J. Cent. South Univ. Technol. (2010) 17: 223-227
DOI: 10.1007/s11771-010-0034-2 
Effects of KMnO4 on microstructure and corrosion resistance of microarc oxidation coatings on 2024 aluminum alloy
YANG Wei(杨巍), JIANG Bai-ling(蒋百灵), SHI Hui-ying(时惠英), XIAN Lin-yun(鲜林云)
School of Materials Science and Engineering, Xi’an University of Technology, Xi’an 710048, China
? Central South University Press and Springer-Verlag Berlin Heidelberg 2010
Abstract: Microarc oxidation (MAO) coatings were prepared on 2024 aluminum alloy in a Na2SiO3-KOH electrolyte with KMnO4 addition varying from 0 to 4 g/L. The microstructure and phases of the coatings were characterized by scanning electron microscopy (SEM) and X-ray diffractometry (XRD), respectively. The corrosion resistance of MAO coatings was evaluated by electrochemical potentiodynamic polarization in 5% (mass fraction) NaCl solution. The results show that when KMnO4 is added into base electrolyte, the growth speed of oxide coatings is increased obviously. The main phase of oxide coatings is Al2O3, and the contents of MnO2 and Mn2AlO4 phases are increased at the top of oxide coatings with increasing the concentration of KMnO4. The solute elements participate in forming the oxide coatings. When a proper concentration of KMnO4 (2.5 g/L) is added into the base solution, the micropores of the MAO coatings are small and compact, and the corrosion resistance of oxide coatings is increased largely.
Key words: 2024 aluminum alloy; KMnO4; microarc oxidation; microstructure; corrosion resistance
1 Introduction
Microarc oxidation (MAO) is a novel surface technique [1-4], which has been widely used to prepare oxide coatings on the surfaces of valve metals and their alloys, e.g., Al, Mg and Ti [5]. In recent years, the MAO technique has aroused researchers’ extensive interest [6-7]. The reasons can be concluded that theoretical feasibility of clean disposal meets the demands of environmental protection for light metal, and also the ceramic characters of the product meet the demands of surface properties for light metal. So it has been a potential surface technique.
The MAO coating on aluminum alloy has strong adhesion, high wear resistance and high corrosion resistance [3, 8-9]. So, it can be used in many fields such as engine cylinder, naval ships and craftwork [10-11]. However, up to now, the way of acquiring proper thickness of oxide coatings on aluminum alloy is to increase the voltage or prolong the disposal time. Generally, the voltage should reach 550 V, and the disposal time should exceed 30 min in MAO process. Thus, the growth speed of oxide coatings on aluminum alloy is low and its power consumption is high. Furthermore, it is well known that high voltage and long disposal time in MAO process will result in deteriorating the surface features and reducing the properties of oxide coatings, such as wear resistance and corrosion resistance [12-13]. Based on the problems of MAO disposal on aluminum alloy, in this work, the electrolyte was further developed by adding KMnO4 into the base electrolyte for increasing the magnitude of oxygen and improving the combining chances of oxygen and aluminum, and the MAO process was carried out at low voltage. Also the microstructure, phase and corrosion resistance of the oxide coatings formed in this modified electrolyte were studied.
2 Experimental
Circular substrates of d25 mm×5 mm cut from a 2024 aluminum alloy stick were used as raw materials, which were polished with 800# abrasive papers. The oxide coatings were fabricated with a homemade alternating-current (AC) MAO system. The device consisted of a potential adjustable AC power supply up to 750 V, a stirring system and a cooling system. The output of the energy adopted constant voltage mode. The MAO parameters were as follows: voltage, 350 V; frequency, 400 Hz, and duty cycle, 10. The solution temperature was controlled at 35 ℃.
The base electrolyte was prepared from distilled water containing Na2SiO3 (6 g/L) and KOH (2.5 g/L). The microstructure, phase and corrosion resistance of oxide coatings formed in the electrolytes with addition of different concentrations of KMnO4, 0 (group 1), 1.0 g/L (group 2), 2.5 g/L (group 3) and 4.0 g/L (group 4) were studied. In this work, growth speed of oxide coatings was investigated, and in each group, five specimens were treated in five different times, 3, 5, 8, 12, and 20 min. Then, the thickness of oxide coatings was measured using the TT230 eddy-current coating-thickness measurement gauge. The surface morphology was observed using a JEOL JSM-6700F scanning electron microscope (SEM), and the surface phase of the coating was analyzed by using X-ray diffractometry (XRD). The corrosion resistance of oxide coatings formed in the electrolytes with different concentrations of KMnO4 was tested by electrochemical potentiodynamic polarization in 5% NaCl solution. During the process of test, the specimen was the working electrode; the platinum sheet was auxiliary electrode; and the saturated calomel electrode was the reference electrode. The scanning speed was 5 mV/s.
3 Results and discussion
3.1 Growth regularity of oxide coatings
In this experiment, the thickness of oxide coatings treated in the base electrolyte for 20 min is only about 1.2 μm. So we mainly discuss the growth regularity of the coatings formed in the electrolyte with different concentrations of KMnO4 (Fig.1). It can be seen that the growth speed of oxide coatings is similar while the concentration of KMnO4 is 1.0 g/L or 2.5 g/L. But it can be improved greatly with increasing the concentration of KMnO4 to 4.0 g/L. Concretely, the thickness of the coatings is 4.6 and 17.8 μm when the oxidation time is 3 and 20 min, respectively. The result illustrates that the growth speed of oxide coatings can be accelerated obviously as the electrolyte contains KMnO4. The reason may be that a lot of oxygen is provided in the MAO process, which increases the combining chances of Al substrate and oxygen. Besides, in each group, it can be also seen that the growth speed of oxide coatings is fast first and then slow. This indicates that oxide coatings are formed easily at the beginning of MAO process, and as the oxide coatings becomes thick, it will be formed difficultly.
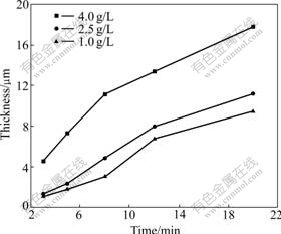
Fig.1 Dependence of MAO coating thickness on concentration of KMnO4 in electrolytes
3.2 Effect of KMnO4 on microstructure and composition of MAO coatings
Fig.2 illustrates the surface features of oxide coatings treated for 12 min in electrolytes with different concentrations of KMnO4. It is clear that the surface morphologies are changed significantly when adding KMnO4 into the base electrolyte. It can be noted that the oxide coatings is thinner, and the nicks of Al substrate or some different dimensions of pores can be seen in certain places on the sample surface (Fig.2(a)). This means that the coating grows very slowly, namely, the oxide coating is prepared difficultly in this base electrolyte. With the addition of KMnO4 into the base electrolyte, different surface appearances can be seen. It is apparent that some islands (regionⅠ) and many micropores (ranging from 1 to 4 ?m) are found on the surface of oxide coating (Fig.2(b)). When the concentration of KMnO4 is added to 2.5 g/L, the surface feature of oxide coating is uniformly porous and the micropores are small and compact (Fig.2(c)). But when the concentration of KMnO4 is increased to 4.0 g/L, the surface feature goes worse (Fig.2(d)). Some larger islands (region Ⅱ) occur at the top of oxide coatings. Several crossed micro- cracks appear (region Ⅲ) and others run through the micropores (region Ⅳ). The reason may be that, from the point of phenomenon of MAO disposal, it can be known that oxidation reaction is poignant with too much KMnO4 added into the base electrolyte, which results in acute splash of molten substances, and then a large number of micropores and cracks are formed on the coating surface.
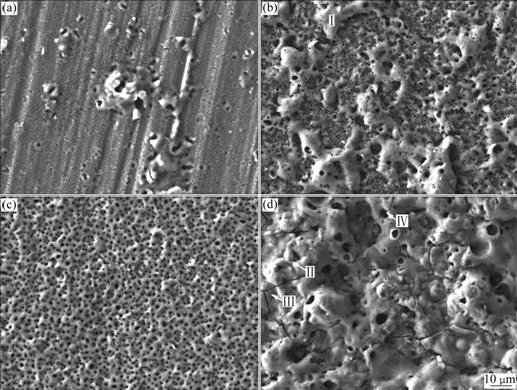
Fig.2 Surface morphologies of MAO coatings formed in electrolytes with different concentrations of KMnO4: (a) 0 g/L; (b) 1.0 g/L; (c) 2.5 g/L; (d) 4.0 g/L
EDS analysis was conducted on the coatings formed in different conditions. The results are shown in Table 1. It can be seen that the elements at the top of oxide coatings are mainly Al, O, Si and Mn. The content of O is increased largely on the surface coating formed in the electrolyte with KMnO4 addition. But the content of Al from the substrate is decreased linearly with increasing the concentration of KMnO4, and the contents of the elements (Si and Mn) from the electrolyte are increased obviously. So, it is believed that a large amount of O is generated during the MAO process when adding KMnO4 into the base electrolyte is provided for the coating growth, and then a lot of decompounding products on the sample surface are increased. So, the components of oxide coatings are changed.
Table 1 Mole fractions (%) of different elements of MAO coatings formed in NaSiO3-KOH electrolyte with KMnO4 addition
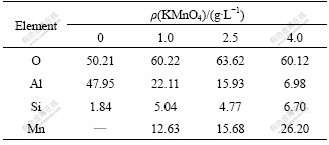
The XRD patterns for MAO coatings formed on 2024 aluminum alloy in different electrolytes are shown in Fig.3, which reveals that Al2O3 is the main phase of the oxide coatings, and the peaks of MnO2 are strongly defined in the XRD patterns with increasing the concentration of KMnO4. Also, a small amount of Mn2AlO4 phase is defined, especially when the concentration of KMnO4 is increased to 4.0 g/L. Compared with the oxide coatings formed in the electrolytes with KMnO4 addition, the coating formed in the base electrolyte mostly consists of Al2O3 phase. So, it is believed that the element of Mn from KMnO4 strongly participates in forming the oxide coating. By analyzing the forming mechanism of the oxide coatings, the reason why Mn exists in the coating surface can be inferred. It is well known that in the process of anodic reaction, the amount of MnO4- from the electrolyte is transferred to the anode (aluminum alloy), and the instantaneously sintering temperature in microarc discharge channel can exceed 2 000 ℃ [14-15]. So, the decomposition reaction of MnO4- is carried out easily and the phases of MnO2 and O2 are formed. Also, Mn2AlO4 phase is formed at the high temperature and pressure. As a result, MnO2 is deposited at top of the oxide coatings in the electric field environment and the growth speed of oxide coatings is improved by increasing the amount of O from the electrolytes.
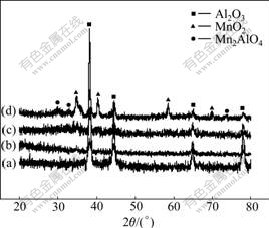
Fig.3 XRD patterns of MAO coatings formed in electrolytes with different concentrations of KMnO4: (a) 0 g/L; (b) 1.0 g/L; (c) 2.5 g/L; (d) 4.0 g/L
3.3 Electrochemistry analysis of oxide coatings
The morphology, phase and growth speed of MAO coatings can be changed with increasing the concentration of KMnO4, and they are bound to influence the corrosion resistance of the oxide coatings. Fig.4 demonstrates the polarization curves of oxide coatings in the electrolytes with different concentrations of KMnO4. It can be obtained that the corrosion current density of oxide coatings formed in the base electrolyte is 2.52×10-2 A/dm2, and it can be reduced to 4.48×10-4 A/dm2 when the concentration of KMnO4 is 2.5 g/L. It is well known that the corrosion current density of coated specimens is often used to characterize the corrosion protective property [16]. Also it is believed that the corrosion resistance property of the coatings can be improved by preventing eroding Cl- anions into the substrates [17], when increasing the compactness and the thickness of the coatings. In this experiment, the growth speed of oxide coatings is increased and the surface morphology is compact when the concentration of KMnO4 is 2.5 g/L. So a perfect corrosion resistance property of oxide coatings formed in the electrolyte with KMnO4 addition is shown.
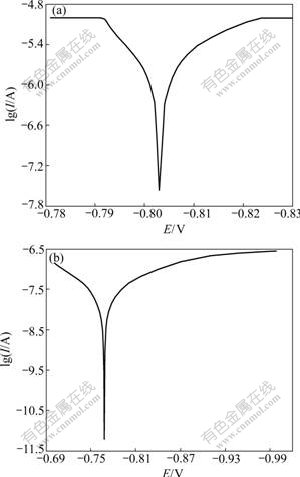
Fig.4 Polarization curves of MAO coatings formed in electrolytes with different concentrations of KMnO4 in 5% NaCl solution: (a) 0 g/L; (b) 2.5 g/L
4 Conclusions
(1) The growth speed of oxide coatings is increased rapidly with increasing the concentration of KMnO4. The micropores of the coatings are small and compact when the concentration of KMnO4 is 2.5 g/L.
(2) The phases of Al2O3, MnO2 and Mn2AlO4 are found on the oxide coating surface formed in the electrolyte with KMnO4 addition. When increasing the concentration of KMnO4 into the base electrolyte, the content of MnO2 is linearly increased.
(3) The corrosion current density of oxide coating is reduced to 4.48×10-4 A/dm2 when the concentration of KMnO4 is 2.5 g/L. Compared with that of the oxide coatings formed in the base electrolyte, the corrosion resistance of this coating is improved largely.
References
[1] XUE Wen-bin, SHI Xiu-ling, HUA Ming, LI Yong-liang. Preparation of anti-corrosion films by microarc oxidation on an Al-Si alloy [J]. Appl Surf Sci, 2007, 253: 6118-6124.
[2] BUTYAGIN P I, KHOKHRYAKOV Y V, MAMAEV A I. Microplasma systems for creating coatings on aluminium alloys [J]. Mater Letts, 2003, 57: 1748-1751.
[3] TIAN Jun, LUO Zhuang-zi, QI Shang-kui, SUN Xiao-jun. Structure and antiwear behavior of micro-arc oxidized coatings on aluminum alloy [J]. Surf Coat Technol, 2002, 154: 1-7.
[4] CHEN Fei, ZHOU Hai, YAO Bin, QIN Zhen, ZHANG Qing-feng. Corrosion resistance property of the ceramic coating obtained through microarc oxidation on the AZ31 magnesium alloy surfaces [J]. Surf Coat Technol, 2007, 201: 4905-4908.
[5] YEROKHIN A L, NIE X, LEYLAND A, MATTHEWS A, DOWEY S J. Plasma electrolysis for surface engineer [J]. Surf Coat Technol, 1999, 122: 73-93.
[6] WU Han-hua, WANG Jian-bo, LONG Bei-yu, LONG Bei-long, JIN Zeng-sun, WANG Nai-dan, YU Feng-rong, BI Dong-mei. Ultra-hard ceramic coatings fabricated through microarc oxidation on aluminium alloy [J]. Appl Surf Sci, 2005, 252: 1545-1552.
[7] SUNDARARAJAN G, RAMA KRISHNA L. Mechanisms underlying the formation of thick alumina coatings through the MAO coating technology [J]. Surf Coat Technol, 2003, 167: 269-277.
[8] NIE X, MELETIS E I, JIANG J C, LEYLAND A, YEROKHIN A L, MATTHEWS A. Abrasive weary corrosion properties and TEM analysis of Al2O3 coatings fabricated using plasma electrolysis [J]. Surf Coat Technol, 2002, 149: 245-251.
[9] XUE Wen-bin, DENG Zhi-wei, CHEN Ru-yi, ZHANG Tong-he, MA Hui. Microstructure and properties of ceramic coatings produced on 2024 aluminum alloy by microarc oxidation [J]. Journal of Materials Science, 2001, 36: 2615-2619.
[10] GNEDENKOV S V, KHRISANFOVA O A, ZAVIDNAY A G, SINEBRUKHOV S L, KOVRYANOV A N, SCOROBOGATOVA T M, GORDIENKO P S. Production of hard and heat-resistant coatings on aluminium using a plasma micro-discharge [J]. Surf Coat Technol, 2000, 123: 24-28.
[11] WANG Chang-zheng, ZHANG Dong, JIANG Yong-feng. Growth process and wear resistance for ceramic coatings formed on Al-Cu-Mg alloy by micro-arc oxidation [J]. Appl Surf Sci, 2006, 253: 674-678.
[12] WEI Tong-bo, YAN Feng-yuan, TIAN Jun. Characterization and wear- and corrosion-resistance of microarc oxidation ceramic coatings on aluminum alloy [J]. Journal of Alloys and Compounds, 2005, 389: 169-176.
[13] LIANG Jun, HU Li-tian, HAO Jing-cheng. Characterization of microarc oxidation coatings formed on AM60B magnesium alloy in silicate and phosphate electrolytes [J]. Appl Surf Sci, 2007, 253: 4490-4496.
[14] HAN Yong, SUN Ji-feng, HUANG Xin. Formation mechanism of HA-based coatings by micro-arc oxidation [J]. Electrochemistry Communications, 2008, 10: 510-513.
[15] LI Jun-ming, CAI Hui, JIANG Bai-ling. Growth mechanism of black ceramic layers formed by microarc oxidation [J]. Surf Coat Technol, 2007, 201: 8702-8708.
[16] BARCHICHE C E, ROCCA E, HAZAN J. Corrosion behaviour of Sn-containing oxide layer on AZ91D alloy formed by plasma electrolytic oxidation [J]. Surf Coat Technol, 2008, 202: 4145-4152.
[17] LIANG Jun, HU Li-tian, HAO Jing-cheng. Improvement of corrosion properties of microarc oxidation coating on magnesium alloy by optimizing current density parameters [J]. Appl Surf Sci, 2007, 253: 6939-6945.
Foundation item: Project(2008BAE63B00) supported by the National Key Technologies Research and Development Program of China
Received date: 2009-05-11; Accepted date: 2009-08-06
Corresponding author: YANG Wei, PhD; Tel: +86-29-82312865; Fax: +86-29-82312617; E-mail: yangwei_smx@163.com
(Edited by CHEN Wei-ping)