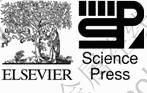
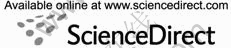
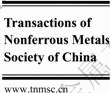
Trans. Nonferrous Met. Soc. China 22(2012) 1081-1085
Evaluation of ultra-fine grained tungsten under transient high heat flux by high-intensity pulsed ion beam
TAN Jun1, ZHOU Zhang-jian1, ZHU Xiao-peng2, GUO Shuang-quan3, QU Dan-dan1,
LEI Ming-kai2, GE Chang-chun1
1. School of Materials Science and Engineering, University of Science and Technology Beijing, Beijing 100083, China;
2. School of Materials Science and Engineering, Dalian University of Technology, Dalian 116024, China;
3. School of Materials Science and Engineering, Southwest Jiaotong University, Chengdu 610031, China
Received 19 April 2011; accepted 9 September 2011
Abstract: Pure tungsten, oxide dispersion strengthened tungsten and carbide dispersion strengthened tungsten were fabricated by high-energy ball milling and spark plasma sintering process. In order to evaluate the properties of the tungsten alloys under transient high heat flues, four tungsten samples with different grain sizes were tested by high-intensity pulsed ion beam with a heat flux as high as 160 MW/(m2·s-1/2). Compared with the commercial tungsten, the surface modification of the oxide dispersion strengthened tungsten by high-intensity pulsed ion beam is completely different. The oxide dispersion strengthened tungsten shows inferior thermal shock response due to the low melting point second phase of Ti and Y2O3, which results in the surface melting, boiling bubbles and cracking. While the carbide dispersion strengthened tungsten shows better thermal shock response than the commercial tungsten.
Key words: tungsten; tungsten alloy; ultra-fine grain; surface effects; thermal shock; transient high heat flux
1 Introduction
Tungsten (W) is one of the most promising plasma facing materials (PFMs) which are exposed to a strong irradiation and high heat flux in the fusion reactor due to its high melting point, low thermal expansion coefficient and low sputtering yield, etc [1-4]. According to the baseline design of international thermo nuclear experimental reactor (ITER), the final step for the plasma facing component (PFC) is presented with the concept of a full tungsten divertor before the start of deuterium- tritium (DT) operation [4,5]. Therefore, it is important to evaluate the performance of tungsten under condition of the high heat loading in the next-step fusion devices.
The ion and electron beam approaches, capable of delivering much higher specific energy density into testing materials as compared to other methods, are preferred for simulating transient high heat fluxes [6,7]. For this purpose, a heat flux parameter in unit of MW/(m2·s-1/2), i.e., a product of power density and square root of pulse duration for the different heat flux testing sources, provides a reference to assess material performance under various transient heat flux with estimated heat fluxes typically from tens to a few hundreds MW/(m2·s-1/2) during normal operation and off-normal events [8,9]. However, cares should be taken to explain the previous results of high heat flux testing based on electron/ion beams since it has been pointed out that electron beam may have a large amount of energy reflection during high heat flux testing of high atomic number Z materials [6] and ion beam testing has a fluctuation of power density output of about 50% [6,10].
It was reported that the ultra-fine grained (UFG) W and particle dispersion strengthened W alloys have improved mechanical properties and lower ductility to brittle transition temperature (DBTT) compared with the usual commercial W [11-13]. However, the data of the ultra-fine grained tungsten and the dispersion strengthened tungsten alloys under the transient heat flux are limited. In this study, high heat flux testing based on ion beam approach with relatively stable parameters was performed for evaluating a series of new grade tungsten. The melting behaviour and crack formation of the various tungsten grades during the high heat flux were analyzed.
2 Experimental
Powders of pure tungsten (average particle size of 2.0 μm, purity of 99.9%), Y2O3 (average particle size of 30 nm, purity of 99.99%), Ti (average particle size of 74 μm, purity of 99.9%) and ZrC (average particle size of 50 nm, purity of 99.99%) were mixed to provide the nominal compositions of W, W-0.5%Y2O3-1%Ti and W-0.5%ZrC (in mass fraction) in a glove box respectively. Then each of the blends was charged into WC vessel with WC balls for high-energy ball milling. The high-energy ball milling process was conducted in a high purity (99.9999%) Ar atmosphere with a rotational speed of 380 r/min and milled for 30 h. Then the as-received powders were sintered immediately by spark plasma sintering (SPS) at 1700 °C for 1 min under a pressure of 50 MPa in vacuum.
For evaluating the performance of W alloys under the high heat flux, four kinds of W samples, sintered pure W (SW), oxide dispersion strengthened (ODS) W (W-0.5%Y2O3-1%Ti), carbide dispersion strengthened (CDS) W (W-0.5%ZrC) and commercial rolled W with different grain sizes were exposed to the high thermal load simulated by high intensity pulsed ion beam (HIPIB). All of the tungsten samples were cut by EDM cutting and polished with diamond pastes to dimensions of 8 mm in a diameter and 2 mm in thickness.
The high heat flux tests were performed on a TEMP-6 high-intensity pulsed ion beam (HIPIB) apparatus which can produce HIPIB with an accelerating voltage of 300 kV, the ion current density up to 500 A/cm2 of 75 ns beam pulse duration and the composition of 70% proton and 30% carbon ions by using a modified magnetically insulated ion diode [14]. It was noted that the fluctuation of HIPIB output can be controlled to be less than 20%, where more consistent results ensure a more reliable evaluation of material performance under the relatively stable repetitive heat flux. In this study, a moderate HIPIB intensity at ion current density of 200 A/cm2 was generated for the high heat flux testing, i.e., about 160 MW/(m2·s-1/2), at the order of the high heat flux of most transient events anticipated for ITER operation [3]. It should be mentioned that HIPIB irradiation at the current density and pulse duration usually delivers a dose of 1013-1014 ion/(cm2·shot), where the element doping effect may be neglected at tens ppm order and then the testing was regarded as a “pure” heating processing. Moreover, the heat flux in this study was also regarded as a surface heat flux for the tungsten samples of 2-3 mm in thickness with a calculated heat affected depth of several micrometers, similar to the case of electron beam heat flux testing on tungsten coated CFC blocks with a electron penetration of a few micrometers in the coatings of 200 μm at an acceleration voltage of 120 kV [15].
3 Results and discussion
3.1 Commercial W
Figure 1 shows the surface morphologies of the commercial W after irradiation by HIPIB. Obvious long cracks with a width of ~0.15 μm occur after single shot at the heat flux of 160 MW/(m2·s-1/2),as shown in Fig. 1(a). As the number of shots increased from 1 to 15, the crack density increased. It is also seen that the crack width increased to about 0.35 μm when the number of shots was up to 15. Otherwise, the high heat flux by TEMP-6 apparatus is up to 160 MW/(m2·s-1/2), which exceeds the melting threshold of W (-50 MW/(m2·s-1/2)), but for the very short pulse duration (75 ns) of HIPIB, the total heat flux is rather low. Therefore, no obvious melting occurred in the commercial W under high heat flux for single and multiple shots.

Fig. 1 SEM images of commercial W surfaces: (a) Irradiated with single shot; (b) Irradiated with 5 shots; (c) Irradiated with 15 shots
3.2 Sintered W, ODS W and CDS W
The sintered W (SW) with equiaxed fine grain (7 μm) and relative density of 96.4% was fabricated by high-energy ball milling and SPS. Figure 2 shows the SEM images of SW samples exposed to the heat flux of 160 MW/(m2·s-1/2). It is obvious that a lot of fine cracks with network structure formed and a few of boiling bubbles with diameter of 8-10 μm occurred on the W surface after irradiating with single shot, which is quite different from that of commercial W. As the number of shots increased to 10, the network of cracks was dense and the crack width increased from 0.2 μm to 0.3 μm. Otherwise, it is interesting that the bubbles disappeared and the loaded surface became smooth and uniform after irradiating with 10 shots. The boiling bubbles may be mainly generated by impurities induced by the fabrication process after irradiating with single shot. But for the surface cleaning effects of the HIPIB technology, the impurities will be boiled, sublimated and vanish after irradiating with several shots, as shown in Fig. 2(b).
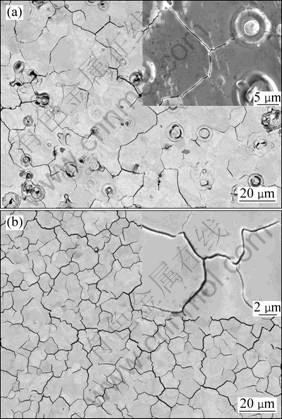
Fig. 2 SEM images of SW surfaces: (a) Irradiated with single shot; (b) Irradiated with 10 shots
Figure 3 shows the surface morphology of oxides dispersion strengthened W with ultra fine grain size (about 0.25 μm) after high heat flux test. It is easily found that the behaviors of bubbles are obviously different from the SW under the same test conditions. Compared with pure W, as Y2O3 and Ti were doped in the W, the melting temperature of W will be decreased, which will influence the anti-irradiation properties of W. Thus, the obvious melting and ablating occurred on the surfaces of ODS W with a feature of existence of craters after irradiating with only single shot, as shown in Fig. 3(b). When the number of shots increased to 10, a smooth and flat surface was found, which may be due to the repeated melting, solidification and filling the caves on the ODS W surface after irradiating with multiple shots. Moreover, the several rapid melting and rapid solidification caused by irradiation brought into the stress, which led to crack in the ODS W sample, as shown in Fig. 3(c).
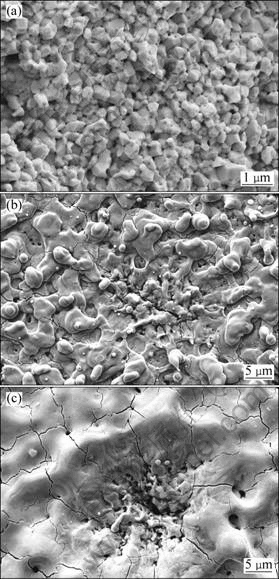
Fig. 3 SEM images of ODS W surfaces: (a) Fracture surface; (b) Irradiated with single shot; (c) Irradiated with 10 shots
The microscopy observation of carbide dispersion strengthened W with ultra fine grain size (about 0.5 μm) presents the cracking and boiling bubbles on the surface exposed to the high heat flux (Fig. 4). The dispersion particle is ZrC with a high melting point. With single shot, only few microcracks with a width of 0.2 μm were found. When the number of shots increased to 10, a network of fine cracks with a width of 0.25 μm formed, which is less than that of the commercial W and the sintered W. This demonstrates that the CDS W sample has a very good thermal shock resistance. Moreover, there is no obvious melting on the surface after irradiating with single shot or multiple shots. But some bubbles can also be found on the loading surface with single shot, which should be due to the impurity introduced by the fabrication process. Figure 5 shows the elemental map distribution measured by EDS before and after high heat loading. For the original sample, it is obvious that the ZrC phases distribute in the W matrix homogenously, but obvious oxygen is also found which may be introduced during MA and sintering process. The element of oxygen is always accompanied with elemental Zr. Combined with the result of XRD, it is believed that the impurity phase is ZrO2. Obviously, the impurity of oxide will decrease the melting point of the CDS W. With single shot, this oxide phase will melt and form the bubbles. From Fig. 5(b) we can see that obvious segregation occurred for Zr and O with single shot due to the melting of ZrO2.
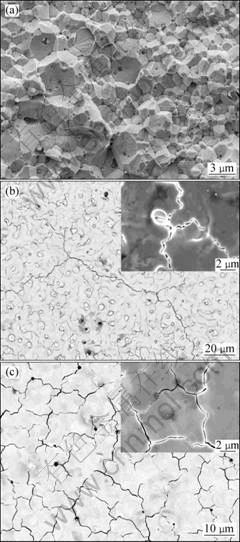
Fig. 4 SEM images of CDS W surfaces: (a) Fracture surface; (b) Irradiated with single shot; (c) Irradiated with 15 shots
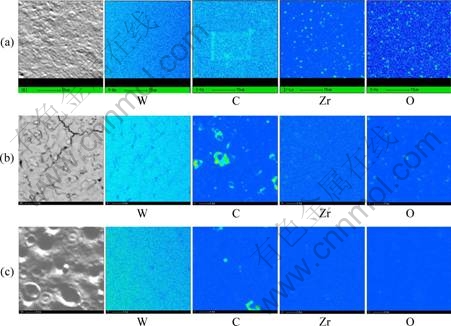
Fig. 5 Elemental map distribution of CDS W surface before and after exposure to heat flux of 160 MW/(m2·s-1/2): (a) Original; (b) Irradiated with single shot; (c) Irradiated with 15 shots
4 Conclusions
1) The effects of ion beam irradiation on the surface damage of different grades of UFG W, and commercial W were studied under high thermal flux simulated by high-intensity pulsed ion beam with a heat flux as high as 160 MW/(m2·s-1/2).
2) Initial results indicated that the performance of W after high heat flux test was mainly related to the microstructure and the second phase. Compared with the commercial W, the ODS W sample showed inferior thermal shock response, due to the low melting point second phase of Ti and Y2O3, which results in the surface melting, boiling bubbles and cracking. While the CDS W sample showed better thermal shock response than commercial W.
References
[1] SMID I, AKIBA M, VIEIDER G, PLOCHL L. Development of tungsten armor and bonding to copper for plasma-interactive components [J]. Journal of Nuclear Materials, 1998, 258-263: 160-172.
[2] SHIMOMURA Y. The present status and future prospects of the ITER project [J]. Journal of Nuclear Materials, 2004, 329-333: 5-11
[3] BOLT H, BARABASH V, FEDERICI G, LINKE J, LOARTE A, ROTH J SATO K . Plasma facing and high heat flux materials—Needs for ITER and beyond [J]. Journal of Nuclear Materials, 2002, 307-311: 43-52.
[4] NEU R, BOBKOV V, DUX R, KALLENBACH A, PUTTERICH T, GREUNER H, GRUBER O, HERRMANN A, HOPF C H, KRIEGER K, MAGGI C F, MAIER H, MAYER M, ROHDE V, SCHMID K, SUTTROP W, ASDEX W T. Final step to an all tungsten divertor tokamak [J]. Journal of Nuclear Materials, 2007, 363-365: 52-59.
[5] BALDWIN M J, DOERNER R P, NISHIJIMA D, TOKUNAGA K, UEDA Y. The effects of high fluence mixed-species (deuterium, helium, beryllium) plasma interactions with tungsten [J]. Journal of Nuclear Materials, 2009, 390-391: 886-890.
[6] LINKE J, ESCOURBIAC F, MAZUL I V, NYGREN R, RODIG M, SCHLOSSER J, SUZUKI S. High heat flux testing of plasma facing materials and components—Status and perspectives for ITER related activities [J]. Journal of Nuclear Materials, 2007, 367-370: 1422-1431.
[7] LINKE J. High heat flux performance of plasma facing materials and components under service conditions in future fusion reactors [J]. Transactions of Fusion Science and Technology, 2008, 53: 278-287.
[8] PINTSUK G, KUHNLEIN W, LINKE J, RODIG M. Investigation of tungsten and beryllium behaviour under short transient events [J]. Fusion Engineering and Design, 2007, 82: 1720-1729.
[9] PESTCHANYI S E, LINKE J. Simulation of cracks in tungsten under ITER specific transient heat loads [J]. Fusion Engineering and Design, 2007, 82: 1657-1663.
[10] RAFFRAY A R, BLANCHARD J, LATKOWSKI J, NAJMABADI F, RENK T, SETHIAN J, SHARAFAT S, SNEAD L. The HAPL team progress towards realization of a laser IFE solid wall chamber [J]. Fusion Engineering and Design, 2006, 81: 1627-1638.
[11] ZHOU Zhang-jian, LINKE J, PINTSUK G, DU Juan, SONG Shu-xiang, GE Chang-chun. High heat load properties of ultra fine grained tungsten [J].Journal of Nuclear Materials, 2009, 386-388: 733-735.
[12] ZHOU Zhang-jian, MA Yao, DU Juan, LINKE J. Fabrication and characterization of ultra-fine grained tungsten by resistance sintering under ultra-high pressure [J]. Materials Science and Engineering A, 2009, 505: 131-135.
[13] KURISHITA H, AMANO Y, KOBAYASHI S, NAKAI K, ARAKAWA H,HIRAOKA Y, TAKIDA T TAKEBE K, MATSUI H. Development of ultra-?ne grained W-TiC and their mechanical properties for fusion applications [J]. Journal of Nuclear Materials, 2007, 367-370: 1453-1457.
[14] ZHU Xiao-peng, DONG Zhi-hong, LEI Ming-kai, MA Teng-cai. Characterization of a high-intensity unipolar-mode pulsed ion source with improved magnetically insulated diode [J]. Review of Scientific Instruments, 2003, 74: 47-52.
[15] HIRAI T, BEKRIS N, COAD J P, GRISOLIA C, LINKE J, MAIER H, MATTHEWS G F, PHILIPPS V, WESSEL E. Failure modes of vacuum plasma spray tungsten coating created on carbon fibre composites under thermal loads [J].Journal of Nuclear Materials, 2009, 392: 40-44.
强流脉冲离子束作用下超细晶钨的抗瞬态热负荷性能评价
谈 军1,周张健1,朱小鹏2,郭双全3,屈丹丹1,雷明凯2,葛昌纯1
1. 北京科技大学 材料科学与工程学院,北京 100083;
2. 大连理工大学 材料科学与工程学院,大连 116024;
3. 西南交通大学 材料科学与工程学院,成都 610031
摘 要:采用高能球磨和放电等离子体烧结技术制备纯钨、氧化物弥散强化钨和碳化物弥散强化钨。为了评价钨在瞬态热冲击下的性能,采用强流脉冲离子束,在热流密度高达160 MW/(m2·s-1/2)的条件下对4种不同晶粒尺寸的钨进行抗热冲击试验。与商品钨相比,弥散强化钨在瞬态高热流作用下显现出不同的行为。氧化物弥散强化钨显现出较差的抗热冲击性能,这主要是由于低熔点的第二相Ti和Y2O3的引入,从而使得钨的表面发生熔融、起泡和开裂。而碳化物弥散强化钨合金则显现出较好的抗热冲击性能。
关键词:钨;钨合金;超细晶;表面作用;热冲击;瞬态高热流
(Edited by YANG Hua)
Foundation item: Project (50634060) supported by the National Natural Science Foundation of China; Project (2010GB109000) supported by the National Basic Research Program of China
Corresponding author: ZHOU Zhang-jian; Tel: +86-10-62334951; Fax: +86-10-62334951; E-mail: zhouzhj@mater.ustb.edu.cn
DOI: 10.1016/S1003-6326(11)61286-7