J. Cent. South Univ. Technol. (2008) 15: 165-169
DOI: 10.1007/s11771-008-0032-9

Thermal residual stress analysis of diamond coating on graded cemented carbides
HUANG Zi-qian(黄自谦)1, HE Yue-hui(贺跃辉)1, CAI Hai-tao(蔡海涛)2,
WU Cong-hai(武从海)3 , XIAO Yi-feng(肖逸锋)1, HUANG Bai-yun(黄伯云)1
(1. State Key Laboratory of Powder Metallurgy, Central South University, Changsha 410083, China;
2. School of Mathematical Science and Computing Technology, Central South University, Changsha 410083, China;
3. College of Science, Henan University of Science and Technology, Luoyang 471003, China)
Abstract: Finite element model was developed to analyze thermal residual stress distribution of diamond coating on graded and homogeneous substrates. Graded cemented carbides were formed by carburizing pretreatment to reduce the cobalt content in the surface layer and improve adhesion of diamond coating. The numerical calculation results show that the surface compressive stress of diamond coating is 950 MPa for graded substrate and 1 250 MPa for homogenous substrate, the thermal residual stress decreases by around 24% due to diamond coating. Carburizing pretreatment is good for diamond nucleation rate, and can increase the interface strength between diamond coating and substrate.
Key words: graded cemented carbides; diamond coating; finite element method; carburizing
1 Introduction
Diamond films are of significant interest for cutting tools applications, such as rotary drills and inserts due to their excellent physical and chemical properties. The deposition of high quality diamond on substrates such as cemented carbides, stainless steel and various metal alloys containing transition elements presents a considerable challenge due to its poor adhesion and low nucleation density[1-5]. Chemical vapor deposition(CVD) of diamond coating has the potential to prolong the lifetime of WC-Co cutting tools when applied to the machining of highly abrasive non-ferrous metallic alloys, composite and ceramic materials. However, the presence of cobalt (Co) binder in the cemented carbide substrate, typically at levels of 6%-10%, has a detrimental influence on the deposition process. Bind materials such as Co can inhibit growth of diamond, which helps the formation of non-diamond carbon phases, i.e. graphitic deposits with poor adhesion[6]. A high Co content in the matrix has been reported to be the main cause of poor adhesion[7]. To improve adhesion, a chemical treatment using Murakami agent and acid etching has been used to successfully remove the Co binder from the substrate surface[8].
In 1980s and 1990s, a new material, described as the most significant innovation in the history of cemented carbides since 1950s, was introduced [9-11]. The patented dual-phase(DP) technology permits an independent increase in the wear resistance and the toughness of cemented carbides, furthermore, a simultaneous increase in both properties. The DP materials were achieved by changing the distribution of the cobalt within the alloy body, i.e. the formation of a cobalt-gradient structure. There are a surface layer with a low cobalt content of around 3% (mass fraction) to provide a high wear resistance required to penetrate rocks, a middle layer with a cobalt content of around 10% to give cemented carbide high toughness, and a core with a cobalt content of around 6% to provide a balance of properties. This graded structure has a hardness distribution across the alloy body with high hardness in the outside and the core, and falling one in the middle, cobalt-rich zone. The DP graded cemented carbides show an increase of 40% in the service lifetime, compared with conventional cemented carbides. Furthermore, substrate denitrification was used to increase the interface strength[12-13].
In this study, cobalt graded structure in the substrate was formed by carburization to reduce the cobalt content in the surface layer of cemented carbides. The variation of interface strength was analyzed by finite element method. In the substrate, the constitutive response to continuous and smooth variation of material properties was developed with constraint factor. Material parameters were continuous and smooth functions of constituent volume fraction of spatial position.
2 Carburizing pretreatment of substrate
The WC-10Co samples with a total carbon content of 5.27% were prepared by conventional powder metallurgy(PM), and then carburized at temperature ranging from 1 420 to 1 460 ℃ for different times in a pure H2 atmosphere. The sectional micrograph was analyzed by scanning electron microscopy(SEM) and the cobalt concentration gradient was analyzed by electron-probe microanalysis(EPMA). Fig.1 shows the three-layered structure of the cemented carbide after the carburization. In the backscattered-electron image, the outer layer and the inner layer are much brighter than the middle layer, in which a Co-rich region is indicated. From Ref.[14], the microstructure of the presintered sample is mainly composed of WC, γ, and η phase. η phase is formed only when the total carbon content of the alloy is below the equilibrium level. In the surface layer, the microstructure is WC-rich, without η phase. The middle layer is Co-rich, also without η phase. The microstructure of the core is almost the same as that of the as-presintered sample.
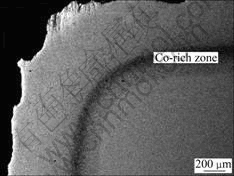
Fig.1 Backscattered-electron image (BSE-SEM) of cemented carbide after being treated at 1 420 ℃ for 80 min
According to the results above, the cobalt content in surface layer decreases to around 3%, which is the ideal concentration for diamond nucleation. In Ref.[15], it was confirmed that on cemented carbide substrate with Co contents ranging from 3% to 8%, high quality adherent diamond coatings can be deposited. As long as the cobalt content is less than 13%, the cobalt content in surface layer can be decreased to less than 8%, high quality diamond coatings can be deposited by carburizing pretreatment.
3 Finite element simulation
3.1 Numerical formulation and material model
A finite element geometric model (Fig.2) for continuous and smooth spatial variation in the composition and properties of substrate materials was built up. The axisymmetric small strain problem of gradient cylinders was considered in the model. The cobalt gradient is near the surface zone of the substrate. The model is available in the MSC. Marc2005 software. In the axisymmetric calculation, a cylindrical coordinate system (r, θ, z) is introduced and calculation results are independent of θ. The dimension of the cylinder is 0≤r≤R, 0≤z≤L, and the ratio of L to R is 3/2. Free boundary condition is assumed for the top edge, the displacement z at the left edge was fixed and the displacement z at the right edge was the same.
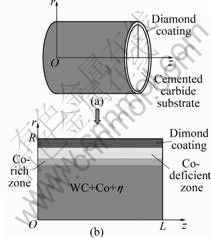
Fig.2 Models for diamond coating on graded cemented carbide: (a) 3D model; (b) Axisymmetric 2D model
For the substrate, the effective values of the thermal expansion coefficient, α, and Poisson ratio, ν, of the compositionally graded solid cylinder were computed from a volume fraction-based interpolation.
(1)
where φi is the volume fraction of material i (0≤φ1, φ2≤1), subscripts 1 and 2 refer to cobalt and tungsten carbide, respectively. Here the isotropic properties of two phases are assumed. The approximate character of the serial rule of mixture in equations is obvious. The effects of internal constraints on the composite at the level of the microstructure are not taken into account. Detailed knowledge of the microstructure is required if a more advanced rule of mixture is to be employed. The present analyses provide first order results for the effect of compositional variations on the overall thermo- mechanical response of graded materials.
The composite stress-strain curves were modeled by using the intermediate law of mixture, as originally shown for cemented carbide by TAMURA et al[16] and later adapted for functionally graded materials(FGMs) by WILLIAMSON et al[17-18]. The gradient cylinder is treated as an isotropic composite, for which the uniaxial stress σ and strain ε are related to the corresponding average uniaxial stress and strain of the two constituent phase as follows:
(2)
where σ1 and ε1 are the stress and stain of cobalt phase, σ2 and ε2 are the stress and stain of tungsten carbide, respectively. And the elastic constraint factor (the ratio of strain transfer) p, is defined as
(3)
If E12, then
1≤p≤
(4)
where Ei is the modulus of elasticity of material i. Obviously, p=1 and p= E2/E1 correspond to properties of equal strain and equal stress, respectively. For Eqns.(2) and (3), effective modulus of elasticity E is derived explicitly as
(5)
According to the test results, p is taken as 3, which generally depends on the internal constraints arising from specific microstructural dispersion of the two phases, the thermomechanical properties, and the residual stresses from processing.
Experimental measurements of elastoplastic deformation in powder-metallurgy processing show that when the mass fraction of Co falls typically below 10%, the graded composite behaves essentially like an elastic solid[19], and there is no plastic deformation. The cobalt content was less than 10%, therefore plastic deformation of WC-Co cemented carbide was ignored in this study. In view of processing point, the above constitutive responses are approximations with respect to the constitutive mass fraction of the metal, which can be controlled in processing in fact. The formulation is complete once mass fraction of Co is known as a function of the depth.
According to experimental results, a function of the cobalt content distribution in the WC-Co graded alloys (i.e. the volume fraction φ1 as a function of radial distance r) was constructed as follows:
, 0≤r≤R (6)
where w represents the nominal cobalt content in raw materials, n denotes the depth of cobalt rich zone, k is the slope of cobalt gradient and l is used to modify the least cobalt content for avoiding the appearance of negative values of cobalt content. By varying w, n, k and l, the different distributions of the cobalt content from the core to the surface zone are obtained. When w, n, k and l equal 6, 0.8, 0.015, 0.035, respectively, the curve of cobalt content distribution is obtained (shown in Fig.3(a)). The corresponding distribution of modulus of elasticity and coefficient of thermal expansion are also shown in Fig.3. The relationship of mechanical properties varied with temperature is listed in Table 1.
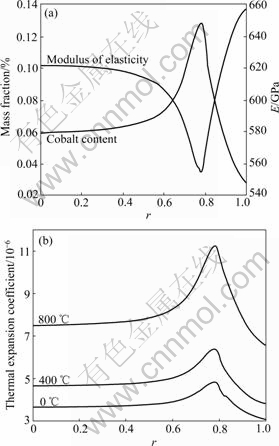
Fig.3 Schematics of materials properties: (a) Cobalt content and modulus of elasticity in substrate; (b) Coefficient of thermal expansion at different temperatures
3.2 Numerical results
An axisymmetric cylinder geometric model for elastic deformation of diamond coating on cemented carbide was built up, in which the temperature decreased from the initial stress-free temperature of 800 ℃ to room temperature. Effect of W interlayer on residual stress distribution was also considered.
Table 1 Temperature dependence of thermomechanical pro- perties of materials
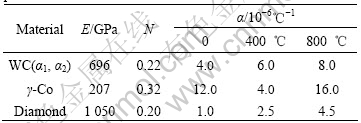
Fig.4 shows the comparison of equivalent von Mises stress and hydrostatic stress between graded substrate and conventional substrate with WC-6Co. It can be found that the equivalent stress is 1 537 MPa for graded substrate and 1 989 MPa for conventional sub- strate, the surface compressive stress is 950 MPa for graded substrate and 1 250 MPa for homogenous sub- strate, thermal residual stress decreases by around 24% due to carburization. Numerical results show that the maximum value of thermal residual strain in diamond coating is 0.001 06 for graded substrate and 0.001 38 for conventional substrate, it also decreases by 23%. Therefore carburization not only reduces the cobalt in the surface zone to satisfy the diamond nucleation condition,
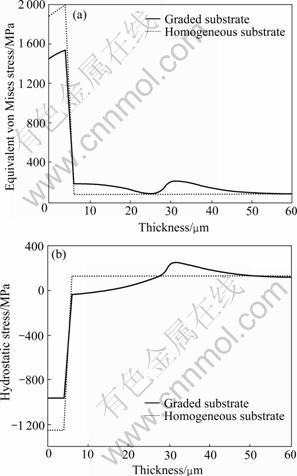
Fig.4 Comparison of thermal residual stress between graded substrate and homogeneous substrate: (a) Equivalent stress; (b) Hydrostatic stress
but also relaxes the thermal residual stress to strengthen the interface adhesion.
Transition layer is noticed by many material researchers. Tungsten interlayer is the ideal element due to its low thermal expansion coefficient that is close to the thermal expansion coefficient of cemented carbide substrate. In this study, tungsten interlayer was employed to inhibit the detrimental influence of cobalt phase.
Fig.5 shows comparison of equivalent von Mises stress in diamond coating on different substrates. There are three types of substrates: graded substrate, conventional substrate, and tungsten interlayer substrate. It is found that the thermal residual stress in graded substrate is smaller than that in conventional interlayer substrates. Equivalent stress increases slightly with adding tungsten interlayer. The maximum value of equivalent stress in diamond coating is 1 989 MPa on conventional substrate, and 2 019 MPa in diamond coating with tungsten interlayer. So transition layer can be employed when cobalt content is rather high in the surface layer of substrate, otherwise, carburizing pretreatment can be employed when the mass fraction of cobalt is less than 13%.

Fig.5 Comparison of equivalent von Mises stress in diamond coating on different substrates
4 Conclusions
1) Carburizing pretreatment is used to decrease the cobalt concentration in surface layer of the substrate and improve adhesion of diamond coating.
2) The surface compressive stress is 950 MPa for graded substrate and 1 250 MPa for homogenous substrate, the thermal residual stress decreases by around 24% due to carburizing.
3) When the mass fraction of cobalt is greater than 13%, transition layer can be employed to inhibit the detrimental influence of cobalt phase for the coated cemented carbides.
References
[1] LEYENDECKER T, LEMMER O, JURGENS A, ESSER S, EBBERINK J. Industrial application of crystalline diamond-coated tools[J]. Surface and Coatings Technology, 1991, 48(3): 253-260.
[2] MURAKAWA M, TAKAEUCHI S. Mechanical applications of thin and thick diamond films[J]. Surface and Coatings Technology, 1991, 49(1/3): 359-365.
[3] YASKIKI T, NAKEMURA T, FUJIMORI N, NAKAI T. Practical properties of chemical vapour deposition diamond tools[J]. Surface and Coatings Technology, 1992, 52(1): 81-85.
[4] INSPECTOR A, BAUER C E, OLES E J. Superhard coating for metal cutting applications[J]. Surface and Coatings Technology, 1994, 68/69: 359-368.
[5] KANDA K, TAKELANA S, YOSHIDA S, WATANABE R, TAKANO S, ANDO H. Application of diamond-coated cutting tools[J]. Surface and Coatings Technology, 1995, 73(1/2): 115-120.
[6] AMIRHAGHI S, REEHAL H S, WOOD R J K, WHEELER D W. Diamond coating on tungsten carbide and their erosive wear properties[J]. Surface and Coatings Technology, 2001, 135(2/3): 126-138.
[7] INSPECTOR A, OLES E J, BQUER C E. Theory and practice in diamond coated metal-cutting tools[J]. International Journal of Refractory Metals and Hard Materials, 1997, 15(1/3): 49-56.
[8] ITOH H, OSAKI T, IWAHARA H, SAKAMOTO H. Microstructural control of boundary region between CVD diamond film and cemented carbide substrate[J]. Journal of Materials Science, 1994, 29(5): 1404-1410.
[9] FISCHER U K R, HARTZELL E T, AKERMAN J G H. Cemented carbide body used preferably for rock drilling and mineral cutting: US Patent, 4743515[P]. 1998-05-10.
[10] AKERMAN J G H, FISCHER U K R, HARTZELL E T. Cemented carbide body with extra tough behavior: US Patent, 5279901[P]. 1994-01-18.
[11] FISCHER U K R, HARTZELL E T, AKERMAN J G H. Cemented carbide body with a binder phase gradient and method of make the same: US Patent, 4820482[P]. 1989-04-11.
[12] CHEN Li, WU En-xi, WANG She-quan, LIU Chang-bin, YIN Fei, LU Yu-xiang. Formation mechanism of surface ductile zones in WC2Ti( C, N)2Co gradient cemented carbide[J]. Journal of Central South University: Science and Technology, 2006, 37(4): 650-654. (in Chinese)
[13] YIN Fei, CHEN Kang-hua, WANG She-quan. Influences of functionally graded structure of substrate on performance of coated cemented carbide[J]. Journal of Central South University: Science and Technology, 2005, 36(5): 776-779. (in Chinese)
[14] LIU Y, WANG H B, YANG J G. Formation mechanism of cobalt-gradient structure in WC-Co hard alloy[J]. Journal of Materials Science, 2004, 39: 4397-4399.
[15] TANG W, WANG Q, WANG S, LU F. Adherent diamond coating on cemented carbide substrates with different cobalt contents[J]. Diamond and Related Materials, 2001, 10(9/10): 1700-1704.
[16] TAMURA I, TOMOTA Y, OZURA H. Strength and ductility of Fe-Ni-C alloys composed of austenite and martensite with various strength [C]// Proc Third Int Conf Strength of Metals and Alloys. Cambridge: Institute of Metals, 1973: 611-615.
[17] WILLIAMSON R L, RABIN B H, DRAKE J T. Finite element analysis of thermal residual stresses at graded ceramic-metal interfaces (Part I): Model description and geometrical effects[J]. Journal of Applied Physics, 1993, 74: 1310-1320.
[18] WILLIAMSON R L, RABIN B H, DRAKE J T. Finite element analysis of thermal residual stresses at graded ceramic-metal interfaces (Part II): Interface optimization for residual stress reduction[J]. Journal of Applied Physics, 1993, 74: 1321-1326.
[19] KIEFFER R, SCHWARZKOPF P. Hardmetals[M]. WANG Shao-gang, translate. Beijing: China Industry Press, 1963. (in Chinese)
(Edited by YANG Hua)
Foundation item: Project(50323008) supported by the National Natural Science Foundation of China
Received date: 2007-09-20; Accepted date: 2007-11-21
Corresponding author: HE Yue-hui, Professor; Tel: +86-731-8877391; E-mail: yuehui@mail.csu.edu.cn