
Properties of vacuum cast CuCr25 and CuCr25Te contact material
XIU Shi-xin(修士新)1, YANG Ren(杨 韧)2, XUE Jun(薛 军)3, WANG Jin-xing(汪金星)3
1. State Key Laboratory of Electrical Insulation and Power Equipment, Xi’an Jiaotong University, Xi’an 710049, China;
2. Shaanxi Electric Power Research Institute, Xi’an 710054, China;
3. Shaanxi Electric Power Company, Xi’an 710004, China
Received 10 June 2009; accepted 15 August 2009
Abstract: The CuCr25 and CuCr25Te contact materials were manufactured by vacuum casting process. The microstructures of two alloys were observed by metallographic microscope, the electrical conductivity, density and hardness were measured. The tensile test was done by universal testing machine while the fractography was observed by SEM, the breaking current tests were carried out in Weil Synthetic Circuit with arc-igniting branch in Xi’an Jiaotong University. The results show that the microstructures and physical parameters change after adding Te element. The tensile strength decreases and the toughness turns bad, which is propitious to improve the anti-welding property. But the breaking current capacity of CuCr25Te alloy is inferior to CuCr25 alloy. Thus, adding Te element has both advantages and disadvantages on main properties of CuCr contact material.
Key words: Te; CuCr contact material; vacuum cast
1 Introduction
Contact material is indispensable for vacuum switch. It decides not only the properties of vacuum switch but also the application area. Now, vacuum switch is extensively applied in medium voltage field[1] because the contact material adapts to the need of application.
In the late 1970s, the contact material developed rapidly as a result of the application of powder metallurgy process, and CuCr contact material was manufactured by US Westinghouse Company and British GE Company[2]. The atomic radius of Cu differs from that of Cr, about 18%, and just few atoms can form solid solution. So, CuCr alloy is a kind of machinery-mixed composite material, and the solid solubility of Cu and Cr phase is very low. Cu has lower melting point, high electrical conductivity, high temperature conductivity and good plasticity, which will be helpful to improve the breaking current capacity and rated current of CuCr alloy. Cr provides a good voltage withstand property and anti-corrosion property of arcing, and hot electron emission is difficult to be engendered[3-4]. The CuCr contact material keeps the intrinsic physical properties of Cu and Cr, so the overall performance of CuCr alloy can be better. But the anti-welding property and chopping current level of CuCr contact are not as well as expectation.
In order to solve the existing problems and further improve the property of CuCr contact material, two methods are used now. One is to improve process parameters or seek new manufacturing process. The other is adding new element into the alloy.
In order to improve the anti-welding property, Te element was added to CuCr alloy. In this work, CuCr25Te alloy was manufactured by vacuum casting process, and its physical property, mechanical property, fractograph and breaking current capacity were tested and compared with ones of vacuum cast CuCr25 alloy.
2 Experimental
Recently, new manufacture methods of CuCr25 contact material includes mechanical alloying method, explosive compaction method, arc melting process, plasma spraying process[5-9]. In this work, CuCr25Te alloy was manufactured by vacuum casting process. The chemical composition includes the conductive component Cu, arc-resistant component Cr and anti-welded component Te. Cu and Cr blocks were configured approximately by the mass ratio of 75?25, and Te element was little. The entire cycle of melting in vacuum induction furnace can be divided into the following main stages, loading, melting, refining, alloying and pouring. Fig.1 shows the process of vacuum casting. The Cu, Cr and Te blocks were put into the furnace which would be pumped to high vacuum(1×10-2-3×10-2 Pa), then the melting was done. The solution temperature would reach higher than 1000 ℃after totally melting. The alloy ingot was obtained after the solution curdling in water-cooled copper mould [10-13]. In order to compare CuCr25Te material with the alloy without Te element, CuCr25 alloy was manufactured with the same process.

Fig.1 Process of vacuum casting
The microstructures of two alloys were observed by metallographic microscope, the electrical conductivity, density and hardness were measured with electrical conductivity meter, Brinell hardness tester, Archimedes drainage method, respectively.
The vacuum cast CuCr25Te and CuCr25 contact materials were processed with machining and finishing to obtain the standard tensile test specimen. Then, the tensile test was done on universal testing machine, and the mechanical properties were determined, the fractgraphy was observed by SEM, and the fracture characteristics were analyzed and compared. Fig.2 shows the specimen after tensile test.
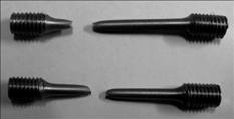
Fig.2 Specimen after tensile test
Two vacuum interrupters with the same structure and the same size were manufactured by using vacuum cast CuCr25Te and CuCr25 contact material. The contact structure was cup-type axial magnetic field, and the shell of vacuum interrupters was ceramic. The contact gap distance was 10 mm.
The processed vacuum interrupters were installed on switch mechanism, and under the same conditions, the breaking current tests were carried out in Weil Synthetic Circuit with arc-igniting branch in Xi’an Jiaotong University. The breaking current increased until the vacuum interrupter failed to break. The arc current signal was gathered by a shunt, and the arc voltage signal was collected by the high-voltage probes fixed on both ends of contacts. The collected signals were imported to a transient oscillograph and recorded.
3 Results and discussion
3.1 Microstructure
Fig.3 shows the microstructures of vacuum cast CuCr25 and CuCr25Te contact material. From Fig.3, it is observed that there are both typically casting structures, Cu matrix and Cr dendrite[14-15]. Since adding Te element, a transition layer is formed between Cu and Cr phases in CuCrTe alloy, and Cr particles become spheral because Te can form Cu2Te and other compounds, and Cr and Te have high solid solubility. During the melting process, Te is melted and reacts with Cu and Cr particles surface. So, the alloy and solution phases are formed. With temperature increasing, the alloy and solution phase with Te element on the particle surface are melted. The particles are rearranged and pilled up, so Cr particles become spheral because of the effect of surface tension.
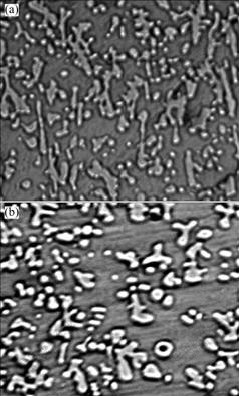
Fig.3 Microstructures of vacuum cast CuCr25 (a) and CuCr25Te alloys (b)
3.2 Physical property
Table 1 shows physical property of vacuum cast CuCr25 and CuCr25Te contact materials. Due to adding Te element, both the electrical conductivity and density of CuCr alloy decrease, but the hardness increases. The mechanical property is improved with hardness
Table 1 Physical properties of materials
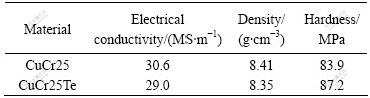
increasing, sequentially, the anti-welted property and chopping current level will be affected greatly.
3.3 Mechanical properties and fractographs
Table 2 shows mechanical properties of CuCr25 and CuCr25Te alloys. Under the tensile test condition, the tensile strength of vacuum cast CuCr25Te alloy is 20-60 MPa, which is lower than that of CuCr25 alloy, but the yield strength changes little. The elongation of vacuum cast CuCr25Te is much smaller than that of CuCr25, which indicates that the former material has worse plasticity.
Table 2 Mechanical properties of materials
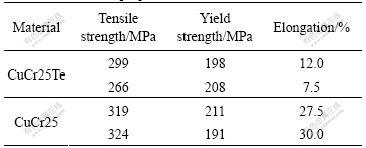
Fig.4 shows the tension fractographs of vacuum cast CuCr25Te and CuCr25 alloys. From Fig.4, the granular brittle fracture characteristic is clearly seen, and there are many Cr particles with big size. This indicates that vacuum cast CuCr25Te alloy has bad toughness. There are obvious dimples with uniform distribution on the fracture surface, and Cr particles with small size distribute evenly in the dimples[16].
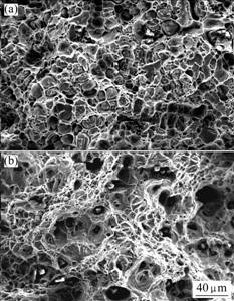
Fig.4 Tension fractographs of vacuum cast CuCr25 (a) and CuCr25Te alloy (b)
Due to adding Te element, the brittle phase is formed at the interface of Cu and Cr particles. So, the tensile strength and the plasticity become bad. From the fractographs, it is seen that adding Te element embrittles the alloy and the toughness turns bad.
The anti-welded property of contact material has direct relationship with its tensile strength. In order to pull open the welding points reliably under the opening force of switch mechanism, welding points must have very low tensile strength. Usually, the tensile strength of contact material matrix is used to evaluate the anti-welded property. The anti-welded property improves with tensile strength decreasing. Also bad toughness is conductive to anti-welded property. So, adding Te element improves the anti-welded property of CuCr contact material.
3.4 Breaking current capacity
Fig.5 shows arc current and arc voltage oscillograms of CuCr25 and CuCr25Te.
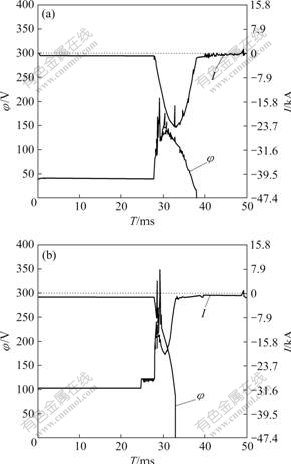
Fig.5 Test waves of CuCr25 and CuCr25Te contact materials: (a) CuCr25; (b) CuCr25Te
The result shows that the limiting breaking current of vacuum cast CuCr25 is 23.9 kA while that of CuCr25Te contact material is 20.1 kA. The breaking current capacity of CuCr25 contact material decreases 3.8 kA after adding Te element.
Adding Te element with low melting point will improve the anti-welded property of CuCr alloy. But low melting point phase has high vapor pressure. It supplies metal vapor to contact gap, which is necessary for arc burning. So, it is bad for arc extinguishing. Moreover, adding Te element reduces the electrical conductivity of CuCr alloy. So, the breaking current capacity decreases after adding Te element.
4 Conclusions
1) Adding Te element makes Cr particles turn to be spheral and their physical property changes.
2) The electrical conductivity, density of CuCr25Te are larger than these of CuCr25, but the hardness is lower.
3) Comparing with CuCr25 alloy, the tensile strength and the plasticity of vacuum cast CuCr25Te alloy decreases, and the toughness becomes bad. All above changes are conductive to improve anti-welded property of contact material.
4) Vacuum cast CuCr25Te alloy has lower breaking current capacity, about 16% that of CuCr25.
References
[1] LI Jian-ji. The development of medium-voltage vacuum circuit breaker market and technology [J]. Shanghai Electric Power, 2006(2): 182-183. (in Chinese)
[2] BOXMAN R L. Twenty-five years of progress in vacuum arc research and utilization [J]. IEEE Tran on Plasma science, 1997, 25(6): 1174-1185.
[3] XIA Cheng-dong, TIAN Bao-hong, LIU Ping, REN Feng-zhang. Current research status on CuCr alloy for contact material [J]. Today’s Foundry, 2007, 28(1): 139-140. (in Chinese)
[4] XIAN Ai-ping. The development of manufacture processing for CuCr contact alloy [J]. Actametallurgica Sinica, 2003, 39(3): 225-233. (in Chinese)
[5] LI Jin-ping, MENG Song-he, HAN Jie-cai. Structure and flaws of CuCr alloys by explosive compaction [J]. Journal of Harbin Institute of Technology, 2005, 12(2): 135-138. (in Chinese)
[6] SCHELLEKENS H. Plasma sprayed contact materials for vacuun interrupters [C]// IEEE 15th International Symposium on Discharges and Electrical Insulation in Vacuum. Damstadt: Germany Vacuum Society, 1992: 499-502.
[7] LI Xiao-yan, WANG Shun-xing, TIAN Bao-hong. Present status and development of Cu-Cr contact materials [J]. Materials Reseach and Application, 2007, 36(4): 266-269. (in Chinese)
[8] ZHU Jian-juan, TIAN Bao-hong, LIU Ping. Progress of proparation technology for CuCr contact materials [J]. Shanghai Nonferrous Metals, 2006, 27(4): 27-32. (in Chinese)
[9] XIAN Ai-ping. CuCr contact materials for high power vacuum interrupters [J]. The Chinese Journal of Nonferrous Metals, 2001, 11(5): 731-738. (in Chinese)
[10] DING Yong-chang. Special fusion [M]. Beijing: Metallurgical Industry Press, 1995. (in Chinese)
[11] FU Su-jia. Design of low welding strength CuCrTe contact material [J]. High Voltage Apparatus, 1997, 33(2): 16-18. (in Chinese)
[12] ZHAO Feng, DING Bin-jun. CuCr25 alloys prepared by melting in vacuum and its behavior [J]. High Voltage Apparatus, 1999, 51(3): 12-14. (in Chinese)
[13] XIAO En-kui, LI Yao-qun. The technology of Cu and Cu-based alloy smelting and casting [M]. Beijing: Metallurgical Industry Press, 2007. (in Chinese)
[14] XIU Shi-xin. Microstructure and properties of CuCrTe contact material for vacuum switches [J]. Vacuum Electronics, 2007, 50(5): 55-58. (in Chinese)
[15] SPAIC S, KOMAC M. Microstructure and properties of sintered CuCr alloy [J]. Materials and Technology, 1989, 28(5): 1069-1073. (in Chinese)
[16] MIAO Bei-he, ZHANG Yan, LIU Guo-xun. The influence of mechanical properties and fractographs of CuCr(75/25) contact materials on the contact performance [J]. Electrical Material, 2006, 37(4): 3-7. (in Chinese)
(Edited by LI Yan-hong)
Corresponding author: XIU Shi-xin; Tel: +86-29-88578218; E-mail: xsx@mail.xjtu.edu.cn