
Melt film formation and disintegration during novel atomization process
LIU Yun-zhong(刘允中)1, K. Minagawa2, H. Kakisawa2, K. Halada2
1. School of Mechanical Engineering, South China University of Technology, Guangzhou 510640, China;
2. Ecomaterials Research Center, National Institute for Materials Science,
1-2-1 Sengen, Tsukuba City, Ibaraki 305-0047, Japan
Received 15 July 2007; accepted 10 September 2007
Abstract: Hybrid atomization is a new powder-making method and can produce economically very fine, clean, spherical tin alloy powders with average particle size about 10mm and narrow size distributions. The key concept of hybrid atomization is to control the liquid film formation on disk for fine powder production. Low-pressure gas atomization was utilized to promote the formation of a very thin stable liquid film before centrifugal breakup and give a better preparation for the final disintegration of melts. Besides the breakup ability of the rotating atomizer, the characteristics of liquid film on rotating disk affect the atomization mechanism and results remarkably. The main disintegration mode of melt is the breakup type of liquid film, which depends on the film instability and the atomization ability of the rotating disk. On the other hand, the mean powder size relates closely to the film thickness. The powder size distribution is mainly controlled by the atomization mode and the stability, flow type of liquid film on the rotating disk. A very thin, stable liquid film with long ligaments and a small pitch in LF mode results in very fine uniform tin alloy powders.
Key words: hybrid atomization; melt film formation; atomization mode
1 Introduction
Metal atomization is the breakup of melts from bulk liquid into fine droplets. In some conventional atomization methods such as centrifugal atomization and confined gas atomization, a liquid film was found to form before the final breakup[1]. It seems that the liquid film formation is an intermediate stage of powder- making in these atomization procedures. Few research results related to this subject were reported[2-5]. However, the role of liquid film formation in these atomization methods is unclear up to now. It is also a problem how to effectively control the liquid film formation in melt atomization for powder production.
A new powder-making technique, hybrid atomization was invented and developed recently to produce very fine spherical powders economically[3-4]. This technology combines low-pressure gas atomization with centrifugal atomization effectively. Its basic idea is to provide a thin but stable liquid film on rotating disk before centrifugal breakup by a low-pressure inert gas atomization. In this work, the influence of liquid film formation and characteristics (thickness, stability, etc.) on the hybrid atomization results, mechanism was investigated and discussed.
2 Experimental
Fig.1 shows a schematic diagram of hybrid atomization procedure. Melts were pre-heated to a proper temperature under the argon atmosphere in a crucible. Firstly they were broken down into coarse liquid droplets by gas atomization. These droplets hit the rotating disk and re-formed a thin stable liquid film on it. Then the film was broken up into fine droplets. After their solidification during flight, powders were collected at the bottom of atomization chamber. Both hybrid atomization and corresponding centrifugal atomization of Sn-9%Zn (mass fraction) and Sn-40%Pb (mass fraction) were carried out in this work. The variation ranges of main processing parameters were as follows. For Sn-9%Zn (mass fraction) alloy, melt temperature 573-823 K; spray distance 100mm; disk rotation speed 524-3 142 r/s
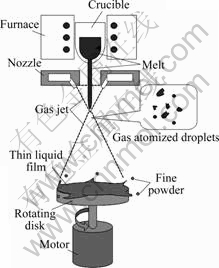
Fig. 1 Schematic diagram of hybrid atomization procedure
(5 000-30 000 r/min); disk diameter 50-100 mm; gas pressure 0.6 MPa; nozzle inner diameter 2.0 mm. For Sn-40%Pb (mass fraction) alloy, melt temperature 673-873 K; spray distance 100mm; disk rotation speed 1 047-2 094 r/s (10 000-20 000 r/min); disk diameter 100 mm; gas pressure 0.5-0.7 MPa; nozzle inner diameter 2.0 mm. Particle size and size distribution of powders were measured with the methods of Sieving and Coulter Counter. To investigate the liquid film thickness in hybrid atomization indirectly, the deposits rapidly solidified from liquid film on a rotating disk were also measured and observed with both optical microscope and scanning electron microscope (JSL5400).
3 Results and discussion
3.1 Deposit thickness and atomization results
As shown in Figs.2 and 3, the thinner the deposit thickness, the finer the particle sizes of powders obtained in hybrid atomization. When the deposit thickness drops from case (a) to case (b) in Fig.2, the powder mass median diameter decreases from 18 mm to 10.6 mm and the geometric standard deviation changes from 1.7 to 1.3. Moreover, the pattern of particle size distribution curve also changes from two peaks to almost one sharp peak. In addition, spherical particles with very few satellites were observed. Thus thinner deposit (film) thickness results in finer powder sizes, narrow size distributions and fewer satellites.
As shown in a vertical direction (45? to the right side) of Fig.4, the deposit is solidified and formed from liquid film layer by layer on disk. The thickness of one layer is about 4-7 mm, which agrees well with the calculated thickness (2-6 mm) during hybrid atomization.
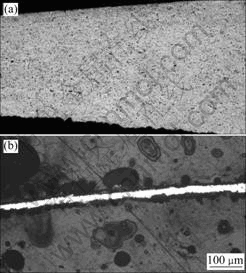
Fig.2 SEM images of Sn-9%Zn alloy deposits in hybrid atomization under different conditions: (a) Thick deposit; (b) Thin deposit
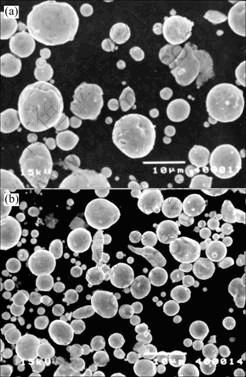
Fig.3 SEM images of Sn-9%Zn alloy powders obtained with different deposits on rotating disk: (a) Thick deposit; (b) Thin deposit
3.2 Comparison of results in hybrid atomization and centrifugal atomization
As shown in Fig.5, under the same centrifugal atomization conditions hybrid atomization gives fine powders of about 10 mm whereas centrifugal atomization
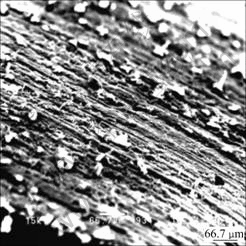
Fig.4 SEM micrograph of deposit in hybrid atomization of Sn-9%Zn alloy
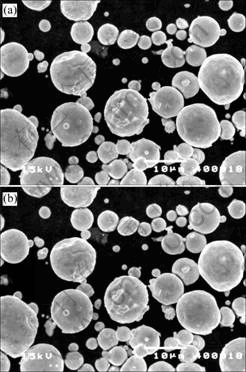
Fig.5 SEM images of Sn-9%Zn alloy powders by hybrid atomization (a) and centrifugal atomization (b)
produces powders of mean particle diameters larger than 60 mm. Powders in hybrid atomization are better spherical than those in centrifugal atomization. As shown in Fig.6, there exists a close relationship between the mass median diameters and deposit thickness. It seems that hybrid atomization can be regarded as a “reinforced” centrifugal atomization with a thinner liquid film on disk.
3.3 Hybrid atomization modes and powders
Based on our work, there are four possible
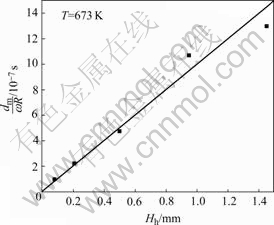
Fig.6 Relation between deposit thickness and mean powder diameter in hybrid atomization of Sn-9%Zn alloy
disintegration modes, i.e., direct drop formation disintegration mode(DDF), ligament formation disintegration mode(LF), film formation disintegration mode(FF) and column formation disintegration mode (CF) in hybrid atomization and centrifugal atomization [2, 4-6]. A schematic diagram of these modes is shown in Fig.7. According to the results of HALADA and SUGA[6], the CF mode is the main atomization mode in their work on centrifugal atomization and can be regarded as a special, instable LF mode, which results in coarse powders. For hybrid atomization of Sn-9%Zn (mass fraction) alloy, it was found that the main atomization mode should be the DDF mode[2, 4]. As shown in Fig.8 and Fig.9, the main atomization mode is LF mode for hybrid atomization of Sn-40%Pb (mass fraction) alloy. Comparing Fig.9 with Fig.10, sample 4 corresponds with the LF/DDF mode transition and results in coarse powders. Sample 1 is located in the LF area and gives fine particles. Fig.10 shows that fine, uniform spherical powders about 10 mm or smaller can be obtained in LF mode. Long ligaments with a small pitch give fine powders.
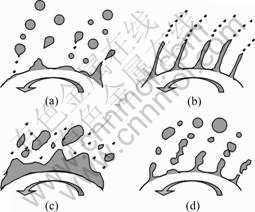
Fig.7 Possible disintegration modes in hybrid atomization and centrifugal atomization: (a) DDF mode; (b) LF mode; (c) FF mode; (d) CF mode
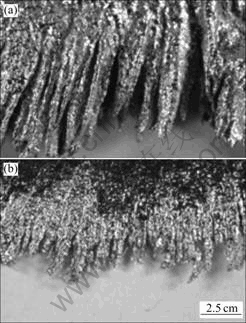
Fig.8 Ligament formation at disk edge in hybrid atomization of Sn-40%Pb alloy: (a) Sample 1; (b) Sample 4
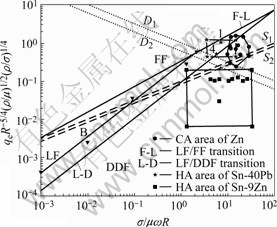
Fig.9 Atomization mode diagram for hybrid atomization and centrifugal atomization
As shown in Fig.9, the atomization mode will be mainly controlled by both X and Y. In our recent work [4],
X=Re/We (1)
Y=q×h×(ρ/m)1/2×(ρ/σ)1/4/2p (2)
where Re is the Reynolds number for rotation and Re=wR2ρ/m; We is the Weber number for rotation and We=ρw2R3/σ; q is the melt volume flow rate; ρ, m, σ are the density, viscosity and surface tension of melt respectively; h is defined as a gas spray factor and h={(P/P0)×[1+K×sin(θ/2)]}-1/2.
In fact, 1/X can be regarded as a parameter
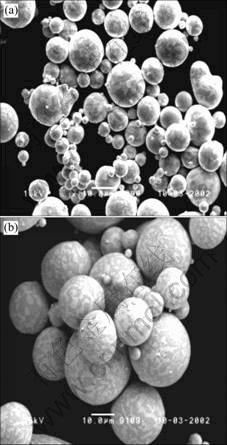
Fig.10 SEM images of Sn-40%Pb alloy powders obtained in LF mode by hybrid atomization: (a) Sample 1; (b) Sample 4
representing the atomization ability of centrifugal atomizer while Y can be regarded as a comprehensive parameter representing the liquid instability. The smaller the X, the bigger the atomization ability. The larger the Y, the more instable the liquid film becomes. In addition, as shown in later in Eqns.(5) and (7), the liquid film thickness on disk has a close relationship with the gas spray factor h. The smaller the h value, the thinner the liquid film. Besides the breakup ability of the rotating atomizer, the characteristics of liquid film on disk affect the atomization mechanism and results remarkably. In fact, the main disintegration mode of melts is the breakup type of liquid film. As shown in Fig.9, it depends heavily on the film instability, thickness and the atomization ability of the rotating disk.
3.4 Liquid film formation on rotating disk
In hybrid atomization a thin film forms on the rotating disk. Although its thickness cannot be measured directly up to now, there is a close relation between the liquid film and the deposit on the disk. Under a certain atomization condition, the deposit average thickness should be in direct proportion to the film thickness. After hybrid atomization, a thin circle deposit that solidifies from the liquid film is usually found on disk to be smaller than disk with a saw-like shape at its rim under typical conditions. And different atomization conditions result in different thicknesses of deposit and liquid film on the disk. When disk rate and superheat increase, the deposit thickness decreases. Besides, the deposit and thus the liquid film also become thin with increasing gas pressure and atomization angle in hybrid atomization.
Based on our theoretical results, if we assume an equivalent flow rate qe=q×h and let qe=q, the film thickness can be treated with and calculated by the equivalent atomization. According to Ref.[6], the film thickness in case of laminar flow should be as follows:
(3)
The average velocity of liquid flow along radial direction on the disk is
(4)
where δc is the film thickness; q is the flow rate in centrifugal atomization; m is the viscosity of metallic melts; ρ is melt density; w and R are angular velocity and diameter of rotating disk.
Therefore theoretically the film thickness in hybrid atomization is
(5)
Since q=2pRdV, the average velocity of liquid flow on the disk is as follows:
(6)
Thus under the same conditions with centrifugal atomization:
dh=dc×h1/3 (7)
The calculated film thickness (2-6 mm) in typical hybrid atomization is thinner than that in centrifugal atomization since h<1. Since the deposit thickness H on the rotating disk is closely related to and in direct proportion to the liquid film thickness d under a certain condition in both hybrid atomization and centrifugal atomization:
Hh/Hc=dh/dc=h1/3=(P/P0)-1/6×[1+K×sin(θ/2)]-1/6 (8)
If melts are atomized in DDF mode, the powder mass median diameter will obey the following equation[4]:
dm=k×h×We-1/2=k×{(ρDw2/σ)×(P/P0)×[1+Ksin(θ/2)]}-1/2
=h×dc (9)
Fig.6 shows the relation of powder mass median diameter and deposit average thickness in hybrid atomization. According to Fig.6, Eqns.(8) and (9), the mean powder size also depends heavily on the liquid film thickness. The smaller the film thickness and the h value, the finer the hybrid atomized powders. This is verified in Fig.3 indirectly.
The thickness and flow state of liquid film on disk affect the powder sizes greatly. In conventional centrifugal atomization, coarse powders probably result from a thick liquid film on the rotating disk because the film is broken down into large droplets slowly and a part of melts are built up on disk. In contrast, as shown in Eqns.(5) and (6), the film is very thin and flows towards the disk rim quickly in hybrid atomization since the melt spray by gas atomization is equivalent to an effective forced spreading of melt on disk before its centrifugal breakup. As a consequence, fine droplets form from a quick disintegration procedure in hybrid atomization.
On the other hand, different atomization modes will give different powder size distributions[8-17]. In the DDF mode, two peaks are usually found in the size distribution curve of powders. However, in LF mode there will be only one sharp peak in the size distribution curve of powders. Theoretically speaking, LF mode yields more uniform powders than DDF mode or CF mode. In addition, the stability and flow type of liquid film on disk also influence the powder size distribution. The typical flow type of liquid film on disk is laminar flow and more stable in hybrid atomization than that (sometimes turbulent flow) in conventional centrifugal atomization. With decreasing film thickness and improved stability, hybrid atomization can give a narrow powder size distribution even in the same atomization mode as centrifugal atomization. As shown in Fig.9, the best condition line can be regarded as a comprehensive optimization of hybrid atomization process. In this case, the LF mode should have a minimum ligament pitch and the liquid film on disk will be very thin and stable. Therefore very fine, uniform powders should be produced.
4 Conclusions
1) A new powder-making method, hybrid atomization is devised and developed recently to produce very fine, spherical powders with narrow size distributions economically. Its key concept is to control the liquid film formation on rotating disk.
2) The liquid film characteristics (thickness, stability and flow state) play an important role in both atomization mechanism and results in hybrid atomization. Powder size depends heavily on the liquid film thickness. Powder size distribution is mainly controlled by the atomization mode and the stability, flow type of liquid film on the rotating disk. A very thin, stable liquid film with long ligaments and a small pitch in LF mode results in very fine uniform tin alloy powders.
References
[1] DUNKLEY J J. Atomization, powder metal technologies and applications, ASM handbook [M] Ohio: ASM International, 1998: 35-52.
[2] MINAGAWA K, LIU Y Z, KAKISAWA H, HALADA K. Production of fine metallic powders by hybrid atomization process [J]. JSME International Journal Series A, 2003, 46(3): 386-392.
[3] MINAGAWA K, LIU Y Z, KAKISAWA H, HALADA K. Production of fine powders by hybrid atomization [C]// 2001 Proceedings of Autumn Meeting of Japan Society of Powder and Powder Metallurgy. Nagoya, Japan: Japan Society of Powder and Powder Metallurgy, 2001, 25A: 84-88.
[4] LIU Y Z, MINAGAWA K, KAKISAWA H, HALADA K. Process optimization and atomization mechanism of hybrid atomization [C]// Advances in Powder Metallurgy & Particulate Materials, 2002: 122-136.
[5] LIU Y Z, MINAGAWA K, KAKISAWA H, HALADA K. Hybrid atomization: Processing parameters and disintegration modes [J]. International Journal of Powder Metallurgy, 2003, 39(2): 29-37.
[6] HALADA K, SUGA H. Theoretical investigation on parameters of centrifugal atomization of metal powder [J]. Journal of the Japan Society of Powder and Powder Metallurgy, 1990, 37(4): 492-499. (in Japanese)
[7] TANASAWA Y, MIYASAKA Y, UMEHARA M. On the filamentation of liquid by means of rotating discs [J]. Journal of Japan Mechanical Society, 1959, 25(156): 879-898.
[8] CHAMPAGNE B, ANGERS R. REP atomization mechanism [J]. Powder Metallurgy International, 1984, 16(3): 125-129.
[9] MATSUMOTO S, SAITO K, TAKASHIMA Y. Disintegration modes of centrifugal atomization [J]. Journal of Chemical Engineering of Japan, 1974, 7(1): 13-20.
[10] LAGUTKIN S, ACHELIS L, SCHEIKHALIEV S, UHLENWINKEL V, SRIVASTAVA V. Atomization process for metal powder [J]. Materials Science and Engineering A, 2004, 383(1): 1-6.
[11] DUNKLEY J J. Atomization of metals—Craft or science [C]// BAUCKHAGE K, FRITSCHING U, UHLENWINKEL V. SDMA 2003 and ICSF V. Germany, Bremen: Bremen University, 2003: 1-11.
[12] LIU Y Z, LI Y Y. A new general equation of mean particle size for different atomization processes [J]. Materials Science Forum, 2007, 534/536: 1-4.
[13] LIU Y Z, LI Y Y. Numerical simulation of thermal history in a novel spray forming process [J]. Materials Science Forum, 2007, 539/543: 1171-1176.
[14] MINAGAWA K, LIU Y Z, KAKISAWA H, OSAWA Y, TAKAMORI S, HALADA K. Hybrid atomization process applied to fine lead-free solder powder production [J]. Materials Transactions JIM, 2003, 44(7): 1316-1319.
[15] MINAGAWA K, LIU Y Z, KAKISAWA H, TAKAMORI S, OSAWA Y, HALADA K. Production of fine uniform lead-free solder powders by hybrid atomization [J]. Materials Science Forum, 2003, 429: 3341-3346.
[16] LIU Y Z. Large undercooling, rapid solidification and nucleation mechanism during multistage atomization [J]. Powder Metallurgy, 2002, 45(2): 134-138.
[17] LIU Y Z. Studies on process optimization of multistage atomization [J]. Materials Science and Technology, 2002, 18(8): 929-934.
(Edited by LI Xiang-qun)
Foundation item: Project(NCET-05-0737) supported by the Program for New Century Excellent Talents in University, China; Project(50774035) supported by the National Natural Science Foundation of China
Corresponding author: LIU Yun-zhong; Tel: +86-20-87112948; E-mail: yzhliu@scut.edu.cn