
Microstructural evolution of rolled Mg-5Zn-3Nd(-Zr) alloy
YANG Lin(杨 林), GAO Xiao-dan(高晓丹), LIN Li(林 立), ZOU Peng(邹 鹏),CHEN Li-jia(陈立佳), LIU Zheng(刘 正)
School of Materials Science and Engineering, Shenyang University of Technology, Shenyang 110870, China
Received 23 September 2009; accepted 30 January 2010
Abstract: A mini-type rolling machine was employed for multi-passes rolling of a Mg-5Zn-3Nd(-Zr)(mass fraction, %) wrought alloy. For the sake of providing experimental basis for magnesium alloy rolling process, optical microscopy, SEM and TEM observations were used to study the microstructure evolution of magnesium alloys subjected to different rolling reductions before and after annealing. Investigations show that multi-passes can be achieved for this alloy at ambient temperature, but 330 ?C, 15 min annealing was needed for next pass rolling, and total deformation degree was 66%. With the increase in total deformation degree, rolling streams form and the average grain size decreases gradually. The microstructure after rolling is mainly composed of twining, and multiple twining in parallel distribution is also observed. The average grain size in the as-cast condition is about 50 μm and decreases to about 10-20 μm after rolling, whereas the twinning spacing is limited to 1-2 μm. SAED analysis in the twinning area indicates that twinning takes place at {10
1} plane. Complete recrystallization can occur in Mg-5Zn-3Nd(-Zr) alloys with various rolling reductions and after 200 ?C, 120 min or 300 ?C, 10 min annealing. Meanwhile, grain growth is apparent under heat treatment at 300 ?C.
Key words: Mg-Zn-Nd-Zr; magnesium alloy; deformation; microstructure; annealing
1 Introduction
Magnesium is one of the lightest metal, and its alloys as structural material have huge potential to solve the energy crisis and environmental problems[1-2]. At the same time, magnesium alloys have low density, high specific strength and specific stiffness, good damping capacity, electromagnetic shielding effectiveness and are easy to be recycled, so they have important application value and wide application prospects in the electronic, electrical appliances, transportation, aviation, aerospace and other fields. Magnesium alloy is known as the 21st century’s most promising metal structural material[3]. However, at present, no more studies on the impact of deformation parameters on deforming resistance of magnesium alloy as well as its microstructure were reported[4-7]. ZK60 magnesium alloy as the typical representative of Mg-Zn-Zr system of wrought magnesium alloys has higher strength, better plasticity corrosion resistance, and a wider range of applications[8-9]. While these alloys also have the disadvantage of low room temperature mechanical properties compared with other alloys. In order to improve the strength of ZK60 magnesium alloy, rare earth elements Nd and Y were added into the ZK60 alloy[10]. Therefore, the basic research on the wrought magnesium alloy focuses on adding refiner to the magnesium alloy or making the grain refined by deformation process, the plastic deformation mechanism of hexagonal close-packed structure, and dynamics recrystallization behavior. The research on wrought magnesium alloy processing focuses on the deformation process of certain components of the wrought magnesium alloy, etc[11-14].
In this work, the microstructures of the as-cast Mg-5Zn-3Nd(-Zr)(mass fraction, %) magnesium alloy after plastic deformation under different deformation degrees were investigated, and compared with those of cast Mg-5Zn-3Nd alloy under different deformation degrees after rolling. In order to provide experimental data and technical support for further research and development of the alloy material, the performance changes of the magnesium by adding Zr contents were also studied.
2 Experimental
The magnesium cast ingot of Mg-5Zn-3Nd(-Zr) (mass fraction, %) was adopted as experimental component (the content of Zr is 0.25%-0.50%). A spark-cutting machine was employed to get sheets with width of 40 mm, length 90 mm, and thickness of 6 mm, 4 mm, 3 mm, respectively. The sheets were heated in the box-type resistance furnace at 330 ?C for 0.5 h, and then rolled on a mini-type rolling machine under the speed of 1.2 m/min. The rolling reduction of every pass was about 0.5 mm, and 330 ?C, 15 min annealing was needed for next pass rolling, finally 2 mm-thick rolled sheet with a total deformation of 33%, 50%, 66% were obtained.
An optical microscope was used to observe and analyze the microstructure of magnesium alloys subjected to different rolling reductions. The etchant was composed of 20 mL acetic acid, 1 mL nitric acid, 60 mL glycol and 20 mL water.
An S-3400N scanning electron microscope was used to observe and analyze compositions of the samples. A JEM2010 transmission electron microscope was used to observe and analyze the phase morphology.
3 Results and discussion
3.1 Microstructure of rolled Mg-5Zn-3Nd(-Zr) magnesium alloy
Fig.1 shows the as-cast microstructure of Mg-5Zn-3Nd-Zr and Mg-5Zn-3Nd alloys. Observation shows that the grain size of Mg-5Zn-3Nd alloy is relatively larger (Fig.1(a)); the grain size becomes significantly smaller after adding element Zr (Fig.1(b)), but the grain size is not uniform. The microstructure evolution on longitudinal direction of rolled magnesium alloys after different total deformation degrees is shown in Fig.2. With the increase of deformation degree, rolling streams form gradually. The grain size is non-uniform when the deformation degree is small, and the average grain size decreases with increase in deformation degree. At the same time, the grain size becomes more uniform, and a large number of twining lines are observed in the interior grains.
3.2 Electron microscopy analysis of rolled Mg-5Zn- 3Nd(-Zr) alloys
Fig.3 shows the selected area electron diffraction (SAED) pattern and the TEM images of the Mg-5Zn-3Nd(-Zr) alloy subjected to a total reduction of 66%. Analysis shows that microstructure is composed of a light-colored matrix phase of Mg-based solid solution and the dark second phase. According to an analysis of selected area electron diffraction (insert in Fig.3(a)), the dark of the second phase is MgZn2. From Fig.3(b), the microstructure after rolling is mainly composed of twining, and multiple twining in parallel distribution is also observed. At the same time, many small granules of the second phase exist in the matrix, and the structure of the phase needs further study. Different microstructure morphologies indicate that the average grain size in the as-cast condition is about 50 μm and decreases to about 10-20 μm after rolling, whereas the twinning spacing is limited to 1-2 μm.
The selected electron diffraction patterns of Mg-5Zn-3Nd(-Zr) alloy twins with the total deformation degree of 66% are shown in Fig.4
. Fig.4(a) shows the TEM microstructures of twin and the positions of selected electron diffraction. Fig.4(b) and 4(c) shows the electron diffraction results of A and B points in Fig.4(a), respectively.
A TEM was used to analyze diffraction pattern of the twin. According to the structure of crystallography and the orientation relationship between twinning and matrix of magnesium alloy, the inter-planar distance and the separation angle of crystal plane were used to index crystallographic plane of diffraction spot, so that the twin type was confirmed, as shown in Fig.4(b) and 4(c).
The twins of magnesium alloy usually are {10
2}
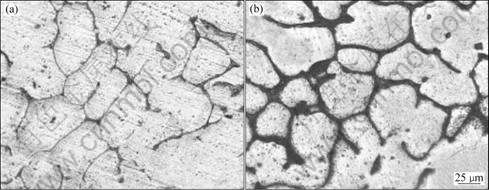
Fig.1 As-cast microstructures of Mg-5Zn-3Nd (a) and Mg-5Zn-3Nd-Zr (b) alloys
Fig.2 Microstructure evolution on longitudinal direction of rolled Mg-5Zn-3Nd-Zr alloy with different total deformation degrees: (a) 33%; (b) 50%; (c) 66%
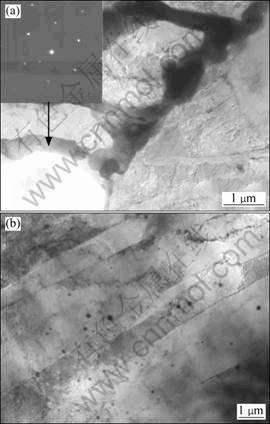
Fig.3 TEM micrographs and SAED pattern of Mg-5Zn-3Nd(-Zr) alloy with total reduction of 66%: (a) Selected area electron diffraction patterns; (b) Twins
and {10
1}, and {10
1} is compression types[15]. The indices of crystallographic plane of a3 and b3 are both (0
11), so it can be concluded that in this experiment, the twining of Mg-5Zn-3Nd(-Zr) alloy is based on {10
1} plane.
3.3 Influence of annealing on rolled Mg-5Zn-3Nd(-Zr) magnesium alloy
Fig.5 shows the microscopic structures of annealed Mg-5Zn-3Nd(-Zr) alloy with different total deformation degrees. The annealing was conducted at 200 ?C or 300 ?C for 120 min. Observation shows that after 200 ?C, 120 min annealing, twinning is observed clearly in the magnesium alloys with total deformation degree of 33%, and only a small amount of recrystallization occurs. A larger number of twinning can be observed in magnesium alloys with total deformation degree of 50%. At the same time, recrystallization also occurs and recrystallization grain size becomes smaller. The twining completely disappears after the total deformation degree of 66%, while the recrystallization appears in large numbers and the recrystallized grains significantly grow bigger than those with the total deformation degree of 50%. When the annealing temperature is increased to 300 ?C, the texture changes of the alloy with total deformation degree of 33% are basically the same with those with annealing at 200 ?C. While a large number of twining in alloy with the total deformation degree of 50% has been ruptured, and recrystallization occurs. The
Fig.4 TEM micrographs and SAED patterns of twins of Mg-5Zn-3Nd(-Zr) alloy with total reduction of 66%: (a) Twins; (b) Electron diffraction at point A; (c) Electron diffraction at point B
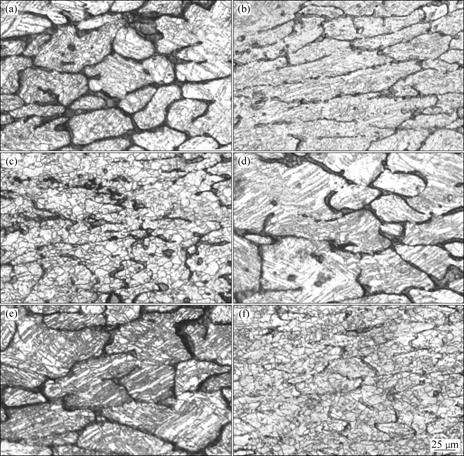
Fig.5 Microstructures of annealed Mg-5Zn-3Nd(-Zr) alloy after different total rolling reductions: (a) Total rolling reduction 33% after 200 ?C, 120 min annealing; (b) Total rolling reduction 50% after 200 ?C, 120 min annealing; (c) Total rolling reduction 66% after 200 ?C, 120 min annealing; (d) Total rolling reduction 33% after 300 ?C, 120 min annealing; (e) Total rolling reduction 50% after 300 ?C, 120 min annealing; (f) Total rolling reduction 66% after 300 ?C, 120 min annealing
twining completely disappears with total deformation degree of 66%. Furthermore, the crystal grain size is smaller than the same deformation alloy annealed at 200 ?C, and grain sizes are uniform.
The experimental results should be directly related to the annealing temperature. With the deformation increasing, the strain energy of material also increases, and the strain energy could enhance the occurrence of the process of recrystallization during annealing process. Since the annealing temperature is higher, the release of strain energy is much more obvious. The alloy annealed at 300 ?C with 66% of the total deformation degree releases a larger strain energy, so the driving force of recrystallization is larger, and a smaller grain size is obtained due to the larger recrystallization nucleation rate.
4 Conclusions
1) With the deformation of Mg-5Zn-3Nd(-Zr) (mass fraction, %) alloy increasing, rolling streams form and the average grain size decreases gradually. Twinning lines are observed in interior grain. The grain size in the as-cast condition is about 50 μm and decreases to about 10-20 μm after rolling, whereas the twinning spacing is limited to 1-2 μm.
2) SAED analysis in the twinning area indicates that twinning takes places at {10
1} plane.
3) Complete re-crystallization can occur in Mg-5Zn-3Nd(-Zr) alloys with various rolling reductions and after 200 ?C, 120 min or 300 ?C, 10 min annealing. Meanwhile, grain growth is apparent under heat treatment at 300 ?C.
References
[1] MORDIKE B L, EBERT T. Magnesium: Properties-applications- potential [J]. Materials Science and Engineering A, 2001, 302(1): 37-45.
[2] KANG Z X. Research and application of wrought magnesium alloys[C]//Proceedings of the 2005 International Conference on Nanotechnology and Advanced Materials. Hong Kong: FMM, 2005: 1-34.
[3] LIU Chu-ming, LIU Zi-juan, ZHU Xiu-rong, HU Bi-wen, WANG Rong, WANG Meng-jun. Influence of isochronal heat treatment on damping behavior of AZ61 alloy [J]. Journal of Central South University of Technology, 2007, 14(3): 315-318.
[4] MYSHLYAEV M M, MCQUEEN H J, MWEMBELA A, KONOPLEVA E. Twinning, dynamic recovery and recrystallization in hot worked Mg-Al-Zn alloy [J]. Materials Science and Engineering A, 2002, 337(1/2): 121-133.
[5] TAN J C, TAN M J. The pathways of dynamic recrystallization in all-metal hip joints [J]. Materials Science and Engineering A, 2003, 339: 124-132.
[6] GUO Qiang, YAN Hong-ge, CHEN Zhen-hua, ZHANG Hui. Hot compression deformation behavior of AZ31 magnesium alloy at elevated temperature [J]. The Chinese Journal of Nonferrous Metals, 2005, 15(6): 900-906. (in Chinese)
[7] WANG Ling-yun, HUANG Guang-sheng, FAN Yong-ge, HUANG Guang-jie. Grain refinement of wrought AZ31 magnesium alloy [J]. The Chinese Journal of Nonferrous Metals, 2003, 13(3): 594-598. (in Chinese)
[8] GALIYEV A, KAIBYSHEV R. Microstructural evolution in ZK60 magnesium alloy during severe plastic deformation [J]. Materials Transactions, 2001, 42: 1190-1199.
[9] MA Yan-long, ZUO Ru-lin, TANG Ai-tao, ZHANG Jing, PAN Fu-sheng. Effect of yttrium on morphologies of precipitation phases along grain boundary of as-cast ZK60 magnesium alloy [J]. Journal of Chongqing University: Natural Science Edition, 2005, 28(2): 51-54. (in Chinese)
[10] MA Chun-jiang, LIU Man-ping, WU Guo-hua. Tensile properties of extruded ZK60-RE alloys [J]. Materials Science and Engineering A, 2003, 349(1/2): 207-212.
[11] GUO Xu-tao, LI Pei-jie, XIONG Yu-hua, LIU Shu-xun, ZENG Da-ben. Application of rare earth in aluminum and magnesium alloys [J]. Journal of Materials Engineering, 2004(8): 60-64. (in Chinese)
[12] WANG Yi-zhi. The new conception of magnesium alloy development [J]. Special Casting & Nonferrous Alloys, 2001(S1): 66-71. (in Chinese)
[13] YU Kun, LI Wen-xian, WANG Ri-chu, MA Zheng-qing. Research, development and application of wrought magnesium alloys [J]. The Chinese Journal of Nonferrous Metals, 2003, 13(2): 277-288. (in Chinese)
[14] COLLEEN J B, MARK A G, OLLEEN J B. Current wrought magnesium alloys: Strengths and weaknesses [J]. JOM, 2005, 57(5): 46-49.
[15] CHEN Zhen-hua. Wrought magnesium alloy [M]. Beijing: Chemical Industry Press, 2005. (in Chinese)
(Edited by LI Xiang-qun)
Foundation item: Project(2007CB613705) supported by the National Basic Research Program of China; Project(2007DFB50150) supported by a Canada-China-USA collaborative Program
Corresponding author: YANG Lin; Tel: +86-24-25694986; E-mail: yanglin318@126.com