
Theory and application research development of semi-solid forming in China
LUO Shou-jing(罗守靖)1, W. C. KEUNG(姜永正)2, KANG Yong-lin(康永林)3
1. School of Materials Science and Engineering, Harbin Institute of Technology, Harbin 150001, China;
2. Ka Shui International Holdings Ltd, Shenzhen 518111, China;
3. School of Materials Science and Engineering, University of Science and Technology Beijing, Beijing 100083, China
Received 13 May 2010; accepted 25 June 2010
Abstract: In order to adapt to the trend of “energy saving and emission reduction” and impel the practical application of semi solid processing (SSP) in China, the progress and application of semi-solid theory in China have been reviewed briefly and systematically. It was emphasized on basic theories, such as formation of globular grains, rheology, high pressure solidification and plastic deformation and applications, such as material design, preparation of semi-solid billets (slurries), thixoforming and application status, which are based on the advantage of semi-solid processing. The results show that the gap of SSP between world level and China exists, especially in application technologies, including market recognition, application fields exploiting, developing of billets (slurries) preparation technologies with low cost and special equipments. The prospect of semi-solid forming development path in China is presented. And we hope that application of SSP has great new breakthrough and development and China will be changed from a large metal processing country to a powerful metal processing country.
Key words: semi-solid processing; theory; production; forming
1 Introduction
As a kind of new near net shape metal processing technology, semi solid processing (SSP) has the brightest future in the 21st century[1-3]. In China, the theory and application of SSP have been developed into a new level, which are accelerated by the policy of energy saving and emission reduction. In this work, the progress and application of semi-solid theory in China have been reviewed systematically.
2 Theoretical research
2.1 Formation of globular grains theory
Spherulite formation theory is referred to the globular grains generated from the interior of melt directly without dendrite formation during solidification, fragmentation and ripping. This viewpoint was supported by results in Refs.[4-5]. According to Ref.[4], vigorous stirring can impel primary crystals to form spherulite directly above liquidus. In Ref.[5], it was considered that the spherulite is the main growth pattern in undercooled melt under the condition of high grain density and slow cooling.
2.2 Rheology theory
1) Rheological mechanics
In Ref.[6] it was proposed that the rheology occurs when the external stress applied to the rheological body reaches the thixotropic strength and the external load decreases quickly with deformation degree increasing and then reaches steady value. Obviously, the thixotropic strength is changed with yield strength.
2) Rheological metallurgy
Experimental results of the influence of spherical microstructure on rheology were obtained in Ref.[6]. The rheology mechanism of interaction was analyzed in detail between the mainstream and non-mainstream phase transition with different liquid volume fractions[7].
2.3 High pressure solidification theory
The deformable body solidifies under high pressure with external stress because the filling time is short and there is liquid phase in the body after filling. Some research results were given in Ref.[2], where the metallurgical equation for high pressure solidification and microstructure refinement was proposed.
2.4 Plastic deformation theory
The plastic deformation exists in high pressure solidification-densification rheological process. The plastic deformation process was analyzed in detail in Ref.[2], and the stress-strain expression and microstructure characteristics were given.
3 Technology application
3.1 Development and design of semi-solid materials
At present, semi-solid materials are used widely in China, for example, Pb, Sn, Zn, Al, Mg, Cu, Ti, steel and composites. Some typical materials are listed as follows.
3.1.1 Aluminum alloy
Application of aluminum alloy is most in semi-solid process. At present the alloys are some cast aluminum alloys, for example A356, A357, A319, A380 and A390. And some wrought aluminum alloys are in experimental considerations[8-9]. Some wrought aluminum alloys and cast aluminum alloys used in semi-solid process are shown in Table 1. Fig.1 shows some typical aluminum alloy microstructures.
3.1.2 Magnesium alloy
The main technologies for magnesium alloys are thixoforming and injection molding. The common alloys are AZ61, AZ80, AZ91D and AM60[10-11]. Table 2 lists the compositions of these alloys. And Fig.2 shows the microstructures of semi-solid billets by SIMA.
3.1.5 Steel
Some kinds of steel materials were studied in University of Science and Technology Beijing with electromagnetic stirring device designed by themselves[12]. Among them the primary austenite grains of 1Cr18Ni9Ti semi-solid billets are spherical or near spherical. The size is 100-200 μm. The solid fraction is 50%-60%. Its fluidity is good. Fig.3 shows the semi-solid microstructures with different parameters. The study of Fe-Cr-C proved that electromagnetic stirring can improve the distribution, morphology and size of carbides availably by XING et al[13] in Beijing Jiaotong University.
3.1.4 Metal matrix composite
Table 1 Thermal properties of aluminium alloy
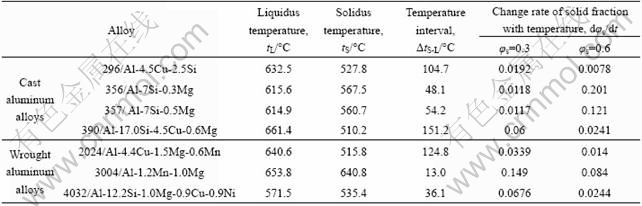
Table 2 Compositions of semi-solid magnesium alloy (mass fraction, %)

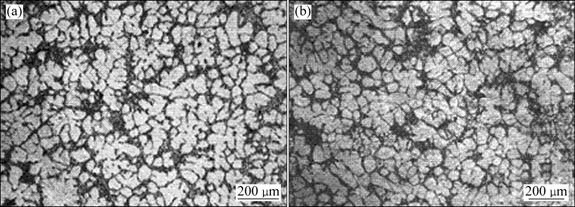
Fig.1 Microstructures of aluminum alloy semi-solid billets: (a) A356 (Near-liquidus pouring); (b) A390 (Ultrasonic vibration)
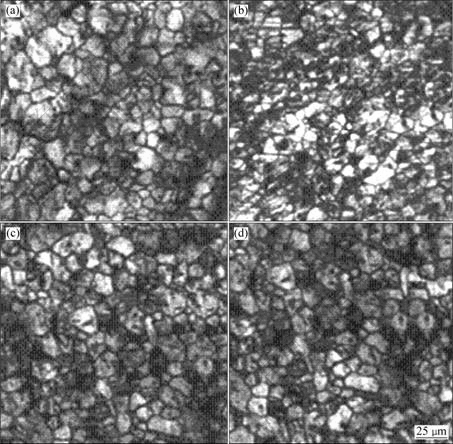
Fig.2 Microstructures of magnesium alloy billets by SIMA: (a) AZ61; (b) AZ80; (c) AZ91D; (d) AM60
Now some metal matrix composites have been used in semi-solid technology, for example, SiC reinforced metal matrix composites. Fig.4 shows the 4.4%TiCp/7075Al metal matrix composite semi-solid billets by near-liquidus cast in Inner Mongolia University of Technology[14].
3.2 Technologies for semi solid billets
There are more than 20 kinds of technologies with different characteristics for semi-solid billets or slurries. In China, they are mechanical stirring, electromagnetic stirring, sloping plate, mechanical (ultrasonic) vibration, cone barrel rotation and near-liquidus pouring, etc[15]. In addition, some new technologies are proposed with many mixed solidification control technologies, for example, low temperature in combination with weak electromagnetic stirring[16], mechanical vibration + sloping plate[17], melt spreading and mixing technique process(MSMT)[18].
3.2.1 Novel sloping plate process
The sloping plate process for semi-solid billets is proposed by Japanese scholars. The process is cost-effective. Today, most studies on it are straight sloping plate. But, there are many faults in it. For example, there are some incrustation on the surface of plate or spheroidization effect is non-ideal. GUO et al[16] in Northeastern University developed a sloping plate with wave shape surface and vibration (Fig.5). Compared with traditional sloping plate technology, the primary solid grains of novel sloping plate process are fine and size of granular grains is uniform.
GUO and YANG[19] in Nanchang University developed a slurry making technique of low superheat pouring with a shear field (LSPSF). The alloy liquid with some superheat degree was poured in delivery pipe. Then, it was changed into metal molten with some solid fraction because of gravity and shearing/cooling action of delivery pipe inner wall. The primary grains of semi solid billets were homogeneously distributed. The theory of LSPSF is shown in Fig.6.
3.2.2 Taper barrel rheomoulding (TBR)
Fig.7 shows the structure diagram of taper barrel rotation for semi-solid slurry production which was proposed by KANG et al[8] in University of Science and Technology Beijing. Now, the device is in the 3rd generation by some years’ development and it has obtained the national patents. The device mainly consists of slurry preparation equipment, transmission system, elevating system, slurry conveying appliance, gas protection and temperature control system. The device is vertical. The production and transportation of semi-solid slurry are realized by the self weight of liquid metal. The grains of primary α(Al) are fine and round. Fig.8 shows the microstructure of A356 in semi-solid state sheared at 590 °C.

Fig.3 Microstructures of semi-solid 1Cr18Ni9Ti at different stirring power and time: (a) 0.58 kW, 80 s; (b) 0.58 kW, 120 s; (c) 0.58 kW, 150 s; (d) 0.8 kW, 120 s; (e) 0.8 kW, 180 s; (f) 1.4 kW, 180 s; (g) 1.4 kW, 230 s; (h) 1.4 kW, 365 s
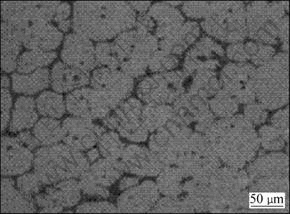
Fig.4 Microstructure of 4.4%TiCp/7075 aluminum matrix composite billet
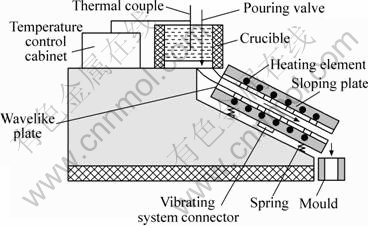
Fig.5 Schematic of vibrating wavelike sloping plate

Fig.6 Schemalic illustration of LSPSF slurry maker
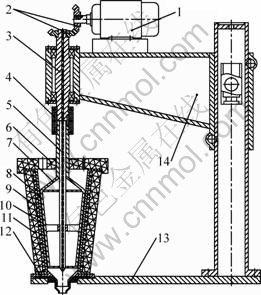
Fig.7 Schematic illustration of TBR machine: 1 Motor; 2 Driving bevel gears; 3 Driving mandrel; 4 Coupling; 5 Argon channel; 6 Thermal cover; 7 Internal taper barrel; 8 External taper barrel; 9 Heating elements; 10 Cooling channels; 11 Muff; 12 Flange; 13 Bottom plate; 14 Elevating system

Fig.8 Microstructure of semi-solid A356 alloy (Shearing temperature of 590 °C)
3.2.3 Melt spreading and mixing technique (MSMT) process
Melt spreading and mixing technique (MSMT) process is a new technology for semi solid billet preparation proposed by SHI et al[18] in General Research Institute for Nonferrous Metals. The device mainly includes melt insulation furnace, slurrying chamber, rotation dispersion disc, temperature control system and collection crucible (Fig.9). The molten metal is poured on the revolving disc and thrown to the inner wall of slurrying chamber. Then, a flow layer is formed with a certain thickness. When the pouring speed and rotational speed of disc are controlled, the flow layer and the temperature are uniform. During flowing process, nucleation takes place homogeneously by heat exchange between the molten metal and the external one. And the supercooling degree for nucleation is satisfied. The slurry collected by crucible cools slowly. The crystal nucleus grow in uniform temperature field and finally reach the needed solid fraction.
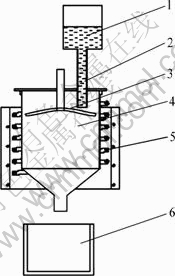
Fig.9 Schematic diagram of MSMT apparatus: 1 Heating furnace; 2 Liquid metal transport tubes; 3 Rotate plate; 4 Slurry making chamber; 5 Temperature control elements for slurry making chamber; 6 Receiving crucible
3.2.4 High intensity ultrasonic preparation
The device of high intensity ultrasonic for semi- solid slurry preparation mainly consists of ultrasonic controller, transducer, amplitude transformer, temperature controller, furnace and insulation cup (Fig.10)[20]. The main flow process is alloy melting, pouring into insulation cup, ultrasonic vibration, slurry transmission, pouring into die chamber and injection molding. Fig.11 shows the microstructures of ZL101 aluminum alloy in semi-solid state by ultrasonic vibration.
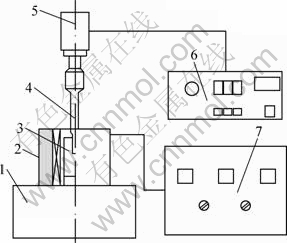
Fig.10 Schematic diagram of ultrasonic vibration device: 1 Supporting disk; 2 Furnace; 3 Insulation cup; 4 Amplitude transformer; 5 Transducer; 6 Ultrasonic controller; 7 Temperature controller
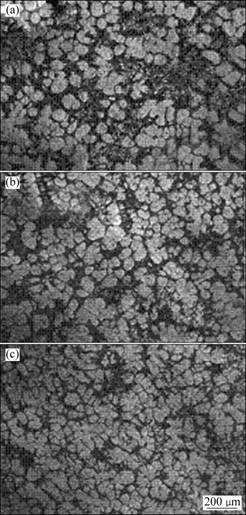
Fig.11 Microstructures of ZL101 alloy in semi-solid state by ultrasonic vibration technology for different vibration time: (a) 0.6 min; (b) 1.2 min; (c) 1.8 min
3.3 Semi-solid processing
Now, many semi-solid processing methods have been used, for example, semi solid rheo-diecasting, semisolid squeeze casting, semi-solid forging and semi-solid rolling[3]. The small batch production or trial production parts includes axlebox, plate, box and bracket parts. These parts involve automobile, military, aerospace, engineering machinery, rail transit, equipment manufacturing and electronic information fields.
3.3.1 Semi solid rheo-diecasting
KANG et al[8, 21] invented the taper barrel rheo-molding machine(TBR). It realizes integrated technology process from slurry preparation, transmission and squeeze casting. And the rheo squeeze casting of AZ91D was studied. Fig.12 shows the architectural scraper by rheo squeeze casting and microstructures at different locations. Compared with the traditional squeeze casting, the grains of the parts are spherical or near spherical, and uniform with low porosity with an average grain size of 45 μm.
YANG et al[9] realized rheo-squeeze casting in combination with LSPSF and traditional squeeze casting technology. And the rheo-squeeze casting of YL112 was studied systematically. The microstructure of parts by this technology is fine and uniform. The average effective diameter of primary solid grains is 70 μm and the average shape factor is 0.93. There is no liquid phase in primary phases. Fig.13 shows the bracket by rheo squeeze casting and its microstructure.
The serpentine channel pouring (SCP) process was proposed by MAO et al[22-24]. It further simplified the process of semi-solid slurry preparation. Firstly, the overheated alloy liquid poured into vertical serpentine channel flows along the inner wall, then into the crucible. Secondly, the alloy liquid solidifies and the semi solid slurry with spherical primary grains forms. Finally, the slurry is formed by semi-solid rheo-diecasting. Fig.14 shows the schematic diagram of SCP process.
3.3.2 Thixoforging in semi solid state
Now, many kinds of aluminum alloys and Cu alloys have been thixo-forged in semi solid state. Most of Al alloys are A356 and A357 prepared by continuous electromagnetic stirring casting. The experimental thixo- forming Al alloys are 2024, 2219, A2618, 6062, A6082, 7021 and 7075 etc[25].
Double control forming in semi-solid state proposed by LUO et al[2, 26] in Harbin Institute of Technology (HIT) based on semi-solid thixo-forging integrates the characteristics of liquid squeeze casting and semi-solid thixo-forging. It can realize the accurate control of shapes, sizes and properties. It combines the advantages of squeeze casting and forging and eliminates the shrinkage of die casting. At the same time, it can form complex high-accuracy part. The schemalic illustration of combination process of diecasting and forging is shown in Fig.15. semi-solid state was designed and manufactured in University of Science and Technology Beijing (as shown in Fig.16). The 60Si2Mn and 1Cr18Ni9Ti semi-solid slurry were prepared by electromagnetic stirring successfully. And microstructure evolution, mechanical behavior and quality of parts of semi-solid slurry during rolling were studied systematically[12, 27]. Some basic researches of semisolid rolling for Mg alloys were studied by General Research Institute for Nonferrous Metals and Nanchang University. The semi- solid slurry was prepared by mechanical stirring. The key point of research is technology parameters of side dam, forming temperature of slurry, rolling speed and rolling force etc[25].

Fig.12 Microstructures of rheo-diecasting architectural scraper at different locations
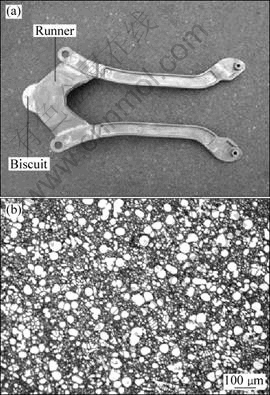
Fig.13 Rheo-diecasting bracket (a) and its microstructure (b)
3.3.3 Semi-solid rolling
The rheo-rolling device for steel materials in
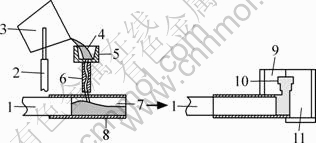
Fig.14 Schematic diagram of SCP process: 1 Plunger; 2 Elevating system; 3 Crucible; 4 Alloy melt; 5 Injection gate; 6 Serpentine channel; 7 Chamber; 8 Slurry; 9 Static die; 10 Casting; 11 moving die
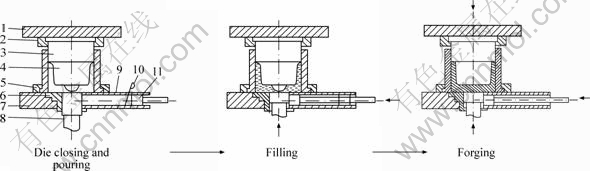
Fig.15 Schemalic illustration of combination process of diecasting and forging: 1 Upper clamping plate; 2 Punch-retainer plate; 3 Lower die; 4 Upper die; 5 Cavity-retainer plate; 6 Charging cylinder; 7 Lower clamping plate; 8 Press head; 9 Transfor tube; 10 Rotation pouring system; 11 Punch
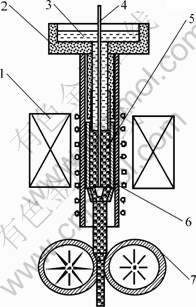
Fig.16 Schematic diagram of semi-solid steels preparation and rheorolling: 1 Electromagnetism stirring; 2 Pouring gate; 3 Liquid steel; 4 Bung; 5 Semi-solid slurry; 6 Stirring crucible; 7 Water-cooling roller
3.4 Application status of semi-solid technology
The semi-solid forming technology has been studied and developed for 30 years. Overseas, it has been in the level of industrial application. The leading countries of application level are American, Italia, Japan, German, England, France, etc. It began late in China (1980s) in some universities and research institutions[28-29]. Great progress has been achieved in basic theory research of semi-solid technology and some kinds of experimental equipments have been self-designed and self- manufactured by University of Science and Technology Beijing, Harbin Institute of Technology, Southeast University, Shanghai University, Tsinghua University, Dalian University of Technology, Nanchang University, Northwestern Polytechnical University, General Research Institute for Nonferrous Metals, etc[30-32] by the support of “863 Program”, “ 973 Program”, National Natural Science Foundation of China during “the 9th Five-Year Plan” and “the 11 Five-Year Plan”. Rheofroming and thixoforming of Mg alloys have been primarily applied in automotive and other industry fields in recent years. For example, the TBR medium test line for rheo squeeze casting of Mg in semi-solid state has been built cooperated by University of Science and Technology Beijing and Beijing Guangling Jinghua Co. Ltd. This built a foundation for its industry application[8, 12]. A new technology for the preparation of semi-solid slurry or billet by composite continuous electromagnetic stirring has been exploited by General Research Institute for Nonferrous Metals. The max diameter of the aluminum alloy semi-solid billet is over 200 mm by this technology. At the same time, a production demonstration line of aluminum alloy semi-solid billet by continuous electromagnetic stirring with annual production of 500 t has been self-designed and built. The production and test bases of semi solid thixo squeeze casting and semi-solid thixoforging have been built by the cooperation between General Research Institute for Nonferrous Metals and Dongfeng Carburetor Co. Ltd, General Research Institute for Nonferrous Metals and Shanghai Chenguang Locomotive Matching Co. Ltd. The Al alloy parts forged in semi-solid state are shown in Fig.17[25, 33]. The AZ91D motor wheels have been prepared by double control forming technology by the cooperation between Changjinmei Technology Co. Ltd of Hongkong Ka Shui Holdings Group and Harbin Institute of Technology[34].
4 Prospect
1) Strengthening the basic research and exploitation of semi-solid forming technology, seeking for technological innovation;

Fig.17 Automobile parts of semi solid Al alloy: (a) Water pump cover; (b) Rod; (c) Piston; (d) Swash plate
2) Reducing the cost of semi-solid billets preparation;
3) Enlarging the application scope of semi-solid forming technology;
4) Exploiting the special alloy system for semi-solid forming technology;
5) Strengthening the professional design and manufacture of devices for semi-solid process;
6) Developing academic exchange, strengthening the cooperation between the university, institute and production enterprises, impelling jointly the application of semi-solid forming technology.
References
[1] KANG Yong-lin, MAO Wei-ming, HU Zhuang-lin. Theory and technology of metal semi solid process [M]. Beijing: Science Press, 2004. (in Chinese)
[2] ZHAO Zu-de, LUO Shou-jing. Semi solid forming technology of light alloy [M]. Beijing: Chemical Industry Press, 2007. (in Chinese)
[3] HUANG Xiao-feng, LIANG Yan, WANG Tao, XIE Rui, CAO Xi-juan, ZHU Kai, TIAN Zai-you. Development of metal semi solid forming study [J]. China Foundry Machinery &Technology, 2009(2): 6-9. (in Chinese)
[4] LI Tao. Evolution of semi solid microstructure and observation of rehology [D]. Xi’an: Northwestern Polytechnical University, 2003. (in Chinese)
[5] GUO Hong-ming. Study on technology and theory of al alloy semi solid rheoforming [D]. Nanchang: Nanchang University, 2007. (in Chinese)
[6] SHAN Wei-wei. Study on semi solid spherical structure formation of ZK60-RE and thixotropy behavior with high solid fraction [D]. Harbin: Harbin Institute of Technology, 2008. (in Chinese)
[7] XIN Shu-ming, TAN Jian-bo, ZHANG Li-zhong. Rheological technology theory of semi-solid alloy [J]. Special Casting and Nonferrous Alloys, 2005: 243-247. (in Chinese)
[8] KANG Yong-lin, YANG Liu-qing, SONG Ren-bo, ZHANG Fan, TAO Tao. Study on microstructure-processing relationship of a semisolid rheocasting A357 aluminum alloy [J]. Solid State Phenomena, 2008, 141/142/143: 157-162.
[9] YANG Yi-tao, SHAO Guang-jie, ZHANF Heng-hua, XU Nuo-ping. Ten years review of the foundation and application study of aluminum alloy forming in semi-solid state [J]. Special Casting and Nonferrous Alloys, 2008, 28(5): 367-371. (in Chinese)
[10] ZHAO Zhen-duo, MAO Wei-min. Preparation of semi-solid AlSi7Mg alloy slurry [J]. Acta Metallurgica Sinica, 2008, 21(2): 139-145.
[11] LI Qiang, HUANG Guo-jie, XIE Shui-sheng, YU Bao-yi. Development of Mg alloy forming in semi-solid state [J]. Hot Working Technology, 2009, 38(23): 61-65. (in Chinese)
[12] SONG R B, KANG Y L, ZHAO A M. Semi-solid rolling process of steel strips [J]. Journal of Materials Processing Technology, 2008, 198: 291-299.
[13] XIN Shu-ming, BAO Pei-wei. Industrial application of semi-solid processing [J]. Special Casting and Nonferrous Alloys, 2009: 337-340. (in Chinese)
[14] ZHANG Fu-yi, LIU Hui-ming, LIU Li. Reheating microstructure of TiCp/7075 Al matrix composite [J]. Journal of University of Science and Technology Beijing, 2009, 31(12): 1583-1587. (in Chinese)
[15] ZHANG Xiao-li, LIU Ting-ju, XIE Shui-sheng. Research development of slurry preparation technology for semi-solid alloy [J]. Rare Metal Materials and Engineering, 2009, 38(8): 1495-1500. (in Chinese)
[16] GUO H M, YANG X J. Low superheat pouring with a shear field in rheoeasting of aluminum alloys [J]. Journal of Wuhan University of Technology (Materials Science Edition), 2008, 23(1): 54-59.
[17] XIE Feng-guang, GUAN Ren-guo, LI Jiang-ping. Direct growth behavior of grains during vibrating wavelike sloping plate [J]. Journal of Northeastern University (Natural Science), 2009, 30(3): 377-380. (in Chinese)
[18] ZENG Yi-dan, SHI Li-kai, ZHANG Zhi-feng. Semi-solid slurry prepared by the melt dispersion mixing [J]. The Chinese Journal of Nonferrous Metals, 2008, 18(4): 630-636. (in Chinese)
[19] GUO Hong-ming, YANG Xiang-jie. Microstructure character of YL112 alloy by rheology injection [J]. The Chinese Journal of Nonferrous Metals, 2008, 18(3): 400-408. (in Chinese)
[20] WU Shu-sen, ZHAO Jun-wen, WAN Li, MAO You-wu. Research of Al alloy semi-solid slurry technology by high-intensity ultrasonic [J]. Special Casting and Nonferrous Alloys, 2009, 29(1): 1-4. (in Chinese)
[21] YANG Liu-qing, KANG Yong-lin, ZHANG Fan. Study of rheological injection microstructure and technology of A357 alloy in semi-solid state [J]. Material Engineering, 2009(6): 64-66. (in Chinese)
[22] MAO Wei-min, LIN Hai, BAI Yue-long, GAO Song-fu. New method for the preparation of semi-solid AlSi7Mg alloy slurry [J]. Journal of University of Science and Technology Beijing, 2007, 14(1): 56-60.
[23] LIU Zheng, MAO Wei-ming, ZHAO Zhen-ze. A356 semi-solid slurry prepared by new technology [J]. Acta Metallurgica Sinica, 2009, 45(4): 507-512. (in Chinese)
[24] MAO Wei-ming, GAO Chong, ZHU Da-ping, CHEN Zhen-zhou, ZHANG Yun-tao. Study on Al alloy semi-solid slurry prepared by serpentine passage [J]. Special Casting and Nonferrous Alloys, 2009, 29(10): 915-917. (in Chinese)
[25] ZHANG Zhi-feng, XU Jun. Study on technology and application of light alloy and its composite forming in semi-solid state [J]. New Technology & New Process, 2009(2): 19-22. (in Chinese)
[26] CHENG Yuan-sheng, LUO Shou-jing. Thixoforging of Al/Al2O3 composite in pseudo-semi-solid state [J]. Acta Materiae Compositae Sinica, 2009, 126(16): 116-120. (in Chinese)
[27] SONG R B, KANG Y L, ZHAO A M. Fabrication of semi-solid slurry for steels and their rheo-rolling process [J]. Solid State Phenomena, 2008, 141/142/143: 457-461.
[28] ZHANG Y F, LIU Y B, CAO Z Y. Mechanical properties of thixomolded AZ91D magnesium alloy [J]. Journal of Materials Processing Technology, 2009, 209(3): 1375-1384.
[29] ZHU Guang-lei, XU Jun, BAI Yue-long. Influence of slurry preparation parameters on microstructure of A357 alloy by ring seam type electromagnetic stirring method [J]. Special Casting and Nonferrous Alloys, 2009(4): 402-405. (in Chinese)
[30] ZENG Yi-dan, ZHANG Zhi-feng, LIANG BO. Influence of flowing velocity of melt on slurry microstructure by CRP [J]. Special Casting and Nonferrous Alloys, 2007(S1): 408-409. (in Chinese)
[31] LI Miao-quan, LU Ya-lin, JIANG Hai-tao, HUANG Wei-chao. Model and application of semi-solid rheology behavior [J]. Materials Review, 2009, 23(2): 1-5 (in Chinese)
[32] HOU Wen-jie, TAN Jian-bo, LIU Jiang-cheng. Research status and development of semi-solid rheohogy injection [J]. Casting Technology, 2009, 3(1): 91-94. (in Chinese)
[33] XU Jun, WANG Hai-dong, ZHANG Zhi-feng. Study on design and optimization of new semi-solid Al alloy [J]. Casting Technology, 2006, 27(3): 249-251. (in Chinese)
[34] LI Yuan-fa, CHEN Liang, SHAN Wei-wei. Investigation of AZ91D alloy mechanical propoties on the motorcycle wheel hub produced by the horizontal double control (die casting & forging) shaping casting [J]. Special Casting and Nonferrous Alloys, 2009(Injection Special Issue): 8-10. (in Chinese)
(Edited by YANG Bing)
Corresponding author: LUO Shou-jing; Tel: +86-451-86418723; E-mail: luosj@hit.edu.cn
DOI: 10.1016/S1003-6326(09)60378-2