
Fabrication and test of reaction bond silicon carbide for optical applications
YAO Wang(姚 旺), ZHANG Yu-min(张宇民), HAN Jie-cai(韩杰才), ZUO Hong-bo(左洪波)
Center for Composite Materials, Harbin Institute of Technology, Harbin 150001, China
Received 21 March 2005; accepted 8 November 2005
Abstract: A reaction bonding fabrication process using various grain size of SiC powder was investigated. The properties such as mechanical, thermal and physic property were tested and analyzed. RBSiC produced using this process is a polycrystalline material and has high specific stiffness (density of 3.09 g/cm3 with elastic modulus of 362.39 GPa), strength (269.64 MPa) and hardness (19.43 GPa). At room temperature its low CTE (3.47×10-6/K), combined with relatively high thermal conductivity (161.14 W/mK) and specific heat capacity (593.86 J/kg?K) can minimize the bothersome thermal distortion. This advantage is outstanding even at higher temperature of test range. Two d 250 mm RBSiC mirror were polished. Surface roughness value less than 5 nm was obtained. Results prove that this reaction bonding process is a feasible method to produced high quality RBSiC optical mirror.
Key words: RBSiC; silicon carbide; fabrication; optical applications; polishability; property measurement
1 Introduction
Silicon carbide may be the best material available for mirror optics because of its outstanding combination of thermal and mechanical properties[1-3]. This material has remarkable dimensional stability even under the disturbances of temperature, humidity and chemicals. Its specific stiffness and elastic modulus are higher than that of beryllium, which has toxicity. The density of SiC is slightly higher than aluminum and its fracture toughness higher than glass. The lower thermal expansion and higher thermal conductivity of SiC promote its use for cryogenic infrared optics[4].
Reaction bonded silicon carbide (RBSiC) is a two phase material consisting of SiC and pure Si[5]. The advantages of property and fabrication process make RBSiC the most attractive material than other forms of SiC and optical glass[6, 7]. Because Si and SiC have different removal rates, limitation of fabrication process now makes it difficult to obtain a dense body and super polished surface of RBSiC for optical applications. ROGER et al[8] obtained 7.5±3.2 ? RMS on small diameter RBSiC samples (15% Si content). EALEY et al[9-11] investigated microstructure of RBSiC and created a CERAFORM SiC that can be polished directly to 7 ? RMS at 1 000 times magnification needless additional easy to polished cladding. But they still can not obtain the same surface quality on machining of large diameter CERAFORM SiC mirrors. In China, study of RBSiC as optical mirror is still on its beginning. Cost of fabrication and machining are the main obstacles to study and use of RBSiC. No super polished RBSiC mirror has been reported.
The objective of this paper is to evaluate a reaction bonding fabrication process of SiC. Firstly, the fabrication process of RBSiC was presented. Secondly, the physical, thermal and mechanical properties and polishability were investigated.
2 Fabrication of basic samples
Carbon and SiC particles were mixed with distilled water and dispersant to a colloidal suspension. The suspension was poured into a near net shape gypsum mold under vibration and vacuum environment. After drying, the green body with silicon powder on it was put into sintering furnace. Heating velocity of furnace increases slowly below 500℃ in order to remove organic dispersant. Above 1 410 ℃, molting silicon began to infiltrate into the green body and reacted with free carbon to form new SiC phase replacing original carbon grains. Residual pores were filled with excessive silicon. If size of pores was smaller than wavelength,pores can be ignored. With accumulation of experience, products can be got with less and smaller pores. In order to control the microstructure of product and to polish it directly, two grain size distributions of SiC powder were tailored and other process parameters such as heating velocity were controlled strictly. The samples were cut from the same RBSiC produced by electrospark wire-electrode cutting firstly and then polished using diamond slurries to roughness value 0.63 mm.
3 Property measurement
3.1 Chemical and physical properties
The microstructure of RBSiC was evaluated using X-ray diffraction and optical microscopy.
The density was measured at room temperature using Archimedes immersion technique. The size of RBSiC samples is 50 mm×4.88 mm×3.56 mm.
3.2 Thermal properties
The size of samples for thermal properties measurement was d 12.5 mm×27.6 mm.
The coefficient of thermal expansion(CTE) was measured using Anter UNITHERM? 1252 Thermal Expansion System over the temperature range 273 K to 1 273 K.
The specific heat capacity and thermal diffusivity of samples were determined using Anter FLASHLINE? 5000 Thermal Diffusivity System over the temperature range of 444 K to 1 096 K.
The thermal conductivity (l) was related to the diffusivity (a) by Eqn.(1)[12]:
λ=αρcp (1)
where r is the density and cp is the specific heat capacity of the material. Assume the density of RBSiC changes little over the temperature range 444 K to 1 096 K. Eqn.(1) can be used to calculate thermal conductivity when values of r, a and cp are available.
3.3 Mechanical properties
A cylindrical sample (d 12.5 mm×20.0 mm, roughness value 0.63 mm) was tested on Zwick1 (100 kN) Testing Instrument using strain gage technique to determine elastic modulus and Poisson’ ratio. The lateral and longitudinal strains of every sample at compressive stress were recorded using Strain Gage Tester (YE2537, Yang Zhou, China). The elastic modulus was calculated from stress and strains.
The flexural strength was measured on Instron-5569 Universal Test Machine using a three point flexure test (two bottom points distance of 30 mm) at room temperature. The sample’s size was 50 mm×4.88 mm×3.56 mm, roughness value 0.63 mm. The fractured samples were collected and then used to test hardness and K1C.
The Vickers and Rockwell hardness were measured respectively using Vickers hardness tester (HVS-5) and Rockwell hardness tester (HRD-150). At Rockwell hardness test the initial load was set to 98 N and total load was set to 490 N. At Vickers hardness test the load was set to 19.6 N.
The measurement of K1C used Vickers indentation micro-fracture technique[13-15]. The polished surfaces were indented with a Vickers diamond indenter at load (P) of 19.6 N. The indentation crack lengths (c) were measured using optical microscope at 400 times magnifications. The indentation K1C was calculated by applying the formula[16] selected based on the pyramidal indenter with half angle 68?:
K1C=0.014·(E/HV) 1/2·P/(c) 3/2
4 Results and discussions
4.1 Chemical and physical properties
The X-ray diffraction pattern is shown in Fig.1. As shown in Fig.1, RBSiC has great ratio in hexagonal structure (6H), which belongs to a-SiC crystal, is mostly oriented in (110), (102), (103) and (116) plane. So the diffraction peaks are identified as a-SiC and Si, respectively.
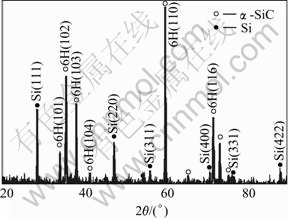
Fig.1 XRD pattern of RBSiC
The diffraction spectroscopy indicates that RBSiC composes of randomly oriented a-SiC and Si, which is polycrystalline material. Typical optical micrograph of polished RBSiC surface is shown in Fig.2.
From Fig.2 it can be seen the bright area is Si and the dark area is SiC. There are residual pores at boundary of Si and SiC, their length is approximately 3 mm or less. With improvement of fabrication process it can reduce pores in size and number to satisfy requirements of applications at a certain extent.
The density of RBSiC is average 3.09±0.01 g/cm3, and its volume percent of Si calculated using mixed law is 13% (ρsintered, SiC = 3.16 g/cm3, ρSi = 2.33 g/cm3).
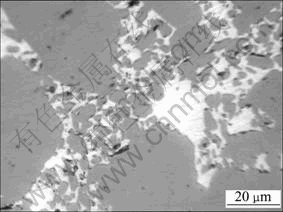
Fig.2 Typical optical micrograph of polished surface
4.2 Thermal properties
The CTE measurement results are shown in Fig.3. Note that the expansion nearly linearly increases with the increase of temperature over the temperature range tested. This means the expansion of RBSiC is symmetrical. No turning in the curve means that no phase transformation occurs.
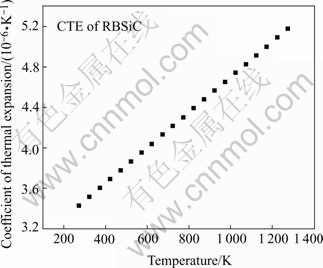
Fig.3 Coefficient of thermal expansion plotted vs temperature (Solid line drawn through points is linearly fit to data according to empirical formula.)
The measurement results of specific heat capacity are shown in Fig.4.
The solid line is an empirical formula form fitting to the data. Note that the specific heat capacity reaches a maximum and keeps unchanged at 1 000 K. This can be explained using Debye heat capacity law[17] that at a certain temperature heat capacity tends to a constant, while under this temperature the heat capacity proportions to T3. The relationship between specific heat capacity and temperature fitted based on empirical formula form is
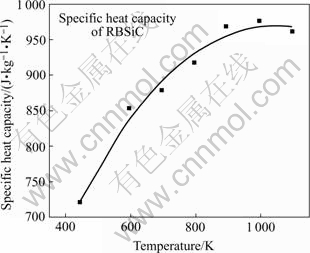
Fig.4 Specific heat capacity of Si/SiC material as function of temperature (Solid line is an empirical formula fitting to data.)
The thermal diffusivity results are shown in Fig.5. It can be seen that the thermal diffusivity decreases as the temperature increases from 444 K to 1 096 K. This means the increase of temperature leads to weaken the ability of diffusivity of heat inside material.
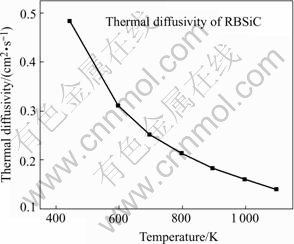
Fig.5 Thermal diffusivity of Si/SiC material as function of temperature
The calculated thermal conductivity plotted as a function of temperature is shown in Fig.6. The solid line is an empirical formula fitting to the data.
With the increase of temperature the heat conductivity decreases. This is because in low temperature range heat conductivity depends on phonon heat conductivity, which decreases with the increase of temperature. After Debye temperature, with increase of temperature, cp tends to a constant, so heat conductivity gets to gentle.
Its relatively low CTE combined with relatively high thermal conductivity and specific heat capacity make RBSiC stand out for minimum thermal distortion.
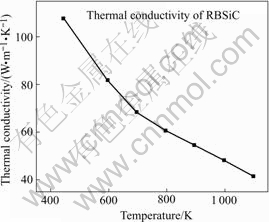
Fig.6 Thermal conductivity of Si/SiC material as function of temperature(Solid line is empirical formula fitting to data.)
4.3 Mechanical properties
The results of elastic modulus and Poisson’s ratio are listed in Table 1. With density of 3.09 g/cm3 specific stiffness of RBSiC is higher, which is the most important factor to reduce cost.
Table 1 Elastic modulus and Poisson’ ratio of RBSiC

The flexural strength and the standard deviation are listed in Table 2.
Table 2 Flexural strength of RBSiC
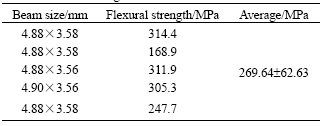
The hardness values presented with the standard deviation are listed in Table 3.
Table 3 Hardness of RBSiC
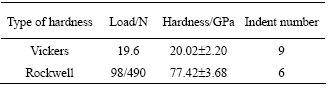
The average indentation fracture toughness, K1C, given with standard deviation is listed in Table 4.
Its high bend strength (269.64 MPa) allows it to light mass. The higher hardness (HV=20.02 GPa) which is the biggest disadvantage makes it difficult to machine super smooth surface.
Table 4 Fracture toughness of RBSiC

5 Polishability of RBSiC
Two polished experimental mirrors have circular shape, one is spherical surface mirror (Mirror-1) and the other is flat (Mirror-2). They all have diameter of 250 mm, face plate and rib thickness of 4mm and total thickness of 30 mm with light mass hexagonal cell on back. Two mirrors were coarsely ground, finely ground and polished in turn using diamond grits. Surface roughness was assessed using Wyko interferometer.
After polishing, below 5 nm Ra surface can be got on both mirrors[18]. The AFM micrographs of polished surfaces are shown in Figs.7 and 8.
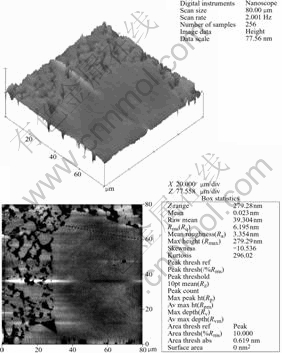
Fig.7 AFM micrographs of spherical mirror(mirror-1)
6 Conclusions
RBSiC is polycrystalline material consisting of a-SiC and pure Si. It has higher specific stiffness. Its relatively low CTE, combined with relatively high thermal conductivity and specific heat capacity make it stand out for minimum thermal distortion. Because hardness of RBSiC is an obstacle to polish to super smooth surface, methods such as using easy to polishing cladding or optimizing micro-structure have been created to resolve it. The surface quality of d 250 mm mirror can be polished to less than roughness value 5 nm.
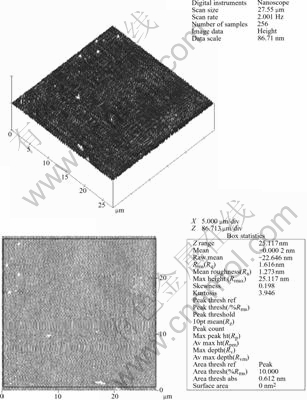
Fig.8 AFM micrograph of spherical mirror(mirror-2)
Investigations of improving fabrication process for obtaining higher polishability and better properties material are undergoing. Although it is difficult to super-polish a two-phase material to a roughness of below 1 nm RMS, by adjusting size distributions of SiC grains and controlling slurry and other process parameters it is believed better surface quality can be achieved on RBSiC.
References
[1] Shih C J, Ezis A. Application of hot-pressed silicon carbide to large high-precision optical structures[A]. EALEY M A. Silicon Carbide Materials for Optics and Precision Structure[C]. Clifornia: SPIE, 1995. 24-37.
[2] Robichaud J. SiC optics for EUV, UV, and visible space missions[A]. BLADES J C, SIEGMUND O H. Future EUV/UV and Visible Space Astrophysics Missions and Instrumentation[C]. SPIE, 2003. 39-49.
[3] Citterio O, Campana S, Conconi P, MAZZILENI F. Silicon carbide( SiC) mirrors for lightweight X-ray optics[A]. HOOVER R B. X-ray Optics, Intruments, and Missions[C]. California: SPIE, 1998. 393-403.
[4] Tobin E, Magida M, Kishner s, Krim m. Design, fabrication and test of a meter-class reaction bonded SiC mirror blank[A]. EALEY M A. Silicon Carbide Materials for Optics and Precision Structures[C]. Clifornia: SPIE, 1995. 12-21.
[5] Ealey M A. Fully active telescope[A]. MACEWEN H A. UV/Optical/IR Space Telescopes: Innovative Technologies and Concepts[C]. Belingham, WA: SPIE, 2004. 19-26.
[6] Johnson S. SiC coating on RBSiC mirror for ultra-smooth surfaces[A]. WILKERSON G W. Rassive Materials for Optical Elements II[C]. SPIE, 1993. 237-247.
[7] LIN Y, Vancoille E Y J, Lee L C. High-quality grinding of polycrystalline silicon carbide spherical surfaces[J]. Wear, 2004, 256: 197-207.
[8] Paquin R A, Magida M B, Vernold C L. Large optics form silicon carbide[A]. PARKS R E. Large Optics II[C]. SPIE, 1992. 53-56.
[9] Ealey M A, Weaver G Q, KIM Y W. Developmental history and trends for reaction bonded silicon carbide[A]. EALEY M A. Advanced Materials for Optical and Precision Structures[C]. SPIE, 1996. 66-72.
[10] Ealey M A, Wellman J A. Ultralightweight silicon carbide mirror design[A]. EALEY M A. Advanced Materials for Optical and Precision Structure[C]. SPIE, 1996. 73-77.
[11] Ealey M A, Wellman J A. Polishability of ceraform silicon carbide[A]. EALEY M A. SPIE, Advanced Materials for Optical and Precision Structures[C]. SPIE, 1996. 81-85.
[12] Pickering m a, Taylor r I, Keeley j t. Chemically vapor deposited silicon carbide(SiC) for optical applications[A]. HALE R R. Space Optical Materials and Space Qualification of Optics[C]. SPIE, 1989. 2-12.
[13] ZHAN Guo-dong, XIE Rong-jun, Mitomo M. Effect of b to a phase transformation on the microstructural development and mechanical properties of fine-grained silicon carbide ceramics[J]. J Am Ceram Soc, 2001, 84(5): 945-950.
[14] Denry I L, Holloway J A. Elastic constants, Vickers hardness, and fracture toughness of fluorrichterite-based glass-ceramics[J]. Dental Materials, 2004, 20: 213-219.
[15] GONG Jiang-hong. Determining indentation toughness by incorporating true hardness into fracture mechanics equations[J]. J Euro Ceram Soc, 1999, 19: 1585-1592.
[16] Roberto D M. A simplified approach for ceramic fracture toughness evaluation by indentation [J]. Engineering Fracture Mechanics, 1995, 51(2): 209-215.
[17] ZHEN Ze-guan. Physical Properties of Inorganic Materials[M]. Beijing: Tsinghua University Press, 1992.
[18] ZHANG Yu-min, ZHANG Jian-han, HAN Jie-cai. Large-scale fabrication of lightweight Si/SiC ceramic composite optical mirror[J]. Materials Letters, 2004, 58: 1204-1208.
Foundation item: Project(90205034) supported by the National Natural Science Foundation of China
Corresponding author: YAO Wang; Tel: +86-451-86412236; E-mail: yaowang21th@163.com
(Edited by LI Xiang-qun)