.1RE alloys and rapidly solidified Sn-9Zn-0.1RE alloys are shown in Fig. 4.
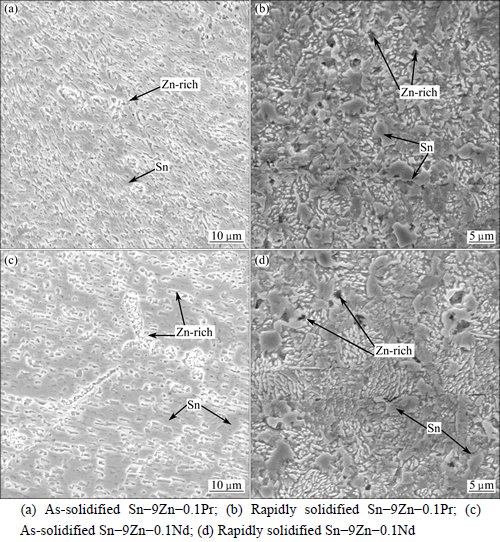
Fig. 3 Microstructures of Sn-9Zn-0.1RE alloys:
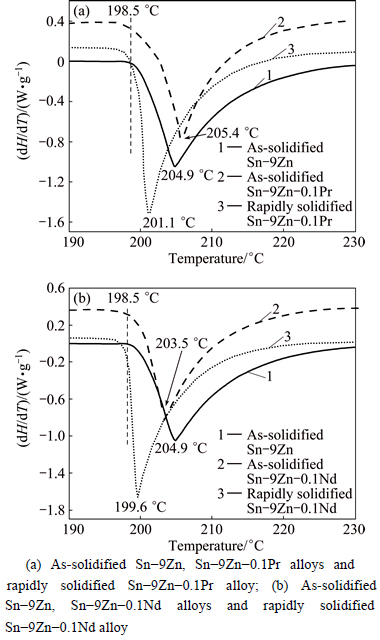
Fig. 4 DSC curves for Sn-Zn(-Pr/Nd) with varying cooling rates:
From Fig. 4, each DSC test curve has only one endothermic peak, indicating that no phase transition occurs before the alloy is molten during heating process. The results also show that the onset temperature of the endothermic peak for each alloy in the DSC heating curves is about 198.5 °C. It can be seen that the effect of solidification rate on the melting point of these alloys is insignificant.
The temperature of the peak point on the DSC heating curve represents the liquidus temperature, and the inflection point of the endothermic peak shows the end of the melting process. The pasty range of alloys is the temperature difference between the solidus temperature and the liquidus temperature. Compared with as-solidified Sn-9Zn alloy, the pasty ranges of the rapidly solidified Sn-9Zn-0.1Pr and Sn-9Zn-0.1Nd alloy are about 2.6 °C and 1.1 °C, respectively, while the pasty range of as-solidified alloy is about 6.4 °C.
Under an extremely cooling condition, the solidified process of alloy is very nonequilibrium. A large amount of crystal latent heat can be absorbed in the rapidly solidified alloy. In the heating process, the rapidly solidified alloys with a metastable thermodynamic state release the crystal latent heat due to the phase inversion, obviously promoting the melting. DSC testing shows that the pasty range of Sn-9Zn-RE alloys is obviously decreased after the rapid solidification. Compared with minor Pr addition, the effect of minor Nd addition on the pasty range of Sn-9Zn-RE alloys is even more obvious. This characteristic of the rapidly solidified solder is beneficial to reducing the thermal damage to electronic components during soldering process.
3.3 Analysis of soldering joints
IMC formation and growth between the molten state solder and substrate is a major issue in soldering process. Figure 5(a) shows the microstructure of the Sn-9Zn/Cu joint after soldering at 240 °C for 3 min. The cross-section SEM image of the bonding area after tensile-shear testing is shown in Fig. 5(b). The phase analysis result of the Sn-9Zn/Cu joint after soldering at 240 °C for 3 min by XRD is shown in Fig. 6.
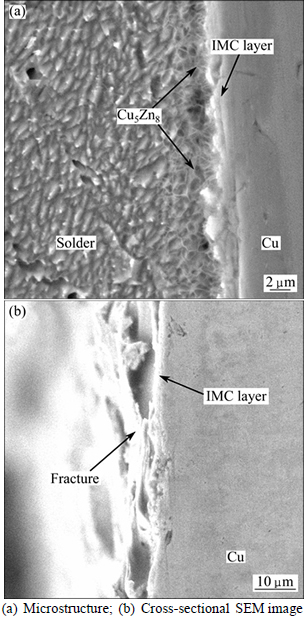
Fig. 5 SEM images of interface of Sn-9Zn solder/Cu joints (240 °C, 3 min):
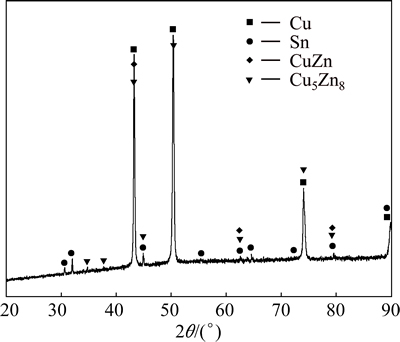
Fig. 6 XRD pattern of Sn-9Zn/Cu joint after soldering at 240 °C for 3 min
From Fig. 5, the interfacial reaction of Sn-9Zn/Cu is obviously uneven. A needle-like IMC layer with about 5 μm in thickness is formed between the solder and the reaction layer in the joint. The IMC layer in the Sn-Zn solder/Cu substrate consists of CuZn and Cu5Zn8 IMCs(Fig. 6), and the Cu5Zn8 layer forms and grows next to the side of solder [3, 5, 8]. In addition, the IMC Cu5Zn8 is formed near the reaction layer due to the diffusion of Cu atoms from Cu substrate to solder and reaction with Zn atoms in the joint. Microstructure of as-solidified Sn-9Zn alloy contains coarse dendrites and large, long rod-like Zn-rich phases (Fig. 1). The inhomogeneous distribution of chemical composition can result in a nonuniform melt in the soldering process. The componential segregation also causes the formation of a nonuniform interfacial reaction layer. Besides, the massive and needle-like IMC Cu5Zn8 are formed unevenly because the Cu atoms react with Zn atoms in the Zn element enriched zone. The IMCs are brittle and unfavorable to the bonding strength.
Microstructure of as-solidified and rapidly solidified Sn-9Zn-RE solder/Cu joints after soldering at 240 °C for 3 min is shown in Fig. 7.
From Fig. 7, by comparison with the as-solidified Sn-9Zn solder/Cu joint (as shown in Fig. 5), the segregation of needle-like IMC Cu5Zn8 does not appear in the interface with the minor addition of RE elements Pr/Nd. The interfacial layer becomes uniform and its thickness decreases due to the strong metamorphism effect by the minor RE addition. During the soldering process, the reaction between Cu and Zn makes a Sn-rich area formed near the IMC layer. Part of the NdSn3/PrSn3 particles are formed which will act as the diffusion barrier of copper and zinc, and thus depress the growth of the IMC layer [18]. On the other hand, the formation of the NdSn3/PrSn3 particles can play a role as the heterogeneous nucleation sites and promote the solidification process. The decreasing of solidification time also reduces the growth of the IMC layer. Figure 7 also shows that the effects of various RE addition in Sn-9Zn alloy are obviously different, mainly in the following three aspects.

Fig. 7 SEM images of interface of solder/Cu joints (240 °C, 3 min) by using various solder:
1) Compared with 0.1% Pr addition, the formation tendency of Kirkendall void is stronger than that of the minor Nd addition, as shown in Fig. 7.
2) There is no obvious Kirkendall void using rapidly solidified Sn-9Zn-RE alloys (Figs. 7(b) and (d)). It is suggested that the interfacial reaction by use of the alloys are more quick and uniform. The distribution of Zn-rich phases in the soldering joints is improved using the rapidly solidified Sn-9Zn-0.1Pr(/Nd) alloys.
3) Compared with rapidly solidified Sn-9Zn-RE alloys, the edge profiles of Cu substrate present little change in as-solidified Sn-9Zn-RE/Cu joint after soldering (Figs. 5(a) and (c)). These results indicate that the interfacial reaction by using rapidly solidified Sn-9Zn-RE alloys is more sufficient. Besides, element Nd has a greater ability to promote the interfacial reaction of Sn-Zn/Cu than element Pr. Under the same soldering condition using rapidly solidified alloys, a uniform scalloped IMC layer is formed at Sn-9Zn-0.1Pr/Cu interface. Meanwhile, the growth of IMC layer at Sn-9Zn-0.1Nd/Cu interface is uneven.
The tensile-shear testing is used to evaluate the effect of minor RE addition in Sn-9Zn alloy on mechanical properties of the solder/Cu joints. Figure 8(a) shows the schematic diagram of soldering joint. Figure 8(b) shows the comparative results of the tensile-shear tests of as-solidified Sn-9Zn/Cu, Sn-9Zn-RE/Cu and rapidly solidified Sn-9Zn-RE/Cu joints at 240 °C for 3 min. Figure 9 shows the typical cross-sectional SEM images of the bonding area after tensile-shear testing for the as-solidified alloys and the rapidly solidified Sn-9Zn-RE alloys.
From Fig. 8, both the minor RE addition in Sn-9Zn alloy and rapid solidification process can improve the bonding strength of the solder/Cu joints. Values of tensile-shear strength of rapidly solidified Sn-9Zn-0.1Pr/Cu joints are the highest due to the formation of uniform scalloped IMC layer in soldering region (Fig. 6(b)). Compared with as-solidified solder/Cu joints, the incrassation of IMC layer is more significant and the bonding interface becomes more uniform and compact (Figs. 8 and 9). This depends on the promotion effect on the molten characteristic and interfacial reaction using the rapid solidified solders during soldering process.
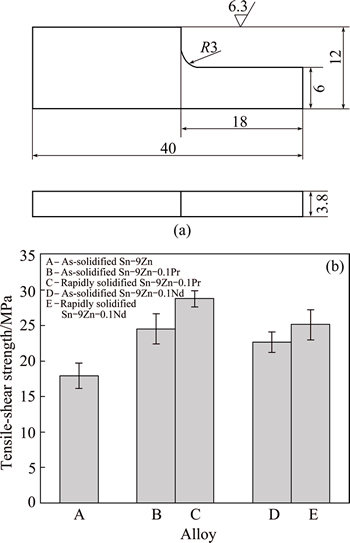
Fig. 8 Schematic diagram of soldering joint (Unit: mm) (a) and results of tensile-shear strength testing (240 °C, 3 min) (b)
The rapidly solidified alloys are in a state of thermodynamics non-equilibrium and contain supersaturated solid solution. During the soldering process, the fusion behavior of the rapidly solidified Sn-9Zn alloy is obviously promoted due to the crystal latent release from the metastable phase. When the rapidly solidified solders are used, the interfacial reaction is more sufficient and the excessive enrichment of Zn phases is avoided (Figs. 7(b) and (d)). On the other hand, by comparison with Fig. 5, Fig. 7 and Fig. 9, it can be seen that the minor RE addition in Sn-9Zn has an obvious suppression effect on the growth of IMC layer in soldering. This prevents the growth of needle-like IMC at the interface. All these factors can promote the joining between solder and Cu substrate.
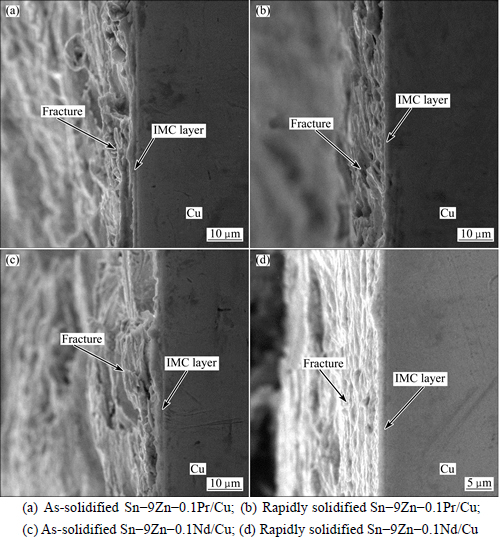
Fig. 9 Cross-sectional SEM images of joint after soldering at 240 °C for 3 min:
4 Conclusions
1) The effects of both minor RE Pr/Nd addition and rapid solidification process on the grain refinement of Sn-9Zn alloy are significant. The metamorphism effect by addition of minor RE elements Pr/Nd is insignificant in rapid solidification process.
2) The effect of solidification rate on the melting point of Sn-9Zn-RE alloys is insignificant. By comparison with as-solidified Sn-9Zn alloy, the pasty range of the rapidly solidified Sn-9Zn-RE alloy is decreased obviously. The effect of minor Nd addition is more remarkable than that of Pr addition.
3) With the addition of minor RE elements Pr or Nd, the formation and growth of interfacial compounds in solder/Cu joints are obviously depressed. The microstructure of the joints becomes more uniform and the mechanical property is improved. These properties are further improved by using the rapidly solidified alloys.
References
[1] MA H, SUHLING J C. A review of mechanical properties of lead-free solders for electronic packaging [J]. Journal of Materials Science, 2009, 44(5): 1141-1158.
[2] LIU S, XUE S B, XUE P, LUO D X. Present status of Sn-Zn lead-free solders bearing alloying elements [J]. Journal of Materials Science: Materials in Electronics, 2015, 26(7): 4389-4411.
[3] ZHANG L, XUE S B, GAO L L, SHENG Z, YE H, XIAO Z X, ZENG G, CHEN Y, YU S L. Development of Sn-Zn lead-free solders bearing alloying elements [J]. Journal of Materials Science: Materials in Electronics, 2010, 21(1): 1-15.
[4] SUGANUMA K, KIM K S. Sn-Zn low temperature solder [J]. Journal of Materials Science: Materials in Electronics, 2007, 18(1-3): 121-127.
[5] HU Y H, XUE S B, YE H, XIAO Z X, GAO L L, ZENG G. Reliability studies of Sn-9Zn/Cu and Sn-9Zn-0.06 Nd/Cu joints with aging treatment [J]. Materials & Design, 2012, 34: 768-775.
[6] XUE P, XUE S B, SHEN Y F, ZHU H, GAO L L. Investigation on the intermetallic compound layer growth of SnZnGa/SnZnGaNd solder joints [J]. Journal of Materials Science: Materials in Electronics, 2014, 25(10): 1-6.
[7] LAVERNIA E J, SRIVATSAN T S. The rapid solidification processing of materials: Science, principles, technology, advances, and applications [J]. Journal of Materials Science, 2010, 45(2): 287-325.
[8] SHALABY R M. Effect of rapid solidification on mechanical properties of a lead free Sn-3.5Ag solder [J]. Journal of Alloys and Compounds, 2010, 505: 113-117.
[9] SHEPELEVICH V G, GUSAKOVA O V. Structure and properties of rapidly solidified Sn-Zn foils [J]. Inorganic Materials, 2008, 44: 485-489.
[10] GUSAKOVA O V, SHEPELEVICH V G. Structure and properties of rapidly solidified foils of alloys of Sn-Zn-Bi system [J]. Inorganic Materials AppliedResearch, 2010, 1: 344-349.
[11] GB 11363—2008. Test method of the strength for brazed and soldered joint (National standard of the People Republic of China) [S]. Beijing: China Standards Press, 2008. (in Chinese)
[12] ZHAO G J, SHENG G M, LUO J, YUAN X J. Solder characteristics of a rapidly solidified Sn-9Zn-0.1Cr alloy and mechanical properties of Cu/Solder/Cu joints [J]. Journal of Electronic Materials, 2012, 41(8): 2100-2106.
[13] ZHAO G J, SHENG G M, XUE H F, YUAN X J. Improved mechanical property of a Cu/Sn-9Zn-0.1Cr/Cu joint using a rapidly solidified solder [J]. Materials Letters, 2012, 68(2): 129-132.
[14] GARCIA L R, OSORIO W R, PEIXOTO L C, GARCIA A. Mechanical properties of Sn-Zn lead-free solder alloys based on the microstructure array [J]. Materials Characterization, 2010, 61(2): 212-220.
[15] JING Y X, SHENG G M, ZHAO G J. Influence of rapid solidification on microstructure, thermodynamic characteristic and the mechanical properties of solder/Cu joints of Sn-9Zn alloy [J]. Materials & Design, 2013, 52(24): 92-97.
[16] HU Zhuang-qi, SONG Qi-hong, ZHANG Hai-feng, LIU Zheng. Metastable metal materials [M]. Beijing: Science Press, 2006: 7-8. (in Chinese)
[17] HU Y, XUE S, WANG H, YE H, XIAO Z, GAO L. Effects of rare earth element Nd on the solderability and microstructure of Sn-Zn lead-free solder [J]. Journal of Materials Science: Materials in Electronics, 2011, 22(5): 481-487.
[18] XIAO Z, XUE S, HU Y, YE H, GAO L, WANG H. Properties and microstructure of Sn-9Zn lead-free solder alloy bearing Pr [J]. Journal of Materials Science: Materials in Electronics, 2011, 22(6): 659-665.
(Edited by YANG Bing)
Foundation item: Project(50675234) supported by the National Natural Science Foundation of China
Received date: 2015-10-20; Accepted date: 2016-03-15
Corresponding author: ZHAO Guo-ji, Professor, PhD; Tel: +86-23-65111826; E-mail: zhaoguoji2006@sina.com