J. Cent. South Univ. Technol. (2011) 18: 1139-1143
DOI: 10.1007/s11771-011-0815-2
Calibration of split Hopkinson pressure bar system with special shape striker
ZHOU Zi-long(周子龙)1, HONG Liang(洪亮)2, LI Qi-yue(李启月)1, LIU Zhi-xiang(刘志祥)1
1. School of Resources and Safety Engineering, Central South University, Changsha 410083, China;
2. Department of Civil Engineering, Hunan City University, Yiyang 413000, China
? Central South University Press and Springer-Verlag Berlin Heidelberg 2011
Abstract: In order to present basic guidance for system calibration of split Hopkinson pressure bar (SHPB) with the special shape striker, wave characteristics and dynamic responses of SHPB under striker impact were analyzed. Stress generated by the special shape striker tends to have a half-sine waveform and has little wave dispersion during its propagation. Impact velocities of the special shape striker and peak values of generated stress still have linear relation but with a different coefficient from that of cylindrical strikers. From stress histories on the surfaces of the input bar impacted by the special shape striker off-axially and obliquely, it is found that the misalignment impacts usually trigger wave distortion and amplitude decrease, which can be used to identify the poor system adjustment. Finally, the system calibration of SHPB with the special shape striker can be classified into four steps: system adjustment, wave distortion identification, measurement calibration and transmission calibration, where the measurement calibration factor and transmission calibration factor are elaborated and redefined.
Key words: split Hopkinson pressure bar; special shape striker; system calibration; misalignment impact
1 Introduction
Proposed as the suggested method of Internal Society of Rock Mechanics (ISRM) to determine dynamic characteristics of rock materials [1], more and more split Hopkinson pressure bar (SHPB) apparatus with special shape strikers will be constructed worldwide. Then, basic problems like striker design, system construction and system calibration should be elaborated, so as to give guidance to people who will work with this innovative apparatus. Details about striker design and system construction can be found in early work of LI and GU [2] and recent improvements by their research team [3-6]. But for the system calibration, no detailed investigation has been made before.
In conventional SHPB system for dynamic tests of metal materials, cylindrical strikers are used. Calibration of this kind of SHPB includes measurement correction and transmission correction that are both quantified into correction factors [7-8]. The measurement correction factor is termed as the ratio of theoretical input stress/strain to measured input stress/strain. The transmission correction factor is calculated with the ratio of the incident stress/strain to the transmitted stress/strain. However, in SHPB system with special shape strikers, curved profiles of the strikers make the theoretical prediction of the generated stress/strain very difficult with current knowledge [9-10]. So, the conventional measurement correction for SHPB with cylindrical strikers tends to be unusable. Besides, the truncated head of the special shape striker makes the axial alignment between the input/output bar and the striker rather difficult. The frequent poor alignment will trigger signal distortion, which must be identified and eliminated before tests. So, the system calibration of SHPB with special shape strikers is very different from that with conventional cylindrical strikers.
In this work, the SHPB system with typical special shape striker is taken for analysis. Problems related to the system calibration are discussed, and the steps of system calibration of SHPB with the special shape striker are presented.
2 Wave characteristics of SHPB with special shape striker
Special shape striker is designed to generate half-sine waves on SHPB to overcome premature failure of brittle specimen firstly. It is found to be able to avoid high signal oscillation and keep specimen deforming at constant strain rates [5-6]. All these advantages lead to its popularity for dynamic rock tests. For special shape striker with different profiles, different stress waves are generated. Taking all the cases into consideration is impossible. Here, a typical striker with profile shown in Fig.1 is taken for analysis. The corresponding SHPB input/output bar is 50 mm thick and 2 000 mm long. The striker and the SHPB bars have the same material properties with elastic modulus of 240 GPa, density of 7 800 kg/m3, and Poisson ratio of 0.285.

Fig.1 Striker profile in ISRM suggested method (unit: mm)
2.1 Stress wave and its propagation along input bar generated by special shape striker
Once the striker impacts the input bar, stress wave will be generated in the input bar and propagate along it. Figure 2(a) gives the axial stresses on surface points at 1/4, 1/2 and 3/4 length of the input bar impacted by the striker at velocity of 10 m/s. For the sake of comparison, the stress histories on the compartment SHPB with cylindrical striker of 50 mm thick and same length are also recorded, as shown in Fig.2(b).

Fig.2 Axial stresses at bar surface: (a) Impacted by special shape striker; (b) Impacted by cylindrical striker
From Fig.2(a), it can be seen that an approximately half-sine wave is generated by the striker of Fig.1 and little wave dispersion is observed during propagation. While for rectangular waves generated by the cylindrical striker, heavy signal oscillation from dispersion exists and the waveforms change during its propagation for dispersion effect (Fig.2(b)) [11]. At the same time, slowly-rising wave heads are observed in the half-sine waves generated by the special shape striker. The slowly-rising wave head is vital for dynamic tests of brittle materials to overcome premature failure [6].
By identifying the peak values of waves in Fig.2(a), the three waves have peak values of -166, -162 and -158 MPa, respectively. The decrease of wave amplitude comes from wave attenuation. The average peak values of rectangular waves in Fig.2(b) show the similar trend. For SHPB with steel bars, this attenuation is generally very small within several meters and can be neglected in data processing. However, some non-elastic SHPB bars have been used to investigate the dynamic behaviors of rock joints, polymers or other soft materials recently [10-12]. In these cases, the wave attenuation will be evident and should be corrected.
2.2 Relations between impact velocity of striker and input stress
In SHPB tests with cylindrical strikers, the stress in the input bar is usually estimated according to the 1D wave theory as
(1)
where ρe and ce are the density and wave velocity of the input/output bar;
is the particle velocity in the stress wave; vs is the impact velocity of the striker.
Equation (1) indicates the difference between microscopic and macroscopic parameters and is widely used to predict the input stress in conventional SHPB apparatus. But, this equation is derived from the rod-rod impact based on 1D wave theory and becomes unusable when a large-diameter bar or non-cylindrical striker is used in SHPB system.
To obtain practical relations between the striker velocity and the generated input stress, tests with different impact velocities of cylindrical striker and special shape striker of Fig.1 are conducted. Stress records at the middle of the input bar are taken for analysis. The peak stresses from waves generated by the special shape striker and the average peak stresses from those generated by cylindrical striker are normalized into |σ/(ρece)| and plotted with striker velocity, as shown in Fig.3. It can be seen that, for large-diameter SHPB system with cylindrical striker, Eq.(1) cannot accurately describe the relations between the striker velocity and the generated stress. The generated stress is larger than that predicted theoretically. When the special shape striker in Fig.1 is used, the striker velocity and peak values of the generated stress still have linear relation with the form of
(2)
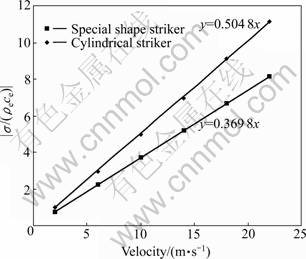
Fig.3 Relations between normalized stress and striker velocity
3 Dynamic response of SHPB under mis- alignment impact by special shape striker
In conventional SHPB system with cylindrical striker, the striker and the input bar are both uniform cylinder with same diameter. The alignment of the striker and input bar can be done easily by keeping them fully contact coaxially. However, when the special shape striker is used, the truncated end of the striker makes the coaxial alignment a bit difficult. Misalignment impacts are prone to happen in tests and cause wave distortion. The dynamic response of SHPB under these misalignment impacts should be investigated so as to identify the system abnormalities by this reason and do corresponding calibration.
Figure 4 schematically shows the normal impact (Fig.4(a)) and misalignment impacts (Fig.4(b) and Fig.4(c)), where the off-axial distance is denoted as L and the oblique angle is denoted as α.
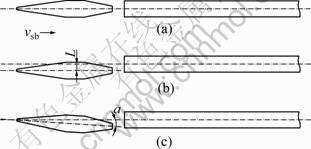
Fig.4 Schematic diagrams of different types of striker impacts: (a) Normal impact; (b) Off-axial impact; (c) Oblique impact
3.1 Off-axial impact
With striker velocity of 10 m/s and off-axial distance of L=6 mm, the axial stresses of surface points are recorded. As the loading condition of the input bar is axially asymmetric in this situation, the stress histories at upper and lower surfaces are both recorded in Fig.5.
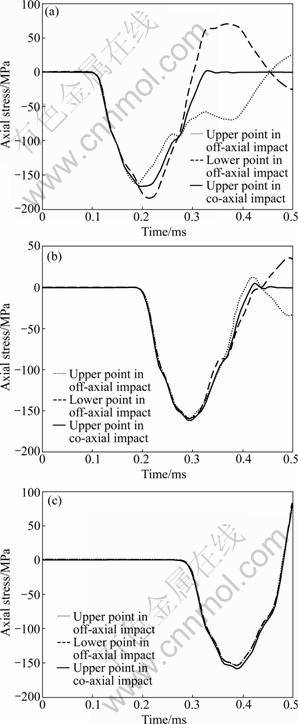
Fig.5 Axial stresses in off-axial impact: (a) At 1/4 bar length; (b) At 1/2 bar length; (c) At 3/4 bar length
It can be seen from Fig.5 that the off-axial impact causes a large wave distortion at the near part of the input bar. Even at the middle of the input bar, the rear part of the stress wave departs from the stress curve by the normal coaxial impact, as shown in Fig.5(b). At 3/4 length of the input bar, the stresses at the upper and lower surface points converge to the same level, but the amplitude shows a bit smaller than that from the normal coaxial impact (Fig.5(c)). So, the off-axial impact not only triggers stress wave distortion, but also leads to larger wave attenuation.
3.2 Oblique impact
For SHPB with special shape striker, the contact area between striker and the internal wall of the firing gun is relatively small. Uneven movement from unstable air pressure in firing gun or local friction on its way may cause the striker to impact the input bar obliquely. Figure 6 gives the axial stresses of surface points on the input bar impacted by the striker with velocity of 10 m/s and oblique angle of 2°.
It can be seen that the oblique impact also triggers large wave distortion. The distortion is so serious that the stress evolution path is totally different from that from the normal coaxial impact. When the axial stresses at the upper and lower surface points converge at 3/4 length of the input bar, their amplitude is obviously smaller than that from the normal impact (Fig.6(c)).
Figures 5 and 6 also indicate that when abnormal stress waves, especially waves with distorted rear parts, are monitored in tests, problems may come from misalignment between the input bar and the striker.
4 Steps of system calibration for SHPB with special shape striker
From the above analyses, SHPB system with a special shape striker has unique responses as compared with conventional SHPB with a cylindrical striker. Although the transmission correction is necessary for both kinds of system, the measurement correction with theoretical prediction from Eq.(1) tends to be unsuitable. In tests with the special shape striker, the checking of the abnormal input stresses appears to be important because of the difficulty in co-axial alignment between the input bar and the striker. Besides, the wave attenuation should be corrected if the damping effect of the bars is strong.
Generally, a SHPB system consists of a striker, an input bar and an output bar, as shown in Fig.7. In tests, the striker is shot out from the gas gun and impacts the input bar. With strain gauges mounted on the middle of the input bar and the output bar, the stress (strain) histories σIncident, σReflected and σTransmitted are measured for calculation. σIncident and σReflected are measured with the same strain gauge.
In order to identify the wave attenuation and distortion for misalignment impact, two additional strain gauges are suggested to glue at the position of 1/4 and 3/4 length of the input bar. The obtained stresses are denoted as σ1/4 and σ3/4.
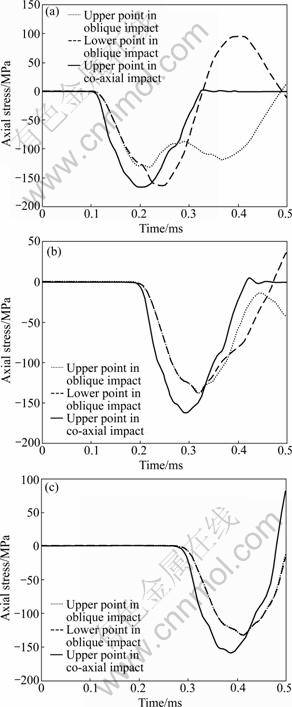
Fig.6 Axial stresses in oblique impact: (a) At 1/4 bar length; (b) At 1/2 bar length: (c) At 3/4 bar length

Fig.7 Sketch of system calibration
Then, the calibration of SHPB system with the special shape striker can be classified into four steps.
Step 1: System adjustment
Tune the brackets under the SHPB to keep the striker, input bar and output bar at the same line axially as much as possible; Make sure that the strain gauges are well glued and the strain meter can get the signals properly.
Step 2: Wave distortion identification
After system adjustment, the striker is fired to impact the input bar which contacts the output bar without specimen, then σ1/4, σ3/4, σIncident and σTransmitted are obtained. In order to distinguish these stresses from those in tests with specimens, they are denoted as
,
and
respectively.
By using the special shape striker, the stress waves on the input bar are expected to have half-sine waveforms, as shown in Fig.2(a). The amplitude can be roughly predicted by Eq.(2) with the striker velocity. And
,
and
should be very similar when there is no damping.
Any discrepancy from waveforms in Fig.2(a) should be checked. The reasons may come from the off-axial impact or oblique impact. Then, the system should be re-adjusted until the discrepancy disappears.
Step 3: Measurement calibration
The measurement correction mainly deals with the attenuation of waves during their propagation. The measurement calibration factor K1 can be defined as
(3)
Then, the incident and reflected waves in normal tests with specimens can be corrected, respectively, as
(4)
(5)
Step 4: Transmission correction
Transmission error mainly comes from the stress loss caused by the little gap between the input bar and the output bar. Besides, the wave attenuation for the traveling distance between specimen and the strain gauge at the middle of the output bar also contributes to the experiment error. By considering the gap effect and the attenuation effect, the transmission calibration factor can be defined as
(6)
So, the measured transmitted wave in tests with specimen should be corrected as
(7)
5 Conclusions
1) The stress generated by the special shape striker has an approximately half-sine waveform and has immunity to dispersion effect.
2) The striker velocity and peak value of stresses generated by the special shape striker have the relation of σ=-0.369 8ρecevs.
3) The misalignment impacts of special shape striker lead to wave distortion and amplitude decrease, which can be used to identify the poor system adjustment.
4) System calibration of SHPB with the special shape striker can be done with four steps: system adjustment, wave distortion identification, measurement calibration and transmission calibration.
References
[1] LI Xi-bing, ZHOU Zi-long, HONG Liang, YIN Tu-bing. Large diameter SHPB tests with a special shaped striker [J]. ISRM News Journal, 2009, 12(1): 76-79.
[2] LI Xi-bing, GU De-sheng. Rock impact dynamics [M]. Changsha: Central South University of Technology Press, 1994: 46-50. (in Chinese)
[3] LOK T S, LI Xi-bing, LIU De-shun. Testing and response of large diameter brittle materials subjected to high strain rate [J]. Journal of Materials in Civil Engineering, 2002, 14(3): 262-269.
[4] LI Xi-bing, ZHOU Zi-long, WANG Wei-hua. Construction of ideal striker for SHPB device based on FEM and neural network [J]. Chinese Journal of Rock Mechanics and Engineering, 2005, 24(23): 4215-4219. (in Chinese)
[5] LI Xi-bing, ZHOU Zi-long, LOK T S. Innovative testing technique of rock subjected to coupled static and dynamic loads [J]. International Journal of Rock Mechanics and Mining Sciences, 2008, 45(5): 739-748.
[6] ZHOU Zi-long, LI Xi-bing, YE Zhou-yuan. Obtaining constitutive relationship for rate-dependent rock in SHPB tests [J]. Rock Mechanics and Rock Engineering, 2010, 43(6): 697-706.
[7] BAZLE A G, SERGEY L L, JOHN W G J. Hopkinson bar experimental technique: A critical review [J]. Appl Mech Rev, 2004, 57(4): 223-250.
[8] ASM Int. High strain rate testing [M]// ASM handbook, Mechanical Testing and Evaluation. Materials Park, 2000: 939-1269.
[9] LUNDBERG B, CARLSSON J, SUNDIN K G. Analysis of elastic waves in non-uniform rods from two-point strain measurement [J]. Journal of Sound and Vibration, 1990, 137(3): 483-493.
[10] BACON C, BRUM A. Methodology for a Hopkinson test with a non-uniform viscoelastic bar [J]. International Journal of Impact Engineering, 2000, 24(3): 219-230.
[11] LIFSHITZ J M, LEBER H. Data processing in the split Hopkinson pressure bar tests [J]. International Journal of Impacting Engineering, 1994, 15(6): 723-733.
[12] LI J C, MA G W. Experimental study of stress wave propagation across a filled rock joint [J]. International Journal of Rock Mechanics and Mining Sciences, 2009, 46(3): 471-478.
(Edited by YANG Bing)
Foundation item: Projects(50904079, 50934006) supported by the National Natural Science Foundation of China; Project(2010CB732004) supported by the National Basic Research Program of China
Received date: 2010-05-11; Accepted date: 2010-09-01
Corresponding author: ZHOU Zi-long, Associate Professor, PhD; Tel: +86-13787202629; E-mail: zlzhou@mail.csu.edu.cn