
Numerical simulation on forging process of TC4 alloy mounting parts
L? Cheng(吕 成)1, 2, ZHANG Li-wen(张立文)1, 2
1. State Key Laboratory for Materials Modification by Later, Ion and Electron Beams,
Dalian University of Technology, Dalian 116024, China;
2. School of Materials Science and Engineering, Dalian University of Technology, Dalian 116024, China
Received 30 March 2006; accepted 22 September 2006
Abstract: In order to eliminate forging defects appearing in production, based on the rigid-viscoplastic FEM principle, the DEFORM3D software package was employed to simulate the forming process of TC4 alloy mounting part and to optimize the process parameters. In this simulation, the temperature dependency of the thermal and mechanical properties of material was considered. Based on the simulation, the metal flow and thermomechanical field variables such as stress and damage are obtained. The simulation results show that the forging defects are caused by improper die dimension and the optimized die dimension was proposed. To verify the validity of simulation results, forging experiments were also carried out in a forging plant. The forging experiments show that the optimized die dimension can ensure the quality of forging part, and it can provide reference to improve and optimize die design process.
Key words: TC4 alloy; forging defect; rigid-viscoplastic FEM; numerical simulation
1 Introduction
The TC4 alloy mounting part is an important part of aeronautic engine. Currently, these mounting parts are mainly manufactured by metal cutting, which is expensive and requires a lot of manufacturing time. Furthermore, in this way the forging flow lines are cut off near the root of head and the mechanical properties, especially the fatigue property decrease obviously. To overcome the disadvantage of machined parts, die forging technique is used to manufacture the TC4 alloy parts, which not only saves processing costs but also makes the microstructure fine and improves strength of the parts. However, due to the inhomogeneous metal flow and non-uniform localized deformation, forging defects may occur if the die is not appropriately designed.
Recently, progress has been made by using the finite element method(FEM) to deal with the forging process [1-8]. With the development of engineering technology, FEM can be used to simulate metal forming process and gain better understanding of material flow within dies, so as to optimize tooling to eliminate tears, laps and other forging defects[9-12]. The DEFORM software package is a professional FEM software, which serves in the forging and other metal-forming industries for economical process evaluation and optimization[13-15].
In this study, numerical simulation was conducted by using DEFORM3D software on the whole forging process for TC4 alloy mounting parts in an effort to investigate the metal flow behavior. The forging experiments were also carried out in a forging plant to validate the simulation results. This study not only helps to understand but also to improve and optimize die design process, which are based on experience combined with a trial-and-error approach.
2 Forging process of TC4 alloy mounting parts
Fig.1 shows the sectional scheme of forging process of TC4 alloy mounting parts. The billet is a cylinder with a flange head. The upper die has a conical shape bottom. When the upper die goes down, the metal of billet above the lower die is upsetted, and then the flange head is forged to the conical shape. During the process, only the top billet over the lower die is the deformation zone. However, when the die design is not optimized, forging defects like underfilling and lap may occur. In practical production, due to the poorly designed die cavity depth HD(Fig.1), the underfilling and tear defects happened in the forging process, as shown in Fig.2. In this research, the forging process of TC4 alloy mounting parts was analyzed by the rigid-viscoplastic FEM, and the optimized die cavity depth HD to obtain a high-quality product without any forming defects was suggested.
3 Finite element analysis model
The material of mounting parts is TC4 alloy whose
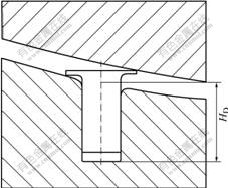
Fig.1 Scheme of forging process of TC4 alloy mounting part
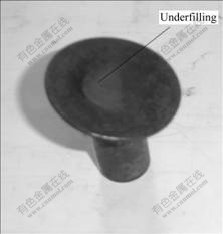
Fig.2 Forging part with some defects
chemical compositions are listed in Table 1. Its true stress—strain curves and thermal physical properties are obtained from material database in DEFORM3D. In the simulation, the billet is a plastic body, whilst the top die and the lower die are rigid bodies. The geometry models of the billet and tooling are generated in UG and then transferred in the STL file format to DEFORM. Friction between the billet and dies is considered the constant shear friction and a friction coefficient of 0.7 is applied to model the dry forging conditions. The die temperature is 20 ℃. The velocity of the top die is 40 mm/s. The process parameters are listed in Table 2. The billet is divided into 27 616 tetrahedral elements and 6 935 nodes, as shown in Fig.3. Finer mesh is placed at the head area of the billet where the billet is deformed severely.
4 Results and analysis of numerical simula- tion
Firstly, the original forging process was simulated, of which the die cavity depth HD is equal to 40.0 mm. Fig.4 shows the distribution of axial stress, effective strain and damage at the end of forging respectively. According to the distribution of effective strain shown in Fig.4(b), the deformation is mainly located in the head area of billet over the lower die, while the deformation of billet in the die cavity is much smaller. As we all known, for the metal, the larger the strain is, the smaller the grain
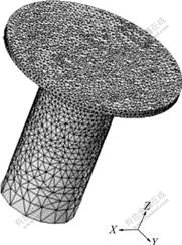
Fig.3 FEM mesh of billet
Table 1 Chemical compositions of TC4 alloy (mass fraction, %)

Table 2 Processing parameters used in simulation

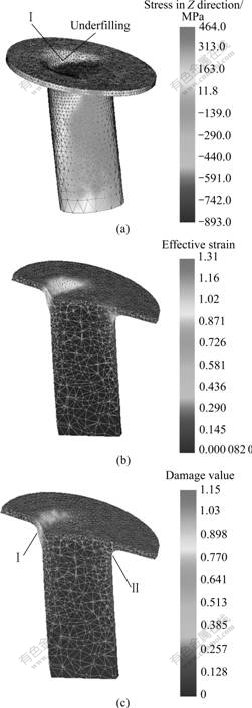
Fig.4 Distribution of field variables (original process with HD of 40.0 mm): (a) Axial stress; (b) Effective strain; (c) Damage
size is. So the forging technique presented in this research can make the microstructure fine at the head area of billet and improve its properties during its service. However, it can be seen that the underfilling defect occurs (Fig.4(a)), which is consistent with the experimental result shown in Fig.2. From Fig.4(a), it can also be seen that the material in area Ⅰ is subject to high tensile stress continually. Under the effect of continual tensile stress, crack may occur in area Ⅰ. Furthermore, based on the damage value that is often used for the estimation of crack development (Fig.4(c)), there is a possibility of developing crack defect. In practice, cracking is observed at the predicted location.
In the technological design process, the billet dimension is unchangeable and the height of billet is 40.00 mm. The height of forging parts is not provided strictly, which is determined by the die cavity depth HD. And the final dimension of parts is decided by the following machining step. Thus, the main objective of forging process is to ensure the part’s head to meet the shape requirements. Furthermore, there should be no defects existing in the head area, such as crack and fold. In this study, the optimal die cavity depth HD can be achieved by virtual trials.
On the basis of the analysis above, due to the poor die design, the billet does not subject to sufficient compressive stress during the forming process, which is the exact reason for underfilling and crack defects. Therefore, through reducing the die cavity depth HD, these defects may be eliminated. Several modified processes were tried by FE simulation and a plausible process shown in Fig.5 was selected for an actual trial. In this process, the die cavity depth was reduced to 35.0 mm. From Fig.5, it can be seen that the underfilling defect is eliminated. What’s more, the principal stress in area Ⅰ is negative, which is a better stress state because it can improve the plasticity of the material and avoid crack defects. Fig.5(b) shows the damage distribution after forging. It can be seen that the maximum damage value in area Ⅰ is only 0.160, which is much smaller than that of original forging process and can protect the part from cracking. However, it is predicted by FE simulation that there is a possibility of developing fold defect in the area Ⅱ based on the flow net pattern, as shown in Fig.6. Through stress analysis shown in Fig.5, the folding is caused by larger compressive stress and non-uniform localized deformation in area Ⅱ. Therefore this fold defect can be eliminated by increasing die cavity depth HD slightly.
It can be seen from the analysis above that the part’s head cannot meet the shape requirements if the die cavity depth is too large. At the same time, the crack defect is caused in area Ⅰ due to the high tensile stress and large damage value. On the contrary, due to the larger compressive stress and non-uniform localized deformation, the fold defect occurs in area Ⅱ if the die cavity depth HD is too small. In order to eliminate the fold defect, several modified processes were tried by FE simulation and an optimized process, of which the die cavity depth HD was 36.5 mm, was selected for the final solution. Fig.7 and Fig.8 show the axial stress distribu-
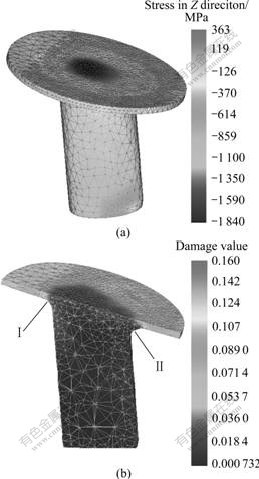
Fig.5 Distribution of field variables (modified process with HD of 35.0 mm): (a) Axial stress; (b) Damage
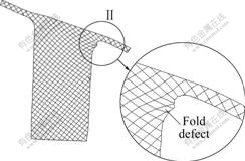
Fig.6 Flow net pattern of modified process with HD of 35.0 mm
tion and flow net pattern after forging according to the optimized process. As shown in Fig.7, the axial stress in area Ⅰ is negative all the time. What’s more, the maximum damage value in area Ⅰ is only 0.208, which shows that the optimized process can protect the part from cracking effectively. Compared with the process above, of which the die cavity depth is 35.00 mm, the axial compressive stress is much smaller in area Ⅱ. This relatively small compressive stress can prevent fold development, as shown in Fig.8.
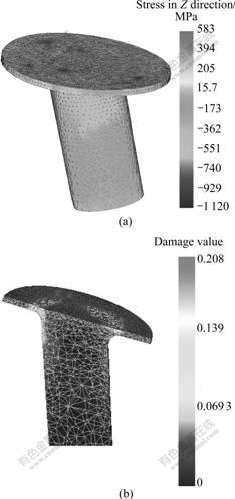
Fig.7 Distribution of field variables (modified process with HD of 36.5 mm): (a) Axial stress; (b) Damage
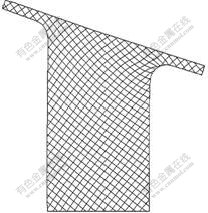
Fig.8 Flow net pattern of optimized process with HD of 36.5 mm
5 Experimental study
In order to verify the optimized process proposed in this paper and the numerical analysis results, the forging experiments were conducted in a forging plant. Fig.9(a) shows the experimental forging part of the optimized process. It can be seen that the billet is forged to the eligible product without underfilling defect. Furthermore, cracking and folding defects do not occur, based on the sectional view of the part’s head shown in Fig.9(b). Through metallographic examination, it is also found that the grain size in the head area is smaller than that in the root area, which can improve the strength of the part.

Fig.9 Experimental parts produced using optimized process: (a) Forging part; (b) Sectional view of part’s head
In this case, only two actual trials were conducted before the final solution was obtained, which might not be possible without the several virtual trials conducted by FE simulations.
6 Conclusions
1) Due to the improper die cavity depth in original forging process, the underfilling defect occurs after forging. Also continual tensile stress in the forging process results in cracking problem at the localized deformation zone.
2) When the die cavity depth is reduced to 35.0 mm, the underfilling and crack defects are eliminated. However, owing to the larger compressive stress and non-uniform localized deformation, a folding problem happens in this case. Through modifying the die cavity depth to 36.5 mm, the folding defect is eliminated too and the product without any defects is obtained.
3) The experiment results agree well with the results of simulation, which shows that the optimized die design proposed and the involving simulation results are correct and reasonable. This can give guidance for selecting process parameters and optimizing die design, even for industrial application in order to save the R&D time of the product.
References
[1] ZHANG Xin-ming, SONG Min, ZHOU Zhuo-ping, ZENG Su-min. Microstructures and mechanical properties of 2014 aluminium alloy forgings made by a new process [J]. Trans Nonferrous Met Soc China, 2000, 10(2): 139-143.
[2] ZHANG Xing-quan, JIA Jian-jun, PENG Ying-hong, RUAN Xue-yu. Ductile damage and simulation of fine blanking process by FEM [J]. Trans Nonferrous Met Soc China, 2000, 10(3): 368-371.
[3] HAO Nan-hai, TIAN Zhu-ping, WEI Xing-hua. Die land optimization of section extrusion by finite element method [J]. Trans Nonferrous Met Soc China, 2001, 11(6): 884-886.
[4] XIE Jian-xin, PEI Qiang, LIU Jing-an. UBET analysis of process of extruding aluminium alloy ribbed thin-wall pipes through a porthole die [J]. Trans Nonferrous Met Soc China, 2002, 12(2): 183-188.
[5] LI G, JINN J T, WU W T, OH S I. Recent development and applications of three-dimensional finite element modeling in bulk forming processes [J]. Journal of Material Processing Technology, 2001, 113: 40-45.
[6] CHANDA T, ZHOU J, DUSZCZYK J. A comparative study on iso-speed extrusion and isothermal extrusion of 6061 Al alloy using 3D FEM simulation [J]. Journal of Material Processing Technology, 2001, 114: 145-153.
[7] ZHANG Hui, YANG Li-bin, PENG Da-shu, LIN Gao-yong. Numerical simulation on microstructural evolution during multi-pass hot-rolling of aluminium alloys [J]. Trans Nonferrous Met Soc China, 2001, 11(2): 231-234.
[8] LI Q, SMITH C, HARRIS C, JOLLY M R. Finite element simulations and experimental studies on inhomogeneous metal flow in aluminium extrusions with three-dimensional complex geometries [J]. Materials Science and Technology, 2002, 18: 1377-1381.
[9] KIM H, YAGI T, YAMANAKA M. FE simulation as a must tool in cold/warm forging process and tool design [J]. Journal of Material Processing Technology, 2000, 98: 143-149.
[10] WALTERS J, WU W T, ARVIND A, LI G, LAMBERT D, TANG J. Recent development of process simulation for industrial applications [J]. Journal of Material Processing Technology, 2000, 98: 205-211.
[11] LIU Y, BAKER T N. A comparison of experimental and computer-simulated isothermal upset forging of IMI685 titanium alloy [J]. Journal of Material Processing Technology, 2001, 117: 56-61.
[12] YANG He, ZHAN Mei, LIU Yu-li. A 3D rigid-viscoplastic FEM simulation of the isothermal precision forging of a blade with a damper platform [J]. Journal of Material Processing Technology, 2002, 122: 45-50.
[13] WANG Guang-chun, ZHAO Guo-qun, XIA Shi-sheng, LUAN Yi-guo. Numerical and experimental study on new cold precision forging technique of spur gears [J]. Trans Nonferrous Met Soc China, 2003, 13(4): 798-802.
[14] LIU Fang, SHAN De-bin, L? Yan. Experimental study and numerical simulation of isothermal closed die forging for aluminium alloy rotor [J]. Trans Nonferrous Met Soc China, 2005, 15(2): 136-141.
[15] WANG Xin-yun, WU You-sheng, XIA Ju-chen, HU Guo-an. FE simulation and process analysis on forming of aluminium alloy multi-layer cylinder parts with flow control forming [J]. Trans Nonferrous Met Soc China, 2005, 15(2): 452-456.
(Edited by LI Xiang-qun)
Foundation item: Project(2005400201) supported by the Aeronautical Science Foundation of Liaoning Province, China
Corresponding author: L? Cheng; Tel: +86-411-84706087; E-mail: commat@student.dlut.edu.cn