
Environmental corrosion resistance of porous TiAl intermetallic compounds
ZHENG Zhi(郑 治)1, 2, JIANG Yao(江 垚)1, DONG Hong-xing(董虹星)1,
TANG Lie-min(汤烈明)1, HE Yue-hui(贺跃辉)1, HUANG Bai-yun(黄伯云)1
1. State Key Laboratory of Powder Metallurgy, Central South University, Changsha 410083, China;
2. The Third Xiangya Hospital, Central South University, Changsha 410013, China
Received 5 March 2008; accepted 9 September 2008
Abstract: Porous TiAl intermetallic compound, as a novel substitute for current inorganic porous material, offsets the shortages of both ceramics and metals. The environmental corrosion resistance of porous TiAl intermetallic compound was investigated. The kinetic equation for the cyclic oxidation of porous TiAl alloy at 600 ℃ is determined to be Δm2=1.08×10-5t. After total oxidation of 140 h, porous TiAl intermetallic compound shows more stability of pore structure and the mass gain of TiAl alloy is 0.042 g/m2, which is only 10.6% that of porous 316L stainless steel. The kinetic equation for the cyclic corrosion behavior of porous TiAl alloy in hydrochloric acid with pH=2 at 90 ℃ is determined to be Δm2=5.41×10-5t-2.08×10-4. After 50 h exposure, the mass loss of TiAl alloy is 0.049 g/m2, which is only 14.8% and 5.57% that of porous Ti and stainless steel, respectively. The kinetic equation in hydrochloric acid with pH=3 is determined to be Δm2=2.63×10-6t-3.72×10-6.
Key words: TiAl intermetallic compound; porous material; high temperature oxidation resistance; corrosion resistance
1 Introduction
Recently, HE et al[1-2] developed a novel technique to fabricate porous TiAl intermetallics using elemental powders by reactive synthesis process. Both the solid diffusion and reaction synthesis during this procedure suppressed the self-propagating high- temperature synthesis(SHS), thus near-net shape of porous TiAl intermetallics with self-control pore structures was realized. Furthermore, intermetallic compounds possess the superior properties of ceramics and metals. Therefore, this novel porous material shows great potential in engineering applications.
It is shown that the intermetallic compounds provide outstanding corrosion resistance because of a mixture of metallic and covalent bonds[3-7], while their brittleness at room temperature restricts their applications. In addition, porous materials call for suitable physical and chemical properties rather than its ductility at room temperature. However, the environmental resistivities of current metals used for porous materials were not good enough to apply in some rugged conditions well[8-13]. The excellent environmental corrosion resistance of the intermetallics implies the wide potential applications of porous intermetallic compounds. In order to investigate the environment resistance behavior of porous materials and provide basic data for future applications, the environmental corrosion resistance of porous TiAl intermetallic compounds including high temperature oxidation resistance and strong acid corrosion resistance are studied in details in this work.
2 Experimental
The studied materials were porous g-TiAl containing 34% Al without any other additional element, 316L porous stainless steel, porous nickel and porous titanium. The cyclic oxidation test was run in air at 600 ℃. One cycle represented 10 h exposure at the experimental temperature, followed by cooling in furnace to room temperature. After each cycle, the mass change due to the oxidation of each specimen was carefully determined. The total exposure time at the corrosion temperature was 140 h.
In the case of acid corrosion experiments, the specimens exposed cyclically to hydrochloric acid at 90 ℃ with pH values of 2 and 3, respectively. Each cycle comprised 10 h exposure in the acid at the corrosion temperature. The mass loss due to the acid corrosion process was accurately determined after careful clean-out for each cycle.
SEM/EDS was used to identify the porous conformation and oxide or acid corrosion resultants after high temperature oxidation at 600 ℃ for 140 h and acid corrosion at 90 ℃ for 50 h, respectively.
3 Results and discussion
3.1 Oxidation experiment of porous TiAl
3.1.1 Oxidation kinetic behaviors
The data shown in Fig.1 illustrate the effect of cyclic oxidation exposure on the mass gain per unit area of porous TiAl alloys and porous 316L stainless steel in air at 600 ℃ for 140 h, respectively. It can be inferred that an initial high rate of oxidation is observed for porous stainless steel compared with porous TiAl alloys. The total mass gain of porous TiAl alloy is only 10.6% that of the stainless steel.
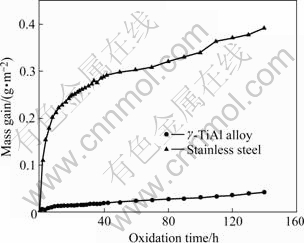
Fig.1 Mass gain per unit area during cyclic exposure of TiAl porous alloy and porous 316L stainless steel in air at 600 ℃
According to Ref.[14], the high temperature oxidation of TiAl alloy as well as most kinds of metals follows the parabolic rate law or linear rate law. The parabolic rate law of oxidation shown in Eq.(1) depends on the ion solid diffusion rate:
?m2=kp?t+C (1)
where Δm is the mass gain per unit area (g/m2) at a given exposure time t (h), C is the oxidation integral constant and kp is the parabolic rate constant of oxidation (g2?m-4?h-l).
The linear rate law of oxidation as shown in Eq.(2) is determined by the chemical reaction rate of oxidation formation directly:
?m=kt?t+Ct (2)
where kt is the linear rate constant of oxidation (g2?m-4?h-l) and Ct is the oxidation integral constant.
The high temperature oxidation rate constant and determinant coefficient of porous TiAl alloy and 316L porous stainless steel are listed in Table 1 by analyzing the mass gain curve based on Eq.(1) and Eq.(2), respectively. It is obvious that the determinant coefficients of the two materials obtained from parabolic rate law show high value compared with those obtained from linear rate law. Therefore, all the oxidation behaviors during the cyclic oxidation test obey the parabolic rate law. By applying the rate constant of oxidation and determinant coefficient of the parabolic rate law, the oxidation kinetics of porous TiAl alloy is
?m2=1.08×10-5 t (3)
Table 1 Oxidation rate constants and determinant coefficients of TiAl porous alloy and porous 316L stainless steel
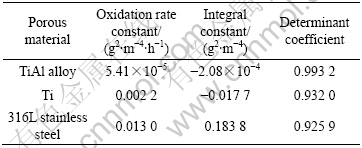
Also, the porous TiAl intermetallic material shows superior high temperature oxidation resistance to porous 316L stainless steel because the rate constant of oxidation of porous TiAl is only 1.3% that of porous 316L stainless steel.
3.1.2 Maximum pore size alteration
Fig.2 displays the effect of cyclic oxidation time on the maximum pore size (representative of porous structures) of porous TiAl alloys, porous Ni, porous Ti and porous 316L stainless steel in air at 600 ℃ for 100 h. It is evident that the maximum pore size of porous TiAl during the oxidation test almost stabilizes at about 37 μm, while the other three popular porous materials (porous Ni, porous Ti and porous 316L stainless steel) are blocked after 20 h oxidation test resulting from the thick oxide formation. Considering the superior pore conformation stability in the air at high temperature, the porous TiAl alloy can be applied to the fields of solid-gas separation due to its excellent high-temperature oxidation resistivity.
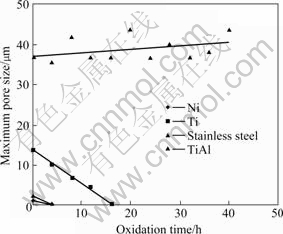
Fig.2 Maximum pore size alteration of porous TiAl alloy, porous Ni, Ti, and 316L stainless steel during cyclic oxidation procedure at 600 ℃
3.1.3 Pore structures
SEM/EDS and XRD were also used to analyze the morphology or surface composition of porous TiAl alloy resulting from high-temperature oxidation after 100 h exposure at 600 ℃. Figs.3(a) and (b) illustrate the SEM surface morphologies of porous TiAl alloy before and after high-temperature oxidation exposure. It is revealed that the pore structures of porous TiAl alloy almost remain the same, though there are some white substances on the surface of the sample after high-temperature oxidation exposure. Weak oxygen peak appears in EDS analysis spectrum (Fig.4), indicating that a little oxides form on the porous surface during the oxidation experiments. Because the amount of the oxides is little, the XRD analysis cannot almost detect it.
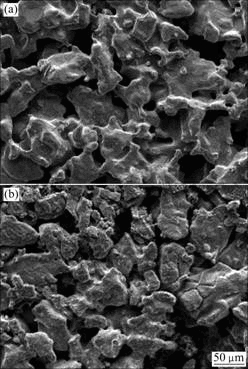
Fig.3 Comparison of pore structures of porous TiAl alloy: (a) Before oxidation; (b) After 100 h cyclic oxidation at 600 ℃
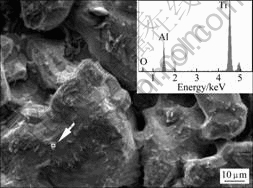
Fig.4 Microstructure and EDS pattern of oxides on surface of porous TiAl alloy
The results presented here reveal very promising high-temperature oxidation resistance of porous TiAl compared with popular porous metal materials. This could be explained based on two combined factors. 1) It is well-known that the dense TiAl intermetallic material has an excellent high-temperature oxidation resistance above 800 ℃[3-5]. 2) Three-dimensional small pores block the air convection and ensure the less mass gain per area during oxidation exposure. The excellent oxidation resistances of porous TiAl alloy at 600 ℃ can solve the hard problem of poor high temperature properties of the current porous metals.
3.2 Acid corrosion resistance of porous TiAl intermetallic material
3.2.1 Kinetic behaviors at pH=2
The data shown in Fig.5 illustrate the effect of cyclic acid corrosion time on the mass loss per unit area of porous TiAl alloys, porous Ti and porous 316L stainless steel in hydrochloric acid with pH=2 for 50 h.
It can be inferred from the plots that acid corrosion behavior of porous TiAl, Ti and 316L stainless steel follows the parabolic law. The total mass loss of porous TiAl alloy is only 14.8% and 5.57% that of the porous Ti and the stainless steel, respectively.
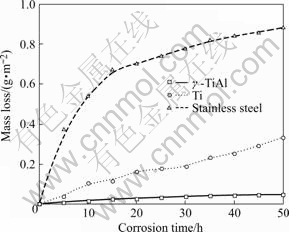
Fig.5 Mass loss per unit area during cyclic exposure of porous TiAl alloy, porous Ti and porous 316L stainless steel in hydrochloric acid with pH=2
According to Eq.(1), the corrosion constants, integral constants and determinant coefficients of the three porous materials are obtained, as listed in Table 2.
Table 2 Regression of parabolic law for corrosion kinetic curves of porous TiAl alloy, Ti and 316L stainless steel
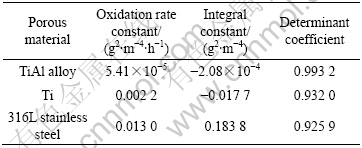
It is ascertained that all the oxidation behaviors during the cyclic corrosion test obey the parabolic rate law. By applying the oxidation rate constant and determinant coefficient of the parabolic rate law, the acid corrosion kinetics of porous TiAl alloy is obtained:
?m2=5.41×10-5t-2.08×10-4 (4)
The oxidation rate constant of porous TiAl (R=5.41×10-5 g2/(m4?h) is only 2.4% and 0.4% that of porous 316L stainless steel and Ti, respectively, which indicates that the porous TiAl intermetallic material shows superior hydrochloric acid corrosion resistance to porous 316L stainless steel and Ti.
3.2.2 Kinetic consideration at pH=3
The data shown in Fig.6 illustrate the effect of cyclic acid corrosion time on the mass loss per unit area of porous TiAl alloys, porous Ti and porous 316L stainless steel in hydrochloric acid with pH=3 for 35 h.
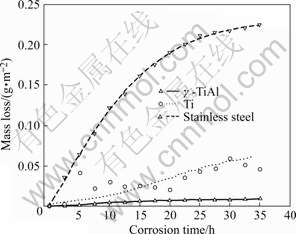
Fig.6 Mass loss per unit area during cyclic exposure of TiAl porous alloy, porous Ti and 316L stainless steel in hydrochloric acid with pH=3
As shown in Fig.6, acid corrosion behavior of porous TiAl, Ti and 316L stainless steel follows the parabolic law. The total mass loss of porous TiAl alloy is only 21.3% and 4.4% that of the porous Ti and stainless steel, respectively. And the total mass loss of porous TiAl alloy in hydrochloric acid with pH=3 is 23.8% that in acid with pH=2, indicating that the mass loss decreases with increasing the pH value.
The acid corrosion kinetic of porous TiAl intermetallic material in hydrochloric acid with pH=3 is obtained:
?m2=2.63×10-6t-3.72×10-6 (5)
Analyzing Eqs.(4) and (5), it is evident that the corrosion rate decreases by 95% when the pH value increases from 2 to 3.
3.2.3 Pore structures
SEM/EDS and XRD were used to analyze the surface composition of porous TiAl intermetallic material resulting from hydrochloric acid corrosion with pH=2 after 50 h exposure. Figs.7(a) and (b) illustrate the SEM images of the surface of porous TiAl before and after acid corrosion. It is revealed that the pore conformation of porous TiAl almost remain the same during the hydrochloric acid experiments. Similar to high-temperature oxidation, the XRD pattern does not show chloride phase other than TiAl phase.
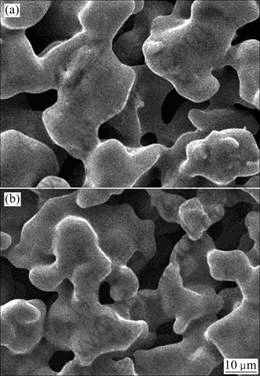
Fig.7 Comparison of pore structures of TiAl porous alloy: (a) Before acid corrosion; (b) After 50 h cyclic corrosion in hydrochloric acid with pH=2
The porous TiAl alloy shows superior corrosion resistance in hot hydrochloric acid to the popular porous metal materials. According to Refs.[15-16], TiAl contains a mixture of metal bond and covalent bond. In addition, the Ti—Ti metal bonds possess high passivating coefficient in acid solutions with certain concentration. Moreover, the covalent bond restricts most of the free electron of the Ti and Al atoms, which block the anodic reaction in the hydrochloric acid. Therefore, the porous TiAl alloys provide superior strong acid corrosion resistance to the porous Ti.
4 Conclusions
1) The porous TiAl alloy shows a significant high-temperature oxidation as well as strong acid corrosion resistance compared with the popular porous metal materials.
2) The oxidation behavior of porous TiAl in air at 600 ℃ follows the parabolic law. After 100 h cyclic exposure, the maximum pore size of TiAl always remains constant, whereas the pores of the porous Ti, Ni and 316L stainless steel are almost blocked within 20 h exposure. The good high-temperature oxidation properties of porous TiAl are due to the essence of TiAl material as well as its pore structures.
3) The corrosion behavior of porous TiAl in hydrochloric acid with pH=2 obeys the parabolic law. The corrosion behavior in hydrochloric acid with pH=3 is similar to that in the hydrochloric acid with pH=2. The mass loss of porous TiAl is 0.010 g/m2, which is only 21.3% and 4.4% that of porous Ti and the 316 stainless steel after 35 h cyclic corrosion experiments, respectively. The superior corrosion resistance of the porous TiAl is based on its chemical bond combined by the metal bond and covalent bond.
References
[1] HE Yue-hui, JIANG Yao, XU Nan-ping, ZOU Jin, HUANG Bai-yun, LIU C T, LIAW P K. Fabrication of Ti-Al micro/ nanometer-sized porous alloys through the Kirkendall effect [J]. Adv Mater, 2007, 19: 2102-2106.
[2] JIANG Yao, HE Yue-hui, XU Nan-ping, ZOU Jin, HUANG Bai-yun, LIU C T. Effects of the Al content on pore structures of porous Ti-Al alloys [J]. Intermetallics, 2008, 16: 327-332.
[3] POVAROVA K B, ANTONOVA A V, BANNYKH I O. High- temperature oxidation of TiAl based alloys [J]. Metally, 2003, 5: 61-72.
[4] TENG L, NAKATOMI D, SEETHARAMAN S. Oxidation behavior of TiAl-8Nb turbine blade alloy [J]. Metallurgical and Materials Transactions B: Process Metallurgy and Materials Processing Science, 2007, 38(3): 477-484.
[5] GAUTHIER V, DETTENWANGER F,SCH?TZE M,SHEMET V,QUADAKKERS W J. Oxidation-resistant aluminide coatings on gamma-TiAl [J]. Oxidation of Metals, 2003, 59(3/4): 233-255.
[6] ZHAO Bin, WU Jian-sheng, SUN Jian, TU Bi-jun, WANG Fei. Oxidation kinetics of the nitrided TiAl-based alloys [J]. Materials Letters, 2002, 56(4): 533-538.
[7] FU C L, YOO M H. Elastic constants, fault energies, and dislocation reactions in TiAl: A first-principles total-energy investigation [J]. Philosophical Magazine Letters, 1990, 62(3): 159-165.
[8] YAO Zhong-ping, JIANG Zhao-hua, WANG Fu-ping, HAO Guo-dong. Oxidation behavior of ceramic coatings on Ti-6Al-4V by micro-plasma oxidation [J]. Journal of Materials Processing Technology, 2007, 190(1/3): 117-122.
[9] YOSHIHARU I, MASAO K, MASAYUKI T, HARUHIKO K. Oxidation behavior of Al-containing ferritic stainless steel in an exhaust gas atmosphere [J]. Journal of the Japan Institute of Metals, 2006, 70(11): 880-889.
[10] AHN H, LEE D, LEE K M, LEE K, BAEK D, PARK S W. Oxidation behavior and corrosion resistance of Ti-10Ta-10Nb alloy [J]. Surface and Coatings Technology, 2008, 202(22/23): 5784-5789.
[11] EBRAHIMI A R, ZAREI F, KHOSROSHAHI R A. Effect of thermal oxidation process on fatigue behavior of Ti-4Al-2V alloy [J]. Surface and Coatings Technology, 2008, 203(1/2): 199-203.
[12] YOSHIO S, TAKASHI E. High temperature oxidation behavior of borided steel [J]. Journal of the Iron and Steel Institute of Japan, 1978, 64(9): 1396-1403.
[13] ZHU Ri-zhang, YANG De-jun, SHEN Zhuo-shen. Metal corrosion [M]. Beijing: Metallurgy Industry Press, 1989: 6-47. (in Chinese)
[14] ZNAM S, NGUYEN-MANH D,PETTIFOR D G, VITEK V. Atomistic modeling of TiAl (I): Bond-order potentials with environmental dependence [J]. Philosophical Magazine, 2003, 83(4): 415-438.
[15] NGUYEN-MANH D, CAWKWELL M J, GR?GER R, MROVEC M, PORIZEK R, PETTIFOR D G, VITEK V. Dislocations in materials with mixed covalent and metallic bonding [J]. Mater Sci Eng A, 2005, 400/401(s1/2): 68-71.
[16] FU C L, YOO M H. Electronic structure and mechanical behavior of transition-metal aluminides: A first-principles total-energy investigation [J]. Materials Chemistry and Physics, 1992, 32(1): 25- 36.
Foundation item: Projects(20636020, 20476106 and 50825102) supported by the National Natural Science Foundation of China; Project(2003CB615707) supported by the National Basic Research Program of China; Project(2006AA03Z511) supported by the Hi-tech Research and Development Program of China; Project(50721003) supported by the Creative Research Group of National Natural Science Foundation of China
Corresponding author: HE Yue-hui; Tel: +86-731-8836144; E-mail: yuehui@mail.csu.edu.cn
DOI: 10.1016/S1003-6326(08)60316-7
(Edited by YANG Bing)