
Preparation and oxygen-sensing properties of TiO2 porous thin films on alumina substrate
LI Ming-li(李明利),XU Ming-xia(徐明霞), LI Yan(李 岩)
School of Materials Science and Engineering, Key Laboratory for Advanced Ceramics and Machining Technology of Ministry of Education, Tianjin University, Tianjin 300072, China
Received 10 April 2006; accepted 25 April 2006
Abstract: The titanium dioxide sols were synthesized with tetrabutyl titanate as precursor, diethanolamine(DEA) as complexing agent , polyethylene glycol (PEG) as organic template. The porous films were prepared by sol-gel method. The structures and morphology of the titanium dioxide porous films were characterized by FE-SEM. The formation mechanism of TiO2 porous films and the relation between the porous structure and oxygen-sensing properties of TiO2 films were studied. Ordered structure was formed by assembling between TiO2 colloid particles and the template molecules. PEG molecules acted on TiO2 colloid particles by hydrogen bond and bridge oxygen. The porous structure was formed after the organic template was decomposed when calcining the films. The diameter, amount and distribution of the pores in the films are related with the content of PEG.. The pore diameter increases with increasing of content of PEG and the pore density reaches the maximum at certain content. Oxygen-sensitivity and response speed of porous TiO2 films are improved compared with films without pores. Both the sensitivity and response speed increase with the increasing of pore diameter and pore density. Oxygen-sensitivity reaches 3 order of magnitude at 800 ℃. Its response time from H2/N2 to O2/N2 atmosphere and vice versa is about 0.11 s and 0.12 s respectively. Although the sensitivity and response speed increase, the resistance-temperature properties of porous films are not notably improved with the increasing of the content of PEG.
Key words: TiO2 porous thin film; organic template; sol-gel method; oxygen-sensitivity
1 Introduction
Titania has become one of the most interesting materials and it has attracted considerable attention in recent years, due to its unique electro-optic properties and its potential applications for photocatalyst[1], photoelectrode[2], gas sensor[3], etc. For many applications, titania with macropores and large surface area are suitable. Increasing the surface area of the film is a promising way to improve the desired functions because almost all of these applications utilize the chemical reactions on the surface. Several methods have been proposed for the preparation of titanium dioxide thin films, e.g. sol-gel[4], spray pyrolysis [5], chemical vapor deposition[6]. Among these preparation techniques, the widely used sol-gel method is relatively simple and can be used to prepare porous titania. Presently researches are focused on the applications of porous TiO2 films to photocatalyst and solar battery and few literatures can be found about its applications to gas sensor, so it is quite valuable to work on its oxygen-sensing application. As the development of automobile industry, the environmental pollution has become more and more serious. In order to reduce harmful emissions and improve fuel economy, stoichiometric air/fuel ratio oxygen sensors are widely used as a feedback element[7]. In this study the porous TiO2 films were prepared by sol-gel method. The formation mechanism of the porous films and the relation between the porous structure and oxygen-sensing properties of TiO2 films are studied.
2 Experimental
2.1 Preparation of TiO2 porous thin film
Precursor solutions for porous TiO2 thin films were prepared by the sol-gel method [4] using tetrabutylorthotitanate, ethanol, hydrochloric acid and diethanola-mine(DEA). Tetrabutylorthotitanate (15.0 mL) and diethanolamine (4.0 mL) were dissolved in ethanol(60.0 mL). After stirring vigorously for 30 min at room temperature, hydrochloric acid (0.8 mL, 0.05 mol/L) and ethanol (10 mL) were mixed together and slowly added to the solution. The molar ratio of water to alkoxide was 1. Keep stirring vigorously for 2 h and then various amounts of polyethyleneglycol (PEG) (HO(CH2CH2O)nH) (molecular mass 2000) were added to the above solution and served as a coating solution. The solutions containing various amounts of PEG were transparent and light yellow. Alumina ceramic plates (50 mm×10 mm×1.5 mm) were used as the support substr-ates. They were carefully cleaned by using ultrasonic treatment with base, acetone solution and alcohol, then dried in an oven at 8 ℃. The porous TiO2 films were prepared by a dip-coating method. The withdrawal speed was 3-5 cm/min. Gel coating films were dried at 80 ℃ for 10 min and then heat-treated at a rate of 20-25 ℃/min to 800 ℃ and kept at that temperature for 10 min in air. PEG contained in the gel thin films decomposed completely at 500 ℃. The thickness of the TiO2 thin films was adjusted by repeating the cycles from withdrawing to heat treatment.
2.2 Characterization
The morphology of the resultant porous TiO2 film surfaces was characterized by scanning electron microscopy(SEM) (XL30ESEM, phlilps, Holand). Oxygen-sensitivity tests were conducted under flowing gas conditions. The gas mixing system consisted of hydrogen, oxygen and nitrogen could provide oxidation(O2/N2, to imitate lean-burn state) and reduction(H2/N2, to imitate rich-burn state) atmospheres with two kinds of gas states. The flowing gas was switched between H2/N2 and O2/N2 atmospheres. The flow rate of the test gas mixture was 1 000 cm3/min. The electric circuit for measuring conductivity changes is shown in Fig.1. A fixed resistance Ro [41.9 kW] was connected in series with the porous film, and the electric current flowing through the film was measured with a personal computer as the potential drop across Ro. A direct current voltage generator (5 V) was used as a source of direct current. The electrodes were deposited on the Al2O3 substrate through the paste technique by which Pt paste was calcined at 1 100 ℃ for 30 min.
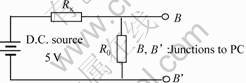
Fig.1 Electric circuit diagram for testing gas-sensing properties
3 Results and discussion
3.1 Mechanism of morphology formation
Polyethylene glycol (PEG, H—(OCH2CH2)n—OH ) consisting of hydrophilic bridge oxygen groups(—O—)and rather hydrophobic chain(—CH2CH2—), shows hackle structure in anhydrous state. When PEG is dissolved into water or ethanol solution, bridge oxygen groups are pulled out by hydrogen bond to act with TiO2 colloid particles. The long chains of PEG restrain the growing of TiO2 colloid particles by enwrapping the surface of the particles. Then a mass of PEG-TiO2 clusters are obtained and ordered PEG-TiO2 loop structure is formed by assembling the clusters finally. The mechanism of porous morphology formation in the TiO2 films can be well interpreted as that the organic template is decomposed and volatilized during the subsequent calcining process and therefore forms porous structure[8, 9].
3.2 Effects of content of PEG on porous structure formation
The content of PEG plays an important part on the porous structure of the TiO2 films. Fig.2 shows the SEM photographs of TiO2 porous thin films obtained from titanium dioxide sols with different addition of PEG(2000). The porous structure isn’t formed when the PEG content is as little as 0.05g just as Fig.2(a) shows. The pores don’t appear until the amount of PEG reaches 0.15 g and numerous get-through pores are observed only when the amount of PEG reaches 0.25 g. The distribution of the pores is not so homogenous, for the alumina substrate is not severely flat. It can be explained as below. When the PEG content is as little as 0.05 g, stable three-dimensional network structure between TiO2 colloid particles and the template molecules doesn’t formed. A few pores left by the volatilization of PEG during calcining process are enveloped because the crystal grains are growing up at the same time. As the addition amount of PEG increases to 0.15 g, the stable three-dimensional network structure is only partially formed, thus get-through pores are merely located on the flat area of the alumina substrate. The shape of the pores is not so regular and the aperture ranges from 400 nm to 600 nm. A whole piece of stable three-dimension network is formed as PEG increases to 0.25 g. The stable network brings uniformity of stress from different directions and consequently restrains the collapse and distortion of the framework during calcining process. Thereby the regular round-shape pores with the diameter ranging from 1 000 nm to 1 500 nm are obtained just like Fig.2(c) shows. Comparing Fig.2(d) with Fig.2(b) one can observe that the pore density is decreased relatively.
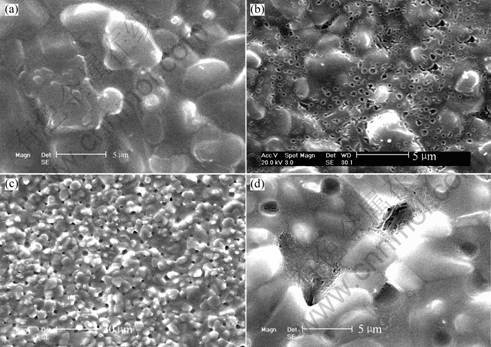
Fig.2 SEM photographs of porous TiO2 films with different contents of PEG: (a) 0.05 g; (b) 0.15 g; (c) 0.25 g; (d) 0.25 g
3.3 Oxygen-sensing properties of porous thin film
The mechanism of oxygen-sensing properties of TiO2, working as n-type semiconductor, is discussed as below. Electrons will be deprived by the O2 absorbed on the surface as Eqn.(1) shows when TiO2 exposes in the high partial pressure of O2 atmosphere. The resistance of this n-type semiconductor increases therefore. When partial pressure of reductive gases like H2 increases,Eqn. (2) takes place and the resistance of TiO2 decreases sharply for the electrons are released.
1/2O2(g)+ne?On-(ads) (1)
On-(ads)+H2 → H2O+ne (2)
The two processes with good reproducibility undergoing circulates in the oxidizing–reducing atmosphere posts that the TiO2 film has good oxygen-sensing properties. Resistance characteristic curves of the TiO2 films at 800 ℃ with different contents of PEG as organic template during preparation are shown in Fig.3. That the jump in the curves at the critical point is bigger than 2 orders of magnitude shows the TiO2 film has good oxygen sensitivity when measured in H2/N2 and O2/N2 atmosphere. We define the oxygen-sensitivity as the ratio of the resistance in O2/N2 atmosphere to that in H2/N2 atmosphere. The oxygen-sensitivity of porous film (the one with 0.25 g PEG during preparation) reaches 3 order of magnitude and it is improved comparing with TiO2 films without pores[9]. One can observe that there is a decrease of the film resistance as the amount of PEG increases at H2 atmosphere. As we all know that the more the pores, the larger the surface area. The mechanism of the resistance of the thin film changing with ambient is closely related to the surface chemical reactivity. Since the porous thin film behaves as a n-type semiconductor, the film resistance decreases with the increasing of PEG according to Eqn. (2). The film resistance is not so evidently affected by the amount and density of the pores under O2 atmosphere for that the influence can be ignored when compared with the large original resistance in O2 condition.
Fig.4 shows the response time of the porous thin films at 800 ℃ with different contents of PEG. We define the response time as the time for the output
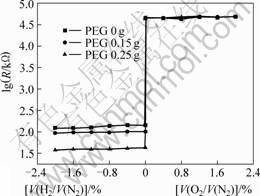
Fig.3 Oxygen-sensitivity curve of porous TiO2 films at 800 ℃ with different contents of PEG
voltage changes from 33% to 66% or from 33% to 66%. In this measurement, the higher is the output voltage across the fixed resistance Ro, the smaller is the resistance of the film. From the result, it can be seen that the porous thin films have good response and the response time from O2 to H2 and vice versa is shorter than 0.5 s. Especially, the response time of the film with 2.5 g PEG even reaches 0.11s and 0.12 s from H2/N2 to O2/N2 atmosphere and vice versa which is excellent.
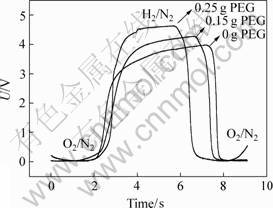
Fig.4 Response curve of porous TiO2 films at 800 ℃ with different contents of PEG
The resistance–temperature stability of the porous films in N2 is not very good compared with the thin films without pores obtained by ZHENG et al[10]. The porous film’s resistance–temperature coefficient Δα= (Rmax-Rmin)/ (RminΔT) =7.58×10-3/℃ (Fig.5).
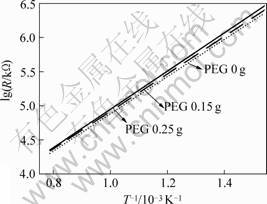
Fig.5 Resistance-temperature curve of porous TiO2 films with different contents of PEG
4 Conclusions
1) PEG molecules act on TiO2 colloid particles by hydrogen bond and bridge oxygen. Ordered structure is formed by assembling between TiO2 colloid particles and the template molecules. The porous structure is formed after the organic template is decomposed when calcining the films.
2) The diameter, amount and distribution of the pores on the surface of films are related with the content of PEG. The pore diameter increases with increasing the content of PEG and the pore density reaches maximum at certain content.
3) Sensitivity and response speed of porous TiO2 films are improved compared with films without pores. Both the sensitivity and response speed increase with increasing the pore diameter and pore density.
4)Although the sensitivity and response speed increase, the resistance-temperature properties of porous films are not notably improved with increasing the content of PEG.
References
[1] SAKKAS V A, ARABATZIS I M, KONSTANTINOU I K, DIMOU A D, ALBANIS T A, FALARAS P. Metolachlor photocatalytic degradation using TiO2 photocatalysts [J]. Applied Catalysis B: Environmental, 2004, 49(3): 195-205.
[2] Regan B O, Gratzel M. A low-cost, high-efficiency solar cell based on dye-sensitized colloidal TiO2 films [J]. Nature, 1991, 353(6346): 737-739.
[3] DUTT A, PRABIR K, DE L, MARLA F. Correlation of catalytic activity and sensor response in TiO2 high temperature [J]. Sens Actuators B Chem, 2006, 115(1): 1-3.
[4] YU J G, ZHAO X J, DU J C, CHEN W M. Preparation, microstructure and photocatalytic activity of the porous TiO2 anatase coating by Sol-Gel processing [J]. J Sol-Gel Sci Tech, 2000, 17(2): 163-171.
[5] YANG G J, LI C J, HAN F, OHMORI A. Microstructure and photocatalytic performance of high velocity oxy-fuel sprayed TiO2 coatings [J]. Thin Solid Films, 2004, 466(1-2): 81-85.
[6] KRUMDIECK S, RAJ R. Growth rate and morphology for ceramic films by pulsed-MOCVD [J]. Surface and Coatings Technology, 2001, 141(1): 7-14.
[7] YANNOPOULOS L N. A P-type semiconductor thick film gas sensor [J]. Sens Actuators B Chem, 1987, 12(3): 263-273.
[8] LI Y, XU M X, LU Y. Study on preparation of porous titania thin films and the factors influencing the structure [J]. Materials Review, 2005, 19(Ⅳ): 341-343.(in Chinese)
[9] LI Y, XU M X, XU Y J. Research and development of TiO2 oxygen-sensing thin films [J]. Journal of Transducer Technology, 2004, 23 (11): 12-14.(in Chinese)
[10] ZHENG L Y, XU M X, XU T X. TiO2-x thin films as oxygen sensor [J]. Sens Actuators B Chem, 2000, 66(1-3): 28-30.
(Edited by CHEN Ai-hua)
Corresponding author: XU Ming-xia; Tel:+86-22-27890489; fax:+86-22-27404724; E-mail: xumingxia@tju.edu.cn, samlml@eyou.com