Trans. Nonferrous Met. Soc. China 20(2010) s943-s947

Electro-pulse modification and reheating process for production of thixotropic microstructure in AlSi7Mg alloy
TIAN Wen-tong(田文彤)1, ZHANG Guang-an(张广安)2
1. College of Mechanical and Electrical Engineering, Changzhou Institute of Technology, Changzhou 213002, China;
2. College of Material and Chemical Engineering, Liaoning Industrial University, Jinzhou 121001, China
Received 13 July 2010; accepted 25 June 2010
Abstract: Electro-pulse modification (EPM) was used to change the dendritic structure of AlSi7Mg alloy to globular one. The effects of the modified temperature, electro-pulse frequency and time on the solidified structure were examined. The results show that these parameters play an important role in the solidified microstructures. That is to say, under the same modified temperature, the solidified microstructure will be improved greatly with the increase of electro-pulse frequency and time, but when they exceed to limit values, the solidified microstructure will become worse, resulting from the decrease of the ratio of nucleation. The experimental results indicate that the suitable modified temperature of AlSi7Mg alloy is 720 °C, and the appropriate electro-pulse frequency and time are 5 Hz and 40 s, respectively. Then the microstructures produced by suitable EPM process were reheated at temperatures between liquidus and solidus, the primary-Al grains ripen further and become more spherical, which is favorable to the semi-solid forming of AlSi7Mg alloy.
Key words: AlSi7Mg alloy; semi-solid alloy; electro-pulse modification; reheating process
1 Introduction
It has been well known that semi-solid processing has lots of significant advantages over conventional casting, such as minimizing the macro-segregation and solidification shrinkage and reducing the forming temperature. The desired starting material for semi-solid metal forming is a partially solidified alloy in which the solid is present as nearly perfect spheroidal particles. The thixotropic effect of the semisolid alloys allows them to be handled as a massive solid and to attain fluid-like properties when being sheared during shaping[1-3]. Many different routes were used to produce non-dendritic microstructure, such as magnetohydrodynamic (MHD) stirring, spray forming, and SIMA[4-6]. Moreover, the researches conducted during the last few years led to the fundamental discovery that the ideal semi-solid structure could be produced directly from the melt by a controlled nucleation and growth phenomenon[7-8]. Since this method does not need stirring and is simple, practical and inexpensive, it has become more attractive. Using this method, several techniques were developed, including the inclined cooling plate, cooling slope tube, and damper cooling tube methods. These techniques are used by pouring the molten metal over an inclined plate or tube so that the nucleation together with mixing occurs during the flow of the liquid, thereby producing a primary microstructure that is fine-grained and less dendritic[9-10]. However, one of the biggest problems in these techniques is the tendency to form shell on the cooling plate.
Based on this finding, various processes have been invented for production of semi-solid metal slurries during the last few years. However, less work was carried out on semi-solid AlSi7Mg alloy by the electro-pulse modification(EPM) cast and partial remelting process. In the present study, the optimum temperature for EPM was decided by thermal analysis, and experiments were conducted to study the influence of electro-pulse frequency and time at 720 °C. The effects of isothermal holding time and temperature on the microstructures of the alloy were investigated in the partial reheating process.
2 Experimental
Chemical composition of AlSi7Mg alloy used in the current research is listed in Table 1. The thermal analysis of the alloy was carried out, the liquidus and solidus temperatures were determined to be 615 and 564 °C, respectively, and the optimum temperature for EPM was 720 °C.
Table 1 Chemical composition of AlSi7Mg alloy(mass fraction, %)

In order to perform experiments, 1 kg of AlSi7Mg alloy was melted in a silicon carbide crucible located at a resistance furnace. After being treated by EPM under given conditions, the melt was poured into a steel mold to produce in situ AlSi7Mg solidified ingots. Subsequently, the ingot was cut into a series of cubic samples of 12 mm×12 mm×12 mm. The partial remelting process was performed in a vertical tube furnace, the samples were reheated to 590-600 °C and held at the temperature for different times, and then they were quenched in cold water.
Metallographic specimens were polished through standard procedure and the microstructures were examined by using an optical microscope. A 0.5% hydrofluoric acid (HF) aqueous solution was used as the etchant of polishing samples. The grain size and area of the primary solid phase were analyzed statistically by a quantitative analysis system. Circular diameter and shape factor were calculated according to the following equations:
(1)
(2)
where Aα and Pα denote the area and perimeter of α(Al) phase, respectively.
3 Results and discussion
3.1 Effects of electro-pulse frequency and time on solidified microtructures
Fig.1 shows a comparison between microstructures of samples cast into the cylindrical mold without and with the EPM. Columnar dendrites of a(Al) phases with a size of more than 320 μm are observable in Fig.1(a). It is shown in Fig.1(b) that applying the EPM at 720 °C gives rise to the fine and non-dendrite grains, because applying EPM can provide multiple nucleation sites and discourage dendritic growth.
Fig.2 shows the microstructures of cast samples at electro-pulse frequency of 3 Hz. At this frequency, the size of primary a(Al) phase decreases as electro-pulse time increases up to 40 s and then increases obviously with further increase in electro-pulse time to 60 s. Moreover, the effect of EPM on solidified microstructure is significant at this frequency. The relationship between a(Al) size and electro-pulse time is shown in Fig.3.
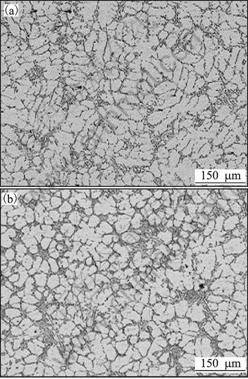
Fig.1 Microstructures of samples with conventional method(a) and EPM method(b)
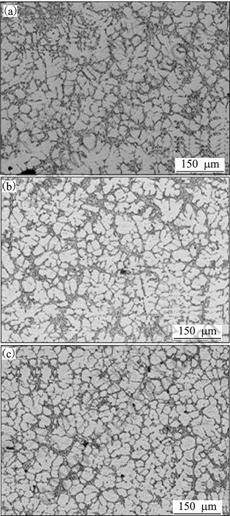
Fig.2 Microstructures of cast samples produced at electro-pulse frequency of 3 Hz and different electro-pulse times: (a) 20 s; (b) 40 s; (c) 60 s
Fig.4 shows the effect of electro-pulse frequency on solidified microstructures at 40 s. A comparison of Figs.4(a) and (b) shows that applying EPM with electro- pulse frequency increasing from 3 to 5 Hz for 40 s leads to finer and more uniform grains in the microstructures. From Figs.4(b) and (c), it can be seen that better refine and globular microstructures cannot be created with further increase of the electro-pulse frequency from 5 to 8 Hz, and the size of a(Al) increases and its shape factor decreases again. The relationship between a-Al size and electro-pulse frequency is shown in Fig.5. Based on the above results, the microstructure, which likes Fig.4(b) is desirable for all solidified samples.
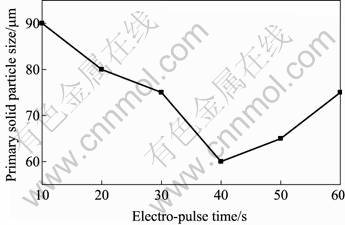
Fig.3 Variation in size of a(Al) phase by applying various electro-pulse time
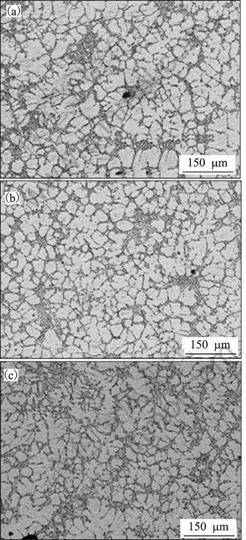
Fig.4 Microstructures of cast samples at electro-pulse time of 40 s and different electro-pulse frequencies: (a) 3 Hz; (b) 5 Hz; (c) 8 Hz
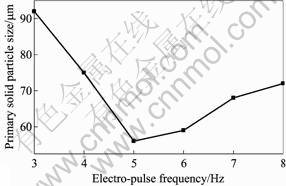
Fig.5 Variation in size of a-Al phase by applying various electro-pulse frequencies
3.2 Effects of reheating parameters on evolution of solidified microstructures
Fig.6 shows the microstructure evolutions of the semi-solid AlSi7Mg alloy isothermally reheated at 590 °C for different times. After isothermally holding for 3 min, almost no liquid phase exists at the grain boundaries. Compared with the original microstructure of solidified samples (Fig.4(b)), the grains grow obviously due to the coalescence of rosette grains, which results in the entrapping of liquid pools in the inner of grains, as shown in Fig.6(a). After isothermally holding for 10 min, small amount of liquid phase appears at the grain boundaries. The grains amalgamate further and grow into equiaxed grains, as shown in Fig.6(b). As the isothermal holding time increases continuously, the liquid fraction continues to increase slowly. The grains keep growing to reduce the surface energy. One growth mechanism is still the coalescence of the adjacent grains, the other growth mechanism is the Ostwald ripening, in which the large grains grow continuously and the small grains remelt gradually. Meanwhile, the grains start to spheroidize due to the Ostwald ripening. After isothermally holding for 30 min, it can be seen from Fig.6(d) that the shape of most grains is near to spherical. However, the grain coarsening is very evident, and the size of which even reaches 80 ?m.
Fig.7 shows the microstructure evolution of the semi-solid AlSi7Mg alloy reheated at 600 °C. It can be seen from Fig.7 that the remelting rate of the semi-solid billet is accelerated obviously. The eutectic phase remelts rapidly and promotes the remelting of solid grain’s periphery, resulting in the rapid increase of liquid phase. After isothermally holding for 5 min, a large amount of liquid phase appears, as shown in Fig.7(a). After isothermally holding for 20 min, the liquid fraction increases further. The grains continue to grow slowly and spheroidize quickly. By comparing Fig.7 with Fig.6, it can also be found that when the isothermal holding time is identical, the grains of semi-solid billet reheated at 600 °C are finer and rounder than those at 590 °C. This can be explained by the theory that accelerating the formation of liquid phase can restrain the coalescence of grains to a certain extent, because the coalescence of grains is the dominant mechanism of grain coarsening during reheating and depends strongly on the extent of adjacent grain connectivity. For example, the higher the liquid fraction is, the sparser the connectivity among adjacent grains is and the harder the coalescence occurs among grains.
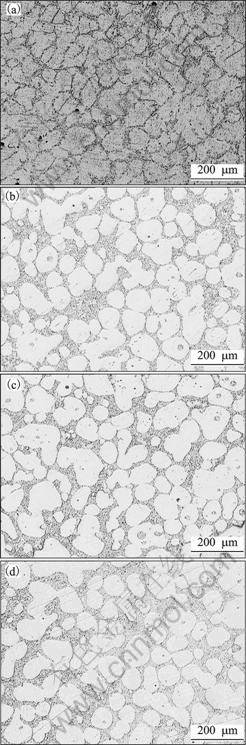
Fig.6 Microstructures of semi-solid AlSi7Mg alloy reheated at 590 °C for different isothermal holding times: (a) 3 min; (b) 10 min; (c) 20 min; (d) 30 min
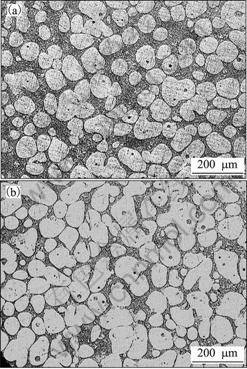
Fig.7 Microstructures of semi-solid AlSi7Mg alloy reheated at 600 °C for different isothermally holding times: (a) 5 min; (b) 20 min
Based on the same theory, the more rapid the liquid phase forms, the earlier the restraining of grain coalescence occurs. It can be seen from Fig.6 that when the semi-solid billet is isothermally reheated at 590 °C, the grains contact tightly to slow the increase of the liquid phase. The coalescence of adjacent grains leads to the rapid growth of grains. Finally, the grain coarsening is very evident. In addition, because the grains contact tightly and stack each other, the grains spheroidize slowly.
4 Conclusions
1) The semi-solid structure of in situ AlSi7Mg alloy is produced by the EPM and partial remelting process.
2) The desirable temperature for EPM is 720 °C. The best refined and globular microstructure of AlSi7Mg is obtained at an electro-pulse time of 40 s and a frequency of 5 Hz.
3) Under the same isothermal holding time, the grains of the semi-solid AlSi7Mg alloy isothermally reheated at 600 °C are finer and rounder than those at 590 °C.
4) Accelerating the formation of liquid phase can restrain the coalescence of grains to a certain extent, thus refining the grain size and promoting the grain spheroidization.
References
[1] HAGA T, KAPRANOS P. Simple rheocasting processes [J]. J Mater Proc Tech, 2002, 130/131: 594-598.
[2] JORSTAD J L. Semisolid metal processing: The high integrity die casting process [J]. Die Casting Engineer, 2004(1): 42-49.
[3] APELIAN D, PAN Q Y, FINDON M. Low cost and energy efficient methods for the manufacture of semi-solid (SSM) feedstock [J]. Die Casting Engineer, 2004 (1): 22-29.
[4] CHANG G W, WANG J Z, XUE Q G. Study on the mechanism of graphitization in molten iron promoted by electro-pulse discharge [J]. Acta Metallurgica Sinica, 2004, 17(6): 790-794.
[5] REISI M, NIROUMAND B. Effects of stirring parameters on rheocast structure of Al-7.1%Si alloy [J]. Journal of Alloys and Compounds, 2009, 470: 413-419.
[6] LASHKARI O, NAFISI S. The effect of partial decanting on the chemical composition of semi-solid hypo-eutectic Al-Si alloys during solidification [J]. Journal of Materials Technology, 2007, 182: 95-100.
[7] ZHAO Jun-wen, WU Shu-sen, XIE Li-zhi. Effects of vibration and grain refiner on microstructure of semisolid slurry of hypoeutectic Al-Si alloy [J]. Trans Nonferrous Met Soc China, 2008, 18: 842-846.
[8] YANG Xiao-rong, MAO Wei-min, PEI Sheng. Influence of process parameters on microstructure of semisolid A356 alloy slug cast through vertical pipe [J]. Trans Nonferrous Met Soc China, 2008, 18: 99-103.
[9] Guo Hong-min, YANG Xiang-jie, ZHANG Meng. Microstructure characteristics and mechanical properties of rheoformed wrought aluminum alloy 2024 [J]. Trans Nonferrous Met Soc China, 2008, 18: 555-561
[10] YANG Xiao-rong, MAO Wei-min. Preparation of semisolid A356 alloy feedstock cast via a pipe consisting of partial inclined and partial vertical sections [J]. J Mater Sci Technol, 2009, 25(2): 273-276.
(Edited by CHEN Wei-ping)
Foundation item: Project(07KJD460007) supported by the Educational Science Foundation of Jiangsu Province, China
Corresponding author: TIAN Wen-tong; Tel: +86-13915830896; E-mail: tian_wentong@163.com