Trans. Nonferrous Met. Soc. China 22(2012) s864-s869
Experiments and computer simulation analysis of impact behaviors of micro-sized abrasive in waterjet cutting of thin multiple layered materials
Jung-Han LEE1, Kang-Su PARK1, Myung Chang KANG2, Bo Sik KANG3, Bo Sung SHIN1
1. Engineering Research Center, Pusan National University, Busan 609735, Korea;
2. National Core Research Center, Pusan National University, Busan 609735, Korea;
3. Mechanical System Safety Research Division, Korea Institute of Machinery and Materials, Daejeon 305343, Korea
Received 21 May 2012; accepted 21 September 2012
Abstract: The abrasive waterjet (AWJ) is now widely used in the advanced cutting processes of polymers, metals, glass, ceramics and composite materials like thin multiple-layered material (TMM). Various research and development efforts have recently been made to understand the science of AWJ. However, the interaction mechanism between a workpiece and high-velocity abrasive particles still remains a complicated problem. In this work, the material removal mechanisms of AWJ such as micro penetration and micro dent were experimentally investigated. In addition, a new computer simulation model considering high strain rate effect was proposed to understand the micro impact behavior of high-velocity micro-sized abrasives in AWJ cutting.
Key words: abrasive waterjet; thin multiple layered materials; micro-sized abrasive; micro penetration; micro dent
1 Introduction
Advanced cutting technologies for IT products were thoroughly investigated to achieve the enhancements of performance levels along with the reduction in the size. Such trends are directly related to the development of various printed circuit boards (PCBs) and thin multi-layered flexible printed circuit boards (FPCBs). In the manufacturing of PCB products, die pressing and laser processing are typically used in the conventional manufacturing methods. However, these processes reach their limitations in terms of machining precision. They cannot meet the requirement of the current PCB development due to defects such as the thermal deformation by the photochemical and photomechanical ablation of the thin layered work piece as well as material damage by the mechanical contact of the die with the work piece [1]. To overcome these problems, the process characteristics of abrasive waterjet (AWJ) cutting were tested practically and verified in computer simulations. The AWJ process can cut various materials such as ceramics, glasses, metals and flexible plastics by injecting highly pressurized water containing micro-sized ceramic abrasives through a nozzle. AWJ has a lot of advantages related to its use of water. It does not generate toxic gases in processing of plastic materials; moreover, it is easy to change the cutting path according to NC data with this method. In addition, heat and mechanical deformation do not occur. A new microcutting technology using AWJ was introduced with the development of a nozzle of with a diameter of 0.1 mm and very fine abrasives [2,3]. However, these have been still unsolvable technical problems related to the crucial wear of the internal surface of the nozzle due to the high-velocity ceramic particles. For mass production, the microcutting speed continues to plague this technology [4].
In order to solve such technical limitations, the waterjet cutting characteristics of thin multiple layered materials (TMM) with a type of PCB material consisting of copper and PPG (Glass F/Epoxy) were investigated in this work. The experimental results were also verified and discussed with the numerical analysis using commercial finite element code, LS-DYNA3D. In the case of high speed impact simulation it is very important to consider the strain rate effect. These results will provide a guide to understand impact behavior such as micro penetration and micro dent due to the dispersion of the high-velocity micro-sized abrasives in AWJ cutting.
2 Priciple
In the AWJ cutting process, the velocity of the high-pressure water and abrasives can be obtained by the following equations based on Bernoulli’s equation [5,6]:
(1)
where vW,0 is the velocity of the high-pressure water before passing the orifice; pW is the water pressure (MPa); and ρW denotes the water density (kg/m3). The properties before the acceleration inside the nozzle and those past the nozzle are determined using Eq. (1):

(2)
where mA, mW and mair refer respectively to the mass flow rates of the abrasive, water and air, while vA,0, vW,0 and vair,0 refer respectively to the initial velocities before the acceleration of the abrasive, water and air inside the nozzle. The composition ratios of the density inside the nozzles, water and abrasive 49% respectively while this value for air is 2%; at the instant of the momentum transfer, the properties of the air may be ignored. The initial velocity of the abrasive, vA,0, may be defined as 0 as it is considered not in motion in this equation. Therefore, the abrasive impact velocity accelerated by the high-velocity water vA,1 can be obtained by Eq. (3):
(3)
From the above equation, the change of the high-pressure water velocity by AWJ, vA,0, and the accelerated abrasive velocity vA,1 are calculated and defined, as shown in Fig. 1. They are then compared to the first applied water velocity vW,0, and the abrasive velocity vA,1 is confirmed to be reduced by three to four times. The marked zone of Fig. 1, which ranges from 180-220 MPa, implies the best optimal cutting conditions. Here, these experimental results obtained from the previous study of TMM are also compared with theoretical results [7]. By theoretical calculation, the water velocity is 600-660 m/s and the abrasive velocity is approximately 180 m/s.
3 Experimental
The AWJ system used in this experiment consists of a CNC x-y table, a high pressure pump unit and a CNC controller. It can be operated under a maximum pressure of 410 MPa, a maximum water flow rate of 3.8 L/mm and a maximum cutting feed rate of 15.0 m/min. A schematic diagram of this system is shown in Fig. 2. Purified water is firstly sent into the intensifier pump and then pressured to 410 MPa. The high pressurized water is kept in an accumulator. The abrasives are sucked into the waterjet due to the vacuum pressure generated by the dynamic pressure of the high-speed waterjet in the orifice of the nozzle.

Fig. 1 Velocity changes of waterjet and abrasive particles according to operation pressure

Fig. 2 Schematic diagram of water flow and control sequences of AWJ system
In this work, several cutting experiments were performed on TMM with thickness of 62 and 448 μm as the primary material of a PCB. The composition and structure of this material are shown in Fig. 3. The mechanical properties of each material are listed in Table 1. A nozzle with a diameter of 0.5 mm and a length of 50.2 mm was used; this size showed the best result in terms of cutting precision with TMM. The standoff distance, the cutting feed rate and the cutting pressure were set to 1.0 mm, 1000 mm/min and 200 MPa, respectively. The mesh number of the garnet abrasive was 220 and the overall size ranged from 40 to 80 μm. The physical properties of garnet abrasives are listed in Table 2 and these shapes are shown in Fig. 4.
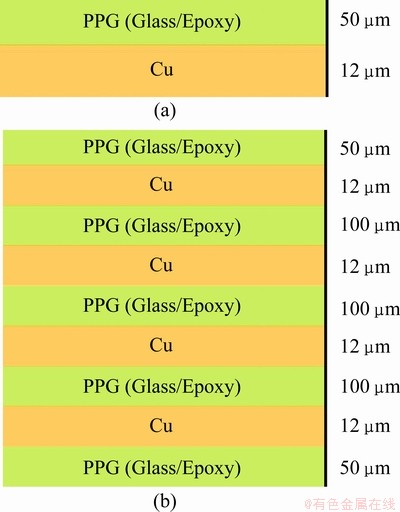
Fig. 3 Composition and structure of TMM with thickness of 62 μm (a) and 448 μm (b)
Table 1 Mechanical properties of TMM
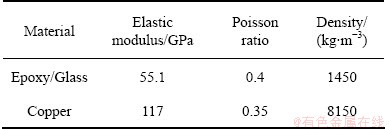
Table 2 Physical properties of garnet abrasives


Fig. 4 Dimensions and shapes of abrasive particles

Fig. 5 Finite element models for micro abrasive penetration (a) and micro dent formation (b)
4 Computer simulation
This AWJ cutting mechanism includes some difficult points in computer simulation, for example, the material and geometrical non-linearity, high strain rate effect, contact with friction, etc. To understand the high-speed abrasive impact process more accurately, a new approach was introduced and compared with and without strain rate effect in AWJ cutting. This model could provide and predict the high-speed abrasive impact phenomena such as micro abrasive penetration, micro dent deformation, and strain and stress distributions. Figure 5 shows the FE model for micro abrasive penetration and micro dent formation simulation, respectively. In general, micro-sized garnet particles are used as the abrasive of AWJ cutting, whose shape is similar to elliptical or irregular as shown in Fig. 4. But, to simply the analysis, the abrasive was perfectly assumed to be a sphere of rigid body. The impact initial velocity of abrasive was 180 m/s. When an abrasive reaches the surface of the workpiece simultaneously, the contact will happen during instant impact time, which is about 4×10-5 s. The hard contact condition was also introduced for this simulation. Here the finite element analysis code, LS-DYNA 3D, was employed for micro-sized particle jetting. The effective plastic stress (σp) of the workpiece should be modified by a scale factor S as shown in Eq. (4):
(4)
where scale factor S will be defined by C and p as given in Eq. (5). Generally, these values are calculated by curve fitting between the flow stress—strain rate relation and Cowper-Symonds relation, in which the temperature of the workpiece is assumed to be 20 °C.
(5)
5 Results and discussion
5.1 Micro penetration
Figure 6 shows the SEM image of the cutting side of the TMM. It is observed that there are a lot of penetration marks machined by micro-sized high velocity abrasives inside the cutting surface. The marked line width is about 30 μm. These marks are purely a result of plastic deformation of ductile material by the penetration of micro abrasives. The abrasive particle impacts vertically on the surface of TMM material with high velocity, which causes material plastic deformation, penetration, and then cutting. To study micro penetration phenomenon in detail, the computer simulation was performed without and with considering the strain rate effect. Figure 7 shows the computer simulation results according to penetration time and the dynamic behavior of the micro-sized garnet abrasives. Total penetration time is about 1×10-6 s. The bur is also observed in the marked areas of both sides where the abrasive particles penetrate trough the TMM workpiece. By comparing with both cases with and without the strain rate effect, the micro penetration width of the case without the strain rate effect is wider than that with the strain rate effect. Actually, the measured penetration width experimentally shows the similar tendency with simulation results of the case considering the strain rate effect. Also the rapid change of strain and stress distributions for the interface with copper and PI of TMM model was found, as shown in Fig. 7(c). It is predicted that the delamination between copper and PI polymer layer will be found in the region where the stress difference is more serious. The simulation results in Figs. 7(c)-(e) show that the case without considering the strain rate effect is more exaggerated than that with the effect. Practically the simulation results of the case with the strain rate effect are more accurate and coincided to experimental results.
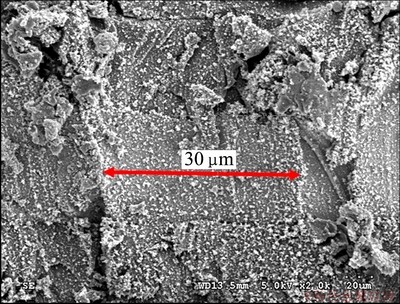
Fig. 6 SEM image of micro-sized abrasive penetration
5.2 Micro dent
The frosting phenomenon of a white color due to the dispersion of the high-velocity micro-sized abrasives can be observed on the cutting surface as shown in Fig. 8. The frosting phenomenon happened when the cutting width of the waterjet was wider than its stabilized region and the high-velocity micro-sized abrasives impacted the outside of the focused area of a workpiece. The end tip of the waterjet was initially injected dispersely as soon as it passed out the focusing nozzle. When the standoff distance from nozzle end tip exceeded optimal value, it was significantly developed more broadly compared to the focusing nozzle width. By carefully inspecting the frosting area, it is observed that there are a lot of micro dents both sides of cutting line. As generally known, the impact of micro abrasive among frosting phenomena is the beginning stage in material removal. It is therefore believed that conventional wear theories for ductile material apply to erosive material removal action in micro dent formation. But it is difficult to describe the micro dent process by the micro garnet particle. In the frosting area there are a lot of micro dents with an average diameter of 20 μm and depth of 5 μm. To understand micro dent formation more than experimentally, the computer simulation was also introduced. Figure 9 shows the computer simulation results according to dent time of approximately 2.0028×10-5 s.
6 Conclusions
From the above results, the impact behavior of the micro-sized abrasive in waterjet cutting of TMM was investigated by experimental observations and computational simulations. First, the velocities of the high-pressure water and abrasive particles according to the operation pressure were determined by theoretical equations. Also, the optimal range of cutting parameters for the TMM was experimentally verified. The optimal pressure condition was found to be 180-220 MPa at this time, the velocity of the abrasive particles is approximately 180 m/s, while that of the water ranges from 600-660 m/s. Second, by surveying the cutting side penetrated by the micro-sized abrasives and the cutting surface with the frosting phenomenon, the shapes, sizes and dimensions of penetration marks and machined micro dents in the AWJ cutting process of the TMM were experimentally investigated. Third, through a FEM computer simulation, it is totally verified that the micro-sized abrasive with high-velocity penetrated through TMM material. It is visually confirmed that the micro dent occurs during AWJ cutting. This is due to the scattering of the high-velocity water and the abrasives on the surface of a workpiece at the initial stage when the water and the abrasive material are mixed. The above results show the potential of the micro-sized AWJ cutting for next-generation very thin PCBs and FPCBs. In the near future, an advanced AWJ system will be developed.
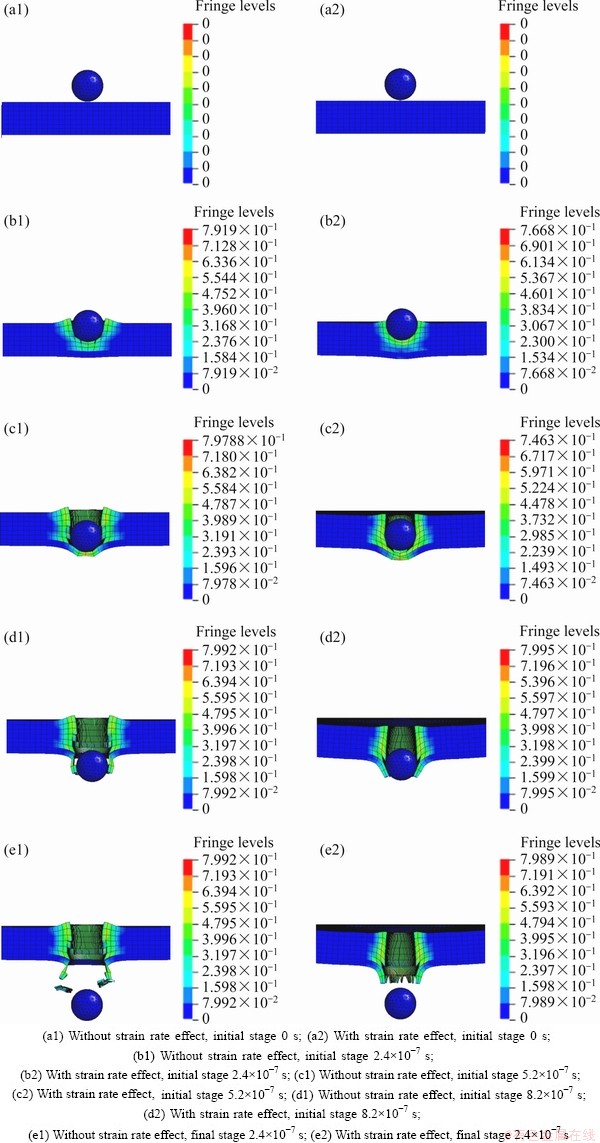
Fig. 7 Simulation results (Contours of effective plastic strain) of penetration behavior of micro-sized abrasive
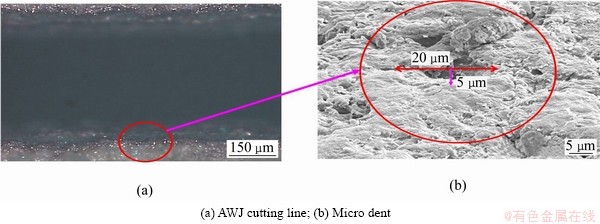
Fig. 8 Experimental SEM images of frosting phenomenon
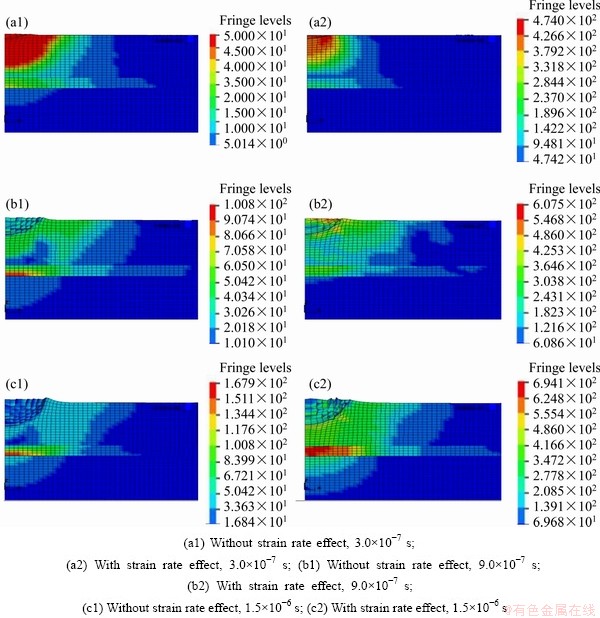
Fig. 9 Simulation results (Contours of effective stress, GPa) of micro dent formation
References
[1] KULECKCI M K. Processes and apparatus developments in industrial waterjet applications [J]. International Journal of Machine Tools and Manufacture, 2002, 42(12): 1297-1306.
[2] BRATTBERG T, CHANSON H. Air entrapment and air bubble dispersion at two dimensional plunging water jets [J]. Chemical Engineering Science, 1998, 53(24): 4127-4133.
[3] MILLER D S. Micromachining with abrasive waterjets [J]. Journal of Materials Processing Technology, 2004, 149: 37-42.
[4] RYAN A, LEWIS H. Manufacturing an environmentally friendly PCB using existing industrial processes and equipment [J]. Robotics and Computer-Integrated Manufacturing, 2007, 23: 720-726.
[5] TAZIBT A, PARSY F, ABRIAK N. Theoretical analysis of the particle acceleration process in abrasive water jet cutting [J]. Comput Mater Sci, 1996, 5: 243-254.
[6] JUKAR M, JURISEVIC B, FAJDIGA M, GRAH M. Finite element analysis of single-particle impact in abrasive water jet machining [J]. International Journal of Impact Engineering, 2006, 32: 1095-1112.
[7] PARK K S, BAHK Y K, GO J S, SHIN B S. A study on the frosting phenomena of abrasive waterjet microcutting for multi-layered materials [J]. Korea Society of Machine Tool Engineers, 2007, 24(4): 183-191.
(Edited by CHEN Wei-ping)
Corresponding author: Bo Sung SHIN; Tel:+82-51-5102787; E-mail: bosung@pusan.ac.kr
DOI: 10.1016/S1003-6326(12)61817-2