DOI:10.19476/j.ysxb.1004.0609.2019.07.21
优先络合-水解沉淀法分离铬铁机理
李金辉1,徐志峰1,高 岩2,剧智华1,陈志峰1,李德顺1
(1. 江西理工大学 冶金与化学工程学院,赣州 341000;
2. 河南省冶金研究所有限责任公司,郑州 450053)
摘 要:针对电镀污泥硫酸浸出液中铬铁分离的难题,本文提出“优先络合-水解沉淀”的方法分离铬铁,在去除铁的同时减少铬的损失。采用紫外分光光度法、质谱法对甲酸钠与硫酸铁、硫酸铬以及硫酸铁、硫酸铬混合液的配位机理进行研究,结果表明:铬、铁离子与甲酸钠都可以生成配合物,但相同条件下水溶液中Fe3+优先于Cr3+与甲酸钠形成配合物,反应热效应计算表明该反应都是吸热反应,高温有利于反应的正向移动尤其是铁的络合。通过对甲酸钠用量、反应温度及保温时间等对分离效果的影响进行研究。按HCOO-/Cr3+摩尔比为5.5的量加入甲酸钠,在温度90 ℃下反应6 h后,加碱调节溶液pH值为2.5并搅拌反应30 min,铁沉淀率达93.65%,铬沉淀率仅为13.37%,Cr3+、Fe3+分离效果良好。
关键词:铬铁分离;电镀污泥;络合;水解;沉淀
文章编号:1004-0609(2019)-07-1528-08 中图分类号:TF641 文献标志码:A
我国电镀企业每年产生约40亿m3电镀废水,处理后产生约0.1亿t电镀污泥[1],但因其含有铬等重金属而被列为危险废物[2],而电镀污泥中的铬又是冶炼不锈钢和电镀行业中重要的资源,且我国原生铬资源匮乏,近年消费量的90%以上依靠进口,占世界铬总进口量的93%[3]。因此,对电镀污泥进行资源化,回收提纯其中的铬具有解决环境污染和资源循环利用的双重意义[4-6]。
目前,含铬电镀污泥资源化利用常见的方法有酸浸法、氨浸法、电积法、微生物提取金属、材料化利用等[7-15],但主要回收集中于铜、镍等有价金属分离提取,回收率约90%以上,而约占电镀污泥中金属价值65%的铬进入渣中未得到有效利用[16-17]。铬没有得到循环利用的主要原因之一就是铬与铁性质相差很小,分离提取难度大,因此铬/铁共存就成为了制约电镀污泥中铬元素资源化利用的“瓶颈”[18]。胡国荣等[19]和邬建辉等[20]分别用针铁矿法和莫尔盐结晶法除去铬铁合金浸出液中的铁,虽然实验结果较为理想,但工艺较为复杂,并且无法从根本上解决损失夹带和二次污染问题。SILVA等[21]将Cr3+氧化成Cr6+,利用碱性体系中Cr6+与Fe3+溶解度差异达到分离目的,但是该方法无法回避Cr6+潜在的致癌性和基因的诱变性问题[22-23]。魏君怡等[24]等通过设计离子液体进行萃取分离Cr6+与Fe3+,取得了较好的分离效果,但大规模工业应用还是需要进一步的研究。BEWTRA等[25]利用细菌吸附金属离子作用进行了电镀污泥的处理,但仍存在生物选择性查差和适用条件苛刻等等难题。
通过加入某种络合剂改变溶液中离子的赋存形态,进而影响其在反应过程中的反应行为,是近年来的一个研究热点[26-29]。因此,本研究将络合反应与水解沉淀相结合,提出了“优先络合-水解沉淀”新方法,首先通过加入络合剂与铁、铬等发生络合反应,进而逐步升高pH,使铁优先沉淀的同时尽量避免铬的夹带损失和因为局部pH过高而引起的铬沉淀。本文通过紫外分光光度法和质谱法对甲酸钠与硫酸铬、硫酸铁以及硫酸铬、硫酸铁混合液的反应机理[30-31]进行研究,为铬铁分离提供理论依据,同时研究了不同因素对铬铁分离效果的影响。研究成果可为综合回收混合电镀污泥中的铬开辟了一条高效的新途径,对于混合电镀污泥中铬的无害化和资源化具有重要意义。
1 实验
1.1 实验原料
实验所用甲酸钠、硫酸铬、硫酸铁、氧化镁均为分析纯试剂。
1.2 实验仪器
UV-6300型紫外可见分光光度计(上海美谱达仪器有限公司)、PHSJ-3F型pH计(上海仪电科学仪器股份有限公司)、ReflexⅢ型MALDI-TOF质谱仪(德国Bruker公司)。
1.3 实验方法
基于工程实践中电镀污泥硫酸浸出液中Fe3+、Cr3+的浓度和酸度,实验以Fe3+、Cr3+浓度为3g/L 、pH值为1.7的硫酸铁和硫酸铬溶液及其混合溶液为研究对象,在前期大量探索性实验基础上,分别按HCOO-/Fe3+、HCOO-/Cr3+和HCOO-/(Cr3++Fe3+)摩尔比为5.5的量在硫酸铁、硫酸铬以及硫酸铁和硫酸铬混合溶液中加入甲酸钠,以相对应的未加甲酸钠的溶液为参比,在200~700 nm下对溶液进行全波长扫描获得溶液的紫外-可见光吸收谱图,并结合高能质谱图对其配位机理、配位动力学和热力学进行研究。
配制Fe3+、Cr3+浓度分别为3 g/L的硫酸铬和硫酸铁混合溶液,加入一定量的甲酸钠在一定温度下反应一段时间,然后加入氧化镁调节溶液pH值,过滤分离分别测定溶液中的铁和铬的含量,考察不同工艺条件对铬铁分离效果的影响。
2 结果与分析
2.1 紫外可见吸收光谱法对铁、铬离子与甲酸钠络合研究
按1.3节中的方法配制硫酸铬溶液、硫酸铁溶液及硫酸铬和硫酸铁混合溶液,分别采用上述溶液与甲酸钠混合后在90 ℃恒温搅拌反应,每2 h取一次样品,再以纯硫酸铬溶液、纯硫酸铁溶液及硫酸铬和硫酸铁混合溶液分别作为参比液,通过紫外分光光度计在200~700 nm下扫描得到硫酸铬溶液、硫酸铁溶液及硫酸铬和硫酸铁的混合溶液紫外吸收谱分别如图1、2和3所示。
由图1可知,硫酸铬与甲酸钠混合溶液的紫外吸收谱在波长251 nm附近出现一个强吸收峰,表明该溶液对紫外和可见光吸收的能力发生改变,说明硫酸铬与甲酸钠发生了络合反应,在溶液中生成了新的络合物。因此,在波长251 nm附近出现的强吸收峰则为该络合物的特征吸收峰。

图1 硫酸铬与甲酸钠溶液紫外吸收谱
Fig. 1 UV absorption spectra of chromium sulfate and sodium formate solution
由图2可知,硫酸铁与甲酸钠混合溶液的紫外吸收谱在波长398 nm附近出现一个强吸收峰,表明该溶液对紫外和可见光吸收的能力发生改变,说明硫酸铁与甲酸钠发生了络合反应,在溶液中生成了新的络合物。因此,在波长398 nm附近出现的强吸收峰则为该络合物的特征吸收峰。
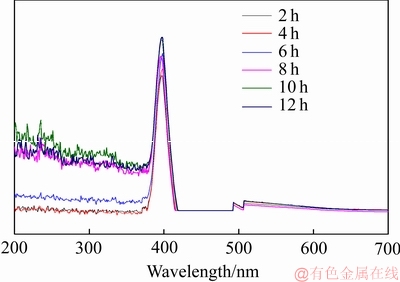
图2 硫酸铁与甲酸钠混合溶液紫外吸收谱
Fig. 2 UV absorption spectra of iron sulfate and sodium formate solution
由图3可知,硫酸铬、硫酸铁混合溶液与甲酸钠混合后的紫外吸收谱在波长409 nm附近出现一个强吸收峰,该吸收峰的出现证明硫酸铬、硫酸铁混合溶液对紫外和可见光吸收的能力发生改变。由于其与硫酸铁与甲酸钠络合的特征吸收峰比较一致,说明在混合体系中主要是铁发生了络合,即铁优先于铬与甲酸钠发生络合作用。在200~380 nm之间无明显的特征吸收峰出现,但随时间的延长,还是出现了一些杂峰。这些杂峰的位置接近铬与甲酸钠络合的特征峰位(251 nm),说明铬也会与甲酸钠络合,但由于受铁的优先络合的影响,铬的络合动力学性质下降了。
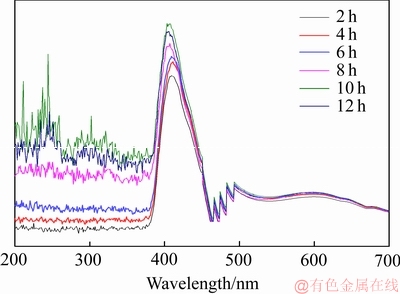
图3 硫酸铬、硫酸铁混合溶液与甲酸钠反应的紫外吸收谱
Fig. 3 UV absorption spectra of reaction between chromium sulfate and ferric sulfate mixed solution with sodium formate
2.2 高能质谱法对铁、铬离子与甲酸钠配位研究
对2.1节中单一硫酸铁与甲酸钠反应的溶液进行质谱分析,结果如图4所示。
由图4可知,单一的纯硫酸铁溶液与甲酸钠反应的产物,得到单一的分子离子峰,m/z的比值为229.8391,而理论产物Fe(HCOOH)3·2H2O的分子量是230,故可推测该分子离子峰是Fe(HCOOH)3·2H2O。
对2.1节中单一硫酸铬与甲酸钠反应的溶液进行质谱分析,结果如图5所示。
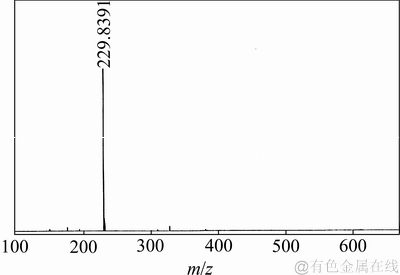
图4 单一硫酸铁溶液与甲酸钠反应的质谱图
Fig. 4 Mass spectrum of single ferric sulfate solution reacted with sodium formate
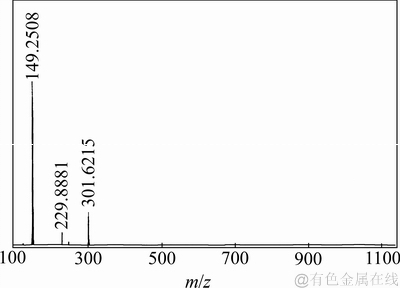
图5 单一硫酸铬溶液与甲酸钠反应的质谱图
Fig. 5 Mass spectra of single chromium sulfate solution reacted with sodium formate
由图5可知,单一的纯硫酸铬溶液与甲酸钠反应的产物,呈现出3种分子离子峰,m/z的比值分别为149.2508、229.8681和301.6215,根据反应物本身的性质,故可推测这3种分子离子峰分别是Cr(OH)3HCOOH、Cr(HCOOH)3·2H2O、Cr2(COOH)2· (OH-)22+·4H2O,显然后两种含量较低。
对2.1中硫酸铬、硫酸铁混合溶液与甲酸钠反应的溶液进行质谱分析,结果如图6所示。
由图6可知,硫酸铁、硫酸铬溶液与甲酸钠反应的产物,得到两种分子离子峰,其中230.0704与图6中的229.8391(Fe(HCOOH)3·2H2O)和图7中的229.8681 (Cr(HCOOH)3·2H2O)基本一致,结合2.1中结论可以推断主要是Fe(HCOOH)3·2H2O。而194.0422可能是由于Cr3+、Fe3+离子均与甲酸形成配合物,相互竞争所生成的某种多金属配合物。
基于紫外和质谱分析检测结果可以发现当铬铁共同存在时,铁优先于铬与甲酸钠发生络合作用,存在形态相对于铬发生较大改变。
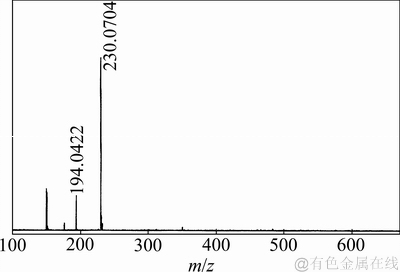
图6 硫酸铁、硫酸铬混合溶液与甲酸钠反应的质谱图
Fig. 6 Mass spectrum of ferric sulfate and chromium sulfate mixed solution with sodium formate
2.3 铬、铁离子与甲酸钠的热力学研究
通过对铬、铁与甲酸钠反应进行热力学研究,进而指导工艺条件参数的选择。由范特霍夫方程变型得
,以最大吸光度(A∞)代替
从而求得反应的热力学焓变
。
2.3.1 铬离子与甲酸钠的反应热力学研究
按1.3节中的方法将硫酸铬溶液与甲酸钠混合,放入反应器中,分别在30、50、70和90 ℃下进行反应12 h,在251 nm波长下的吸光度,以lg A∞对1/T作图,通过计算机对一次方程进行线性拟合,得到一条直线,实验结果如图7所示。
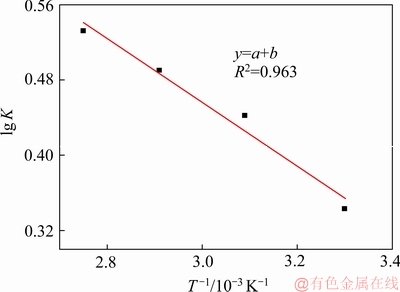
图7 硫酸铬的lg K-1/T图
Fig. 7 Diagram of lg K-1/T of chromium sulfate
由图7可以看出,拟合程度为0.963,拟合程度较好,直线斜率为-339.178,由
得,
=2.82 kJ。
2.3.2 铁离子与甲酸钠的反应热力学研究
将硫酸铁溶液与甲酸钠混合,放入反应器中,分别在30、50、70和90 ℃下反应12 h,在398 nm波长下的吸光度,以lg A∞对1/T作图,通过计算机对一次方程进行线性拟合,得到一条直线,实验结果如图8所示。
由图8可以看出,拟合程度为0.9767,直线斜率为-2882.88913由
得,
=23.983 kJ。
综上所述,可以发现上述络合反应均为吸热反应,并且铁与甲酸钠络合的热效应大于铬与甲酸钠络合热效应,说明高温更有利于铁的络合。
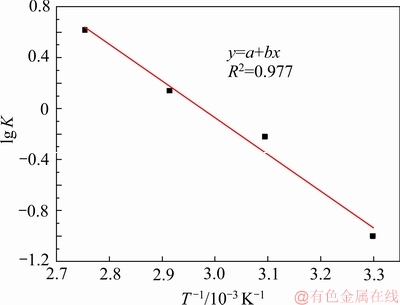
图8 硫酸铁的lg K-1/T图
Fig. 8 Diagram of lg K-1/T of iron sulfate
2.4 络合-沉淀分离铬铁工艺研究
采用条件实验考察络合-沉淀分离铬铁过程中甲酸钠用量、反应温度及保温时间对分离效果的影响,实验初始配制Fe3+、Cr3+浓度为3 g/L,采用氧化镁调节溶液pH,搅拌转速350 r/min,探究甲酸钠络合-沉淀分离铬铁方法的最优工艺条件。
2.4.1 络合剂用量的影响
依次向Cr3+、Fe3+的溶液中加入不同量的甲酸钠,控制溶液初始pH=1.7,加热溶液至90 ℃,反应6 h,络合反应结束后,加入氧化镁调节溶液pH至2.5,在350 r/min速度下搅拌反应30 min,考察络合剂用量对铬铁分离效果的影响,实验结果如图9所示。
由图9可见,随着n(HCOO-)/n(Cr3+)由1增大至5.5时,铬的损失率由31.44%降至13.37%,铁的沉淀率均保持在93%以上。进一步增大甲酸钠加入量,铬、铁的沉淀率均呈现降低趋势。这可能是因为Fe3+与甲酸钠发生络合,导致其水解沉淀速度变缓,沉淀颗粒更容易长大,结晶度有所提高。实验操作也表明,“先络合后水解”相比较直接水解,其沉淀过滤性能大大加强,在沉淀过程中对铬的夹带受到抑制,因而铬的损失显著降低。增大n(HCOO-)/n(Cr3+)至11,铁的沉淀率降为78.82%,降幅明显,这是由于甲酸钠的大量加入使得Fe3+发生强络合,其沉淀动力学过程被抑制。尽管此时铬沉淀率降至8.66%,但铬损失率变化幅度较小,因而甲酸钠用量按n(HCOO-)/n(Cr3+)=5.5为宜。
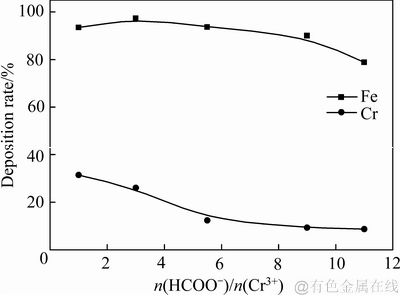
图9 络合剂用量对铬、铁分离影响
Fig. 9 Effect of amount of complexing agent on separation of chromium and iron
2.4.2 络合温度的影响
按n(HCOO-)/n(Cr3+)=5.5向Cr3+、Fe3+的溶液中加入甲酸钠,控制溶液初始pH=1.7,加热溶液至实验温度,反应6 h,络合反应结束后,将溶液升温至90 ℃,加入氧化镁调节溶液pH=2.5,在350 r/min速度下搅拌反应30 min,考察不同络合反应温度对铬铁络合效果的影响,实验结果如图10所示。
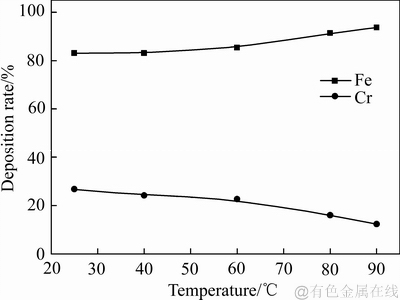
图10 温度对铬、铁分离影响
Fig. 10 Effect of temperature on separation of chromium and iron
由图10可见,随着络合反应温度升高,铁的沉淀率不断升高。主要原因是当温度较高时,会有少量的铁生成铁钒渣沉淀,即加入碱调pH之前就有部分铁进入渣相。2.3节的热力学研究表明络合反应为吸热反应,升高温度有利于络合物的生成,因此进一步由图中趋势可推断,络合温度升高有利于减小铬损失,但为减少操作能耗,温度选择为90 ℃为宜。
2.4.3 络合时间的影响
按n(HCOO-)/n(Cr3+)=5.5向Cr3+、Fe3+的溶液中加入甲酸钠,加入过程保持溶液pH=1.7,加热溶液至90 ℃开始计时,反应一定时间。保持温度不变加入氧化镁调节至溶液pH=2.5,在350 r/min速度下搅拌反应30 min,实验结果图11所示。
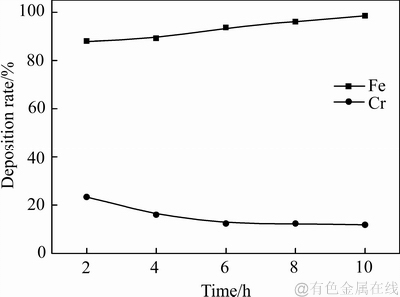
图11 络合时间对铬、铁分离影响
Fig. 11 Effect of complexing time on separation of chromium and iron
由图11可见,随着络合时间延长,铁的沉淀率不断上升,络合反应时间为10 h,铁沉淀率高达98.53%,此时沉淀终液铁浓度为0.04 g/L。随络合时间由2 h延长至6 h,铬沉淀率由23.35%降至13.37%,进一步延长络合时间在6~10 h,铬沉淀率无明显变化,综合考虑甲酸钠络合反应时间选择6 h。
3 结论
1) 水溶液中的铁离子与甲酸钠形成络合物的能力比铬离子更强,即当混合溶液中同时存在铬、铁离子时,铁离子将优先与甲酸钠发生络合反应,但铬离子的存在将会对铁离子与甲酸的络合反应产生影响。
2) 硫酸铬与甲酸钠的反应、硫酸铁与甲酸钠的反应热力学焓变
都是正值,故两个反应均为吸热反应,而升高温度有利于平衡的正向移动;硫酸铁与甲酸钠的反应热大于硫酸铬与甲酸钠的反应热,说明温度对铁和甲酸络合的影响要大于铬和甲酸钠的络合,高温更加有利于铁的络合。
3) 对甲酸钠、氧化镁联合使用络合-沉淀分离铬、铁工艺进行了实验研究,其最优工艺条件为:按n(HCOO-)/n(Cr3+)=5.5的量向溶液中加入甲酸钠,加入过程保持溶液pH=1.7,90 ℃下反应6 h,保持温度不变加入氧化镁调节溶液pH=2.5,搅拌反应30 min,铁沉淀率可达93.65%,铬沉淀率仅为13.37%,相较于传统加碱分离铬铁过程铬的沉淀率为35%有很大改善,Cr3+、Fe3+分离效果大大改善。
REFERENCES
[1] 袁文辉, 徐志峰. 混合电镀污泥中铬铁的选择性分离工艺[J]. 有色金属(冶炼部分), 2016(9): 55-58.
YUAN Wen-hui, XU Zhi-feng. Selective separation of ferrochromium in mixed electroplating sludge[J]. Non-ferrous Metals (Smelting Section), 2016(9): 55-58.
[2] 江秋月. 高铅硅锌渣绿色回收锗铟的新工艺研究[J]. 有色金属(冶炼部分), 2014(4): 51-53.
JIANG Qiu-yue. High-lead silicon zinc slag green germanium indium recovery of new technology research[J]. Nonferrous Metals (Smelting Section), 2014(4): 51-53.
[3] 潘自维, 王大卫, 杜 浩,陈 刚,郑诗礼,王少娜,张 懿. 活性炭强化钒渣中钒、铬提取技术[J]. 中国有色金属学报, 2014, 24(8): 2171-2180.
PAN Zi-wei, WANG Da-wei, DU Hao, CHEN Gang, ZHENG Shi-li, WANG Shao-na, ZHANG Yi. Technique of extracting vanadium and chromium from vanadium slag by activated carbon[J]. The Chinese Journal of Nonferrous Metals, 2014, 24(8): 2171-2180.
[4] 李 磊, 唐 伟, 朱渊博,顾文秀,王海军,邹路易. 电镀污泥的铁氧体化研究[J]. 现代化工, 2013, 33(10): 62-65.
LI Lei, TANG Wei, ZHU Yuan-bo, GU Wen-xiu, WANG Hai-jun, ZOU Lu-yi. Studies on ferrite of electroplating sludge[J]. Modern Chemical Industry, 2013, 33(10): 62-65.
[5] 康 义. 我国有色金属工业全面协调可持续发展值得重视的若干问题[J]. 中国钨业, 2004, 19(5): 15-17.
KANG Yi. Nowadays, it is necessary to pay attention to the all-round, coordinated and sustainable development of China’s nonferrous metals industry[J]. China Tungsten Industry, 2004, 19(5): 15-17
[6] ZHANG Yi, LI Zuo-hu, QI Tao, ZHENG Shi-li, LI Hui-quan, XU Hong-bin. Green manufacturing process of chromium compounds[J]. Environmental Progress and Sustainable Energy, 2005, 24(1): 44-50.
[7] SILVAJ E,PAIVAA P,SOARES D, LABRINCHA J A, CASTRO F. Solvent extraction applied to the recovery of heavy metals from galvanic sludge[J]. Journal of Hazardous Materials, 2005, B120: 113-118.
[8] SILVA J E, SOARES D, PAIVAA P, LABRINCHA J A, CASTRO F. Leaching behaviour of a galvanic sludge in sulphuric acid and ammoniacal media[J]. Journal of Hazardous Materials, 2005, 121: 195-202.
[9] 郑 顺, 李金辉, 李洋洋, 熊道陵, 杨金鑫. 电镀污泥氯化焙烧-弱酸浸出工艺研究[J]. 矿冶工程, 2014, 34(6): 105-109.
ZHENG Shun, LI Jin-hui, LI Yang-yang, XIONG Dao-ling, YANG Jin-xin. Electroplating sludge chlorination roasting- weak acid leaching process[J]. Mining and Metallurgical Engineering, 2014, 34(6): 105-109.
[10] 陈 娴, 程洁红, 周全法, 殷 燕, 张雨晴, 唐雪弢. 火法-湿法联合工艺回收电镀污泥中的铜[J]. 环境工程, 2012, 30(2): 68-71.
CHEN Xian, CHENG Jie-hong, ZHOU Quan-fa, YIN Yan, ZHANG Yu-qing, TANG Xue-tao. Fire-wet combined recovery of copper plating electroplating sludge[J]. Environmental Engineering, 2012, 30(2): 68-71.
[11] 郭学益, 石文堂, 李 栋, 田庆华. 采用旋流电积技术从电镀污泥中回收铜和镍[J]. 中国有色金属学报, 2010, 20(12): 2425-2430.
GUO Xue-yi, SHI Wen-tang, LI Dong, TIAN Qing-hua. Recovery of copper and nickel from electroplating sludge using cyclone electrowinning technology[J]. The Chinese Journal of Nonferrous Metals, 2010, 20(12): 2425-2430.
[12] ZHANG Yi,WANG Zhi-kuan,XU Xia,CHEN Yong-qi,QI Tao, ZHANG Yi,WANG Zhi-kuan,XU Xia. Recovery of heavy metals from electroplating sludge and stainless steel pickle waste liquid by ammonia leaching method[J]. Journal of Environmental Sciences, 1999, 11(3): 381-384.
[13] 程洁红, 陈 娴, 孔 峰, 周全法. 氨浸-加压氢还原法回收电镀污泥中的铜和镍[J]. 环境科学与技术, 2009, 33(6): 135-137.
CHENG Jie-hong, CHEN Xian, KONG Feng, ZHOU Quan-fa. Recovery of copper and nickel from electroplating sludge by ammonia leaching-pressurized hydrogen reduction[J]. Environmental Science and Technology, 2009, 33(6): 135-137.
[14] 郭学益, 石文堂, 李 栋, 田庆华. 从电镀污泥中回收镍、铜和铬的工艺研究[J]. 北京科技大学学报, 2011, 33(3): 328-333.
GUO Xue-yi, SHI Wen-tang, LI Dong, TIAN Qing-hua. Recycling process of nickel, copper and chromium from the electroplating sludge[J]. Journal of University of Science and Technology Beijing, 2011, 33(3): 328-333.
[15] 陈 可, 石太宏, 王卓超, 苏 瞒. 电镀污泥中铬的回收及其资源化研究进展[J]. 电镀与涂饰, 2007, 26(5): 43-46.
CHEN Ke, SHI Tai-hong, WANG Zhun-chao, SU Man. Chromium recovery from electroplating sludge and its resource utilization[J]. Electroplating and Finishing, 2007, 26(5): 43-46.
[16] 袁文辉, 王成彦, 徐志峰, 陈剑峰. 含铬电镀污泥资源化利用技术研究进展[J]. 湿法冶金, 2013, 32(5): 284-287.
YUAN Wen-hui, WANG Cheng-yan, XU Zhi-feng, CHEN Jian-feng. Research progress of resource utilization technology of chromium electroplating sludge[J]. Hydrometallurgy of China, 2013, 32(5): 284-287.
[17] 王成彦, 邱定蕃, 徐盛明, 金属二次资源循环利用意义现状及亟需关注的几个领域[J]. 中国有色金属学报, 2008, 18(S1): s359-s366.
WANG Cheng-yan, QIU Ding-fan, XU Sheng-ming. Recycling significance of metal secondary resources, the status quo and the need to pay attention to several areas[J]. The Chinese Journal of Nonferrous Metals, 2008, 18(S1): 359-366.
[18] LONG H M, MENG Q M, WANG P. Preparation of chromium-iron metal powder from chromium slag by reduction roasting and magnetic separation[J]. Journal of Iron and Steel Research International, 2015, 9(22): 771-776.
[19] 胡国荣, 李 国, 邓新荣, 彭忠东,曹雁冰. 针铁矿法从铬铁合金硫酸浸出液中除铁[J]. 湿法冶金, 2006, 25(4): 195-200.
HU Guo-rong, LI Guo, DENG Xin-rong, PENG Zhong-dong, CAO Yan-bing. Iron removal from extract of ferrochromium sulfate by goethite[J]. Hydrometallurgy of China, 2006, 25(4): 195-200.
[20] 邬建辉, 阳伦庄, 湛 菁, 张传福. 铬铁合金中的铬、铁分离研究[J]. 湿法冶金, 2011, 30(1): 51-56.
WU Jian-hui, YANG Lun-zhuang, ZHAN Jing, ZHANG Chuan-fu. Research on separation of chromium and iron in waste ferrochromium alloy[J]. Hydrometallurgy of China, 2011, 30(1): 51-56.
[21] DE SOUZA E SILVA P T, DE MELLO N T, DUARTE M M M, CONCEICAO M, MONTENEGRO B S M, ARAUJO A N, DE BARROS NETO B, DA SILVA V L. Extraction and recovery of chromium from electroplating sludge[J]. Journal of Hazardous Materials, 2006, 128(1): 39-43.
[22] 柴立元, 刘 恢, 闵小波, 郑 粟, 王云燕. 改性活性污泥处理含铬废水[J]. 中国有色金属学报, 2005, 15(9): 1458-1464.
CHAI Li-yuan, LIU Hui, MIN Xiao-bo, ZHENG Su, WANG Yun-yan. Determination of chromium containing wastewater by modified activated sludge[J]. The Chinese Journal of Nonferrous Metals, 2005, 15(9): 1458-1464.
[23] 柴立元, 许友泽, 王海鹰, 向仁军, 杨志辉, 苏长青, 王 兵. Pannonibacter phragmitetus对Cr(Ⅵ)污染土壤的修复效应[J].中国有色金属学报, 2009, 19(12): 2230-2236.
CHAI Li-yuan, XU You-ze, WANG Hai-ying, XIANG Ren-jun, YANG Zhi-hui, SU Chang-qing, WANG Bing. Remediation effect of Pannonibacter phragmitetus on Cr(Ⅵ) contaminated soil[J]. The Chinese Journal of Nonferrous Metals, 2009, 19 (12): 2230-2236.
[24] 魏君怡, 李 勇, 薛向欣. 基于离子液体的“可设计性”和“软酸”性质萃取分离电镀污泥中Cr6+/Fe3+[J]. 化工学报, 2017, 68(9): 3451-3458.
WEI Jun-yi, LI Yong, XUE Xiang-xin. Cr6+/Fe3+ extraction separation from electroplating sludge based on design ability and soft acidity of ionic liquids[J]. CIESC Journal, 2017, 68(9): 3451-3458.
[25] BEWTRA J K, BISWAS N, HENDERSON W D, NICELL J A. Recent advances in treatment of selected hazardous wastes[J]. Water Pollution Research of Canada, 1995, 30(1): 115-125.
[26] 韩新罡, 席晓丽, 马立文, 聂祚仁, 周志理. 配合-沉淀体系中铁与钴、镍的分离性能[J]. 中国有色金属学报, 2013, 23(11): 3218-3224.
HAN Xin-gang, XI Xiao-li, MA Li-wen, NIE Zuo-ren, ZHOU Zhi-li. Separation properties of ion to cobalt and nickel in complexation-precipitation system[J]. The Chinese Journal of Nonferrous Metals, 2013, 23(11): 3218-3224.
[27] ROYA, EATON H C, CARTLEDGE F K, TITTLEBAUM M E.The effect of sodium sulfate on solidification electroplating/stabilization of a synthetic electroplating sludge in cementitious binders[J]. Journal of Hazardous Materials, 1992, 30(3): 23-26.
[28] 李建文, 黄 坚. 铬的形态分析研究与展望[[J]. 冶金分析, 2006, 26(5): 38-43.
LI Jian-wen, HUANG Jian. Studies and prospect on the speciation analysis of chromium[J]. Metallurgical Analysis, 2006, 26(5): 38-43.
[29] 马立文, 聂祚仁, 席晓丽, 韩新罡. Co-Ni-Fe-Mn 配合-沉淀体系的平衡热力学[J]. 中国有色金属学报, 2013, 23(2): 516-527.
MA Li-wen, NIE Zuo-ren, XI Xiao-li, HAN Xin-gang. Thermodynamic equilibrium in Co-Ni-Fe-Mn complexation precipitation system[J]. The Chinese Journal of Nonferrous Metals, 2013, 23(2): 516-527
[30] 郑怀礼, 谢礼国, 高朝勇, 孙秀萍, 杨 铀, 唐 雪. 红外光谱法及单晶X衍射法研究 Fe(Ⅲ)水解形态分布[J]. 光谱学与光谱分析, 2009, 29(2): 540-543.
ZH ENG Huai-li, XIE Li-guo, GAO Chao-yong, SUN Xiu-ping, YANG You, TANG Xue. Study on the hydrolysis distribution of ferric saline by infrared spectrophotometry and single crystal X-ray diffraction method[J]. Spectroscopy and Spectral Analysis, 2009, 29(2): 540-543.
[31] CC K U, WANG H P, LEE P H, HSIAO M C, HUANG H L. Speciation of chromium in an electroplating sludge during thermal stabilization[J]. Bulletin of Environmental Contamination and Toxicology, 2003, 71(4): 860-865.
Mechanism of ferro-chrome separation by prior complexing-hydrolysis precipitation method
LI Jin-hui1, XU Zhi-feng1, GAO Yan2, JU Zhi-hua1, CHEN Zhi-feng1, LI De-shun1
(1. School of Metallurgical and Chemical Engineering, Jiangxi University of Science and Technology, Ganzhou 341000, China;
2. Henan Institute of Metallurgy Co., Ltd., Zhengzhou 450053, China)
Abstract: Aiming at the separation problem of iron and chromium in sulfuric acid leaching solution of electroplating sludge, this paper presented a method of “preferential complexing-hydrolysis precipitation” to separate ferro-chrome and reduce the loss of chromium while removing iron. The complexing mechanism of sodium formate with ferric sulfate, chromium sulfate, mixed solution of ferric sulfate and chromium sulfate was studied comprehensively by UV spectrophotometry and mass spectrometry. The results show that both chromium and ferric ions can form complexes with sodium formate. But under the same conditions, the complexing of Fe3+ and sodium formate in aqueous solution is prior to that of Cr3+. The calculation of reaction heat effect shows that these reactions are endothermic and the high temperature is favorable for these reactions especially ferric than chromium. The effects of amount of sodium formate, reaction temperature and holding time on the separation efficiency between iron and chromium were studied. The results show that when the molar ratio of HCOO-/Cr3+ is 5.5, reaction temperature is 90 ℃, holding time is 6 h, the pH value of the solution is adjusted to 2.5 with addition of alkali and the reaction time is 30 min, the iron precipitation rate is 93.65%, the chromium precipitation rate is only 13.37%. The separation effect of Cr3+ and Fe3+ is good.
Key words: separation of iron and chromium; electroplating sludge; complexing; hydrolysis; precipitation
Foundation item: Project(51464018) supported by the National Natural Science Foundation of China; Project (20161ACG70010) supported by the Jiangxi Science and Technology Department, China; Project (182102210361) supported by the Science and Technology Research Project of Henan Province, China
Received date: 2018-04-27; Accepted date: 2018-08-20
Corresponding author: XU Zhi-feng; Tel: +86-797-8312047; E-mail: xu.zf@jxust.edu.cn
(编辑 何学锋)
基金项目:国家自然科学基金资助项目(51464018);江西省科技厅项目(20161ACG70010);河南省科技攻关项目(182102210361)
收稿日期:2018-04-27;修订日期:2018-08-20
通信作者:徐志峰,教授,博士;电话:0797-8312047;E-mail:xu.zf@jxust.edu.cn