
Effect of Zn on mechanical property and corrosion property of extruded Mg-Zn-Mn alloy
YIN Dong-song(尹冬松)1, ZHANG Er-lin(张二林)2, ZENG Song-yan(曾松岩)1
1. School of Materials Science and Technology, Harbin Institute of Technology, Harbin 150001, China;
2. Institute of Metal Research, Chinese Academy of Sciences, Shenyang 110016, China
Received 31 October 2007; accepted 21 January 2008
Abstract: The effect of Zn on the microstructure, the mechanical property and the corrosion property in simulated body fluid(SBF) of an extruded Mg-Mn alloy was studied. The results indicate that the addition of Zn element can significantly refine the grain size of the extruded Mg-Mn alloy. When Zn content is increased from 0% to 3%, the grain size decreases from 12 μm to 4 μm. Meanwhile, the mechanical properties also increase remarkably with increasing Zn content. When Zn content is 3%, the ultimate tensile strength and the yield strength are increased by 54.7 MPa and 69.7 MPa, respectively. Zn can also improve the anti-corrosion property of the alloy. The best anti-corrosion property is obtained with 1% Zn. However, further increase of Zn content up to 3% deteriorates the corrosion property. Finally, the influence mechanism of Zn on the microstructure, the mechanical property and the corrosion property was discussed.
Key words: Mg-Zn-Mn alloy; hot extrusion; microstructure; mechanical property; corrosion; simulated body fluid
1 Introduction
Since the elastic modulus of magnesium alloys is close to that of human bones, magnesium alloys can effectively avoid the stress shield that exists in other metallic bone implantation. Moreover, Mg is a basic element in metabolism and bone tissue and has better biocompatibility. Much importantly, Mg and Mg alloys have a very low equilibrium electrode potential, therefore, they can be easily corroded or degraded in Cl- containing solution. Thus, the second surgical operation can be avoided in the case of bone implant made of magnesium alloy. So magnesium alloy shows a special application potential and attracts world-wide attention [1-4].
However, as a biomedical material, the fast corrosion rate of magnesium alloy results in high concentration of Mg ion and hydrogen gas release, and subcutaneous emphysema[3]. In addition, the yield strength of pure magnesium is only about 20 MPa, much lower than that of human long bone (106-133 MPa). So it is very necessary to take relevant measures to control the corrosion rate and improve the mechanical properties.
So far, two kinds of methods have been used to improve the corrosion resistance of magnesium alloys: surface treatment technology, such as chemical conversion film[5], micro-arc oxidation[6], organic coatings and plating[7-8] and alkali-heat-treatment[9], and element alloying and structure control, such as high purification treatment[10], heat-treatment and rapid solidification[11-12].
Element alloying can not only improve the corrosion resistance but also enhance the mechanical properties of magnesium alloy. It was reported that the addition of Mn could weaken the disadvantageous effects of the impurity Fe on the corrosion properties of magnesium alloys[13]. Aluminium contained magnesium alloy can form a dense passivation film that protects alloy from fast corrosion [14]. Y and Nd can purify the magnesium alloys and increase the stability of the protective surface film[15-16]. The addition of Zn element can effectively increase the strength and improve the plasticity[17]. Meanwhile, Zn can also weaken the disadvantageous effects of the impurity Fe[18]. Moreover, Zn is a necessary microelement and component of many proteins, nucleic acid synthetase of human body. Also Zn can accelerate the metabolism of cells[19]. In the previous study[20], Zn and Mn elements were selected to develop a biomedical magnesium alloy. The results have shown that Zn can remarkably improve the mechanical properties and corrosion resistance of the as-cast Mg-Mn alloy. However, the yield strength of the as-cast Mg-Zn-Mn magnesium alloy is still too low to be used as bone implant materials. In this work, hot extrusion was used to improve the mechanical properties of Mg-Zn- Mn. Primary research results were focused on the effect of Zn on the mechanical properties and the corrosion resistance of the extruded Mg-Zn-Mn alloy and the possible application of Mg alloy as bone implant.
2 Experimental
2.1 Material preparation
High purity Mg (99.99%), Zn (99.99%), Al (99.99%) (mass fraction) and analytic grade reagent MnCl2 were used to prepare Mg-Zn-Mn alloys. The melting was conducted in an electronic resistance furnace, protected by 99.5% CO2+0.5% SF6 (mole fraction) mixture gas. The melting temperature was 750 ℃. After proper treatment, magnesium melts were cast in a metal mould preheated to 200 ℃. Then, the ingot was extruded at 280 ℃ into a bar with 15 mm in diameter under an extrusion ratio of 10?1 and an extrusion rate of 22 mm/s. The chemical compositions of the alloys were analyzed by an IRIS Intrepid inductively coupled plasma atomic emission spectrometer, as listed in Table 1.
Table 1 Chemical compositions of Mg-Zn-Mn alloys (mass fraction, %)
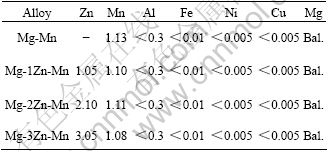
2.2 Immersion test
A simulated body fluid(SBF) was selected as the corrosion medium. The chemical composition (g/L) was: 6.0 NaCl, 0.4 KCl, 0.06 Na2HPO4, 0.06 KH2PO4, 0.35 NaHCO3, 0.2 MgSO4?7H2O and 0.14 CaCl2. Immersion samples with a dimension of 10 mm×10 mm×3 mm were cut from the extruded bar along the extrusion direction and the cross-section direction, named longitudinal sample and cross-section sample, respectively. Before immersion, the samples were ground by SiC paper up to 2000#, and then supersonically cleaned. Samples were immersed in the SBF solution (total surface area to solution volume ratio 1 cm2: 150 mL) at (37±1) ℃ for 216 h. The solution was refreshed every 24 h. Then the samples were supersonically washed in distilled water. The mass of sample was measured before and after the immersion by a balance with an accuracy of 0.1 mg. To calculate the mass loss, the immersed samples were cleaned using a boiling 20% chromic acid + 1%AgNO3 solution to remove the surface corrosion product, and then rinsed with ethanol, dried in air and finally weighted. Three parallel samples were used for each condition.
2.3 Electrochemical test
The samples for electrochemical test were cut from the extruded bar along the longitudinal direction and the cross-section direction, respectively. The samples were mounted by epoxy resins with an exposed area of 1 cm2. The surface was polished up to 1 μm after being ground by 200#-1000# SiC papers. The polarization test was carried out at (37±1) ℃ in a beaker containing 300 mL of the SBF using a standard three-electrode configuration with the saturated calomel as a reference, a platinum electrode as the counter and the sample as the working electrode. In the potentiodynamic polarization tests, the working electrode was first immersed in the solution for 20 min and then the polarization curve was measured at a scanning rate of 0.3 mV/s.
2.4 Microstructure observation and mechanical property test
The microstructure was observed by ZEISS- MC800X optical microscope(OM). The samples were etched by a 5% (mass fraction) trinitrophenol grain alcohol solution. Plate tensile samples with a dimension of 20 mm in gauge length, 6 mm in gauge width and 2 mm in gauge thickness were cut from the extruded bar. Tensile strength was tested on an INSTRON Series IX Auto Testing System. Three parallel samples were used for each condition.
3 Results
3.1 Microstructure
The microstructure of the extruded Mg-Zn-Mn alloy is shown in Fig.1. On the cross-section, the microstructure is mainly composed of equiaxed grains. On the longitudinal section, some elongated grains are also found besides the equiaxed grains.
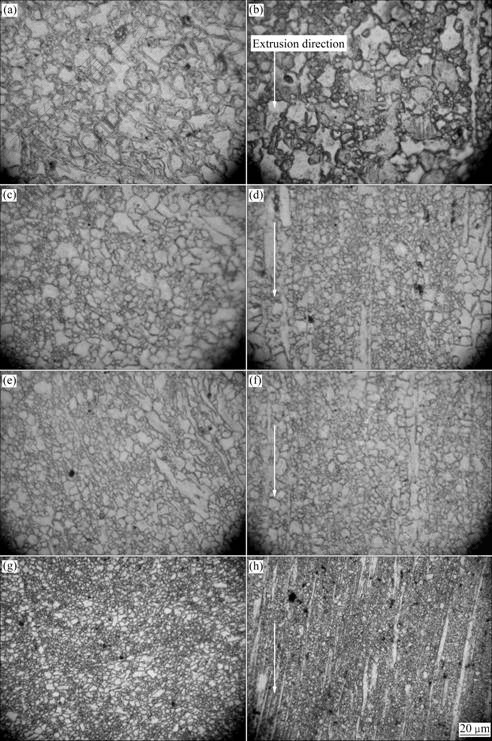
Fig.1 Microstructures of extruded Mg-Zn-Mn alloys: (a) Cross section of Mg-Mn alloy; (b) Longitudinal section of Mg-Mn alloy; (c) Cross section of Mg-1Zn-Mn alloy; (d) Longitudinal section of Mg-1Zn-Mn alloy; (e) Cross section of Mg-2Zn-Mn alloy; (f) Longitudinal section of Mg-2Zn-Mn alloy; (g) Cross section of Mg-3Zn-Mn alloy; (h) Longitudinal section of Mg-3Zn-Mn alloy
Fig.2 shows the relationship between the grain size and the content of Zn. It can be found that the average grain sizes of Mg-Mn alloy on the cross-section and the longitudinal section are 12.1 μm and 12.3 μm, respectively. With the increase of Zn content, the grain size decreases. At 3% Zn, the grain sizes on the cross section and the longitudinal section are 4.2 μm and 3.9 μm, respectively.
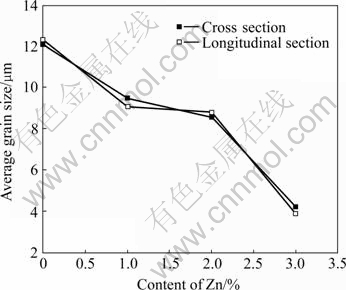
Fig.2 Relationship between average grain size of extruded Mg-Zn-Mn alloys and Zn content
3.2 Mechanical properties
Table 2 lists the mechanical properties of the extruded Mg-Mn and Mg-Zn-Mn alloys. With the increase of Zn content, both the tensile strength and the yield strength increase remarkably. At 3% Zn, the tensile strength is 315 MPa, which is increased by 54.7 MPa in comparison with that of Mg-Mn alloy, while the yield strength is 275 MPa, which is increased by 69.7 MPa. On the contrary, the elongation decreases obviously with increasing the addition of Zn. However, the elongation is still as high as 10% at 3% Zn.
Table 2 Mechanical properties of extrude Mg-Zn-Mn alloys
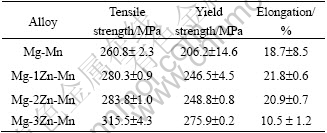
3.3 Corrosion properties
3.3.1 Mass loss rate
Fig.3 shows the change of the mass loss rate of Mg-Zn-Mn alloys with Zn content in Hank’s solution after 216 h immersion. A little difference in the mass loss rate was found between the cross-section sample and the longitudinal sample. The mass loss rate is influenced seriously by the addition of Zn, and it is in the following order from low to high: Mg-Zn-Mn, Mg-2Zn-Mn, Mg- Mn and Mg-3Zn-Mn. The lowest mass loss rate was obtained at 1%-2% Zn. Further increasing of Zn content increases the mass loss rate.
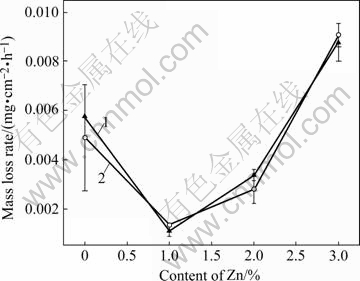
Fig.3 Mass loss rate of extruded Mg-Zn-Mn alloys: 1 Cross section sample; 2 Longitudinal sample alloys
3.3.2 Electrochemical test
Fig.4 shows the electrochemical polarization curves of the extruded magnesium alloys. Table 3 lists the characteristic parameters obtained from Fig.4. The addition of Zn into Mg-Mn alloys can obviously move the corrosion potential and the pitting potential to be nobler, indicating that the Zn element can improve the stability of the passivation film and the corrosion resistance. The best corrosion resistance is obtained at 1% Zn.
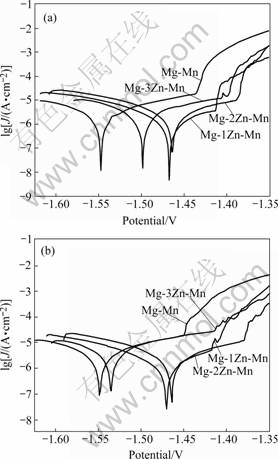
Fig.4 Electrochemical polarization curves of extruded Mg-Zn-Mn alloys: (a) Cross section sample; (b) Longitudinal sample
Table 3 Electrochemical parameters of extruded Mg-Zn-Mn alloys

4 Discussion
4.1 Microstructure
From the microstructures of the extruded Mg-Zn-Mn alloy in Fig.1, it can be clearly found that the grain size decreases remarkably with the increasing of Zn content. Therefore, Zn element can refine the microstructure of the extruded Mg-Mn alloy. The previous work[20] showed that Zn was mainly dissolved into primary magnesium in the as-cast Mg-Zn-Mn alloy when Zn content was 1%-2%, while a few Mg-Zn phases were observed. Since Zn element can hinder the movement of the recrystallized grain boundary[21], the grain can be refined. When Zn content increased to 3%, many Mg-Zn phases precipitated from the matrix and became very fine due to extrusion, such as nanometer size[20,22-23]. This fine second phase can pin the recrystallized grain boundary and restrict the grain growth[24], and in turn refine the grain. It is generally accepted that finer second phase has better refinement on the grain size than the solid solution element[25]. Therefore, the grain size decreases remarkably when Zn content increases to 3%.
4.2 Strengthening mechanism of Zn element
From Table 2, it can be found that the tensile strength and the yield strength increase with the increasing of Zn content. On one hand, the addition of Zn remarkably refines the grain size. According to the Hall-Path formula, the yield strength increases with the decreasing of grain size. On the other hand, Zn element mainly resolves in primary magnesium when Zn content is 1%-2%, which can improve the strength of the alloy by solid-solution strengthening. When Zn content is 3%, many Mg-Zn phases will precipitate from matrix, which enhances the strength by a dispersion strengthening mechanism[26-27]. Therefore, the strength of the alloy is further improved at the level of 1%-2% Zn, but the elongation is reduced. In addition, Mg-Zn phases will inhibit the dislocation recovery, and increase the density of dislocation and substructure, which contributes to the reduction of the elongation.
4.3 Effect of Zn content on corrosion property
From the electrochemical date in Table 3 and the mass loss curves in Fig.4, the addition of 1%-2% Zn significantly improves the anti-corrosion property of Mg-Mn alloy. But when Zn content exceeds 3%, the anti-corrosion property significantly decreases. The change of the pitting potential in Table 3 shows that adding Zn can move the pitting potential to a nobler value to some extent. It was reported that the addition of Zn in magnesium alloy could benefit the formation of a compact passive film[18]. Zn-rich film was observed on the surface of Zn contained magnesium alloy after being exposed to humid air[28]. It is reasonably concluded that the enrichment of Zn on the surface film can protect the alloy from further corrosion. By comparing Mg-2Zn-Mn alloy with Mg-1Zn-Mn alloy, the corrosion property is decreased. The probable reason might be that the volume fraction of Mg-Zn phase is higher in Mg-2Zn-Mn than that in Mg-1Zn-Mn alloy. When Zn content is up to 3%, many second phases precipitate from matrix, and act as cathode in the corrosion process, which accelerates the corrosion and reduces the anti-corrosion properties of magnesium. In addition, it has been widely accepted that Zn can reduce the effects of Fe, Ni on corrosion properties and then improve the anticorrosion properties of Mg[29].
5 Conclusions
1) The addition of Zn element can refine the grain size of the extruded Mg-Zn-Mn alloy.
2) The mechanical property of the extruded Mg- Zn-Mn alloy can be improved by Zn element. The tensile strength and the yield strength are increased by 54.7 MPa and 69.7 MPa, respectively, when 3% Zn is added.
3) Anti-corrosion property of the extruded Mg- Zn-Mn alloy can be effectively improved by Zn element when the content is less than 3%.
References
[1] WITTE F, KAESE V, HAFERKAMP H, SWITZER E, MEYER-LINDENBER G A, WIRTH C J, WINDHAGEN H. In vivo corrosion of four magnesium alloys and the associated bone response [J]. Biomaterials, 2005, 26(17): 3557-3563.
[2] WITTE F, FISCHER J, NELLESEN J, CROSTACK H A, KAESE V, PISCH A, BECKMANN F, WINDHAGEN H. In vitro and in vivo corrosion measurements of magnesium alloys [J]. Biomaterials, 2006, 27(7): 1013-1018.
[3] STAIGER M P, PIETAK A M, HUADMAI J, DIAS G. Magnesium and its alloys as orthopedic biomaterials: A review [J]. Biomaterials, 2006, 27(9): 1728-1734.
[4] GAO Jia-cheng, LI Long-chuan, WANG Yong, QIAO Li-ying. Biocompatibility of magnesium after surface modification by heat- organic films-treatment [J]. Rare Metal Materials and Engineering, 2005, 34(6): 904-905. (in Chinese)
[5] JIN Hua-lan, YANG Xiang-jie, WEI Ren-jie, CHEN Xiang. Effect of chemical conversion film on corrosion resistance of magnesium alloy [J]. The Chinese Journal of Nonferrous Metals, 2007, 17(6): 964- 968. (in Chinese)
[6] WANG Y, WANG J, ZHANG J, ZHANG Z. Characteristics of anodic coatings oxidized to different voltage on AZ91D Mg alloy by micro-arc oxidation technique [J]. Materials and Corrosion, 2005, 56(2): 88-89.
[7] MORI K, HIRAHARA H, OISHI Y, KUMAGAI N. Effect of triazine dithiols on the polymer plating of magnesium alloys [J]. Polymer Journal, 2003, 35(7): 568-572.
[8] ZHANG E L, XU L P, YANG K. Formation by ion plating of Ti-coating on pure Mg for biomedical applications [J]. Scripta Materialia, 2005, 53(5): 523-527.
[9] GAO Jia-cheng, LI Long-chuan, WANG Yong. Surface modification on magnesium by alkali-heat-treatment and its corrosion behaviors in SBF [J]. The Chinese Journal of Nonferrous Metals, 2004, 14(9): 1509-1510. (in Chinese)
[10] WANG Yi-zhi. Influence of impurities on the anticorrosion of high purity magnesium alloys [J]. Foundry, 2001(2): 61-65. (in Chinese)
[11] CHANG J W, FU P H, GUO X W, PENG L M, DING W J. The effects of heat treatment and zirconium on the corrosion behaviour of Mg-3Nd-0.2Zn-0.4Zr (mass fraction, %) alloy [J]. Corrosion Science, 2007, 49(6): 2612-2627.
[12] YAMASAKI M, HAYASHI N, IZUMI S, KAWAMURA Y. Corrosion behavior of rapidly solidified Mg-Zn-rare earth element alloys in NaCl solution [J]. Corrosion Science, 2007, 49(1): 255- 262.
[13] ZHOU Xu-hua, NIU Jie-xin, WEI Zhong-lin, CHENG Qiu-rong. Effect of elemental RE and Mn on corrosion resistance of Mg-9AI alloy [J]. Light Alloy Fabrication, 2006, 34(10): 49-51. (in Chinese)
[14] BALLERINI G, BARDI U, BIGNUCOLO R, CERAOLO G. About some corrosion mechanisms of AZ91D magnesium alloy [J]. Corrosion Science, 2005, 47(9): 2173-2184.
[15] BEN-HAMU G, ELIEZER D, SHIN K S, COHEN S. The relation between microstructure and corrosion behavior of Mg-Y-RE-Zr alloys [J]. Journal of Alloys and Compounds, 2007, 431(1): 269-276.
[16] HUANG Liang, HUANG Yuan-wei, WANG Chen, WEI Zhong-ling. Study on corrosion product film of magnesium-aluminum alloy containing rare-earth element in NaCl solution [J]. Journal of Chinese Society for Corrosion and Protection, 2002, 22(3): 168-171.
[17] CHENG Zhen-hua. Magnesium alloys [M]. Beijing: Chemical Industry Press, 2004: 312-313. (in Chinese)
[18] ZHANG Zhong-lin, LIU Zhao-jing, LI Feng-zhen. Study on burning point & the corrosion resistance & the mechanical property of magnesium alloy [J]. Light Alloy Fabrication, 2003, 31(7): 31-33. (in Chinese)
[19] XIE Miao, WANG Bin, DENG Hai-yan, GAN Chun-ji. Preparation and nutrition assessment on dietary fiber of kelp [J]. Journal of Henan University of Science and Technology (Agricultural Science), 2004, 24(4): 56-57. (in Chinese).
[20] YIN Dong-song, ZHANG Er-lin, ZENG Song-yan. Effect of Zn on mechanical properties and corrosion properties of cast Mg-Mn alloy [J]. The Chinese Journal of Nonferrous Metals, 2008, 18(3): 388-390. (in Chinese).
[21] L? Yan. Controlling of microstructure and properties of forged pieces [M]. Beijing: National Defence Industry Press, 1983: 177- 179. (in Chinese)
[22] SOMEKAWA H, OSAWA Y, MUKAI T. Effect of solid-solution strengthening on fracture toughness in extruded Mg-Zn alloys [J]. Scripta Materialia, 2006, 55(7): 593-596.
[23] MAENG D Y, KIM T S, LEE J H, HONG S J, SEO S K, CHUN B S. Microstructure and strength of rapidly solidified and extruded Mg-Zn alloys [J]. Scripta Materialia, 2000, 43(5): 385-389.
[24] WU An-ru, XIA Chang-qing. Effects of addition of cerium on microstructure and mechanical properties of ZK60 alloy [J]. Transactions of Materials and Heat Treatment, 2006, 27(1): 46-47. (in Chinese)
[25] CHEN Zhen-hua. Metamorphosed magnesium alloys [M]. Beijing: Chemical Industry Press, 2005: 166-168. (in Chinese)
[26] BOEHLERT C J, KNITTEL K, VENKATESAN K. The micro- structure, tensile properties and creep behavior of Mg-Zn alloys containing 0-4.4% Zn [J]. Materials Science and Engineering A, 2006, 417(1): 315-321.
[27] DSA A, LIU G, FAN Z. Investigation on the microstructural refinement of an Mg-6%Zn alloy [J]. Materials Science and Engineering A, 2006, 419(1): 349-356.
[28] FAN Yu, WU Guo-hua, GAO Hong-tao, ZHAI Chun-quan. Current state and development of research on the corrosion of magnesium alloys [J]. Foundry Technology, 2004, 25(12): 941-942. (in Chinese)
[29] LI Guan-qun, WU Guo-hua, FAN Yu, DING Wen-jiang. Effect of the main alloying elements on microstructure and corrosion resistance of magnesium alloys [J]. Foundry Technology, 2006, 27(1): 81-82. (in Chinese)
Foundation item: Project supported by Hundreds Talent Program of Chinese Academy of Sciences and Shenyang Sciences and Technology Program
Corresponding author: ZHANG Er-lin; Tel/Fax: +86-24-23971605; E-mail: erlin.zhang@imr.ac.cn
(Edited by LI Xiang-qun)