DOI:10.19476/j.ysxb.1004.0609.2019.06.19
铁粉还原法沉淀Cu(Ⅱ)、As(Ⅲ)的反应行为
郑 宇,邓志敢,樊 光,魏 昶,樊 刚,李兴彬,李存兄,李旻廷
(昆明理工大学 冶金与能源工程学院,昆明 650093)
摘 要:以锌浸渣还原浸出液作为研究对象,研究铁粉与还原浸出液中Cu(Ⅱ)、As(Ⅲ)的反应行为。热力学计算表明,在锌浸渣还原浸出液中,加入铁粉使溶液中Cu(Ⅱ)、As(Ⅲ)转化为Cu2O和Cu3As沉淀是可行的。实验结果表明:最佳反应条件为铁粉加入系数1.2、反应时间25 min、反应温度70 ℃,在此条件下,还原浸出液中铜、砷的沉淀率能达到99%以上;通过对沉铜渣进行XRD分析表明,沉铜渣中主要成分为Cu2O和Cu3As;SEM-EDS检测显示,反应产物Cu2O和Cu3As在铁粉表面呈点状、散乱分布,没有对铁粉表面形成致密包裹,使反应充分进行。此外,增大铁粉加入系数、提高反应温度都能促进Cu2O和Cu3As的形成。
关键词:还原浸出液;铁粉;反应行为;热力学
文章编号:1004-0609(2019)-06-1298-10 中图分类号:TF803.23 文献标志码:A
从锌浸出渣中回收锌的常规方法有热酸浸出法、回转窑挥发法、Ausmelt炉挥发法等[1-2]。热酸浸出法处理锌浸渣时,铜、铟回收率低,锌、铟分离困难。采用回转窑挥发法、Ausmelt挥发法等常规火法工艺处理锌浸渣时,不利于高沸点金属回收,产生的烟气和窑渣对环境污染严重。近年来,国内外学者又探索出了机械活化法、还原浸出法等新型方法处理锌浸渣[3-6]。
本课题组前期实验[7]采用SO2还原浸出的方法处理锌浸出渣,锌的浸出率达到了99%,铜、铟的浸出率分别为95%和97%,实现了主要有价金属的高效浸出;在还原浸出过程中,SO2还原气氛有效促进了溶液中Fe(Ⅲ)向Fe(Ⅱ)的转变;此外,还原浸出液中的砷含量达到了0.56 g/L,主要以As(Ⅲ)的形式存在。
在湿法炼锌过程中,锌精矿中的砷会在冶炼过程中进入到溶液中,未经处理排放会对环境造成极大的危害[8-9];当前比较系统的处理含砷废水的方法有:化学沉淀法,物理化学法,生物化学法等。这类中和法获得的砷酸盐稳定性差,长期堆存易造成二次污染[10-11]。除了砷之外,还原浸出液中还含有一定量的铜,对于低浓度含铜溶液中铜的回收有置换法、电解法、结晶及化合物析出法等,其中离子交换法相对成熟[12]。STEFANOWICZ等[13-15]利用铜的标准电位与金属沉淀剂不同,一些电负性比铜大的金属可以从溶液中将铜置换沉淀。由金属的标准电位可知:镁、铝、锌、铁等都可以从溶液中把铜置换沉淀,这些金属都常用来置换回收铜或者处理含铜的废水。从SO2还原浸出锌浸渣过程得到的含铜还原浸出液酸度较高,Fe(Ⅲ)浓度低,且后续除铁方法为赤铁矿除铁工艺,采用铁粉置换沉铜,能在不引入其他杂质离子的前提下,达到富集铜、沉淀砷的目的。
刘志宏等[16]对酸性水溶液中,还原铁粉与As(Ⅲ)反应的砷分配比进行了研究,证实了金属铁与As(Ⅲ)的反应不会有AsH3生成,符合GB 17055-1997[17]所规定的车间空气中AsH3浓度要求规定。铁粉置换沉铜相较于电解法和化合物析出法回收铜,具有原料来源广泛、价格低廉等优点[18]。除此之外,还原铁粉法处理还原浸出液,能在富集铜的同时将砷大量地沉淀于渣中,为后续工段铜的回收和砷的脱除创造了条件。本文作者对还原浸出液中砷、铁、铜的反应行为进行研究,为处理污酸硫化砷渣、黑铜粉、湿法炼锌窑渣铁精矿等矿石或精矿提供了思路。
1 实验原理
还原铁粉微观结构疏松、表面积大,还原铁粉与溶液体系中Cu(Ⅱ)、As(Ⅲ)等离子发生反应一般经过以下几个步骤:溶液体系中反应组分向反应物表面扩散,并在铁粉的表面形成一层电解质层;电解质层中Cu(Ⅱ)、As(Ⅲ)等反应组分吸附在还原铁粉表面并在界面上发生化学反应;反应完成后,反应产物从界面上脱离并由反应界面向溶液体系中扩散。反应发生过程中,Cu(Ⅱ)、As(Ⅲ)在溶液中的迁移速率是整个反应限制性环节,除少数几个体系的反应动力学会受电化学反应机理控制外,大多都属扩散控制机理。
铁粉沉砷、富集铜涉及氧化还原反应,物种的氧化性强弱与反应体系pH关系密切。就水溶液中发生的化学反应而言,根据φ-pH图可以直观了解不同氧化还原电势和pH值条件下反应体系内各种形态化合物或离子的相互平衡情况。谢学军等[19]绘制的Cu-H2O体系φ-pH图(溶液温度298 K, 活度a=1),如图1所示。由Cu-H2O体系φ-pH图可知,Cu(Ⅱ)在酸性溶液中存在的优势区域较大,利用铁粉表现出来的还原性和酸性体系中Cu(Ⅱ)所表现出来的氧化性,设计的反应体系具有较高的热力学反应趋势。
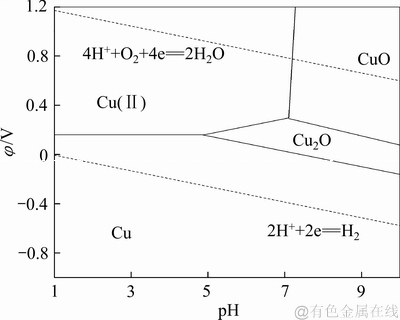
图1 Cu-H2O体系φ-pH图
Fig. 1 φ-pH predominance diagram of Cu-H2O system (298 K, a=1)
按照金属活动顺序,加入的铁粉会先与还原浸出液中的Cu(Ⅱ)发生反应(1),反应(1)所生成的铜是一种不同于金属晶体的新生态原子铜,它会迅速与体系中存在的Cu(Ⅱ)继续发生氧化还原反应(2),并最终生成氧化亚铜[20]。就整个过程来说,反应(3)为生成氧化亚铜的总反应。
Fe+CuSO4=FeSO4+Cu (1)
Cu+CuSO4+H2O=Cu2O+H2SO4 (2)
Fe+2CuSO4+H2O=FeSO4+Cu2O+H2SO4 (3)
除此之外还发生副反应:
Fe+Fe2(SO4)3=3FeSO4 (4)
在298 K时,根据热力学数据,计算得到反应(3)的
= -117.83 kJ/mol,反应具有较大的热力学推动力,因此利用铁粉的还原性在水溶液中还原Cu(Ⅱ)的工艺是可行的。
陈白珍等[21]绘制的Cu-As-H2O体系φ-pH图(298 K, a=1),如图2所示。由Cu-As-H2O体系φ-pH图可知,Cu3As存在的稳定区域较大,由于前期是采用二氧化硫还原浸出锌浸渣,还原浸出液中的砷主要以As(Ⅲ)的形式存在,在加入铁粉的情况下,溶液中As(Ⅲ)的沉淀可按反应(5)进行。
6Cu(Ⅱ)+2As(Ⅲ)+9Fe=9Fe(Ⅱ)+2Cu3As (5)
在298 K时,根据热力学数据,计算得到反应(5)的
= -1165.8 kJ/mol,反应(5)的热力学推动力较大,因此加入铁粉使体系中As(Ⅲ)和Cu(Ⅱ)以Cu3As的形式共同沉淀是可行的。
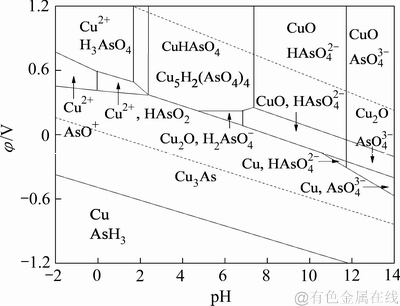
图2 Cu-As-H2O体系φ-pH图[20]
Fig. 2 φ-pH predominance diagram of Cu-As-H2O system (298 K, a=1)[20]
2 实验
2.1 实验原料
实验所用分析纯级还原铁粉的SEM像如图3所示,实验所用还原浸出液化学组成如表1所示。
表1 还原浸出液化学组成
Table 1 Chemical composition of reductive leach solution
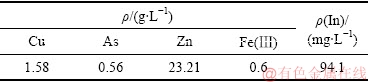
由图3可知,还原铁粉呈多孔、类球形烧结体形貌,颗粒直径在20~30 μm;还原铁粉主要成分为结构疏松的单质铁。由于还原铁粉本身已为粉末状,再加之其微观结构又十分疏松,故其表面积极大,在化工生产及实验室作业中是一种十分优质的还原剂。实验所用还原浸出液中,Fe(Ⅲ)含量低,仅为0.6 g/L;有价金属铜含量高,达到了1.58 g/L;与此同时,As的含量也达到了0.56 g/L,n(Cu)/n(As)约为3.3。
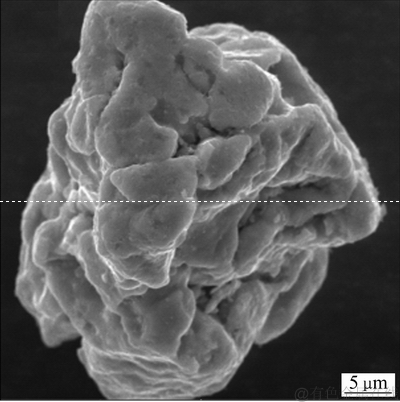
图3 还原铁粉的SEM像
Fig. 3 SEM images of reduced iron powders
2.2 实验设备与方法
将HH-S26S型数字显示电子恒温水浴锅(金坛市大地自动化仪器厂生产)固定在实验平台上,用量筒(天津市天玻玻璃仪器有限公司生产)量取实验预定用量的锌浸渣还原浸出液,置于三口烧瓶(天津市天玻玻璃仪器有限公司生产)中,将三口烧瓶固定在恒温水浴锅内,并在三口烧瓶一侧开口安装温度计,实时测定反应体系温度;然后设定恒温水浴锅温度、开启具有转速显示功能的AM200W-H型无极调速电动搅拌机(上海昂尼仪器仪表有限公司生产)对三口烧瓶中的液体进行搅拌和加热。将三口烧瓶中的锌浸渣还原浸出液加热到预定实验温度后,将预备好的实验用量的分析纯级铁粉(天津市恒兴化学试剂制造有限公司生产)一次性加入三口烧瓶中,反应开始,开始计时;观察并记录反应过程中的实验现象。
实验达到预定的反应时间后,停止搅拌和加热,并对冷却后的反应终点的液体通过2XZ-2型旋片式真空泵(浙江台州求精真空泵有限公司生产)进行固液分离,将所得的液体送分析,将渣置于DZF-6090真空干燥箱(上海一恒科学仪器有限公司生产)中恒温烘干,称量记录、分析成分。
2.3 分析检测与计算
本实验研究中,沉铜后液和沉铜渣中铜和砷的检测委托昆明冶金研究院分析测定,并借助X射线衍射仪对沉铜渣进行晶相组成分析,采用钨丝灯扫描电镜对沉铜渣进行宏观、微观形貌分析;铜、砷的沉淀率采用式(6)进行计算:
(6)
式中:η为铜或砷的沉淀率,%;c1为反应前溶液中铜或砷的含量,g/L;V1为反应前的溶液体积,L;c2为反应后的溶液中铜或砷的含量,g/L;V2为反应后的溶液体积,L。实验中,还原铁粉加入系数(n)采用式(7)进行计算:
(7)
式中:m(Fe)为实际铁粉加入量,g;m1(Fe)、m4(Fe)分别为反应(1)和(4)的理论铁粉消耗量,g。
3 结果与讨论
3.1 铁粉加入系数对沉铜过程的影响
当控制体系温度为80 ℃、搅拌转速为400 r/min、反应时间为20 min时,不同铁粉加入系数对铜、砷沉淀率的影响如图4所示;铁粉加入系数不同时沉铜渣的XRD谱、SEM像和EDS分析结果分别如图5、6和7所示。
铁粉加入系数对铜、砷沉淀率的影响如图4所示。由图4可知:随着铁粉加入系数的增大,铜、砷的沉淀率都呈增大趋势;在铁粉加入系数从0.7增加到1.1过程中,砷的沉淀率提高迅速,从53%提高到了94%;铁粉加入系数达到1.3时,砷接近完全沉淀。铁粉加入系数从0.9增加到1.2的过程中,铜的沉淀率迅速提高,当铁粉加入系数达到1.2时,还原浸出液中铜沉淀完全。
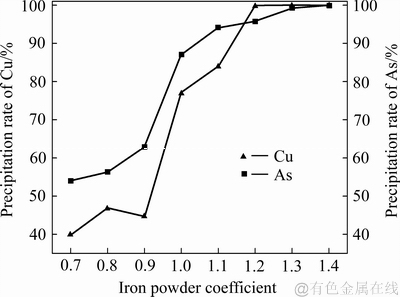
图4 铁粉加入系数对沉砷率、沉铜率的影响
Fig. 4 Effect of iron powder coefficients on precipitation rates of As and Cu
随着铁粉加入系数的提高,铜、砷沉淀率增大;当加入到还原浸出液中的铁粉量较少时,铁粉全部溶解,并有气泡冒出,但没有沉淀产生。当铁粉加入系数提高到1时,铜、砷的沉淀率仅为76%和86%,主要是因为在溶液中不仅还原铁粉和Cu(Ⅱ)、As(Ⅲ)离子进行反应,溶液中H+和Fe(Ⅲ)离子也能与还原铁粉发生反应,这些副反应将消耗部分还原铁粉。
铁粉加入系数为0.7、1.0、1.2的沉铜渣的XRD谱如图5所示。由图5可知:铁粉加入系数较低时,Cu2O的特征衍射峰十分微弱;随着铁粉加入系数的增大,Cu2O的特征衍射峰逐渐增强。这可能是由于铁粉加入量较少时,生成的Cu2O含量较低或结晶度较差,因此反应产物中Cu2O的特征衍射峰不明显。
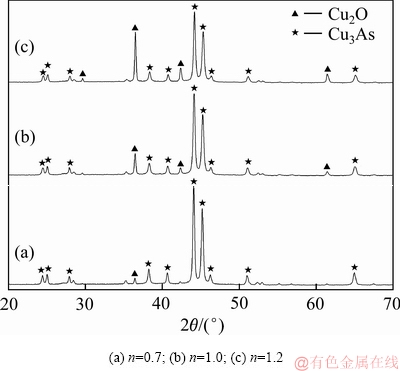
图5 不同铁粉加入系数试验滤渣的XRD谱
Fig. 5 XRD patterns of precipitates produced at different iron powder coefficients
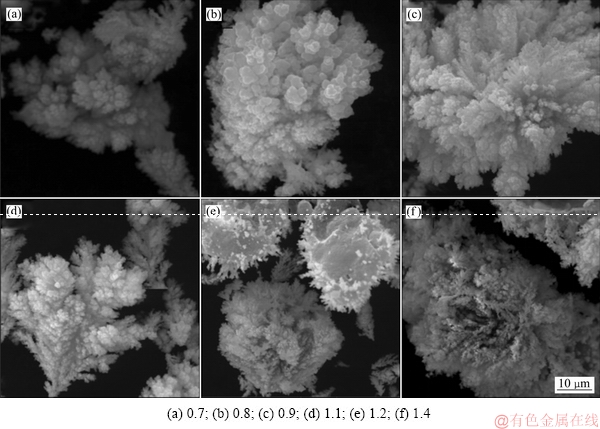
图6 铁粉加入系数试验滤渣SEM像
Fig. 6 SEM images of precipitates produced at different iron powder coefficients
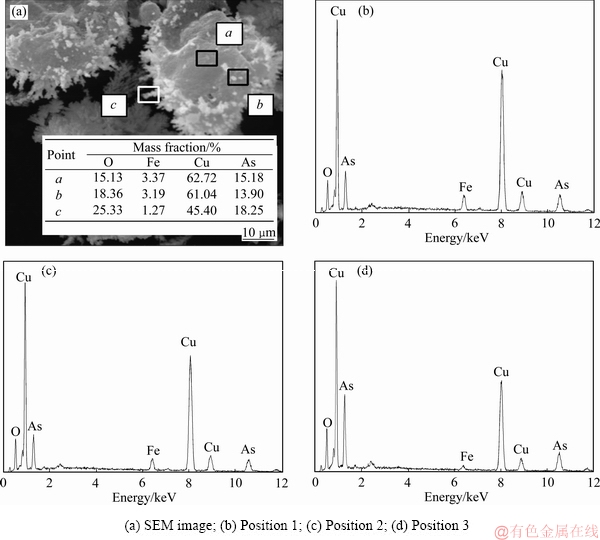
图7 沉铜渣SEM像及EDS谱
Fig. 7 SEM image of copper slag and EDS spectra in different areas
对沉铜渣进行SEM分析可知,铁粉加入系数较低时,生成物主要是团球状物体;随着铁粉加入系数的增大,生成物物相中丝絮状物体占据主导,而且形状更加规则、边界更加清晰。分别对沉铜渣中铁粉表面、团球状物体及丝絮状物相进行了EDS分析,结果如图7所示。由图7可知,铁粉表面铁的特征峰十分明显,生成物氧含量低,主要是铜、砷物相(见图7(b));团球状物相中除铜、砷物相外还明显出现了氧的衍射峰(见图7(c));丝絮状物相中氧的衍射峰进一步增强,而铁的衍射峰接近消失(见图7(d))。由此推断,铁粉表面先生成Cu3As;团球状物体主要为Cu3As以及少量的Cu2O,后期生成的丝絮状物体主要是Cu2O。反应过程中Cu3As和Cu2O松散地分布在铁粉表面,Cu2O附着于Cu3As边缘生成,生成物没有在铁粉表面形成包裹,又较易从铁粉表面脱落,因此该条件下铜、砷的沉淀率较高。
3.2 反应时间对沉铜过程的影响
当控制体系温度为80 ℃、搅拌转速为400 r/min、铁粉加入系数为1.1时,不同反应时间对铜、砷沉淀率的影响如图8所示。由图8可知:反应时间对沉铜过程影响的实验在铁粉过量条件下进行,反应前期铜的沉淀比砷快,反应时间5 min时,铜、砷的沉淀率分别能达到97%和89%;反应时间延长到10 min时,铜就能沉淀完全;反应10 min后,随着反应时间继续延长,铜并没有出现反溶的情况;在反应时间从5 min 延长至25 min的过程中,砷的沉淀率呈现出递增趋势;在反应时间达到25 min时,砷接近完全沉淀。
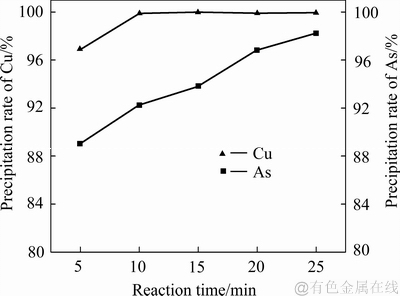
图8 反应时间对沉砷率、沉铜率的影响
Fig. 8 Effects of reaction time on precipitation rates of As and Cu
对不同反应时间所得的沉铜渣进行XRD检测分析,结果如图9所示。由图9可知:在铁粉过量的条件下,反应5 min时就出现了较高的Cu2O和Cu3As衍射峰,表明了在较短的反应时间内就能生成大量的Cu2O和Cu3As。对沉铜渣的SEM分析结果如图10所示。由图10可知:丝絮状Cu2O较球团状Cu3As更多,这是因为还原浸出液中铜含量较砷含量高,n(Cu)/n(As)达到了3.3,因此,沉铜渣中Cu2O含量较高。随着时间延长,丝絮状Cu2O沉淀占据主导,其形状更加规则、边缘更加清晰。
3.3 反应温度对沉铜过程的影响
当控制铁粉加入系数为1.1、搅拌转速为400 r/min、反应时间为20 min时,不同反应温度对铜、砷沉淀率的影响如图11所示,XRD和SEM检测结果分别如图12和13所示。由图11可知:反应温度为50 ℃时,砷的沉淀率仅为67%,铜的沉淀率达到了92%,随着反应体系温度的升高,分子热运动更加剧烈,反应体系内活性分子的比例增大,单位时间内参加反应的分子数量增多,铜、砷的沉淀率都呈现出增大趋势;其中砷的沉淀率随温度升高增大剧烈,当反应温度从50 ℃提高至60 ℃时,砷的沉淀率从67%增大到了92%;当反应温度达到70 ℃时,反应20 min就能使铜和砷全部沉淀完全。
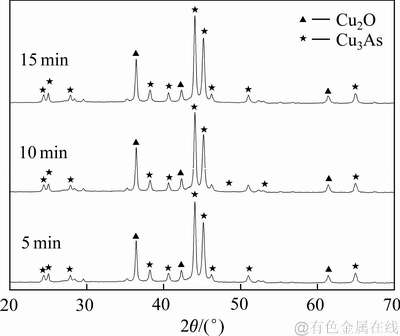
图9 不同反应时间下沉铜渣的XRD谱
Fig. 9 XRD patterns of precipitates produced at various reaction time
在铁粉过量的条件下,对不同反应温度下的沉铜渣进行XRD检测分析,结果如图12所示。由图12可知:在铁粉过量的条件下,反应温度为50 ℃,反应产物中就具有较为清晰的Cu2O、Cu3As衍射峰;在反应温度从50 ℃增加到80 ℃的过程中,随着温度的提高,Cu2O的特征衍射峰逐渐增强,而Cu3As的衍射峰并没有较大变化。由此可知,体系内反应温度对Cu3As形成过程影响较小,且温度越高,Cu2O的结晶度越好,Cu2O的特征衍射峰越强。
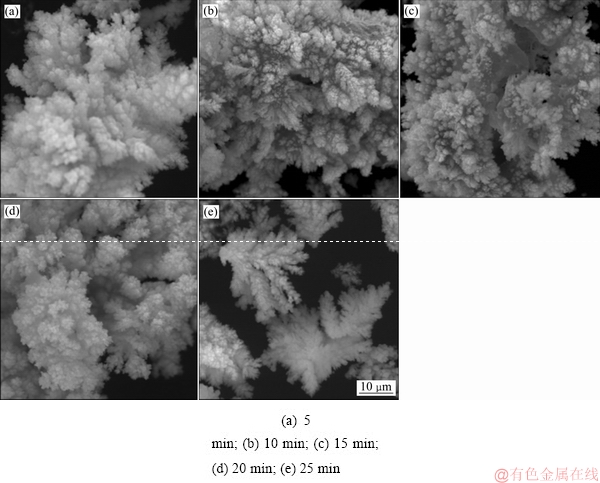
图10 不同反应时间下沉铜渣的SEM像
Fig. 10 SEM images of precipitates produced at various reaction time

图11 反应温度对沉砷率、沉铜率的影响
Fig. 11 Effects of reaction temperature on precipitation rates of As and Cu
不同反应温度下沉铜渣的SEM像如图13所示。由图13可知:反应温度为50 ℃时,产物中球团状物质占据主导,在反应温度增加的过程中,反应产物向丝絮状转变,形状更加稳定,边缘更加清晰。
4 综合条件实验
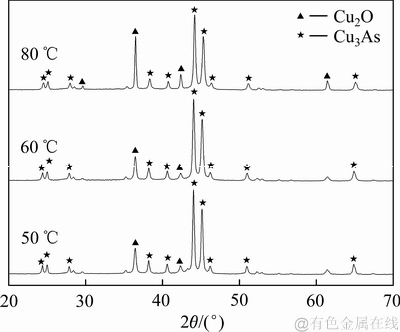
图12 不同反应温度下沉铜渣的XRD谱
Fig. 12 XRD patterns of precipitates produced at various reaction temperatures
以上三组单因素条件实验结果表明,还原铁粉法能使还原浸出液中的铜、砷实现较大程度的富集、沉淀。固定搅拌转速为400 r/min,按照单因素实验所确定的最佳反应条件(铁粉加入系数1.2,反应温度70 ℃,反应时间25 min),进一步开展了综合验证研究。
对综合验证条件沉铜后液进行了定性分析,化学成分如表2所示。沉铜后液中铜、砷含量分别为4.9 mg/L和4.22 mg/L,铜、砷的沉淀率均达到了99%以上;锌、铟损失率分别为2%和3%。综合条件实验沉铜渣化学组成如表3所示。由表3可见,铜、砷含量分别达到了62.27%和18.49%,铁粉利用率高,沉铜渣中铁含量仅为0.81%。除此之外,沉铜渣中有价金属铟仅为20.2 g/t,未检测到锌的存在,表明铟、锌得到了充分的富集。
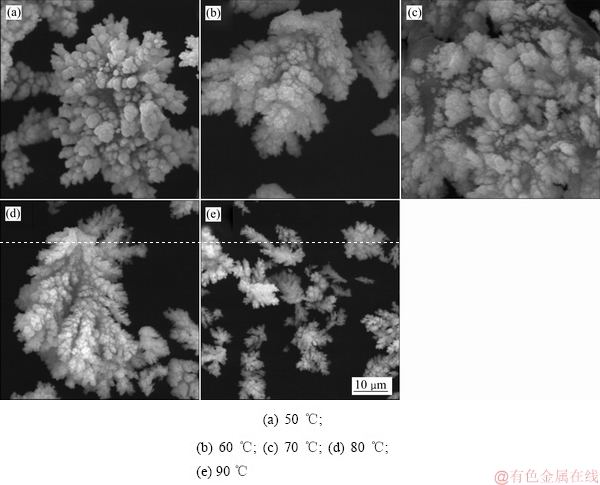
图13 不同反应温度下沉铜渣的SEM像
Fig. 13 SEM images of precipitates produced at various reaction temperatures
沉铜渣的XRD物相分析的结果如图14所示。由图14可知:样品中Cu2O和Cu3As的特征衍射峰尖锐,表明生成物的晶型良好;将检测得到的XRD波形与标准卡片对比,证明探测到的主要物相为Cu2O和Cu3As,基本没有杂质相。
表2 综合实验结果
Table 2 Comprehensive experiment results
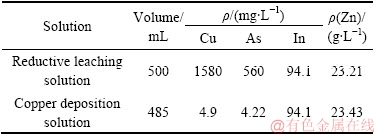
表3 沉铜渣化学组成
Table 3 Chemical composition of precipitates produced

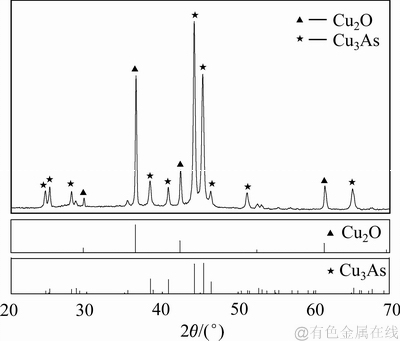
图14 沉铜渣的XRD谱
Fig. 14 XRD patterns of precipitates produced
5 结论
1) 在锌浸渣还原浸出液中,加入铁粉使溶液中Cu(Ⅱ)、As(Ⅲ)转化为Cu2O和Cu3As沉淀在热力学上是可行的;在固定搅拌转速为400 r/min、铁粉加入系数为1.2、反应温度为70 ℃、反应时间为25 min的条件下,铜、砷沉淀率都能达到99%以上;渣中铜、砷含量分别为62.27%和18.49%,为后续工段中铜的回收和砷的脱除创造了条件。
2) 铁粉加入系数和体系反应温度对Cu(Ⅱ)、As(Ⅲ)转化为Cu2O和Cu3As进行沉淀的过程有显著影响;增大铁粉加入系数、提高反应温度都能促进Cu2O和Cu3As的形成。
3) 在铁粉还原法沉淀Cu(Ⅱ)、As(Ⅲ)的过程中,反应产物Cu2O和Cu3As呈点状、疏松态分布在铁粉表面,没有对铁粉表面形成包裹,铁粉利用率高,铁粉反应充分且反应连续性好。
REFERENCES
[1] 刘洪萍. 锌浸出渣处理工艺概述[J]. 云南冶金, 2009, 38(4): 34-37.
LIU Hong-ping. Surveying the disposal process of zinc leaching-slag[J]. Yunnan Metallurgy, 2009, 38(4): 34-37.
[2] 马喜红, 覃文庆, 吴雪兰, 任浏祎. 热酸浸出锌浸渣中镓锗的研究[J]. 矿冶工程, 2012, 32(2): 71-75.
MA Xi-hong, QIN Wen-qing, WU Xue-lan, REN Liu-yi. Extracting gallium and germanium from zinc-leaching residues by hot-acid leaching process[J]. Mining and Metallurgical Engineering, 2012, 32(2): 71-75.
[3] 韩俊伟, 刘 维, 覃文庆, 蔡 鑫, 罗虹霖, 王大伟. CO还原焙烧铁酸锌的选择性分解行为[J]. 中国有色金属学报, 2016, 26(6): 1324-1331.
HAN Jun-wei, LIU Wei, QIN Wen-qing, CAI Xin, LUO Hong-lin, WANG Da-wei. Selective decomposition behavior of zinc ferrite by reduction roasting with CO[J].The Chinese Journal of Nonferrous Metals, 2016, 26(6): 1324-1331.
[4] POLSILAPA S, INTAKUEAN P, PROMBOOBPA A, The decomposition of zinc ferrite in electric arc furnace dust by carbon[J]. Key Engineering Materials, 2015, 658: 156-160.
[5] 刘 洋, 谭 军, 尹周澜, 刘常青, 陈启元, 张平民, 廖 舟, 王心皞. 湿法炼锌沉铁渣和浸锌渣的焙烧预处理[J]. 中国有色金属学报, 2016, 26(1): 212-222.
LIU Yang, TAN Jun, YIN Zhou-lan, LIU Chang-qing, CHEN Qi-yuan, ZHANG Ping-min, LIAO Zhou, WANG Xin-hao. Roasting pretreatment of iron-sinking slag and zinc leaching residue in zinc hydrometallurgy[J]. The Chinese Journal of Nonferrous Metals, 2016, 26(1): 212-222.
[6] SENANAYAKE G, CHILDS J, AKERSTROM B D, PUGAEVD. Reductive acid leaching of laterite and metal oxides—A review with new data for Fe(Ni, Co)OOH and a limonitic ore[J]. Hydrometallurgy, 2011, 110(1/4): 13-32.
[7] 郑 宇,邓志敢,樊 刚,魏 昶,樊 光,李兴彬,李存兄,李旻廷. 二氧化硫还原分解铁酸锌及锌浸渣工艺[J]. 中国有色金属学报,2019, 29(1): 170-178.
ZHENG Yu, DENG Zhi-gan, FAN Gang, WEI Chang, FAN Guang, LI Xing-bin, LI Cun-xiong, LI Min-tin. Reductive decomposition of zinc ferrite and zinc residues by sulfur dioxide[J]. The Chinese Journal of Nonferrous Metals, 2019, 29(1): 170-178.
[8] 张 晖, 周明达, 张利民, 刘国聪. 改性沸石处理水中砷的研究[J]. 贵州化工, 2006, 31(2): 7-9.
ZHANG Hui, ZHOU Ming-da, ZHANG Li-min, LIU Guo-cong. Study on the removal of arsenic from water by modified clinoptilolite[J]. Guizhou Chemical Industry, 2006, 31(2): 7-9.
[9] 袁铁锤, 周科朝, JIA Yong-feng, DEMOPOULOS G P. 结晶型砷酸镍的溶解性[J]. 化工学报, 2006(1): 122-125.
YUAN Tie-chui, ZHOU Ke-chao, JIA Yong-feng, DEMOPOULOS G P. Solubility of annabergite[J]. CIESC Journal, 2006(1): 122-125.
[10] 方兆珩, 石 伟, 韩宝玲, 夏光祥. 高砷溶液中和脱砷过程[J]. 化工冶金, 2000(4): 359-362.
FANG Zhao-heng, SHI Wei, HAN Bao-ling, XIA Guang-xiang. Removal of arsenic from high arsenic solutions by scorodite precipitation[J]. Engineering Chemistry and Metallurgy, 2000(4): 359-362.
[11] 陆晶晶. LED含砷废水处理工程高效运行技术研究[D]. 北京: 清华大学, 2012: 10-13.
LU Jing-jing. Study on the improvement of running performance for LED wastewater treatment process[D]. Beijing: Tsinghua University, 2012: 10-13.
[12] 刘建华, 王瑞祥. 离子交换法处理贫铜浸出液的研究[J]. 江西有色金属, 2002(3): 22-23, 42.
LIU Jian-hua, WANG Rui-xiang. Study on treatment of lean-copper leach with ion-exchange[J]. Jiangxi Nonferrous Metals, 2002(3): 22-23, 42.
[13] DJOKIC S S. Cementation of copper on aluminum in alkaline solutions[J]. Journal of the Electrochemical Society, 1996, 143(4): 1300-1305.
[14] MUBARAK A A, EL-SHAZLY A H, KONSOWA A H. Recovery of copper from industrial waste solution by cementation on reciprocating horizontal perforated zinc disc[J]. Desalination, 2004, 167: 127-133.
[15] STEFANOWICZ T, OSINSKA M, NAPIERALSKA- ZAGOZDA S. Copper recovery by the cementation method[J]. Hydrometallurgy, 1997, 47(1): 69-90.
[16] 刘志宏, 潘庆琳, 刘智勇, 李玉虎, 李启厚. As(Ⅲ)在酸性水溶液中与金属铁的反应行为[J]. 中国有色金属学报, 2015, 25(10): 2945-2952.
LIU Zhi-hong, PAN Qing-lin, LIU Zhi-yong, LI Yu-hu, LI Qi-hou. Reactive behaviors between As(Ⅲ) and metallic iron in acidic aqueous solution[J]. The Chinese Journal of Nonferrous Metals, 2015, 25(10): 2945-2952.
[17] GB 17055-1997. 车间空气中砷及其无机化合物卫生标 准[S].
GB 17055-1997. Hygienic standard for arsenic and its inorganic compounds in the air of workplace[S].
[18] 朱洪涛, 王 军. 铁屑在重金属废水处理中的应用[J]. 工业安全与环保, 2005(8): 6-8.
ZHU Hong-tao, WANG Jun. Application of iron chip in treatment of wastewater containing heavy metals[J]. Industrial Safety and Environmental Protection, 2005(8): 6-8.
[19] 谢学军, 吕 珂, 晏 敏, 潘 玲. 铜水体系电位-pH图与发电机内冷水pH调节防腐[J]. 腐蚀科学与防护技术, 2007, 19(3): 162-163.
XIE Xue-jun, Lü Ke, YAN Min, PAN Ling. Potential-pH chart for copper-water system and controlling pH of internal cooling water to prevent generator from corrosion[J]. Corrosion Science and Protection Technology, 2007, 19(3): 162-163.
[20] 吴 臣, 王建刚, 朱毅暋, 李东风. 经典铁置换铜反应的研究和工业应用[J]. 高等学校化学学报, 1996, 17(7): 1092-1095.
WU Chen, WANG Jian-gang, ZHU Yi-min, LI Dong-feng. A study and industry application of classical Fe-Cu replacement reaction[J]. Chemical Journal of Chinese Universities, 1996, 17(7): 1092-1095.
[21] 陈白珍, 唐仁衡, 龚竹青, 仇勇海. 砷酸铜制备工艺过程热力学分析[J]. 中国有色金属学报, 2001, 11(3): 510-513.
CHEN Bai-zhen, TANG Ren-heng, GONG Zhu-qing, QIU Yong-hai. Thermodynamic analysis of copper arsenate preparation process[J]. The Chinese Journal of Nonferrous Metals, 2001, 11(3): 510-513.
Reaction behavior of precipitation of Cu(Ⅱ) and As(Ⅲ) by metallic iron
ZHENG Yu, DENG Zhi-gan, FAN Guang, WEI Chang, FAN Gang, LI Xing-bin, LI Cun-xiong, LI Min-ting
(Faculty of Metallurgical and Energy Engineering, Kunming University of Science and Technology, Kunming 650093, China)
Abstract: Taking a reductive leaching solution as the research object, the reactive behaviors between Fe, Cu(Ⅱ) and As(Ⅲ) in the reductive leaching solution were investigated thermodynamically and experimentally. The thermodynamic calculation results show that the reactions between Fe, Cu(Ⅱ) and As(Ⅲ) in the reductive leaching solution, which produce both Cu2Oand Cu3As, respectively, are feasible thermodynamically. And the experimental results show that the optimal reaction condition as follows: iron powder coefficient of 1.2, reaction time of 25 min and reaction temperature of 70 ℃. Under the optimum conditions, the Cu and As precipitation rates reach more than 99%. The main compositions of the residue are Cu2O and Cu3As, and the precipitates deposit in punctate form, and do not closely coat the surface of iron powders, according to XRD and SEM-EDS analyses. Furthermore, increasing the coefficient of iron powders and temperature can improve the Cu2O and Cu3As deposition.
Key words: reductive leaching solutions; metallic iron; reactive behaviors; thermodynamically
Foundation item: Projects(51804146, 51564030, 51664030, 51664029) supported by the National Natural Science Foundation of China; Project(2014CB643404) supported by the National Basic Research Development Program of China; Project(2016FB097) supported by Yunnan Applied Basic Research, China
Received date: 2018-05-25; Accepted date: 2018-08-20
Corresponding author: WEI Chang; Tel: +86-13708791256; E-mail: weichang502@sina.cn
(编辑 何学锋)
基金项目:国家自然科学基金资助项目(51804146,51564030,51664030,51664029);国家重点基础研究发展计划资助项目(2014CB643404);云南省应用基础研究计划项目(2016FB097)
收稿日期:2018-05-25;修订日期:2018-08-20
通信作者:魏 昶,教授,博士;电话:13708791256;E-mail:weichang502@sina.cn