
Effects of minor yttrium addition on hot deformability of lamellar Ti-45Al-5Nb alloy
CHEN Yu-yong(陈玉勇), LI Bao-hui(李宝辉), KONG Fan-tao(孔凡涛)
School of Materials Science and Engineering, Harbin Institute of Technology, Harbin 150001, China
Received 22 September 2006; accepted 5 December 2006
Abstract: The effects of 0.3%(molar fraction, the same below) yttrium addition on hot deformability of lamellar Ti-45Al-5Nb alloy were investigated by simulated isothermal forging tests. The ingots with the nominal compositions of Ti-45Al-5Nb and Ti-45Al-5Nb-0.3Y were prepared by induction skull melting. Simulated isothermal forging tests were conducted on Gleeble 1500D thermo-simulation machine using a 6 mm in diameter and 10 mm in length compressive specimen at the deformation temperatures of 1 100, 1 150, 1 200 ℃ and strain rates of 1.0, 0.1, 0.01 s-1. The results show that yttrium addition remarkably improves hot deformability of Ti-45Al-5Nb alloy. An appropriate hot deformation processing parameter of Ti-45Al-5Nb-0.3Y alloy is determined as 1 200 ℃, 0.01 s-1. The flow stresses are decreased by yttrium addition under the same compressive conditions. The activation energies of deformation Q are calculated as 448.6 and 399.5 kJ/mol for Y-free and Y-containing alloys, respectively. The deformed microstructure observation under 1 200 ℃, 0.01 s-1 condition indicates that Ti-45Al-5Nb-0.3Y alloy shows more dynamic recrystallization. The improvement of hot deformability of Ti-45Al-5Nb-0.3Y alloy induced by yttrium addition should be attributed to that the smaller the original lamellar colonies, the lower the deformation resistance and activation energy of deformation are, and the more the dynamic recrystallization is.
Key words: TiAl alloy; hot deformability; rare earth yttrium; thermo-simulation
1 Introduction
Gamma titanium aluminides are considered mainly for applications in aerospace vehicle, energy and automotive industry because they have low density, good specific strength and modular ratio, excellent creep resistance and sufficient oxidation resistance[1]. However, the major obstacle to engineering application is their poor ambient temperature ductility and hot workability due to the strong covalent bonding and anisotropy. It is difficult for TiAl alloys to be deformed plastically even at elevated temperature by conventional methods. Therefore, great effort has been devoted to improving hot workability of TiAl alloys[2-6].
The hot deformation behaviors of TiAl alloys mainly depend on the alloy composition, various microstructure and processing parameters[5]. The hot workability can be improved by the microstructure refinement and the introduction of β phase induced by the addition of B, C, Si and Cr, V, Mn, Nb[5,7-8]. Current studies on hot workability of TiAl alloys were usually conducted at the temperature between Te and Tα. The hot workability can be better at higher deformation temperature, especially above Tα[9]. Besides, a two-step forging method has been developed and the last forging was conducted even below Te[10]. Furthermore, it is found that the duplex microstructure is more suitable for hot workability.
Recent research showed that rare earth element Y can refine microstructure and improve oxidation resistance of TiAl alloys[11-13]. Grain size reached nearly 60-80 μm by YAl2 phase segregation at grain boundaries preventing grain growth[11,14]. In this paper, the effects of yttrium addition on hot workability of lamellar Ti-45Al-5Nb alloy were examined and results of the observations were discussed. The purpose of this investigation is to explore methods to improve hot workability of TiAl alloys.
2 Experimental
Two ingots with the compositions of Ti-45Al-5Nb and Ti-45Al-5Nb-0.3Y (all in molar fraction, %) were prepared by induction skull melting(ISM). The parent materials used in this study were Ti sponge (99.99%, mass fraction), high purity Al (99.99%, mass fraction), Al-Nb alloy and Al-Y alloy. The ingot size was about 60 mm in diameter and 120 mm in height. The ingots were homogenized in a hot isostatic presser at 1 250 ℃ for 4 h under an argon pressure of 170 MPa, then heat treated at 900 ℃ for 48 h and subsequent cooled to room temperature. Chemical compositions of ingots were analyzed by XRF method listed in Table 1.
Table 1 Chemical composition of Ti-45Al-5Nb and Ti-45Al- 5Nb-0.3Y alloys (molar fraction, %)
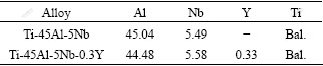
Cylindrical compression specimens, with 6mm in diameter and 10 mm in length, were cut by electric spark wire cutting from the HIP/HT ingots. Simulated isothermal forging tests were conducted on Gleeble 1500D thermo-simulation machine at the deformation temperatures of 1 100, 1 150, 1 200 ℃ and strain rates of 1.0, 0.1, 0.01 s-1, respectively. Total deformation was almost 60%. In order to reduce the friction force between pressure indenter and two head faces of specimens, a graphite lubricant was used for the isothermal hot-compression tests. Specimens after deformation were air-cooled to room temperature.
The microstructures of deformed specimens were examined by optical microscopy(OM), backscatter electron microscopy(BSE) and transmission electron microscopy(TEM). The polished surface for OM was etched in a modified Kroll’s reagent of 10% HF, 4% HNO3 and 86% H2O (volume fraction). Specimens for TEM observation were prepared using standard procedures by a two-jet thinner.
3 Results
3.1 Original microstructures
Fig.1 shows the microstructures of Ti-45Al-5Nb and Ti-45Al-5Nb-0.3Y alloys after HIP/HT. Ti-45Al-5Nb alloy has fully coarse lamellar structures. The addition of 0.3%Y obviously refines the microstructure of Ti-45Al-5Nb alloy, as shown in Fig.1(b). In Fig.1(c), there appear the lamellar colonies (grain) clearly. Furthermore, 0.3%Y addition leads to the formation of a new Y-rich phase—YAl2 compound, which was determined in previous literatures[12,14-15]. These Y-rich phases uniformly distribute in the lamellar colonies and along the grain boundaries, as shown in Fig.1(d).
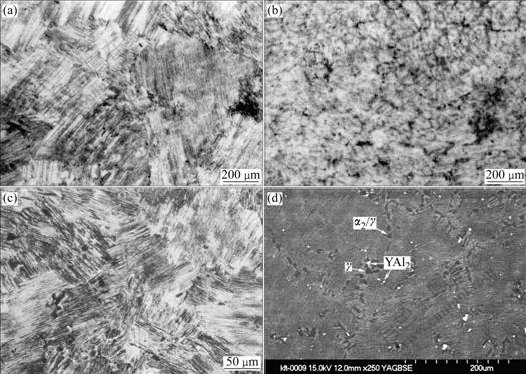
Fig.1 Microstructures of TiAl alloys after HIP/HT: (a) Ti-45Al-5Nb alloy; (b)-(d) Ti-45Al-5Nb-0.3Y alloy; (d) BSE mode
3.2 Observation on appearance of specimens
From the appearance of specimens after hot deformation, all the specimens that are not fractured show the shape of drum. After hot compression, some specimens show surface cracks on the side of specimens. Some cracks grow quickly until whole of the specimen fractures. The study reveals that deformation temperature and strain rate have obvious effects on material deformability. Increasing temperature and/or decreasing strain rate are beneficial to the hot compression deformation of TiAl alloys.
Fig.2 shows the appearance of some typical specimens before and after the hot deformation. Below 1 200 ℃, the specimens crack or fracture and the specimens crack more seriously at 1 100 ℃. At 1 200℃, for Ti-45Al-5Nb alloy, there appear cracks with the strain rate of 1.0 s-1 and 0.1 s-1. While with the strain rate of 0.01 s-1, a few small cracks appear on the side of specimens. For Ti-45Al-5Nb-0.3Y alloy, the specimens with the strain rate of 1.0 s-1 show large cracks and don’t fracture. Under 1 200 ℃, 0.1 s-1, the specimens only have some small cracks. While the specimens under 1 200 ℃, 0.01 s-1 have no cracks. These results indicate that Ti-45Al-5Nb-0.3Y alloy has better hot deformability in comparison with Ti-45Al-5Nb alloy at the same processing parameters. The optimal hot deformation parameters are determined for Ti-45Al-5Nb-0.3Y under the deformation temperature of 1 200 ℃ and strain rate of 0.01 s-1.
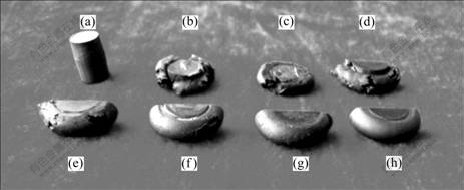
Fig.2 Several typical specimens before and after hot deformation (Sample 1 Ti-45Al-5Nb alloy; Sample 2 Ti-45Al-5Nb-0.3Y alloy): (a) Before deformation; (b) Sample 1, 1 100 ℃, 0.01 s-1; (c) Sample 2, 1 100 ℃, 0.01 s-1; (d) Sample 1, 1 150 ℃, 0.1 s-1; (e) Sample 1, 1 150 ℃, 0.01 s-1; (f) Sample 1, 1 200 ℃, 0.01 s-1; (g) Sample 2, 1 150 ℃, 0.01 s-1; (h) Sample 2, 1 200 ℃, 0.01 s-1
3.3 True stress—strain curves
The true stress—strain curves of simulated isothermal forging of Ti-45Al-5Nb alloy and Ti-45Al-5Nb-0.3Y alloy are shown in Fig.3. On the curves, A, B and C indicate 1 100, 1 150 and 1 200 ℃, respectively. 1, 2 and 3 indicate strain rates of 1.0, 0.1 and 0.01 s-1, respectively. The flow stresses firstly increase with increasing strain and quickly reach a peak, then decrease as the strain further increases, and finally reaches a steady state, where the flow stresses remain approximately constant. A peak flow stress exists on each curve, which suggests that dynamic recrystallization occurs during the hot deformation. The difference of the true stress-strain behaviors between the alloys is that the flow stress of Ti-45Al-5Nb-0.3Y is lower than that of free-Y TiAl alloy.
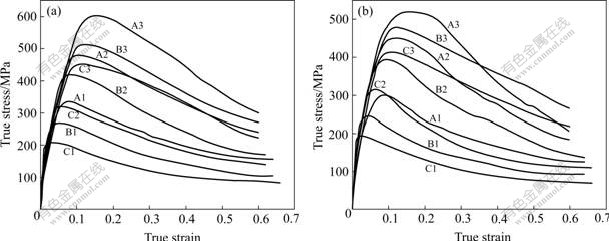
Fig.3 True stress—strain curves of TiAl alloys: (a) Ti-45Al-5Nb alloy; (b) Ti-45Al-5Nb-0.3Y alloy
Fig.3 also reveals hot deformation behavior of both the TiAl alloys at different deformation temperatures and strain rates. At the same temperature, the flow stresses increase with the increase of strain rates. This is the reason that high strain rate results in the shortening of required time of unit strain during deformation, and plastic deformation cannot fully complete in some regions and the flow stresses ascend. At the same strain rate, the flow stresses decrease with the increase of deformation temperature, since higher temperature brings about enhancement of thermal activation, decrease of atomic critical shear stress and increase of softening degree of the alloys.
3.4 Deformed microstructures of alloys
The deformed microstructures of the alloys under 1 200℃, 0.01 s-1 condition are shown in Fig.4. In Ti- 45Al-5Nb alloy, the deformed microstructure is mainly comprised of bended and fractured lamella and recrystallization is not obvious. The deformed microstructures of Ti-45Al-5Nb-0.3Y alloy are much finer and recrystallizaion occurs obviously. A lot of fine equiaxed γ grains are formed by dynamic recrystallization, as shown in Fig.4(b). TEM image of recrystallized microstructure of Ti-45Al-5Nb-0.3Y alloy is shown in Fig.5.
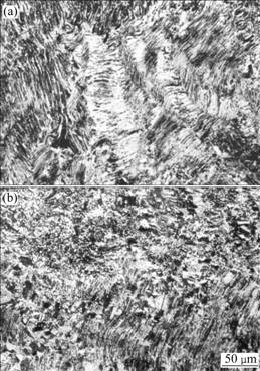
Fig.4 Deformed microstructures under 1 200℃, 0.01 s-1: (a) Ti-45Al-5Nb alloy; (b) Ti-45Al-5Nb-0.3Y alloy
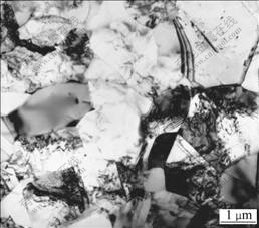
Fig.5 TEM image of recrystallized microstructure of Ti-45Al-5Nb-0.3Y alloy
3.5 Activation energy of deformation
During the hot deformation, the thermal activation is a critical factor to affect the hot deformability. The relationship among deformation temperature T, strain rate ε and stress σ is described as[16]
(1)
where Q is activation energy of deformation and indicates the hot deformability of materials; B and β are the material constants; R=8.314 J/(mol?K). So under the condition of given T and ε, Z is a constant. According to Eqn.(1), the following equation can be deduced:
(2)
where σ is peak stress. According to the true stress—train curves (Fig.3), the curves of σ—lnε and σ—1/T can be made and the slopes are calculated. The values of activation energies of deformation of Ti-45Al-5Nb alloy and Ti-45Al-5Nb-0.3Y alloys are calculated by Eqn.(2) and given in Table 2. It is found that the addition of 0.3%Y decreases the activation energy of deformation of Ti-45Al-5Nb alloy.
Table 2 Activation energy values of deformation of TiAl alloys

4 Discussion
In TiAl alloys, increasing deformation temperature, decreasing strain rate, fostering dynamic recrystallization and grain boundary movement, avoiding cracks along grain boundary and improving microstructure anisotropy have positive influences on hot deformability. Through the above experiments, Ti-45Al-5Nb-0.3Y alloy has lower flow stresses and activation energy of deformation, and more and finer recrystallized grains. All the facts reveal that the addition of 0.3%Y can effectively improve the hot deformability of Ti-45Al-5Nb alloy.
Original refined microstructure due to the addition of yttrium is well suitable for the homogeneous deformation at elevated temperature. From the view of microstructures, refining grains and increasing grain boundaries are feasible to deformability of TiAl alloys. For TiAl alloys with lamellar structures, high temperature deformation among different lamellar colonies shows obvious anisotropic property and discontinuation as a result of block effect by γ/γ interface and α2/γ interface and α2 brittle phase. Especially, in the TiAl alloys with coarse lamella, the number of grains in the unit volume is less and the orientation deviation among different lamella is relatively greater. As a result, the deformation of the TiAl alloys with coarse lamella is not homogeneous and restrained. If lamellar size is relatively fine, the orientation deviation among different lamella is relatively less. Plastic deformation doesn’t concentrate on some certain lamella but homogeneously spread around in the tested specimens. As a result, continuous and homogeneous plastic deformation appears, and hence hot deformability of TiAl alloys is improved accordingly. Furthermore, fine grains also benefit to grain boundary slide by increasing more favorable grain orientations. Previous study revealed that Ti-45Al-5Nb alloy was comprised of α2/γ two phases, fully coarse lamellar structure[9]. The addition of Y remarkably refined the lamellar colony, up to average size of 60 μm. Based on the above analysis, such small lamellar colony is feasible to homogeneous deformation.
The addition of yttrium into Ti-45Al-5Nb alloy enhances the dynamic recrystallization, which leads to finer recrystallized grains during the hot deformation (Fig.4(b)). These fine recrystallized grains can promote boundary movement and grain rotation during the deformation. As a result, the flow stress decreases and the alloys tend to soften. Large deformation can be obtained and hot deformability is improved.
The reasons for the improvement of dynamic recrystallization due to Y addition may be as the follows. Firstly, dynamic recrystallization nucleation is promoted by the increase of boundary areas due to the refinement effect of Y addition. Secondly, the dispersion of YAl2 phases can enhance recrystallized nucleation of Ti-45Al-5Nb alloy. A large number of fine YAl2 phases distribute in the matrix and are further broken into small pieces after deformation. During deformation a mass of dislocations pile up and jam around the YAl2 phases, which leads to the increase of accumulated energy in the regions. Therefore, the existence of accumulated energy improves the driving force of recrystallized nucleation. Thirdly, the fine and broken YAl2 phases can effectively block the growth of recrystallized grains after nucleation. In fact, growth of the recrystallized grains is the shift of boundaries. The dispersed second phase of YAl2 particles produces great resistance to the shift of boundaries, and growth of recrystallized grains is suppressed.
The addition of Y can remarkably decrease flow stress and activation energy of deformation, which improves the hot workability of Ti-45Al-5Nb alloy obviously. The effects are considered the comprehensive results of grain refinement and dynamic recrystallization.
5 Conclusions
1) The addition of 0.3%Y remarkably refines the microstructure of Ti-45Al-5Nb alloy and leads to the formation of a Y-rich phase—YAl2 compound.
2) Increasing deformation temperature and decreasing strain rate can improve the hot deformability of TiAl alloys. An appropriate hot deformation processing parameter of Ti-45Al-5Nb-0.3Y alloy is determined to be 1 200 ℃, 0.01 s-1.
3) The addition of 0.3%Y obviously improves the hot deformability of lamellar Ti-45Al-5Nb alloy. The smaller the original lamellar colonies, the lower the deformation resistance and activation energy of deformation are, and the more the dynamic recrystallizaion is.
References
[1] CHEN Yu-yong, KONG Fan-tao, TIAN Jing, CHEN Zi-yong, XIAO Shu-long. Recent developments in engineering γ-TiAl intermetallics [J]. Trans Nonferrous Met Soc China, 2002, 12(4): 605-609.
[2] LORIA E A. Gamma titanium aluminides as prospective structural materials [J]. Intermetallics, 2000, 8: 1339-1345.
[3] HUANG Zhao-hui. Isothermal forging of γ-TiAl based alloys [J]. Trans Nonferrous Met Soc China, 2003, 13(6): 1325-1328.
[4] MAZIASZ P J, LIU C T. Development of ultrafine lamellar structures in two-phase γ-TiAl alloys [J]. Metall Mater Trans A, 1998, 29A: 105-117.
[5] APPEL F, OEHRING M, PAUL J D H, KLINKENBERG C, CAMEIRO T. Physical aspects of hot-working gamma-based titanium aluminides [J]. Intermetallics, 2004, 12: 791-802.
[6] SEMIATIN S L, SEETHARAMAN V, WEISS I. Hot workability of titanium and titanium aluminide alloys—An overview [J]. Mater Sci Eng A, 1998, A243: 1-24.
[7] APPEL F, OEHRING M, WAGNER R. Novel design concepts for gamma-base titanium aluminide alloys [J]. Intermetallics, 2000, 8: 1283-1312.
[8] TETSUI T, SHINDO K, KOBAYASHI S, TAKEYAMA M. Strengthening a high-strength TiAl alloy by hot-forging [J]. Intermetallics, 2003, 11: 299-306.
[9] JIN Z, GEORGE T, GRAY III, KIM Y W. Texture evolution during α-forging of γ-TiAl alloys [J]. Mater Sci Eng A, 1997, A239/240: 729-735.
[10] IMAEV V M, IMAEV R M, KUZNETSOV A V, OEHRING M, APPEL F. New approaches to the thermomechanical treatment of cast intermetallic alloys based on aluminides (γ-TiAl+α2-Ti3Al) [J]. Physics of Metals and Metallography, 2005, 100: 142-152.
[11] CHEN Y Y, LI B H, KONG F T. Effect of rare earth Y (0.3 at%) on as-cast microstructure of Ti-45Al-5Nb alloy [J]. Rare Metal Materials and Engineering, 2006, 35(1): 1-4. (in Chinese)
[12] KONG Fan-tao, CHEN Zi-yong, TIAN Jing, CHEN Yu-yong. Grain and lamellar refinement in TiAl based alloy by yttrium addition [J]. Trans Nonferrous Met Soc China, 2003, 13(S1): 133-135.
[13] WU Y. HAGIHARA K, UMAKOSHI Y. Influence of Y-addition on the oxidation behavior of Al-rich γ-TiAl alloys [J]. Intermetallics, 2005, 12: 519-532.
[14] CHEN Y Y, KONG F T, HAN J C, CHEN Z Y, TIAN J. Influence of yttrium on microstructure, mechanical properties and deformability of Ti-43Al-9V alloy [J]. Intermetallics, 2005, 13: 263-266.
[15] LI B H, KONG F T, CHEN Y Y. Effect of yttrium addition on microstructures and room temperature tensile properties of Ti-47Al alloy [J]. Journal of Rare Earths, 2006, 24: 352-356.
[16] ZHANG J, ZHANG Z H, SU X, ZOU D X, ZHONG Z Y, LI C G. Microstructure preparation and hot-deformation of Ti-46.2Al-2.0V- 1.0Cr-0.5Ni alloy [J]. Intermetallics, 2000, 8: 321-326.
Foundation item: Project(50274035) supported by the National Natural Science Foundation of China
Corresponding author: LI Bao-hui; Tel: +86-451-86418802; E-mail: hitlbh@hit.edu.cn
(Edited by LI Xiang-qun)