
Flow field simulation of double layer atomizer
ZHAO Wen-jun(赵文军), CAO Fu-yang(曹福洋), NING Zhi-liang(宁志良), SUN Jian-fei(孙剑飞)
School of Materials Science and Engineering, Harbin Institute of Technology, Harbin 150001, China
Received 10 June 2009; accepted 15 August 2009
Abstract: The influences of parameters, such as delivery tube structure, gas pressure and the distance between the primary atomizer and the secondary atomizer, on gas flow field were investigated by simulation. The effects of primary pressure on gas velocity at the centerline were compared. Water atomizing experiment was carried out to validate gas scatter angle. The results show that the structure of primary atomizer plays an important role in the flow field near the exit of delivery tube. Metal protector with conical surface at the body extends certain length into the gas flow field to generate greater negative pressure near the tip of delivery tube. The application of primary gas can suppress the circulation generated by only using the secondary atomizer.
Key words: atomization; gas flow field; simulation
1 Introduction
The outline and the microstructures of the spray forming product depend on the shape and size of droplets together with fraction solid and the distribution of the droplets along the jet direction greatly during spray forming process[1-5]. The states of all droplets are significantly affected by gas flow field generated by the atomizer. Research on the gas flow field benefits better understanding the influence of the gas flow on the droplets[6-8]. The design of conventional atomizer includes closed atomizer and open atomizer, as shown in Fig.1(a). The two atomizers have their own advantages and disadvantages[9]. The former generates a negative pressure zone, which causes a drag force on the melt in the delivery tube to keep steady metal flow. A close combination between closed atomizer and the delivery tube makes the kinetic energy transformed easily from gas jet to the melt and the sound droplets are produced. But it often causes solidification for the melt in the delivery tube and restricts the moving of atomizer. The design of open atomizer as shown in Fig.1(b) is simple and does not need a delivery tube with complicated structure and precise sizes. This design is often applied to atomizing high activation melt to permit the moving of the atomizer. Its disadvantage lies in its long distance between the exit of nozzle and the melt, leading to the loss of kinetic energy and unstable spraying. For designingan atomizer with suitable structure, lots of research work was loaded on analysis of the flow fields generated by various atomizers[10-14]. Double layer scanning atomizer as shown in Fig.1(c) combines the advantages of both atomizers motioned above[15]. Using this atomizer, the melt flowing out from the delivery tube keeps steady and the spray core scans freely.
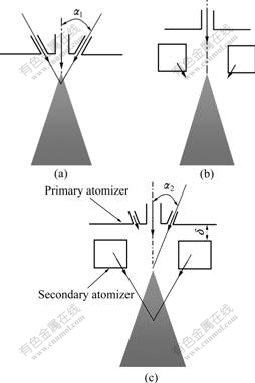
Fig.1 Sketches of three atomizer structures: (a) Closed atomizer; (b) Open atomizer; (c) Double layer scanning atomizer
In the present study, the effects of parameters on gas flow field were investigated and validated by water atomization experiments, aiming at the structure and processes optimization.
2 Experimental
The double layer atomizer with laval type primary nozzle and straight orifice secondary nozzle was used. The inside diameter of delivery tube was 3.2 mm. Secondary atomizer was located at a horizontal position. 2D axisymmetric swirling model, as shown in Fig.2, was applied due to the rotational symmetry of this set-up. The numerical simulation area was 400 mm in length and 200 mm in width, in which the meshes comprise triangles and quadrangles. Compressibility and turbulence effects were taken into account. Nitrogen gas for simulation and validation experiment was used. The gas pressure was relative pressure. Both primary and secondary nozzles were circle orifices with areas of 1.27×10-5 m2 and 2.23×10-4 m2, respectively. The Fluent software was applied to simulating the gas flow field.
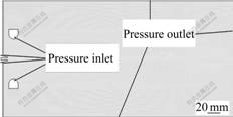
Fig.2 2D numerical model area of atomization gas flow field
3 Results and discussion
3.1 Influence of delivery tube structure on gas flow field
The primary atomizer plays the role of delivering mainly similar to the traditional closed atomizer and the atomizing effect of primary atomizer is unconspicuous. So angle α2 of the primary atomizer between primary orifice and centerline was selected to be 12.5? in Fig.1(c), smaller than angle α1 of 15?-30? for closed atomizer commonly used in Fig.1(a). The atomization operation was carried out by the secondary atomizer mostly with the function of scanning at the same time. The influence of the primary gas pressure of 0.5 MPa and the secondary gas pressure of 0 MPa on pressure distribution and gas velocity streamlines is shown in Fig.3. The structure of metal protector and the length of delivery tube out of the metal protector play an important role in the flow of gas jet from primary atomizer. In Fig.3(a), the end of metal protector is a conical surface with a certain length out of primary atomizer. There is a non-uniform pressure distribution at tip of the tube with two higher pressure zones of 0.137 MPa in point A and 0.026 MPa in point C with a distance of 10 mm from delivery tube tip. The formation of the higher pressure zone A originates from that gas jets impinge on the outside wall of delivery tube and reflect, resulting in a reduction in the velocity and an increase in pressure caused by the energy changing from kinetic energy to potential energy. An aspiration pressure area (pB=-0.034 MPa) is generated near position B, which forms a pumping action on the melt in the delivery tube and benefits the flow of the melt. In Fig.1(b), the velocity streamline distribution shows that the gas flow is steady without circulation. For the second structure, the end of metal protector is a flat surface keeping the same height with the exit of primary nozzle, as shown in Fig.3(c). For the structure, there are two higher pressure zones of 0.111 MPa pressure in point E and 0.013 MPa in point G and two negative pressure zones of -0.113 MPa in point D and -0.015 7 MPa in point F. Compared with Fig.3(a), there is one more negative pressure zone in point D, which disturbs steady gas flow ejected from the primary nozzle. There is a circulation near point D, as shown in Fig.3(d). During operation of the double layer atomizer, viscous molten metal will clog the gas orifice easily when a little metal droplet is transported to negative pressure zone D. Compared with negative pressure near the exit of the delivery tube generated by both units, the negative value in point F is smaller than that in point B. Flow streamline distribution in Figs.3(b) and (d) shows that the structure in Fig.3(a) is better than that in Fig.3(c).
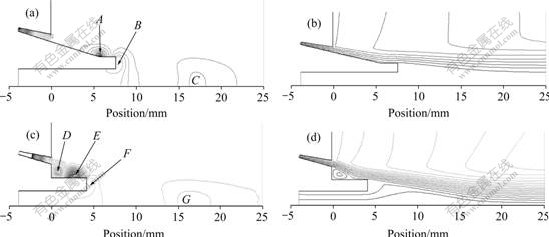
Fig.3 Pressure and flow streamline distribution: (a) Primary gas pressure distribution of metal protector with circular conical surface; (b) Velocity streamlines of structure in Fig.3(a); (c) Primary gas pressure distribution of metal protector with cylinder surface; (d) Velocity streamlines of structure in Fig.3(c)
During the operation the molten metal flowing out of the tube is expected to be transported into the center hole of secondary atomizer as soon as possible, which needs a small distance of δ in Fig.1(c). The diameter of secondary atomizer should be larger in order to avoid the molten metal clogging on the inside surface of secondary atomizer caused by gas turbulence. When the atomizer works, the secondary atomizer should keep a certain distance from the primary atomizer because of scanning. Both factors influence the unit design.
The gas velocity distribution as a function of radical distance at different axial distances is shown in Fig.4. The operation conditions are the same as those in Fig.3(a) and the axial distances used are 20, 30, 40 and 50 mm from the tip of delivery tube, respectively. The maximum gas velocity along radius decreases gradually with increasing axial distance, as shown in Fig.4. At the axial distance of 20 mm, the influence scope of gas jet is15 mm, and increases to 25 mm when axial distance changes to 50 mm. Meanwhile, the gas ejected from annular gap expands and stacks at the centerline, resulting in an increase in the axial velocity within the axial scope. The simulation results indicate that the diameter of center hole should be more than 25 mm when the distance between primary and secondary atomizer is less than 50 mm. Taking account of safety and stability, the diameter of secondary atomizer is larger than 50 mm in the present study. The distance δ in Fig.1(c) is in the range of 10-20 mm when the secondary atomizer scans to a limited position. Considering the secondary atomizer’s volume and the gas supplying channel, a certain distance should be kept between the secondary and primary atomizers.
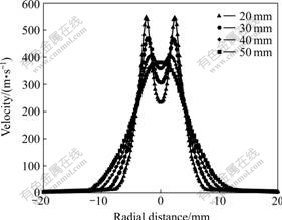
Fig.4 Gas velocity distribution as function of radial distance at different axial distances
3.2 Gas flowing field of double layer scanning atomizer
Fig.5 shows the effect of primary gas pressure up to 1 MPa on gas flow with a constant secondary pressure of 1 MPa. The gas flow field is illustrated in Fig.5(a) when only the secondary atomizer is applied. The velocity streamline distribution in Fig.5(a) indicates that there are two intense circulation flow areas in points M and N. The scope of circulation M extends from underneath the secondary atomizer to the primary atomizer and decreases with increasing primary gas pressure to 1 MPa. Scope N is relatively small and the effect of primary gas pressure on it can be neglected. The circulation forming is restrained effectively within a certain limit by increasing primary gas pressure.
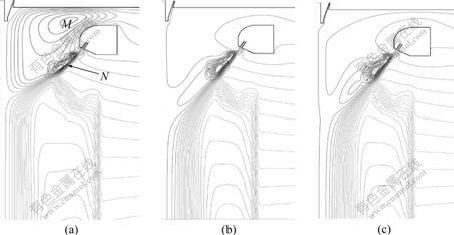
Fig.5 Effect of primary gas pressure on gas flow velocity streamlines at constant secondary pressure of 1 MPa: (a) 0; (b) 0.5 MPa; (c) 1 MPa
Keeping secondary gas pressure of 1 MPa, the effect of axial gas flow velocity on the centerline of the atomizer is shown in Fig.6. Increasing primary gas pressures from 0.5 to 1.5 MPa, the axial gas velocity increases within distance of 100 mm and almost keeps same in the distance range of 100-400 mm. When both primary pressure and secondary pressure are applied the axial gas velocity is slower than that when the secondary pressure is applied only in the distance range of 50-250 mm, similar to the results in Ref.[16]. One reason is that after increasing the primary pressure, the gas is originally centered on the centerline scatters, so the axial gas velocity reduces, as shown in Fig.7. The velocities along radial direction at axial distances of 100 and 150 mm are shown in Figs.7(a) and (b), respectively. The influencing scope of gas increases in radial direction when both atomizers are applied. Another reason lies in the change of the position for the highest gas pressure zone. The highest pressure zones are located at the position underneath the secondary atomizer at axial distances of 50 and 65 mm as shown in Fig.8, respectively, for different primary gas pressures. The gas streamlines bend downwards caused by the moving down of the highest pressure zone. Therefore, the influence of the secondary atomizer on the gas velocity at the centerline goes down. Otherwise, the impinging between primary gas and secondary gas results in the loss of kinetic energy and the decrease in the gas velocity.
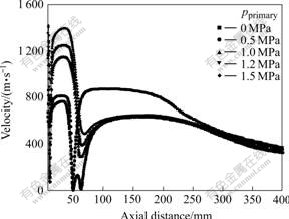
Fig.6 Axial gas velocity as function of axial distance
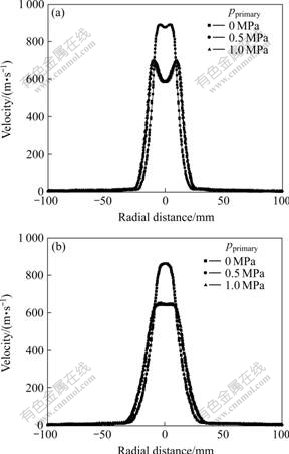
Fig.7 Velocity distribution as function of radial distance at secondary gas pressure of 1.0 MPa and axial distance of 100 mm(a) and 150 mm(b)
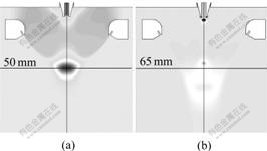
Fig.8 Pressure distribution of two operating conditions: (a) Primary gas pressure of 0 MPa; (b) Primary gas pressure of 0.5 MPa
Water atomization experiments are used to validate the outline of numerical gas flow field, and the results are shown in Fig.9. Comparing the contour of velocity field and one of the experiment photo of water atomizing at the primary pressure of 0.5 MPa and secondary pressure of 1.0 MPa, the gas scattering angle simulated is 18?, which is very close to the measured one of 19?, indicating that the simulation model can be used to simulate the gas flow field effectively.

Fig.9 Gas velocity distribution and water atomization: (a) Numerical result of velocity distribution; (b) Water atomization photo
4 Conclusions
1) Atomizer with the tip of the metal protector extending certain length out of the primary nozzle generates greater negative pressure.
2) According to the scatter scope of gas emitted from primary atomizer, the diameter of secondary atomizer center hole is determined, which is larger than 25 mm at least, but for security, this diameter is set to be 50 mm.
3) The gas from primary atomizer stabilizes the atomization process and suppresses the circulation flow generated by secondary gas, which is used to atomize the liquid mainly.
4) At axial line, when only secondary atomizer is applied the gas velocity is higher than that when both atomizers work. The influence of gas ejected from the primary atomizer in the axial line area becomes weaker after the primary gas pressure is increased. Therefore, the gas velocity at center line slows down, but scatter scope becomes larger.
References
[1] GRANT P S. Spray forming progress[J]. Materials Science, 1995, 39(4/5): 497-545.
[2] LAVERNIA E J, WU Y. Spray atomization and deposition[M]. New York: John Wiley, 1996: 51-68.
[3] GRANT P S, CANTOR B. Modeling of droplet dynamic and thermal histories during spray forming-Ⅱ. Effect of progress parameters[J]. Acta Metallurgica et Materialia, 1993, 41(11): 3109-3118.
[4] LI Xian-guo. Mechanism of atomization of a liquid jet[J]. Atomization and Sprays, 1995, 5(1): 89-105.
[5] TING J, CONNOR J, RIDDER S. High-speed cinematography of gas-metal atomization[J]. Mater Sci Eng A, 2005, 390(1/2): 452-460.
[6] LI Zhou, ZHANG Zhi-hui, ZHANG Guo-qing, MI Guo-fa, LIU Zhong-wu, TIAN Shi-fan, YAN Ming-gao. Velocity of atomization gas during spray forming[J]. The Chinese Journal of Nonferrous Metals, 1999, 9(S1): 92-99. (in Chinese)
[7] LASHERAS J C, HOPFINGER E J. Liquid jet instability and atomization in a coaxial gas stream[J]. Annu Rev Fluid Mech, 2000, 32: 275-308.
[8] TING J, ANDERSON I E. A computational fluid dynamics (CFD) investigation of the wake closure phenomenon[J]. Mater Sci Eng A, 2004, 379(1/2): 264-276.
[9] MATES S P, SETTLES G S. A study of liquid metal atomization using close-coupled nozzles. Part 1: Gas dynamic behavior[J]. Atomization and Sprays, 2005, 15(1): 19-40.
[10] HECK U, FRITSCHING U, BAUCKHAGE K. Gas flow effects on twin-fluid atomization of liquid metals[J]. Atomization and Sprays, 2000, 10(1): 25-46.
[11] ZEOLI N, GU S, KAMNIS S. Numerical modeling of metal droplet cooling and solidification[J]. International Journal of Heat and Mass Transfer, 2008, 51(15/16): 4121-4131.
[12] TONG M M, BROWNE D J. Modelling compressible gas flow near the nozzle of a gas atomiser using a new unified model[J]. Computers and Fluids, 2009, 38(6): 1183-1190.
[13] JEYAKUMAR M, GUPTA G S, KUMAR S. Modeling of gas flow inside and outside the nozzle used in spray deposition[J]. Journal of Materials Processing Technology, 2008, 203(1/3): 471-479.
[14] OUYANG Hong-wu, HUANG Bai-yun, CHEN Xin, YU Wen-tao. Melt metal sheet breaking mechanism of close-coupled gas atomization[J]. Trans Nonferrous Met Soc China, 2005, 15(5): 985-992.
[15] CAO Fu-yang, WU Pei-lian, NING Zhi-liang, ZHAO Wen-jun, SUN Jian-fei. Shape-predicted model of spray forming rod under scanning atomization[J]. Rare Metals, 2007, 26: 30-35.
[16] CZISCH C, FRITSCHING U. Flow-adapted design option for free-fall atomizers[J]. Atomization and Sprays, 2008, 18(6): 511-522.
(Edited by CHEN Wei-ping)
Corresponding author: SUN Jian-fei, Professor; Tel: +86-451-86418317; E-mail: jfsun_hit@263.net