
Damage analysis for particle reinforced metal matrix composite by ultrasonic method
YANG Zhi-guo(杨治国), LONG Shi-guo(龙士国)
Key Laboratory for Advanced Materials and Rheological Properties of Ministry of Education,
Faculty of Material Photoelectron Physics, Xiangtan University, Xiangtan 411105, China
Received 10 April 2006; accepted 25 April 2006
Abstract: The damage characteristic of particle reinforced metal matrix composite (PMMC) was studied by ultrasonic non-destructive evaluation method. After the sample was damaged induced by tensile load, the ultrasonic wave that propagated in the sample were collected. The damage parameter was defined by ultrasonic parameter and the wave signals were analyzed by correlation method. The results show that with the increase of tensile load, the damage parameter increases and the correlation coefficient decreases. The fracture section morphologies of PMMC under tensile load were observed by SEM. It is found that there are many concaves in the metal matrix. Therefore the damage evolution can be concluded. The initial damage is induced by void nucleation, growth and subsequent coalescence in the matrix or interface separation.
Key words: particle reinforced metal matrix composite; damage analysis; ultrasonic method; non-destructive testing
1 Introduction
Particle reinforced metal matrix composite (PMMC) can be fabricated by standard techniques, considerably reducing the manufacturing cost and providing a good balance between price and mechanical properties. They are excellent candidates for structural components in the aerospace and automotive industries due to their high specific modulus, strength, and thermal stability [1-9]. With the development of this material, the non-destructive evaluation method for the component of the PMMC becomes more and more urgent. Usually the traditional non-destructive evaluation method for metal material can not be available for this new composite [10]. The ultrasonic characterization of materials offers many advantages compared to the slow, expensive, and destructive metallographic methods. Ultrasonic signal is always composed of a series of transient feedback impulsive waves, which are created during the propagation of ultrasonic energy when it meets the discontinuities within the material, such as inclusions, voids, micro-cracks. It is typically used to determine the elastic constants of materials but rarely to measure damage of materials [11, 12]. Non-destructive evaluation with ultrasonic method is significant in the life prediction and failure mechanism for the materials system with interface between particle and matrix or thin film and substrate [13, 14].
In this paper, the damage characteristic of PMMC was studied by ultrasonic non-destructive evaluation method. After the sample was damaged induced by tensile load, the ultrasonic wave that propagated in the sample were collected and analyzed.
2 Experimental
2.1 Materials
SiC particle/6061 aluminum alloy composite was chosen as a model PMMC sample for this study. The composite with 15% SiC (volume fraction) was fabricated by melt casting route, and as-cast ingots of the composite were subsequently extruded. The SEM image of this material shows that SiC particles are distributed uniformly through the aluminum alloy matrix. This uniformity of microstructure is believed to be responsible for the isotropic nature of mechanical properties. The average size of the reinforced particle was 10 μm. The typical microstructure of experimental material is shown in Fig.1.
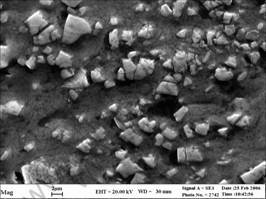
Fig.1 Typical microstructure of experimental material
2.2 Experiment processing
Fig.2 shows the schematic of the specimen configuration and load mode. In order to study the damage evolution of the specimen under tensile load, when tensile load were up to the designed value, the tension was paused. Then the longitudinal velocity of ultrasonic transmitted in the specimen was measured by ultrasonic equipment to determine the damage of the specimen. After that, the specimen was again tensioned. The longitudinal velocity of ultrasonic transmitted in the specimen was measured again. In this case, the damage evolution of the specimen due to the tensile load could be determined.

Fig.2 Schematic diagram of specimen configuration and load mode
The schematic of measurement apparatus is shown in Fig.3. The emitting and receiving piezoelectric sensors with the center frequency of 400 kHz were coupled to the specimen with a couplet. The ultrasonic instrument was controlled by the software in the computer. When the command beginning to measure was sent out through software, the ultrasonic instrument gave out a signal to the emitting sensor. Then ultrasonic wave was induced by the emitting sensor and transmitted to the specimen through couplet. When the ultrasonic wave traveled in the specimen, it could catch the information of the specimen’s characterization. The receiving sensor could detect the ultrasonic wave as soon as it arrived. The ultrasonic instrument sent the received ultrasonic wave to the computer and the software could show the wave on the screen and analyze the character of the wave, such as the traveling time and the frequency of the wave.
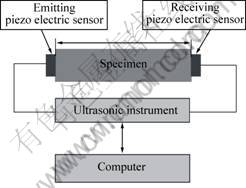
Fig.3 Schematic diagram of ultrasonic measurement apparatus
In order to quantitatively determine the damage levels, the damage parameter ω is defined as [10]
(1)
where vL is the longitudinal velocity of ultrasonic wave traveled in the initial sample and
is the longitudinal velocity of ultrasonic wave traveled in the damage sample. Two series experiment were conducted. One was the determination of ultrasonic velocity in original specimen, which was not damaged by any loading. The other was the determination of ultrasonic velocity in damaged specimen, which was damaged by the tensile load. The velocity of longitudinal wave vL can be calculated as
(2)
where L and t are the distance and time of the longitudinal wave traveled, respectively.
In the determination of ultrasonic velocity both in non-damaged specimen and damaged specimen, the dimension of all the specimens was 49 mm×6 mm×1.5 mm. This meant that the distances of the ultrasonic wave traveled in all specimens were the same, i.e. 49 mm. Therefore Eqn.(1) can be written as
(3)
where t and
are the time of the longitudinal wave traveled in the non-damaged specimen and damaged specimen, respectively. So long as traveling time of ultrasonic wave in the damage and non-damage specimen was measured, the damage parameter ω can be calculated through the above equation.
3 Results and discussion
Fig.4 shows the typical ultrasonic waves traveled in the initial specimen and the specimens induced by 200 MPa tensile load. The figure shows that the time of longitudinal wave traveled in the initial specimen is 8.05 μs. The time of longitudinal wave traveled in the damage specimens acted by 200 MPa tensile load is 8.10 μs. Comparison the ultrasonic waves traveled in the non-damage specimen and damage specimen, it is found that the amplitude of the longitudinal wave in non-damage specimen is higher than that in the damaged specimen. This means that the attenuation coefficient of the longitudinal wave traveled in the non-damaged specimen is less than that in the damaged specimen. With the increase of tensile load, the time of longitudinal wave increases. Therefore, the ultrasonic wave traveled in the specimen can reflect the specimen properties change.
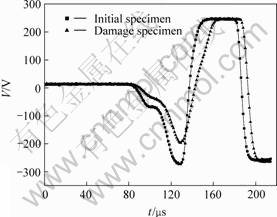
Fig.4 Typical ultrasonic waves traveled in initial specimen and specimens induced under 200 MPa tensile load
For all the specimens that were damaged by the tension loads of 100, 150, 200, 250, 300 and 350 MPa, the time of the longitudinal waves traveled in the damage specimens were measured. The results are listed in Table 1.
According to Eqn.(3), the damage parameter ω can be determined for all the damage specimens that induced
Table 1 Measured results

under the different tensile loads. The results are shown in Fig.5. The figure shows that when the tensile load is less than 300 MPa, the damage parameter almost does not change. When the tensile load exceeds 300 MPa, the damage parameter changes with tensile load quickly.
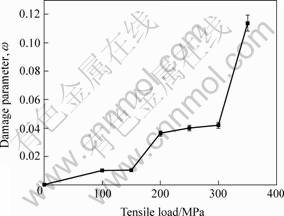
Fig.5 Relationship between damage parameter and tensile load
In order to deeply understand the damage of PMMC, the ultrasonic signal traveled in the specimen damaged under different tensional loads was analyzed by correlation method. For two signals y1(n) and y2(n), the correlation coefficient is defined as
(4)
According to the definition of the correlation coefficient, the correlation coefficients of the ultrasonic signals traveled in the damaged sample and that traveled in the initial sample were determined. The result is shown in Fig.6. The figure shows that the correlation coefficient decreases with the increase of the tensile load.
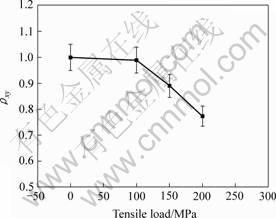
Fig.6 Correlation coefficient of ultrasonic signals traveled in damaged sample and in initial sample under different loads
Ultrasonic signal is always composed of a series of transient feedback impulsive waves, which are created during the propagation of ultrasonic energy when it meets the discontinuities within the material, such as inclusions, voids, micro-cracks. In order to understand how the material is damaged under the tensile load, the fracture section morphologies was observed by SEM. Fig.7 shows the fracture section morphologies of PMMC under the tensile load.
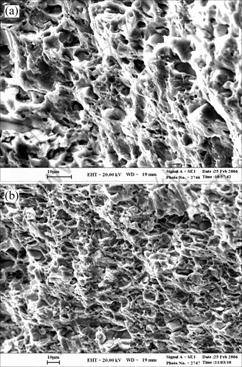
Fig.7 Fracture section morphologies of PMMC under tensile load
From Fig.7, it can be seen that there are many concaves in the metal matrix. Therefore the damage evolution can be concluded. The initial damage is induced by void nucleation, growth and subsequent coalescence in the matrix or interface separation. With the increase of the tensile load, the micro-crack comes into being at the initial damage location and the micro-crack propagation and forms the macro-crack.
4 Conclusions
1) The damage of the specimens induced by the different tensile load was determined by ultrasonic method. With the increase of tensile load, the damage parameter increases.
2) The ultrasonic signal traveled in the specimen damaged induced under different tensional load was analyzed by correlation method. With the increase of tensile load, the correlation coefficient decreases.
3) The fracture section morphologies of PMMC under tensile load were observed by SEM. There are many concaves in the metal matrix. Therefore the damage evolution can be concluded. The initial damage is induced by void nucleation, growth and subsequent coalescence in the matrix or interface separation.
References
[1] LLORCA J. Fatigue of particle- and whisker- reinforced metal- matrix composites [J]. Progress in Material Science, 2002, 47(3): 283-353.
[2] BIERMANN H, KEMNITZER M. On the temperature dependence of the fatigue and damage behavior of a particulate-reinforced metal-matrix composite [J]. Material Science Engineering A, 2001, 319: 671-674.
[3] HAN N L, WANG Z G, WANG W L, ZHANG G D. Low-cycle fatigue behavior of a particulate SiC/2024Al composite at ambient and elevated temperature [J]. Composites Science Technology, 1999, 59: 147-155.
[4] XIA Z, ELLYIN F. Multiaxial fatigue of an alumina particle reinforced aluminum alloy [J]. Internal Journal of Fatigue, 1998, 20: 51-56.
[5] HAN N L, ZHANG G D. Effect of reinforcement size on the elevated temperature tensile properties and low-cycle fatigue behavior of particulate SiC/Al composites [J]. Composites Science Technology, 1997, 57: 1491-1499.
[6] OLSSON M, GIANNAKOPOULOS A E, SURESH S. Elastoplastic analysis of thermal cycling: Ceramic particles in a metallic matrix [J]. Journal of Mechanics Physics Solids, 1995, 43: 1639-1671.
[7] LONG S G, ZHOU Y C. Thermal fatigue of particle reinforced metal matrix composite induced by laser heating and mechanical load [J]. Composites Science and Technology, 2005, 65: 1391-1400.
[8] ZHOU Y C, LONG S G. Thermal failure mechanism and failure threshold of SiC particle reinforced metal matrix composites induced by laser beam [J]. Mechanics Material, 2003, 35: 1003-1020.
[9] ZHOU Y C, LONG S G. Thermal damage and fracture of particulate reinforced metal matrix composites induced by laser beam [J]. Trans ASME Journal Engineering Material, 2001, 123: 251-260.
[10] LONG S G, ZHOU Y C. Determination of damage parameter in particle reinforced metal matrix composite by ultrasonic method [J]. Journal of Material Science Letter, 2003, 22: 911-913.
[11] ROKHLIN S I, CHU Y C, HUANG W. Ultrasonic evaluation of fatigue damage in metal matrix composites [J]. Mechanics Material, 1995, 21: 251-263.
[12] YANG W X, HULL J B, SEYMOURB M D. A contribution to the applicability of complex wavelet analysis of ultrasonic signals [J]. NDT&E International, 2004, 37: 497-504.
[13] ZHENG X J, ZHOU Y C, LIU J M, LI A D. Use of the nanmechanical fracture-testing for determining interfacial adhesion of PZT ferroelectrics thin films [J]. Surface and Coating Technology, 2003, 176: 67-74.
[14] ZHENG X J, ZHOU Y C, LIU J M, LI A D. Interfacial adhesion analysis of Pb(Zr0.52Ti0.48)O3 ferroelectrics thin films by nano- indentation test [J]. Physics letters A, 2002, 304: 110-113
(Edited by LI Xiang-qun)
Foundation item: Project(104014) supported by Fok’Ying Tong Education Foundation, China; Project(05B008) supported by the Scientific Research Fund of Hunan Provincial Education Department, China
Corresponding author: LONG Shi-guo; Tel: +86-732-8293577; Fax: +86-732-8292468; E-mail: longsg@xtu.edu.cn