
Deformation and microstructure characterization during semi-solid extrusion of Al-4Cu-Mg alloy
LU Ya-lin(卢雅琳)1, 2, LI Miao-quan(李淼泉)1, LI Xing-cheng(李兴成)1
1. School of Materials Science and Engineering, Northwestern Polytechnical University,
Xi’an 710072, China;
2. School of Mechanical and Automobile Engineering, Jiangsu Teachers University of Technology,
Changzhou 213000, China
Received 28 July 2006; accepted 15 September 2006
Abstract: Effects of the process parameters, including deformation temperature, punch velocity and extrusion ratio, on the deformation and microstructure characterization during the semi-solid extrusion of Al-4Cu-Mg alloy, were investigated. The experimental results show that the load decreases with an increase of deformation temperature and/or a decrease of punch velocity. When the displacement is more than 4 mm, the load decreases significantly with an increase of the deformation temperature, which is related to the high liquid fraction. The microstructure varies with the process parameters and deformation regions. It can be found that the dynamic recovery occurs during the semi-solid extrusion of Al-4Cu-Mg alloy at lower deformation temperature. Subsequently, the microstructure elongated gradually polygonizes with an increase of deformation temperature. So, the higher deformation temperature should be chosen during the semi-solid extrusion of Al-4Cu-Mg alloy because the grains polygonized and high liquid fractions are beneficial to deformation.
Key words: Al-4Cu-Mg alloy; semi-solid extrusion; deformation characterization; microstructure
1 Introduction
Semi-solid processing is a novel technology offering several potential advantages over casting and forging, such as reduction of macrosegregations, reduction of porosity and low forming efforts. Furthermore, the coexistence of the liquid and solid phases is helpful to enhance the formability and decrease the loads[1-2].
The deformation characterization of semi-solid materials can be considered in terms of their deformation response and microstructural evolution[3-8]. KANG et al[3] analyzed the effect of deformation parameters on compression behavior and microstructure of semi-solid A356 alloy and concluded that more homogeneous structure and macroseparation can be observed with greater compression velocity. CHINO et al[4] studied the deformation behavior of AZ91 magnesium alloy containing a small volume of liquid. It was suggested that the liquid serves to relax the stress concentrations
and resulting in acceleration in flow of the solid. Also, grain refinement due to dynamic recrystallization was attained.
In this paper, deformation and microstructure characterization during the semi-solid extrusion of Al-4Cu-Mg alloy have been investigated. The main aim of this research was to determine effect of the process parameters on the deformation and microstructure of Al-4Cu-Mg alloy in the semi-solid state and optimize further deformation process parameters.
2 Experimental
The experimental alloy was Al-4Cu-Mg alloy with equiaxed grains fabricated by a strain induced melt activation process (SIMA)[9-10]. The chemical composition of as-received alloy is shown in Table 1. The semi-solid temperature range of this alloy was 514-648 ℃ measured by differential scanning calorimeter analysis(DSC).
Table 1 Chemical composition of Al-4Cu-Mg alloy (mass fraction, %)

The samples of semi-solid Al-4Cu-Mg alloy machined 20 mm in diameter and 15 mm in height were extruded at an INSTRON 1196 material testing machine as shown in Fig.1. The half samples and die were machined in order to extract easily the samples from the die. The samples were heated to the required semi-solid temperature by an electrical resistance furnace. Chromel-alumel thermo-couples, which were welded at the middle of the samples, were used to measure and monitor the specimen temperature during the extrusion. The samples were held for 10 min to equilibrate the temperature field of the whole specimen and melt adequately the low melting point phase at the given deformation temperature prior to deformation. Subsequently, the samples were immediately immersed in water at room temperature after extrusion to retain the as-deformed microstructures. In order to reduce frication and remove conveniently the samples from mold, graphite lubricant was used during the extrusion.
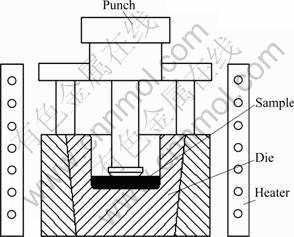
Fig.1 Experimental apparatus of extrusion
To investigate effect of the process parameters on deformation and microstructure characterization, the samples were extruded at the deformation temperatures of 560, 580 and 600 ℃, punch velocities of 5 mm/s and 0.5 mm/min, the extrusion ratios of 3.6 and 1.73, respectively. Microstructure after extrusion was observed using optical microscopy at OLYMPUS PMG3 and linked with metallographic analysis software of SISC IAS V8.0.
3 Results and discussion
3.1 Microstructure during semi-solid extrusion of Al- 4Cu-Mg alloy
Fig.2 shows the extruded samples of semi-solid Al-4Cu-Mg alloy at different extrusion ratios. It can be observed that the crack phenomenon did not occur in the samples during extrusion in the semi-solid state. This attributes to existence of three-dimension compression stress during extrusion of the Al-4Cu-Mg alloy, which the separation between liquid and solid phase did not happen easily.
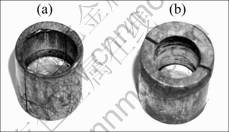
Fig.2 Samples of semi-solid Al-4Cu-Mg alloy after extrusion: (a) Extrusion ratio of 3.60; (b) Extrusion ratio of 1.73
During the semi-solid extrusion, the microstructure varies with the different process parameters and deformation regions. In order to study the effect of different deformation regions of the extruded samples on microstructure characterization, points 1, 2 and 3 are chosen as shown in Fig.3.
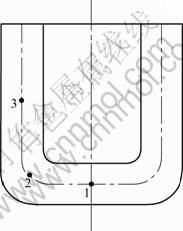
Fig.3 Observed location of microstructure in extruded samples
Fig.4 shows the microstructures of semi-solid Al- 4Cu-Mg alloy during extrusion at different deformation regions and deformation temperature of 580 and 600 ℃. The significant effect of the deformation temperature and deformation regions on the microstructure can be seen in Fig.4. From Figs.4(a), (b) and (c), the dynamic recovery occurs during the semi-solid extrusion of Al-4Cu-Mg alloy at deformation temperature of 580 ℃ and grains are elongated normal to the loading direction as expected. With the increase of deformation temperature, the elongated grains transform to a polygonization at deformation temperature of 600 ℃. The dynamic recovery occurs easily during extrusion of Al-4Cu-Mg alloy because of higher stacking fault energy. When there is a higher deformation temperature, the dislocation is activated adequately. The edge dislocation is arranged to the sub-boundary with small angle normal to the slip direction as expected, in which the grain polygonization occurs. The driving force for the grains polygonization comes from the decrease of self-strain energy during extrusion.
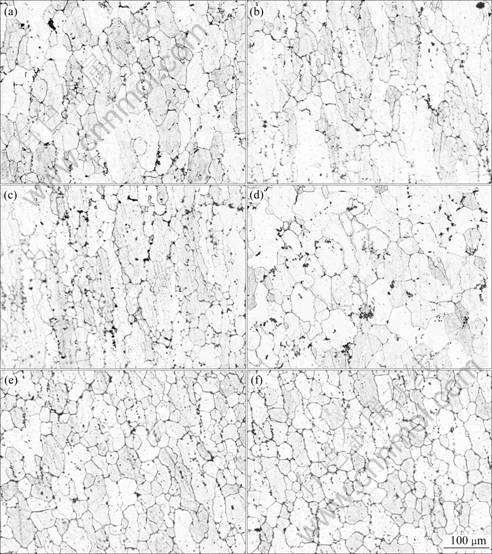
Fig.4 Optical micrographs during semi-solid extrusion of Al-4Cu-Mg alloy: (a) Point 1, 580 ℃, 5 mm/min; (b) Point 2, 580 ℃, 5 mm/min; (c) Point 3, 580 ℃, 5 mm/min; (d) Point 1, 600 ℃, 5 mm/min; (e) Point 2, 600 ℃, 5 mm/min; (f) Point 3, 600 ℃, 5 mm/min
From Fig.4, the effect of deformation region on the microstructures during extrusion is also obvious at both the dynamic recovery and the polygonization stage, which is related to different strain at three deformation regions.
On basis of the experimental results, the higher deformation temperature should be chosen during the semi-solid extrusion of Al-4Cu-Mg alloy because the polygonized grains and high liquid fraction are beneficial to deformation.
3.2 Extrusion of semi-solid Al-4Cu-Mg alloy
Typically load-displacement curves of semi-solid Al-4Cu-Mg alloy at different process parameters are shown in Fig.5. From Fig.5(a), it can be found that the effect of deformation temperature on the load is inappreciable at the early stage of extrusion because of the liquid flow. Because of three-dimension compression stress during extrusion, the liquid phase distributed on the grain boundaries is difficult to be extruded out the deformation regions. So, the load increases rapidly with the increase of displacement. It is considered that the load is affected by softening effect from the dynamic recovery during the semi-solid extrusion, which leads to the steady load occurring. The higher the deformation temperature, the stronger the softening effect from the dynamic recovery, and the lower the load.
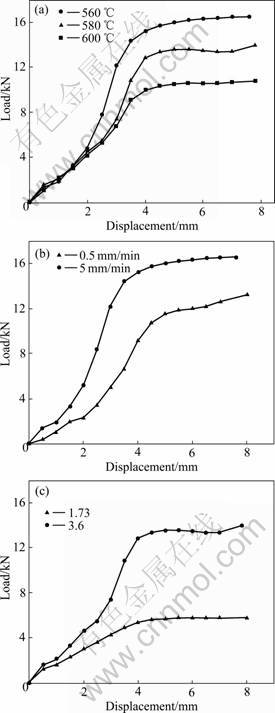
Fig.5 Load—displacement curves during semi-solid extrusion of Al-4Cu-Mg alloy: (a) Extrusion ratio 3.60, punch velocity 5 mm/min; (b) Extrusion ratio 3.60, deformation temperature 560 ℃; (c) Deformation temperature 580 ℃, punch velocity 5 mm/min
From Fig.5(b), the load decreases with the decrease of punch velocity during the semi-solid extrusion. There is more time for the liquid phase to distribute on the grain boundaries at a lower punch velocity, which results in the easy movement of the solid phase. On the other hand, the deformation resistance is low at lower punch velocity and the load is low accordingly.
Fig.5(c) shows the variation of the load as a function of extrusion ratio. The experimental results show that the load increases significantly with the increase of extrusion ratio. It is known that the load must overcome deformation resistance to ensure move and/or plastic deformation of the solid phase particles during extrusion. Hence, the larger the extrusion ratio is, the greater the load is.
4 Conclusions
1) The microstructure during the semi-solid extrusion of Al-4Cu-Mg alloy varies with the process parameters and deformation regions.
2) High deformation temperature should be chosen during the semi-solid extrusion of Al-4Cu-Mg alloy because the polygonized grains and high liquid fraction are beneficial to deformation.
3) The load decreases markedly with the increase of deformation temperature and the decrease of punch velocity.
4) The load is affected by the softening effect from the dynamic recovery. The higher deformation temperature is, the smaller the load is.
References
[1] FLEMINGS M C. Behavior of metal in the semi-solid state [J]. Metall Trans, 1991, 22A: 957-981.
[2] KAPRANOS P, WARD P J, ATKINSON H V, KIRKWOOD D H. Near net shaping by semi-solid metal processing [J]. Mater Design, 2000, 21: 387-394.
[3] KANG C G, CHOI J S, KIM K H. The effect of strain rate on macroscopic behavior in the compression forming of semi-solid aluminum alloy [J]. J Mater Process Technol, 1999, 88: 159-168.
[4] CHINO Y, KOBATA M, IWASAKI H, MABUCHI M. An investigation of compressive behaviour for AZ91 Mg alloy contain a small volume of liquid [J]. Acta Mater, 2003, 51: 3309-3318.
[5] HAAFTEN W M, KOOL W H, KATERMAN L. Tensile behavior of semisolid industrial aluminum alloys AA3104 and AA5182 [J]. Mater Sci Eng A, 2002, A336: 1-6.
[6] KOPP R, CHOI J, NEUDENBERGER D. Simple compression test and simuEAtion of an Sn-15%Pb alloy in the semi-solid state [J]. J Mater Process Technol, 2002, 6376: 1-7.
[7] TZIMAS E, ZAVALIANGOS A. Evaluation of volume fraction of solid in alloys formed by semisolid processing [J]. J Mater Sci, 2000, 35: 5319-5329.
[8] LIU D, ATKINSON H V, KAPRANOS P, JIRATTITICHAROEAN W, JONES H. Microstructural evolution and tensile mechanical properties of thixoformed high performance aluminium alloys [J]. Mater Sci Eng A, 2003, A361: 213-224.
[9] JIANG Hai-tao, LI Xiao-li, XIONG Ai-min, LI Miao-quan. Fabrication and microstructure evolution of semi-solid LY11 alloy by SIMA [J]. J Mater Eng Perform, 2003, 12: 249-253.
[10] JIANG Hai-tao, LU Ya-lin., HUANG Wei-chao, LI Miao-quan. Microstructural evolution and mechanical properties of the semisolid Al-4Cu-Mg alloy [J]. Mater Character, 2003, 51: 1-10.
(Edited by HE Xue-feng)
Foundation item: Project(BK2005025) supported by the Fundamental Research Project of Jiangsu Province, China
Corresponding author: LU Ya-lin; Tel: +86-29-88460465; E-mail: luyalin@163.com