
Effect of Ni content on corrosion behavior of
Ni/(10NiO-90NiFe2O4) cermet inert anode
TIAN Zhong-liang(田忠良), LAI Yan-qing(赖延清), LI Jie(李 劼), LIU Ye-xiang(刘业翔)
School of Metallurgical Science and Engineering, Central South University, Changsha 410083, China
Received 28 May 2007; accepted 27 August 2007
Abstract: Ni/(10NiO-90NiFe2O4) cermet inert anodes with metal Ni content of 0, 5, 10, 15 and 20 (mass fraction, %) were prepared and their corrosion behavior in Na3AlF6-Al2O3 melts was investigated in laboratory electrolysis tests. The results indicate that the content of metal Ni in anodes has little effect on the steady-state concentration of impurities Ni and Fe in electrolyte and the values range in (114-173)×10-6 and (287-385)×10-6, but the content of impurities in the metal aluminum manifolds. There is preferential corrosion for metal Ni in NiO-NiFe2O4 based cermet anodes. Considering the corrosion resistance and electrical conductivity, the cermet containing 5%Ni (mass fraction) behaves best among NiO-NiFe2O4 based cermet anodes studied, and should be further studied.
Key words: aluminum electrolysis; inert anode; NiFe2O4 based cermet; corrosion resistance
1 Introduction
It is well known that the Hall-Héroult process, developed in 1886, is the only commercial method for production of aluminum and it has many disadvantages including energy consumption, carbon wasting and environmental pollution. The implementation of new technology based on the inert electrodes could result in significant energy and environmental benefits, and it has become a research focus[1-2]. Despite intensive research efforts, no fully satisfactory inert anode material has been found. Compared with metals and oxides, NiFe2O4 based cermet, which seems promising to have the desirable properties of metallic materials as well as those of ceramics, is one of the most promising materials as inert anode for aluminum electrolysis[3-4].
In our previous work, the effect of content of NiO on the corrosion resistance of NiFe2O4 based cermet has been studied, and the content of NiO in ceramic phase was determined 10% (mass fraction, the same below)[5]. However, its corrosion resistance to Na3AlF6-Al2O3 melts is affected not only by the ceramic phase but also by the metallic phase. Though the results[6-8] showed that Ni was an unacceptable metal phase in cermet inert anode because of its tendency to anodically dissolve, OLSEN and THONSTAD[9] asserted that the mass transfer coefficient of Ni from electrolyte to molten aluminum was 1/2 that of Cu, and the preferential corrosion of metal Ni didn’t occur. In addition, according to our previous research [10], the wettability between Cu and NiFe2O4 is worse than that between Ni and NiFe2O4, which shows better sintering performance. So it is necessary to conduct a systematic study on the effect of Ni content on the corrosion behavior of Ni/(10NiO-90NiFe2O4) cermets in aluminum electrolysis.
In this work, 10NiO-NiFe2O4 based cermet inert anodes with Ni content of 0, 5, 10, 15 and 20 (mass fraction, %) were prepared by cold pressing-sintering based on our previous works, and their corrosion resistance to cryolite-alumina melts was tested under conventional electrolysis condition. The purpose of this work is to determine which kind of metal content should be selected to improve the corrosion resistance of 10NiO- NiFe2O4 based cermet inert anodes.
2 Experimental
2.1 Preparation of ceramic and cermets
The raw materials, metal Ni powder, NiO and Fe2O3 were all of reagent grade. 10Ni-NiFe2O4 based cermet samples were prepared by conventional cold isostatic pressing-sintering process[11]. Proper amounts of NiO and Fe2O3 were mixed using a ball mill and then calcined to obtain 10NiO-NiFe2O4 ceramic powder. The calcined ceramic powder was mixed again with different contents (0, 5%, 10%, 15%, 20%) of Ni powder by ball milling in the media containing dispersant and adhesive that were organic to avoid the metal oxidation. Finally, the mixed ceramic-metal powder was dried and isostatic pressed into cylindrical blocks (d20 mm×40 mm) at the pressure of 2×108 Pa, and sintered at 1 350 ℃ for 2 h in atmosphere of efficaciously controlled oxygen partial pressure to get the desired cermet samples. The composition and correlative properties of these cermet inert anodes prepared are listed in Table 1.
Table 1 Composition and correlative properties of inert anode samples
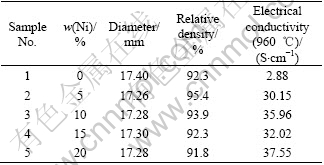
2.2 Cell design
A sketch of the experimental cell is presented in Fig.1. A hole was drilled at the bottom of graphite crucible and 90 g metal aluminum was added. Thus, a steady cathode surface could be obtained during electro- lysis. Alumina sleeve was set in the graphite crucible and about 800 g electrolyte was contained. Under the operating conditions of the laboratory test, the cell would not be thermally self-sustained. It was necessary to provide extra heat by placing the cell with the anode in a vertical laboratory furnace and the furnace was heated to the desired temperature. The temperature was measured with Pt/Pt-10%Rh thermocouple and controlled to ±1℃ by TCE-II programmable temperature control unit.
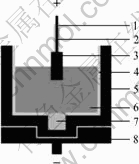
Fig.1 Schematic diagram of experimental cell: 1 Al2O3 sleeve; 2 Stainless steel anode rod; 3 Cermet inert anode; 4 Al2O3 liner; 5 Graphite crucible; 6 Electrolyte; 7 Metal aluminum; 8 Graphite mechanical support
2.3 Electrolysis test
The electrolyte was made up of reagent grade Na3AlF6, Al2O3 and CaF2, technical grade AlF3, with CR (molar ratio of NaF to AlF3) 2.3, 5.0%CaF2 and 4% Al2O3. All compositions were dried at 120 ℃ for 48 h to remove the water before being used. Metal aluminum was added prior to electrolysis. The temperature was monitored at 970 ℃, i.e. with superheat of 10 ℃. The anode-bath contacting area was controlled by immersing the anode depth, which was 1 cm. The current density of anode bottom was 1 A/cm2. The current and the cell voltage were supplied and monitored by a Multi-Purpose Potentiostat/Galvanostat (model 273A/10, Perkin-Elmer Instruments). According to the calculation, the concentration of Al2O3 in the bath decreases by 1.5% during lasting 8 h electrolysis if the current efficiency is 85%[12] and Al2O3 is not added. Moreover, alumina sleeve also contributes to keep the concentration of Al2O3. So, Al2O3 was not added during testing.
After electrolysis, the anode was raised out of the melt while maintaining polarization so as to prevent reduction of the anode material by dissolved metal aluminum. The cell was left to cool with the anode resting above the electrolyte. The anodes tested were sectioned, mounted, polished, and analyzed by XRMA (JSM-5600LV). Some samples of bath and the aluminum samples in the bottom hole were analyzed by X-ray fluorescence spectrum (analytic error below 5%) for getting the concentration of Ni and Fe in bath and cathode aluminum.
3 Results and discussion
3.1 Varieties of impurities concentration in bath during electrolysis
DEYOUNG[13] pointed out it took approximately 8 h for stoichiometric NiFe2O4 in cryolite melts to reach steady-state concentration, which was taken to be solubility. LAI et al[14] pointed that this process would last 4-6 h. Therefore in present work, all electrolysis experiments lasted 8 h. The varieties of the concen- trations of impurities, which were corroded from Ni/(10NiO-90NiFe2O4) cermet inert anode components into the melts, are listed in Table 2 and Table 3.
Table 2 Concentrations of impurity Fe in bath during electrolysis for different cermet anodes
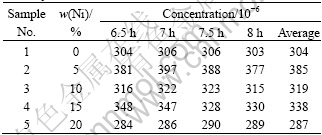
Table 3 Concentrations of impurity Ni in bath during electrolysis for different cermet anodes
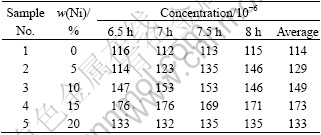
From Table 2, for the cermet inert anodes investigated, the contents of metal Ni are 0%, 5%, 10%, 15% and 20%, and the steady-state concentrations of impurity Fe in the bath are about 304×10-6, 385×10-6, 319×10-6, 338×10-6 and 287×10-6 respectively, which are far below the solubility (580×10-6) mentioned by DEYOUNG (bath ratio 1.1, with 6.5% Al2O3, 1 000 ℃)[13].
The data listed in Table 3 show that, for the cermet inert anodes investigated, the steady-state concentration of impurity Ni in the bath ranges between 114×10-6 and 173×10-6. And the content of metal Ni in cermet makes little effect on the steady-state concentration of impurity Ni in the bath during the electrolysis of 10NiO-NiFe2O4 based cermets. That is to say, with the content of metal Ni in 10NiO-NiFe2O4 based cermet increasing, there is little effect on the steady-state concentration of impurities Ni and Fe in the bath. It should be noted that the concentrations of impurities Ni and Fe decrease when the content of metal Ni is 20%. The reason may be that the corrosion control process is changed. Of course, the exact reason requires to study further.
3.2 Effect of metal Ni content on content of impurities in metal aluminum
The content of anode constituents Fe and Ni in the metal aluminum recovered at cathode after testing is listed in Table 4. It is very obvious that the content of impurities in metal content aluminum increases when the metal Ni is added. In the content range of 0-20% of metal Ni, the contents of impurity Fe and Ni vary in (2 300-4 088)×10-6, (198-1 519)×10-6, respectively. It should be noted that the content of impurity in metal aluminum is the highest when the content of metal Ni is 15%, and the total content of impurities is 5 556×10-6, which corresponds with the concentration of impurities in the bath. The reason is not clear and should be studied further.
Table 4 Content of impurities in metal aluminum after testing
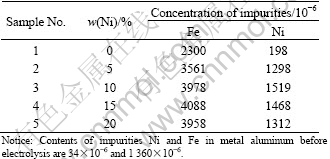
In addition, the mass ratio of impurities Fe to Ni in metal aluminum neither ranges from 3 to 8, as DEYOUNG mentioned[13], nor are about 1.4 as that in cermets, but 2.6-11.6. The following reasons may explain the phenomenon. Firstly, the addition of Ni and NiO restrains the dissolution of Fe from anodes, and decreases the mass ratio. Secondly, the polarized corrosion mechanism of ceramic phase in the cermets, affected by chemical dissolution, electrochemical corrosion and so on, is probably different from the static corrosion mechanism (unpolarized corrosion mechanism), which is only controlled by chemical dissolution. Thirdly, the transferring velocity for different impurities from electrolyte to molten aluminum is different, and the velocity of impurity Fe is about twice that of impurity Ni[8].
3.3 Microstructure of cermet inert anodes after electrolysis
To obtain more information about the corrosion process, the cermet inert anodes 1, 2, 3 and 5 are sectioned, mounted and polished after electrolysis experiments. The back-scattered images of the cermet inert anodes are shown in Fig.2.
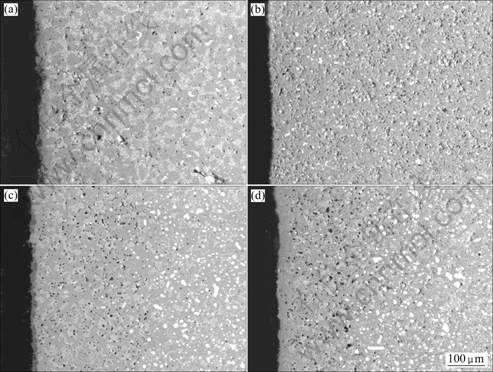
Fig.2 SEM backscattered images of cermet inert anodes at anode bottom after electrolysis: (a) Sample 1; (b) Sample 2; (c) Sample 3; (d) Sample 5
From Figs.2(a) and (b), the corrosion of inert anodes is not obvious. However, comparing Figs.2(c) and (d) with (b), though the metallic phase Ni and other phases are distributed evenly in the uncorroded area, it can be found obviously that the metal phase Ni is leached preferentially, and there is a lot of holes and pores left. The distribution of metallic phase near the surface is complex and it may be regarded as three layers that are preferential corrosion layer, transition-layer and the body respectively. This may imply that the corrosion resistance will weaken with the content of metal increasing, and the cermet inert anodes containing low content metal should be selected. In addition, there are some metal grains in the sample 1, which were introduced during preparation process.
Generally speaking, the cermet inert anodes investigated may deteriorate in operating Hall cells by a number of possible mechanisms such as chemical dissolution, electrochemical corrosion, reduction by dissolved metal aluminum, electrolyte penetration, and grain boundary attack. Normally, a thin oxide coating would be always present on the anode surface. However, under electrolysis condition, it should be further noted that the Ni metal present in the anode may fluorinate:
3Ni(s)+2AlF3(s)=3NiF2(s)+2Al(l) (1)
As for influence of alumina concentration and electrolysis temperature, the decomposition voltage of reaction (1) at 965 ℃ is 1.912 V, which is lower than 2.240 V for oxygen production under same condition. Thus, the metallic phase Ni is corroded preferentially and pores are left.
About the electrolyte penetration, it may result from two reasons. The first one is due to pores left by the electrochemical dissolution of metallic phase when anode is polarized, or the metallic phase oxidation and the following preferential chemical dissolution, and bath penetrates into these pores by capillary effect. The second one is the selective dissolution of Fe, since in the ceramic phase of the NiFe2O4-based cermet inert anode, impurity Fe has a fairly high solubility in cryolite molten compared with Ni. To restrain or eliminate effectively the above-mentioned factors, which are adverse to resistance corrosion of inert anode, it is necessary to improve the relative density and decrease the content of metallic phase.
4 Conclusions
1) With the content of metal Ni in cermet inert anodes increasing from 0% to 20%, there is little effect on the steady-state concentration of impurities Ni and Fe in the bath, and the values are (114-173)×10-6 and (287-385)×10-6. But the contents of impurities Ni and Fe in the metal aluminum manifold and range in (198- 1 519)×10-6 and (2 300-4 088)×10-6, respectively.
2) The microstructure of inert anodes after electrolysis shows that the metallic phase Ni in cermet inert anodes is found to be corroded preferentially and produces many holes and pores, and the distribution of metallic phase near surface can be regarded as preferential corrosion layer, transition-layer and the body.
3) From the post-examination with SEM study of cermet inert anodes and the content of impurity in metal aluminum recovered at cathode, the low content of metal Ni cermet inert anode should be selected to improve its corrosion resistance. Considering the corrosion resistance and electrical conductivity, the cermet containing 5% metal Ni behaves best among NiO- NiFe2O4 based cermet anodes studied, and should be studied further.
references
[1] KENIRY J. The economics of inert anodes and wettable cathodes for aluminum reduction cells [J]. JOM, 2001, 53(5): 43-47.
[2] NANCY M, JACK E. Inert anode roadmap—A framework for technology development [R]. Washington: The Aluminum Association in Conjunction with the U.S. Department of Energy, 1998.
[3] OLSEN E, THONSTAD J. Nickel ferrite as inert anodes in aluminum electrolysis (part I): Material fabrication and preliminary testing [J]. Journal of Applied Electrochemistry, 1999, 29: 293-299.
[4] PAWLEK R P. Inert anodes: An update [C]// TABEREAUX A T. Light Metals 2004. Warreudale PA: TMS, 2004: 283-287.
[5] LAI Yan-qing, DUAN Hua-nan, LI Jie, SUN Xiao-gang, LIU Ye-xiang. On the corrosion behaviour of Ni-NiO-NiFe2O4 cermets as inert anodes in aluminium electrolysis [C]// KVANDE K. Light Metals 2005. Warreudale PA: TMS, 2005: 529-534.
[6] TARCY G R. Corrosion and passivation of cermet inert anodes in cryolite-type electrolytes [C]// MILLER R E. Light Metals 1986. Warrendale, Pa, USA: TMS, 1986: 309-320.
[7] WEYAND J D, DEYOUNG D H, RAY S P, TARCY G R, BAKER F W. Inert anodes for aluminium smelting [R]. PA 15069, Washington D C: Aluminum Company of America, 1986.
[8] WINDISCH C R Jr, STEVEN C M. Electrochemical polarization studies on Cu and Cu-containing cermet anodes for the aluminum industry [C]// ZABREZNIK R D. Light Metals 1987. Warrendale, PA, USA: TMS, 1987: 351-355.
[9] OLSEN E, THONSTAD J. Nickel ferrite as inert anodes in aluminum electrolysis (partⅡ): Material performance and long-term testing [J]. Journal of Applied Electrochemistry, 1999, 29(3): 301-311.
[10] ZHANG Gang, LAI Yan-qing, TIAN Zhong-liang, QIN Qing-wei, LI Jie, LI wen-xian. Preparation of nickel ferrite based cermets for aluminum electrolysis [J]. Journal of Material Science and Engineering, 2003, 21(4): 44-47. (in Chinese)
[11] LAI Yan-qing, ZHANG Gang, LI Jie, LIU Ye-xiang. Effect of adding Cu-Ni on mechanical capacity and electrical conductivity of NiFe2O4-based cermets [J]. Journal of Central South University (Science and Technology), 2004, 35(6): 880-884. (in Chinese)
[12] LI Jie, DUAN Hua-nan, LAI Yan-qing, TIAN Zhong-liang, LIU Ye-xiang. Effect of NiO content on the corrosion behaviour of Ni-xNiO-NiFe2O4 cermets in Na3AlF6-Al2O3 melts [J]. Trans Nonferrous Met Soc China, 2004: 14(6): 1180-1186.
[13] DEYOUNG D H. Solubilities of oxides for inert anodes in cryolite–based melts [C]// MILLER R E. Light Metals 1986: 1986. Warrendale, PA, USA: TMS, 1986: 299-307.
[14] LAI Yan-qing, TIAN Zhong-liang, QIN Qing-wei, ZHANG Gang, LI Jie. Solubility of composite oxide ceramics in Na3AlF6-Al2O3 melts [J]. Journal of Central South University of Technology, 2003, 34(3): 245-248.
Foundation item: Project(2005CB623703) supported by the National Basic Research Program of China
Corresponding author: TIAN Zhong-liang; Tel: +86-731-8876454; E-mail: tianzhongliang@126.com
(Edited by LI Xiang-qun)