J. Cent. South Univ. (2016) 23: 2346-2353
DOI: 10.1007/s11771-016-3293-8

Minimum safe thickness of rock plug in karst tunnel according to upper bound theorem
YANG Zi-han(杨子汉), ZHANG Jia-hua(张佳华)
School of Civil Engineering, Central South University, Changsha 410075, China
Central South University Press and Springer-Verlag Berlin Heidelberg 2016
Abstract: High pressure and water-bearing caverns ahead of a karst tunnel face tend to cause geological disasters, such as water and mud bursts. So, the determination of safe thickness of the reserved rock plug is a key technical problem to be solved for karst tunnel construction. Based on the Hoek-Brown nonlinear failure criterion, the minimum safe thickness of rock plug was investigated in the light of the limit analysis theory. On the basis of the proposed failure mode, the expression of the minimum thickness for rock plug was obtained by means of upper bound theorem in combination with variational principle. The calculation results show the influence of each parameter on safe thickness and reveal the damage range of rock plug. The proposed method is verified by comparing the results with those of the drain cavern of Maluqing Tunnel. The research shows that with the increase of compressive strength and tensile strength as well as constant A of Hoek-Brown criterion, the safe thickness decreases, whereas with the increase of cavern pressure, tunnel diameter, and constant B from Hoek-Brown criterion, the safe thickness increases. Besides, the tensile strength, or constants A and B affect the shear failure angle of rock plug structure, but other parameters do not. In conclusion, the proposed method can predict the minimum safe thickness of rock plug, and is useful for water burst study and prevention measures of tunnels constructed in high-risk karst regions.
Key words: karst tunnels; rock plug; minimum safe thickness; upper limit theorem; failure mode
1 Introduction
Unfavorable karst areas are widely distributed in our country. With the vigorous construction of transport infrastructures, more and more tunnels are built in those areas. In these areas where karst is intensely developed, rocks, mainly limestone, are likely to develop into numerous water-bearing caverns with rich water and high pressure as a result of underground water’s corrosion, erosion, and replenishment. When a tunnel is constructed near these zones, inadequate safe thickness of reserved rock plug may result in the failure of supporting structure and even the water and mud bursts into the tunnel before the drainage process, which not only affect construction progress, but also endanger people’s lives and property [1-4]. For karst tunnels with high-pressure water-bearing caverns, how to determine the minimum safe thickness of rock plug according to geophysical prospecting results is therefore an important engineering technical problem that cannot be neglected.
A great number of scholars carried out researches on this related topic and many achievements have been made. MEGUID and DAND [5] used the elastic-plastic finite element theory to analyze the impact of cavities (formed due to the dissolution of carbonate horizon) on lining structure of tunnel, and concluded that cavity size was the major factor affecting the circumferential stress of tunnel lining. GEREMEW [6] employed the linear regression principle to study the minimum safe thickness, and presented three quantitative methods to calculate the safe distance. According to the geophysical prospecting results, PESENDORFER and LOEW [7] obtained the change laws of transient water pressure of deep tunnels in karst regions. As for karst tunnels with water inrust induced by hydraulic fracturing, LI et al [8-9] divided the safe thickness range of rock plug into relaxation section, safe thickness section, and fissure section, then deduced the semi-analytical expressions for each section. As for caverns beside tunnels, GUO [10] established the mechanical prediction model of safe thickness for middle rock plug of tunnels with side high-pressure and water- bearing caverns, and analyzed each factor’s influence on the minimum safe distance. To sum up, there are three methods for calculating the minimum safe thickness, namely experience analogy, numerical simulation, and theoretical calculation. The result obtained by experience analogy, which is 0.9-1.4 times tunnel diameter, is too conservative. In addition, this method is only related to tunnel diameter, but other important factors, such as rock mass type, quality grade, geo-stress, caverns pressure, cannot be taken into account. Therefore, experience analogy method can only be used to give a preliminary judgment. Both numerical simulation and theoretical calculation take a variety of factors into consideration. However, the main purpose of numerical simulations is prone to verify theoretical method. For relatively intact rock mass, the minimum safe thickness is generally researched by the elastic thick plate theory with the control conditions of tensile failure or shear failure. This method, which is convenient and easy to understand, places extra emphasis on mechanical equilibrium, but overlooks the stress-strain relationship of rocks.
This work considers the stress-strain relationship of rocks in the analysis based on the limit analysis theory [11-15]. The minimum safe thickness of rock plug was deduced on the basis of the established failure mode from the point of view of energy theory, when there is a water-bearing cavern in front of tunnel face. Meanwhile, influence of each parameter on the safe thickness and extent of damage area is analyzed and discussed in the light of calculation results. In general, the rock plug minimum safe thickness calculated according to the limit analysis theory is accurate, and able to serve as the basis of tunnel structure design and construction.
2 Basic theories
2.1 Upper bound theorem of limit analysis
Limit analysis theory is an algorithm for calculating ultimate load. Its most remarkable advantage is that no matter how complicated the structure’s geometrical shapes and loads are, a practical failure load can always be obtained through this algorithm. Limit analysis theory composed of upper bound theorem and lower bound theorem can be utilized to determine the upper and lower bound solutions of an ultimate load for geotechnical structures, between which range the real ultimate load can be found.
Using the upper bound theorem of limit analysis, this work aims to determine the minimum safe thickness of rock plug in tunnels around which water-bearing caverns exist. The upper bound theorem is basically defined as follows: if the assumed kinetically admissible velocity field complies with displacement boundary conditions, the solution determined by the equating the rate of internal energy dissipation with external force power is definitely not less than the actual load under the ultimate limit state [16]. Its mathematical expression is
(1)
where
represents the internal energy dissipation rate of plastic strain rate vector; Ti and Fi are external forces, namely surface forces and body forces, respectively; vi denotes the velocity vector in the kinetically admissible velocity field.
2.2 Hoek-Brown failure criterion
Since 1980, the Hoek-Brown yield criterion has been widely accepted by domestic and overseas scholars, and been applied to a mass of projects [17-21]. The Hoek-Brown criterion not only can be described with effective major and minor principal stresses, but also can be expressed with effective normal and shear stresses [22-27]. Because this work adopts the upper bound theorem of limit analysis, which requires the normal and shear stresses in the calculation of internal energy dissipation, the Hoek-Brown criterion expressed in the form of effective normal and shear stresses is employed here. Its expression is
(2)
where τn and σn refer to the effective shear stress and normal stress; respectively; σci is the uniaxial compressive strength of a intact rock material; and σtm is the tensile strength; A and B, which change from 0 to 1.0, are non-dimensional material parameters. When B=1.0, the Hoek-Brown failure criterion is reduced to the Mohr-Coulomb linear yield criterion.
3 Calculation of minimum safe thickness of rock plug
3.1 Determination of failure mode
For a fixed tunnel, the positions of concealed caverns are relatively stochastic. That is to say, in tunnel construction, caverns may appear ahead of or at the side of tunnel face. However, for different positions, mechanical models of the rock plug safe thickness vary as well. For simplification, only the special condition that concealed water-bearing cavern locates right ahead of tunnel face is considered herein. The failure mode of rock plug structure, shown as Fig. 1, is established with reference to the models presented by FRALDI [28].
In Fig. 1, D indicates the tunnel diameter; H is the minimum safe thickness of rock plug, and also the unknown value to be finally determined according to the limit analysis theory; w refers to the assumed thickness of separating layer at failure transiently; p is the pressure of caverns, and L is the range of cavern pressure acting on the half rock plug structure.
From Fig. 1, rock plug structure collapses as a whole at the speed v as a results of the cavern pressure.
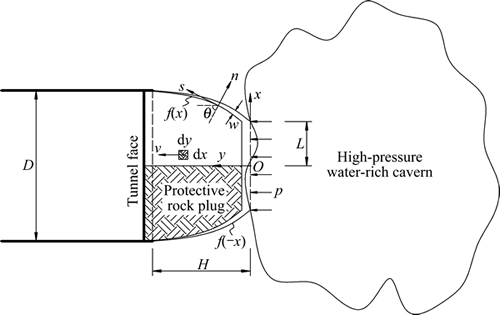
Fig. 1 Failure mode of rock plug safe thickness
Two detaching curves f(x) and f(-x), which are symmetrical to each other along axis y, are used to bound the failure block. To simplify the calculation, half system in the positive x axis is taken as the object to study. Meanwhile, the local coordinate system s-n with tangent direction and outer normal direction as positive directions is established on the detach curve f(x). Therefore, the algebra relation between θ and f′(x) is expressed
(3)
For the purpose of simplification, the presented problem is assumed as a 2-D problem. Besides, some assumptions are made as follows:
1) The work of gravity is zero since the collapsing of rock plug is normal to the gravity direction. Hence, gravity is neglected in the calculation process;
2) Rock mass of tunnel is characterized by the Mohr-Coulomb criterion, and complies with the associated flow rule;
3) Cavern pressure is uniformly distributed on the surface of karst cavities, and the surface bearing the cavern pressure is idealized as a plane, which is plotted as a dotted line coinciding with x axis in Fig. 1.
3.2 Calculation process of rock plug thickness
Plastic potential function should be first obtained before the determination of the expression of stress-strain rate according to the normality law. For Mohr-Coulomb materials, since the yield surface overlaps the plastic potential surface, plastic potential function g(σn, τn) can be expressed with yield function f(σn, τn) when materials yield. Therefore, as for tunnel surrounding rocks with the Hoek-Brown failure criterion, their plastic potential function is expressed as
(4)
Normal and tangent strain rate are determined according to the orthogonal flow rule:
(5)
where λ is the plastic proportionality coefficient. In addition, the strain rate of any point on the detaching curve f(x) can be also acquired from the definition, namely the ratio of velocity and volume. Therefore, the following formulas can be obtained according to the trigonometric function in Eq. (3).
(6)
After the combination of Eqs. (5) and (6), λ and w are divided out to obtain the normal stress expression as
(7)
The established failure mode (Fig. 1) shows that the internal energy dissipation of rock plug structure only occurs in the separating shear layer with the thickness w. Furthermore, the separating layer’s deformation is composed of tensile deformation at the normal direction and shear deformation at the tangential direction. Therefore, the internal energy dissipation of the detaching curve f(x) can be expressed as

(8)
With
, the internal energy dissipation power of the entire rock plug structure is acquired:
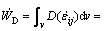
(9)
Pressure of water-bearing caverns is the surface force, and its power is
(10)
The gravity is the body force, and the power is equal to zero due to the direction of failure body perpendicular to the direction of gravity, namely,
(11)
Substituting Eqs. (9), (10) and (11) into Eq. (1) leads to:
(12)
Based on the upper bound theorem, the detaching curve f(x) determined by Eq. (12) is a series of upper bound solutions higher than or equal to real values. Therefore, the following target function is constructed as

(13)
The optimum upper bound solution can be determined through a optimization of Eq. (13). It is easy to discover that the extreme value of target function R is completely determined by functional δ. Hence, the current problem is converted as the optimization of functional δ. Based on the variation principle, Euler equation of functional δ can be computed, which converts the problem of the optimization of functional δ into a solving of Euler equation [29-32]. Euler equation of functional δ is
(14)
By substituting functional δ into Euler equation, a second order differential equation simplified is found.
(15)
Solving the high-order differential equation, the expression of the detach curve f(x) containing undetermined constants is given by
(16)
Therefore, without consideration of gravity, the detaching curve is a straight line under the 2D failure mode. Parameters c0 and c2 are constant to be determined. By assuming
the detaching curve can be simplified as
(17)
After the determination of the detaching curve expression, the equation set including the minimum safe thickness H of rock plug and acting scope L of cavern pressure is attained in accordance with the geometrical relationship in failure mode.
(18)
Since the equation set still contains undetermined constants c1 and c2, the minimum safe thickness H of rock plug cannot be acquired directly. Therefore, more equations including these unknown parameters are needed according to the upper bound theorem and mechanical boundary conditions.
First of all, based on virtual work principle, namely that internal energy dissipation is equal to power of external forces, the expression between L and c1 can be set up.
(19)
The formula can be simplified as
(20)
Combining Eq. (18) and Eq. (20), the upper bound expression of the minimum safe thickness of rock plug is
(21)
However, c1 is still an unknown constant. So, another function is required for its solution. A micro-unit from the interface of detaching curve and water-bearing cavern is taken for analysis, shown as Fig. 2. Thus, the mechanical equilibrium equation along the vertical direction is established. After the simplification, the expression of shear stress τyx is given by
(22)
According to mechanical boundary conditions, there is no shear stress distribution on the surface of water-bearing cavern. Therefore, τyx is equal to zero at the point (x=L, y=0). Substituting Eqs. (2), (3) and (7) into Eq. (22) and after simplification, the equation for solving c1 is finally obtained.
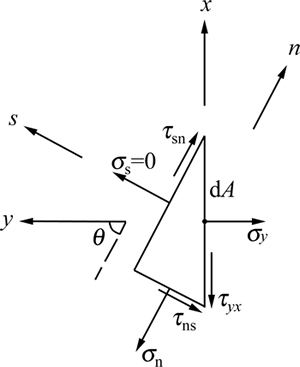
Fig. 2 Sketch map for stress analysis of micro-unit
(23)
It should be noted that since the solution to constant c1 is closely related to the value of parameter B, it is impossible to directly solve the expression of c1 from the above equation. However, when all parameters are known, the value of c1 can be calculated. Then, with substitution of c1 into Eq. (21), the minimum safe thickness H of rock plug can finally be determined.
4 Results and parameters analysis
According to the analysis mentioned above, the property of rock plug structure is subject to the influence of various factors, such as compressive strength σci, tensile strength σtm, dimensionless material parameters A and B, cavern pressure p, and tunnel excavation diameter D. In order to study the single influence of each parameter on rock plug structure, 16 cases with different parameters were extracted in this work. And the values of minimum safe thickness H, cavern pressure effect range L, and gradient c1 and intercept c2 of detaching curve f(x) were solved by Eqs. (21) and (23). The calculated results are listed in Table 1.
In order to clearly observe the change of minimum safe thickness with each parameter, the failure shape and range of rock plug structure are plotted in Fig. 3 on the basis of data in Table 1.
From Table 1 and Fig. 3, it can be found that with the increase of compressive strength σci, and tensile strength σtm as well as material parameter A, theminimum safe thickness of rock plug is declining gradually; whereas with the rise of cavern pressure p, tunnel diameter D, and material constant B, rock plug thickness is increasing. On the other hand, as for the gradient c1 of the rock plug detaching curve f(x), changes of compressive strength σci, cavern pressure p and tunnel diameter D have no impact on c1, which means that shear failure angle θ remains constant at failure, namely θ = arctan1.56 ≈ 57°; however, variations of tensile strength σtm and material constants A as well as B influence the values of c1.
Table 1 Minimum safe thickness values under different parameters
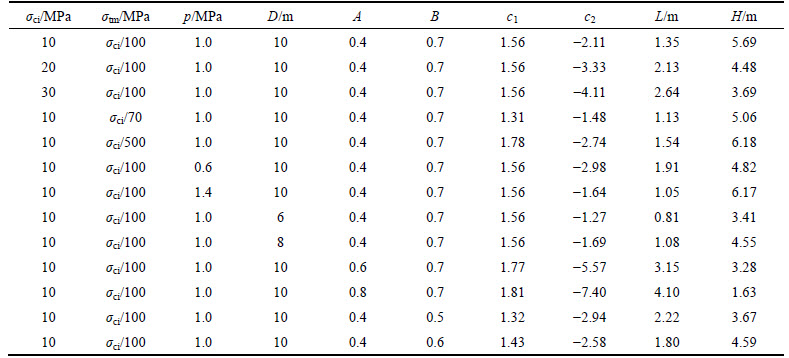
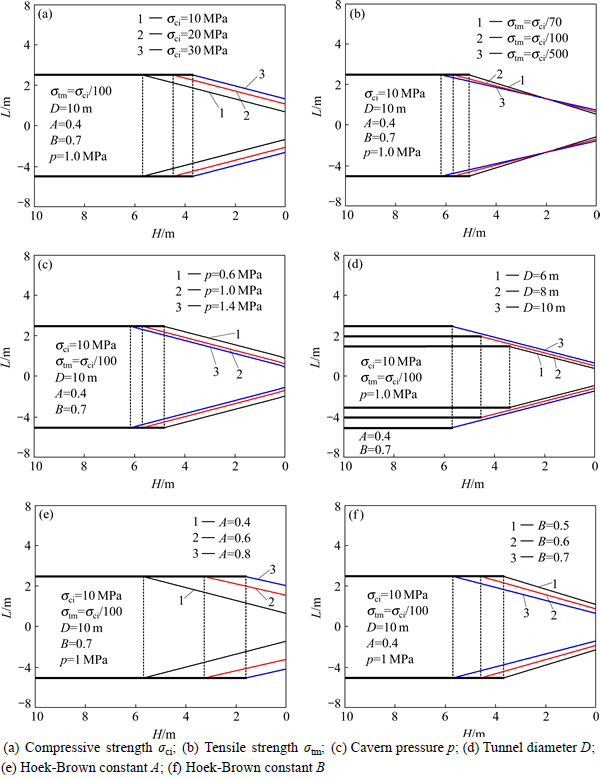
Fig. 3 Change laws of minimum safe thickness with different parameters:
These changes reveal that the safe thickness of rock plug is affected simultaneously by a variety of factors. Nevertheless, when strength parameters of rock material are given, the Hoek-Brown dimensionless constants A and B affect not only the minimum safe thickness, but also the shear failure angle at failure. Therefore, the input of A and B which have a significant influence on the calculation results of minimum safe thickness should be paid more attention to in actual engineering applications.
5 Engineering example
Maluqing Tunnel of Yiwan Railway is located at the boundary of Enshi City and Lichuan City of Hubei Province. The total length of the tunnel is about 7800 m, and surrounding rocks are mainly limestone. The tunnel area is characterized by developed karst, complicated geological structure and rich water replenishment, so water and mud bursts disaster happened repeatedly during the tunnel construction. To attempt to verify this proposed method, the minimum safe thickness of rock plug is computed for the drain cavern of “978 karst cavity” of Maluqing Tunnel.
The drain cavern of “978 karst cavity” in Maluqing Tunnel is a 5 m × 5.75 m (width × height) rectangular section. Before the karst cavity are exposed by drain caverns, the internal water pressure is 0.8-1.2 MPa, so the average value 1.0 MPa is adopted in the calculation. Moreover, according to GUO’s [10] results of uniaxial compressive test and Brazilian test on a number of tunnel limestone samples of Yiwan Railway, the uniaxial compressive strength σci and tensile strength σtm in Maluqing Tunnel are taken to be 89.51 MPa and 5.03 MPa respectively via engineering analogy. Values of Hoek-Brown material constants A and B are taken as 0.1 and 0.6, respectively, which are relatively conservative values. After substituting these values into Eqs. (21) and (23), the minimum safe distance of rock plug in Maluqing Tunnel drain cavern can be calculated as 1.39 m.
Table 2 shows the thickness of reserved rock plug under different cavern pressures for intact rock mass of “Yiwan Railway”. According to Table 2, the actual thickness of rock plug of the drain cavern in Maluqing Tunnel is 1.5m, which is a little bigger than the result calculated by the proposed method. Therefore, when surrounding rocks of tunnel face are intact, the proposed method can be used as an approximated algorithm to evaluate the minimum safe thickness of rock plug structure.
Table 2 Reserved thicknesses of tock plug under intact rock mass conditions in Yiwan Railway
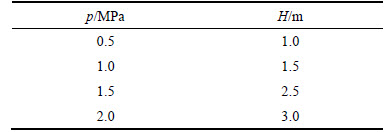
6 Conclusions
1) Based on the Hoek-Brown nonlinear failure criterion, for the first time, limit analysis is used to compute the minimum safe distance of rock plugs. Meanwhile, according to the presented 2D failure mode, the calculation processes of rock plug thickness are deduced by means of the upper bound theorem and variation principle. As a consequence, the expression of minimum safe thickness is obtained.
2) Influence of each parameter on the safe thickness of rock plugs is investigated, and the corresponding damage area is plotted according to the calculation results. The results show that: with the increase of compressive strength σci, tensile strength σtm and material parameter A, the minimum safe thickness of rock plug is on the gradual decline, while with the increase of cavern pressure p, tunnel diameter D and material parameter B, rock plug thickness is on the gradual rise. On the other hand, the varies of tensile strength σtm and material parameters A and B cause the change of gradient c1 of the detaching curve f(x), but other parameters do not.
3) Taking the drain cavern of “978 karst cavity” in Maluqing Tunnel as the example, the minimum safe thickness of rock plug is calculated to be 1.39 m by the proposed method, which is close to the actual safe thickness 1.5 m adopted in this project. This proves the validation of the proposed method. Therefore, the method can be taken as an approximated algorithm for assessing the minimum safe thickness of rock plug structure.
4) Although the calculated result in the paper is basically consistent with engineering practice, the failure mode and the calculation process are based on 2D cases, which may be different from the actual case to a certain extent. Therefore, the further study should be performed on 3D cases in the future.
References
[1] SENENT S, MOLLON G, JIMENEZ R. Tunnel face stability in heavily fractured rock masses that follow the Hoek-Brown failure criterion [J]. International Journal of Rock Mechanics and Mining Sciences, 2013, 60(1): 440-451.
[2] YANG X L, ZOU J F. Stability factors for rock slopes subjected to pore water pressure based on the Hoek-Brown failure criterion [J]. International Journal of Rock Mechanics and Mining Sciences, 2006, 43(7): 1146-1152.
[3] YANG X L, WANG J M. Ground movement prediction for tunnels using simplified procedure [J]. Tunnelling and Underground Space Technology, 2011, 26(3): 462-471.
[4] YANG X L. Seismic bearing capacity of a strip footing on rock slopes [J]. Canadian Geotechnical Journal, 2009, 46(8): 943-954.
[5] MEGUID M A, DAND H K. The effect of erosion voids on existing tunnel linings [J]. Tunneling and Underground Space Technology, 2008, 4(2): 1-9.
[6] GEREMEW A M. Pore-water pressure development caused by wave-induced cyclic loading in deep porous formation [J]. International Journal of Geomechanics, 2011, 13(1): 65-68.
[7] PESENDORFER M, LOEW S. Subsurface exploration and transient pressure testing from a deep tunnel in fractured and karstifiedlimestones (L
tschberg Base Tunnel, Switzerland) [J]. International Journal of Rock Mechanics and Mining Science, 2010, 47(1): 121-137.
[8] LI Li-ping, LI Shu-cai, ZHANG Qing-song. Study of mechanism of water inrush induced by hydraulic fracturing in karst tunnels [J]. Rock and Soil Mechanics, 2010, 31(2): 523-528. (in Chinese)
[9] YANG X L, YIN J H, LI L. Influence of a nonlinear failure criterion on the bearing capacity of a strip footing resting on rock mass using a lower bound approach [J]. Canadian Geotechnical Journal, 2003, 40(3): 702-707.
[10] GUO Jia-qi. Study on against-inrush thickness and water-burst mechanism of karst tunnel [D]. Beijing: Beijing Jiaotong University, 2011. (in Chinese)
[11] YANG X L. Seismic passive pressures of earth structures by nonlinear optimization [J]. Archive of Applied Mechanics, 2011, 81(9): 1195-1202.
[12] YANG X L, YIN J H. Estimation of seismic passive earth pressures with nonlinear failure criterion [J]. Engineering Structures, 2006, 28(3): 342-348.
[13] YANG X L, YIN J H. Slope stability analysis with nonlinear failure criterion [J]. Journal of Engineering Mechanics, 2004, 130(3): 267-273.
[14] YANG X L, ZOU J F. Cavity expansion analysis with non-linear failure criterion [J]. Proceedings of the Institution of Civil Engineers- Geotechnical Engineering, 2011, 164(1): 41-49.
[15] YANG X L, LI L, YIN J H. Seismic and static stability analysis for rock slopes by a kinematical approach [J]. Geotechnique, 2004, 54(8): 543-549.
[16] CHEN W F. Limit analysis and soil plasticity [M]. The Netherland: Elsevier, 2013: 37-39.
[17] LI A J, MERIFIELD R S, LYAMIN A V. Stability charts for rock slopes based on the Hoek-Brown failure criterion [J]. Rock Mechanics and Mining Sciences, 2008, 45(5): 689-700.
[18] FRALDI M, GUARRACINO F. Limit analysis of collapse mechanisms in cavities and tunnels according to the Hoek-Brown failure criterion [J]. International Journal of Rock Mechanics and Mining Sciences, 2009, 46(4): 665-673.
[19] YANG X L, HUANG F. Three-dimensional failure mechanism of a rectangular cavity in a Hoek-Brown rock medium [J]. International Journal of Rock Mechanics and Mining Sciences, 2013, 61: 189- 195.
[20] YANG X L, HUANG F. Collapse mechanism of shallow tunnel based on nonlinear Hoek-Brown failure criterion [J]. Tunnelling and Underground Space Technology, 2011, 26(6): 686-691.
[21] YANG X L, YIN J H. Slope equivalent Mohr-Coulomb strength parameters for rock masses satisfying the Hoek-Brown criterion [J]. Rock Mechanics and Rock Engineering, 2010, 43(4): 505-511.
[22] HOEK E, CARRANZA C, CORKUM B. Hoek-Brown failure criterion-2002 edition [C]// HAMMAH R, BAWDEN W F, CURRAN J. Proceedings of the North American Rock Mechanics Society NARMS-TAC 2002. Toronto: University of Toronto Press, 2002: 267-273.
[23] HOEK E, BROWN E T. Practical estimates of rock mass strength [J]. International Journal of Rock Mechanics and Mining Sciences, 1997, 34(8): 1165-1186.
[24] PAUL M, HOEK E. Estimating the geotechnical properties of heterogeneous rock masses such as flash [J]. Bulletin of Engineering Geology and the Environment, 2001, 60(2): 85-92.
[25] YANG X L, YIN J H. Upper bound solution for ultimate bearing capacity with a modified Hoek-Brown failure criterion [J]. International Journal of Rock Mechanics and Mining Sciences, 2005, 42(4): 550-560.
[26] YANG X L, LI L, YIN J H. Stability analysis of rock slopes with a modified Hoek-Brown failure criterion [J]. International Journal for Numerical and Analytical Methods in Geomechanics, 2004, 28(2): 181–190.
[27] YANG X L. Seismic displacement of rock slopes with nonlinear Hoek-Brown failure criterion [J]. International Journal of Rock Mechanics and Mining Sciences, 2007, 44(6): 948-953.
[28] FRALDI M, GUARRACINO F. Analytical solutions for collapse mechanisms in tunnels with arbitrary cross sections [J]. International Journal of Solids and Structures, 2010, 47(2): 216-223.
[29] SUN Zhi-bin, ZHANG Dao-bing. Back analysis for soil slope based on measuring inclination data [J]. Journal of Central South University, 2012, 19(11): 3291-3297.
[30] SUN Zhi-bin, LIANG Qiao. Back analysis of general slope under earthquake forces using upper bound theorem [J]. Journal of Central South University, 2013, 20(11): 3274-3281.
[31] YANG X L, Long Z X. Seismic and static 3D stability of two-stage rock slope based on Hoek-Brown failure criterion [J]. Canadian Geotechnical Journal, 2016, 53(3): 551-558.
[32] YANG X L, XU J S, LI Y X, YAN R M. Collapse mechanism of tunnel roof considering joined influences of nonlinearity and non-associated flow rule [J]. Geomechanics and Engineering, 2016, 10(1): 21-35.
(Edited by DENG Lü-xiang)
Foundation item: Project(2013CB036004) supported by the National Basic Research Program of China; Project (51378510) supported by the National Natural Science Foundation of China; Project (CX2014B069) supported by Hunan Provincial Innovation Foundation for Postgraduate, China
Received date: 2015-04-08; Accepted date: 2015-07-28
Corresponding author: YANG Zi-han, PhD; Tel: +86-15874279829; E-mail: yangkepler@163.com