
Comparison of two NiCoCrAl/YSZ microlaminates deposited on substrates with different surface roughness by EB-PVD
SHI Guo-dong (史国栋), LIANG Jun (梁 军), CHEN Gui-qing (陈贵清), DU Shan-yi (杜善义)
Center for Composite Materials, Harbin Institute of Technology, Harbin 150001, China
Received 15 July 2007; accepted 10 September 2007
Abstract: Two substrates with surface roughness (Ra) of about 1.6 and 0.8, respectively, were employed to fabricate two NiCoCrAl/YSZ microlaminates by using EB-PVD method. The average ceramic-layer thicknesses of the two NiCoCrAl/YSZ microlaminates are different, about 0.9 μm and 1.2 μm, respectively, but their average metal-layer thicknesses are equal, about 5 μm. The microstructures and fractographs were examined by SEM. Uniaxial tensile testing was performed to determine the mechanical properties. The results show that the microlaminate deposited on the relatively coarse substrate (MDCS) contains wavy layer interfaces and larger flaws, while the microlaminate deposited on the relatively smooth substrate (MDSS) has relatively flat layer interfaces and no larger flaws. The tensile specimens of the two microlaminates display obvious difference in tensile strengths and fracture modes. The ratio of strength of MDCS to that of MDSS is 0.5 at room temperature, 0.67 at 700 ℃ and 1.33 at 1 000 ℃, increasing with increasing temperature. The factors which caused the variation of the strength ratio were discussed. It is found that the larger flaws in MDCS result in the relatively low strength ratio at room temperature and 700 ℃, and the wavy layer interface in MDCS is responsible for the relatively great strength ratio at 1 000 ℃.
Key words: NiCoCrAl/YSZ; microlaminate; EB-PVD; flaw; layer interface; tensile property
1 Introduction
Metal/ceramic composites have been a topic of interest for many researchers for various reasons[1-5]. The motivation for developing metal/ceramic composites is to fabricate structures that possess superior high temperature creep resistance compared with metals, simultaneously having better toughness and structural integrity compared with monolithic ceramics[6-7]. In various ductile-brittle composite systems, there are numerous reinforcement shapes employed, including particulates, fibres and laminate reinforcements. Early studies show that the ductile layer reinforced composites generally promote greater levels of toughening than ductile particulate or fibre reinforced composites[8-10].
A microlaminate comprised of alternating layers of brittle ceramic and ductile metal is a particularly attractive composite architecture. One major advantage of the microlaminate is that the distribution and volume fraction of the phases can be readily controlled by altering the layer thicknesses[11]. The small size scales lead to increases in the ductile layer strength from enhanced constraint and, possibly, various strengthening mechanisms. In principle, smaller length scales may also increase the ceramic material cracking stresses by limiting the sizes of potential processing flaws[12]. So far, only a few studies have been performed to investigate the microlaminate composites[13-19], and most of them only concentrate on the intermetallic/ metallic systems. The investigation of metal/ceramic microlaminates is far insufficient.
In the present study, the tensile properties of the two NiCoCrAl/YSZ microlaminates were examined at room temperature and high temperature, and the effects of ceramic-layer thickness, flaw size, residual stress and interface morphology on their tensile strengths were discussed.
2 Experimental
Two NiCoCrAl/YSZ microlaminates were deposited on the steel substrates with surface roughness (Ra) of about 1.6 and 0.8 respectively by EB-PVD. Thesubstrates used were grinded mechanically and all scratch marks on their surfaces were along the direction of grinding. Both the microlaminate deposited on the relatively coarse substrate (MDCS) and the one deposited on the relatively smooth substrate (MDSS) contained 50 ceramic layers and 50 metal layers. And there existed equal average metal-layer thicknesses (about 5 μm), but different average ceramic-layer thicknesses (about 0.9 μm and 1.2 μm, respectively) in MDCS and MDSS.
During the deposition process, the substrate was mounted on the holder and rotated at 25 r/min around the horizontal axis and the substrate temperature was maintained at 950 ℃. To facilitate the removal of the microlaminates from the substrates, the substrates were coated with 10-20 μm of ZrO2 prior to depositing the microlaminates. The layer thicknesses of microlaminates were controlled by deposition time. In the following deposition the foils were removed from their substrates and then annealed in vacuum (10-4 Pa) at 1 050 ℃ for 30 min. At the end of each anneal, the samples were furnace cooled to room temperature under vacuum.
To assess the mechanical properties of the microlaminates, tensile specimens were milled from free standing microlaminate foils. Prior to tensile testing the edges of the foils were mechanically polished. Tensile tests were conducted on the foils using an INSTRON-5500 universal materials testing machine with a crosshead displacement speed of 0.01 mm/min at room temperature, 700 ℃ and 1 000 ℃. In this work, five specimens were tested to get an average value at each temperature. The microstructures of the cross- sections of the foils and the fracture surfaces of the tensile specimens were observed with SEM.
3 Results
The stress-strain curve is one of the fundamental mechanical properties of materials. In room temperature tensile tests, both microlaminates display typical characteristics of linear elastic fracture with no evidence of yielding, as shown in Fig.1(a). In the case, elastic loadings are terminated by fast fracture at a peak load. The fracture stress and elongation of MDSS are 594 MPa and 0.35%, respectively, both of the values are about 2 times greater than those of MDCS (about 277 MPa and 0.17%, respectively). The fracture stress obtained for MDSS is comparable to those obtained by HEERDEN et al[11] on Nb/Nb5Si3 microlaminates (590-640 MPa). Fig.1(b) shows the stress—strain curves of tensile specimens tested at 700 ℃. Both of the microlaminates show larger elongations (more than 2%). The tensile strength of MDSS is 412 MPa, less than the one at room temperature. But the strength of MDCS is 276 MPa, as much as the one at room temperature. And no evidence of yielding is seen again in the stress—strain curves from either of them. At 1 000 ℃, both stress—strain curves of microlaminates show evidence of plastic deformation, as shown in Fig.1(c). For MDSS, a uniform plastic deformation region followed by a locally deformed region is exhibited. And its tensile strength and failure strain of MDSS are about 75 MPa and 6%, respectively. While MDCS shows only a uniform plastic deformation region and almost no local deformation. And its elongation (about 3.8%) is lower but tensile strength (about 100 MPa) is higher.
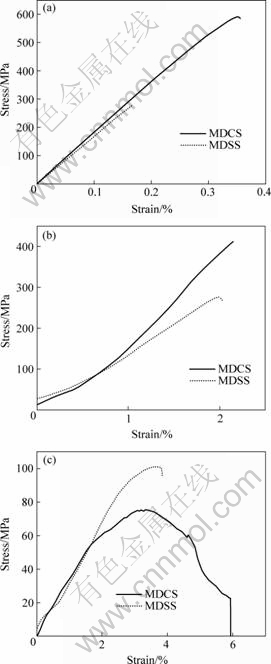
Fig.1 Stress—strain curves of NiCoCrAl/YSZ microlaminates: (a) At room temperature; (b) At 700 ℃; (c) At 1 000 ℃
Fig.2 shows the plan-view photographs of microlaminates. As shown in Fig.2(a), MDCS displays a mixture of shear cracking and cracking along flaws. The shear cracks are seen as the diagonal portions of fracture paths. Redirection of fracture paths along longitudinal flaws is seen between the shear cracks. And with increasing temperature of tensile test, the number and lengths of fracture paths along flaws decrease, which indicates that the sensitivity of microlaminates to the flaws decreases. This can be seen in plan-view photographs of MDCS specimens tested at 700 ℃ and 1 000 ℃ (Fig.2(b) and 2(c)). However, MDSS specimens display a normal tensile break at room temperature (Fig.2(d)). Redirection of fracture paths along flaws can not be seen in plan-view photographs of MDSS specimens tested at high temperature.
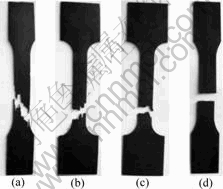
Fig.2 Plan-view photographs of microlaminates: (a) MDCS specimen tested at room temperature; (b) MDCS specimen tested at 700 ℃; (c) MDCS specimen tested at 1 000 ℃; (d) MDSS specimen tested at room temperature
The discrepancy between the cracking modes of the microlaminates is caused by their different microstructures. MDCS specimens contain a lot of larger longitudinal flaws while MDSS specimens do not. The formation of flaws can be explained by shadowing effect. During the microlaminate deposition, the rotation of substrate brings the interruption of the vapor flux to the substrate, which results in a shadowing effect[20]. As shown in Fig.3, shadowing occurs when the edge of a scratch existing on the surface of substrate blocks the majority of the flux and produces a shadow area because of the ‘sunrise’ and ‘sunset’ incidence of vapor onto substrates during rotation. The longitudinal flaws easily form in the microlaminates within shadowed areas. And the greater the shadowing effect is, the larger the flaws formed in the shadowed regions are. The cross-sectional micrograph of MDCS in the direction normal to scratch is shown in Fig.4(a). The wavy interfaces between the layers are observed. All of the longitudinal flaws are locate at joints between the waves and they penetrate some of the layers, even more than half of the layers in the microlaminate thickness direction. However, there are only relatively flat interfaces between the layers and no relatively large flaws are seen from the microstructure of MDSS (Fig.4(b)). This is because the smaller surface roughness of the substrate used for depositing MDSS causes a minor shadowing effect.
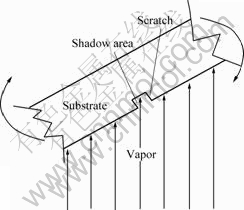
Fig.3 Formation of shadow area during microlaminate deposition on substrate with surface scratches
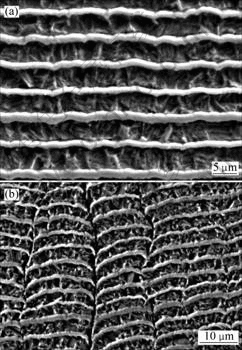
Fig.4 Cross-sectional micrographs of microlaminates in direction normal to scratches on substrate surfaces: (a) MDCS; (b) MDSS
A representative SEM micrograph of the fracture surface of MDSS tensile specimen tested at room temperature is shown in Fig.5(a). The ceramic layers fail by intergranular brittle fracture between the columnar grains and the metal layers fail by chisel point failure
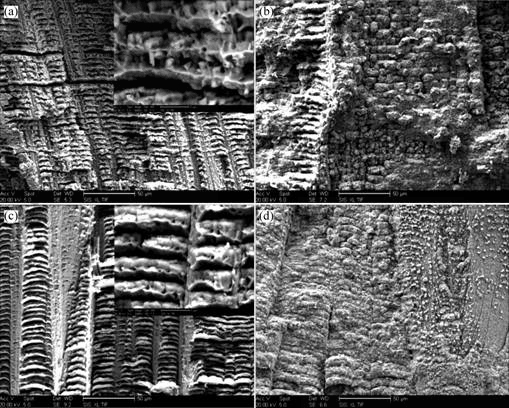
Fig.5 Micrographs of fracture surfaces of microlaminates: (a) MDSS specimen tested at room temperature; (b) MDSS specimen tested at 1 000 ℃; (c) MDCS specimen tested at room temperature; (d) MDCS specimen tested at 1 000 ℃
with fracture surfaces necked to ‘knife edge’ features. A lot of secondary cracks vertical to layer planes in ceramic layers are observed, which indicates the bond strength between the ceramic columnar grains and tensile strength of ceramic layer are very low. The interfacial debondings are also very evident.
On the fracture surface of MDCS specimen tested at room temperature (Fig.5(c)), the sections of shear cracking have a similar surface feature to that of MDSS, while the sections of cracking along flaws are smooth, which indicates fast (unstable) fractures occur along the flaws. In the fast fracture regions, both metal layers and ceramic layers fail by brittle intergranular fracture with featureless surfaces and no evidence of interfacial debonding is seen.
For tensile specimens tested at high temperature, the details of fractographs are not clear due to high temperature oxidation of specimens, but interfacial debondings may been observed yet (Fig.5(b) and Fig.5(d) ). Furthermore, the fractograph of MDCS tensile sample tested at 1 000 ℃ displays a relatively flat fracture surface on which few fast fracture regions along longitudinal flaws are observed due to reduced sensitivity to flaws.
4 Discussion
The tensile strength (σcom) of the NiCoCrAl/YSZ microlaminate may be estimated by mixture law, as given by
(1)
where σ and φ are the tensile strength and volume fraction of metal (or ceramic) layers respectively. The tensile strength of NiCoCrAl foil produced by EB-PVD is 600 MPa[21]. While the tensile strength of bulk yttria partially stabilised zirconia is only 110 MPa. And the tensile strength of YSZ coating is much less than that of bulk YSZ. Plasma sprayed YSZ coatings have a lower value for tensile strength (9-36 MPa) due to more flaws[22-24]. ANDRITSCHKY and ALPUIM[25] also found that the linkage between the growing columns in PVD YSZ coatings was so weak that coatings would fail as soon as the applied tensile stress surpasses their residual compressive stresses. Similarly, the true tensile strength of EB-PVD YSZ coating should also be much less than that of bulk YSZ due to large numbers of flaws and weak linkage between columnar grains in the coating. This means that the true tensile strength of ceramic layer is much less than that of the metal layer in the microlaminates. Moreover, ceramic layers have much lower volume fractions than the metal layers, and are in compression due to residual stress. As a result, the tensile strength of NiCoCrAl/YSZ microlaminate will depend mostly on the tensile strength and volume fraction of its metal layers. So equation (1) can be simplified to
(2)
where φm is the volume fraction of metal layers.
According to the number and thicknesses of metal layers and ceramic layers, φm in MDCS is calculated to be 84.7% and the value in MDSS is calculated to be 80.6%. Supposing MDCS and MDSS have the same metal layers in strength, one can predict that the tensile strength of MDCS will be 1.05 times greater than that of MDSS. But the result of test shows that the tensile strength ratio of MDCS to MDSS is 0.5 at room temperature, 0.67 at 700 ℃ and 1.33 at 1 000 ℃. This indicates that both of the tensile strengths of the metal layers for the two microlaminates and their variations with temperature are different. Thus, the difference in the strengths of the microlaminates will depend mostly on the difference in strengths of their metal layers. Three factors having important influences on the tensile strengths of metal layers could account for the variation in the strength ratio of microlaminates with temperature.
Firstly, EB-PVD metal layers contain more flaws due to shadowing effect. And their breaking strength, σ, decreases with increasing flaw size, a, according to the relationship given by Orowan’s eqution:
(3)
where E and γp are the elastic modulus and plastic deformation work of the metal layers, respectively.
Secondly, when cooling the free-standing microlaminates from the annealing temperature (1 050 ℃) to room temperature, thermal stresses develop due to the mismatch in the thermal contraction of the metal layers and ceramic layers. Because the metal layers will contract more than the ceramic layers on cooling, the metal layers will develop tensile stresses while the ceramic layers will develop compressive stresses. The compressive residual stresses in ceramic layers that have very low tensile strengths don’t have important influence on the tensile strengths of microlaminates, so they may be ignored.
Assuming there is no relaxation on cooling, one can estimate the final residual thermal stresses for a free-standing microlaminate. The residual thermal stress of metal layer (σr), may be described by
(4)
where t is the thickness of individual layer, and using the linear thermal expansion term, k = αΔT, where α is the CTE of individual layer and ΔT is the change in temperature. The maximal applied tensile stress, σmax, which a metal layer can bear increases with decreasing tensile residual stress according to the following relationship:
(5)
where σ0 is the tensile strength of the metal layer in which no residual stress is present.
Eqns.(4) and (5) suggest that the residual stress of metal layers in MDSS is greater than that in MDCS due to MDSS containing thicker ceramic layers and the tensile strength of MDSS decreases more than that of MDCS due to residual stress.
A third likely source of the difference in tensile strengths of metal layers is interfacial microstructure. A wavy layer interface appears to be able to strengthen the metal layers more than a flat layer interface due to better restraining the plastic deformation of metal layers in tension. So wavy layer interfaces are probably more helpful to improve the tensile strengths of microlaminates.
Compared with MDSS, MDCS has the metal layers containing lower residual stresses and wavy layer interfaces, but also contains larger flaws. Thus, it is evident that the influence of residual stress and interfacial microstructure on the tensile strengths of microlaminates is apt to improve the ratio of tensile strength of MDCS to that of MDSS, while the effect of flaws is inclined to reduce the value. When ignoring the difference in the three factors between microlaminates, the strength ratio should be about 1.05. At room temperature, however, the strength ratio is only 0.5 and MDCS tensile specimens display longer fracture paths along the flaws, which indicates that the larger flaws in MDCS cause a larger decrease in its tensile strength and the flaw size is the most important one of the three factors influencing the strengths of microlaminates. At elevated temperature, residual stresses of microlaminates are much less than those at room temperature, due to less temperature difference and larger creep deformation of metal layers and even ceramic layers. And it may be believed that almost all of residual stresses will be relieved at 1 000 ℃. So, the effect of residual stresses on the tensile strengths of microlaminates is not important any more at high temperature. Because the ductility of metal layers becomes better when temperature is elevated, it is guessed why the sensitivity of metal layers to flaws will decrease and the strengthening effect of layer-interfaces on metal layers will be more outstanding with increasing temperature, which is the reason that the strength ratio obtained by testing increases with increasing temperature. The testing results justify this view.
The strength ratio and the fracture paths along flaws in MDCS specimens at 700 ℃ are larger and shorter than those at room temperature, respectively. This shows that the effect of flaws on the strengths of microlaminates decreases compared with that of other two factors, when temperature increases from room temperature to 700 ℃. But the strength ratio is much less than 1.05 yet, which suggests that the flaw size is still the dominant one of three factors influencing the strengths of microlaminates. At 1 000 ℃, the greater tensile strength of MDCS than that of MDSS as well as the relatively flat fracture surface of MDCS specimen shows the influence of flaws on the strengths of microlaminates has been unimportant. And the strength ratio much more than 1.05 and the lower elongation shown in the stress—strain curve of MDCS indicate that wavy layer interfaces can certainly constrain the plastic deformation of metal layers better and improve the tensile strengths of microlaminates more than flat layer interfaces. It is obvious that the effect of layer interfaces on strengths of microlaminates surpasses that of flaws at 1 000 ℃.
5 Conclusions
1) Two substrates with different surface roughness were employed to fabricate two NiCoCrAl/YSZ microlaminates by EB-PVD method.
2) In tensile tests, MDCS specimens display a mixture of shear cracking and cracking along the flaws and their fracture paths along the longitudinal flaws become less and shorter with increasing temperature, while MDSS specimens display a normal tensile break.
3) When the temperature increasing from room temperature to 1 000 ℃, the ratio of strength of MDCS to that of MDSS increases from 0.5 to 1.33. The factors which causes the variation of the strength ratio are mostly flaw sizes, residual stresses and layer interface microstructures. But the influence of residual stresses on the strength ratio is not significant compared with other two factors.
4) The relatively coarse substrate not only introduces larger flaws which result in a more decrease of tensile strengths at room temperature into the microlaminate, but also introduces wavy layer interfaces which are more helpful to improve the tensile strengths than the flat ones at high temperature into the microlaminate.
References
[1] PAVESE M, FINO P, UGUES D, BADINI C. High cycle fatigue study of metal-ceramic co-continuous composites[J]. Scripta Materialia, 2006, 55: 1135-1138.
[2] RANGARAJ S, KOKINI K. Influence of particle shape and aspect ratio on thermally activated viscoplastic (time-dependent) response of ceramic (zirconia)-metal (NiCoCrAlY) particulate composites[J]. Mater Sci Eng A, 2004, 366: 356-366.
[3] NERALLA S, KUMAR D, YARMOLENKO S, SANKAR J. Mechanical properties of nanocomposite metal-ceramic thin films[J]. Composites B, 2004, 35: 157-162.
[4] ZENG T, WU L Z. Numerical simulation on crack growth of multilayered ceramic/metal composites[J]. Mechanics Research Communications, 2004, 31: 55-63.
[5] BROWN I W M, OWERS W R. Fabrication, microstructure and properties of Fe-TiC ceramic-metal composites[J]. Current Applied Physics, 2004, 4: 171-174.
[6] SHANG C H, HEERDEN D V, GAVENS A J, WEIHS T P. An x-ray study of residual stresses and bending stresses in free-standing nb/nb5si3 microlaminates[J]. Acta Materialia, 2000, 48: 3533-3543.
[7] AGRAWA P, SUN C T. Fracture in metal-ceramic composites[J]. Composites Science and Technology, 2004, 64: 1167-1178.
[8] LI M, WANG R, KATSUBE N, SOBOYEJO W O. An investigation of fracture behavior in layered NiAl/V composites[J]. Scripta Materialia, 1999, 40: 397-402.
[9] LI M, SOBOYEJO W O. Synergistic toughening of a hybrid NiAl composite reinforced with partially stabilized zirconia and molybdenum particles[J]. Mater Sci Eng A, 1999, A271: 491-495.
[10] EL-SHAER Y, DERBY B. Modelling of R-curve behaviour in ceramic–metal laminates[J]. Mater Sci Eng A, 2004, A365: 196-201.
[11] van HEERDEN D, GAVENS A J, FOECKE T, WEIHS T P. Evaluation of vapor deposited Nb/Nb5Si3 microlaminates[J]. Mater Sci Eng A, 1999, 261: 212-216.
[12] HEATHCOTE J, ODETTE G R, LUCAS G E, ROWE R G, SKELLY D W. On the micromechanics of low temperature strength and toughness of intermetallic/metallic microlaminate composites[J]. Acta Materialia, 1996, 44(11): 4289-4299.
[13] WAS G S, FOECKE T. Deformation and Fracture in Microlaminates[J]. Thin Solid Film, 1996, 286: 1-31.
[14] CHUNG H, JILAVI M H, DUFFEY T P. Nanocrystalline NbAl3/Al multilayer thin films deposited by exciter laser ablation[J]. Scripta Materialia, 1998, 38: 429-435.
[15] WAS G S, KALNAS C E, JI H, JONES J W. Ion beam assisted deposition in the synthesis and fracture of metal-ceramic microlaminates[J]. Nuclear Instruments and Methods in Physics Research B, 1995, 106: 147-152.
[16] BLOYER D R, VENKATESWARA RAO K T, RITCHIE R O. Laminated Nb/Nb3Al composites: effect of layer thickness on fatigue and fracture behavior[J]. Mater Sci Eng A, 1997, 239/240: 393-398.
[17] LI Y, ZHAO J P, ZENG G, GUAN C L, HE X D. Ni/Ni3Al microlaminate composite produced by EB-PVD and the mechanical properties[J]. Materials Letters, 2004, 58: 1629-1633.
[18] BLOYER D R, VENKATESWARA RAO K T, RITCHIE R O. Resistance-curve toughening in ductile/brittle layered structures: behavior in Nb/Nb3A1 laminates[J]. Mater Sci Eng A, 1996, 216: 80-90.
[19] XU W H, MENG X K, YUAN C S, NGAN A H W, WANG K L, LIU Z G. The synthesis and mechanical property evaluation of Ni-Ni3Al microlaminates[J]. Materials Letters, 2000, 46: 303-308.
[20] JANG B K, MATSUBARA H. Surface roughness and microstructure of yttria stabilized zirconia EB-PVD coatings[J]. Surface and Coatings Technology, 2006, 200: 4594-4600.
[21] LI Xiao-hai. Research on large scale Ni-based superalloy sheets deposited by EB-PVD[D]. Harbin: Harbin Institute of Technology, 2006. 1-135. (in Chinese)
[22] WANG Quan-sheng, WANG Fu-chi, MA Zhuang, Lü Guang-shu. Study of manufacturing process and properties of thick gradient thermal barrier coatings on aluminum alloy substrate[J]. China Surface Engineering, 2004, 4: 35-41. (in Chinese)
[23] WANG De-peng, YU Chao-xia, WANG Xu-dong, LIANG Shi-jun, ZHANG Wen-jian, FENG Zong-jie, MU Hong-bin. Effect of spraying distance on tensile strength of thermal barrier coatings[J]. Hot Working Tecknology, 2007, 36(7): 46-49. (in Chinese)
[24] DONG Z L, KHOR K A, GU Y W. Microstructure formation in plasma-sprayed functionally graded NiCoCrAlY/yttria-stabilized zirconia coatings[J]. Surface and Coatings Technology, 1999, 114: 181-186.
[25] ANDTITSCHKY M, ALPUIM P. Strength measurements of thin brittle ZrO2 coatings produced by magnetron sputtering on steel substrates[J]. Vacuum, 1997, 48(5): 417-422.
(Edited by LONG Huai-zhong)
Foundation item: Project (90405016) supported by the National Natural Science Foundation of China; Project (20040213034) supported by the Research Fund for the Doctoral Program of Higher Education, China
Corresponding author: SHI Guo-dong; Tel: +86-451-86402432; E-mail: sgdinhit@yeah.net, shiguodong78@sohu.com