
Barium titanate ceramic inks for continuous ink-jet printing synthesized by mechanical mixing and sol-gel methods
ZHOU Zhen-jun(周振君)1, YANG Zheng-fang(杨正方)2, YUAN Qi-ming(袁启明)2
1. College of Earth Sciences and Resources Management, Chang’an University, Xi’an 710054, China;
2. Institute of Materials Science and Engineering, Tianjin University, Tianjin 300072, China
Received 13 March 2007; accepted 3 September 2007
Abstract: Ink-jet printing of ceramic thick films is one of low cost on-site ceramic pattern fabrication methods. It is necessary to investigate the rheological behaviour of ceramic inks and drying behaviour of droplets. Two kinds of BaTiO3 ceramic inks were prepared by mechanical mixing and sol-gel methods, respectively. The effect of preparation parameters, such as quantity of polyacrylic acid(PAA) and solid content, on physicochemical and rheologic properties of the ceramic inks was investigated. The results show that they satisfy the requirements of continuous ink-jet printing. The appearances of printed dots and single printed layers were observed by SEM. The SEM images indicate that dots printed with mixing method ink are in ring shape, and dots printed with sol-gel method ink are in pancake shape, so the printed layer surface with the latter ink is smoother. The causes of these phenomena were discussed.
Key words: ceramic ink; rheologic properties; barium titanate; sol-gel method; mechanical mixing
1 Introduction
Direct ceramic-ink-jet printing(DCIJP) has been developed for the fabrication of small ceramic components[1-2], thin ceramic walls[3-4], thick ceramic films[5-7] and ceramic microdot arrays[8-9] in recent years. The properties of inks are critical to ensure high quality direct ink-jet printing[10]. Ceramic inks consist of ceramic powder, organic solvents and additives. It is vital that the ceramic powder is well dispersed in the liquid carrier, for the ceramic ink flows through small nozzles (40-100 ?m in diameter) at high speed[11]. Many different methods such as homogeneous precipitation method[12], sol-gel method[13] and microemulsion method[14], were used to prepare ceramic inks. The dot shape, line width and film morphology printed on substrate are affected by the rheological behaviour[15] and drying behaviour[16] of ceramic inks.
In the present work, two kinds of BaTiO3 ceramic inks were made through mechanical mixing and sol-gel methods, respectively, and the effects of parameters such as the amount of dispersant and solid loading on their rheologic properties were reported. The appearance of printed dots and single printed layer was observed by means of SEM. The rheological behaviour and drying behaviour of the two kinds of ceramic inks were explained.
2 Experimental
2.1 Ink formulation
BaTiO3 powder with a median particle size of 0.2 ?m and a specific surface area of 6.5 m2/g was used as raw material for the preparation of BaTiO3 ceramic ink by the mechanical mixing method. BaTiO3 powder was ground with various amounts of dispersant (polypropylene acid, PPA), conductivity salt (ammonium nitrate), and provisional binder (polyvinylbutyral) in deionized water in a conventional ball mill for 36 h. Agate balls with 5 mm in diameter were used for pulverizing the soft agglomerated particles into primary particles. The suspensions were left to settle for over 6 d before decanting the stable supernatant for eliminating the hard agglomerated particles, then the water amount was adjusted to produce inks with desired solid volume fraction for rheologic studies.
The BaTiO3 ceramic inks were prepared by the sol-gel process involving the mixing of titanium isopropoxide and barium acetate in deionized water under continuous stirring at room temperature. The amount of titanium isopropoxide and barium acetate was in a molar ratio of 1?1. Acetic acid, acetylacetone and KOH were used for controlling the hydrolysis rate of titanium alkoxide and the forming rate of BaTiO3. BaTiO3 powders with a median particles size of 50 nm and a specific surface area of 68 m2/g were prepared. In order to avoid precipitation and satisfy the requirements of continuous ink-jet printing, a little amounts of polyacrylic acid, ammonium nitrate and polyvinylbutyral were added.
2.2 Characterization
The sedimentation behavior of the inks was studied to evaluate their stability. Inks were placed into centrifuge tube with scale and then consolidated by centrifugation at 2 000 r/min for 30 min. The height of sediment in each sample was measured as a proportion of their stability. Dynamic rheologic measurements were conducted in a concentric cylinder-type rheometer. The rotor was accelerated from rest at rate of 3 s-1 until 1 000 s-1. The surface tension of each ceramic ink was measured by using a standard dynamic contact angle analyzer. The dc conductivities of the ceramic inks were measured at ambient temperature by a cell that consisted of two brass electrodes and a plastic cylindrical tube.
2.3 Printing of ceramic inks
The printing operation was performed using a Cannon PJ-1080A Color Ink-Jet Printer. This printer used piezoelectric technology to squirt ink droplets from a nozzle with 65 ?m opening. Pneumatic air (0.2-0.3 MPa) was used to pump the ink to the nozzle. In order to observe single dots, the resolution was chosen as 100×72 dpi. For preparing uniform layer, there must be sufficient overlap among dots, so the resolution was increased to 200×216 dpi.
3 Results and discussion
3.1 Dispersion of powder
Fig.1 shows the effects of PAA content on the stability of the ceramic inks. At low PAA content, the stability of inks tends to increase with the increasing of the content of PAA. This result implies that PAA molecules are adsorbed on the particles surfaces and prevent agglomeration. The van der Waals interaction between the particles is decreased by the adsorbed layer of dispersants, which are long chain polymeric molecules. This can attribute both to the fact that the layer of stabilizer keeps the particles apart, thus increasing the distance between the centers of particles, and to the modification of the intensity of attractive interaction between two particles caused by the presence of the shell of adsorbed dispersant molecules. The optimum content of PAA is to achieve complete monolayer coverage. However, as the PAA content become higher, the stability of inks gradually decreases, because the excess dispersant molecules present in the liquid phase. By comparing the stability of two kinds of inks with the same solid content, inks made by sol-gel method have better stability, because BaTiO3 particles in this kind of inks are small and round, and BaTiO3 particles in the inks made by mechanical mixing method are irregular and angular.
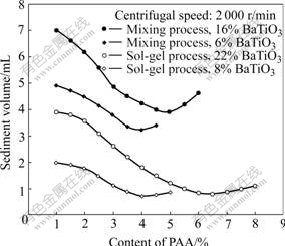
Fig.1 Effect of content of PAA on stability of BaTiO3 ceramic inks
3.2 Rheologic properties
The rheologic properties of ceramic inks are influenced by the solid content and the characteristics of the solid particles, as well as the composition and chemical nature of the solvent itself.
The plots of viscosity versus shear rate and ceramic content are shown in Fig.2 and Fig.3. It is seen from Fig.2 that the viscosities increase with increasing solid content, and the viscosities of inks synthesized by sol-gel method are considerably lower than those made by mixing method at the same solid content. As seen in Fig.3, higher solid contents (≥22% (volume fraction) for sol-gel method, ≥16% for mixing method) and comparable shear rates, yield shear thinning because of the break down of structures (created by interparticle forces) and orientation effects in the flow direction.
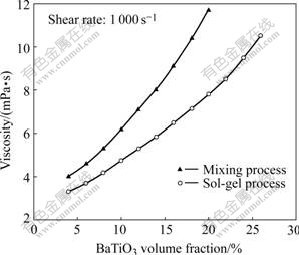
Fig.2 Viscosity of ceramic inks as function of oxide volume fraction
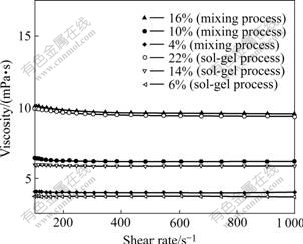
Fig.3 Rheologic property of ceramic inks at different volume fraction of BaTiO3
3.3 Printing trials
Two kinds of inks decanted after 12 h of sedimentation were used in printing trials. Fig.4 shows SEM appearance of a single printed dot and scans for Ba along line denoted in SEM image. From Fig.4(a), the dot with ink made by mixing method is in ring shape. The line scan of Ba confirms that there is a high concentra- tion of Ba in the edge region. A micro-fluid-flow has been proposed to explain the formation of ring-shaped “coffee stain”. When the drop of ink dries on the surface with a pinned contact line, such a flow takes place in order to compensate the difference in the volume change and evaporation rate across the droplet, as illustrated in Fig.5. In the edge region of the drop, the evaporation rate of solvent is high, but the volume change is restricted with the pinned connect line. In the center region, however, a larger volume change happens instead of the lower evaporation rate. The radial micro-fluid-flow supplies the ink to the edge region from center to compensate this difference. The BaTiO3 powders in ink are carried by the flow from the center to the edge, and deposit there. As a result, there is an enhanced deposition of the BaTiO3 powder in the edge region and thinner layer is formed in the center region.
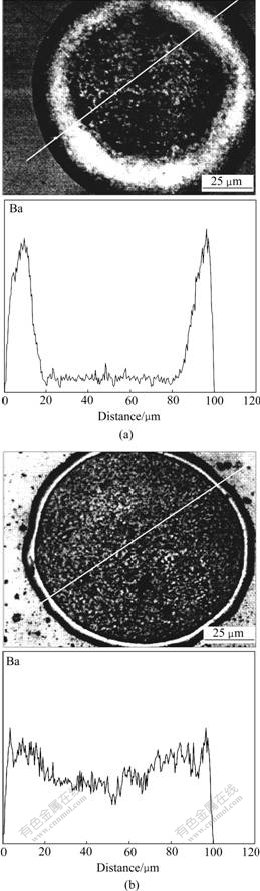
Fig.4 SEM appearance of single printed dot and scan for Ba along line denoted in SEM image: (a) Ink made by mixing process; (b) Ink made by sol-gel process
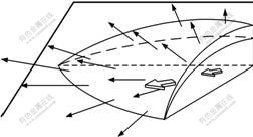
Fig.5 Schematic illustration of internal micro-flow in drying of ink made by mixing method
From Fig.4(b), the dot with ink made by sol-gel method is in pancake shape. The line scan of Ba confirms that the concentration of Ba in whole dot is uniform. When the solvent of ink evaporates, the gel structures form in whole dot, which restrains a micro- fluid-flow in the dot.
When direct ceramic-ink-jet printing is used to produce coating, the top surface single layer printing comes into consideration. Fig.6 shows the micrographs of single layer printed by the two kinds of inks. In the single layer, all dots overlap with their neighboring dots. As expected, the top surface of single layer printed with mixing process ink generates strips which are thick in the middle and thin in the ends of printing line. While the top surface of single layer printed with sol-gel process ink produces thin coating of uniform thickness.
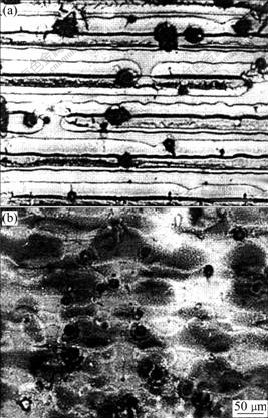
Fig.6 SEM micrographs of single layer print: (a) Ink made by mixing process; (b) Ink made by sol-gel process
4 Conclusions
1) Sol-gel route and mechanical mixing method were used to prepare jet printing inks, respectively. The inks can be subjected to reliable registration for long periods. An available dispersant was used to optimize the sediment packing density and viscosity of a ceramic ink developed for use in the production of ceramic layer direct jet printing. The optimum addition of 4%-7% of dispersant corresponds to the highest adsorption level on the powder, the maximum sediment-packing efficiency, and the minimum ink viscosity.
2) The image of dot printed with mixing method ink is in ring shape, and the image of dot printed with sol-gel method ink is in pancake shape. The top surface of single layer printed with mixing process ink generates strips, while the top surface of single layer printed with sol-gel process ink produces thin coating of uniform thickness.
References
[1] SMITH P, DERBY B, REIS N, WALLWORK A, AINSLEY C. Measured anisotropy of alumina components produced by direct ink-jet printing [J]. Key Engineering Materials, 2004, 264/268(1): 693-696.
[2] DEBEDA-HICKEL H, LUCAT C, MENIL F. Influence of the densification parameters on screen-printed component properties [J]. Journal of the European Ceramic Society, 2005, 25(12): 2115-2119.
[3] ZHAO X L, EVENS J R G, EDIRISINGHE M J. Direct ink-jet printing of vertical walls [J]. Journal of the American Ceramic Society, 2002, 85(8): 2113-2115.
[4] WANG D Z, EDIRISINGHE M J, JAYASINGHE S N. Solid freeform fabrication of thin-walled ceramic structures using an electrohydrodynamic jet [J]. Journal of the American Ceramic Society, 2006, 89(5): 1727-1729.
[5] MATSUO A, GALLAGE R, FUJIWARA T, WATANABE T, YOSHIMURA M. On-site fabrication of ceramics films from solution precursors by ink-jet and spray assisted processes [J]. Journal of Electroceramics, 2006, 16(4): 533-536.
[6] GENTIL S, DAMJANOVIC D, SETTER N. Pb(Mg1/3Nb2/3)O3 and (1-x)Pb(Mg1/3Nb2/3)O3-xPbTiO3 relaxor ferroelectric thick films: Processing and electrical characterization [J]. Journal of Electroceramics, 2004, 12(3): 151-161.
[7] SAKAI Y, FUTAKUCHI T, IIJIMA T. Preparation of (Ba,Sr)TiO3 thick film on ZrO2 substrates by inkjet printing [J]. Japanese Journal of Applied Physics, 2006, 45(2): 846-849.
[8] MOUGENOT M, LEJEUNE M, BAUMARD J F, BOISSIERE C, RIBOT F, GROSSO D, SANCHEZ C, NOGUERA R. Ink jet printing of microdot arrays of mesostructured silica [J]. Journal of the American Ceramic Society, 2006, 89(6): 1876-1882.
[9] ZHAO X, EVANS J R G, EDIRISINGHE M J, SONG J H. Formulation of a ceramic ink for a wide-array drop-on-demand ink-jet printer [J]. Ceramics International, 2003, 29(8): 887-892.
[10] PRASAD P S R, REDDY A, RAJESH P K, PONNAMBALAM P, PRAKASAN K. Studies on rheology of ceramic inks and spread of ink droplets for direct ceramic ink jet printing [J]. Journal of Materials Processing Technology, 2006, 176(1/3): 222-229.
[11] SAFARI A, ALLAHYERDI M, AKDOGAN E K. Solid freeform fabrication of piezoelectric sensors and actuators [J]. Journal of Materials Science, 2006, 41(1): 177-198.
[12] KWON Y, KIM Y, KIM D. Synthesis and characterization of near-monodisperse yttria particles by homogeneous precipitation method [J]. Powder Technology, 2004, 142(2/3): 136-153.
[13] VIRICELLE J P, RIVIERE B, PIJOLAT C. Optimization of SnO2 screen-printing inks for gas sensor applications [J]. Journal of the European Ceramic Society, 2005, 25(12): 2137-2140.
[14] GUO R S, QI H T, YANG Z F, CHEN Y R. Preparation and properties of the AEO9/alcohol/alkane/water reverse microemulsion ceramic inks [J]. Ceramic International, 2004, 30(8): 2259-2267.
[15] VON D P, BARNETT S. A study of screen printed yttria-stabilized zirconia layers for solid oxide fuel cells [J]. Journal of the American Ceramic Society, 2005, 88(12): 3361-3368.
[16] WANG J, EVANS J R G. Drying behaviour of droplets of mixed powder suspensions [J]. Journal of the European Ceramic Society, 2006, 26(15): 3123-3131.
Foundation item: Project(106151) supported by the Major Program of the Ministry of Education of China; Project(59842001) supported by the National Natural Science Foundation of China
Corresponding author: ZHOU Zhen-jun; Tel: +86-29-82339086; E-mail: zhenjunz@chd.edu.cn
(Edited by YUAN Sai-qian)