
Effect of Cr on oxidation of Ni-xAl alloy
ZHANG Xue-jun(张学军)1, 2, GAO Chun-xiang(高春香)1, WANG Lei(王蕾)1, NIU Yan(牛焱)2
1. College of Applied Chemistry, Shenyang Institute of Chemical Technology, Shenyang 110142, China;
2. State Key Laboratory for Corrosion and Protection, Institute of Metal Research,
Chinese Academy of Sciences, Shenyang 110016, China
Received 15 July 2007; accepted 10 September 2007
Abstract: The oxidation of the Ni-10Cr-xAl(x=7%, 10%, molar fraction) alloys was studied at 1 100 ℃ under 0.1 MPa O2 and compared with that of the binary Ni-7Al and Ni-10Al alloys. The results show that the binary alloys form NiO external scales associated with an internal oxidation of Al. On the contrary, the ternary Ni-10Cr-7Al and Ni-10Cr-10Al form external alumina scale in contact with the alloy substrate. An addition of 10%Cr(molar fraction) into Ni-7Al and Ni-10Al inhibits the internal oxidation of aluminum and considerably reduces the critical content of Al needed to form exclusive alumina scales with respect to binary Ni-Al alloy, providing an example of third-element effect.
Key words: Ni-10Cr-xAl alloy; oxidation; third-element effect
1 Introduction
For applications in oxygen-rich environments at very high temperatures, alloys and coatings are often designed to develop surface layers of Al2O3. Ni-based alloys are often used as model to investigate the processes occurring in the oxidation of complex and multi-component alloys. The minimum aluminum concentration needed to form protective Al2O3 scales on Ni- based binary alloys has been estimated in the range from 8% and 17%(mole fraction)[1-4]. Unfortunately, these aluminum levels in binary alloys often result in unacceptable mechanical properties. The Ni-Cr-Al system forms a γ-γ′ structure that exhibits improved mechanical properties and better oxidation resistance than the corresponding binary alloys. Therefore, this system becomes a basis for the development of more oxidation-resistant materials by the addition of further alloying elements. In practice, adding chromium to Ni-Al alloys decreases the concentration of aluminum required to establish Al2O3 scale, providing a case of the third-element effect (TEE), which is of considerable interest for optimizing the composition of commercial alloys. The classical interpretation, initially proposed by WAGNER[5], assumes that the third element can reduce the flux of oxygen into the alloy, favoring the formation of external scales of the most reactive component. However, the precise role of the third element has not been yet very clear. One of other possible mechanisms advanced later[6], originally proposed by GIGGINS and PETTIT[7], is based on the idea that the simultaneous internal precipitation of the oxides of the two reactive components produces an overall volume fraction of internal oxide sufficient for the transition to an external scale according to a criterion defined by WAGNER[8] for binary alloys under reduced contents of the most reactive component than in binary alloys. In the present study, the effect of 10% Cr on the oxidation of Ni-7Al and Ni-10Al alloys at 1 100 ℃ was studied.
2 Experimental
The nominal compositions of the four alloys were Ni-7Al, Ni-10Cr-7Al, Ni-10Al, and Ni-10Cr-10Al. The corresponding actual composition of each alloy is listed in Table 1. The alloy ingots were prepared from high-purity metals by arc-melting under a Ti-gettered argon atmosphere using non-consumable tungsten electrodes from appropriate amounts of pure nickel (99.99%), aluminum (99.999%) and Cr (99.99%). The alloy ingots were subsequently annealed in argon atmosphere at 1 200 ℃ for 24 h to remove the residual mechanical stresses to achieve a better equilibration of the alloy phases.
Flat specimens with a surface area of about 2 cm2 were cut from the ingots by a diamond wheel saw, ground down to 1 200 emery paper, washed in water, alcohol and acetone and then dried immediately before use. Oxidation tests were carried out in 0.1 MPa of pure oxygen at 1 100 ℃ for 24 h with continuous mass gain measurement using a microbalance. The microstructures of the alloys and the oxide scales were characterized with scanning electron microscopy (SEM) and an energy-dispersive X-ray spectrometer (EDAX) attached to the SEM to establish the nature, composition, and spatial distribution of the compounds formed by oxidation.
Table 1 Actual compositions of four alloys(molar fraction, %)

3 Results and discussion
3.1 Scaling kinetics
The kinetics curves of Ni-7Al and Ni-10Cr-7Al oxidized at 1 100 ℃ are shown in Fig.1(a) and (b) as normal plots and parabolic plots, respectively. The oxidation kinetics of Ni-7Al obeys the parabolic rate law for the whole duration of the test with rate constant of 2.01×10-9 g2/(cm4?s). On the contrary, the mass change curves of Ni-10Cr-7Al are composed of an initial parabolic stage with rate constant equal to 2.17×10-10 g2/(cm4?s) for the first 0.6 h. After the first stage the slope of the parabolic plot decreases continuously with time down to a final value of about 1.18×10-12 g2/(cm4?s).
The normal plots and parabolic plots of Ni-10Al and Ni-10Cr-10Al oxidized at 1 100 ℃ under 0.1 MPa O2 are shown in Figs.2(a) and (b), respectively. The corrosion rate of Ni-10Al from the beginning of oxidation to 12 h obeys the parabolic rate law with a parabolic rate constant equal to 2.14×10-9 g2/(cm4?s), which is followed by a second stage whose instantaneous parabolic rate constant (IPRC, i.e. the slope of the parabolic plot) decreases with time down to 1.64×10-10 g2/(cm4?s). On the contrary, the oxidation kinetics of Ni-10Cr-10Al is composed of different stages with parabolic rate constants equal to 1.97×10-12 g2/(cm4?s) from initial to 1 h and then followed by a very slow oxidation stage. However, the specimen shows a very slight mass gain loss after 10 h oxidation possibly due to the volatilization of CrO3 produced by the reaction of Cr2O3 with O2.
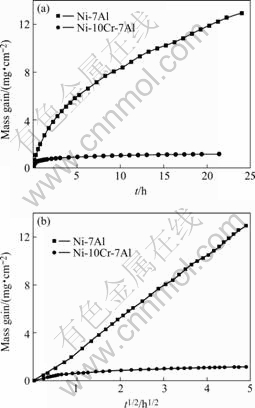
Fig.1 Scaling kinetics of Ni-7Al and Ni-10Cr-7Al alloys oxidized at 1 100 ℃ under 0.1 MPa O2: (a) Normal plots; (b) Parabolic plots
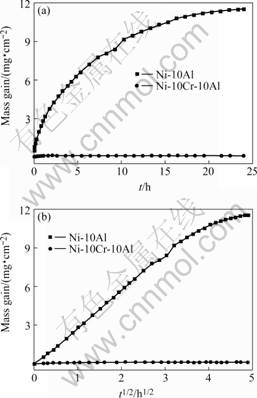
Fig.2 Scaling kinetics of Ni-10Al and Ni-10Cr-10Al alloys oxidized at 1 100 ℃ under 0.1 MPa O2: (a) Normal plots; (b) Parabolic plots
In general, the oxidation rate of the ternary alloy containing Cr is much slower than that of the corresponding binary alloy. In particular, the average parabolic rate constants of Ni-10Cr-7Al and Ni-10Cr- 10Al are about three orders of magnitude smaller than that for the corresponding binary alloys.
3.2 Scale microstructure and composition
The microstructure of the scales formed on the four alloys after oxidized at 1 100 ℃ under 0.1 MPa O2 for 24 h are shown in Fig.3. Ni-7Al forms a dense external layer of NiO containing some Ni-Al spinel particles in an inner region corresponding to the alloy consumption zone, which is followed by a zone of internal oxidation of aluminum. Intergranular oxidation and a discontinuous alumina scale in the front of the internal oxidation are also observed, as shown in Fig.3(a). On the contrary, after 24 h oxidation of Ni-10Cr-7Al at 1 100 ℃, an outermost lighter layer of NiO, a subscale is composed of a mixture of oxides of all the alloy components and also their double oxides, and a very thin but continuous layer of alumina formed at the interface of oxide scale and the substrate, as shown in Fig.3(b). The scale formed on Ni-10Al after 24 h oxidation at 1 100 ℃(Fig.3(c)) contains the outermost lighter layer of NiO, the intermediate layer made up of the mixture of NiO, Al2O3, and Ni-Al spinel, and the innermost layer of precipitates of alumina. A continuous alumina scale formed at the front of the subscale is observed. An exclusive external scale of alumina formed on Ni-10C-10Al (Fig.3(d)).
3.3 Discussion
A systematic study of the oxidation of ternary Ni-Cr-Al alloys at 1 000-1 200 ℃ carried out by GIGGINS and PETTIT[7] has identified three groups of alloys. Alloys of groupⅠformed external NiO scales associated with an internal oxidation of chromium plus aluminium; alloys of group Ⅱ formed external chromia scales coupled to an internal oxidation of aluminium; and alloys of group Ⅲ formed exclusive external alumina scales. In addition, it has been found that the addition of chromium reduces the critical aluminum content needed to form alumina scales with respect to binary Ni-Al alloys[7].
The exclusive growth of external Al2O3 scales in the oxidation of ternary Ni-Cr-Al alloys requires to avoid two different kinds of internal oxidation: 1) the coupled internal oxidation of Al and Cr beneath external NiO scales and 2) the internal oxidation of Al beneath external chromia scales. The critical Al contents needed for the transitions from these forms of internal oxidation to the external oxidation of Al have been calculated by ZHANG et al[9-11]. It was concluded that the critical Al content needed to avoid the coupled internal oxidation of Cr + Al beneath external NiO scales,
(t, NiO), decreases almost linearly with an increase of the Cr content of the alloy. A second critical Al content needed for the transition between the internal oxidation beneath Cr2O3 scale and the formation of external alumina scales,
(t, Cr2O3), which is again a function of the chromium content in the bulk alloy,
. According to the theoretical oxidation map[10-11], Ni-10Cr-7Al and Ni-10Cr-10Al fall into the zone of forming alumina protective scale. The present experimental results agreed with the theoretical analysis[10-11] and with the oxidation map obtained by GIGGINS and PETTIT[7].

Fig.3 Cross sections (SEM/BEI) of Ni-7Al (a), Ni-10Cr-7Al (b), Ni-10Al (c) and Ni-10Cr-10Al (d) oxidized at 1 100 ℃ under 0.1 MPa O2 for 24 h
4 Conclusions
1) The oxidation rate of the ternary alloy containing 10% Cr(molar fraction) is much slower than that of the corresponding binary alloys.
2) Ni-7Al and Ni-10Al alloys form external NiO scales followed by a zone of internal oxidation of Al. Conversely, the scales formed on Ni-10Cr-7Al and Ni-10Cr-10Al alloys are protective.
3) An addition of 10%Cr to Ni-7Al and Ni-10Al alloys is sufficient to prevent the internal oxidation of Al and to induce the formation of external alumina scales, providing an example of third-element effect.
References
[1] WOOD G C, STOTT F H. Establishment and breakdown of α-Al2O3 scale on Ni-Al alloys at high temperatures[J]. Br Corros J, 1971, 6: 247-256.
[2] PETTIT F S. Oxidation mechanism for nickel-aluminium alloys at temperatures between 900 ℃ and 1 300 ℃[J]. Trans Metall Soc AIME, 1967, 239: 1296-1305.
[3] SMIALEK J L. Oxide morphology and spalling model for Ni-Al[J]. Met Trans, 1978, 9A: 309-320.
[4] HINDAM H M, SMELTZER W W. Growth and microstructure of α-Al2O3 on Ni-Al alloys: Internal precipitation and transition to external scale[J]. J Electrochem Soc, 1980, 127: 1622-1630.
[5] WAGNER C. Passivity and inhibition during the oxidation of metals at elevated temperatures[J]. Corros Sci, 1965, 5: 751-764.
[6] STOTT F H, WOOD G C, STRINGER J. The influence of alloying elements on the development and maintenance protective scales[J]. Oxid Met, 1995, 44: 113-145.
[7] GIGGINS C S, PETTIT F S. Oxidation of Ni-Cr-Al alloy between 1 000-1 200 ℃[J]. J Electrochem Soc, 1971, 118: 1782-1790.
[8] WAGNER C. Types of reaction in the oxidation of alloys[J]. Z Elektrochem, 1959, 63: 772-782.
[9] ZHANG Xue-jun, GESMUNDO F, NIU Y. The third-element effect on the oxidation of Ni-xCr-7Al alloys (x=0, 5, 10, molar%) at 1 173 K[J]. High Temp Mater Proc, 2005, 24: 369-374.
[10] NIU Yan, ZHANG Xue-jun, WU Ying, GESMUNDO F. The third-element effect in the oxidation of Ni-xCr-7Al (x=0, 5, 10, 15, molar%) alloys in 1 atm O2 at 900-1 000 ℃[J]. Corros Sci, 2006, 48: 4020-4036.
[11] ZHANG Xue-jun, WANG Shui-yong, GESMUNDO F, NIU Yan. The effect of Cr on the oxidation of Ni-10Al in 1 atm O2 at 900- 1 000 ℃[J]. Oxid Met, 2006, 65: 151-165.
Foundation item: Project(03206) supported by Shenyang Institute of Chemical Technology, China; Project(50571107) supported by the National Natural Scientific Foundation of China
Corresponding author: ZHANG Xue-jun; Tel: +86-24-89383297; E-mail: xjzhang_syict@163.com
(Edited by CHEN Wei-ping)