
Structural characterization and property of in-situ synthesized AZ91-Mg2Si composite
DONG Long-xiang(董龙祥)1,2, WU Yao-ming(吴耀明)2, DOU Chuan-guo(豆传国)2,
XU Guo-gen(许国根)1, WANG Li-min(王立民)
1. Department of Environmental Engineering, The Second Artillery Engineering Institute, Xi’an 710025, China;
2. Key Laboratory of Rare Earth Chemistry and Physics, Changchun Institute of Applied Chemistry,
Chinese Academy of Sciences, Changchun 130022, China;
Received 28 July 2006; accepted 15 September 2006
Abstract: A new-type Mg2Si composite was prepared with Mg-9Al-1Zn (AZ91) alloy and vermiculite as raw materials by melt infiltration method. The results show that the microstructure of composite consists of a large amount of Mg2Si precipitates and a little amount of MgO embedded in α-Mg matrix. The Vickers hardness of the composite is obviously higher than that of matrix of AZ91 alloy. Moreover, the composite exhibits excellent compressive property. The ultimate compressive strength of the material is 290 MPa, the yield strength is 175 MPa, and the elongation is about 5%, which are higher than those of AZ91alloy.
Key words: Mg-based alloy; composite; Mg2Si; microstructure; mechanical property
1 Introduction
Magnesium (Mg) and its alloys have been proven to be promising light-mass materials mainly due to their potential physical properties such as low density, high damping capacity, excellent castability and superior mechanicability[1-3]. However, Mg alloys have been limited for application in large scale because of their low strength, stiffness and wear-resistance especially at elevated temperature[4]. So the reinforcement of Mg-based composites with various hard particles has been the focus of study[5-11]. Recently, Mg2Si particles are found to be beneficial for reinforcing Mg alloy because Mg2Si exhibits low density, high hardness and high melting point[12-14]. But owing to the high embrittlement of the Mg2Si particle, the toughness of Mg alloys may be destroyed by directly introducing Mg2Si particles. To overcome the limitations of conventional processes, new in-situ processing techniques have been developed, in which Mg2Si is synthesized in the Mg-based composite by chemical reactions between Mg and SiO2 or Si during the fabrication process. Moreover, the interfaces between Mg2Si particles and matrix were clean, and the interfacial contact strength was high[15-16]. But much of research use Si as the raw material, unfortunately, such raw material is too expensive to be accepted by the engineering community for general applications. Therefore, to prepare Mg-based composite by low-cost materials seems to be the most hopeful route when facing further commercial demand. In this paper, a new-type Mg-Mg2Si composite is prepared by using Mg-9Al-1Zn alloy and low-cost vermiculite as the raw materials through in-situ reaction method, and the structure and mechanical properties of the composite material are investigated. The purpose of this study is to develop a cheap raw material to produce Mg2Si particle reinforced Mg-based composite.
2 Experimental
Mg-9Al-1Zn (mass fraction, %) alloy and vermiculite were used as the starting materials, and the composition of the vermiculite is listed in Table 1. An Mg-9Al-1Zn alloy was melted in an electromagnetic induction furnace using steel crucibles under a flux of melting salt in a temperature range of 700-750 ℃, and the melt was put into a quartz tube filled with the vermiculite. Then the composite was obtained. The structure of the sample was examined by optical microscope (OM), environment scanning electron microscope (ESEM) (XL30 ESEM FTG) with an energy dispersive spectrometer (EDS) attached and X-ray diffractometer(XRD) (Rigaku D/max-ⅡB). The Vickers hardness of the composite was measured by the microhardness tester (FM-700). The compressive property test was carried out by material test machine (Instron-5869). The diameter of the sample was 10 mm and the length was 17 mm. The strain rate was 9.8× 10-4 s-1.
Table 1 Compositions of vermiculite(mass fraction, %)

3 Results and discussion 3.1 Structure
The optical micrograph of the composite is shown in Fig.1. It can be observed that a large amount of multiangular particles are formed and distributed in the matrix. The XRD result of the composite material with addition of 20% vermiculite is shown in Fig.2. It shows that besides α-Mg, MgO and Mg17Al12, Mg2Si phases are also detected in the composite, which may be conjectured that Mg2Si and MgO phases create from the reaction of vermiculite with Mg, and the reaction equation is shown as the follows:
4Mg + SiO2 → Mg2Si + 2MgO
The ESEM image of the composite is shown in Fig.3. In order to know the formation of the particle in the composite, a typical EDS spectrum of the gray particle is shown in Fig.4. It can be seen that the particle is mainly composed of Mg and Si elements, and the average molar ratio of Mg to Si element is approximately 2:1. Consequently, the particle is Mg2Si compound.
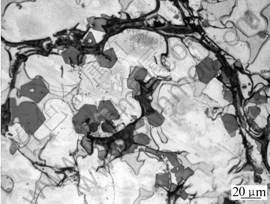
Fig.1 Optical micrograph of composite
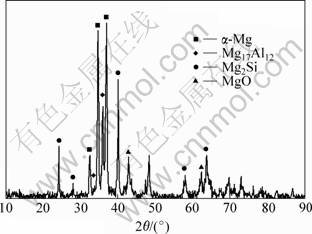
Fig.2 XRD spectrum of composite
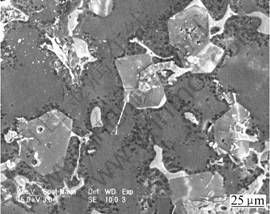
Fig.3 ESEM image of composite material
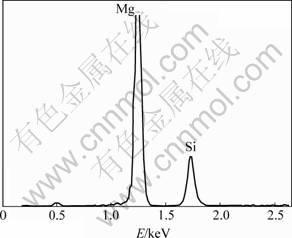
Fig.4 EDS spectrum of particle A in sample
3.2 Vickers hardness and compressive properties
The results of Vickers micro-hardness measurement are demonstrated and the results are given in Fig.5. The average hardness value of the matrix phase is HV 67 and that of the Mg2Si phase is HV 516. It has been obviously indicated that the hardness value of Mg2Si phase is higher than that of the matrix phase. Thus, the produced Mg2Si phase by in-situ reaction effectively enhances the hardness for the composite. The stress—stain curve for AZ91 and the composite is shown in Fig.6. The ultimate compressive strength (σf) of the alloy is 290 MPa, the yield strength (σy) is 175 MPa, and the elongation is about 5%, respectively. The compressive strength of the AZ91 alloy is approximately 238 MPa, the yield strength (σy) is 98 MPa, and the elongation is about 3%, respectively. The values of compressive strength of the investigated composite are slightly higher than those of the AZ91 alloy.
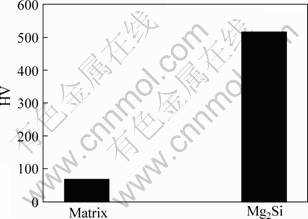
Fig.5 Microhardness of composite
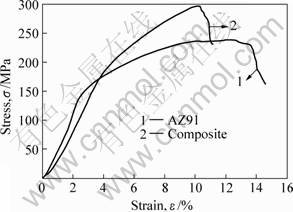
Fig.6 Compression curve for AZ91 and composite
The in-situ synthesis technique is attractive in present research, because the composites synthesized by in-situ method have advanced performance due to fine reinforcements and clear interface between metal matrix and reinforcement[17-18]. In the present work, many Mg2Si particulates are formed from the melt with the addition of vermiculite, and subsequent growth of the crystals around the grain boundaries (Fig.1). This phenomenon indicates that the growth rate of the primary α-Mg phase may be reduced when the Mg2Si particulates act as diffusion barriers to their growth. Therefore, a special structure of the AZ91-Mg2Si composites is achieved in the solidification process. The Mg2Si compound exhibits higher hardness compared with the matrix (Fig.5), and the particles distribute evenly, which leads to the higher compressive strength of the AZ91-Mg2Si composite compared with the AZ91 alloy. In a word, the high strength attributes to the addition of vermiculites in AZ91 matrix which form the precipitation of Mg2Si phase.
4 Conclusions
AZ91-Mg2Si composite material is synthesized successfully through the in-situ reaction by using vermiculite and AZ91. It is found that many multiangular Mg2Si particles are dispersed along the grain boundary. The hardness of the Mg-9Al-1Zn alloy is effectively improved by the Mg2Si particles, and the compressive strength is enhanced. The high strength attributes to the addition of vermiculites in AZ91 matrix, which form the precipitation of Mg2Si phase.
References
[1] MORDIKE B L, EBERT T. Magnesium (properties-application- potential)[J]. Mater Sci Eng A, 2001, 302: 37.
[2] KAMADO S, IWASAWA S, OHUCHI K, KOJMA Y, NINAMIYA R. Japan Inst Light Metal, 1992, 42: 727.
[3] BEE S, FROMMEYER G, SCHMID E, Mordike B L, Hehmann F. Magnesium Alloys and Their Application[C]. Germany, 1992. 317.
[4] MABUCHI M, KUBOTA K, HIGASHI K. Elevated temperature mechanical properties of magnesium alloys[J]. Mater Sci Tech, 1996, 12(1): 35-39.
[5] QI Qing-ju. Evaluation of sliding wear behavior of graphite particle-containing magnesium alloy composites[J]. Trans Nonferrous Met Soc China, 2006, 16(5): 1135-1140.
[6] WANG Yan, WANG Hui-yuan, XIU Kun, WANG Hong-ying, JIANG Qi-chuan. Fabrication of TiB2 particulate reinforced magnesium matrix composites by two-step processing method[J]. Mater Lett, 2006, 60(12): 1533-1537.
[7] LIM C Y H, LEO D K, ANG J J S,GUPTA M. Wear of magnesium composites reinforced with nano-sized alumina particulates[J]. Wear, 2005, 259(1/6): 620-625.
[8] XI Y L, CHAI D L, ZHANG W X, ZHOU J E. Ti-6Al-4V particle reinforced magnesium matrix composite by powder metallurgy[J]. Mater Lett, 2005, 59(14/15): 1831-1835.
[9] DONG Q, CHEN L Q, ZHAO M J, BI J. Synthesis of TiCp reinforced magnesium matrix composites by in situ reactive infiltration process[J].Mater Lett, 2004, 58(6): 620-926.
[10] XI Y L, CHAI D L, ZHANG W X, ZHOU J E. Titanium alloy reinforced magnesium matrix composite with improved mechanical properties[J]. Scripta Mater, 2006, 54: 19-23.
[11] CHUA B W, LU L, LAI M O. Influence of SiC particles on mechanical properties of Mg based composite[J]. Compos Struct, 1999, 47: 595-601.
[12] LU L, THONG K K, GUPTA M. Mg-based composite reinforced by Mg2Si[J]. Compos Sci Technol, 2003, 63: 627-632.
[13] MABUCHI M, HIGASHI K. Strengthening mechanisms of MgSi alloys[J]. Acta Mater, 1996, 44: 4611-4618.
[14] MABUCHI M, KUBOTA K, HIGASHI K. High strength and high strain rate superplasticity in a Mg-Mg2Si composite[J]. Scr Metall Mater, 1995, 33: 331-335.
[15] ZHANG J, FAN Z, WANG Y Q, ZHOU B L. Microstructural development of Al-15vol%Mg2Si in situ composite with mischmetal addition[J]. Mater Sci, 2000, A281: 104-112.
[16] MURTHY V S R, RAO B S. Microstructure development in the directed melt-oxidized (DIMOX) Al-Mg-Si alloys[J]. Mater Sci, 1995, 30: 3091-3097.
[17] Maity P C, Panigrahi S C. Metal and intermetallic matrix in-situ particle composites[J]. Key Eng Mater, 1995, 313: 104-107.
[18] Tjong S C, Ma Z Y. Microstructural and mechanical characteristics of in situ metal matrix composites[J]. Mater Sci Eng R, 2000, 29: 49-113.
(Edited by YANG Bing)
Foundation item: Project(KGCX2-SW-216) supported by the Science Program of Chinese Academy of Sciences; project(05GG54) supported by the Science and Technology Program of Changchun Province, China
Corresponding author: WU Yao-ming; Tel: +86-431-85262404; E-mail: ymwu@ciac.jl.cn