
Thermal expansion and mechanical properties of
Al/Si composites fabricated by pressure infiltration
ZHENG Jing(郑晶)1, SONG Wen-juan(宋文娟)2, MA Guang(马光)1, JIA Zhi-hua(贾志华)1
1. Electronic Material Research Centre, Northwest Institute for Nonferrous Metal Research, Xi’an 710016, China;
2. School of Materials Science and Engineering, Xi’an University of Technology, Xi’an 710048, China
Received 15 July 2007; accepted 10 September 2007
Abstract: High reinforcement content Al/Si composites were fabricated by pressure infiltration technology. The composites are free of porosity and silicon particles distribute uniformly in the composites. The properties and fracture behavior of the composites were studied. The composites fracture is aroused by silicon brittle fracture and extends to the composites inward through the metallurgical structure and fracture analysis. The thermal expansion behavior of the composites was investigated by a high-precision thermomechanical analyzer,and compared with the predictions of theoretical model. The mean linear coefficient of thermal expansion (CET) of Al/Si composites ranges from 8×10-6 to 10×10-6/℃ and decreases with increasing silicon volume fraction.
Key words: Al/Si composites; CET; fracture; pressure infiltration
1 Introduction
With component size reduction and computing capability increase, thirty percent of current chip performance is limited by electronic packaging materials[1]. Thus, more and more attention has been paid to electronic packaging materials. In microelectronic circuits, thermal fatigue results from the difference between coefficient of thermal expansion of chips and carrier substrate. Overheating will also lead to a crash. In addition, some packaging materials have also been used in the aerospace field, for which not only suitable coefficients of thermal expansion and thermal conductivity are required but also low density and appropriate mechanical strength. Al/Si composites are identified as a potentially suitable material system because they have high thermal conductivity, low coefficient of thermal expansion and low density[2]. The coefficient of thermal expansion, thermal conductivity and density of Al/Si composites were studied by JACOBSON et al[3] and CHIEN et al[4-5]. The processes for obtaining the composite materials include solid-state processes such as powder metallurgy (PM), where metal and ceramic powders are blended and hot-pressed[4], and liquid-state processes such as melt infiltration[5]. The composites are also produced by spay-formed method[6]. For melt matrix composites (MMCs), PM is costly, but is suitable for small components. The advantages of pressure casting are high productivity and ease of fabrication, but the pressure casting machine and the die are expensive. The composite produced by spray-formed method has up to 4%(volume fraction) porosity and has to be followed by hot isocratic pressing[7]. To authors’ knowledge, very few studies have been performed using the pressure infiltration method to produce the composite[8], even though both processing and equipment are simple.
Furthermore, the CET of MMCs is recognized as one of the important thermomechanical property because the thermal stability can be a critical issue in the design of components subjected to temperature variations[9]. Tailoring the CET is an important consideration in minimizing the expansion-contraction mismatch or to maintain specific dimensional tolerances between components subjected to various temperature gradients. In addition, a thermal expansion study of MMCs is required in order to investigate thermal stresses for particular applications such as electronic packaging[10].
The purpose of this study is to use pressure infiltration method to produce the Al/Si composites and examine their properties. The effect of reinforcement volume fraction is also explored, which is known to exert a significant influence on the thermal expansion behavior of Al/Si composite. In this work, CET of the Al/Si composites is measured between 20 ℃ and 180 ℃, and the fracture behavior of Al/Si is also studied.
2 Experimental
2.1 Preparation of composites
The experiments were conducted using powdered aluminum and silicon of 74 μm. Firstly, the powdered aluminum and silicon powder were ball milled for a period of time. After ball milling, the aluminum powder and silicon powder were mixed by V mixer machine. Taking account of problem of the powder oxidization, the method of wet-mixing was used. The absolute alcohol was used as the solvent of wet-mixing. The rotational speed was 67 r/min.
The mixture of the aluminum powder and the silicon powder was pressed in the compacting tool, whose diameter was 50.0 mm. The preform containing 25%-50% volume fraction silicon was obtained, and then the perform was put in a preheated metal mold (400 ℃). At the same time, after filtering the slag, the melt of ZL102 was poured into the die, and then was rapidly compressed and held for 60 s. After solidification, the column composite with a diameter of 55 mm was gained. The specimen for metallographic observation was corroded with 0.5% hydrofluoric acid solution. The microstructure was observed with a optical microscope (LEICAMEF4M OM), and a scanning electron microscope (Philips S-520 SEM).
2.2 Measurement of properties
Indentation method was used in this experiment to test the Brinell hardness of the composites. The hardness test under the conditions of the load of 7 350 N, diameter of steel ball 5 mm and load time 30 s was done on a HB-3000 Brinell hardness tester. The hardness values were the average of three hardness values from each specimen.
The size of the specimen for thermal expansion test was 3 mm×3 mm×10 mm. The specimen was cut from the composite using the diamond blade and was burnished. The experiment data obtained from three specimens which were cut from the same composite were taken as the average value. The coefficient of thermal expansion of specimens was tested from 20 ℃ to 180 ℃, with the heating rate of 5 ℃/min, by a common thermo-mechanical analyzer.
3 Results and discussion
3.1 Properties of Al/Si composites
Fig.1 shows the typical optical micrographs of composites containing of 30%, 40%, 50% of silicon particles. It can be seen that the silicon particles are distributed homogeneously. No un-melted region is discovered. The silicon particle and metal are combined tightly under pressure.
Fig.2 shows the relation of hardness with the volume fraction of silicon particle. The hardness of Al/Si composite material increases with increasing the volume fraction of silicon particle.
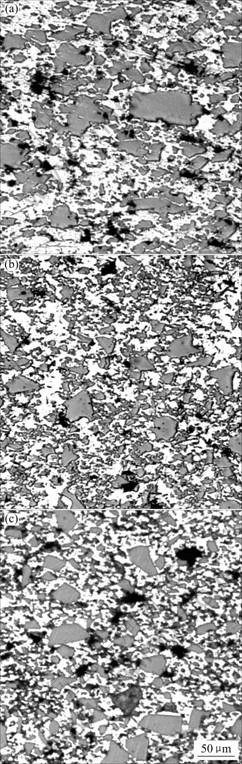
Fig.1 OM micrographs of Al/Si composites with silicon particles at different contents: (a) 30%; (b) 40%; (c) 50%
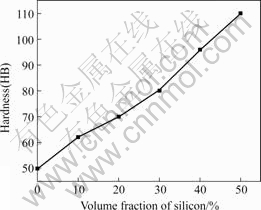
Fig.2 Relation of volume fraction of silicon with hardness
3.2 Fracture mechanism of Al/Si composites
Fig.3 shows the SEM fractographs of Al/Si composites. From the fractograph of the fracture surface of Al/Si composites with 50% silicon particles, the fracture of Al/Si composite is a typical brittle mode. As shown in Fig.3(a), the fracture surfaces of most silicon particles are clear cleavage, indicating that fracture propagates through the particles with shear model. As a ductile metal matrix aluminum is drawn to a certain extent, it undergoes certain plastic deformation. The deformation of reinforcing particles generally remains elastic due to the much higher yield stress. So the stress concentration within the particles will be very high. In the process of load transfer, the matrix transfers the load to the silicon particles. For a good interfacial bond, if the transferred load exceeds the Griffith’s criterion, the transferred load will result in brittle fracture of the silicon particles. Fig.3 (b) shows the high magnification image of the fracture surface. It is shown that at room temperature silicon is inherently brittle and that there is no dislocation activity at the crack tip.
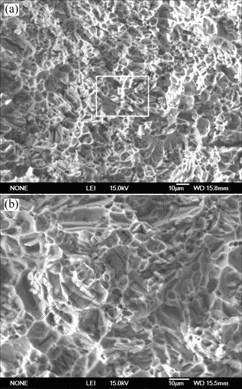
Fig.3 SEM images of fracture surface of Al/Si composites
From Fig.3, it is clear that the fracture of silicon particles is serious due to its native brittleness. It is very clear that the fracture path of the Al/Si composite is that cracks pass through silicon particles. There are less debonding silicon particles and cracks passing along the interface between aluminum and silicon particles. Therefore, the fracture behavior of this composite is that stress results in the brittle fracture of silicon particles, and then cracks will enter into the ductile matrix and lead to the final fracture of the composite.
3.3 Thermal expansion
As we known, several theoretical models were proposed to predict the CET of particulate reinforced composite. Turner’s model[11] considers the uniform hydrostatic stresses and gives the CET of a composite as:
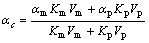
where K is the bulk modulus; G is shear modulus; αm is thermal expansion coefficient of basal phase; αp is thermal expansion coefficient of strong phase; Vm is volume fraction of basal phase; Vp is volume fraction of swell phase; Km is elastic modulus of basal phase; Kp is elastic modulus of swell phase. The elastic modulus of silicon is 1.9×105 MPa, and that of aluminum is 0.69×105 MPa (supposing that Si is included in ZL102, the rest of 12% is Al). The thermal expansion coefficient of silicon is 3.06×10-6/℃, and that of aluminum is 23.6×10-6/℃.
As shown in Fig.4, with the increase of the silicon content, the thermal expansion coefficient reduces, which is related to the low thermal expansion coefficient of silicon. At the same time, the silicon grains distribute dispersively in the material, which can restrain the high thermal expansion coefficient of aluminum well.
Fig.4 shows the difference of thermal expansion coefficient between experimental and theoretical values.
Thermal expansion coefficient is related to the volume content of the grain, however, the different thermodynamics characteristic of ZL102 melt and grain silicon in composite should be considered simultaneously. The thermal expansion coefficient of grain silicon, and the mutuality characteristic of ZL102 aluminum are the reason why the thermal expansion coefficient of composite reduces with increasing content of grain silicon. In general, heat expansion behavior of composite is the result of complicated interaction between grain silicon phase and microstructure of aluminum matrix.
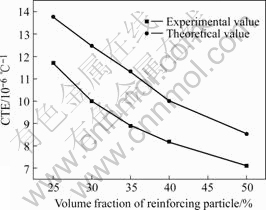
Fig.4 Relationship between coefficient of thermal expansion and volume fraction of reinforcing particle
4 Conclusions
1) With proper ratio of silicon particles to aluminum particles, Al/Si composites were fabricated by pressure infiltration. The composites are macroscopically dense and homogeneous. The Brinell hardness increases from 60 MPa to 110 MPa with increasing volume fraction of silicon.
2) The fracture behavior of Al/Si composite is that the stress results in the brittle fracture of silicon particles, and then the cracks enter into the ductile matrix and leads to the final fracture of the composites.
3) The mean linear coefficients of thermal expansion (20-180 ℃) of Al/Si composites range from 8×10-6 to 10×10-6 ℃-1 and decrease with increasing silicon volume fraction. The volume fraction of the reinforcing particles is the major factor in the determination of thermal expansion coefficients of composites.
References
[1] LEE S K, BYUN J H, HONG S H. Effect of fiber geometry on the elastic constants of the plain woven fabric reinforced aluminum matrix composites[J]. Mater Sci Eng A, 2003, 347: 346-358.
[2] MISEREZ A, MORTENSEN A. Fracture of aluminium reinforced with densely packed ceramic particles: Influence of matrix hardening [J]. Acta Materialia, 2004, 52: 5331-5345.
[3] EVANS R D, BOYD J D. Near-interface microstructures in a SiC/Al composite[J]. Scripta Materialia, 2003, 49: 59-63 .
[4] CHIEN C W, LEE S L, LIN J C, JAHN M T, et al. Effects of Si size and volume fraction on properties of Al/Si composites[J]. Materials Letters, 2002, 52: 334-341.
[5] CHIEN C W, LEE S L, et al. Processing and properties of high volume fraction aluminium/silicon composites[J]. Mater Sci Technol, 2003, 19(9): 1231-1237.
[6] ARSLA G,KARA F, VE TURAN S. Phase studies of reactive infiltrationboron carbide-aluminum composite by quantitative XRD[J]. Key Engineering Materials, 2002, 759: 206-213.
[7] JACOBSON D M. Lightweight electronic packaging technology based on spray formed Si-Al[J]. Powder Metallurgy, 2000, 43(3): 200-209.
[8] PARK J, KANG M K. A numerical simulation of the resin film infusion process[J] .Composite Structures, 2003, 60: 431-437.
[9] KI M B G, DONG S L, PARK S D. Effects of thermal processing on thermal expansion coefficient of a 50 vol%SiCP/Al composite[J]. Materials Chemistry and Physics, 2001, 72: 42-47.
[10] DUCRET D, EL GUERJOUMA R, GUY P, R’MILI M, BABOUX J C, MERLE P. Characterisation of anisotropic elastic constants of continuous alumina fibre reinforced aluminium matrix composite processed by medium pressure infiltration[J]. Composites(Part A), 2000, 31: 45-55.
[11] TURNER P S. Thermal expansion stresses in reinforced plastics[J]. Res Natl Bureau Standard, 1989, 37: 239-245.
Corresponding author: ZHENG Jing; Tel: +86-29-86224473; E-mail: zhengorjing@sina.com
(Edited by YUAN Sai-qian)